Abstract of masters work
Content
Introduction
Introduction
An important processing unit is a modern caster tundish (CT), its design has a significant impact on product quality. Currently, the use of PCs is expanded to universal smelting aggregate functions for additional refining of steel. In this regard, the development of theoretical and practical aspects of the development of metal refining technology in the CT is an urgent task. An important element of the research process of continuous casting of steel is hydro-physical modeling of processes occurring in the bath CT, which is now becoming the subject of attention of scientists-metallurgists. Many domestic and foreign researchers studying the behavior of the metal and slag bath CT and hydrodynamic features of the casting process using advanced physical models.
Training and Simulation
The purpose of this work is the theoretical and experimental investigation of the processes occurring at argon refining steel in a continuous casting machine CT using physical modeling. To study the processes taking place in the CT, the physical model tundish, created at the Department of DonNTU MOZCHM imitating tundish two-strand slab caster PJSC "AMC" with a capacity of 60 t (Figure 1) was used. From the similarity of hydrodynamic conditions and respect for equality and for her full-scale object, criteria and Froude homochronicity geometric model scale is 1:5. The model is made of a transparent material (Plexiglas) that allows you to monitor processes in the CT tub, and includes basic functional units, which are available on an industrial site. When you create a model for similarity flows taking into account surface tension forces taken into account the observance of equal numbers of Weber. Calculation model casting speed was conducted taking into account the action of gravity (Froude number). After calculating the speed scale time scale it has been determined taking into account the criteria homochronicity characterizing the time course of transients. Proceeding from the conditions of continuity of flow determines the amount of fluid flow. The working fluid, which simulates the molten steel, the water used at a temperature of 18-25 °C, and as the liquid slag - engine oil. The choice of water as simulation liquid due to the fact that the values of the viscosity of water and became in-furnace treatment temperature sufficiently close to each other. The choice of the engine oil due to its slag properties, which are high in surface tension and viscosity depending on the change in temperature over a wide range, which enables the study blown bubble process exit gas to the surface of the liquid bath and to evaluate the possibility of involving in stirring the slag cover. It is known that the system "water - engine oil" is widely used by many researchers to model the behavior of the slag.
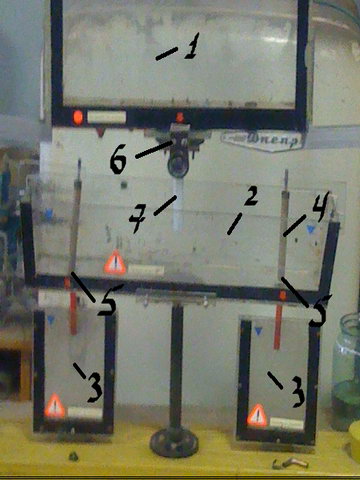
Implementation experience
According to our calculations, for the diameter of the bubble at the time of passing through equal 10-11 mm layer of slag (the optimum value of argon bubble) bubble diameter at the time of the separation of 4,0-4,9 mm [5]; annular tuyere hole diameter d = 1,5 mm and odnosoplovoy - 1.8 mm. Hole spacing L = 10×d [6]. The air supply was carried out through a laboratory compressor with receiver at three flow rate - 10, 12 and 15 l/min. In the course of experiments visual evaluation was performed motion trajectory bubbles in the liquid metal bath from the CT into the slag through a lance during blowing and bottom blowing tuyere through an annular top. The dynamics of fluid flow propagation is shown in Figure 2.
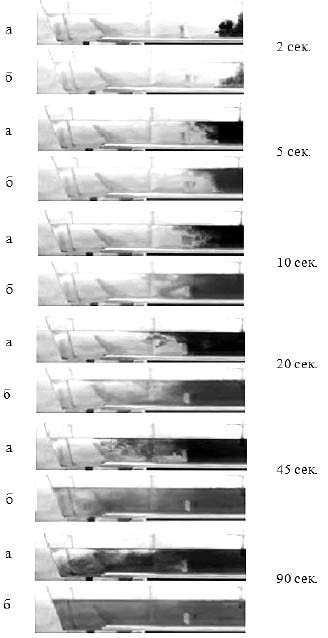
Figures 3 and 4 show embodiments of purging the liquid bath in the CT through a variety of devices on top and bottom.

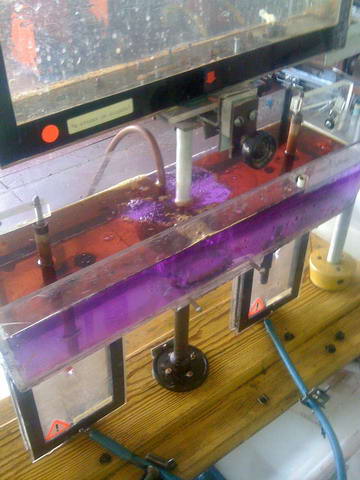
Conclusions
As the pictures (2 - 4), the process of blowing through an annular tuyere top much more efficient purging bottom in view of the fact that the slag begins to move over to the wall of the tundish, thus giving free access for metal flowing from the ladle, not allowing slag to fall into teeming glass PC while purging bottom slag distributes purge only near place. Furthermore bottom purge control requires a certain purging intensity as possible splashes of metal from the ladle, while devoid of the annular tuyere of defect and can perform the purge process in a quiet mode,.
Bibliography
1. Смирнов А.Н. Процессы непрерывной разливки стали / Смирнов А.Н., Пилюшенко В.Л., Минаев А.А. и др. - Донецк: ДонНТУ, 2002. - 536 с.
2. Еронько С.П., Быковских С.В. Физическое моделирование процессов внепечной обработки и разливки стали. - К.: Техника,1998. - 196 с.
3. Еронько С.П., Ошовская Е.В., Штепан Е.В. и др. // Металлургические процессы и оборудование. - 2009. - №4(18). - С.20 - 32.
4. Научно-практическая конференция «Инновационные технологии внепечной металлургии чугуна и стали» / Смирнов А.Н., Кравченко А.В., Куберский С.В., Кузнецов Д.Ю, 2011. - 182 с.
5. Дейч М.Е. Техническая газодинамика / М.Е. Дейч. - М.: Госэнергоиздат, 1974. - 671 с.
6. Кутателадзе С.С., Стыркович М.А. Гидродинамика газожидкостных систем / С.С. Кутателадзе, М.А. Стыркович. - М.: Энергия, 1976. - 296 с.