Реферат по теме выпускной работы
Содержание
- Введение
- 1. Актуальность темы
- 2. Цель и задачи исследования
- 3. Значение и применение продукции
- 4. Экспериментальная часть
- 4.1 Методика изготовления экспериментальных образцов
- 4.2 Исследование составов с добавлением технического глинозема
- Выводы
- Список источников
Введение
В связи с интенсивным развитием научных и технических процессов, требования, предъявляемые к конструкционным материалам, для обеспечения наибольшей производительности аппаратов, беспрестанно растут. Тепловые агрегаты длительное время могут использоваться в условиях резких колебаний температуры, воздействии агрессивных сред, эрозионного и коррозионного износа, все это негативно сказывается на сроке их службы, а также качестве выпускаемой продукции. Как показывает практика, применение качественных, а, следовательно, и более дорогих материалов для кладки производственных печей не всегда возможно или целесообразно, вследствие чего обычно используют более дешевые изделия, которые менее устойчивы к действию различных разрушающих факторов. В свою очередь, это приводит, во–первых, к быстрому износу футеровки аппаратов и увеличению отходов, большая часть которых идет в отвалы, а во–вторых, увеличивается расход исходных сырьевых компонентов на производство новых материалов для кладки печей.
Для продление срока службы футеровки промышленных печей и других тепловых агрегатов, а также для уменьшения образования производственных отходов и более рационального использования природных ресурсов, используют защитные покрытия различного состава, состоящие из огнеупорных порошков заданной зернистости и связующего. Покрытия наносят в виде обмазок и торкрет–масс не только для защиты огнеупорной футеровки и продления срока службы печи, но и для ремонта тепловых агрегатов как в холодном виде, так и при высоких температурах без их остановки.
1. Актуальность темы
Актуальность исследования обусловлена с наличием в нашем регионе большого количества металлургических, коксохимических и других производств, использующих высокотемпературные тепловые аппараты, что обуславливает необходимость продления срока службы футеровок печей.
2. Цель и задачи исследования
Целью данной работы является изучение основных свойств и характеристик уже существующих огнеупорных покрытий, их свойств (таких как плотность, пористость, водопоглощение, механическая прочность и термическая стойкость), а также исследование влияния различных добавок на свойства огнеупорных покрытий и проработка возможности замены традиционных огнеупорных заполнителей техногенными продуктами.
3. Значение и применение продукции
Огнеупорные покрытия представляют собой порошки из различных огнеупорных материалов определенной зернистости, в которые для связывания вводят различные добавки. Эти покрытия наносят на рабочую поверхность огнеупорной футеровки методом торкретирования при помощи специальных аппаратов, а в отдельных случаях вручную в виде обмазок, для предохранения их от преждевременного износа при воздействии шлаков и других разрушающих реагентов, а также для ремонта повреждений, как во время остановок, так и в процессе эксплуатации печных агрегатов, что в целом способствует продлению срока службы кладки [1]. Толщина слоя обмазки должна составлять 3 – 7 мм. При большей толщине покрытие может растрескаться в процессе сушки и отпасть, при меньшей толщине понижается ее стойкость. Схватывание и твердение обмазок происходит в результате высыхания и спекания массы при нагреве.
Состав и зернистость покрытий определяются способом их нанесения, родом ремонтируемой или защищаемой ими кладки и условиями службы. В составах масс содержится заполнитель с зернами размером менее 2 мм и при содержании тонких фракций менее 0,2 – 0,5 мм порядка 50 %, химическая связка, пластификатор и вода. Огнеупорный заполнитель обычно подбирают по аналогии с природой защищаемой кладки. Пластификаторами являются бентониты или пластичные огнеупорные глины, вводимые в количестве 5 – 10 %. Химической связкой могут являться вводимые в количествах 1 – 15 % растворимое стекло, хроматы, фосфаты, соли магния, шлаки, железистые добавки и др. Однако применение этих добавок допустимо лишь в тех случаях, когда понижение огнеупорных свойств массы не может ухудшить ее стойкость в службе [2].
Например, масса для ремонтов динасовой кладки коксовых печей содержит 90 – 95 % шамота и 5 – 10 % огнеупорной глины. Для связывания массы вводят ортофосфорную кислоту в количестве 15 – 17 % сверх массы сухих компонентов [3].
Для горячего торкретирования мартеновских и электродуговых печей используют хромомагнезитовые массы с различным содержанием хромитового, хромомагнезитового и магнезитового порошка. В эти массы в водят около 5 – 10 % пластичной огнеупорной глины. В отдельных случаях также вводят шлак или окалину.
В массах для печей цветной металлургии с динасовой кладкой используют динасовый бой или кварцит с 5 – 10 % глины, а для хромомагнезитовой и магнезитовой кладки – бой хромомагнезитового кирпича, хромитовую руду, магнезитовый металлургический порошок.
Для защиты шамотной футеровки паровых котлов и различных печей используют хромитовую, шамотную, шамотно–корундовую обмазки, содержащие 6 % глины, сходного типа обмазку применяют для защиты шамотных легковесов [4].
Предъявляемые к покрытиям требования очень разнообразны. В одних случаях требуется высокая стойкость против больших тепловых нагрузок, в других – обеспечение высоких физико–механических характеристик. Чаще всего от огнеупорных обмазок требуется хорошая схватываемость с ремонтируемыми или защищаемыми ими материалами футеровок, малые объемные изменения при сушке и высоких температурах, стойкость против химических и механических разрушений.
Во многих случаях от покрытия требуется комплекс свойств, обеспечивающих его длительную работу в условиях эксплуатации. Естественно, весь этот комплекс свойств трудно совместить в одном материале. Однако, при анализе соответствующей литературы [1 – 12], можно сделать вывод, что при правильном подборе соотношения основных компонентов смеси обмазки и введении соответствующих добавок можно существенно повысить эксплуатационные свойства защитных покрытий.
Большие возможности открывает применение композиционных покрытий [6], представляющих собой сочетание двух или нескольких разнородных материалов, позволяющее наиболее полно использовать преимущества отдельных компонентов. Сочетание компонентов с различными свойствами дает возможность получить покрытия требуемых характеристик.
4. Экспериментальная часть
4.1 Методика изготовления экспериментальных образцов
Для проведения исследований, в качестве стандартного состава, от которого в дальнейшем будут отталкиваться все проводимые исследования, был выбран состав на основе шамота 90 % и огнеупорной глины 10 %, используемых для ремонта кладки коксовых печей [3]. В качестве вяжущего используется фосфорная кислота с концентрацией 57 % в количестве 15 – 17 % (из расчета к массе сухих порошков). В дальнейшем, за счет уменьшения содержания шамота в массе, для улучшения тех или иных свойств покрытий, в небольших количествах вводят различные добавки.
Для проверки главного свойства покрытий – сцепления с поверхностью, а так же для убеждения в целесообразности использования конкретного покрытия, был приготовлен и нанесен на образцы огнеупорного кирпича ряд обмазок различного состава.
В качестве огнеупорной подложки для анализа покрытий, были взяты шамотные огнеупорные изделия общего назначения и распилены на небольшие образцы размером ~ 2,5 × 3,5 см.
Огнеупорную обмазку готовят следующим образом. Взятые в необходим соотношении компоненты массой 5 г, в сухом состоянии тщательно перемешивают. Добавляют нужное количество вяжущего (для стандартного состава 1,2 мл Н3РО4, для новых составов – устанавливается экспериментально) и продолжают смешение до получения однородной смеси. Полученную обмазку наносят тонкими слоями на предварительно подготовленные образцы огнеупоров при комнатной температуре (рис. 1).
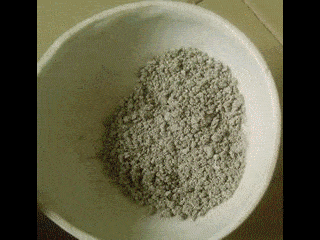
Рисунок 1 – Приготовление
обмазки и её нанесение на поверхность подложки
(анимация: 7 кадров, 10 циклов повторения,
135 килобайт)
Все образцы, с нанесенным покрытием, не зависимо от скорости его твердения, проходят сушку на воздухе в течение суток, а затем в течение 2 часов подвергаются сушке и обжигу.
При удовлетворительном сцеплении покрытия с огнеупором, для дальнейших экспериментальных определений основных свойств обмазок (прочность, плотность, водопоглощение и т.д.), с помощью лабораторного ручного пресса (рис. 4.2) и металлической пресс–формы диаметром 20 мм (рис. 4.3), методом полусухого прессования (относительная влажность смеси ~ 8 %) готовят цилиндрические образцы, того же состава.
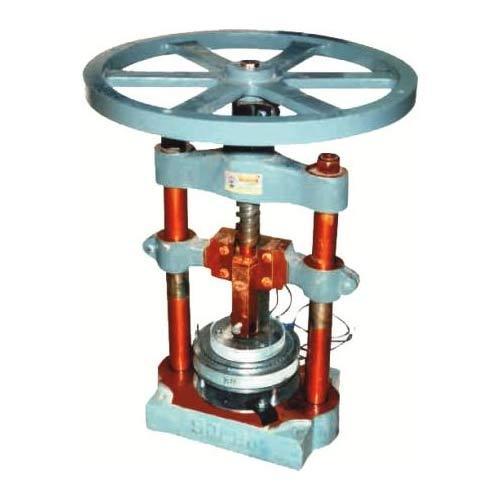
Рисунок 4.2 — Пресс
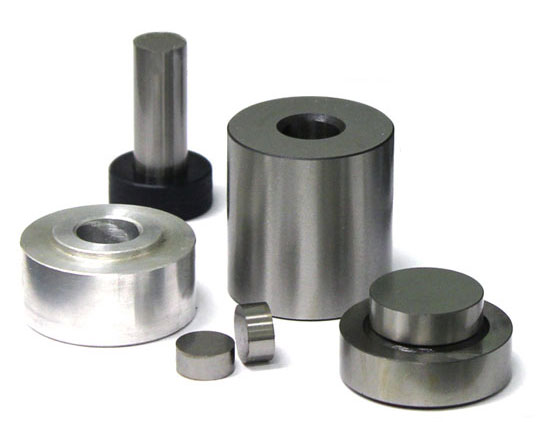
Рисунок 4.3 — Пресс–формы
Для придания формируемым образцам высоты равной их диаметру, т.е. ~ 20 мм, необходимая масса сухих компонентов должна составлять примерно 11 грамм (установлено экспериментально).
Сформованные образцы нумеруются и также подвергаются сушке на воздухе (в течение суток) и в сушильном шкафу (течение 2 часов при 100 °C). Высушенные образцы (рис.4.4) подлежат тщательному осмотру для выявления разного вида брака (трещин, цеков), а затем направляются на обжиг. Температура обжига зависит от исходного состава компонентов. Время выдержки при максимальной температуре обжига 30 – 35 минут.
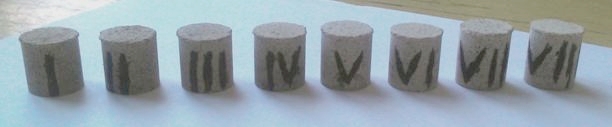
Рисунок 4.4 — Вид готовых цилиндрических образцов для испытаний
4.2 Исследование составов с добавлением технического глинозема
В настоящее время проведены экспериментальные исследования покрытий на основе шамота и огнеупорной глины, используемых для ремонта кладки коксовых печей, с добавлением технического глинозема.
Глинозем представляет собой распространенную природную форму оксида алюминия Al2O3. В чистом виде он встречается в виде минерала корунда, ярко выражен в составе бокситов – горных глинистых пород, а также алунитов, нефелинов и каолинов. Технический глинозем – это тонкодисперсный порошок белого цвета, имеющий примерно следующий химический состав (на прокаленное вещество): Al2O3 99,0 – 99,8 %, SiО2 0,1 – 0,25 %, Na2О 0,30 – 0,50 %, прочие оксиды 0,05 – 0,1 %. Огнеупорность глинозема приведенного состава около 2000 °С [11].
Для определения влияния глинозема на свойства покрытий, были приготовлены и исследованы обмазки состава, приведенного в таблице 4.1.
Таблица 4.1 – Состав огнеупорного покрытия
Компоненты | Состав, масс. % | |||
I | II | III | IV | |
Шамот | 90 | 80 | 70 | 60 |
Глина огнеупорная | 10 | 10 | 10 | 10 |
Глинозём | 0 | 10 | 20 | 30 |
Все приготовленные составы имели хорошую удобоукладываемость и сцепление с поверхностью огнеупора, однако при увеличении процентного содержания глинозема эти показатели увеличивались, а также заметно уменьшалось время твердения обмазки.
Для определения качества исследуемых покрытий было проведено экспериментальное определение плотности, пористости, водопоглощения, усадки, термостойкости и механической прочности на сжатие.
При испытании образцов на термостойкость (способность покрытий выдерживать, не разрушаясь, резкие колебания температур), в лабораторных условиях используют метод определения по числу теплосмен до разрушения покрытия. Сущность метода заключается в том, что исследуемое покрытие нагревают до температуры 900 °С, выдерживают 5 – 10 минут, а затем охлаждают в течение 20 минут на воздухе, далее повторяют цикл.
Все выбранные составы показали хорошую стойкость к тепловым ударам, выдержав по 20 циклов теплосмен (без образования каких–либо повреждений). На рисунках 4.5 и 4.6 показаны образцы с нанесённым покрытием до и после определения термостойкости.
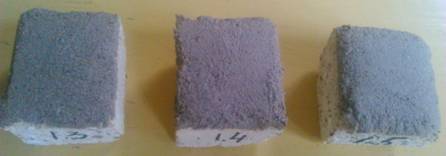
Рисунок 4.5 — Образцы до термообработки
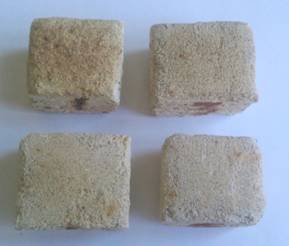
Рисунок 4.6 — Образцы после 20 теплосмен
Методика определения открытой пористости и кажущейся плотности изделий состоит в следующем: предварительно высушенные и взвешенные испытуемые цилиндрические образцы насыщают водой при кипячении в течение 45 минут, затем взвешивают насыщенные образцы на воздухе и гидростатическим взвешиванием в той же жидкости, которой они насыщены. По полученным результатам рассчитывают показатели плотности, пористости и водопоглощения.
Прочностные свойства покрытий оценивают по пределу прочности при сжатии, для этого цилиндрические образцы устанавливают в центр испытательного стола гидравлического пресса, вручную опускают верхнюю плитку до соприкосновения с образцом, включают пресс и плавно увеличивают нагрузку. Давление на образец прекращают, когда стрелка динамометра начнет возвращаться в первоначальное положение.
Результаты всех испытаний приведены в таблице 4.2 (средние арифметические значения из трех параллельных опытов).
Таблица 4.2 – Сводная таблица результатов определения свойств составов с глинозёмом
Температура обжига, °C | Состав обмазки | Показатели | |||
водопоглощение, % | открытая пористость, % | кажущаяся плотность, г/см3 | прочность на сжатие, МПа | ||
900 | I II III IV |
11,53 13,13 15,79 19,23 |
22,33 24,97 28,76 33,49 |
1,94 1,90 1,82 1,74 |
22,58 18,63 11,52 8,87 |
1100 | I II III |
11,14 12,70 19,28 |
22,03 24,78 34,82 |
1,98 1,95 1,81 |
23,61 20,95 9,31 |
1300 | I II III |
9,80 11,70 11,92 |
18,65 22,27 23,42 |
1,90 1,90 1,97 |
42,18 35,18 37,05 |
После сушки и термообработки образцы цилиндрической формы данных составов не претерпевали объемных изменений и сохраняли свои размеры (отсутствие усадки является положительным свойством для покрытий).
Анализируя данные сводной таблицы 4.2, можно отметить, что при увеличении содержания глинозема в составе покрытия пропорционально увеличивается его водопоглощение и пористость, а это в свою очередь снижает показатели плотности и прочности, что является нежелательным. Однако из таблицы также видно, что с увеличением температуры обжига увеличиваются прочностные свойства покрытий, что связанно с лучшим спеканием исходных сырьевых компонентов.
Таким образом, можно сделать вывод, что введение глинозема рекомендуется только в том случае, если необходимо значительно увеличить огнеупорность или термостойкость защищаемого материала при высоких температурах службы, в иных случаях это является нецелесообразным.
Выводы
Длительность и эффективность работы высокотемпературных промышленных агрегатов зависит от уровня их технической эксплуатации, своевременной диагностики возникающих дефектов и качественного проведения профилактических ремонтов. Своевременное выполнение необходимого объёма и применение наиболее рациональных профилактических ремонтов с применением огнеупорных покрытий, позволяют значительно продлить срок службы промышленных печей.
В дальнейшем планируется расширить круг добавок с целью улучшения таких свойств покрытий как:
- повышение адгезии защитной обмазки к поверхности керамических материалов;
- увеличение прочности покрытия;
- уменьшение коэффициента термического расширения;
- сокращение времени твердения;
- улучшение шлакоуствойчивости покрытия и его технологичности при нанесении на футеровку.
Список источников
- Огнеупорное производство: В 2 т. Справ, изд. / Под ред. Д. И. Гавриша. – М.: Металлургия, 1965. – Т. 2 – 584 с.
- Будников, П. П. Химическая технология керамики и огнеупоров / П. П. Будников. – М.: Стройиздат, 1972. – 552 с.
- Справочник коксохимика: В 6 т. Справ, изд. / Под ред. В. И. Рудыки, Ю. Е. Зингермана. – Харьков: Издательский дом ИНЖЭК, 2014. – Т. 2: Производство кокса. – 728 с.
- Огнеупоры для промышленных агрегатов и топок: В 2 т. Справ, изд. / Под ред. И.Д. Кащеева, Е.Е. Гришенкова. – М.: Интермет Инжиниринг, 2002. – Т. 2: Служба огнеупоров. – 656 с.
- База патентов СССР [Электронный ресурс]. – Режим доступа: http://patents.su.
- Демиденко, Л. М. Высокоогнеупорные композиционные покрытия / Л. М. Демиденко. – М.: Металлургия, 1979. – 216 с.
- Кащеев, И. Д. Химическая технология огнеупоров: Учебное пособие / И.Д. Кащеев, Стрелов К.К., Мамыкин П.С. – М.: Интермет Инжиниринг, 2007.
- Огнеупорные материалы. Структура, свойства, испытания: Пер. с нем./ Под ред. Г. Роучка, X. Вутнау. – М.: Интермет Инжиниринг, 2010. – 392 с.
- Стрелов, К. К. Теоретические основы технологии огнеупорных материалов / К.К. Стрелов. – М.: Металлургия, 1985. – 480 с.
- Кащеев, И. Д. Свойства и применение огнеупоров: Справочное издание / И. Д. Кащеев. – М.: Теплотехник, 2004. – 430 с.
- Огнеупорное производство: В 2 т. Справ, изд. / Под ред. Д. И. Гавриша. – М.: Металлургия, 1965. – Т. 1 – 580 с.
- Каталог–справочник. Огнеупоры: материалы, изделия, свойства и применение: В 2 т. Под. ред. И. Д. Кащеева. – М.: Теплоэнергетик, 2003. – Т. 1. – 336 с.
При написании данного реферата магистерская работа ещё не завершена. Окончательное завершение: май 2018 года. Полный текст работы и материалы по теме могут быть получены у автора или его руководителя после указанной даты.