Реферат за темою випускної роботи
Зміст
- Вступ
- 1. Актуальність теми
- 2. Мета й задачі дослідження
- 3. Значення та застосування продукції
- 4. Експериментальна частина
- 4.1 Методика виготовлення експериментальних зразків
- 4.2 Дослідження складів з додаванням технічного глинозему
- Висновки
- Перелік посилань
Вступ
У зв'язку з інтенсивним розвитком наукових і технічних процесів, вимоги, що пред'являються до конструкційних матеріалів, для забезпечення максимальної продуктивності апаратів, безперестанку ростуть. Теплові агрегати тривалий час можуть використовуватися в умовах різких коливань температури, дії агресивних середовищ, ерозійного та корозійного зносу, все це негативно позначається на терміні їх служби, а також якості продукції, що випускається. Як показує практика, застосування якісних, а, отже, і більш дорогих матеріалів для кладки виробничих печей не завжди можливо або доцільно, внаслідок чого зазвичай використовують більш дешеві вироби, які менш стійкі до дії різних руйнуючих факторів. У свою чергу, це призводить, по–перше, до швидкого зносу футеровки апаратів і збільшення відходів, велика частина яких йде у відвали, а по–друге, збільшується витрата вихідних сировинних компонентів на виробництво нових матеріалів для кладки печей.
Для продовження терміну служби футеровки промислових печей та інших теплових агрегатів, а також для зменшення утворення виробничих відходів і більш раціонального використання природних ресурсів, використовують захисні покриття різного складу, що складаються з вогнетривких порошків заданої зернистості та зв'язуючого. Покриття наносять у вигляді обмазок і торкрет–мас не тільки для захисту вогнетривкої футеровки і продовження терміну служби печі, але і для ремонту теплових агрегатів як в холодному вигляді, так і при високих температурах без їх зупинки.
1. Актуальність теми
Актуальність дослідження зумовлена наявністю в нашому регіоні великої кількості металургійних, коксохімічних та інших виробництв, які використовують високотемпературні теплові апарати, що обумовлює необхідність продовження терміну служби футеровок печей.
2. Мета й задачі дослідження
Метою даної роботи є вивчення основних властивостей і характеристик вже існуючих вогнетривких покриттів, методів їх контролю (таких як щільність, пористість, водопоглинання, механічна міцність і термічна стійкість), а також дослідження впливу різних добавок на властивості вогнетривких покриттів та опрацювання можливості заміни традиційних вогнетривких наповнювачів техногенними продуктами.
3. Значення та застосування продукції
Вогнетривкі покриття являють собою порошки з різних вогнетривких матеріалів певної зернистості, в які для зв'язування вводять різні добавки. Ці покриття наносять на робочу поверхню вогнетривкої футеровки методом торкретування за допомогою спеціальних апаратів, а в окремих випадках вручну у вигляді обмазок, для запобігання їх від передчасного зносу при впливі шлаків і інших руйнівних реагентів, а також для ремонту пошкоджень, як під час зупинок, так і в процесі експлуатації пічних агрегатів, що в цілому сприяє продовженню терміну служби кладки [1]. Товщина шару обмазки повинна складати 3 – 7 мм. При більшій товщині покриття може растрескаться в процесі сушіння і відпасти, при меншій товщині знижується її стійкість. Схоплювання і твердіння обмазок відбувається в результаті висихання і спікання маси при нагріванні.
Склад і зернистість покриттів визначаються способом їх нанесення, родом кладки яка ремонтуєься або захищається ними, та умовами служби. У складах мас міститься заповнювач з зернами розміром менше 2 мм при утриманні тонких фракцій менше 0,2 – 0,5 мм близько 50 %, хімічна зв'язка, пластифікатор і вода. Вогнетривкий заповнювач зазвичай підбирають за аналогією з природою захищаємої кладки. Пластифікаторами є бентоніти або пластичні вогнетривкі глини, що вводяться в кількості 5 – 10 %. Хімічною зв'язкою можуть бути введені в кількостях 1 – 15 % розчинне скло, хромати, фосфати, солі магнію, шлаки, залізисті добавки та ін. Однак застосування цих добавок допустимо лише в тих випадках, коли зниження вогнетривких властивостей маси не може погіршити її стійкість в службі [2].
Наприклад, маса для ремонту динасової кладки коксових печей містить 90 – 95 % шамоту та 5 – 10 % вогнетривкої глини. Для зв'язування маси вводять ортофосфорну кислоту в кількості 15 – 17 % понад маси сухих компонентів [3].
Для гарячого торкретування мартенівських та електродугових печей використовують хромомагнезитові маси з різним вмістом хромітового, хромомагнезитового та магнезитового порошку. У ці маси вводять близько 5 – 10 % пластичної вогнетривкої глини. В окремих випадках також вводять шлак або окалину.
В масах для печей кольорової металургії з динасовою кладкою використовують динасовий бій або кварцит з 5 – 10 % глини, а для хромомагнезитової і магнезитової кладки – бій хромомагнезитової цегли, хромітову руду, магнезитовий металургійний порошок.
Для захисту шамотної футеровки парових котлів і різних печей використовують хромітової, шамотну, шамотно–корундову обмазки, що містять 6 % глини, схожого типу обмазку застосовують для захисту шамотних легковаговиків [4].
Запропоновані до покриттів вимоги дуже різноманітні. В одних випадках потрібна висока стійкість проти великих теплових навантажень, в інших – забезпечення високих фізико–механічних характеристик. Найчастіше від вогнетривких обмазок потрібна хороше зчеплення з матеріалами футеровок які ремонтуються або захищяються ними, малі об'ємні зміни при сушінні і високих температурах, стійкість проти хімічних і механічних руйнувань.
У багатьох випадках від покриття потрібно комплекс властивостей, що забезпечують його тривалу роботу в умовах експлуатації. Природно, весь цей комплекс властивостей важко поєднати в одному матеріалі. Однак, при аналізі відповідної літератури [1 – 12], можна зробити висновок, що при правильному підборі співвідношення основних компонентів суміші обмазки і введенні відповідних добавок можна істотно підвищити експлуатаційні властивості захисних покриттів.
Великі можливості відкриває застосування композиційних покриттів [6], що представляють собою поєднання двох або декількох різнорідних матеріалів, що дозволяє найбільш повно використовувати переваги окремих компонентів. Поєднання компонентів з різними властивостями дає можливість отримати покриття необхідних характеристик.
4. Експериментальна частина
4.1 Методика виготовлення експериментальних зразків
Для проведення досліджень, в якості стандартного складу, від якого в подальшому будуть відштовхуватися всі проведені дослідження, був обраний склад на основі шамоту 90 % і вогнетривкої глини 10 % (використовується для ремонту кладки коксових печей) [3]. В якості в'яжучого використовується фосфорна кислота з концентрацією 57 % в кількості 15 – 17 % (з розрахунку до маси сухих порошків). Надалі, за рахунок зменшення вмісту шамоту в масі, для поліпшення тих чи інших властивостей покриттів, в невеликих кількостях вводять різні добавки.
Для перевірки головного властивості покриттів – зчеплення з поверхнею, а так само для переконання в доцільності використання конкретного покриття, був приготований і завдано на зразки вогнетривкої цегли ряд обмазок різного складу.
В якості вогнетривкої підкладки для аналізу покриттів, були взяті шамотні вогнетривкі вироби загального призначення і розпиляні на невеликі зразки розміром ~ 2,5 × 3,5 см.
Вогнетривку глину готують наступним чином. Взяті в необхідному співвідношенні компоненти масою 5 г, в сухому стані ретельно перемішують. Додають потрібну кількість в'яжучого (для стандартного складу 1,2 мл Н3РО4, для нових складів – встановлюється експериментально) і продовжують змішання до отримання однорідної суміші. Отриману обмазку наносять тонкими шарами на попередньо підготовлені зразки вогнетривів при кімнатній температурі (рис. 1).
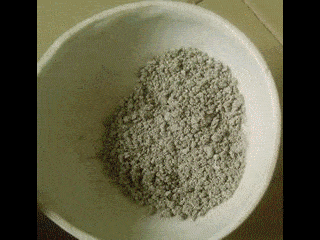
Рисунок 1 –
Приготування обмазки та її нанесення на поверхню підкладки
(анімація: 7 кадрів, 10 циклів повторення,
135 килобайт)
Всі зразки, з нанесеним покриттям, не залежно від швидкості його твердіння, проходять сушку на повітрі протягом доби, а потім протягом 2 годин піддаються сушці і випалу.
При задовільному зчепленні покриття з вогнетривом, для подальших експериментальних визначень основних властивостей обмазок (міцність, щільність, водопоглинання і т.д.), за допомогою лабораторного ручного преса (рис. 4.2) і металевої прес–форми діаметром 20 мм (рис. 4.3), методом напівсухого пресування (відносна вологість суміші ~ 8 %) готують циліндричні зразки, того ж складу.
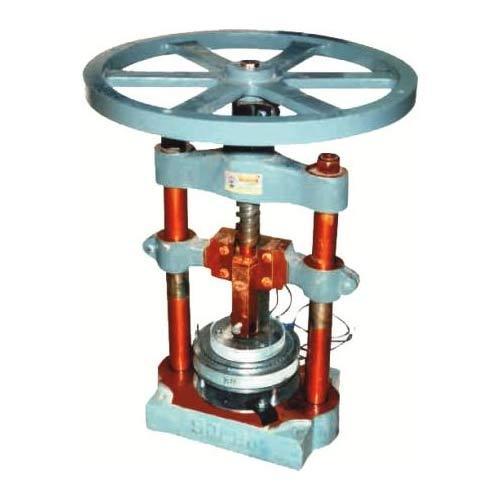
Рисунок 4.2 — Прес
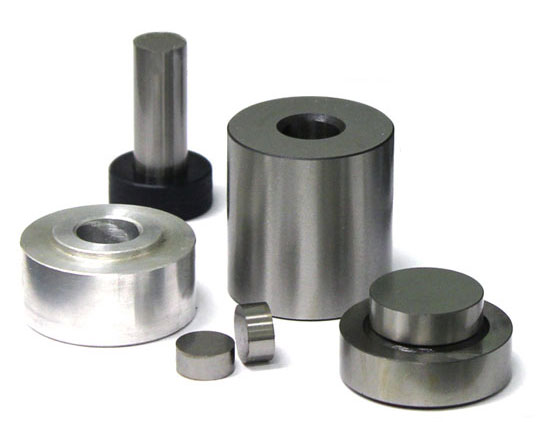
Рисунок 4.3 — Прес–форма
Для додання зразкам висоти рівній їх діаметру, тобто ~ 20 мм, необхідна маса сухих компонентів повинна становити приблизно 11 грам (встановлено експериментально).
Сформовані зразки нумеруються і також піддаються сушці на повітрі (протягом доби) і в сушильній шафі (протягом 2 годин при 100 °C). Висушені зразки підлягають ретельному огляду для виявлення різного виду дефектів (тріщин, цеков), а потім направляються на випал (рис.4.4). Температура випалу залежить від вихідного складу компонентов. Час витримки при максимальній температурі випалу 30 – 35 хвилин.
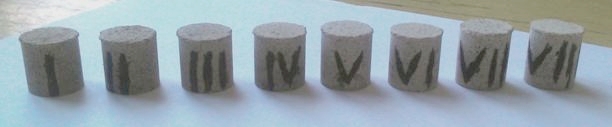
Рисунок 4.4 — Вигляд готових циліндричних зразків для випробувань
4.2 Дослідження складів з додаванням технічного глинозему
В даний час проведені експериментальні дослідження покриттів на основі шамоту і вогнетривкої глини, що використовуються для ремонту кладки коксових печей, з додаванням технічного глинозему.
Глинозем являє собою поширену природну форму оксиду алюмінію Al2O3. В чистому вигляді він зустрічається у вигляді мінералу корунду, яскраво виражений в складі бокситів – гірських глинистих порід, а також алунитов, нефелинів і каолінів. Технічний глинозем – це тонкодисперсний порошок білого кольору, який має приблизно наступний хімічний склад (на прожарену речовину): Al2O3 99,0 – 99,8 %, SiО2 0,1 – 0,25 %, Na2О 0,30 – 0,50 %, інші оксиди 0,05 – 0,1 %. Вогнетривкість глинозему наведеного складу близько 2000 °С [11].
Для визначення впливу глинозему на властивості покриттів, були приготовлені і досліджені обмазки складу, наведеного в таблиці 4.1.
Таблиця 4.1 – Склад вогнетривкого покриття
Компоненти | Склад, мас. % | |||
I | II | III | IV | |
Шамот | 90 | 80 | 70 | 60 |
Глина вогнетривка | 10 | 10 | 10 | 10 |
Глинозем | 0 | 10 | 20 | 30 |
Всі приготовані склади мали гарну легкоукладальність і зчеплення з поверхнею іогнетрива, однак при збільшенні процентного вмісту глинозему ці показники збільшувалися, а також помітно зменшувалася час твердіння обмазки.
Для визначення якості досліджуваних покриттів було проведено експериментальне визначення щільності, пористості, водопоглинання, усадки, термостійкості і механічної міцності на стиск.
При випробуванні зразків на термостійкість (здатність покриттів витримувати, не руйнуючись, різкі коливання температур), в лабораторних умовах використовують метод визначення за кількістю теплозмін до руйнування покриття. Суть методу полягає в тому, що досліджуване покриття нагрівають до температури 900 °С, витримують 5 – 10 хвилин, а потім охолоджують протягом 20 хвилин на повітрі, далі повторюють цикл.
Всі вибрані склади показали хорошу стійкість до теплових ударів, витримавши по 20 циклів теплозмін (без утворення будь–яких ушкоджень). На малюнках 4.5 і 4.6 показані зразки з нанесеним покриттям до і після визначення термостійкості.
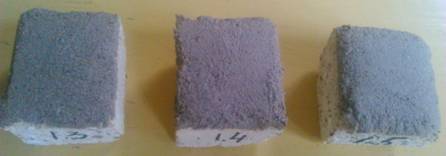
Рисунок 4.5 — Зразки до термообробки
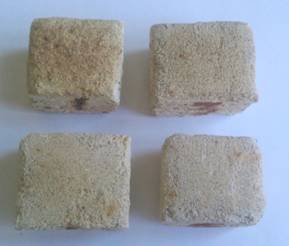
Рисунок 4.6 — Зразки після 20 теплозмін
Методика визначення відкритої пористості і уявної щільності виробів полягає в наступному: попередньо висушені і зважені випробовувані циліндричні зразки насичують водою при кип'ятінні протягом 45 хвилин, потім зважують насичені зразки на повітрі і гідростатичним зважуванням в тій же рідини, якою вони насичені. За отриманими результатами розраховують показники щільності, пористості і водопоглинання.
Міцність покриттів оцінюють за межою міцності при стисненні, для цього циліндричні зразки встановлюють в центр випробувального столу гідравлічного пресу, вручну опускають верхню плитку до зіткнення із зразком, включають прес і плавно збільшують навантаження. Тиск на зразок припиняють, коли стрілка динамометра почне повертатися в початкове положення.
Результати всіх випробувань наведені в таблиці 4.2 (середнє арифметичне значення з трьох паралельних дослідів).
Таблиця 4.2 – Зведена таблиця результатів визначення властивостей складів з глиноземом
Температура випалу, °C | Склад обмазки | Показники | |||
водопоглинання, % | відкрита пористість, % | уявна густина, г/см3 | міцність на стиск, МПа | ||
900 | I II III IV |
11,53 13,13 15,79 19,23 |
22,33 24,97 28,76 33,49 |
1,94 1,90 1,82 1,74 |
22,58 18,63 11,52 8,87 |
1100 | I II III |
11,14 12,70 19,28 |
22,03 24,78 34,82 |
1,98 1,95 1,81 |
23,61 20,95 9,31 |
1300 | I II III |
9,80 11,70 11,92 |
18,65 22,27 23,42 |
1,90 1,90 1,97 |
42,18 35,18 37,05 |
Після сушіння і термообробки зразки циліндричної форми даних складів не зазнавали об'ємних змін і зберігали свої розміри (відсутність усадки є позитивною властивістю для покриттів).
Аналізуючи дані зведеної таблиці 4.2, можна відзначити, що при збільшенні вмісту глинозему в складі покриття пропорційно збільшується його водопоглинання і пористість, а це в свою чергу знижує показники щільності і міцності, що є небажаним. Однак з таблиці також видно, що зі збільшенням температури випалу збільшуються міцнісні властивості покриттів, що пов'язано з кращим спіканням вихідних сировинних компонентів.
Таким чином, можна зробити висновок, що введення глинозему рекомендується тільки в тому випадку, якщо необхідно значно збільшити вогнетривкість або термостійкість захисного матеріалу при високих температурах служби, в інших випадках це є недоцільним.
Висновки
Тривалість і ефективність роботи високотемпературних промислових агрегатів залежить від рівня їх технічної експлуатації, своєчасної діагностики виникають дефектів і якісного проведення профілактичних ремонтів. Своєчасне виконання необхідного обсягу і застосування найбільш раціональних профілактичних ремонтів з застосуванням вогнетривких покриттів, дозволяє значно продовжити термін служби промислових печей.
Надалі планується розширити коло добавок з метою покращення таких властивостей покриттів як:
- підвищення адгезії захисної обмазки до поверхні керамічних матеріалів;
- збільшення міцності покриття;
- зменшення коефіцієнта термічного розширення;
- скорочення часу твердіння;
- поліпшення шлакостійкість покриття і його технологічності при нанесенні на футеровку.
Перелік посилань
- Огнеупорное производство: В 2 т. Справ, изд. / Под ред. Д. И. Гавриша. – М.: Металлургия, 1965. – Т. 2 – 584 с.
- Будников, П. П. Химическая технология керамики и огнеупоров / П. П. Будников. – М.: Стройиздат, 1972. – 552 с.
- Справочник коксохимика: В 6 т. Справ, изд. / Под ред. В. И. Рудыки, Ю. Е. Зингермана. – Харьков: Издательский дом ИНЖЭК, 2014. – Т. 2: Производство кокса. – 728 с.
- Огнеупоры для промышленных агрегатов и топок: В 2 т. Справ, изд. / Под ред. И.Д. Кащеева, Е.Е. Гришенкова. – М.: Интермет Инжиниринг, 2002. – Т. 2: Служба огнеупоров. – 656 с.
- База патентов СССР [Электронный ресурс]. – Режим доступа: http://patents.su.
- Демиденко, Л. М. Высокоогнеупорные композиционные покрытия / Л. М. Демиденко. – М.: Металлургия, 1979. – 216 с.
- Кащеев, И. Д. Химическая технология огнеупоров: Учебное пособие / И.Д. Кащеев, Стрелов К.К., Мамыкин П.С. – М.: Интермет Инжиниринг, 2007.
- Огнеупорные материалы. Структура, свойства, испытания: Пер. с нем./ Под ред. Г. Роучка, X. Вутнау. – М.: Интермет Инжиниринг, 2010. – 392 с.
- Стрелов, К. К. Теоретические основы технологии огнеупорных материалов / К.К. Стрелов. – М.: Металлургия, 1985. – 480 с.
- Кащеев, И. Д. Свойства и применение огнеупоров: Справочное издание / И. Д. Кащеев. – М.: Теплотехник, 2004. – 430 с.
- Огнеупорное производство: В 2 т. Справ, изд. / Под ред. Д. И. Гавриша. – М.: Металлургия, 1965. – Т. 1 – 580 с.
- Каталог–справочник. Огнеупоры: материалы, изделия, свойства и применение: В 2 т. Под. ред. И. Д. Кащеева. – М.: Теплоэнергетик, 2003. – Т. 1. – 336 с.
При написанні даного реферату магістерська робота ще не завершена. Остаточне завершення: травень 2018 року. Повний текст роботи та матеріали по темі можуть бути отримані у автора або його керівника після зазначеної дати.