Abstract
The contents
- Introduction
- 1. Theme urgency
- 2. Goal and tasks of the research
- 3. The calculation of the elastic movements of the front end of the spindle at different values of the radial component of the cutting force Py in the machining of the holes on the internal grinding machine 3A227П
- Conclusion
- References
Introduction
Obtaining the surfaces of products of the required quality in abrasive machining depends, as a rule, on ensuring the optimal combination of the dynamic state of the machine with technological factors. Often during machining, the instability of the cutting process leads to a deterioration in the quality of machining due to the excitation of unacceptably high levels in the cutting zone. In order to reduce the probability of forming deterministic vibration at the frequencies of natural and forced oscillations, the limitation of cutting conditions is usually used, which undesirably affects the productivity of the process. Improving the dynamic parameters of the machine often provides a shift in the permissible borders of the modes toward their increase. Hence the conclusion about the potential for improving the quality of machining by improving the dynamic state of the machine.
However, the desire to design the most critical components of metal-working equipment with improved dynamic characteristics does not always lead to the desired result. This is due to the ability of the forming machine subsystems to form, when cutting, the dynamic properties different from the expected ones [1].
1. Theme urgency
Grinding is characterized by high speeds of rotation of grinding wheels, as a result of which even a slight imbalance generates significant periodic forces, leading to the occurrence of vibrations. Given the high demands on the accuracy of the surfaces obtained by grinding, the problem of oscillations becomes especially important when working on grinding machines.
Modeling the dynamics of the spindle units of the internal grinding machine will make it possible to establish dependencies reflecting the influence of the dynamic parameters of the spindle units of the internal grinding machine on the microgeometry of ground face.
2. Goal and tasks of the research
The purpose is to study the influence of dynamic parameters of spindle units of internal grinder on microgeometry of ground face.
Main tasks of the research:
- To analyze the structure of spindles units of internal grinding machines and their dynamic characteristics.
- Establish a relationship between the dynamic characteristics of spindle units and the quality of ground face with internal grinding.
- To investigate the influence of dynamic parameters using the compiled mathematical model.
- Analyze the obtained data.
Research object: technological system of internal grinding.
Research subject: influence of dynamic parameters of spindle units of internal grinder on microgeometry of ground face
3. The calculation of the elastic movements of the front end of the spindle at different values of the radial component of the cutting force Py in the machining of the holes on the internal grinding machine 3A227П
The input data for calculating the elastic movements of the spindle end are the design parameters of the spindle unit, which make up the cutting forces on the grinding wheel, and the force at the rear end of the spindle from the prestressing of the belt branches.
When calculating the deformations, the spindle is represented as a beam of a step-variable section on compliant point supports. The elastic movement of the spindle at the cross-section of its front end is determined by assuming that the movements cause only deformations of the spindle body and its supports.
The bearings of the spindle are ball bearings of the 36200 series, located by tandem [2]. We assume that the rigidity of the supports with pre-tension does not depend on the workload on the spindle [3].
In calculating the elastic displacements of the end of the spindle, all the forces acting on it are reduced to two mutually perpendicular planes (Fig. 1).
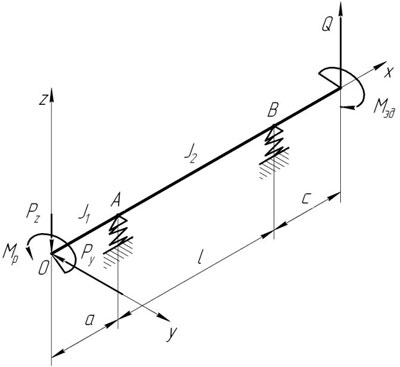
Figure 1. The calculation scheme of the spindle unit of the internal grinding machine 3A227П
The spindle of the grinding head on the grinding wheel side is loaded with the tangential component of the cutting force Pz located in the ZOX plane, by the torque from the cutting force Mc in the plane ZOY, the radial component Py in the plane YOX. On the other side of the spindle, the vertical component of the force from the tension of the belt branches in the ZOX plane and the torque from the electric motor Mem act on it. The moments M c and Mem twist the body of the spindle, but do not affect the elastic movement of the spindle end. In this regard, they can be excluded from the calculation.
The radial displacement of the forward end of the spindle is calculated by the method described in [4]. The tangential component of the cutting force Pz used in the calculation is expressed in terms of the grinding factor Kg:
The initial data for the calculation of the design parameters of the spindle and its supports are selected from the design documentation for the machine (Figure 2) and the reference literature.
Initial data on the mechanical characteristics of the spindle material, the power factors of the machining process and the modes of internal grinding on the machine model 3А227P:
- modulus of elasticity of spindle material (steel 40X) Ε = 2·105 MPa;
- pinch factor in front support ε = 0,15 [5];
- Poisson's ratio μ = 0,28;
- prestressing force of a belt drive branches Рpb = 80 N, sufficient for machining with power 1 kw;
- cutting speed Vw = 26 m/s;
- coefficient of grinding during machining of blanks from alloyed steels Cg = 0,30;
- radial component of cutting force Pу: 20, 40, 60, 80, 100 N.
The results of calculating the elastic displacement of the forward end of the spindle for different values of the radial component of the cutting force Py are given in Table. 1 and are shown in Fig. 3. For comparison, Fig. 3 also indicate the lines corresponding to 1/3 of the 7th quality class for the size of the minimum hole (line 1) machined on the machine 3A227П and 1/3 of the 7th quality class for the size of the maximum machined holes (line 2).
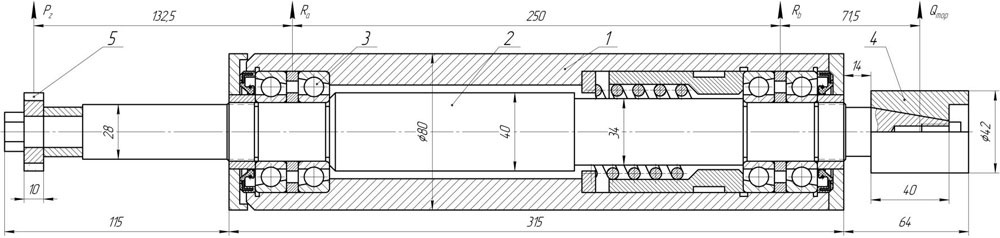
Figure 2. Design parameters of the spindle head of the internal grinding machine 3A227П [2] 1 – body; 2 – spindle; 3 – complex bearing units of 36206K series, located in tandem; 4 – pulley at the rear end of the grinding head spindle; 5 – grinding wheel 1А1 40×10×16×3
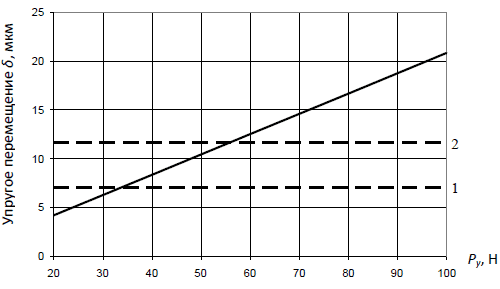
Figure 3. Influence of the radial component of the cutting force on the elastic movements of the front end of the spindle of the grinding machine 3A227П
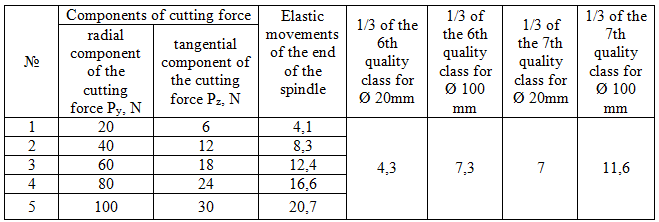
Table 1. Elastic movements of the front end of the spindle of the internal grinding machine 3A227П for different values of the radial component of the cutting force
According to the obtained data, the permissible radial component of the cutting force Py during the machining of the hole Ø 20mm with the 7th quality class is 33 N, and when machining the hole Ø 100 mm with the 7th quality class – 56 N. At the same time, when machining the hole Ø 20 mm with a tolerance of 6th quality class, the cutting force Py should not exceed 22 N, and when machining the hole Ø 100 mm with the approval of the 6th quality class – 30 N, which causes significant technological difficulties in grinding holes with accuracy above the 7th quality class.
Conclusion
It is planned that during the implementation of my master's work, the dependencies of influence of dynamic parameters of spindle units of internal grinder on microgeometry of ground face will be established.
When writing this essay, the master's work is not yet complete. Final completion: July 2018. The full text of the work and materials on the topic can be obtained from the author or his supervisor after the specified date.
References
- Бржозовский, Б.М. Обеспечение качества обработки шлифованием на основе синтеза оптимальных динамических свойств станка / Б.М. Бржозовский, М.Б. Бровкова, И.Н. Янкин // Известия Волгоградского государственного технического ун-та. – 2006. – № 2. – С. 20-22.
- Внутришлифовальные станки моделей 3А227, 3А227В, 3А227П: Руководство по эксплуатации. – Саратов: ЦБТИ, 1967. – 44 с.
- Кирилин, Ю.В. Расчёт и проектирование шпиндельных узлов металлорежущих станков с опорами качения: Учеб. пособие / Ю. В. Кирилин, А.В. Шестернинов. – Ульяновск: УлГТУ, 1998. – 72 с.
- Матюха П. Г. Визначення сили навантаження шліфувальної головки при внутрішньому шліфуванні за пружною схемою / П. Г. Матюха, В. В. Габітов, А. О. Благодарний // Надёжность инструмента и оптимизация технологических систем: Сб. научных трудов. – Краматорск: ДГМА, вып. 27, 2010. – С. 20-29.
- ГОСТ 831–75. Шариковые радиально-упорные однорядные подшипники. – Москва: Стандартинформ, 2005. – 13с.