Зміст
- Вступ
- 1. Мета і завдання дослідження
- 2. Аналіз конструктивних особливостей систем для швидкої зміни дозуючих і погружних
- 3. Розробка вдосконалений пристрій дозуючих і погружних склянок
- 3.1 Дослідження енергосилових параметрів системи швидкої зміндозуючих і погружних склянок
- 3.2 Напруг в вогнетривких елементах пристрої для швидкої заміни склянок - дозаторівковшів мнлз
- Висновки
- Перелік посилань
Вступ
Сучасне металургійне виробництво вимагає постійного підвищення ефективності систем для швидкої зміни дозуючих і заглибних склянок в процесі безперервного розливання довгими і понад-довгими серіями на МБЛЗ. Основними вимогами до таких систем є: надійність роботи в умовах тривалого впливу високих температур; здатність конструкції протистояти значним навантаженням, при виконанні технологічних операцій; простота в обслуговуванні і експлуатації.
1. Мета і завдання дослідження
Метою даного дослідження є розробка та обґрунтування конструктивних і енергосилових параметрів системи швидкої зміни дозуючих і заглибних склянок, при функціонуванні якої виключався б важка фізична праця обслуговуючого персоналу МБЛЗ, скорочувався час проведеної технологічної операції, мінімізувалися енергетичні витрати на її виконання і раціонально використовувалося, вільне місце на робочому майданчику.Для досягнення поставленої мети необхідно вирішити такі завдання:
1. На основі порівняльного аналізу існуючих технічних рішень розробити вдосконалену комплексну систему швидкої зміни дозуючих і заглибних вогнетривких склянок.
2.Розробити методику розрахунку кінематичних і енергосилових параметрів запропонованої системи
3. Провести перевірку правильності прийнятих технічних рішень і отриманих розрахункових залежностей на фізичному аналогу запропонованої системи.
4. Видати рекомендації для промислового використання запропонований-ної розробки
5. Виконати оцінку техніко-економічної ефективності раз-працюємо технічних рішень.
2. Аналіз конструктивних особливостей систем для швидкої зміни дозуючих і погружних
Найбільш широко використовуваними на металургійних підприємствах є пристрої фірм: INTERSTOP, VESUVIUS і IFGL, конструктивні схеми яких показані на мал. 1 – 3.
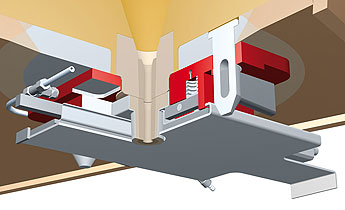
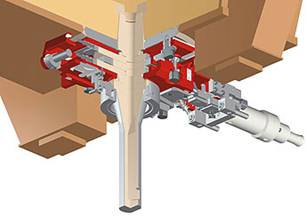
Малюнок 1. Система компанії INTERSTOP
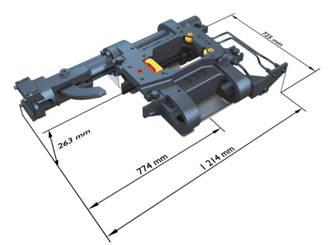
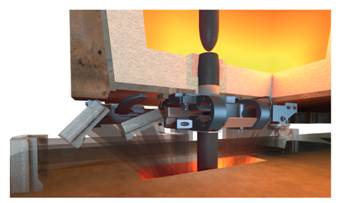
Малюнок 2. Система компанії VESUVIUS
Одними з головних недоліків в зазначених системах є складність конструктивних рішень при розробці і обслуговуванні вузла притиснення склянки-дозатора до верхнього базовому вогнетривкому блоку. Конструкція вимагає ретельного підбору всіх встановлюваних пружин для забезпечення однакових пружних характеристик, а також проведення їх регулярного контролю.
Аналіз можливості виконання операцій з налаштування та обслуговуванні, що у систем, розроблених фірмами INTERSTOP і VESUVIUS (рис.1, рис. 2), здійснення контролю сили пружності, що розвивається кожної пружиною, і її заміна при виході з ладу можливі тільки після зняття всього пристрою з ковша і повного його розбирання на стенді в майстерні.
Система, запропонована фірмою IFGL (рис.3), дозволяє виконати контроль пружних характеристик пружин безпосередньо на ковші, одна-ко для їх заміни потрібне часткове розбирання вузла притиснення змінного вогнетривкого елемента.
Досвід експлуатації таких пристроїв показав, що показники ефек-тивності їх застосування істотно відрізняються. Головною причиною це-го є відсутність в технічній літературі методик для розрахунків і оптимізації робочих параметрів розливних систем даного класу, що в свою чергу призводить до руйнування змінного дозуючого елемента.
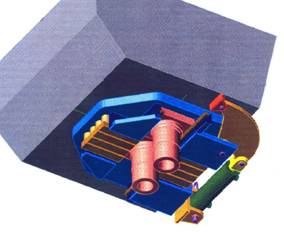
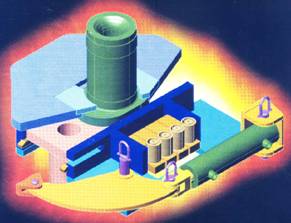
Малюнок 3 – Система компанії IFGL
3. Розробка вдосконалений пристрій дозуючих і погружних склянок
В результаті аналізу переваг та недоліків існуючих вуст-влаштування, а також на підставі результатів лабораторних досліджень та математичного моделювання напружено-деформованого стану елементів конструкції співробітниками кафедри «Механічне обладнання заводів чорної металургії імені професора Седуш В.Я.» ДонНТУ була запропонована нова конструкція пристрою для швидкої заміни склянок-дозаторів рис.4 [1].Пристрій складається з металевого корпусу 3, який гвинтами 4 кріпиться до зовнішньої поверхні днища проміжного ковша 2.У корпусі 3 розміщений вогнетривкий гніздовий блок зі сталевою пускною склянкою 1 проміжного ковша. У корпусі 3 розміщений змінний вогнетривкий склянку-дозатор 12, який має можливість переміщення знімним силовим гідроциліндром 5. Притиснення склянки-дозатора до гніздового блоку здійснюється механізмом, що включає поворотні елементи 11, встановлені на осях 10 по обидва боки склянки-дозатора 12. Для передачі сили притиснення до склянки-дозатора 12 поворотні елементи 11 кінематично пов'язані між собою з пружинами 8, розміщеними на напрямних стрижнях 9 в горизонтальних циліндричних каналах, виконаних в металевому корпусі блоку 6.
На внутрішніх поверхнях цих каналів нарізана різьба для вгвинчування пробок 7. Для обертання пробки вона виходить назовні торцевой частини передбачений або шліц під викрутку, або головка під ключ.
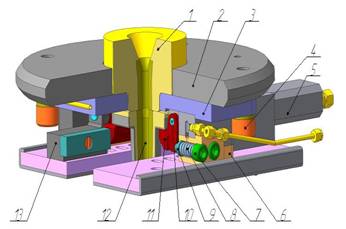
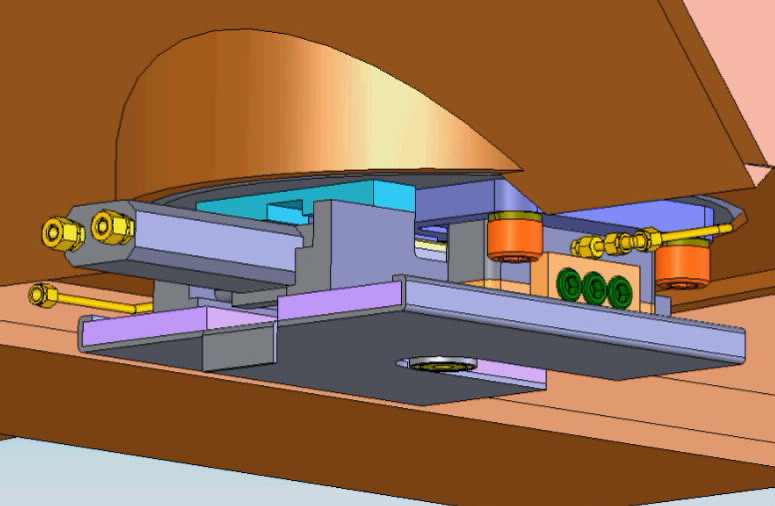
Малюнок 4 – Система ДонНТУ
Під час дозованого переливу сталі з проміжного ковша в кристалізатори МНЛЗ при необхідності заміни вийшов з ладу склянки-дозатора резервним, здійснюють запуск гідроприводу, силовий циліндр якого проштовхує дозуючі елементи на розрахункове рас-стояння, в результаті чого нове вогнетривке виріб займає місце відпрацьованого. Завдяки удосконаленню конструкції опорного вузла розливної системи, відпала необхідність в її повному розбиранні при здійсненні контролю сили, що розвивається кожної з пружин, або в разі їх заміни. Крім цього, вдалося розширити допустимі межі відхилення жорсткості пружних елементів від заданого значення, оскільки запропонована конструкція дозволяє виконувати індивідуальне регулювання сили впливу пружини на дозуючий стакан, не знімаючи розливний пристрій з ковша.
При обслуговуванні розливної системи для контролю жорсткості пружин в отвір кожного з поворотних елементів по черзі вводять хвостовикдинамометричного ключа і, повертаючи елемент на осі на невеликий кут, визначають забезпечується пружиною пружну силу як показано на рис. 5. У разі відхилення цієї сили від заданого значення, необхідно повернути в потрібному напрямку пробку, стискаючи або послаблюючи пружину. Якщо після такої регулювання все ж не вдається досягти бажаного результату, який прийшов став непридатним пружину заміняють нової, вигвинтивши повністю з нарізного гнізда пробку [2].
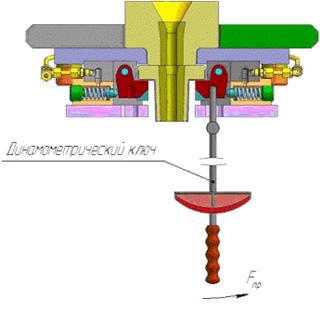
Малюнок 5 – Схема контролю пружної сили, що розвивається пружиною вузлапритиснення склянки-дозатора
3.1 Дослідження енергосилових параметрів системи швидкої зміндозуючих і погружних склянок
Дані пристрої в конструктивному виконанні ідентичні двохплитних змінним затвору, однак використання для розрахунку силових характеристик їх приводів залежностей, отриманих для затворів шиберного типу [3], не представляється можливим, тому що швидкісні режими роботи згаданих розливних систем практично непорівнянні. При однаковому робочому ході рухливих частин у обох систем, що становить 120-130 мм, тривалості їх переміщення з одного крайнього положення в інше відрізняються на порядок, так як плита затвора здійснює повний хід за 3-7 с, а стакан-дозатор - за 0, 3 - 0,5 с.
Різке наростання швидкості руху відпрацьованого і резервного склянок-дозаторів в початковій стадії процесу їх зміни, що забезпечується гідравлічним приводом, тягне за собою розвиток динамічних навантажень, що діють на елементи конструкції розливного пристрою. Встановлення та облік характеру зміни статичних і інерційних сил, який може здолати приводом, дозволить обгрунтувати і оптимізувати значення його енергосилових параметрів, що в кінцевому підсумку сприятиме підвищенню надійності та економічності всієї рухової системи, а також розвитку теоретичних основ її розрахунку [4]. Досягти поставленої мети можна лише, грунтуючись на відомих методах вирішення завдань динаміки приводу гідромеханічних систем, що застосовуються в металургії [5, 6], і доповнивши їх новими положеннями, розробленими з урахуванням специфіки функціонування пристроїв дозованого переливу сталі з проміжних ковшів МБЛЗ. З огляду на екстремальні умови експлуатації сталеразливочного обладнання і пов'язані з ними труднощі використання контрольно-вимірювальних засобів для отримання даних про силове навантаженні натурного зразка під час виконання операції із заміни вийшов з ладу вогнетривкого елемента, необхідну інформацію про значення і характер наростання сил технологічного опору встановили за результатами поставлених спеціальних експериментальних досліджень. Для їх проведення спроектували і виготовили фізичний аналог системи швидкої зміни склянки-дозатора проміжного ковша сортової МБЛЗ (рис. 6), який в конструктивному відношенні і за масштабом в точності відповідав реальному зразком і відрізнявся лише способом забезпечення сили притиснення змінного вогнетривкого елемента. Контрольовану силу віз-дії на опорну поверхню його металевої обойми розвивали за допомогою набору вантажів, що навішуються на два важелі. За рахунок зміни маси вантажів і довжини важелів досягали суворої фіксації в широкому діапазоні значень сили притиснення склянки-дозатора, що дозволяло підвищити точність проведених вимірювань.
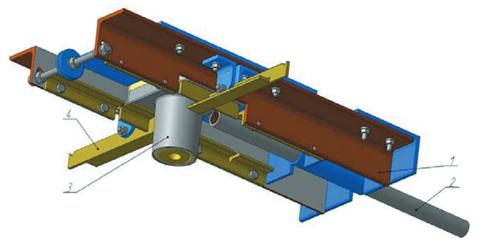
Малюнок 6 – Фізичний аналог промислового пристрою для швидкоїзаміни склянок-дозаторів
3.2 Напруг в вогнетривких елементах пристрої для швидкої заміни склянок - дозаторівковшів мнлз
Найбільш термічно навантаженим елементом конструкції являє¬ся стакан-дозатор, тому на першому етапі досліджень було прийнято рішення розглянути розподіл температур в ньому. Стакан-дозатор являє собою елемент, що складається з металевого кожуха, середовищ-ній вогнетривкої частини і цирконієвої вставки, матеріали яких мають різні теплофізичні властивості. З огляду на тривалість процесу розливки довгою серією, в ході моделювання розглядалася стаціонарна завдання теплопровідності. При цьому температурне поле склянки описується рівнянням теплопровідності:
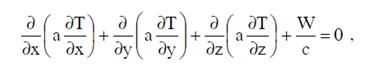
де а - коефіцієнт температуропровідності, що відображає теплоінерційну властивість в даній точці склянки-дозатора; а = ? / с;
с, л - об'ємна теплоємність і коефіцієнт теплопровідності матеріалів склянки;
Т - температура в даній точці склянки-дозатора;
х, у, г - координати розглянутої точки;
W - потужність джерела тепла.
Температурний вплив на склянку виявляється струменем рідкої сталі, що проходить через канал, а також випромінюванням дзеркала металу, знаходящегося в кристалізаторі. З причини складної просторової конструкції склянки, рішення задачі виконувалося за допомогою прикладного пакету ANSYS, реалізуючого метода кінцевих елементів [7]. Так як стакан-дозатор є осесімметрічним елементом, то для розрахунку була створена геометрична модель, відповідна чверті склянки (рис.7 а). В якості граничних умов використовувалися наступні: на поверхні сталеразливочного каналу - конвективна тепловіддача від рідкої сталі з температурою 1600 ° С (коефіцієнт тепловіддачі 0,27 МВт / (м2 • К) [8]); на нижній поверхні циліндричної частини - тепловіддача випромінюванням з щільністю теплового потоку 20 кВт / м2 [8]; на зовнішній поверхні кожуха склянки - конвективна тепловіддача в навколишнє середовище (Температура повітря прийнята 30 0С). В ході моделювання розглядалися два варіанти (№ »1 і №2) конструкціі склянки-дозатора, що відрізняються висотою борту кожуха. При цьому звичайно-елементні моделі (рис.7 б) складалися з 33775 і 33499 елементів відповідно.
В результаті виконаних розрахунків отримано розподіл температурних полів в конструкції склянки-дозатора (рис.8).Як можна побачити, найбільшу температуру має цирконієва вставка, далі в середній частині відбувається інтенсивне падіння температури. Температура кожуха знаходиться в діапазоні 60 ... 250 ° С.
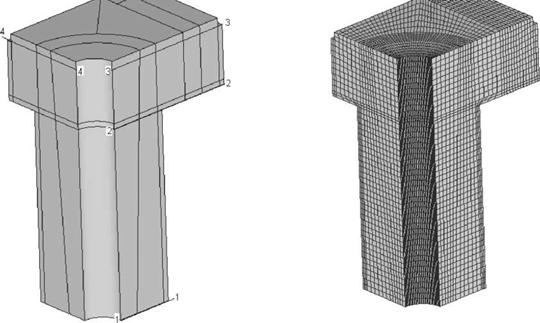
Малюнок 7 – Геометрична модель (а) і кінцево-елементна модель (б) стакана-дозатора (1, 2, 3, 4 характерні перетини)
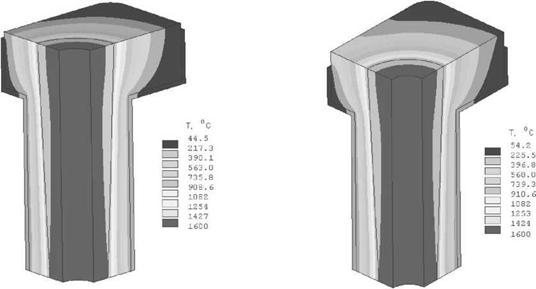
Малюнок 8 – Картини розподілу температурних полів в склянці-дозатор:а) варіант № 1; б) варіант № 2
Графіки зміни температур уздовж окремих перетинів показані на рис.9. Слід зазначити, що в цілому розподіл температурних полів подібно для обох варіантів конструкції склянки, але для варіанта №2 (з коротким бортом кожуха) температура кожуха на 10-17 0С вище.
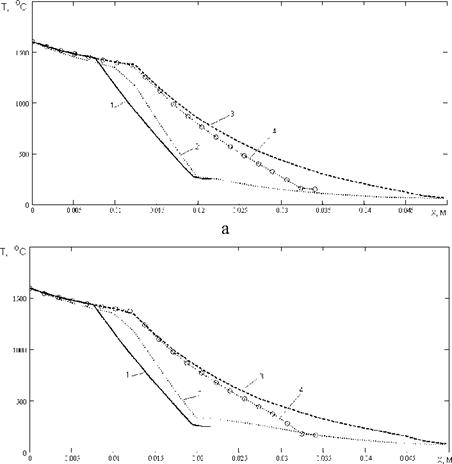
Малюнок 9 – Зміна температури в характерних перетинах склянки дозатора (1, 2, 3, 4 - характерні перетини): а) варіант №1; б) варіант №2
Під дією температурних полів в конструкції склянки-дозатора виникають термічні напруги, які описуються соотвідносинами Дюгамеля-Неймана [9]:
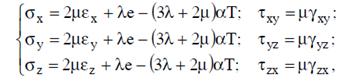
де Єх, Єу, Єz - нормальні напруги вздовж осі х, у z відповідно;
Тху, Туz, Тzх - дотичні напруження;
Ех, Еу, Еz - відносні лінійні деформації по осі х, у z відповідповідно;
Уху, Ууz, Уzх - відносні кутові деформації;
л, у - коефіцієнти Ляме, що залежать від коефіцієнта Пуассона у і модуля пружності Е матеріалів склянки-дозатора:
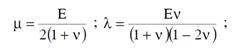
де е - об'ємна деформація: е = Ех + Еу + Еz;
? - коефіцієнт лінійного розширення матеріалів стакана - дозатора;
Т - температура в даній точці конструкції.
Завдання про напружено-деформований стан склянки-дозатора, викликаного температурними впливами, також вирішувалася за допомогою пакета ANSYS. При цьому в якості навантаження використовувалися температури, отримані для кожного вузла кінцево-елементних моделей, а обмежання на переміщення були задані на верхній поверхні склянки-дозатора, що є місцем контакту з базовою вогнетривкою плитою, розміщеної у фланці днища проміжного ковша.
В результаті розрахунку отримано розподіл напружень в тілі склянки-дозатора (рис.10).
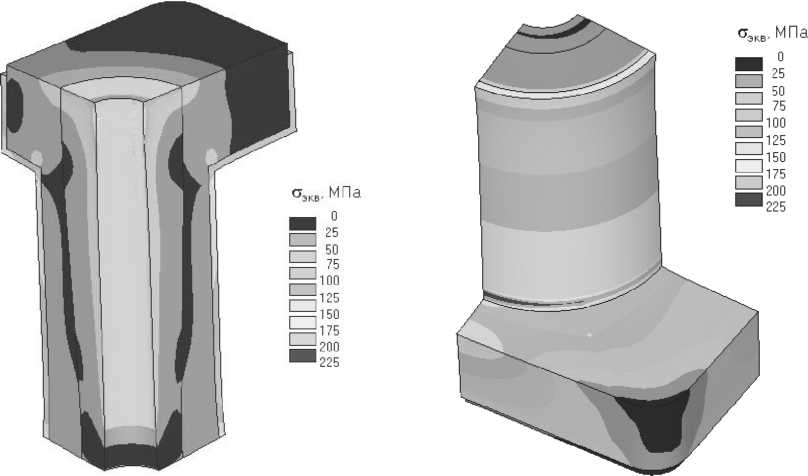
Малюнок 10 – Картини розподілу еквівалентних напруг в склянці-дозатор
Встановлено, що максимальні еквівалентні напруження в вогненаполегливих частинах склянки не перевищують 37 МПа, а в металевому кожусі - 210 МПа, що нижче допустимих значень - 52 МПа і 240 МПа. Для конструкції склянки з коротким бортом (варіант № 2) напруги в це-лом на 5..10% вище. Максимальні напруги виникають на поверхні склянки-дозатора, зверненої до дзеркала металу в кристалізаторі, а також на кожусі в місці з'єднання циліндричної і плоскої частин. Максимальні лінійні деформації в напрямку осей x і у (розширенням конструкції) досягають 1 мм, а в напрямку осі z (подовження конструкції) не перевищують 2 мм. Отримані розрахункові значення деформацій вогнетривкого елемента враховували при призначенні конструктивних розмірів і гарантованих зазорів в опорних і напрямних вузлах механічної системи дослідно-промислового зразка розробленого розливного пристрою [9].
Висновок
- Пат. 74507 Україна, В 22 В 41/56. Пристрій для зміни стаканів-дозаторів проміжного ковша машини безперервного лиття заготовок. Опубл. 15.12.2005. Бюл. № 12.
- Удосконалення конструкції пристрою для швидкої зміни стаканів-дозаторів промковша МБЛЗ / С.П. Еронько, А.Н. Смирнов, Д.А. Яковлєв та ін. // Металургійна та гірничорудна промисловість.- 2006.м №8.- С. 107-109.
- Еронько С. П. Розрахунок енергосилових параметрів ковшових затворів // Металургійна та гірничорудна промисловість. - 2007. - No 3. - С. 104-108.
- Большаков В. І. Дослідження динамічних навантажень металургійних машин // Захист металургійних машин від поломок. Межвузівській тематичний збірник наукових праць. - Маріуполь: ПДТУ, 1999. - С. 6-14.
- Кожевников С. Н., пешат В. Ф. Гідравлічний і пневматичний приводи металургійних машин. - М .: Машинобудування, 1977. - 310 с.
- Свят А. В. Гидропривод в металургії. - М .: Металургія, 1973. - 336 с.
- Каплун А.Б., Морозов Е.М., Олферьева М.А. ANSYS в руках інженера. - М .: Едіторіал УРСС, 2003. - 272 с.
- Огурцов А.П., Жульковская І.І., Кулик А.Д. Розрахунок температурного стану ковшового шиберного затвора при різних способах розливання сталі // Изв. ву¬зов. Чорна металургія. - 2001. - №4. - С.11- 15.
- Пристрій для швидкої заміни склянок-дозаторів проміжного ковша сортової МБЛЗ / С.П. Еронько, О.Н Смирнов, Д.А. Яковлєв та ін. // «Черметінформація». Бюлл. " Чорна металургія". - 2007. - №2 - С. 70-73.
В результаті проведеного аналізу достоїнств і недоліків існуючих систем швидкої зміни стаканів, а також на основі результатів практичних і лабораторних випробувань, розроблений новий варіант системи швидкої зміни стаканів-дозаторів. Застосування запропонованого пристрою дозволить спростити його обслуговування і експлуатацію в порівнянні з відомими зарубіжними аналогами.
При написанні даного реферату магістерська робота ще не завершена. Остаточне завершення: червень 2018 року. Повний текст роботи та матеріали по темі можуть бути отримані у автора або керівника після зазначеної дати.