Реферат
- Вступ
- 1 Актуальность темы
- 2 Цілі і завдання дослідження, плановані результати
- 3 Опис конструкції
- 4 Огляд досліджень по темі
- 5 Основна частина
- Висновок
- Перелік посилань
Вступ
В даний час йде бурхливий розвиток технологій. З'являються все нові і нові можливості для проведення тих чи інших операцій, пов'язаних як з повсякденними справами, так і в області медицини, сільського господарства і металургії. У металургії йде розвитку старих способів роботи з металами, та з'являтися абсолютно нові технології і методи.
Розвиток металургії, тісно пов'язане зі зростаючими потребами людства в металі, він використовується повсюдно: у житлових будівлях, в транспорті, в речах, створених людством для зручності, для досліджень, в космічній промисловості і т.д.
Тільки в 2015 році у всіх країнах світу було випущено близько 1622,80 млн.т. стали. І з кожним роком ця цифра збільшується. Найбільшим виробником сталі є Китай. Його частка продукції, що випускається стали є половиною від всієї продукції створеної на планеті.
1 Актуальність теми
В сучасній металургії основними способами виплавки сталі є киснево-конвертерний, мартенівський і електросталеплавильний.
Електросталеплавильний процес Виплавка сталі в електричних печах має ряд переваг в порівнянні з іншими сталеплавильними процесами. Основні переваги - це можливість створення високої температури в плавильному просторі печі (більше 2000 ° С) і виплавки сталі і сплавів будь-якого складу, використання вапняного шлаку, що сприяє хорошому очищенню металу від шкідливих домішок сірки і фосфору.
Розрахунок довговічності опорного кільця проводиться відповідно до методики фірми Rothe Erde GmbH, викладеної в [2] .Цей підхід є типовим для визначення довговічності опорних кілець, які працюють в тривалому або повторно-короткочасному режимі роботи з повним поворотом. Розрахунковий термін служби виконаний для умов ЕДП-120 і ДСП-50 становить відповідно 5,6 років і 48,2 року. Фактичний ресурс опорних кілець склав 4,2 року для ЕДП-120 і 3,1 року для ДСП-50. Якщо розбіжність в 30% для ЕДП-120 цілком допустимо, то 15-ти кратна помилка для умов ДСП-50 показує, що методика не враховує всіх факторів роботи опорного кільця в складі механізму повороту склепіння, зокрема обмежений кут повороту, значну консольную навантаження і вплив динамічних сил.
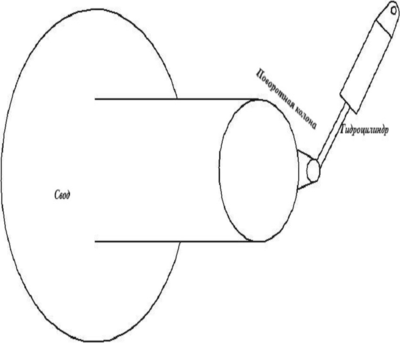
Анімація 1 - Процес повороту колони. (Малюнок анімований. Кількість кадрів 8, size 134kb.)
2 Цілі і завдання дослідження, плановані результати
Метою моєї роботи є розробка алгоритму діагностування опорного кільця підйомно-поворотної колони звіду печі електродуги.
Для цього були поставлені завдання :
- Проаналізувати конструкції електродугової печі
- Виконати аналіз видів і причин несправностей опорного кільця
- Розробити математичну модель навантаження опорного кільця і розрахувати сили діють на опорне кільце
- Провести ряд експеремент на моделі опрно кільця для підтвердження математичної моделі
- Розробити послідовність дій для розпізнавання технічного состояни опорного кільця
3 Опис конструкції
У конструкції механізму повороту склепіння електродугової печі часто використовується опорне кільце [1, 2] на якому встановлюється поворотна колона з приводом за допомогою гідроциліндра (рисунок 1).
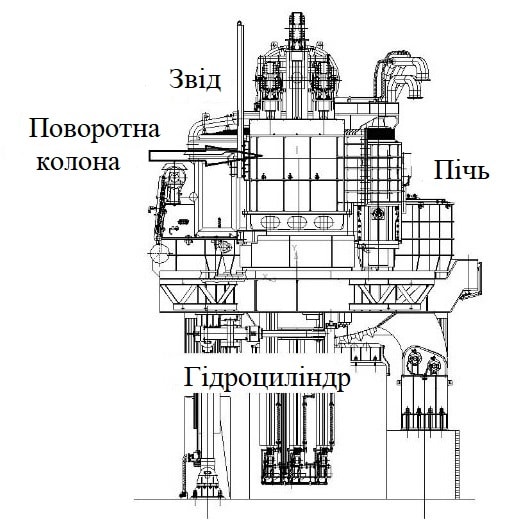
а
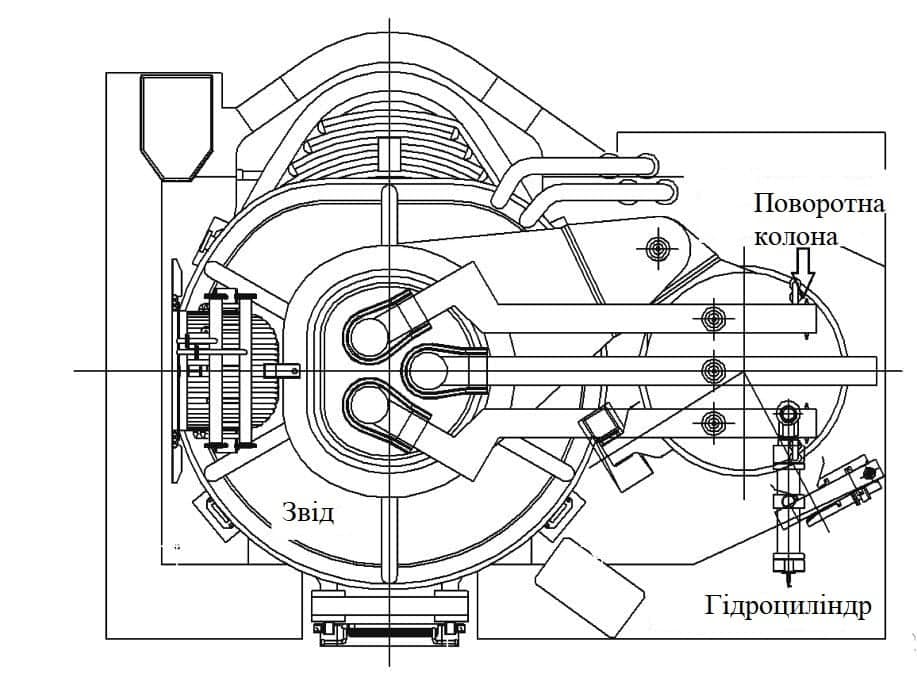
б
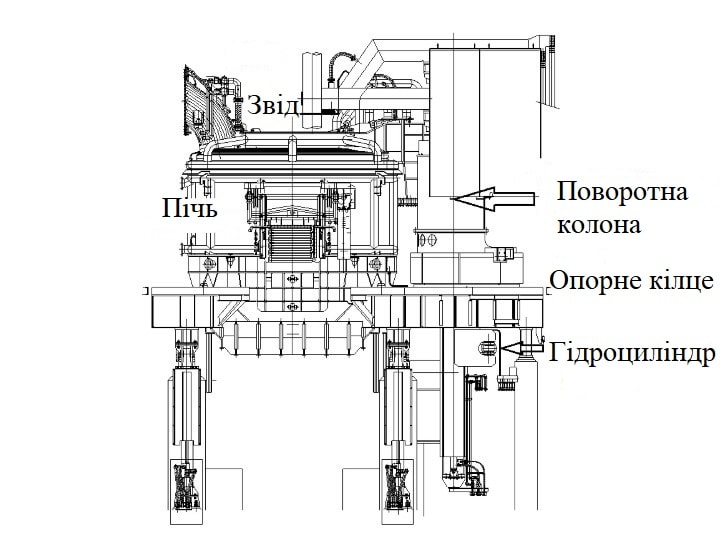
в
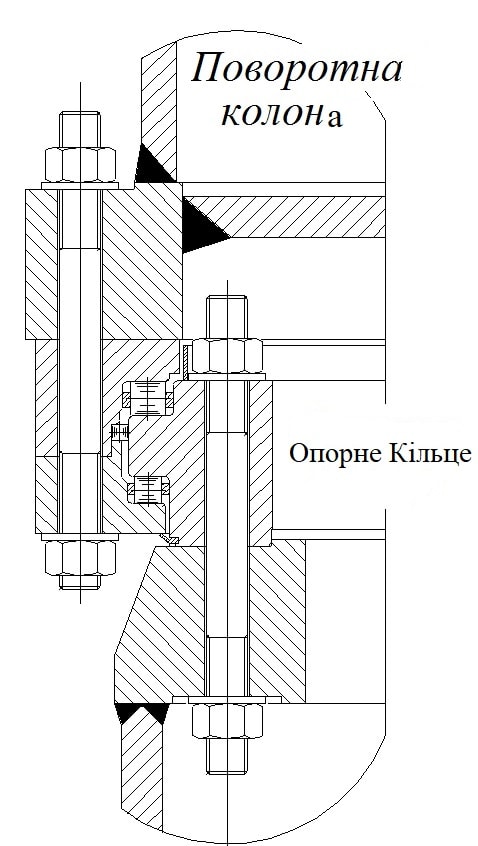
г
Малюнок 1 - Схема розташування механізму повороту склепіння щодо конструкцій електродугової печі: а) вид від газоотвода; б) вид від робочого вікна; в) вид зверху; г) опорне кільце
Поворот зводу на кут 70 ... 90 здійснюється за допомогою гідроциліндра, шток якого кріпиться до важеля поворотної колони (рисунок 1г). Колона, з'єднана зі звіду печі, які мають можливість вертикального переміщення. Для повороту колони на рамі пічної платформи встановлено трехрядное роликопідшипників поворотне кільце (рисунок 1в). Діаметр опорного кільця становить 2,5 ... 3,5 м, висота 150 ... 190 мм. Заміна опорного кільця призводить до тривалої зупинки сталеплавильного комплексу: зазвичай стан погіршується раптово, термін виготовлення кільця за індивідуальним замовленням складає 3 ... 4 місяці, тривалість зміни становить 3 ... 5 діб через необхідність демонтажу і установки поворотної колони і всіх розташованих в ній механізмів.
4 Огляд досліджень по темі
Найбільш ефективним і перспективним методом отримання стали в даний час є виплавка в електродугової печі. Розвиток механічного обладнання електродугових печей призвело практично до повної відмови від електромеханічного приводу. У сучасних конструкціях печей переважає гідравлічний привід, до переваг якого слід віднести реалізацію поступального руху, малі швидкості пересування, мінімізацію динамічних процесів, створення значних сил при малих габаритах, можливість безступінчатого регулювання швидкості руху. Дані переваги гідроприводу дозволяють найбільш повно використовувати їх в механізмах: підйому і повороту склепіння, нахилу печі, переміщення електродів. Одночасно з цим виникає завдання вивчення експлуатаційних властивостей гідроприводу в специфічних умовах металургійного виробництва. У статті виконано аналіз характерних ушкоджень механізмів 120-Тітона електродугової печі з гідравлічним приводом для визначення напрямків підвищення безвідмовності даного класу обладнання.
Основні технічні характеристики механізму повороту склепіння 120-Тітона електродугової печі: кут повороту склепіння - 95 °; швидкість повороту склепіння - 5 ° / с; маса зводу - 50 т. Для повороту колони зі звіду на рамі пічної платформи встановлено трирядне роликопідшипників опорне кільце (рисунок 1) - опорний підшипник. Звід печі з'єднаний з колоною і має можливість вертикального переміщення. На поворотній колоні встановлені також механізм переміщення електродів і механізм переміщення зводу.
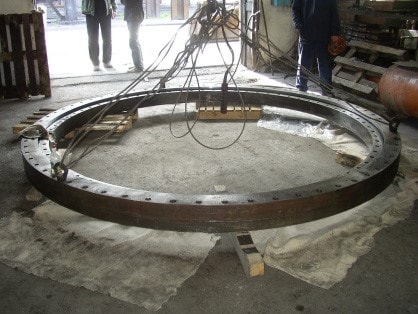
а
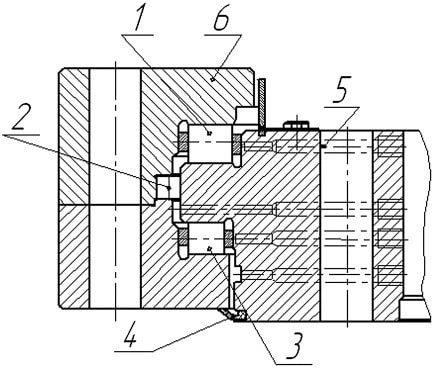
б
Малюнок 1 - трьохрядний роликопідшипників поворотне кільце розливного крана а) загальний вигляд; б) конструкція: 1 - опорні ролики; 2 - радіальні ролики; 3 - контропорние ролики; 4 - ущільнення; 5 - нерухоме кільце; 6 - рухливе кільце.
Подальший візуальний огляд опорного підшипника вказав на абразивний знос елементів верхнього ряду роликів, при цьому знос радіальних і контропорних роликів був відсутній. На поверхні опорних роликів зафіксована плівка продуктів коксування мастильного матеріалу (рисунок 3).
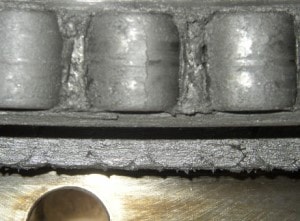
Малюнок 3 - Плівка продуктів коксування мастильними матеріалу
Зроблено висновок, що зношування опорних роликів викликано окисленням (коксуванням) мастильного матеріалу і накопиченням продуктів зносу в застійної зоні верхнього ряду роликів. Це призвело до прискореного зносу опорних роликів і їх бігових доріжок і нерівномірного розподілу сил між тілами кочення, яке викликало перекіс роликів, припинення перекочування тіл кочення, деформацію роликів верхнього ряду і пошкодження сепаратора (рисунок 4).
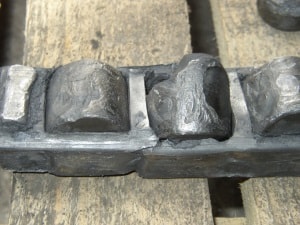
Рисунок 4 — Повреждения сепаратора и деформация роликов
Аналіз тиску в порожнинах гідроциліндра здійснювався на підставі графіків параметрів руху зводу, що надаються системою автоматизованого управління. Для контролю за зміною тиску обрано такі ділянки руху: початок руху зводу при відкритті; усталений рух зводу при відкритті; початок руху зводу при закритті; усталений рух зводу при закритті. Контроль здійснювався щодня при виборі випадкової реалізації одного циклу відкриття і закриття зводу протягом однієї доби. На малюнку 5 наведено типові графіки параметрів руху зводу. Розгляд поданих кривих дозволяє виділити ряд характерних тенденцій зміни параметрів.
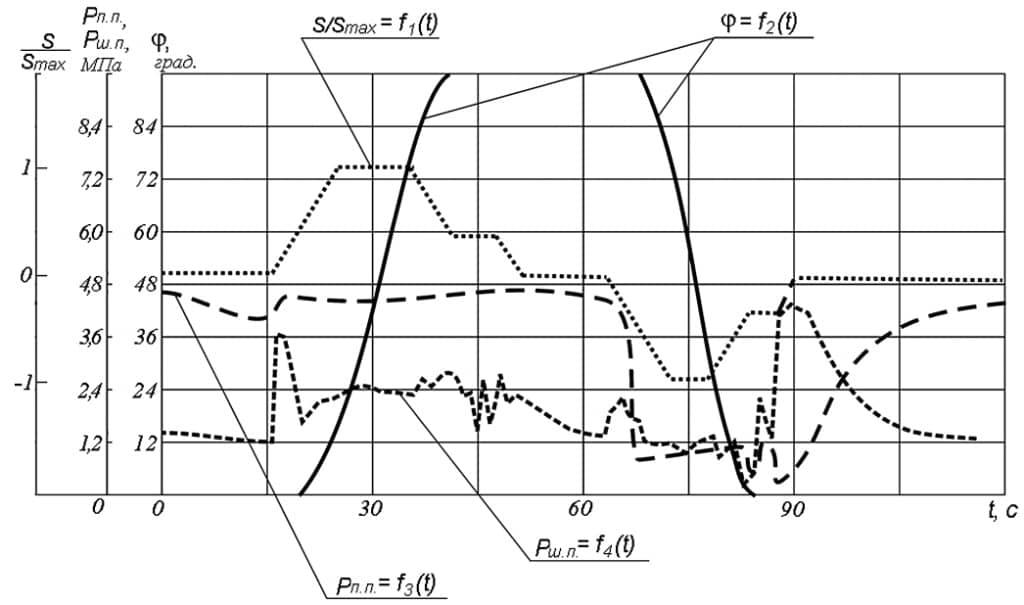
Малюнок 5 типові графіки параметрів руху зводу
Початок руху зводу при відкритті супроводжується підвищенням тиску в штоковой порожнини з подальшим зниженням тиску при початку руху. Це дозволяє оцінити співвідношення між коефіцієнтом тертя спокою і коефіцієнтом тертя руху в опорному підшипниковому кільці. В середньому ці коефіцієнти відрізняються в два рази. Розгляд зміни тиску в поршневий порожнини вказує на те, що при закритті зводу таке явище не спостерігається. Це може бути пов'язано з малим часом зупинки при відкритті зводу і відсутністю впливу вібраційних коливань від палаючої дуги. При зупинці зводу у відкритому положенні спостерігаються динамічні коливання, пов'язані з піддатливістю елементів кріплення.
Проведені вимірювання тиску в жовтні 2008 року і в січні 2009 року дозволили встановити, що тиск в штоковой порожнини для точки початку руху зводу збільшилася від 5,5 до 6,3 МПа, а для усталеного руху від 2,4 до 3,2 МПа; тиск в поршневий порожнини також збільшилася від 8,0 до 9,5 МПа при сталому русі зводу.
Виходячи з цих даних, розраховані сила при відкриванні склепіння печі - 159,5 ... 182,7 кН (при страгивании) і 70,2 ... 91,6 кН (при сталому русі); сила при закритті зводу - 392,0 ... 465,5 кН. Таким чином, збільшення тиску за період жовтень 2008 року - січень 2009 року склало 14 ... 18%. У той же час сила, необхідна при закритті в 2,5 рази більше сили при відкриванні зводу, що може бути наслідком відхилення від вертикальності поворотної колони і рами підстави. Припущення про відхилення від вертикальності осі поворотної колони підтвердилося після аналізу результатів геодезичної зйомки.
Значення коефіцієнта опору , розрахованого виходячи з отриманих даних, перевищує прийняте при розрахунках значення
більше ніж в 10 разів. Це дозволило стверджувати, що в підшипниковому вузлі відбулися незворотні зміни, а технічний стан його елементів відхилилося від нормального (перейшло в іншу категорію).
На підставі даних фактів в травні 2009 року і була проведена планова заміна опорного кільця, яка підтвердила правильність прийнятої методики контролю його технічного стану. Наступне 10-тикратному збільшення коефіцієнта і, відповідно, моменту опору могли свідчити про аварійний стан підшипникового кільця.[7]
5 Основна частина
Вихідними даними є сумарна вертикальна навантаження Fa і сумарний перекидаючий момент Мk (рисунок 6а). Виходячи з емпіричного графіка допустимих значень навантаження для базових 30000 циклів (рисунок 6б) визначається коефіцієнт навантаження підшипника fL для вертикального навантаження Fa і перекидаючого моменту Мk:
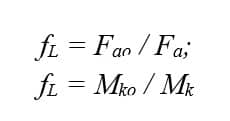
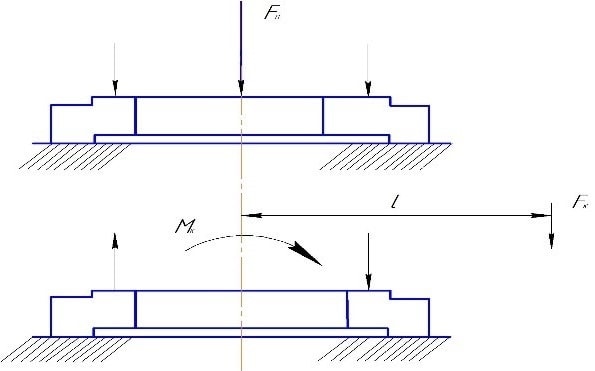
Малюнок 6а
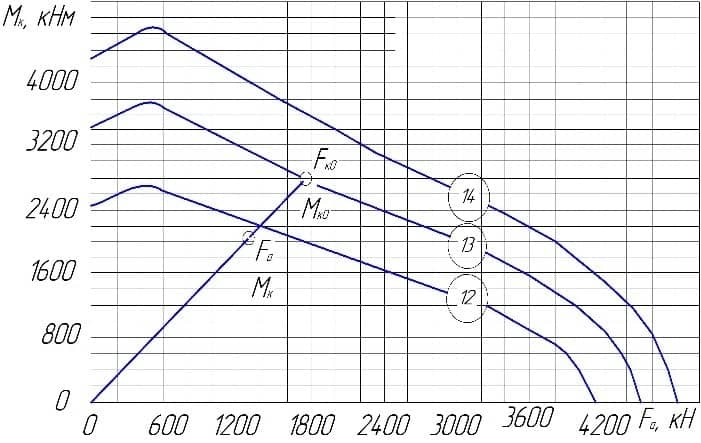
Малюнок 6б
Малюнок 6 - Схема до визначення коефіцієнта навантаження опорного кільця з умовним позначенням 13: а) розташування діючих сил;б) графік допустимих значень навантаження для різних розмірів опорних кілець з умовними позначеннями - 12, 13, 14
Отримане значення використовувалися для визначення терміну служби опорного кільця, як допустимого числа циклів роботи, що розраховується за формулою:
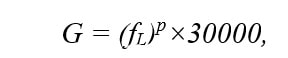
де р = 3 - показник ступеня
Даний підхід є типовим для визначення довговічності опорних кілець, які працюють в тривалому або повторно-короткочасному режимі роботи з повним поворотом. Розрахунковий термін служби виконаний для умов ЕДП-120 і ДСП-50 становить відповідно 5,6 років і 48,2 року. Фактичний ресурс опорних кілець склав 4,2 року для ЕДП-120 і 3,1 року для ДСП-50. Якщо розбіжність в 30% для ЕДП-120 цілком допустимо, то 15-ти кратна помилка для умов ДСП-50 показує, що методика не враховує всіх факторів роботи опорного кільця в складі механізму повороту склепіння, зокрема обмежений кут повороту, значну консольную навантаження і вплив динамічних сил.
Робота опорного кільця пов'язана з впливом консольної навантаження, частими поворотами, одностороннім нагріванням від дугового печі і розжареного зводу, запиленість атмосферою і вібраціями при роботі електричної дуги. Перспективним є розробка методики розрахунку враховує фактичний розподіл навантаження в елементах опорного кільця [3] і експлуатаційні впливу, що знижують довговічність [4]: підвищена температура, вібрація, підвищене тертя і нерівномірний розподіл навантаження між тілами кочення.
Встановлено, що переважаючим в опорному кільці є осповідного викришування і абразивний знос в обмеженому секторі. Послідовність розвитку руйнування пов'язана з порушеннями режиму змащування і в загальному випадку включає:
- окислення мастильними матеріалу під дією температури і порушення руху мастильними матеріалу;
- впливу електричній дуги, особливо в період плавки
- в змішуванні окислення мастильними матеріалу і продуктів зносу, що призводять до прискорення абразивного зносу
Рідке змазування (1 раз в 2 ... 3 діб) і підвищена температура опорного кільця приводять до коксування мастила [6]. Проведені вимірювання температури в районі опорного кільця показали значення 60 ... 800 С, що і призводить до окислення мастила. Контроль температури опорного кільця показав доцільність використання повітряного охолодження опорного кільця в літній період, забезпечуючи зниження температури до 55 ... 600 С.
Відшарувалися частки металу присутні в опорному кільці через осповідного зносу тіл кочення і бігових доріжок виникає при змінних навантаженнях і високому тиску, що перевищують межу витривалості. Накопичення продуктів зносу в мастилі призводить до інтенсивного абразивного зносу. Вторинними ознаками розвитку пошкоджень, що призводять до заклинювання опорного кільця є: пошкодження і руйнування сепаратора, деформація і розворот роликів уздовж бігової доріжки.
Визначення закономірностей розподілу навантажень в елементах опорного кільця проведено на підставі результатів вимірювань значень зносу. Встановлено, що кільця підшипника в секторі 90 ... 1200 не мають слідів зносу. Характер зносу - одноманітний.
Знос верхнього поворотного кільця опорного підшипника розташований симетрично щодо осі зводу. Сектор зносу верхнього поворотного кільця опорного підшипника менше, а глибина зносу більше в порівнянні з нерухомим кільцем. Залежність між зносом і видаленням від найбільш навантаженої зони носить лінійний характер.
Знос верхнього поворотного кільця опорного підшипника більше, ніж знос нерухомого кільця. Верхній ряд опорних роликів переміщався з проскальзиваніем щодо поворотного кільця. Залежність між зносом і видаленням від найбільш навантаженої зони носить лінійний характер і виражається функцією:

де Yв, Yс - знос верхнього і середнього кілець; x - кутова координата.
Переважання абразивного зносу дозволяє використовувати припущення про пропорційність між розподілом сил на тіла кочення і діаграмою розподілу зносу верхнього поворотного кільця, в разі переважання абразивного зносу. Виходячи з даного припущення, проведено розрахунок фактичних напружень в зоні контакту. Отримані значення 1300 ... 1500 МПа в 2,5 ... 3,1 рази менше граничного значення 4000 МПа зазначеного в стандарті [5].
Конкретні значення сектора і глибини зносу різні. Однак, результати розрахунку по визначенню напружень в зоні контакту показали, що максимальні нормальні напруження мали один рівень значень. Отже, статичне навантаження не могла послужити причиною виникнення осповідного викришування.
Вібрація опорного кільця змінюється частотою і формою коливань по режимам роботи. Ці відмінності пов'язані з технологічними періодами роботи електричної дуги. Реалізації по етапах плавки відрізняються зміною амплітудних значень від 1,8 ... 3,0 в режимі доведення до 5,5 ... 14,2
при початку плавки. При роботі електричної дуги зафіксовані значення віброшвидкості 73
в розмаху. Тому, зниження терміну служби опорного кільця в порівнянні з розрахунковим, пов'язано зі збільшеною вібрацією і появою динамічного навантаження. Орієнтовно оцінити значення динамічної складової можна за формулою:

де m - маса поворотної колони
Висновок
Складання алгоритму діагностований опорного кільця підйомно-поворотною колони електродугової печі не завершено, він буде остаточно зроблений в червні 2018 Года.Полний текст роботи та матеріали по її темі можуть бути отримані у автора або його керівника.
Список літератури
- Воскобойников В.Г., Кудрин В.А., Якушев А.М.
Общая металлургия: учебник для вузов
;Воскобойников В.Г., Кудрин В.А., Якушев А.М. - 6-изд., перераб и доп. - МИКЦАкадемкнига
, 2005 - 768 с. - Rothe Erde GmbH. D-44137. Dortmund. 2004. – 172 c.
- Сидоров В.А., Аввакумов С.И., Шепель В.М., Золкин И.Г. Определение характера распределения нагрузок в элементах металлургических машин по износу деталей. Научно-технический и производственный журнал
Металлургическая и горнорудная промышленность
№1, 2006 г. - С. 99 - 102 - Сидоров В.А. Ускоренный износ опорного кольца свода электродуговой печи
Сталь
. 2015 г. № 5. С. 71-75 - ГОСТ 18854-94. Подшипники качения. Статическая грузоподъемность. Введ. с 01.09. 1996. - М.: ИПК Издательство стандартов, 1996. – 18 с.
- RENOLIT CXI 2
- Кожевников С.Н. Гидравлический и пневматический приводы металлургических машин С.Н.Кожевников, В.Ф.Пешат. – Машиностроение, 1973. – 360 с.