Реферат по теме выпускной работы
Содержание
- Введение
- 1. Актуальность темы
- 2. Цель и задачи исследования, планируемые результаты
- 3. Обзор исследований
- Выводы
- Список источников
Введение
Изделия с зубчатыми передачами являются наиболее широко распространенными силовыми механизмами, поскольку зубчатые передачи представляют собой наиболее распространенный вид передач в современном машиностроении. Они очень надежны в работе, обеспечивают постоянство передаточного числа, компактны, имеют высокий КПД, просты в эксплуатации, долговечны и могут передавать любую мощность. Основным рабочим элементом зубчатых колес является зубчатый венец, который работает в сложных эксплуатационных условиях, предусматривающих: высокие изгибные и контактные напряжения, неравномерность распределения нагрузки в зацеплении, кромочный контакт и пр. При этом основные эксплуатационные свойства и параметры качества ЗК формируются на заключительных технологических операциях, среди которых: операции отделочной механической обработки для обеспечения требуемой точности и качества поверхностей; и операции упрочняющей обработки, выполняемые с целью повышения физико-механических свойств основного материала детали или рабочих поверхностных слоев.
Среди требований, определяющих эксплуатационные свойства зубчатых колес, наиболее важными являются требования к износостойкости зубьев и повышению качества рабочих поверхностей с помощью специальных покрытий без ущерба для себестоимости изготовления зубчатых колес.
1. Актуальность темы
В ЗК наиболее трудоемкими в изготовлении и точными являются элементы зубчатого венца, в наибольшей степени определяющие работоспособность и эксплуатационные свойства. Причем требуемые параметры точности, качества поверхности, и физико-механических свойств элементов зубчатого венца формируются на этапах чистовой и отделочной обработки. Поэтому разработка рациональной структуры данных операций, является первостепенной задачей повышения качества ЗК.
Для достижения требуемых физико-механических свойств ЗК, наиболее часто используют методы термической обработки и поверхностно-пластической деформации. Данные методы позволяют обеспечивать свойства для достаточно протяженных участков ЗК, и, как правило, требуют значительного объема последующей механической обработки. При последующей эксплуатации ЗК зачастую наблюдаются некоторые искажения профиля зуба, вызванные неравномерностью износа по высоте зуба. Нанесения специальных покрытий на элементы ЗК, не получили широкого распространения, однако обладают преимуществами, что подтверждается их использованием для других изделий машиностроения [1,2,3,4].
На основании вышеизложенного, данная работа актуальна, и посвящена решению вопросов повышения качества ЗК на основе применения специальных покрытий и методов комбинированной обработки на этапах отделочной обработки зубьев.
2. Цель и задачи исследования.
Цель работы: повышение качества рабочей поверхности ЗК за счет нанесения вакуумных ионно-плазменых покрытий и повышение эффективности отделочной обработки
Основные задачи исследования:
- Выполнить анализ причины износа рабочих поверхностей зубьев.
- Выполнить анализ методов обеспечения физико-механических свойств рабочих поверхностей зубьев.
- Предложить метод повышения производительности процесса нанесения покрытий на рабочие поверхности зубьев.
- Проанализировать кинематическую структуру движения зубчатых колес в вакуумной камере. Предложить наиболее рациональную структуру движения зубчатых колес относительно плазменных потоков.
Предпологаемая новизна
- Установлено, что процесс деления ЗК на функциональные элементы необходимо выполнять в соответствие с выполняемыми эксплуатационными функциями, а свойства данных элементов обеспечивать в зависимости от особенностей эксплуатации.
- Установлено, что обеспечивая изменяющиеся свойства рабочей поверхности зуба, в зависимости от скорости взаимного скольжения профилей, достигается более равномерный износ по высоте зуба, и рациональное использование ресурса ЗК.
Предполагаемая практическая польза
- 1. Разработаны рекомендации, которые позволяют создавать технологическое обеспечение и формировать рациональную структуру технологического процесса отделочной обработки на основе нанесения покрытий, исходя из условий работы ЗК; а также определять требуемые параметры качества поверхностного слоя на этапах подготовки поверхностей к нанесению покрытий.
- Результаты работы внедрены в производство на Снежнянском машиностроительном заводе ОАО
Мотор-Сич
, в Донецком машиностроительном заводе ОДОБуран
, а также в учебном процессе кафедрыТехнология машиностроения
ДонНТУ.
3. Обзор исследований
Зубчатые передачи широко используют в механическом оборудовании для передачи и преобразования параметров вращательного движения. Срок их службы определяет показатели безотказности работы механизма и является одним из критических звеньев дерева отказов. Отказы механического оборудования из-за износа или разрушения зубчатых колес приводят к наиболее длительным простоям и требуют больших затрат для восстановления работоспособности. Предупредить аварийное разрушение зубьев и увеличить срок службы передачи позволяют своевременные ремонтные мероприятия, обоснованные результатами визуального износа.
На работоспособность зубчатых передач влияют как внешние факторы, определяющие передаваемые крутящие моменты и характер вращения зубчатых колес, так и внутренние, зависящие от технического состояния механизма. Взаимодействие внешних и внутренних факторов создает многообразие возможных повреждений зубчатых передач. Несмотря на неизменность в процессе эксплуатации передаточного отношения зубчатой передачи, данные факторы изменяются, приводя к преобладанию определенного вида износа или повреждения. При определении причин повреждения необходимо рассматривать зубчатое колесо как деталь, имеющую посадочную поверхность, несущие элементы и контактную, взаимодействующую поверхность.
На работоспособность зубчатого зацепления влияют такие внешние факторы:
- Значение фактической прилагаемой силовой нагрузки, поскольку расчетная, номинальная нагрузка не приводит к изменению формы зуба и не оставляет значительных следов деформации на рабочей поверхности зубчатой передачи.
- Наличие абразивных частиц, способствующих абразивному износу; или химических веществ вызывающих коррозию поверхностей зубьев, способствующих возникновению газовой или жидкостной эрозии. Основная причина коррозии – наличие воды в смазочном материале – проявляется в виде равномерного или неравномерного слоя ржавчины на поверхности зубьев. Степень коррозии может быть различной.
- Степень взаимного перемещения зубчатого колеса относительно вала. Неподвижность посадочных поверхностей зубчатого колеса и вала удовлетворяет проектным требованиям в том случае, если сопрягаемые детали остаются неподвижными при приложении нагрузки. Появление малых перемещений сопрягаемых деталей приводит к фреттинг-коррозии, проявляющейся в виде темных пятен на посадочной поверхности детали.
- Характер взаимодействия контактирующих поверхностей, которая определяется видом трения на контактирующих поверхностях. Если преобладает жидкостное трение, обеспечивающее минимальный коэффициент трения, и происходит полное разделение контактирующих поверхностей слоем масла, то состояние оценивают как хорошее. В этом случае преобладающим является окислительный износ. Возникновение граничного трения приводит к контакту двух деталей, проявляясь в полировании рабочих поверхностей зубьев. Наиболее часто граничное трение проявляется на начальной стадии приработки новых зубчатых колёс.
Для того чтобы исключить преждевременный выход из строя и продлить время эксплуатации зубчатых колес вводятся различные операции дополнительного упрочнение поверхностных слоев зубьев, направленные на повышение физико-механических свойств рабочих поверхностей зубьев. Это достигается применением методов термической и химико-термической обработки, применением специальных покрытий, применением композиций из нескольких материалов различных свойств в одном изделии. Одним из таких методов является нанесение вакуумных ионно-плазменных покрытия. Такие покрытия получили широкое применение, и позволяют обеспечивать требуемых свойства отдельных элементов детали.
Исходя из особенностей процесса нанесения вакуумных ионно-плазменных покрытий, рассмотренных ранее[10], установлено, что функционально-ориентированный технологический процесс обработки зубьев, повышает физико-механические свойства ЗК.
Этот вид упрочнения ЗК является самым эффективным в данный момент. И для достижения максимальной производительности процесса нанесения покрытий при установившихся технологических параметрах необходимо рационально использовать объём рабочей камеры для нанесения вакуумных ионно-плазменных покрытий.
Реализация условия максимальной технологически допустимой концентрации изделий в рабочей зоне дает возможность одновременно наносить покрытия на все изделия, установленные в камере. В этом случае цикловая производительность вакуумной ионно-плазменной установки
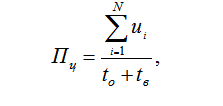
где Пц – цикловая производительность вакуумной ионно-плазменной установки;
to – основное время технологического воздействия при нанесении покрытия;
tв – вспомогательное время, не связанное с технологическим воздействием.
ui – количество изделий каждого типоразмера;
N – общее количество типоразмеров изделий, установленных в камере.
Основное время технологической операции при нанесении покрытия определяется как сумма следующих составляющих:
где to1 – время ионной очистки и термоактивации поверхностей заготовок;
to2 – время конденсации (осаждения) покрытия на поверхность заготовки;
to3 – время охлаждения заготовок.
Вспомогательное время определяется суммой следующих составляющих:
где tв1 – время на установку заготовок в камере;
tв2 – время на закрепление заготовок в рабочих позициях;
tв3 – время на создание вакуума в рабочей камере;
tв4 – время на съем и извлечение заготовок из камеры.
В конструкции установки ННВ6.6-И1 для нанесения покрытий с использованием плазменного напыления предусмотрен вращающийся стол с планетарным механизмом, обеспечивающий вращение заготовок как вокруг своей оси, так и вокруг оси камеры. Для более полного использования рабочего пространства вакуумной камеры предложены различные варианты расположения заготовок деталей типа зубчатое колесо
(рис 1).
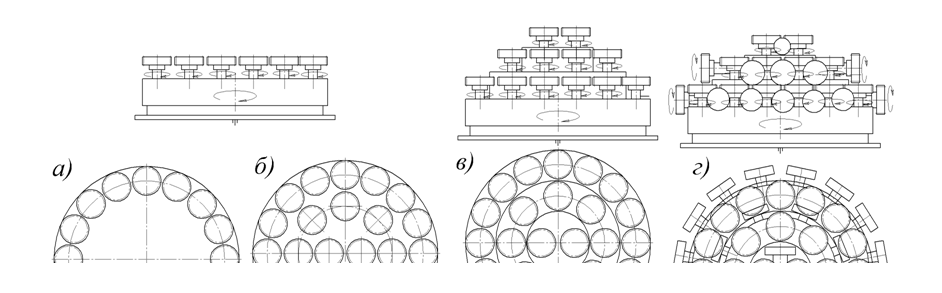
Рисунок 1 – Варианты размещения заготовок в процессе нанесения покрытий[6]
По способу размещения заготовок, планетарный стол может быть следующих вариантов:
- одноуровневое с заполнением заготовок по периферии стола в один ряд (риcунке 1, а),
- одноуровневое многорядное, с размещением заготовок по всей площади окружности стола (рисунке 1, б);
- многоуровневое, с размещением заготовок на каждом уровне, и параллельным вертикальным положением осей вращения заготовок (допуская скрещивание на небольшие углы при сообщении прецессионного качания) (рисунке 1, в);
- многоуровневое, со скрещивающимися осями дополнительных заготовок, расположенных в промежутках между заготовками с вертикальной осью вращения (рисунке 1, г)
При известных технологических параметрах, цикловая производительность установки зависит от количества одновременно обрабатываемых изделий.
При многоуровневом размещении с дополнительными заготовками в промежутках между заготовками с вертикальной осью вращения, общее количество заготовок одного уровня в камере удваивается, а параметром, ограничивающим рабочее пространство камеры, является толщина выступающей заготовки.
На рисунке 2 представлены варианты конструкций вращающегося стола вакуумной камеры, позволяющие реализовать рассмотренные схемы размещения заготовок (рисунка 1).
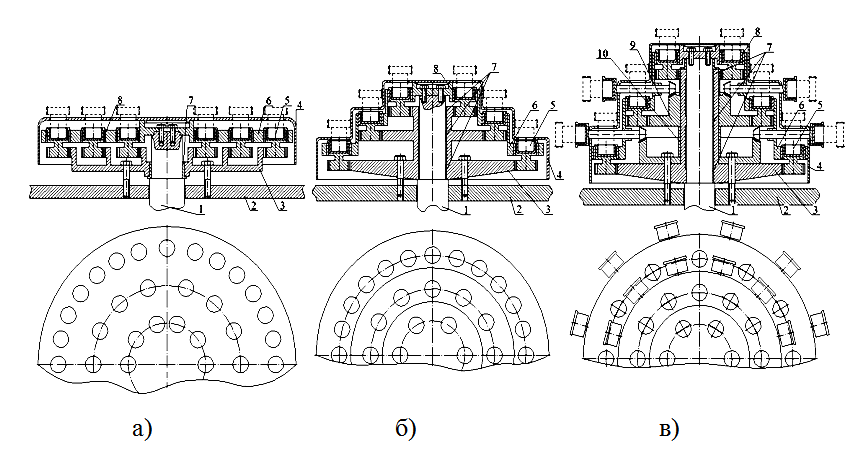
Рисунок 2 – Устройства для размещения заготовок в камере для нанесения покрытий[7]
Устройствах имеются центральные (солнечные) неподвижные колеса 3 и планшайбы 6, выполняющие роль водила планетарной передачи, установленной соосно центральному колесу и вращающиеся от приводного вала 1. Также на планшайбе имеются сателлиты 5, вращающиеся в подшипниках скольжения 8, которые запрессованы в отверстия планшайбы. При этом вращение сателлитов осуществляется от зацепления с неподвижным центральным колесом 3, при вращающейся планшайбе 6. В отверстиях сателлитов устанавливаются заготовки зубчатые колеса, либо приспособления для закрепления заготовок.
В первом устройстве на (рисунке 2, а) заготовки размещаются на одной плоскости в отверстиях сателлитов 5, при этом солнечное колесо 3 является многовенцовым, в котором все зубчатые венцы расположены на одном уровне. Сателлиты установлены в планшайбу 6, соединенную с приводным валом 1. Перемещение заготовок по окружности осуществляется вместе с планшайбой, а их вращение вокруг своих осей - от сателлитов, входящих в зацепление с зубьями неподвижного солнечного колеса 3.
Во втором устройстве (рисункa 2, б) заготовки размещаются на трех уровнях, а солнечное колесо является трехвенцовым зубчатым блоком. Планшайба 6 выполнена в виде пирамиды, на каждой ступени которой расположен ряд сателлитов 5 с заготовками. Также, планшайба вращается от приводного вала 1, а вращение сателлитам передается от зацепления с неподвижными венцами солнечного колеса 3.
В третьем устройстве (рисункa 2, в), имеется два дополнительных ряда заготовок, оси которых перпендикулярны оси планшайбы, и скрещиваются по отношению к осям остальных заготовок. На центральном колесе закреплены два дополнительных зубчатых венца конической передачи, приводящих во вращение заготовки с горизонтальными осями. В планшайбе имеются радиальные отверстия, в которых установлены сателлиты с коническими шестернями.
Рассмотренные варианты конструкций вращающихся столов вакуумной камеры в силу их конструктивных особенностей могут быть использованных в следующих случаях.
Первый вариант конструкции (рисункa 2, а) характеризуется малой высотой стола с заготовками, и может использоваться для вакуумных камер с ограниченной высотой рабочего пространства. Однако ввиду того что заготовки на внутренних окружностях стола находятся в тени от соседних заготовок, ограничивающих поток от боковых катодов, нанесение покрытий на них должно осуществляться от верхних катодов.
Второй вариант (рисункa 2, б) характеризуется большей высотой стола и позволяет располагать большее количество заготовок при равном с первым наибольшими диаметрами столов. Также, заготовки расположенные на внутренних окружностях стола не закрываются заготовками наружных окружностей, поэтому нанесение покрытий для всех заготовок возможно от боковых катодов. Таким образом данный вариант, наряду с возможностью равномерного доступа потока плазмы для всех заготовок, позволяет более рационально использовать рабочее пространство вакуумной камеры. Между тем, поскольку диаметры окружностей расположения заготовок в большей степени зависят от размеров приспособлений для крепления заготовок, данный вариант целесообразно использовать для ЗК большого диаметра.
Третий вариант (рисункa 2, в) позволяет размещать вдвое большее количество заготовок, обеспечивая наибольшую производительность нанесения покрытий. Однако в связи с необходимостью наличия дополнительного пространства для размещения заготовок с горизонтальными осями вращения, а также для предотвращения перекрытия ближайших к ним заготовок, увеличивается высота вращающегося стола. Также, в связи с различным положением осей заготовок, действие потока плазмы по отношению к рабочим элементам ЗК различно. Поэтому данный вариант целесообразно использовать для вакуумных камер с достаточно большой высотой рабочего пространства, а также с наличием катодов, расположенных по периферии и в верхней части вакуумной камеры.
Реализация требуемой кинематической структуры движения изделий в рабочей зоне вакуумной камеры, за счет непрерывной смены положения заготовок, позволяет обеспечить равномерный доступ потока наносимого покрытия ко всему зубчатому венцу, и решить следующие задачи:
- исключить теневые зоны, затрудняющие нанесения покрытий;
- расширить технологические возможности процесса, позволяя наносить специальные виды покрытий (пятнистые и функционально- ориентированные) и с закономерно изменяющейся толщиной.
Толщина покрытия в любой точке изделия зависит от интенсивности плазменного потока и угла между нормалью к поверхности изделия. Заметим, что толщина покрытия на поверхности изделия увеличивается по нормали к каждой точке исходной поверхности изделия, и зависит от угла между нормалью к точке поверхности, и суммарным вектором направления действия потока плазменной струи (рисунок 3). Изменение вектора действия потока, обуславливается особенностями кинематики движения изделия в вакуумной камере.
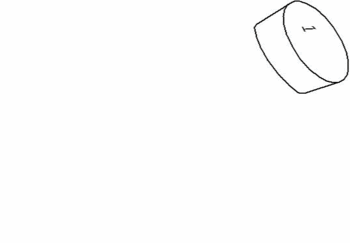
Рисунок 3 – Действие потока плазмы в точках наносимой поверхности
(анимация: 9 кадров, 79 килобайт)
(yk – угол под каким наноситься покрытие, 1 – катод, 2 – нормали к точкам поверхности, h – толщина покрытия, v,u – параметры поверхности изделия)
Выводы
Таким образом в работе выполнен анализ основных эксплуатационных характеристик зубчатых колес. Рассмотрены причины износа зубьев а также рассмотрены способ позволяющий повысить работоспособность ЗК. Также были проанализированы возможные варианты размещения заготовок в вакуумной камере, можно отметить, поскольку количество заготовок размещаемых в камере не зависит от длительности технологического воздействия, основным направлением дальнейшего повышения производительности процесса нанесения покрытий является увеличение количества заготовок в камере, обеспечивая при этом требуемое положение и кинематику движения заготовок относительно плазменных поток.
Список литературы
- Васильев А. Ф. Создание функционально-градиентных износостойких покрытий с регулируемой твердостью методом сверхзвукового холодного газодинамического напыления для изделий машиностроения. / А. Ф. Васильев, Д.А. Геращенков, Б. В. Фармаковский, М. А. Юрков /Сборник трудов XIV международной научно-технической конференции
Машиностроение и техносфера XXI века
. – Донецк: ДонНТУ, 2007. Т.1. – С. 163 – 171. - Внуков Ю.Н., Марков А.А., Лаврова Л.В., Бердышев Н.Ю. Нанесение износостойких покрытий на быстрорежущий инструмент. – Киев, Тэхника, 1992. – 143 с.
- Гончаров М.В. Технология и оборудование получения комплексных покрытий с особыми свойствами. / М.В. Гончаров, В.С. Гончаров // Современные тенденции развития автомобилестроения в России. Труды Всероссийской научно-технической конференции. – Тольятти: ТГУ, 2003. №3. С. 448 – 452.
- Костржицкий А.И., Лебединский О.В. Многокомпонентные вакуумные покрытия. М.: Машиностроение, 1987. – 208 с.
- Михайлов А.Н. Основные принципы и особенности синтеза функционально-ориентированных технологий машиностроения. / А.Н. Михайлов //Сборник трудов XIII международной научно-технической конференции: Машиностроение и техносфера XXI века. В 5-ти томах. – Донецк: ДонНТУ, 2006. Т. 3. С. 61 – 77.
- Михайлов А.Н. Основы синтеза поточно-пространственных технологических систем непрерывного действия. - Донецк: ДонНТУ, 2003. – 379 с.
- Михайлов А.Н. Основы синтеза функционально-ориентированных технологий машиностроения. – Донецк: ДонНТУ, 2008. – 346 с.
- Михайлов А.Н. Общие особенности функционально-ориентированных технологий и принципы ориентации их технологических воздействий и свойств изделий. / А.Н. Михайлов //Сборник трудов XIV международной научно-технической конференции: Машиностроение и техносфера XXI века. В 5-ти томах. – Донецк: ДонНТУ, 2007. Т. 3. С. 38 – 52.
- Технология производства и методы обеспечения качества зубчатых колес и передач. Учеб .пособие / В.Е. Антонюк, А.А. Сусин, С.П. Руденко и др.; под ред. В.Е. Старжинского и М.М. Канне. – Минск: УП
Технопринт
, 2003. – 766 с. - Юдин Д.Л. Пути повышения качества отделочно-упрочняющей обработки зубьев зубчатых колес ППД / Д.Л. Юдин, А.И. Иунихин, М.А. Порхачев, В.А. Фомин // Вестник машиностроения, 1981. – № 3. – С. 49 – 50.