Реферат за темою випускної роботи
Зміст
- Вступ
- 1. Актуальність теми
- 2. Мета і задачі дослідження та заплановані результати
- 3. Огляд досліджень та розробок
- Висновки
- Перелік посилань
Вступ
Вироби з зубчастим зацепленням є найбільш поширеними силовими механізмами, оскільки зубчасті передачі являють собою найпоширеніший вид передач у сучасному машинобудуванні. Вони дуже надійні в роботі, забезпечують постійність передаточного числа, компактні, мають високий ККД, прості в експлуатації, довговічні і можуть передавати будь-яку потужність. Основним робочим елементом зубчастих коліс є зубчастий вінець, який працює в складних експлуатаційних умовах, що передбачають: високі деформаційні і контактні напруги, нерівномірність розподілу навантаження в зачепленні, для обробки країв контакт і пр. При цьому основні експлуатаційні властивості та параметри якості ЗК формуються на заключних технологічних операціях, серед яких: операції опоряджувальної механічної обробки для забезпечення потрібної точності та якості поверхонь; і операції зміцнюючої обробки, що виконуються з метою підвищення фізико-механічних властивостей основного матеріалу деталі або робочих поверхневих шарів.
Серед вимог, що визначають експлуатаційні властивості зубчастих коліс, найбільш важливими є вимоги до зносостійкості зубів і підвищення якості робочих поверхонь за допомогою спеціальних покриттів без шкоди для собівартості виготовлення зубчастих коліс.
1. Актуальність теми
У ЗК найбільш трудомісткими у виготовленні і точними є елементи зубчастого вінця, найбільшою мірою визначають працездатність та експлуатаційні властивості. Причому необхідніпараметри точності, якості поверхні, фізико-механічних властивостей елементів зубчастого вінця формуються на етапах чистового та оздоблювальної обробки. Тому розробка раціональної структури даних операцій, є першочерговим завданням підвищення якості ЗК.
Для досягнення необхідних фізико-механічних властивостей ЗК, найбільш часто використовують методи термічної обробки і поверхнево-пластичної деформації. Дані методи дозволяють забезпечувати властивості для досить протяжних ділянок ЗК, і, як правило, вимагають значного обсягу подальшої механічної обробки. При подальшій експлуатації ЗК найчастіше спостерігаються деякі спотворення профілю зуба, викликані нерівномірністю зношення по висоті зуба. Нанесення спеціальних покриттів на елементи ЗК, не отримали широкого розповсюдження, однак володіють перевагами, що підтверджується їх використанням для інших виробів машинобудування [1-4.].
На підставі вищевикладеного, дана робота є актуальною і присвячена вирішенню питань підвищення якості ЗК на основі застосування спеціальних покриттів і методів комбінованої обробки на етапах оздоблювальної обробки зубів.
2. Мета і задачі дослідження та заплановані результати
Мета роботи: підвищення якості робочої поверхні ЗК за рахунок нанесення вакуумних іонно-плазмових покриттів і підвищення ефективності оздоблювальної обробки
Основні задачі дослідження:
- Виконати аналіз причини зносу робочих поверхонь зубів.
- Виконати аналіз методів забезпечення фізико-механічних властивостей робочих поверхонь зубів.
- Запропонувати метод підвищення продуктивності процесу нанесення покриттів на робочі поверхні зубів.
- Проаналізувати кінематичну структуру руху зубчастих коліс у вакуумній камері. Запропонувати найбільш раціональну структуру руху зубчастих коліс щодо плазмових потоків.
Передбачувана наукова новизна
- Встановлено, що процес ділення ЗК на функціональні елементи необхідно виконувати у відповідність з виконуваними експлуатаційними функціями, а властивості даних елементів забезпечувати в залежності від особливостей експлуатації.
- Встановлено, що забезпечуючи змінюються властивості робочої поверхні зуба, в залежності від швидкості взаємного ковзання профілів, досягається більш рівномірний знос по висоті зуба, і раціональне використання ресурсу ЗК.
Передбачувана практична користь
- Розроблені рекомендації, які дозволяють створювати технологічне забезпечення і формувати раціональну структуру технологічного процесу оздоблювальної обробки на основі нанесення покриттів, виходячи з умов роботи ЗК; а також визначати необхідні параметри якості поверхневого шару на етапах підготовки поверхонь до нанесення покриттів.
- . Результати роботи впроваджені у виробництво на Сніжнянському машинобудівному заводі ВАТ
Мотор-Січ
, у Донецькому машинобудівному заводі ТДВБуран
, а також у навчальному процесі кафедриТехнологія машинобудування
ДонНТУ.
3. Огляд досліджень та розробок
Зубчасті передачі широко використовують в механічному обладнанні для передачі і перетворення параметрів обертального руху. Термін їх служби визначає показники безвідмовності роботи механізму і є одним з критичних ланок дерева відмов. Відмови механічного обладнання із-за зносу або руйнування зубчастих коліс призводять до найбільш тривалих простоїв і вимагають великих витрат для відновлення працездатності. Попередити аварійне руйнування зубів і збільшити термін служби передачі дозволяють своєчасні ремонтні заходи, обґрунтовані результатами візуального зносу.
На працездатність зубчастих передач впливають як зовнішні фактори, що визначають передаються крутні моменти і характер обертання зубчастих коліс, так і внутрішні, що залежать від технічного стану механізму. Взаємодія зовнішніх і внутрішніх факторів створює різноманіття можливих пошкоджень зубчастих передач. Незважаючи на незмінність у процесі експлуатації передавального відношення зубчастої передачі, дані фактори змінюються, приводячи до переважання певного виду зносу чи пошкодження. При визначенні причин пошкодження необхідно розглядати зубчасте колесо як деталь, що має посадочну поверхню, несучі елементи і контактну, що взаємодіє поверхню.
На працездатність зубчастого зачеплення впливають такі зовнішні фактори:
- Значення фактичної додається силового навантаження, оскільки розрахункова, номінальна навантаження не призводить до зміни форми зуба і не залишає значних слідів деформації на робочій поверхні зубчастої передачі.
- Наявність абразивних частинок, що сприяють абразивного зносу; або хімічних речовин, що викликають корозію поверхонь зубів, що сприяють виникненню газової або рідинної ерозії. Основна причина корозії – наявність води в смазочном матеріалі – проявляється у вигляді рівномірного чи нерівномірного шару іржі на поверхні зубів. Ступінь корозії може бути різною.
- Ступінь взаємного переміщення зубчастого колеса відносно вала. Нерухомість посадочних поверхонь зубчастого колеса і вала задовольняє проектним вимогам у тому випадку, якщо сполучаються деталі залишаються нерухомими при додатку навантаження. Поява малих переміщень деталей, що сполучаються призводить до фреттинг-корозії, що виявляється у вигляді темних плям на посадковій поверхні деталі.
- Характер взаємодії контактуючих поверхонь, яка визначається видом тертя на контактуючих поверхнях. Якщо переважає рідинне тертя, що забезпечує мінімальний коефіцієнт тертя, і відбувається повне розділення контактуючих поверхонь шаром масла, то стан оцінюють як добрий. У цьому випадку переважаючим є окислювальний знос. Виникнення граничного тертя призводить до контакту двох деталей, проявляючись у полірування робочих поверхонь зубів. Найбільш часто граничне тертя проявляється на початковій стадії припрацювання нових зубчастих коліс.
Для того щоб виключити передчасний вихід з ладу і продовжити час експлуатації зубчастих коліс вводяться різні операції додаткового зміцнення поверхневих шарів зубів, спрямовані на підвищення фізико-механічних властивостей робочих поверхонь зубів. Це досягається застосуванням методів термічної і хіміко-термічної обробки, застосуванням спеціальних покриттів, застосуванням композицій з декількох матеріалів різних властивостей в одному виробі. Одним з таких методів є нанесення вакуумних іонно-плазмових покриття. Такі покриття отримали широке застосування, і дозволяють забезпечувати необхідних властивостей окремих елементів деталі.
Виходячи з особливостей процесу нанесення вакуумних іонно-плазмових покриттів, розглянутих раніше[10], встановлено, що функціонально-орієнтований технологічний процес обробки зубів, підвищує фізико-механічні властивості ЗК.
Цей вид зміцнення ЗК є самим ефективним в даний момент. І для досягнення максимальної продуктивності процесу нанесення покриттів при сталих технологічних параметрів необхідно раціонально використати об'єм робочої камери для нанесення вакуумних іонно-плазмових покриттів.
Реалізація умови максимальної технологічно допустимої концентрації виробів в робочій зоні дає можливість наносити покриття на всі вироби, встановлені в камері. У цьому випадку циклова продуктивність вакуумної іонно-плазмової установки
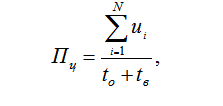
де Пц – циклова продуктивність вакуумної іонно-плазмової установки;
t o – основний час технологічного впливу при нанесенні покриття;
t в – допоміжний час, не пов'язане з технологічним впливом.
u i – кількість виробів кожного типорозміру;
N – загальна кількість типорозмірів виробів, встановлених в камері
Основний час технологічної операції при нанесенні покриття визначається як сума наступних складових:
де to1 – час іонног очищення і термоактивації поверхонь заготовок;
to2 – час конденсації (осадження) покриття на поверхню заготовки;
to3 – час охолодження заготовок.
Допоміжний час визначається сумою наступних складових:
де tв1 – час на установку заготовок в камері;
tв2 – час на закріплення заготовок на робочих позиціях;
tв3 – час на створення вакууму в робочій камері;
tв4 – час на зняття та витяг заготовок з камери.
В конструкції установки ННВ6.6-И1 для нанесення покриттів з використанням плазмового напилення передбачений обертовий стіл з планетарним механізмом, що забезпечує обертання заготовок як навколо своєї осі, так і навколо осі камери. Для більш повного використання робочого простору вакуумної камери запропоновані різні варіанти розташування заготовок деталей типу зубчасте колесо
(мал 1).
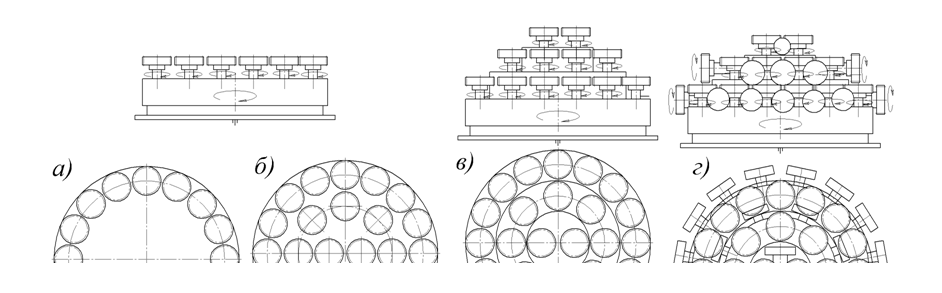
Малюнок 1 – Варіанти розміщення заготовок у процесі нанесення покриттів[6]
По способу розміщення заготівель, планетарний стіл може бути наступних варіантів:
- однорівнева з заповненням заготовок по периферії столу в один ряд (мал. 1,а),
- однорівнева багаторядне, з розміщенням заготівель по всій площі кола столу (мал. 1, б);
- багаторівневе, з розміщенням заготівель на кожному рівні, і паралельним вертикальним положенням осей обертання заготовок (допускаючи схрещування на невеликі кути при повідомленні прецесійного гойдання) (мал. 1, в);
- багаторівневе, з мимобіжними осями додаткових заготовок, розташованих в проміжках між заготівками з вертикальною віссю обертання (мал.1,г).
При відомих технологічних параметрах, циклова продуктивність установки залежить від кількості одночасно оброблюваних виробів.
При багаторівневому розміщення з додатковими заготовками в проміжках між заготівками з вертикальною віссю обертання, загальна кількість заготовок одного рівня в камері подвоюється, а параметром, що обмежує робочий простір камери, є товщина виступаючої заготовки.
На мал.2 представлені варіанти конструкцій обертового стола вакуумної камери, що дозволяють реалізувати розглянуті схеми розміщення заготовок (мал. 1).
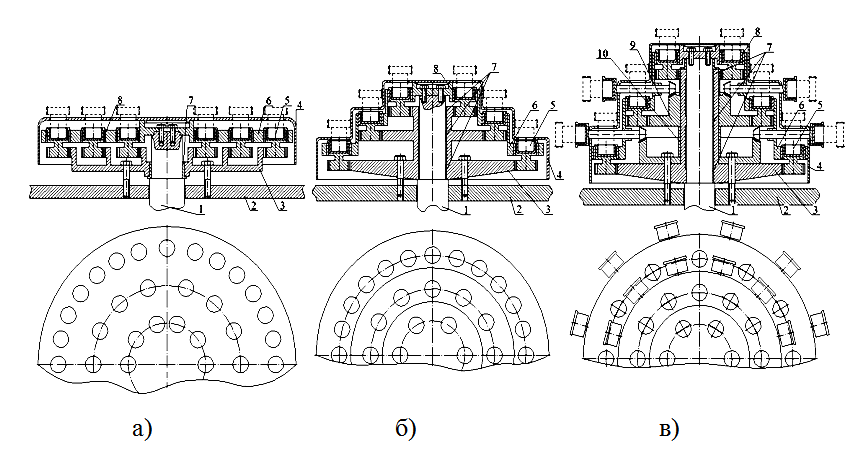
Малюнок 2 – Пристрої для розміщення заготовок в камері для нанесення покриттів[7]
В пристроях є центральні (сонячні) нерухомі колеса 3 і планшайби 6, виконують роль водила планетарної передачі, встановленої співвісно центральному колесу і обертаються від приводного вала 1. Також на планшайбі є сателіти 5, що обертаються в підшипниках ковзання 8, які запресовані в отвори планшайби. При цьому обертання сателітів здійснюється від зачеплення з нерухомим центральним колесом 3, при обертової планшайбі 6. В отворах сателітів встановлюються заготовки (ЗК), або пристосування для закріплення заготовок.
У першому пристрої (мал.2, а) заготовки розміщуються на одній площині в отворах сателітів 5, при цьому сонячне колесо 3 є многовенцовым, в якому всі зубчасті вінці розташовані на одному рівні. Сателіти встановлені в планшайбу 6, з'єднану з приводним валом 1. Переміщення заготовок по колу здійснюється разом з планшайбою, а їх обертання навколо своїх осей - від сателітів, що входять у зачеплення з зубами нерухомого сонячного колеса 3. У другому пристрої (мал. 2, б) заготовки розміщуються на трьох рівнях, а сонячне колесо є трехвенцовым зубчастим блоком. Планшайба 6 виконана у вигляді піраміди, на кожній сходинці якої розташований низку сателітів 5 із заготовками. Також, планшайба обертається від приводного валу 1, а обертання сателітів передається від зачеплення з нерухомими вінцями сонячного колеса 3.
У третьому пристрої (мал. 2, в), є два додаткових ряду заготовок, осі яких перпендикулярні осі планшайби, і схрещуються по відношенню до осей інших заготовок. На центральному колесі закріплені два додаткових зубчастих вінця конічної передачі, що приводять в обертання заготовки з горизонтальними осями. В планшайбі є радіальні отвори, в яких встановлені сателіти з конічними шестернями.
Розглянуті варіанти конструкцій обертових столів вакуумної камери в силу їх конструктивних особливостей можуть бути використані в наступних випадках. Перший варіант конструкції (мал. 2, а) характеризується малою висотою столу з заготовками, і може використовуватися для вакуумних камер з обмеженою висотою робочого простору. Однак зважаючи на те що заготовки на внутрішніх окружностях столу знаходяться в тіні від сусідніх заготовок, що обмежують потік від бічних катодів, нанесення покриттів на них повинно здійснюватися від верхніх катодів.
Другий варіант (мал. 2, б) характеризується більшою висотою столу і дозволяє розташовувати більшу кількість заготовок при рівному з першим найбільшими діаметрами столів. Також, заготівлі розташовані на внутрішніх окружностях столу не закриваються заготовками зовнішніх кіл, тому нанесення покриттів для всіх заготовок можливо від бічних катодів. Таким чином даний варіант, поряд з можливістю рівномірного доступу потоку плазми для всіх заготовок, дозволяє більш раціонально використовувати робочий простір вакуумної камери. Між тим, оскільки діаметри кіл розташування заготовок більшою мірою залежать від розмірів пристосувань для кріплення заготовок, даний варіант доцільно використовувати для ЗК великого діаметру.
Третій варіант (мал. 2,в) дозволяє розміщувати вдвічі більшу кількість заготовок, забезпечуючи найбільшу продуктивність нанесення покриттів. Однак у зв'язку з необхідністю наявності додаткового простору для розміщення заготовок з горизонтальними осями обертання, а також для запобігання перекриття найближчих до них заготовок, збільшується висота обертового стола. Також, у зв'язку з різним положенням осей заготовок, дія потоку плазми по відношенню до робочих елементів ЗК різному. Тому цей варіант доцільно використовувати для вакуумних камер з досить великою висотою робочого простору, а також з наявністю катодів, розташованих по периферії і у верхній частині вакуумної камери.
Реалізація необхідної кінематичної структури руху виробів у робочій зоні вакуумної камери, за рахунок безперервної зміни положення заготовок, що дозволяє забезпечити рівномірний доступ потоку наносимого покриття до всього зубчастому вінцю, і вирішити наступні завдання:
- виключити тіньові зони, що ускладнюють нанесення покриттів;
- розширити технологічні можливості процесу, дозволяючи наносити спеціальні види покриттів (плямисті і функціонально-орієнтовані) та з закономірно змінною товщиною.
Товщина покриття в будь-якій точці виробу залежить від інтенсивності плазмового потоку і кута між нормаллю до поверхні виробу. Зауважимо, що товщина покриття на поверхні виробу збільшується по нормалі до кожної точки вихідної поверхні виробу, і залежить від кута між нормаллю до точки поверхні, і сумарним вектором напрямку дії потоку плазмового струменя (мал. 3). Зміна вектора дії потоку, обумовлюється особливостями кінематики руху виробу в вакуумній камері.
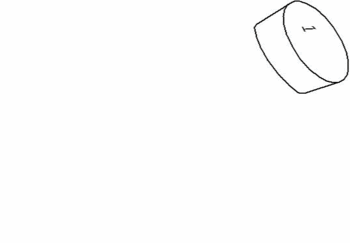
Малюнок 3 – Дія потоку плазми в точках поверхні наноситься
(анімація: 9 кадрів, 79 кілобайт)
(yk – кут під яким наноситься покриття, 1 – катод, 2 – нормалі до точок поверхні, h – товщина покриття, v,u – параметри поверхні виробу)
Висновок
Таким чином в роботі виконаний аналіз основних експлуатаційних характеристик зубчастих коліс. Розглянуто причини зносу зубів, а також розглянуті спосіб дозволяє підвищити працездатність ЗК. Також були проаналізовані можливі варіанти розміщення заготовок у вакуумній камері, можна відзначити, оскільки кількість заготовок розміщуються в камері не залежить від тривалості технологічного впливу, основним напрямком подальшого підвищення продуктивності процесу нанесення покриттів є збільшення кількості заготовок в камері, забезпечуючи при цьому потрібне положення і кінематику руху заготовок щодо плазмових потік.
Перелік посилань
- Васильев А. Ф. Создание функционально-градиентных износостойких покрытий с регулируемой твердостью методом сверхзвукового холодного газодинамического напыления для изделий машиностроения. / А. Ф. Васильев, Д.А. Геращенков, Б. В. Фармаковский, М. А. Юрков /Сборник трудов XIV международной научно-технической конференции «Машиностроение и техносфера XXI века». – Донецк: ДонНТУ, 2007. Т.1. – С. 163-171.
- Внуков Ю.Н., Марков А.А., Лаврова Л.В., Бердышев Н.Ю. Нанесение износостойких покрытий на быстрорежущий инструмент. – Киев, Тэхника, 1992. – 143 с.
- Гончаров М.В. Технология и оборудование получения комплексных покрытий с особыми свойствами. / М.В. Гончаров, В.С. Гончаров // Современные тенденции развития автомобилестроения в России. Труды Всероссийской научно-технической конференции. – Тольятти: ТГУ, 2003. №3. С. 448 – 452.
- Костржицкий А.И., Лебединский О.В. Многокомпонентные вакуумные покрытия. М.: Машиностроение, 1987. – 208 с.
- Михайлов А.Н. Основные принципы и особенности синтеза функционально-ориентированных технологий машиностроения. / А.Н. Михайлов //Сборник трудов XIII международной научно-технической конференции: Машиностроение и техносфера XXI века. В 5-ти томах. – Донецк: ДонНТУ, 2006. Т. 3. С. 61 – 77.
- Михайлов А.Н. Основы синтеза поточно-пространственных технологических систем непрерывного действия. – Донецк: ДонНТУ, 2003. - 379 с.
- Михайлов А.Н. Основы синтеза функционально-ориентированных технологий машиностроения. – Донецк: ДонНТУ, 2008. – 346 с.
- Михайлов А.Н. Общие особенности функционально-ориентированных технологий и принципы ориентации их технологических воздействий и свойств изделий. / А.Н. Михайлов //Сборник трудов XIV международной научно-технической конференции: Машиностроение и техносфера XXI века. В 5-ти томах. – Донецк: ДонНТУ, 2007. Т. 3. С. 38 – 52.
- Технология производства и методы обеспечения качества зубчатых колес и передач. Учеб .пособие / В.Е. Антонюк, А.А. Сусин, С.П. Руденко и др.; под ред. В.Е. Старжинского и М.М. Канне. – Минск: УП "Технопринт", 2003. – 766 с.
- Юдин Д.Л. Пути повышения качества отделочно-упрочняющей обработки зубьев зубчатых колес ППД / Д.Л. Юдин, А.И. Иунихин, М.А. Порхачев, В.А. Фомин // Вестник машиностроения, 1981. – № 3. – С. 49 – 50.