Реферат по теме выпускной
работы
Содержание
- Введение
- 1. Актуальность темы
- 2. Цель и задачи исследования, планируемые результаты
- 3. Обзор исследований по теме
- 4. Основная часть
- Вывод
- Список источников
Введение
Алмазное шлифование крупногабаритных сложнопрофильных тонкостенных оболочек из хрупких неметаллических материалов является неотъемлемой частью технологического процесса создания элементов конструкций изделий авиационной и ракетной техники, эффективность которого определяет трудоемкость, себестоимость и качество изделий. Требования к качеству, предъявляемые к рассматриваемым деталям, определяются условиями их эксплуатации. Основными требованиями являются обеспечение аэродинамичности конструкции, высокой механической прочности, способной сохраняться при эксплуатационных температурах, а также селективное пропускание электроэнергии в заданном интервале частот и относительно малая масса изделия. Аэродинамические требования обеспечиваются формой рассматриваемых деталей-оболочек. Требования к прочности, радиопрозрачности и небольшой массе обеспечиваются физико- механическими свойствами материала (ситалла АС–418), из которых изготавливают рассматриваемые изделия. Обеспечение необходимых радиотехнических свойств изделия возможно при соблюдении высоких требований по точности формы, отклонению от заданной толщины стенки не более ±0,1 мм и шероховатости обработанной поверхности Ra≤2,5 мкм. Прочность изделия в основном обеспечивается отсутствием дефектности в приповерхностном слое [1].
Ситаллы (стеклокристаллические материалы), неорганические материалы, получаемые направленной кристаллизацией разлиных стекол при их термической обработке. Состоят из одной или нескольких кристаллических фаз. В ситаллах мелкодисперсные кристаллы (до 2000 нм) равномерно распределены в стекловидной матрице. Впервые ситаллы были изготовлены в 50–х гг. 20 в. Материалы, подобные ситаллам, за рубежом называют пирокерамом, девитрокерамом, стеклокерамом [2].
1. Актуальность темы
Темой магистерской работы
является: Разработать и
исследовать систему управления точность обработки тонкостенных деталей
из ситаллов
.
В настоящее время в мире наблюдается тенденция производства изделий из неметаллических и композиционных материалов, которые все шире заменяют металлы во многих отраслях промышленности. Эта тенденция связана со снижением себестоимости продукции при одновременном повышении их срока службы, надежности и экологической чистоты. Особое место среди неметаллических материалов занимает керамика. Физико–механические свойства конструкционной керамики (в том числе и ситаллов) по сравнению со всеми видами металлов, которые в настоящее время применяются в качестве главных материалов для изготовления деталей машин, имеют такие отличительные характеристики, как высокую температуру плавления, твердость, высокую износостойкость, коррозионную стойкость, стойкость к воздействию химикатов и т.д. Эти факторы и обусловили широкий интерес к изучению свойств ситаллов, их наблюдению и в конечном итоге разработке методов влияния на свойства в ходе механической обработки.
2. Цель и задачи исследования, планируемые результаты
Целью исследования разработка и исследование системы управления точность обработки тонкостенных деталей из ситаллов.
Основные задачи исследования:
- Анализ факторов влияющих на формирование точности механической обработки изделия.
- Анализ вариантов и выбор метода управления точностью обработки ситаллового обтекателя.
- Выбор параметров САУ обработки.
- Разработка управляющей программы в параметрическом виде.
Объект исследования: Процесс алмазного шлифования ситаллового обтекателя.
Предмет исследования: Процесс формирования точности наружного контура при алмазном шлифовании.
3. Обзор исследований по теме
Технологический процесс обработки изделий включает многооперационную обработку шлифованием как наружного, так и внутреннего их контуров на станках типа РТ 66202, оснащенных агрегатной шлифовальной головкой и системой прямого копирования. В статье приведены результаты исследований динамических характеристик системы СПИД при шлифовании наружной поверхности детали, схема которой представлена на рис. 1
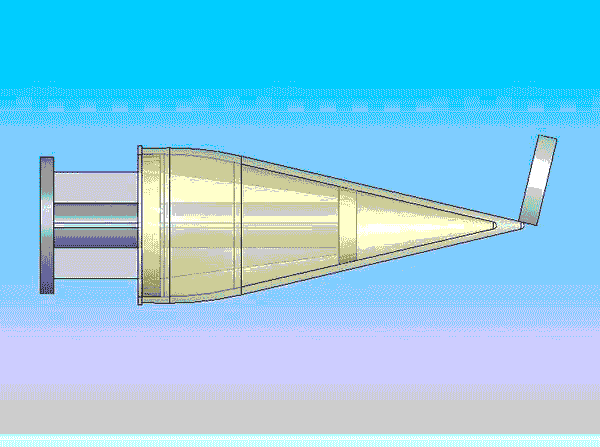
Рисунок 1 – Наружная обработка изделия (анимация: 10 кадров, 10 повторов, 132 килобайт)
Особенности обработки изделий рассматриваемого класса из ситаллов в значительной степени обусловлены следующими факторами. Основные размеры изделия: длина до 1,0 м; максимальный диаметр 450...500 мм; толщина стенки заготовки 20 мм при толщине готового изделия 5 мм. На обработку внутреннего контура изделия затрачивается примерно 18–20 часов машинного времени; обработка наружного контура занимает 6–10 часов при значительной доле ручного труда, применяемого на операции чистовой обработки наружного профиля. Эксплуатационные характеристики изделий предполагают соблюдение повышенных требований по точности и качеству обработки, в частности, обеспечение минимальной глубины дефектности поверхностного слоя, которая определяет продолжительность последующих операций химического травления и упрочнения механически обработанных поверхностей [3].
Для повышения точности механической обработки ситаллового обтекателя необходимо нивелировать факторы влияющие на нее.
Основной причиной образования погрешности на шлифованной поверхности изделия является изменение положения в пространстве обрабатываемой поверхности относительно траектории, заданной формой и профилем детали. Причинами, вызывающими изменение расстояния между заданной и реальной траекториями формообразования, являются вибрации в технологической системе обработки, а также неточности геометрической формы шлифовального круга и погрешность его установки [4].
Рассмотрим факторы влияющие на точность обработки.
Известно, что при шлифовании
тонкостенных оболочек вращения (схема установки заготовки на станке
представлена на рисунке 2) в зоне контакта заготовки со шлифовальным
кругом возникают изгибные колебания на двух частотах 60±5 Гц
и 123±10 Гц, близких к собственным частотам подсистемы шпиндельный
узел станка – приспособление – заготовка
[5].
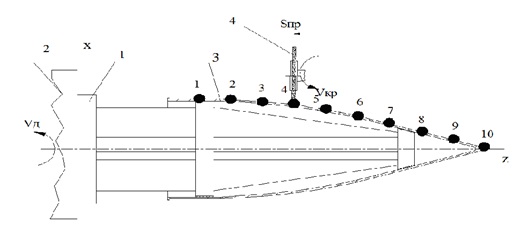
Рисунок 2 – Схема технологической системы при наружном круглом шлифовании заготовки – тонкостенной оболочки вращения из ситалла: 1 – оправка; 2 – шпиндель станка; 3 – обрабатываемая заготовка; 4 – шлифовальный круг 1А1 200х10х3х76 А 315/250–4–М2–01, установленный в агрегатной головке. Точки 1…10 – точки, ограничивающие области изменения параметров рассматриваемой технологической системы
Также предполагается, что в зоне контакта шлифовального круга с заготовкой возникают параметрические колебания детали – тонкостенной оболочки вращения, под воздействием перемещающейся силы резания. На основании данных, приведенных в работе [6], проведен анализ устойчивости системы на параметрические колебания, который показал, что наибольшей неустойчивостью обладают области заготовки в районе точек 1 – 5 (см. рисунок 1). Области, ограниченные точками 6 – 10, находятся в зоне устойчивости к параметрическим колебаниям. Схема алмазно-абразивной обработки оболочки, представлена на рис. 3.
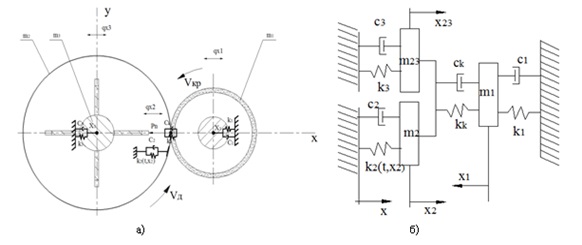
Рисунок 3 – Схема шлифования (а) и расчетная схема (б) алмазно-абразивной обработки тонкостенной оболочки вращения из ситаллa
Обрабатываемая заготовка представляет собой тонкостенную оболочку вращения, динамику которой невозможно описать при помощи системы с сосредоточенной массой, к которой приводится рассматриваемая технологическая система. Поэтому анализ динамического поведения оболочки необходимо провести в соответствии с законами теории оболочек. Для каждой области, ограниченной точками, указанными на рисунке 2, при помощи модели, разработанной в программе Simulink, были определены частота и амплитуда колебаний. Динамическое поведение технологической системы при обработке рассматриваемой заготовки – тонкостенной оболочки вращения из ситалла при перемещении инструмента от вершины изделия к фланцу не постоянно, что сказывается на качестве обработанной поверхности. Характер колебаний, их амплитуда, частота, форма изменяются в зависимости от участка относительно оси заготовки, который проходит инструмент [4].
Исследования особенностей
вынужденных колебаний подсистемы приспособление–заготовка
[7]
также показали переменную интенсивность уровня вибраций по длине
заготовки, сходную с экспериментальной кривой амплитуды колебаний. На
рис. 4 по длине заготовки относительно оси Z приведены динамические и
упругие показатели подсистемы шпиндельный
узел–приспособление–заготовка
.
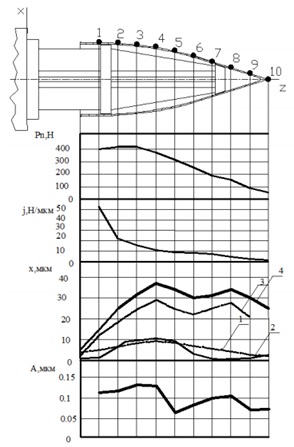
Рисунок
4 – Сравнительные диаграммы изменения динамических и упругих
характеристик подсистемы шпиндельный
узел – оправка – заготовка
вдоль оси детали: Pn – нормальной составляющей силы резания,
Н; j – изгибной жесткости, H/мкм; x – статических
прогибов, мкм (1 – суммарные радиальные перемещения
шпиндельного узла, 2 – радиальные перемещения обрабатываемой
заготовки, 3 – радиальные перемещения подсистемы приспособление–заготовка
,
4 – суммарные радиальные перемещения подсистемы шпиндельный
узел – приспособление–заготовка
);
А – амплитуды вибраций, мкм. 18
Однако полученные теоретические данные имели некоторые расхождения с их экспериментальными значениями. Это можно объяснить следующим. При моделировании не были учтены ряд свойств обрабатываемой заготовки как замкнутой тонкостенной оболочки, а также факторы, связанные с механической обработкой детали на специальном станке, что требует решения задачи моделирования поведения системы при шлифовании на более высоком уровне [8].
4. Основная часть
Анализ процесса образования погрешности контурной обработки на станках с ЧПУ и ее составляющих показывает, что автоматическое управление можно проводить за счет коррекции эквидистанта или управлением режимами резания с целью стабилизации или компенсации возмущений. Применяют также комбинированные методы, которые сочетают управление режимами обработки с коррекцией эквидистанта. По характеру применяемой информации методы автоматического управления можно разделить на методы, использующие априорную, текущую и апостериорную информацию.
Управление режимами резания по априорной информации. Этот метод целесообразно применять при существенном влиянии нестабильности режимов резания на качество обработанной поверхности, например, при шлифовке. Метод базируется на установленном связи между возмущениями, управляющими воздействиями и параметрами качества обработки, то есть на заранее детерминированных передаточных функциях Wnpx и Wencx.
В этом случае процесс резки должен быть представлен как минимум с двумя входами: по вектору относительного формообразующего движения хт, заданным без всякой коррекции и по управляющим воздействием S (рис. 5). Итак, силовой фактор, который спроектирован на координату х, определяется зависимостью:

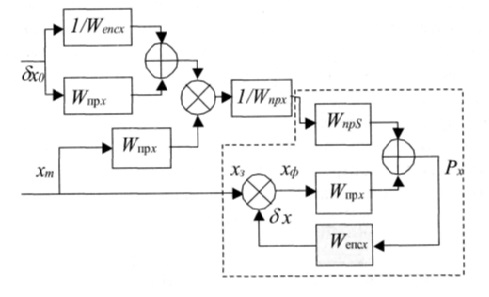
Рисунок 5 – Схема управления для стабилизации условий обработки
Управление режимами резания по
текущей информацией. Метод предусматривает создание САУ, замкнутой
через процесс резки и работающей по принципу сведение
баланса
, то есть за ошибкой.
Несмотря на общий принцип управления, этот метод отличается от
рассмотренного выше метода управления траекторией формообразующего
движения по текущей информацией. Согласно схеме метода (рис. 6) влияют
на выходные характеристики процесса, в частности, точность обработки,
через режимы резания. При этом за непосредственное цель управления
выбирают любой параметр процесса резания, контролируется и интегрирует
в себе максимум информации. Таким параметром является, как правило,
силовой фактор, обычно измеряется через упругие деформации системы.
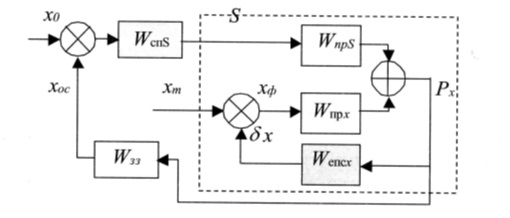
Рисунок 6 – Схема управления режимами обработки по текущей информации
Метод целесообразно применять не только для стабилизации, но и для программного управления любыми параметрами процесса в цикле обработки. Например, при различном шлифовке система может обеспечить алгоритм управления поперечной врезной подачей, что требуется, в функции координаты оставленного припуска. Для этого в САУ должно быть обеспечено непрерывное измерение фактической координаты в направлении врезки и применен дополнительный программный блок, которым заданный алгоритм управления.
Согласно одному из представленных методов производится разработка и исследование системы управления точность обработки тонкостенных деталей из ситаллов.
Вывод
Магистерская работа посвящена разработке и исследованию системы управления точность обработки тонкостенных деталей из ситаллов. При написании данного реферата магистерская работа еще не завершена. Окончательное завершение: июнь 2018 года. Полный текст работы и материалы по теме могут быть получены у автора или его руководителя после указанной даты.
Список использованных источников
- Гусев В.В., Калафатова Л.П. Повышение виброустойчивости технологической системы во время алмазного шлифования тонкостенных оболочек вращения из ситаллов //ISSN 2078–7405. Резание и инструмент в технологических системах, 2013, выпуск 83. Харьков: КПИ..
- ХИМИК. Сайт о химии. Ситаллы // [Электронный ресурс] – Режим доступа: http://www.xumuk.ru/encyklopedia/2/4086.html
- Калафатова
Л.П. Прогнозирование качества поверхностного слоя при обработке изделий
из технических ситаллов // Приложение №9 к журналу
Инженерный журнал. Справочник
Инженерия поверхности. – М.: Машиностроение. – 2002. – №9. – С.5–8. - Калафатова Л.П., Гусев В.В., Олейник С.Ю. Исследование динамического состояния технологической системы алмазно–абразивной обработки тонкостенных оболочек из ситаллов // Вісник СевНТУ: зб. наук. пр. Вип. 128/2012. Серія: Машиноприладобудування та транспорт. – Севастополь, 2012 с.60–67
- Гусев В.В. Исследование динамических характеристик элементов системы СПИД при шлифовании деталей сложной пространственной формы из ситаллов / В.В. Гусев, Л.П. Калафатова, И.С. Каракуц // Надійність інструменту та оптимізація технологічних систем. Збірник наукових праць. – Краматорск, 2007. – Вип. №21. – С. 148 – 155.
- Якушев Н.З. Коническая оболочка под действием подвижных нагрузок / Якушев Н. З., Якушев Р. С. // Исследования по теории пластин и оболочек. – Казань: Изд–во Казанского ун–та, 1975. – С. 303 – 316
- Гусев В.В. Повышение качества алмазного шлифования тонкостенных оболочек из ситалла путем снижения вибраций в технологической системе / Гусев В.В., Калафатова Л.П., Олейник С.Ю. // Наукові праці ДонНТУ– Донецк, 2010. – Вип. № 7(166).– С. 156–167.
- Петраков Ю.В.Драчев О.И. Теория автоматического управления технологическими системами / М.: Машиностроение, 2008. – C. 158 – 162