Реферат за темою випускної роботи
Зміст
- Вступ
- 1. Актуальність теми
- 2. Мета і задачі дослідження та заплановані результати
- 3. Огляд досліджень та розробок
- 3.1 САУ на основі нечіткої логіки
- 3.2 Система адаптивного управління процесом обробки деталей на верстатах з ЧПУ
- 3.3 Система управління гідравлічних машин на прикладі термопластавтомата
- Висновки
- Перелік посилань
Вступ
Системи автоматичного управління та контролю (далі САУ) є невід'ємною частиною сучасних підприємств і грають ключову роль в забезпеченні їх надійної та безпечної роботи. Сучасні САУ зазвичай служать для вирішення двох основних завдань: автоматичне керування технологічними процесами (ТП) і автоматичний контроль параметрів і режимів роботи.
1. Актуальність теми
Автоматизація ТП дозволяє істотно збільшити ефективність роботи конкретного устаткування (об'єкта управління) і роботи підприємства в цілому. Автоматизація технологічного процесу базується на описі технологічних операцій (технологічних алгоритмів), розробленому інженерами-технологами і забезпечує сам ТП. Автоматизація дозволяє істотно знизити час, що витрачається на виконання стандартних (заздалегідь визначених) дій (операцій, циклів) автоматизируемого обладнання, за рахунок збільшення швидкостей виконавчих механізмів об'єктів управління, відсутності зупинки між виконанням окремих дій, що рухаються, реалізації спільного руху декількох механізмів, оптимізації траєкторії руху керованого устаткування і т. п. в сьогоднішній час існує безліч різних САУ і в даній роботі, розглянуті лише кілька з них.
2. Мета і задачі дослідження та заплановані результати
Основна мета автоматизації та механізації верстатів при модернізації - зменшення допоміжного часу при одночасному збереженні або підвищенні точності обробки та полегшення праці верстатника.
Останнім часом першорядне значення має підвищення точності і інші якісні показники модернізованого обладнання. Досвід показує, що модернізація прецизійних верстатів для підвищення їх точності в більшості випадків економічно виправдана, так як придбання нового обладнання більш високого класу точності завжди пов'язано зі значними матеріальними витратами. При складанні планів модернізації враховуються раціоналізаторські пропозиції. Причому найбільший ефект приносять, як правило, ті пропозиції, які розроблені творчими бригадами в складі робочих-верстатників, майстрів і інженерів.
Основні задачі дослідження:
- Аналіз сучасних систем автоматичного управління.
- Вибір параметрів САУ обробки.
- Проектування САУ для токарного верстата моделі 16К20Т1
Об'єкт дослідження: процес токарної обробки деталі.
Предмет дослідження: процес підвищення якості обробки при точінні циліндричних поверхонь.
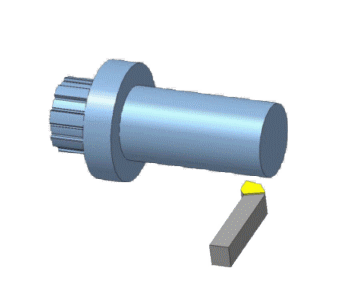
Токарна обробка надтвердих матеріалів (анімація: 7 повторів, 8 кадрів, 104 кілобайт)
У верстатів токарної групи в необхідних випадках встановлюють механізми прискорених поздовжніх переміщень супорта при холостих ходах і застосовують пристрої для автоматичного вимкнення поздовжніх подач. При використанні верстата протягом тривалого часу для обробки конусів автоматизують подачу верхніх поворотних санчат супорта шляхом зв'язку ходового вала з гвинтом подачі кінематичної ланцюгом, що складається з зубчастих коліс, проміжного кронштейна і телескопічного вала з шарнірами Гука по кінцях. У необхідних випадках для автоматизації подачі пінолі задньої бабки встановлюють гідропневматичні пристрою.
3. Огляд досліджень та розробок
3.1 САУ на основі нечіткої логіки
Для початку розглянемо систему автоматичного управління режимами різання на основі нечіткої логіки.
Традиційно серед всіх режимних параметрів виділяють Pz і θ як найбільш інформативні при дослідженні та управлінні процесом різання, а також найбільш доступні для вимірювання.
Температура в зоні різання і головна складова сили різання при точінні визначаються за наступними емпіричних залежностях[1]:
де CPz – константа, що залежить від властивостей оброблюваного матеріалу, по суті своїй представляє питому силу різання, що припадає на одиницю площі поперечного перерізу зрізу, Н/мм2; tp – глибина різання, мм; S – подача, мм/об, V – скорость різання, м/мин; KP – загальний коефіцієнт, що представляє собою твір приватних коефіцієнтів, що враховують конкретні умови різання; Cθ – коефіцієнт, що виражає залежність тепловіддачі від оброблюваного матеріалу і умов різання; φ – головний кут в плані, градуси. Ступеня x, y, z, m, n, q – є речовими числами, що показують ступінь впливу кожного з параметрів режиму різання відповідно на силу різання і температуру в зоні різання [4].
Модель ПТ повинна бути багатовимірної (S, V, tp – керуючі параметри; Pz, θ – керовані параметри) і многорежимной (забезпечити дослідження, наприклад, чорнового і чистового режимів різання). Ці обставини призводять до необхідності пошуку принципово нових підходів до вирішення завдання побудови моделей ПТ, що дозволяють забезпечити необхідну для САУ багатовимірність, багаторежимна, багатозв'язна (велике число параметрів ПТ знаходяться в складних взаємозв'язках, які чинять спротив формалізації) і нелінійність ПВ. В даному прикладі пропонується метод нечіткого моделювання Такагі – Сугено [5] в якості вирішення проблеми побудови моделі в даних умовах. Суть даного методу зводиться до апроксимації нечіткими множинами нелінійних компонентів моделі і всіх компонентів, точне визначення яких або важко, або призводить до значного ускладнення моделі. Апарат нечіткої логіки Такагі – Сугено дозволяє апроксимувати трудноформалізуемие компоненти моделі і разом з тим забезпечує необхідні якості багатовимірності, багатозв'язна і т. Д.
Мета управління визначається вимогами оптимальності перехідних процесів вихідних координат Pz, θ на всіх режимах функціонування системи (по швидкодії і перерегулювання), підтримкою сталості значень Pz = const і θ = const для кожного режиму різання і мінімумом помилок неузгодженості між перетвореними вимірювальною системою сигналами EPz(t), Eθ(t) вихідних координат Pz, θ відповідно, і заданих впливів uPz, uθ :
Схему САУ процесу точіння можна представити в наступному вигляді (рис. 1).
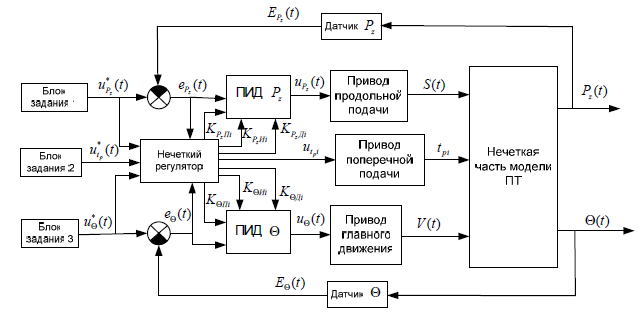
Рисунок 1 – Схема САУ процесом точіння [6]
На рис. 1 блоки завдання 1, 2, 3 призначені для подачі задають напруг upz(t), uθ(t) ,utp(t) відповідно. САУ режимами різання являє собою два ПІД-регулятора для регулювання координат Pz ,θ і адаптивної надбудови у вигляді нечіткого регулятора, який виконує функцію налаштування ПІД-регуляторів і формування керуючого напруги для приводу поперечної подачі на певний режим різання. Налаштування ПІД-регуляторів здійснюється подачею відповідних коефіцієнтів.
Дана САУ режимами різання, яка забезпечує оптимальне формування режимних параметрів процесу точіння (ПТ) для чорнового і чистового режимів різання в реальному режимі часу, що дозволяє заощадити час на переналагодження верстата і підвищити ефективність ПВ. Забезпечення сталості значень параметрів Pz, θ і раціональна настройка режимних параметрів ПТ дозволяють поліпшити якість продукції, що випускається підвищити техніко-економічні показники ПВ. Використовувана при розробці алгоритму управління нечітка модель ПТ дозволяє значно знизити невизначеність ПТ шляхом використання двох вимірюваних координат (Pz і θ) замість звичайної однієї і обліку залежностей Pz (S, V, tp) і θ (S, V, tp), що в свою чергу дозволяє підвищити точність САУ. Однак головний недолік цієї моделі: громіздкість і значні вимоги до обчислювальних ресурсів. Тому представлену нечітку модель ПТ буде важко використовувати у вбудованих автоматичних системах управління. Головним призначенням цієї моделі є застосування в дослідженні процесу точіння і в розробці алгоритмів керування для систем управління ПВ. Ця особливість моделі і наявність таких особливостей, як багатовимірність і багаторежимна, практично повністю виключають можливість використання класичних методів управління, адаптивних методів управління з еталонною моделлю, а також використання всіляких спостерігачів стану системи.
3.2 Система адаптивного управління процесом обробки деталей на верстатах з ЧПУ
Наступною розглянемо систему адаптивного управління процесом обробки деталей на верстатах з ЧПУ.
При обробці деталі різанням на інструмент впливають фактори різної природи: механічне навантаження, електричні струми, вібрації, хімічні впливи, пружні деформації ТОС, наростообразованіе. Все це призводить до інтенсивного зносу конструктивних елементів різця і, навіть, до його поломки. Що веде до зниження точності, якості, продуктивності або до появи шлюбу, що несе за собою економічні збитки і велику собівартість оброблюваних деталей [7].
Отже, для поліпшення параметрів якості, точності, собівартості оброблюваних деталей варто використовувати систему адаптивного управління ріжучим інструментом, безпосередньо в процесі обробки, що дасть можливість виявляти момент попередній поломки інструменту, для своєчасної його заміни.
Система адаптивного управління процесом різання повинна володіти високою точністю інформації про зону різання і стані інструменту, в реальному часі відстежувати ступінь зносу, ЕРС пари інструмент-деталь, і силі, що діє на інструмент. Система повинна працювати стабільно, а також з низькою ймовірністю помилкової оцінки стану ріжучого інструменту і збоїв в системі автоматизованого контролю процесу обробки деталі. Реалізація даної системи повинна бути такою, щоб її можна було застосувати без особливих конструктивних змін приводів верстата і технологічної обробної системи (ТОС) [8].
Згідно з дослідженнями проведеними в Національному технічному університету України, найбільш підходящим з інформаційних параметрах, на основі яких можна судити про стан обробного інструменту, є ЕРС різання і сила різання.
Виходячи з цього, система адаптивного управління процесом різання заснована на вимірі виникають ЕРС різання і сили різання, які виникають в процесі обробки природним чином.
Основним параметром для контролю є ЕРС різання, що виникає в результаті підвищення температури в зоні різання, так як збільшення ЕРС свідчить про збільшення контакту інструмент-деталь (КИД), що в свою чергу говорить про збільшення зносу інструменту.
Система адаптивного управління процесом обробки деталей має 2 контури контролю. Перший контур контролю є підсистемою швидкого аварійного відключення приводів верстата, яка в разі перевищення допустимої сили різання посилає команду на безпечний відведення різця із зони різання і відключення приводів верстата. Другий контур є підсистемою оцінки і прогнозування зносу інструмента на основі сигналів ЕРС різання.
На малюнку (рис. 2) показана блок – схема пристрою, що реалізує запропоновану систему адаптивного управління.
Відповідно до пропонованої системою в процесі обробки вимірюють сигнали термоерс, і ЕРС пружних переміщень технологічної системи за допомогою датчиків 1, відокремлюють постійні і змінні складові сигналів, що вимірюються в блоці 2, який може бути виконано у вигляді електронного фільтра. Постійні складові подають в блок управління 3, де формують керуючі команди на зміну режимів різання, а змінні за допомогою перетворювача 4, який може бути виконаний у вигляді когерентного оптичного процесора, перетворюють у взаімокоррелірующіе функції, які зчитуються в пристрої 5, а потім подають в блок корекції 6, яким формують коригуючі команди на зміну режимів різання. Команда коригування на зміну режимів різання потрапляє в блок управління 3, де створюються команди управління приводами верстата.

Рисунок 1 – Блок-схема системи адаптивного управління процесом обробки деталей на верстатах з ЧПУ [9]
Використання запропонованого способу дозволяє з високим ступенем точності по ряду параметрів отримати більш точну інформацію про швидкість зносу ріжучого інструменту в процесі обробки і тим самим найбільш повно використовувати інструмент за його властивостями стійкості, що в кінцевому підсумку дозволяє підвищити продуктивність обробки деталей на верстатах з ЧПУ і знизити собівартість оброблюваних деталей.
3.3 Система управління гідравлічних машин на прикладі термопластавтомата
І останній є система управління гідравлічних машин на прикладі термопластавтомата.
Основні функції системи:
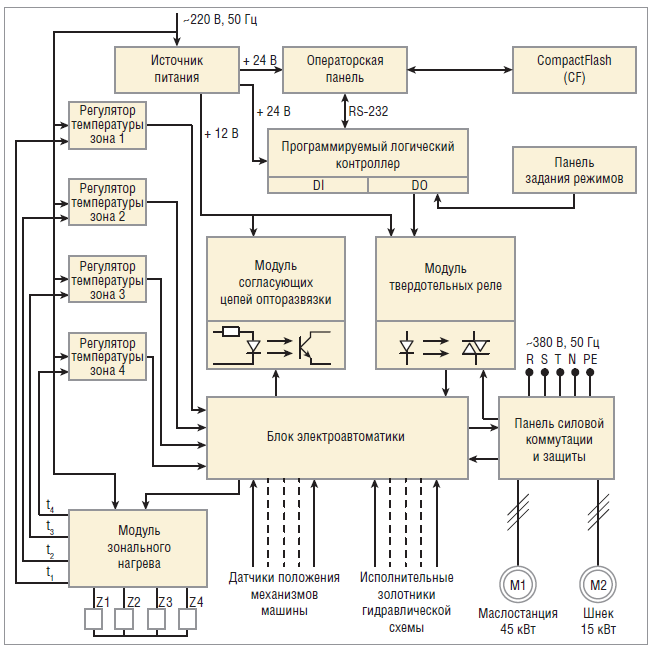
Рисунок 1 – Структурна схема системи управління термопластавтоматами [10]
Умовні позначення: M1, M2 - електродвигуни; Z1 ... Z4 - нагрівальні елементи; R, S, T - фази напруги; N - нейтраль; PE - заземлення; t1 ... t4 - температура в зонах нагріву; DO, DI - дискретні входи і виходи [10].
Запропонований варіант модернізації СУТ впроваджений поки тільки на двох машинобудівних підприємствах: ВАТ Тульський збройовий завод
і ВАТ Тульський машинобудівний завод ім. Рябикова
. Майже дворічний термін експлуатації підтвердив спроможність обраних інженерних рішень, що дозволило досягти:
Крім цього, конфігурація апаратно-програмних засобів СУТ дозволяє в разі модернізації в найкоротші терміни адаптуватися до особливостей обладнання практично будь-який гідравлічної машини для лиття під тиском, що дає реальний шанс для тиражування розробленої системи на аналогічних виробництвах і, як наслідок, дозволяє домогтися економії коштів .
Висновки
Магістерська робота присвяченій підвищенню якості обробки за рахунок модернізації системи управління токарного верстата моделі 16К20Т1. При написанні даного реферату магістерська робота ще не завершена. Остаточне завершення: червень 2018 року. Повний текст роботи та матеріали по темі можуть бути отримані у автора або його керівника після зазначеної дати.
Перелік посилань
- Бобров З.Ф. Основы теории резания металлов / З.Ф. Бобров. - М.: Машиностроение, 1975. - 344 с.
- Грановский Г.И. Резание металлов / Г.И. Грановский, В.Г. Грановский. - М.: Высшая школа, 1985. – 304 с.
- Основы автоматизации и управления технологическими процессами в машиностроении / Под ред. В.Ц. Зориктуева. - Уфа: Уфимск. гос. авиац. техн. ун-т, 2000. - 406 с.
- Рубенштейн С.А. Основы учения о резании металлов и режущий инструмент / С.А. Рубинштейн [и др.]. – М.: Машиностроение, 1968. – 386 с.
- KazouT., H. O. Wang. Fuzzy control systems design and analysis. JohnWiley&Sons, Inc, 2001. 303 p.
- Зориктуев В.Ц. Система автоматического управления режимами резания на основе нечеткой логики / В.Ц . Зориктуев, Р.Р. Шангареев. - Уфа: УГАТУ, 2010. - 8 с.
- Васильев С.В. ЭДС и температура резания / С.В. Васильев // Станки и инструмент, 1980, №10. – C. 20-22.
- Остафьев В.А. Адаптивная система управления / В.А Остафьев, В.В. Шевченко, Г.С. Тымчик // Механизация и автоматизация управления. – Киев, №1, 1983. – С. 18-20.
- Шарабура С.Н. Система адаптивного управления процессом обработки деталей на станках с ЧПУ / С.Н. Шарабура, В.В. Шевченко // Современные научные исследования и инновации. 2014. – № 6. Ч. 1.
- Деркач А.Д. Примеры решений на базе сенсорных панелей Weintek для АСУ ТП и встраиваемых систем / А.Д. Деркач, Р.В, Камалиев. В.Н. Маценко // Современные технологии автоматизации. – 2014. – № 3.