Реферат по теме выпускной работы
Содержание
- Введение
- 1. Актуальность темы
- 2. Цель и задачи исследования, планируемые результаты
- 3. Обзор исследований и разработок
- 3.1 САУ на основе нечеткой логики
- 3.2 Система адаптивного управления процессом обработки деталей на станках с ЧПУ
- 3.3 Система управления гидравлических машин на примере термопластавтомата
- Выводы
- Список источников
Введение
Системы автоматического управления и контроля (далее САУ) являются неотъемлемой частью современных предприятий и играют ключевую роль в обеспечении их надежной и безопасной работы. Современные САУ обычно служат для решения двух основных задач: автоматическое управление технологическими процессами (ТП) и автоматический контроль параметров и режимов работы.
1. Актуальность темы
Автоматизация ТП позволяет существенно увеличить эффективность работы конкретного оборудования (объекта управления) и работы предприятия в целом. Автоматизация технологического процесса базируется на описании технологических операций (технологических алгоритмов), разработанном инженерами-технологами и обеспечивающем сам ТП. Автоматизация позволяет существенно снизить время, затрачиваемое на выполнение стандартных (заранее определенных) действий (операций, циклов) автоматизируемого оборудования, за счет увеличения скоростей исполнительных механизмов объектов управления, отсутствия останова между выполнением отдельных действий движущимися частями, реализации совместного движения нескольких механизмов, оптимизации траектории движения управляемого оборудования и т. п. В сегодняшнее время существует множество различных САУ и в данной работе, рассмотрены лишь несколько из них.
2. Цель и задачи исследования, планируемые результаты
Основная цель автоматизации и механизации станков при модернизации — уменьшение вспомогательного времени при одновременном сохранении или повышении точности обработки и облегчении труда станочника.
В последнее время первостепенное значение имеет повышение точности и другие качественные показатели модернизируемого оборудования. Опыт показывает, что модернизация прецизионных станков для повышения их точности в большинстве случаев экономически оправдана, так как приобретение нового оборудования более высокого класса точности всегда связано со значительными материальными затратами. При составлении планов модернизации учитываются рационализаторские предложения. Причем наибольший эффект приносят, как правило, те предложения, которые разработаны творческими бригадами в составе рабочих-станочников, мастеров и инженеров.
Основные задачи исследования:
- Анализ современных систем автоматического управления.
- Выбор параметров САУ обработки.
- Проектирование САУ для токарного станка модели 16К20Т1
Объект исследования: процесс токарной обработки детали.
Предмет исследования: процесс повышения качества обработки при точении цилиндрических поверхностей.
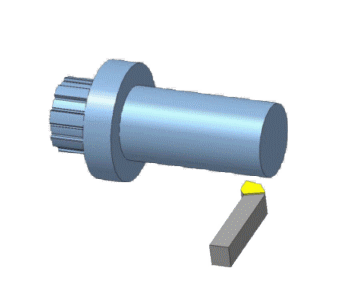
Токарная обработка сверхтвердых материалов (анимация: 7 повторов, 8 кадров, 104 килобайт)
У станков токарной группы в необходимых случаях устанавливают механизмы ускоренных продольных перемещений суппорта при холостых ходах и применяют устройства для автоматического выключения продольных подач. При использовании станка в течение продолжительного времени для обработки конусов автоматизируют подачу верхних поворотных салазок суппорта путем связи ходового вала с винтом подачи кинематической цепью, состоящей из зубчатых колес, промежуточного кронштейна и телескопического вала с шарнирами Гука по концам. В необходимых случаях для автоматизации подачи пиноли задней бабки устанавливают гидропневматические устройства.
3. Обзор исследований и разработок
3.1 САУ на основе нечеткой логики
Для начала рассмотрим систему автоматического управления режимами резания на основе нечеткой логики.
Традиционно среди всех режимных параметров выделяют Pz и θ как наиболее информативные при исследовании и управлении процессом резания, а также наиболее доступные для измерения.
Температура в зоне резания и главная составляющая силы резания при точении определяются по следующим эмпирическим зависимостям [1]:
где CPz – константа, зависящая от свойств обрабатываемого материала, по сути своей представляющая удельную силу резания, приходящуюся на единицу площади поперечного сечения среза, Н/мм2; tp – глубина резания, мм; S – подача, мм/об, V – скорость резания, м/мин; KP – общий коэффициент, представляющий собой произведение частных коэффициентов, учитывающих конкретные условия резания; Cθ – коэффициент, выражающий зависимость теплоотдачи от обрабатываемого материала и условий резания; φ – главный угол в плане, градусы. Степени x, y, z, m, n, q – являются вещественными числами, показывающими степень влияния каждого из параметров режима резания соответственно на силу резания и температуру в зоне резания [4].
Модель ПТ должна быть многомерной (S, V, tp – управляющие параметры; Pz, θ – управляемые параметры) и многорежимной (обеспечить исследование, например, чернового и чистового режимов резания). Эти обстоятельства приводят к необходимости поиска принципиально новых подходов к решению задачи построения моделей ПТ, позволяющих обеспечить требуемую для САУ многомерность, многорежимность, многосвязность (большое число параметров ПТ находятся в сложных взаимосвязях, не поддающихся формализации) и нелинейность ПТ. В данном примере предлагается метод нечеткого моделирования Такаги – Сугено [5] в качестве решения проблемы построения модели в данных условиях. Суть данного метода сводится к аппроксимации нечеткими множествами нелинейных компонентов модели и всех компонентов, точное определение которых либо затруднительно, либо приводит к значительному усложнению модели. Аппарат нечеткой логики Такаги–Сугено позволяет аппроксимировать трудноформализуемые компоненты модели и вместе с тем обеспечивает требуемые качества многомерности, многосвязности и т. д.
Цель управления определяется требованиями оптимальности переходных процессов выходных координат Pz, θ на всех режимах функционирования системы (по быстродействию и перерегулированию), поддержанием постоянства значений Pz = const и θ = const для каждого режима резания и минимумом ошибок рассогласования между преобразованными измерительной системой сигналами EPz(t), Eθ(t) выходных координат Pz, θ соответственно, и заданных воздействий uPz, uθ :
Схему САУ процесса точения можно представить в следующем виде (рис. 1).
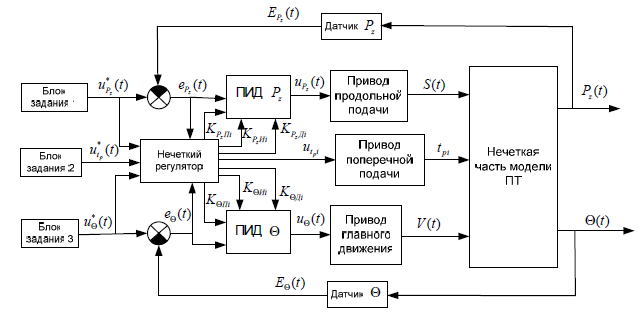
Рисунок 1 – Схема САУ процессом точения [6]
На рис. 1 блоки задания 1, 2, 3 предназначены для подачи задающих напряжений upz(t), uθ(t) ,utp(t) соответственно. САУ режимами резания представляет собой два ПИД-регулятора для регулирования координат Pz ,θ и адаптивной надстройки в виде нечеткого регулятора, который выполняет функцию настройки ПИД-регуляторов и формирования управляющего напряжения для привода поперечной подачи на определенный режим резания. Настройка ПИД-регуляторов осуществляется подачей соответствующих коэффициентов.
Данная САУ режимами резания, которая обеспечивает оптимальное формирование режимных параметров процесса точения (ПТ) для чернового и чистового режимов резания в реальном режиме времени, что позволяет сэкономить время на переналадку станка и повысить эффективность ПТ. Обеспечение постоянства значений параметров Pz, θ и рациональная настройка режимных параметров ПТ позволяют улучшить качество выпускаемой продукции повысить технико-экономические показатели ПТ. Используемая при разработке алгоритма управления нечеткая модель ПТ позволяет значительно снизить неопределенность ПТ путем использования двух измеряемых координат (Pz и θ) вместо обычной одной и учета зависимостей Pz (S, V, tp ) и θ(S, V, tp ), что в свою очередь позволяет повысить точность САУ. Однако главный недостаток этой модели: громоздкость и значительные требования к вычислительным ресурсам. Поэтому представленную нечеткую модель ПТ будет затруднительно использовать во встраиваемых автоматических системах управления. Главным предназначением данной модели является применение в исследовании процесса точения и в разработке алгоритмов управления для систем управления ПТ. Эта особенность модели и наличие таких особенностей, как многомерность и многорежимность, практически полностью исключают возможность использования классических методов управления, адаптивных методов управления с эталонной моделью, а также использование всевозможных наблюдателей состояния системы.
3.2 Система адаптивного управления процессом обработки деталей на станках с ЧПУ
Следующей рассмотрим систему адаптивного управления процессом обработки деталей на станках с ЧПУ.
При обработке детали резанием на инструмент воздействуют факторы различной природы: механическая нагрузка, электрические токи, вибрации, химические воздействия, упругие деформации ТОС, наростообразование. Все это приводит к интенсивному износу конструктивных элементов резца и, даже, к его поломке. Что ведет к снижению точности, качества, продуктивности или к появлению брака, что несет за собой экономические убытки и большую себестоимость обрабатываемых деталей [7].
Следовательно, для улучшения параметров качества, точности, себестоимости обрабатываемых деталей стоит использовать систему адаптивного управления режущим инструментом, непосредственно в процессе обработки, что даст возможность выявлять момент предшествующий поломке инструмента, для своевременной его замены.
Система адаптивного управления процессом резания должна обладать высокой точностью информации о зоне резания и состоянии инструмента, в реальном времени отслеживать степень износа, ЭДС пары инструмент-деталь, и силе, действующей на инструмент. Система должна работать стабильно, а также с низкой вероятностью ложной оценки состояния режущего инструмента и сбоев в системе автоматизированного контроля процесса обработки детали. Реализация данной системы должна быть таковой, чтоб ее можно было применить без особых конструктивных изменений приводов станка и технологической обрабатывающей системы (ТОС) [8].
Согласно исследованиям проведенным в Национальном техническом университет Украины, наиболее подходящим по информационным параметрам, на основе которых можно судить о состоянии обрабатывающего инструмента, есть ЭДС резания и сила резания.
Исходя из этого, система адаптивного управления процессом резания основана на измерении возникающих ЭДС резания и силы резания, которые возникают в процессе обработки естественным образом.
Основным параметром для контроля является ЭДС резания, что возникает в следствии повышения температуры в зоне резания, так как увеличение ЭДС свидетельствует об увеличении контакта инструмент-деталь (КИД), что в свою очередь говорит об увеличении износа инструмента.
Система адаптивного управления процессом обработки деталей имеет 2 контура контроля. Первый контур контроля является подсистемой быстрого аварийного отключения приводов станка, которая в случае превышения допустимой силы резания посылает команду на безопасный отвод резца из зоны резания и отключение приводов станка. Второй контур является подсистемой оценки и прогнозирования износа инструмента на основе сигналов ЭДС резания.
На рисунке (рис. 2) показана блок – схема устройства, реализующего предложенную систему адаптивного управления.
В соответствии с предлагаемой системой в процессе обработки измеряют сигналы термоэдс, и ЭДС упругих перемещений технологической системы с помощью датчиков 1, отделяют постоянные и переменные составляющие сигналов, измеряемых в блоке 2, который может быть выполнено в виде электронного фильтра. Постоянные составляющие подают в блок управления 3, где формируют управляющие команды на изменение режимов резания, а переменные с помощью преобразователя 4, который может быть выполнен в виде когерентного оптического процессора, превращают во взаимокоррелирующие функции, которые считываются в устройстве 5, а затем подают в блок коррекции 6, которым формируют корректирующие команды на смену режимов резания. Команда корректировки на изменение режимов резания попадает в блок управления 3, где создаются команды управления приводами станка.

Рисунок 2 – Блок-схема системы адаптивного управления процессом обработки деталей на станках с ЧПУ [9]
Использование предлагаемого способа позволяет с высокой степенью точности по ряду параметров получить более точную информацию о скорости износа режущего инструмента в процессе обработки и тем самым наиболее полно использовать инструмент по его свойствам устойчивости, что в конечном итоге позволяет повысить производительность обработки деталей на станках с ЧПУ и снизить себестоимость обрабатываемых деталей.
3.3 Система управления гидравлических машин на примере термопластавтомата
И последней является система управления гидравлических машин на примере термопластавтомата.
Основные функции системы:
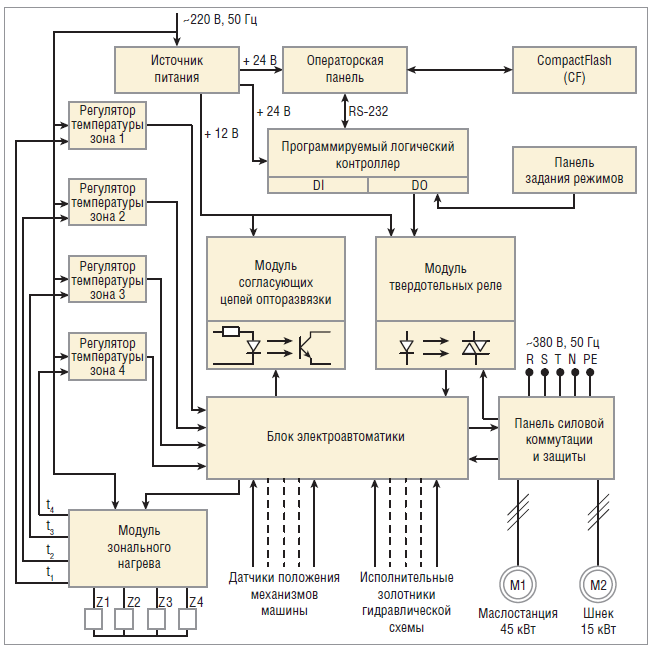
Рисунок 3 – Структурная схема системы управления термопластавтоматом [10]
Условные обозначения: M1, M2 – электродвигатели; Z1…Z4 – нагревательные элементы; R, S, T – фазы напряжения; N – нейтраль; PE – заземление; t1 …t4 – температура в зонах нагрева; DO, DI – дискретные входы и выходы [10].
Предложенный вариант модернизации СУТ внедрён пока только на двух машиностроительных предприятиях: ОАО Тульский оружейный завод
и ОАО Тульский машиностроительный завод им. Рябикова
. Почти двухлетний срок эксплуатации подтвердил состоятельность выбранных инженерных решений, что позволило достичь:
Кроме этого, конфигурация аппаратно-программных средств СУТ позволяет в случае модернизации в кратчайшие сроки адаптироваться к особенностям оборудования практически любой гидравлической машины для литья под давлением, что даёт реальный шанс для тиражирования разработанной системы на аналогичных производствах и, как следствие, позволяет добиться экономии денежных средств.
Выводы
Магистерская работа посвещенна повышению качества обработки за счет модернизации системы управления токарного станка модели 16К20Т1. При написании данного реферата магистерская работа еще не завершена. Окончательное завершение: июнь 2018 года. Полный текст работы и материалы по теме могут быть получены у автора или его руководителя после указанной даты.
Список источников
- Бобров З.Ф. Основы теории резания металлов / З.Ф. Бобров. - М.: Машиностроение, 1975. - 344 с.
- Грановский Г.И. Резание металлов / Г.И. Грановский, В.Г. Грановский. - М.: Высшая школа, 1985. – 304 с.
- Основы автоматизации и управления технологическими процессами в машиностроении / Под ред. В.Ц. Зориктуева. - Уфа: Уфимск. гос. авиац. техн. ун-т, 2000. - 406 с.
- Рубенштейн С.А. Основы учения о резании металлов и режущий инструмент / С.А. Рубинштейн [и др.]. – М.: Машиностроение, 1968. – 386 с.
- KazouT., H. O. Wang. Fuzzy control systems design and analysis. JohnWiley&Sons, Inc, 2001. 303 p.
- Зориктуев В.Ц. Система автоматического управления режимами резания на основе нечеткой логики / В.Ц . Зориктуев, Р.Р. Шангареев. - Уфа: УГАТУ, 2010. - 8 с.
- Васильев С.В. ЭДС и температура резания / С.В. Васильев // Станки и инструмент, 1980, №10. – C. 20-22.
- Остафьев В.А. Адаптивная система управления / В.А Остафьев, В.В. Шевченко, Г.С. Тымчик // Механизация и автоматизация управления. – Киев, №1, 1983. – С. 18-20.
- Шарабура С.Н. Система адаптивного управления процессом обработки деталей на станках с ЧПУ / С.Н. Шарабура, В.В. Шевченко // Современные научные исследования и инновации. 2014. – № 6. Ч. 1.
- Деркач А.Д. Примеры решений на базе сенсорных панелей Weintek для АСУ ТП и встраиваемых систем / А.Д. Деркач, Р.В, Камалиев. В.Н. Маценко // Современные технологии автоматизации. – 2014. – № 3.