Реферат по теме выпускной работы
Содержание
- Введение
- 1. Актуальность темы
- 2. Цель проектирования. Требования к системе автоматизации ленточного конвейера
- 3. Обзор исследований и разработок
- 3.1 Аппаратура автоматизации конвейерного транспорта шахты
- 3.2 Функции устройства автоматического управления ленточным конвейером технологического процесса транспорта шахты
- 3.3 Структурная схема устройства автоматической стабилизации нагрузки на ленточный конвейер
- 3.4 Обеспечение безопасной эксплуатации устройства автоматизации
- Вывод
- Список источников
Введение
В связи с тяжелыми условиями производства к большинству технических средств горной автоматики предъявляются требования повышенной надёжности, защищённости в условиях влажности, запылённости, вибраций и, главным образом, искро– и взрывобезопасности.
Задачами автоматизации являются обеспечение высокой эффективности производства, безопасности работы за счёт автоматического контроля основных параметров оборудования и опасных факторов (газа, отсутствие проветривания), предупреждение опасных режимов работы оборудования и персонала, автоматические сигнализация, блокировки, регулирование и управление.
Эффективность внедрения автоматизации зависит от поточности операций в технологии производства, наличия комплексной механизации, правильной эксплуатации аппаратуры и других компонентов.
Основным средством доставки грузов на современных горнодобывающих предприятиях является конвейерный транспорт. Ленточные конвейеры эффективно заменяют локомотивную и канатную откатку, что обусловлено такими их преимуществами, как непрерывность, широкие возможности для автоматизации, возможность транспортирования грузов в наклонных выработках, простота наращивания и разветвления линии, относительная безопасность.
1. Актуальность темы
Основной особенностью конвейерного транспорта как объекта управления является высокая неравномерность грузопотока, вызванная тем, что конвейерная линия по своему технологическому назначению является транспортным объектом, обслуживающим очистной и подготовительный забой. А технологические паузы в работе механизмов (аварийная остановка лавы, периодические изменения скорости перемещения комбайна вдоль лавы и т.д.) являются причиной неравномерного грузопотока. Неравномерность поступления груза ведет к нерациональному использованию мощности привода (при недогрузке), а также чрезмерному износу тягового органа и снижению надежности АД (при перегрузе) [2].
В настоящее время существует 2 способа уменьшения неравномерности грузопотока: регулирование частоты вращения приводного электродвигателя конвейера и применение промежуточных накопительных бункеров.
Грузопоток из лавы не является постоянной величиной, вследствие чего значительную часть времени конвейер работает с неполной загрузкой. Мощность приводных двигателей конвейеров достигает сотен киловатт, поэтому улучшение энергетических показателей привода позволит уменьшить расходы на электроэнергию. Для решения этой задачи целесообразно регулировать скорость движения ленты в зависимости от грузопотока[ 14].
Существуют два основных способа измерения массы грузопотока– это тензовесы и весы с применением ультразвукового устройства измерения.
Ультразвуковое устройство измеряет объемную производительность циклически с частотой питающей сети. Производительность измеряется только во время движения ленты с номинальной скоростью. Ультразвуковой импульс, направленный в сторону ленты, что движется, отражается от поверхности материала и направляется в приемный преобразователь. Приемный преобразователь формирует электрический импульс, который направляется в блок сравнения. В блоке сравнения сравнивается время посылки импульса со временем его возвращения, и вырабатывается электрический импульс, пропорциональный по величине времени прохождения ультразвуковым импульсом прямого и обратного пути[5].
2. Цель и задачи исследования, планируемые результаты
Целью магистерской работы является повышение эффективности работы ленточного конвейера путем обоснования алгоритма управления и разработки системы автоматизации с устройством автоматического управления конвейером.
Требования к системе автоматизации ленточного конвейера следующие:
- запуск и останов конвейера;
- контроль технологических параметров и режимов работы ленточного конвейера;
- автоматическая защита ленточного конвейера и его приводного электродвигателя при отклонении текущих значений технологических параметров от заданных или нарушении режима работы конвейера;
- автоматическое регулирование режима работы ленточного конвейера в зависимости от грузопотока;
- передача данных в компьютер системы автоматизации ленточного конвейера (верхний уровень управления) для хранения информации и визуализации состояния режимов работы конвейера;
- прием команд управления от промышленного компьютера системы автоматизации;
- конструктивное исполнение и
схемное решение технических средств системы автоматизации должны
соответствовать требованиям
Правил изготовления взрывозащищенного и рудничного электрооборудования
– иметь вид взрывозащитывзрывонепроницаемая оболочка
иискробезопасная электрическая цепь
, а монтироваться и эксплуатироваться в соответствии сПравилами технической эксплуатации угольных и сланцевых шахт
[6].
3. Обзор исследований и разработок
Анализ ленточного конвейера шахты как объекта автоматизации.
Технологический процесс транспорта горного предприятия осуществляется с помощью конвейерного и рельсового транспорта.
Процесс конвейерного транспорта шахты – это технологический процесс перемещения горной массы, материалов, а в некоторых случаях и людей с помощью конвейеров по горным выработкам[ 5,14] .
На шахтах для конвейерного транспорта применяются ленточные и скребковые конвейера. Объектом автоматизации в магистерской диссертации является ленточный конвейер в составе конвейерной линии. Ленточный конвейер — транспортирующее устройство непрерывного действия с объединённым грузонесущим и тяговым органом в виде замкнутой гибкой ленты. Лента приводится в движение силой трения между ней и приводным барабаном; опирается по всей длине на стационарные роликоопоры. Общий вид шахтного ленточного конвейера приведен на рисунке 1.
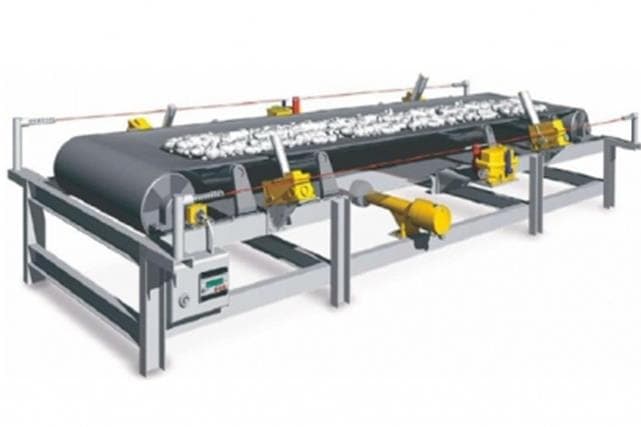
Рисунок 1. Общий вид шахтного ленточного конвейера
Конвейерные линии характеризуются значительной протяженностью (десятки километров) и разветвленность транспортных магистралей, изменяющих со временем свои параметры: длину, топологию и т.п. В условиях шахт конвейерная линия может быть не разветвленной и разветвленной. Под неразветвленной конвейерной линией понимают однопоточную линию, в которой груз на каждый конвейер поступает только с одного предыдущего конвейера, а под разветвленной – многопоточную линию, состоящую из ответвлений и сборной части. Для разветвленных конвейерных линий требуется согласование режимов работы основных – магистральных конвейеров с участковыми конвейерами[3] .
На крупных угольных шахтах доставка угля от очистных забоев до скипового подъема осуществляется по многопоточной линии транспорта, состоящей из участковых конвейерных линий и сборных конвейеров – магистральных конвейерных линий. Участковая ленточная конвейерная линия обеспечивает транспортирование угля от очистного забоя до места перегрузки на магистральную конвейерную линию. Как правило перегрузка осуществляется через накопительный бункер.В настоящее время почти все ленточные конвейерные линии на шахтах автоматизированы. Основным видом управления является автоматизированное управление, техническая сущность которого заключается в централизации управления процессами пуска – останова конвейеров в линии, при обеспечении автоматической защиты от развития аварии в случае возникновении аварийных ситуаций[9] .
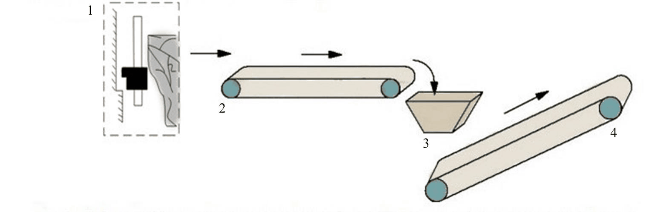
Рисунок
2 –Технологическая схема многопоточной линии транспорта угля
от очистного
забоя
(анимация: 4 кадров, 125 килобайт)
(1– очистной забой, 2
– участковая конвейерная линия, 3
– бункер, 4–магистральная конвейерная линия)
3.1 Аппаратура автоматизации конвейерного транспорта шахты
Для автоматизации ленточных конвейерных линий используют следующую комплексную аппаратуру:
–комплекс автоматизированного
управления конвейерами АУК.1М. Комплекс
предназначен для управления и контроля работы стационарных и
полустационарных неразветвленных конвейерных линий;
–
система
автоматизированного управления конвейерными линиями САУКЛ. Система
автоматизированного управления разветвленными конвейерными линиями
САУКЛ предназначена для централизованного автоматизированного
управления и контроля работы разветвленными и неразветвленными
конвейерными линиями, состоящие из ленточных конвейеров,
предназначенных для транспортирования груза и перевозки людей, с числом
конвейеров управляемых через один комплект АПУ и АЛС до 60 единиц, и
неограниченным числом маршрутов и
централизованного или местного
автоматизированного управления и контроля работы отдельными
конвейерами, входящими или не входящими в состав конвейерной линии;
–
телеуправления и контроля состояния сопутствующим вспомогательным
оборудованием (типа шибер
,
перегружатель
,
питатель
);
автоматической регистрации и сохранения информации о работе конвейеров
и сопутствующего оборудования, командах управления и настройках,
защитных отключениях и блокировках [8]
.
3.2 Функции устройства автоматического управления ленточным конвейером технологического процесса транспорта шахты
Устройство автоматического
управления должно выполнять следующие функции:
–
пуск ленточного конвейера путем включения магнитного пускателя
приводного электродвигателя конвейера;
–
останов ленточного конвейера
путем отключения магнитного пускателя приводного электродвигателя
конвейера;
–
контроль скорости ленты;
–
контроль схода ленты с роликоопор конвейера;
–
контроль заштыбовки
места перегрузки транспортируемого материала на последующий конвейер
или в приёмный бункер;
–
контроль частоты вращения приводного барабана;
–
контроль аварийного уровня загрузки приемной емкости конвейера;
–
контроль наличия пожароопасности;
–
управление скоростью ленты;
–
контроль крутящегося момента на валу приводного электродвигателя;
–
защитное отключение конвейера при снижении скорости ленты более 25%
от номинального значения в не зарегулированным режиме работы путем
отключения магнитного пускателя приводного электродвигателя конвейера;
–
защитное отключение конвейера при пробуксовки ленты в не
зарегулированном режиме относительно приводного барабана путем
отключения магнитного пускателя приводного электродвигателя конвейера;
–
защитное отключение конвейера при сходе ленты с роликоопор конвейера
путем отключения магнитного пускателя приводного электродвигателя
конвейера;
–
защитное отключение конвейера при заштыбовки места перегрузки
транспортируемого материала на последующий конвейер или в приёмный
бункер путем отключения магнитного пускателя приводного
электродвигателя конвейера;
–
защитное отключение конвейера при аварийном уровне загрузки приемной
емкости конвейера путем отключения магнитного пускателя приводного
электродвигателя конвейера;
–
защитное отключение конвейера при наличии пожароопасности путем
отключения магнитного пускателя приводного электродвигателя конвейера;
–
защитное отключение конвейера при перегрузке ленты путем отключения
магнитного пускателя приводного электродвигателя конвейера;
–
индикация состояния конвейера (включен, выключен);
–
индикация причины останова конвейера:
а) оперативный останов;
б) останов по причине при снижении скорости ленты;
в) останов по
причине схода ленты с роликоопор конвейера;
г) останов по причине заштыбовки места перегрузки транспортируемого
материала на последующий конвейер или в приёмный бункер;
д) останов по причине аварийного уровня загрузки приемной емкости
конвейера;
е) останов по причине наличия пожароопасности;
ё) останов по причине перегрузки ленты
- передача данных о состоянии конвейера и причин остановки в
промышленный компьютер автоматизированного рабочего пульта диспетчера
на центральный диспетчерский пульт шахты или на пульт транспортного
диспетчера шахты[
4,13]
.
3.3 Структурная схема устройства автоматической стабилизации нагрузки на ленточный конвейер
Структурная схема устройства автоматической стабилизации нагрузки на ленточный конвейер приведена на рисунке 2.
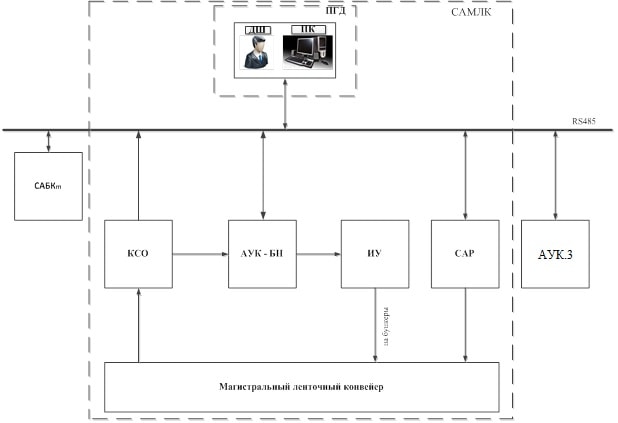
Рисунок 2. Система автоматизации магистрального ленточного конвейера
На рисунке 2 обозначено: КСО – комплекс средств отбора информации: датчики, преобразователи, устройства контроля; ИУ – исполнительные устройства; САР – система автоматического регулирования частоты вращения приводного электродвигателя конвейера; ДШ – диспетчер шахты, ПК – промышленный компьютер; ПГД – пульт горного диспетчера; САБК – система автоматизации бункером конвейера; АУК.3 – комплекс автоматизированного управления конвейерами; САМЛК – система автоматизации магистрального ленточного конвейера.
Структура системы АСУ ТП двухуровневая. На верхнем уровне осуществляется обмен, контроль, хранение и анализ информации о магистральном ленточном конвейере. Для обеспечения непрерывности процесса конвейера при необходимости формируются управляющие команды на пуск, остановку или регулирование режимов работы, визуализация процесса работы конвейера на дисплее промышленного компьютера. Функции верхнего уровня выполняет автоматизированное рабочее место диспетчера, которое включает в себя блок преобразования интерфейса для обмена информацией между нижним уровнем управления и промышленным компьютером. Визуальный контроль за ходом технологического процесса осуществляет диспетчер шахты на дисплее промышленного компьютера[ 7,10] .
На нижнем уровне управления расположено n–ое количество систем автоматизации ленточного конвейера. Обмен информацией между нижним и верхним уровнями обеспечивает промышленная сеть (например, Profibus).
Структурная схема устройства автоматической стабилизации нагрузки на ленточный конвейер приведена на рисунке 3.
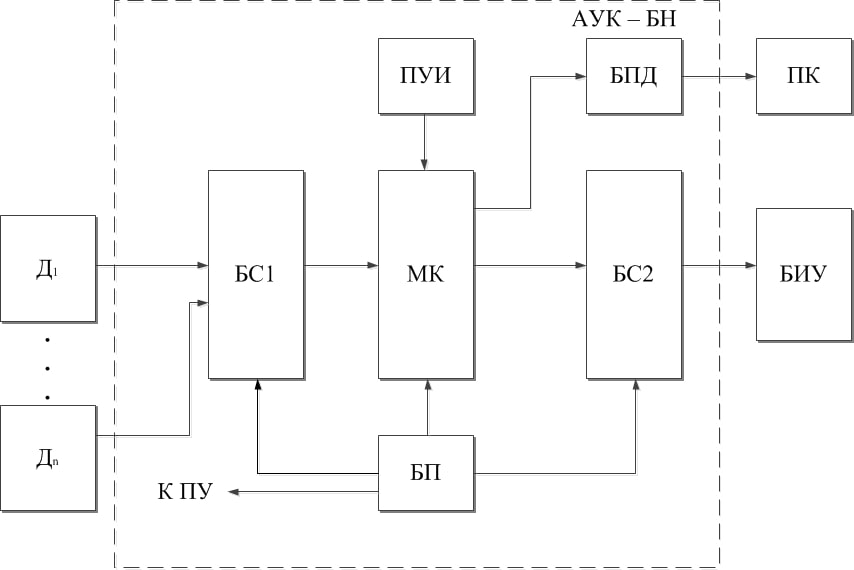
Рисунок 3. Структурная схема устройства автоматической стабилизации нагрузки на ленточный конвейер типа АУК – БН
На рисунке 3 обозначено: МК – микроконтроллер; Д – датчики; БС1 – блок согласования входных сигналов с МК; БС2 – блок согласования выходных сигналов с исполнительным устройством; ПУИ – пульт управления индикаций; БПД – блок передачи данных; БП – блок питания; ПК- промышленный компьютер; БИУ – блок исполнительных устройств.
Блок БС1 предназначен для:
–
согласования уровня напряжения, коммутируемого дискретными датчиками,
с рабочим напряжением микроконтроллера устройства;
–
согласования входных сигналов от датчиков и защиты микроконтроллера
от возможных повреждений линий связи.
Блок БС1 состоит из 2 – х субблоков: субблок ввода дискретных сигналов СбД, и субблока ввода аналоговых сигналов СбА.
Субблок СбД предназначен для согласования входных сигналов от дискретных датчиков с блоком микроконтроллера МК, а также для предотвращения возникновения воспламенения внутри устройства управления АУК – БН. Субблок СбА предназначен для согласования входных сигналов от аналоговых датчиков с блоком микроконтроллера МК.
Блок микроконтроллера МК представлен микроконтроллером серии AVR типа ATmega16, основной функцией которого является обработка входных сигналов от датчиков, тумблеров и кнопок, а также вывод согласно алгоритму управления соответствующие управляющие команды.
Блок БС2 предназначен для:
–
согласования уровня напряжения, коммутируемого дискретными или
аналоговыми датчиками, с рабочим напряжением исполнительных устройств
системы автоматизации;
–
согласования выходных сигналов микроконтроллера и защиты
микроконтроллера от возможных повреждений линий связи. Блок ПУИ
предназначен для индикация технологических событий с помощью
светодиодов: скорость конвейера, сход, проскальзывание, скорость ленты,
пожароопасность, заштыбовка конвейерной линии.
3.4 Обеспечение безопасной эксплуатации устройства автоматизации
Устройство автоматического регулирования погонной нагрузки на конвейерную ленту предназначено для обеспечения выработки управляющего действия на пускатели приводов ленточного конвейера и станции натяжения при пуске и в процессе работы конвейерной линии. Управляющий сигнал воспроизводится с сигналов от датчиков контроля скорости ленты, схода ленты, нагрузки транспортируемого материала, частоты вращения приводного барабана, пожароопасности, натяжении ленты, крутящего момента на валу приводного электродвигателя, а также сигнала с АУК – БН на пуск и стоп конвейера. Устройство обеспечивает защиту ленточного конвейера от недопустимых режимов работы. Устройство автоматического регулирования погонной нагрузки на конвейерную ленту состоит в зависимости от количества ленточных конвейеров в линии. Устройство может быть установлено на один и несколько конвейеров[ 12] .
Выходные цепи управления и связи устройства имеют искробезопасное выполнения.
Мероприятия по обеспечению безопасной эксплуатации устройства
автоматизации регламентируются действующими Правилами
безопасности в угольных шахтах
и
Правилами
технической эксплуатации электроустановок
.
Для обеспечения надежной и безаварийной работы конвейера с
разработанным устройством необходимо выполнять следующие мероприятия:
–
устройство перед спуском в шахту должен подвергаться контрольному
осмотру ответственными лицами;
–обслуживание, ремонт и монтаж данного устройства должны
производиться
только лицами, имеющими удостоверения на право производства работ в
электроустановках напряжением до 1000 В;
–
устройство должно подвергаться периодическому осмотру;
–
ремонт и монтаж устройства должны производиться в соответствии с
«Инструкцией по безопасному ведению работ в подземных
электроустановках» в присутствии лица технического надзора;
–
ежесменно должны проверяться качество заземления и целостность
корпуса устройства. Запрещается эксплуатация устройства, корпус
которого имеет трещину, вмятины, царапины, неплотное прилегание крышки
и другие дефекты, ведущие к потери взрывозащищенности и
взрывонепроницаемости данного устройства;
–
в кабельных вводах кабель должен быть уплотнен специальными
эластичными прокладками. Незадействованные введения должны быть закрыты
специальными заглушками. Запрещается производить уплотнение кабеля
изоляционной лентой, сырой резиной, обрезками оболочки гибких резиновых
кабелей;
–
запрещается делать какие – либо переключения в схеме
устройства,
шунтирование или отключение отдельных элементов и блоков;
–
категорически запрещается нарушать электромеханические блокировки
данного устройства и включать его при открытых крышках:
- лицами, работающими на машинах и механизмах, а также дежурными электрослесарями участка – ежесменно;
- механиком участка или его заместителем – еженедельно с занесением результатов в оперативный журнал участка;
- главным энергетиком (главным механиком) шахты или назначенными им лицами – не реже одного раза в З месяца с занесением в книгу;
- по графику, утвержденным
главным инженером шахты, специальной
группой электрослесарей шахты под контролем главного энергетика
(главного механика) шахты или лица, им назначенного, устройство должно
подвергаться ревизии и проверке его взрывобезопасности в соответствии с
Инструкцией по осмотру и ревизии рудничного взрывобезопасного электрооборудования
с занесением результатов вКнигу регистрации состояния электрооборудования и заземления
[ 1,14] .
Для обеспечения безопасной эксплуатации ленточных конвейеров обязательным условием является прямолинейность выработки по всей длине става конвейера и отсутствие участков с резким изменением угла ее наклона в вертикальной плоскости.
Выводы
В магистерской диссертации выполнен анализ работы шахтного ленточного конвейера как объект автоматизации и сформулированы требования к устройству автоматического управления ленточным конвейером.
Предложена структура системы автоматизации ленточным конвейером, которая имеет два уровня управления: верхний – уровень главного диспетчера шахты и нижний уровень ленточного конвейера. На верхнем уровне предусмотрена компьютеризированная промышленная рабочая станция, а на нижнем – новое устройство, разработанное в работе – устройство автоматической стабилизации нагрузки на ленточный конвейер типа АУК – БН.
При разработке устройства АУК–БН были выполнены все этапы проектирования: сформулированы функции устройства, разработан алгоритм автоматического управления ленточным конвейером, разработаны структурные схемы системы автоматизации и устройства АУК – БН, разработана принципиальная электрическая схема устройства АУК – БН. Устройство АУК – БН выполнено на базе микропроцессорной техники.
Таким образом, за счет применения разрабатываемого устройства, можно достичь не только высокого экономического эффекта, но и существенно улучшить условия труда рабочих, повысить безопасность, а самое главное – повышаются технико – экономические показатели предприятия в целом, что приводит к повышению уровня жизни работников этого предприятия.
Во время написания данного реферата магистерская работа еще не завершена. Окончательное завершение: июнь 2018 года. Полный текст работы и материалы по теме могут быть получены у автора или его руководителя после указанной даты.
Список источников
- НПАОП 10.0-1.01-10. Правила безпеки у вугільних шахтах. Наказ Державного комітету України з промислової безпеки, охорони праці та гірничого нагляду №62 від 23.03.2010. – 150с.
- Пейсаховича Г.Я. Подземный транспорт шахт и рудников/ Под общей ред. Г.Я. Пейсаховича, И.П. Ремизова. –– М.: Недра, 1985. – 565 с.
- Груба В. И. Технические средства автоматизации в горной промышленности. – В. И. Груба, Э. К. Никулин, А. С. Оголобченко – К.: ИСМО, 1998.– 373 с.
- Стадник Н.И. Справочник по автоматизации шахтного конвейерного транспорта / Н. И. Стадник, В. Г. Ильюшенко, С. И. Егоров и др. – К.: Техника, 1992. – 438с.
- Иванов А.А. Автоматизация подземных горных работ/ Под ред. проф. А. А. Иванова. – К.: Вища школа, 1987. – 328с.
- Бедняк Г.И. Автоматизация производства на угольных шахтах/ Г. И. Бедняк, В. А. Ульшин, В. П. Довженко и др. – К.: Техника, 1989. – 272с.
- Хананов
Д.В. Аналіз процесів нагріву конвеєрної стрічки
при повній пробуксовці приводного барабана шахтного конвеєра в
аварійному режимі роботи. Наукові праці Донецького національного
технічного університету. Донецьк: ДВНЗ
ДонНТУ
, 2009. – 256–265c. - Толпежников Л.И. Автоматическое управление процессами шахт и рудников. –М.: Недра, 1985. –352 с.
- Овсянников Ю.А. Автоматизация подземного оборудования/Овсянников Ю.А., Кораблев А.А., Топорков А.А. : Справочник рабочего. - М.: Недра, 1990. – 287с.
- Жуйков В.А. Схемотехніка електронних систем: Підручник в двох томах/ Жуйков В.А., Бойко В.І., Зорі А.А., Співак В.М.. – К.: Аверс, 2002. - 772с. Том I. Аналогова схемотехніка та імпульсні устрої / Жуйков В.А., Бойко В.І., Зорі
- Гутников В. С. Интегральная электроника в измерительных устройствах. – Л.: Энергоатомиздат, 1988. – 304с.
- Петков О. Н. Разработка и исследование системы автоматического управления скоростью ленточного конвейера по входному грузопотоку / Диссертация на соискание ученой степени кандидата технических наук. – М.: Московский Ордена Трудового Красного Знамени Горный Институт, 1984. – 143с.
- Шахмейстер Л. Г., Дмитриев В. Г. Вероятностные методы расчета транспортирующих машин. – М.: Машиностроение, 1983. – 256с.
- Дмитриева В. В., Певзнер Л. Д. Автоматическая стабилизация погонной нагрузки ленточного конвейера: Отдельные статьи Горного информационно-аналитического бюллютеня. – 2004. – № 12. – М.: Издательство Московского государственного горного университета. – 25с.
- Папоян Р. Л. Повышение эффективности использования шахтных конвейерных линий автоматическим, регулированием скорости и определением грузопотоков. Кандидатская диссертация. – М., 1967. – 213с.