Обоснование структуры электронной системы вибродиагностики добычного комбайна
Содержание
- Введение
- 1. Цель и задачи исследования, планируемые результаты
- 2. Анализ Объекта и постановка задачи
- 3. Техническое задание на разработку микропроцессорной системы вибродиагностики добычного комбайна
- 4. Проэктирование микропроцессорной системы вибродиагностики добычного камбайна
- 5. Разработка конструкции, технология изготовления и наладка микропроцессорной вибродиагностики добычного камбайна
- Выводы
- Список источников
Введение
Каменный уголь занимает по запасам и добыче первое место в мире среди полезных ископаемых. Каждый год в мире добывают свыше 4,5 млрд. т. каменного и бурого угля. По прогнозам в новом столетии его доля в мировом энергетическом балансе будет расти.
Достижения темпов возможно только при надежности техники, что позволяет работать без аварий. Как показывает опыт эксплуатации проходческих комбайнов часто простои машин вызывают поломки редукторов, выходят из строя подшипники редукторов и электродвигатели. Это вызвало возможным технологическими нарушениями изготовления и эксплуатационных правил использования машин. Иногда простои из-за значимых причин составляют от 20 до 25% рабочего времени комбайнов. Поэтому, создание приспособлений определяющие возникновение предаварийных ситуаций, есть первоочередной задачей.
Одним из критериев возможного возникновения ухудшения технического состояния привода, есть возрастание вибраций механизмов, что приводит к выводу из строя машин. Техническое состояние машины может быть определено с помощью анализа параметров, характеризующих ее вибрацию. Создание приспособления определенного по уровням вибрации возможность дальнейшей эксплуатации комбайнов, есть актуальной задачей.
Данной проблемой занимаются ученые странах СНГ и за рубежом. “Автоматгормаш” разработал приспособление автоматической диагностики горных машин при пуско-наладчиских работах и ремонтным путем измерений и анализа вибрации для конвейеров [3]. В Сионском научно-исследовательском институте предлагается решать данную проблему определенным комплексным показателем спектральных характеристик вибросигнала [4].
Основа и теоретические предпосылки решения данной задачи есть. Необходимо создать приспособление, которое позволяет, анализировать параметры вибросигнала, определять техническое состояние машины и возможность дальнейшего ее использования.
1. Цель и задачи исследования, планируемые результаты
Цель работы - создать микропроцессорную систему вибродиагностикидобычного комбайна, надежно работающей в сложных условиях эксплуатации, которая позволит контролировать вибрации и выявить предаварийные ситуации привода резки, чем повысить надежность и производительность работы комбайна.
Задачи, решены разработкой:
-автоматизация процесса диагностики проходческого комбайна,
-сокращение расходов на техническое обслуживание и ремонт за счет выявления дефектов на ранних стадиях их развития прогнозирование технического состояния привода резки,
-повышение качества налаживания и регулирования за счет предоставления ремонтному персоналу информации о текущих значениях контролируемых параметров,
-повышение безопасности работы обслуживающего персонала.
Полученные результаты - спроектирована микропроцессорная система вибродиагностики привода резки проходческого комбайна. Разработаны структурные, принципиальные схемы, печатные платы этой системы, а также программное обеспечение. Блоки системы реализованы на современной элементной базе.[5]
2. Анализ Объекта и постановка задачи
Проходческий комбайн П-160 назначенный для проведения горизонтальных и наклонных, до ±10 %, подготовительных выработок сечением от 9 до 33 м2 в проходке по породным, смешанным и угольным забоям при крепости пород до 100 МПа при одном сжатии, и абразивности до 15 мг в шахтах, опасных по газу и пыли. Форма выработки каждая, с плоским грунтом.
Продуктивность и качество работы проходческих комбайнов в основном зависит от качества и умения управлять комбайном в процессе его работы. Существенное влияние на эффективность управления комбайнами избирательного действия составляют следующие факторы: сильное пылеобразование; невозможность достичь стабильности в регулировании нагрузки исполнительного органа и оградить от перенагрузки; недопустимые отклонения направления проведенной выработки от заданного вследствии существующих грубых способов контроля, которые приводят к значительным перебоям при обработке забоя выработки заданного сечения и до необходимости ввести исправления.
Существующие системы управления проходческими комбайнами дают возможность эксплуатировать последние в режимах, которые влияют быстрому износу его отдельных узлов и, так же, комбайна в целом. Для ускорения ремонта необходима очень высокая квалификация обслуживающего персонала, которые не всегда возможны для шахтных условий. В данное время создаются устройства автоматизации обеспечивающие диагностику исправности станции управления и основных частей проходческого комбайна. Это возможность ускорения поиска неисправности, распознавание предаварийных и аварийных ситуаций.[6]
Способы диагностики установленные на таких проходческих комплексах не обеспечивает диагностику поводов резки. Повод резки проходческого комбайна представляет собой последовательное соединение электродвигателя и редуктора и как объект диагностики характеризуется этой специфической особенностью, который непосредственно в шахтных условиях, не всегда ремонтируется. Для осуществления или ремонта замены нужна выдача их на поверхность, что есть сложным и трудоемким процессом. Актуальной задачей есть отличие предаварийных ситуаций поломок редуктора и электродвигателя. Одним из индикаторов есть повышение уровня вибрации. Для измерения параметров вибрации используются вибродатчики. Эти датчики возможно ставить на опорные муфты между электродвигателем и редуктором. Качество монтажа соединительных муфт и их техническое состоянии, которое укрепляется в процессе эксплуатации, во многом обозначает общее техническое состояние агрегата.
Для диагностики состояния механических передач наибольшее распространение получил метод вибродиагностики. Данная диагностика необходима для проходческого комбайна, потому что будет возможность установить термины износа подшипников, которые повышают продуктивность и качество работы комбайна.
Разрабатывающая микропроцессорная система вибродиагностики проходческого комбайна П-160 предназначена для контроля общей вибрации привода резки и выявления в результате диагностики таких дефектов оборудования: дисбаланс масс ротора, нарушения воздушного зазора в подшипниках, несовместимость приводного электродвигателя и редуктора исполнительного органа. Общая структура МШС содержит в себе обработку сигнала с вибродатчика, вывод на дисплей информацию о диагностике, отключения электродвигателя при недопустимых уровнях вибрации и режимах работы привода.[9]
По полученным результатам диагностики можно далее выявить причины возникновения деффектов в оборудовании. Например: причины возникновения дисбаланса в оборудовании могут иметь разную природу, быть в результате многих особенностей конструкции и эксплуатации. Их возможно свести в несколько основных групп:
- дефект изготовления ротора его элементов на заводе, на ремонтном предприятии, недостаточный выходной контроль предприятия - изготовление оборудования, удары во время перевозок, плохие условия хранения,
- неправильная сборка оборудования при первичном или монтаже после сделанного ремонта,
- наличие на роторе изношенных, поломанных, дефектных, отсутствующих, недостаточно крепко закрепленных и т.д. деталей и узлов,
- результат влияния параметров технологических процессов и особенностей эксплуатации данного оборудования, которые приводят к неравномерному нагреванию и искривлению роторов.
Выявление предаварийных ситуаций главный показатель разрабатывающей микропроцессорной системы, которая обеспечивает эффективность функционирования проходческого комбайна.
3. Техническое задание на разработку микропроцессорной системы вибродиагностики добычного комбайна
Проходческий комбайн П-160, для которого разрабатывается данная микропропроцесорна система, предназначен для проведения горизонтальных и наклонных до ± 10%, подготовительных выработок сечением от 9 до 33 м2, в проходке по породным, смешанных и угольных забоях при прочности пород до 100 МПа при одном сжатия и абразивности до 15 мг в шахтах, опасных по газу и пыли. Форма выработок любая, с плоским грунтом.
Объектами диагностирования в проходческий комбайн является редуктор исполнительного органа, электродвигатель и муфта. Технические характеристики объектов диагностирования:
-частотный диапазон изменения вибрации (без учета вибрации подшипников) от 5 до 200 Гц [7]
-диапазон изменения СКУ Виброскорость в линейном частотном спектре (от технического состояния "Норма" до "Авария") от 0.4 до 20 мм / с.
Микропроцессорная система состоит из блока вибропреобразователя, бло-ку диагностики, блока обработки информации и кабельных перемычек. Такой состав позволяет иметь функционально законченные узлы и до минимума сократить кабельные связи. Каждый блок расположен на отдельной плате с клемниками.
Блок вибропреобразователя предназначен для преобразования механических ко-Ливане поводу резки в электрический сигнал и включает в себя пьезоэлектрический измерительный Вибродатчик и предусилителя.
Блок диагностики предназначен для усиления, фильтрации и обработки выходных сигналов с вибропреобразователя.
Блок обработки информации включает в себя микропроцессорный узел и три светодиода. Блок предназначен для обработки информации, поступающей из блока диагностики; реализации алгоритмов диагностирования; формирование массива информации о техническом состоянии объекта; выдачи информации на индикацию и передачу ее контроллеру электронной системы управления проходческим комбайном.
Кабельные перемычки предназначены для соединения блока диагностики с вибропреобразователями. В кабельных перемычках используется специальный вибрационный кабель.
Микропроцессорную систему вибродиагностики проходческого комбайна необходимо размещать в взрывобезопасном корпусе с электронной системой управления проходческим комбайном, причем каждая печатная плата по-должна еще быть в отдельном пластмассовом корпусе. Минимальные размеры корпусов, не более 300х150х250 мм.
Конструктивное оформление изделия должно соответствовать требованиям эстетики, эргономики и инженерной психологии. Уровень художественно-конструктивного решения должен соответствовать лучшим современным отечественным и зарубежным образцам.
При выборе марок и сортиментов материалов необходимо руководствоваться требованиями снижения материалоемкости изделия и снижения расхода остродефицитных материалов.[1]
4. Проэктирование микропроцессорной системы вибродиагностики добычного камбайна
Объектом проектирования в данном дипломном проекте является микропроцессорная система вибродиагностики проходческого комбайна П-160.
Для измерения механических вибраций применяются вибродатчики. Вибродатчики можно разделить на генераторные и параметрические. В отдельную группу можно отнести сравнительно недавно появились, лазерные вибродатчики. Параметрические, в свою очередь, делятся на индуктивные и емкостные.
Основными недостатками параметрических датчиков являются:
- необходимость в дополнительном источнике питания;
- необходимость первоначальной установки или зазора калибровки;
- более сложная схема;
- возникновение параметрических шумов при малых уровнях сигнала.
К генераторных датчиков относятся пьезоэлектрические. Это наиболее распространенные на сегодняшний день датчики. К их недостаткам можно отнести:
- невозможность проведения бесконтактных измерений;
- невозможность измерения постоянной составляющей вибрации.
Достоинства генераторных датчиков по сравнению с параметрическими вибродатчик: нет необходимости в дополнительном источнике питания, отсутствие первоначальной установки зазора, более простая схема, отсутствие шумов при малых уровнях сигнала.
Принцип действия лазерного вибродатчик основан на измерении сдвига частоты лазерного излучения, рассеянного движущимся с определенной скоростью (эффект Доплера).
Достоинства лазерного виброизмерителей:
- бесконтактный измерение; [14]
- нет необходимости подготавливать поверхность для измерений;
- широкий диапазон частотного спектра измеряемого сигнала;
- возможность измерения вибрации поверхностей с высокой температурой.
Недостатки лазерных виброизмерителей:
- высокая стоимость;
- сложность схемы;
- измерение Виброскорость.
Выходной сигнал вибродатчиков должен быть пропорционален величине вибросмещения (виброметры), Виброскорость (велосиметры) и виброускорения (акселерометры). При измерении каждой из этих величин можно получить другие. Так для виброметра при дифференцировании вибросмещения получаем виброскорость, а при двойном дифференцировании получим виброускорения. В случае велосиметра путем интегрирования выходного сигнала датчика получим сигнал пропорционален вибросмещения, а при дифференцировании - виброускорению.
Расчет фильтра верхних частот [15]
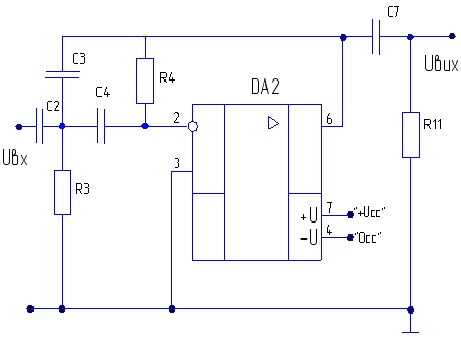
Рисунок 1 – Фильтр верхних частот
Фильтр верхних частот с много петлевой обратной связью имеет передаточную функцию следующего вида:
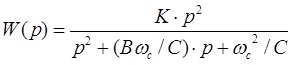
Рисунок 2 – Фильтр верхних частот с много петлевой обратной связью
где В и С нормировнные коэффициенты.
Из справочной литературы [14]: B = 1.41214; C = 1
Фильтр на ОУ DA2, показанный на рисунке 3.17, реализует функцию верхних частот второго порядка с инвертирующим коэффициентом усиления.
Частота среза фильтра 300Гц, коэффициент усиления K = 1. Выберем номинальное значение емкости С2 = С4 (близкое к значению 10 / fc мкФ). С2=10/300=0.0333 мкФ.
Вычислим значение R3 и R4 по формулам

Рисунок 3 – Вычисление резисторов R3 и R4
Круг С7R11 предназначено для исключения из сигнала постоянной составляющей. С7 выбирается преимущественно близкое к значению 10 / f мкФ. С7 = 33нФ Построим амплитудно-частотную характеристику фильтра

Рисунок 4 – Амплитудно частотная характеристика фильтра высоких частот
(анимация: 6 кадров, 10 циклов повторения, 160 килобайт)
5. Разработка конструкции, технология изготовления и наладка микропроцессорной вибродиагностики добычного камбайна
Добысные комбайны работают в сложных условиях - высокая влажность (90%), большая запыленность, температура, меняется (10 - 60 ° С). Кроме того, наличие газа метана предусматривает взрывозащищенное и искробезопасное исполнение корпусов и узлов устройств, выполнение особых требований.
В соответствии с техническим заданием микропроцессорная система вибродиагностики проходческого комбайна П-160 состоит из 4 вибропреобразователей, блока диагностики, блока обработки информации и кабельных перемычек. Каждый блок расположен на отдельной плате с клеммами для соединения.
Каждый вибропреобразователь состоит из вибродатчика и предусилителя.
Вибропреобразователи устанавливаются на подшипниковые опоры муфт между редуктором и двумя электродвигателями.
Блок вибродиагностики, располагается в пульте местном электронной системы управления проходческим комбайном.
Блок обработки информации также размещен в пульте местном.[13]
Каждый вибропреобразователь связан с блоком вибродиагностики кабельной перемычкой.
Разработка печатных плат предусматривает выбор размещения элементов принципиальной схемы по площади платы и разводку печатных объединяя проводников. Размер корпуса 110x110x50, печатная плата разрабатывается по форме корпуса.
На печатной плате блока вибродиагностики размещаются два клеммных. Эти клеммы нужны для соединения с блоками вибропреобразователей, блоком обработки информации, подключения источника питания.
Расчет размеров печатной платы выполняем с учетом размещения компонентов схемы, а также с учетом специальных полей, на которых не выполняется трассировки печатных соединений и полей закрепления печатной платы.
Размеры места размещения микросхем зависят от типа корпуса, расстояние между микросхемами определяется с учетом поля для размещения окружающих дискретных элементов.
Размеры печатной платы находим составлением всех размеров отдельных полей с учетом требований ГОСТ 10317 - 79 и рекомендованного отношение сторон.
Печатная плата должна иметь прямоугольную форму. Рекомендуемые отношение сторон 1:1, 1:3, 2:3, 2:5, но не более 3:1. Сложив размеры всех полей, руководствуясь данными [11], находим габариты платы. С учетом отношение 2:3, получаем размеры печатной платы 110 x 110 мм.
Выводы
В дипломном проекте спроектирована микропроцессорая система вибродиагностики проходческого комбайна П-160. Для этого был проведен обзор аналогов, обоснование выбора первоначальных вибропреобразователей. В качестве вибродатчиков были выбраны генераторные пьезоэлектрические акселерометры. Реализованы такие методы измерения вибрации привода резки проходческого комбайна: оценка общей вибрации электродвигателей и редуктора по СКУ Виброскорости, измерение вибрации по информативных частотах, оценка технического состояния подшипников по измерению ударных импульсов. Разработано техническое задание на проектирование системы. Проведенный расчет узлов принципиальной схемы и оценены метрологические характеристики системы. Сделан обзор различных современных цифровых интегральных схем и микроконтроллеров. Разработанная конструкция и программное обеспечение системы. Согласно ГОСТам сделана вся техническая и конструкторская документация. Спроектированная система полностью удовлетворяет требованиям поставленной к ней в техническом задании. Проектирование может считаться законченным. Систему можно изготавливать и применять на производстве.
[5]Список источников
- Журнал “Уголь Украины” №1, 2004. – 80 с
- Журнал “Уголь Украины” №2, 2004. – 80 с..
- Журнал “Уголь Украины” №3, 2004. – 80 с.
- Журнал “Современные технологии автоматизации” №7, 1999. – 80 с.
- Бауман Э. Измерение сил электрическими методами; Под ред. И.И.Смыслова. - М.: Мир, 1978. - 430 с.
- Соливанов М.Н., Фридмак А.Э., Кудряшова Ж.Ф. Качество измерений: Метрологическая справочная книга – Л: Лениздат 1987. – 290 с.
- Расчет электронных схем. Примеры и задачи. Учебн. Пособие для ВУЗов/Г.И. Изъюрова и др. М.Ж., 1987. – 332 с.
- Руденко В.С., Сенько В.И. и др. Основы промышленной электроники. – К.: Вища школа, 1985.- 400 с.
- Гутников В. С. Интегральная электроника в измерительных устройствах.- 2-е изд., перераб.и доп.-Л.: Энергоиздат. Ленинград. отд-ние, 1988.-304 с.
- Якубовский С.А., Барканов Н.А,. Кудряшов В.П. Аналоговые и цифровые интегральные микросхемы: Справочное пособие / Под ред. С.В.Якубовского. М.: Радио и связь, 1985. с. – 336 с.
- Источники электропитания радиоэлектронной аппаратуры. Справочник. Под. ред. Г.С. Найквиста. – М. Радио и связь, 1986.
- Полупроводниковые приборы: тиристоры. Справочник. Под. ред. Н.Н. Горюнова, 1983.
- Панфилов Д.И., Чепурин И.И., Миронов В.Н. и др. Электротехника в экспериментах и упражнениях: Практикум на Electronics Workbench: т. 1,2. - М.: ДОДЕКА, 2000. 288 с.
- Харинский А.А. Основы конструирования элементов радиоаппаратуры. – Л.: Энергия, - 1971. – 464 с.
- ГОСТ 2.001-70. ЕСКД. Основные положения.
- ГОСТ 2.109-73. ЕСКД. Основные требования к чертежам.
- ГОСТ 15.001-73. ЕСКД. Схема разработки и поставка продукции на производстве.
- ГОСТ 2.417-78. ЕСКД. Правила выполнения чертежей печатных плат.
- Бизнес-план инвестиционного проекта. Практическое пособие/ Под. ред. Иванниковой И.А. – М.: „Экспертное бюро” – М., 1997. – 112 с.