Обгрунтування структури електронної системи вібродіагностики видобувного комбайна
Зміст
- Вступ
- 1. Мета і завдання дослідження, та заплановані результати
- 2. Аналіз об'єкту і постановка задачі
- 3. Технічне завдання на розробку мікропроцесорної системи вібродіагностики видобувного комбайна
- 4. Проектування мікропроцесорної системи вібродіагностики видобувного камбайна
- Висновки
- Перелік посилань
Вступ
Кам'яне вугілля займає за запасами і видобутку перше місце в світі серед корисних копалин. Щороку в світі видобувають понад 4,5 млрд. Т. Кам'яного і бурого вугілля. За прогнозами в новому столітті його частка в світовому енергетичному балансі буде рости.
Досягнення темпів можливо тільки при надійності техніки, що дозволяє працювати без аварій. Як показує досвід експлуатації прохідницьких комбайнів часто простої машин викликають поломки редукторів, виходять з ладу підшипники редукторів і електродвигуни. Це викликало можливим технологічними порушеннями виготовлення і експлуатаційних правил використання машин. Іноді простої через значущих причин становлять від 20 до 25% робочого часу комбайнів. Тому, створення пристосувань визначають виникнення передаварійних ситуацій, є першочерговим завданням.
Одним з критеріїв можливого виникнення погіршення технічного стану приводу, є зростання вібрацій механізмів, що призводить до виведення з ладу машин. Технічний стан машини може бути визначено за допомогою аналізу параметрів, що характеризують її вібрацію. Створення пристосування певного за рівнями вібрації можливість подальшої експлуатації комбайнів, є актуальним завданням.
Даною проблемою займаються вчені країнах СНД і за кордоном. "Автоматгормаш" розробив пристосування автоматичної діагностики гірських машин при пуско-наладчіскіх роботах і ремонтним шляхом вимірювань і аналізу вібрації для конвеєрів [ 3 ]. У Сіонському науково-дослідному інституті пропонується вирішувати дану проблему певним комплексним показником спектральних характеристик вібрації [ 4 ].
Основа і теоретичні передумови вирішення даного завдання є. Необхідно створити пристосування, яке дозволяє, аналізувати параметри вібросигналу, визначати технічний стан машини і можливість подальшого її використання. P>
1. Мета і завдання дослідження, та заплановані результати
Мета роботи - створити мікропроцесорну систему вібродіагностікідобичного комбайна, надійно працює в складних умовах експлуатації, яка дозволить контролювати вібрації і виявити аварійні ситуації приводу різання, ніж підвищити надійність і продуктивність роботи комбайна.
Завдання, вирішені розробкою:
-автоматизація процесу діагностики прохідницького комбайна,
-cкорочення витрат на технічне обслуговування і ремонт за рахунок виявлення дефектів на ранніх стадіях їх розвитку прогнозування технічного стану приводу різання,
-підвищення якості налагодження і регулювання за рахунок надання ремонтному персоналу інформації про поточні значення контрольованих параметрів,
-підвищення безпеки роботи обслуговуючого персоналу.
Отримані результати - спроектована мікропр цессорная система вібродіагностики приводу різання прохідницького комбайна. Розроблено структурні, принципові схеми, друковані плати цієї системи, а також програмне забезпечення. Блоки системи реалізовані на сучасній елементній базі. [ 5 ]
2. Аналіз об'єкту і постановка задачі
Прохідницький комбайн П-160 призначений для проведення горизонтальних і похилих, до ± 10%, підготовчих виробок перетином від 9 до 33 м2 в проходці по породним, змішаним і вугільним вибоїв при міцності порід до 100 МПа при одному стисненні, і абразивності до 15 мг в шахтах, небезпечних за газом та пилом. Форма вироблення кожна, з плоским грунтом.
Продуктивність і якість роботи прохідницьких комбайнів в основному залежить від якості і вміння керувати комбайном в процесі його роботи. Істотний вплив на ефективність управління комбайнами вибіркової дії складають такі чинники: сильне пилоутворення; неможливість досягти стабільності в регулюванні навантаження виконавчого органу і захистити від перенавантаження; неприпустимі відхилення напрямки проведеної виробки від заданого внаслідок існуючих грубих способів контролю, які призводять до значних перебоїв при обробці вибою виробки заданого перетину і до необхідності ввести виправлення.
Існуючі системи управління прохідницькими комбайнами дають можливість експлуатувати останні в режимах, які впливають швидкого зносу його окремих вузлів і, так само, комбайна в цілому. Для прискорення ремонту необхідна дуже висока кваліфікація обслуговуючого персоналу, які не завжди можливі для шахтних умов. В даний час створюються пристрої автоматизації забезпечують діагностику справності станції управління і основних частин прохідницького комбайна. Це можливість прискорення пошуку несправності, розпізнавання передаварійних і аварійних ситуацій. [ 6 ]
Способи діагностики встановлені на таких прохідницьких комплексах не забезпечує діагностику приводів різання. Привід різання прохідницького комбайна є послідовне з'єднання електродвигуна і редуктора і як об'єкт діагностики характеризується цієї специфічної особливістю, який безпосередньо в шахтних умовах, не завжди ремонтується. Для здійснення або ремонту заміни потрібна видача їх на поверхню, що є складним і трудомістким процесом. Актуальним завданням є відмінність передаварійних ситуацій поломок редуктора і електродвигуна. Одним з індикаторів є підвищення рівня вібрації. Для вимірювання параметрів вібрації використовуються вибродатчики. Ці датчики можна встановлювати на опорні муфти між електродвигуном і редуктором. Якість монтажу з'єднувальних муфт і їх технічне стані, яке зміцнюється в процесі експлуатації, багато в чому позначає загальний технічний стан агрегату.
Для діагностики стану механічних передач найбільшого поширення набув метод вібродіагностики. Дана діагностика необхідна для прохідницького комбайна, тому що буде можливість встановити терміни зношування підшипників, які підвищують продуктивність і якість роботи комбайна.
розробляє мікропроцесорна система вібродіагностики прохідницького комбайна П-160 призначена для контролю загальної вібрації приводу різання і виявлення в результаті діагностики таких дефектів обладнання: дисбаланс мас ротора, порушення повітряного зазору в підшипниках, несумісність приводного електродвигуна і редуктора виконавчого органу. Загальна структура МШС містить в собі обробку сигналу з вібродатчика, вивід на дисплей інформацію про діагностику, відключення електродвигуна при неприпустимих рівнях вібрації і режимах роботи приводу. [ 9 ]
За отриманими результатами діагностики можна далі виявити причини виникнення дефектів в обладнанні. Наприклад: причини виникнення дисбалансу в обладнанні можуть мати різну природу, бути в результаті багатьох особливостей конструкції і експлуатації. Їх можна перекласти в кілька основних груп:
- дефект виготовлення ротора його елементів на заводі, на ремонтному підприємстві, недостатній вихідний контроль підприємства - виготовлення обладнання, удари під час перевезень, погані умови зберігання
- неправильна збірка обладнання при первинному або монтажі після зробленого ремонту,
- наявність на роторі зношених, поламаних, дефектних, відсутніх, недостатньо міцно закріплених і т.д. деталей і вузлів,
- результат впливу параметрів технологічних процесів і особливостей експлуатації даного обладнання, які призводять до нерівномірного нагрівання і викривлення роторів.
Виявлення передаварійних ситуацій головний показник розробляє мікропроцесорної системи, яка забезпечує ефективність функціонування прохідницького комбайна.
3. Технічне завдання на розробку мікропроцесорної системи вібродіагностики видобувного комбайна
Прохідницький комбайн П-160, для якого розробляється дана мікропропроцесорна система, призначений для проведення горизонтальних і похилих до ± 10%, підготовчих виробок перетином від 9 до 33 м2, в проходці по породним, змішаних і вугільних вибоях при міцності порід до 100 МПа при одному стиснення і абразивності до 15 мг в шахтах, небезпечних за газом та пилом. Форма виробок будь-яка, з плоским грунтом.
Об'єктами діагностування в прохідницький комбайн є редуктор виконавчого органу, електродвигун і муфта. Технічні характеристики об'єктів діагностування:
-частотний діапазон зміни вібрації (без урахування вібрації підшипників) від 5 до 200 Гц [ 7 ]
-діапазон зміни СКУ Віброшвидкість в лінійному частотному спектрі (від технічного стану "Норма" до "Аварія") від 0.4 до 20 мм / с.
Мікропроцесорна система складається з блоку віброперетворювача, блоку діагностики, блоку обробки інформації та кабельних перемичок. Такий склад дозволяє мати функціонально закінчені вузли і до мінімуму скоротити кабельні зв'язку. Кожен блок розташований на окремій платі з клемниками.
Блок віброперетворювача призначений для перетворення механічних коливаня приводу різання в електричний сигнал і включає в себе п'єзоелектричний вимірювальний Вібродатчик і зовнішній підсилювач.
Блок діагностики призначений для посилення, фільтрації і обробки вихідних сигналів з віброперетворювача.
Блок обробки інформації включає в себе мікропроцесорний вузол і три світлодіода. Блок призначений для обробки інформації, що надходить з блоку діагностики; реалізації алгоритмів діагностування; формування масиву інформації про технічний стан об'єкта; видачі інформації на індикацію і передачу її контролеру електронної системи управління прохідницьких комбайном.
Кабельні перемички призначені для з'єднання блоку діагностики з віброперетворювачі. У кабельних перемичках використовується спеціальний вібраційний кабель.
мікропроцесорних систем вібродіагностики прохідницького комбайна необхідно розміщувати в вибухонебезпечному корпусі з електронною системою управління прохідницьких комбайном, причому кожна друкована плата по-повинна ще бути в окремому пластмасовому корпусі. Мінімальні розміри корпусів не більш 300х150х250 мм.
Конструктивне оформлення виробу повинно відповідати вимогам естетики, ергономіки і інженерної психології. Рівень художньо-конструктивного рішення повинен відповідати кращим сучасним вітчизняним і зарубіжним зразкам.
При виборі марок і сортиментів матеріалів необхідно керуватися вимогами зниження матеріаломісткості вироби і зниження витрат гостродефіцитних матеріалів. [ 1 ]
4. Проектування мікропроцесорної системи вібродіагностики видобувного камбайна
Об'єктом проектування в даному дипломному проекті є мікропроцесорна система вібродіагностики прохідницького комбайна П-160.
Для вимірювання механічних вібрацій застосовуються вибродатчики. Вибродатчики можна розділити на генераторні і параметричні. В окрему групу можна віднести порівняно недавно з'явилися, лазерні вибродатчики. Параметричні, в свою чергу, діляться на індуктивні і ємнісні.
Основними недоліками параметричних датчиків є: p>
- необхідність в додатковому джерелі живлення;
- необхідність початкової установки або зазору калібрування;
- більш складна схема;
- виникнення параметричних шумів при малих рівнях сигналу.
До генераторних датчиків відносяться п'єзоелектричні. Це найбільш поширені на сьогоднішній день датчики. До їх недоліків можна віднести:
- неможливість проведення безконтактних вимірювань; P>
- неможливість вимірювання постійної складової вібрації.
Переваги генераторних датчиків в порівнянні з параметричними вибродатчик: немає необхідності в додатковому джерелі живлення, відсутність початкової установки зазору, простіша схема, відсутність шумів при малих рівнях сигналу.
Принцип дії лазерного вибродатчик заснований на вимірюванні зсуву частоти лазерного випромінювання, розсіяного рухаються з певною швидкістю (ефект Доплера).
Переваги лазерного віброізмерітелей:
- безконтактний вимір; [ 14 ]
- немає необхідності готувати поверхню для вимірювань;
- широкий діапазон частотного спектра вимірюваного сигналу;
- можливість вимірювання вібрації поверхонь з високою температурою.
Недоліки лазерних віброізмерітелей:
- висока вартість;
- складність схеми;
- вимір Віброшвидкість.
Вихідний сигнал вібродатчиків повинен бути пропорційний величині вібросмещенія (віброметри), Віброшвидкість (велосіметри) і віброприскорення (акселерометри). При вимірюванні кожної з цих величин можна отримати інші. Так для віброметра при диференціюванні вібросмещенія отримуємо віброшвидкість, а при подвійному диференціюванні отримаємо віброприскорення. У разі велосіметра шляхом інтегрування вихідного сигналу датчика отримаємо сигнал пропорційний вібросмещенія, а при диференціюванні - віброприскоренню.
Розрахунок фільтра верхніх частот [ 15 ]
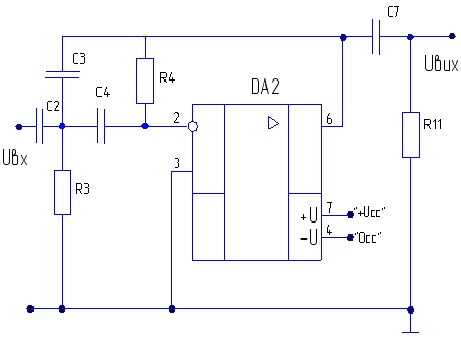
Малюнок 1 – Фільтр верхніх частот
Фільтр верхніх частот з багато петлевий зворотним зв'язком має передавальну функцію такого вигляду:
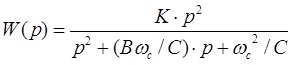
Малюнок 2 – Фільтр верхніх частот з багато петлевий зворотним зв'язком
де В і С норміровнние коефіцієнти.
З довідкової літератури [ 14 ]: B = 1.41214; C = 1
Фільтр на ОУ DA2, показаний на малюнку 3.17, реалізує функцію верхніх частот другого порядку з інвертуючим коефіцієнтом посилення.
Частота зрізу фільтра 300Гц, коефіцієнт посилення K = 1. Виберемо номінальне значення ємності С2 = С4 (близьке до значення 10 / fc мкФ). С2 = 10/300 = 0.0333 мкФ.
Обчислимо значення R3 і R4 за формулами

Малюнок 3 – Обчислення резисторів R3 і R4
Коло С7R11 призначене для виключення з сигналу постійної складової. С7 вибирається переважно близьке до значення 10 / f мкФ. С7 = 33нФ Побудуємо амплітудно-частотну характеристику фільтра

Малюнок 4 – Амплітудно частотна характеристика фільтра високих частот
(анимація: 5 кадрів, 10 циклів повторення, 160 килобайт)
Висновки
У дипломному проекті спроектована мікропроцесорів система вібродіагностики прохідницького комбайна П-160. Для цього було проведено огляд аналогів, обґрунтування вибору початкових віброперетворювачів. Як вібродатчиків були обрані генераторні п'єзоелектричні акселерометри. Реалізовані такі методи вимірювання вібрації приводу різання прохідницького комбайна: оцінка загальної вібрації електродвигунів і редуктора по СКУ віброшвидкостей, вимір вібрації по інформативних частотах, оцінка технічного стану підшипників по вимірюванню ударних імпульсів. Розроблено технічне завдання на проектування системи. Проведений розрахунок вузлів принципової схеми і оцінені метрологічні характеристики системи. Зроблено огляд різних сучасних цифрових інтегральних схем і мікроконтролерів. Розроблена конструкція і програмне забезпечення системи. Згідно ГОСТам зроблена вся технічна та конструкторська документація. Спроектована система повністю задовольняє вимогам поставленого до неї в технічному завданні. Проектування може вважатися закінченим. Систему можна виготовляти і застосовувати на виробництві.
Перелік посилань
- Журнал "Вугілля України" №1, 2004. - 80 с
- Журнал "Вугілля України" №2, 2004. - 80 с
- Журнал "Вугілля України" №3, 2004. - 80 с
- Журнал "Сучасні технології автоматизації" №7, 1999. - 80 с.
- Бауман Е. Вимірювання сил електричними методами; Під ред. І.І.Смислова. - М .: Світ, 1978. - 430 с.
- Соліванов М.Н., Фрідмак А.Е., Кудряшова Ж. Ф. Якість вимірювань: Метрологічна довідкова книга - Л: Лениздат 1987. - 290 с.
- Розрахунок електронних схем. Приклади і задачі. Навч. Посібник для вузів / Г.І. Із'юрова і ін. М.Ж., 1987. - 332 с.
- Руденко В.С., Сенько В.І. та ін. Основи промислової електроніки. - К .: Вища школа, 1985.- 400 с.
- Гутников В. С. Інтегральна електроніка в вимірювальних устройствах.- 2-е изд., Перераб.и доп.-Л .: Енергоіздат. Ленінград. отд-ня, 1988.-304 с.
- Якубовський С.О., Барканов Н.А ,. Кудряшов В.П. Аналогові і цифрові інтегральні мікросхеми: Довідкове посібник / За ред. С.В.Якубовского. М .: Радио и связь, 1985. с. - 336 с.
- Джерела електроживлення радіоелектронної апаратури. Довідник. Під. ред. Г.С. Найквиста. - М. Радіо і зв'язок, 1986.
- Напівпровідникові прилади: тиристори. Довідник. Під. ред. М.М. Горюнова, 1983.
- Панфілов Д.І., Чепурин І.І., Миронов В.Н. та ін. Електротехніка в експериментах і вправах: Практикум на Electronics Workbench: т. 1,2. - М .: додека, 2000. 288 с.
- Харінскій А.А. Основи конструювання елементів радіоапаратури. - Л .: Енергія, - 1971. - 464 с.
- ГОСТ 2.001-70. ЕСКД. Основні положення.
- ГОСТ 2.109-73. ЕСКД. Основні вимоги до креслень.
- ГОСТ 15.001-73. ЕСКД. Схема розробки і постачання продукції на виробництві.
- ГОСТ 2.417-78. ЕСКД. Правила виконання креслень друкованих плат.
- Бізнес-план інвестиційного проекту. Практичний посібник / Під. ред. Іваннікова І.А. - М .: "Експертне бюро" - М., 1997. - 112 с.