Abstract
content
- Introduction
- 1. Goals and objectives of the study
- 2. Scientific novelty and practical value
- 3. Analytical review
- 4. Objects of study
- 5. Research methods
- 6. experimental part
- 7. Research results
- Conclusion
- References
Introduction
The unsatisfactory state of the coking raw materials base, its insecurity in the future with sintering coals necessitated the acceleration of the development and introduction of new methods for the preparation and coking of coals to obtain coke of the required quality from charges with a high proportion of enhanced sintering components. One of such methods is the introduction of organic additives into the mixture. When assessing the role of organic additives in coal sintering processes, it should be borne in mind that it can be ambiguous, since, firstly, the properties of various organic additives can be very diverse, and secondly, coals of different degrees of metamorphism, to which various additives are also very different in sintering. In this case, one of the additives can enter into chemical interaction with the products of the primary destruction of coal and thereby fundamentally influence the processes of formation of the coal plastic mass, making it more or less fluid, reactive, and curable. Organic additive affects the characteristic indicators of the formed coal plastic mass, but in the first case, its effect is deeper. It not only affects the plastic properties, but also makes a significant contribution to the formation of the molecular structure of the curable plastic mass, making it more or less graphitized. In the second case, the additive practically does not affect the molecular structure of the solid residue of thermal decomposition, but only increases or decreases its strength. In other words, the additive in this case plays the role of an additional amount of liquid non-volatile products in the coal plastic mass. If it is enough, it can reduce the strength of the solid residue, and vice versa. Thus, additives to coal can be considered as one of the possible ways to control thermochemical transformations of coal and the formation of their molecular structure, physical and chemical properties of solid residues. For example, the use of chemical waste from coke production as additives will simultaneously solve the problem of their utilization. Since at present a significant amount of resinous waste from coke-chemical plants does not find qualified use, it becomes expedient to use them as additives to the charge in the production of coke. Many scientists have devoted their research to the study of sintering additives. Using this method, they tried to solve two main tasks: first, to expand the raw material base of coking to use domestic low-coking coal and, second, to recycle waste from various industries.
1. Goals and objectives of the study
In order to rationalize the use of coal, it is necessary to determine their structure, since it is precisely it that determines their properties and the direction of the most efficient processing. One of the most informative methods for the study of the supramolecular organization of coal is X-ray structural analysis. The purpose of this work is to assess the effect of additives DAK (dinitrile of acrylic acid) and absorbing oil on the structure of semi-coke, obtained from non-caking long-flame coal of the Donetsk basin, according to x-ray structural analysis..
Tasks:
- find out the effect of organic additives on the yield of solid, liquid and gaseous products and the structure of semi-cokes;
- find out the effect of radical polymerization initiators on the processes of thermal transformations in the solid phase.
2. Scientific novelty and practical value
Currently, there is no consensus on the interpretation of the results of X-ray structural analysis for such a complex structure, What is coal and its pyrolysis products. The fact is that the supramolecular structure of coal in the general case can be represented as a combination of two components, having substantially different properties: crystalline and amorphous phases..[2]
With the help of X-ray analysis, it is possible not only to study the structure of a single sample of coal, but also to investigate the change in the structure of coal as a result of the occurrence of such processes as metamorphism and pyrolysis.
3. Analytical review
The functions of active intermediate products in radical polymerization are performed by free radicals. Common monomers entering into radical polymerization include ethylene, vinyl chloride, vinyl acetate, vinylidene chloride, tetrafluoroethylene, acrylonitrile, methacrylonitrile, methyl acrylate, methyl methacrylate, styrene, butadiene, chloroprene, etc. Radical polymerization usually involves several chemical steps: initiation, chain growth, chain termination, and chain transfer. Indispensable stages are the initiation and growth of the chain..
The initiation of radical polymerization consists in creating free radicals in the reaction system capable of starting reaction chains. The most common method is based on the implementation in the monomer environment of thermal homolytic decomposition of unstable substances - initiators. Various types of peroxides are widely used as initiators: alkyl peroxide (tert-butyl peroxide), hydroperoxide (cumene hydroperoxide), peresters (tert-butyl perbenzoate), acyl peroxide (benzoyl peroxide), etc. When heated, peroxides decompose as follows (for example, benzoyl peroxide):

In addition to peroxides, azo compounds are widely used as initiators, among which 2,2'-azobis-isobutyronitrile (AIBN) is most widely used:
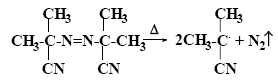
Radical polymerization initiators usually do not differ in their selective action with respect to different monomers, therefore the choice of initiator is most often determined by the temperature at which the desired free radical generation rate can be achieved in each specific case. So, AIBN used at 50-70 ° C.
Dinitrile azobisisobutyric acid (DAK) is an organic substance of the class of azo compounds and nitriles. Used as an initiator of radical polymerization and other radical reactions[3].
Taking into account that pyrolytic transformations of coal occur with the participation of free radicals, in this work we used the additive AIBN, a radical polymerization initiator and a product of distillation of coal tar (absorption oil). Absorption oil is an absorption fraction of coal tar washed from phenols. In the near future, the release of absorption oil in the form of a product of rectification of the absorption fraction is planned.
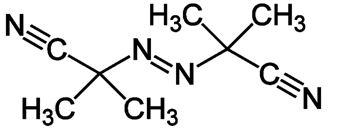
Picture 1 – Formula initiator radical polymerization
The disadvantage of coal absorption oil is its insufficient chemical resistance. In the course of long-term work, the density of the oil and its viscosity increase, as well as its boiling point increases, the amount of distillate decreases to 300 ° C, and the molecular weight increases (from 170–180 to 200–220).
Objects of study
The objects of study used isometamorphic pairs (of the same stage of metamorphism) of the coal of the Donets Basin of different genetic types in terms of reduction (type a and b), differing in sintering and sulfur content. Samples of recovered and weakly recovered coal were taken from the closest coal seams in the same mine.
The data of elemental and technical analysis of the coal studied are given in table. 1.
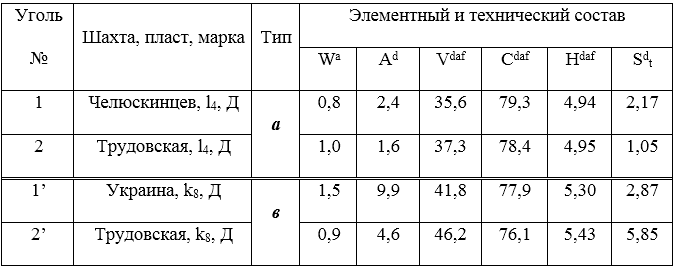
Preliminary chemical treatment of the charge was carried out by dissolving organic additives in ethyl acetate or acetone for the most uniform application and further mixing the resulting solution with coal.
Research methods
In the work used the following research methods:
- semi-coking;
- technical and elemental analysis of the investigated coal (according to GOST R 53355-2018);
- quantitative analysis of semi-coke gas;
- determination of the yield of semi-coking;
- elemental and technical analysis of solid pyrolysis products;
- X-ray analysis method;
- EPR spectroscopy method;
- IR spectroscopy method.
The X-ray analysis method is based on the phenomenon of interference or scattering of rays through a microcrystalline lattice. Rays scattered by individual atoms can reinforce or weaken each other.
X-ray diffraction analysis records the supramolecular structure of coal. Coal matter is considered to be a carbon mesh construction. From the small-angle dispersion curves in samples of hard coal, it can be established that loose, medium globules prevail in the low-grade metamorphism, while the anthracites are dominated by fibrils.
The method of electron paramagnetic resonance is used to study paramagnetic centers and their environment in a substance. The EPR method can determine the concentration and identify paramagnetic particles in any state of aggregation. The EPR method is used if there are unpaired electrons with corresponding magnetic moments in the molecule of the original substance. The driving charge in turn creates a magnetic field. The motion of an electron in an orbit creates an orbital magnetic moment, and the rotation around its own axis is spin. Each spin orientation corresponds to a certain value of the moment interaction energy with the magnetic field[4].
The method of IR - spectroscopy makes it possible to obtain information about the structural - group components of organic substances, as well as to evaluate the nature of the bond between atoms, which is of fundamental importance when studying the structural and informational properties of various substances.
The basis of this method is the resonant absorption of infrared radiation by the material. Infrared radiation is also called “thermal” radiation, since all bodies, solid and liquid, heated to a certain temperature, emit energy in the infrared spectrum. In this case, the wavelengths emitted by the body depend on the heating temperature: the higher the temperature, the shorter the wavelength and the higher the radiation intensity [5].
Experimental part
Semi-coking was carried out under standard conditions according to GOST 3168-93 (ISO 647-74). The essence of this method is to heat a sample of 20 g of fuel in an aluminum retort without air access to 520 ° C and to determine the yield of semi-coke, gas, as well as tar and pyrogenic water, followed by their separation [6].
The analysis of semi-coke gas was carried out in a gas analyzer VTI (All-Union Thermal Engineering Institute. The essence of the analysis is to pump the gas sample through the reagents to absorb the various components of the gas.
Research results
The results obtained during the laboratory semi-coking of the coal charge with additives are given in table. 2
Table 2 - The results of the study of the coking of unequally reduced coals.

With an increase in the final heating temperature, the amount of semi-coke gas increases, its composition changes. Analysis of the obtained semi-coke gas (Table 2) shows that during the pyrolysis of different types of coals, a significant influence of chemical additives on the content of CH4, H2 and H2S in the gas (Fig. 2) is observed, which is more pronounced during the pyrolysis of type a coal. The decrease in the concentration of methane and hydrogen and the increase in the concentration of hydrogen sulfide occurs more intensely under the action of oil.
The yield of semi-coke increases with the introduction of additives, first of all, DAK for coals of both reduced and weakly reduced types, which indicates an intensification of polyrecombination reactions during chemical processing.
In type A coal of the Chelyuskintsev mine, one can observe a significant increase in semi-coke from the initial 63.5% to 70.9% under the action of DAK, and 70.0% with the addition of absorption oil. In turn, the yield of steam-gas products has significantly decreased, especially with the introduction of the additive DAK.
In the type a coal of the Trudovskaya mine with the introduction of an additive, on the contrary, the yield of semi-coke did not change at all, but when adding oil it increased by 1.5%. The same was observed when the steam-gas products came out, DAK did not change their yield at all, and the oil reduced the yield by 1.5%.
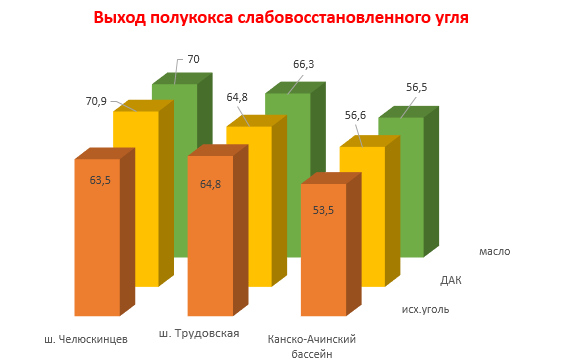
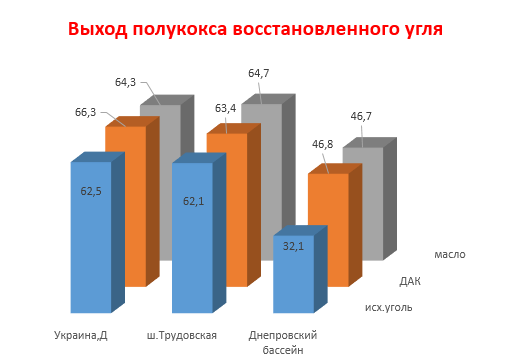
Picture 2 - Output of coal char semi-coke with additives
Table 3 presents the results of X-ray analysis of two pairs of coal and the semi-cokes obtained from them with and without additives. It follows from the table that when the coal under study is heated to 520 ° C, the thickness (Lc) and the length (La) of the package increase both in the reduced and in the weakly reduced coals. In the second case (sh. Chelyuskintsev), this dependence is more pronounced. The interplanar distance does not change and the number of grids remains constant. The h / l ratio increases 1.5 times due to the loss of oxygen in the form of CO2 and CO.
Table 3 The results of x-ray analysis of the original coal and the products of their pyrolysis
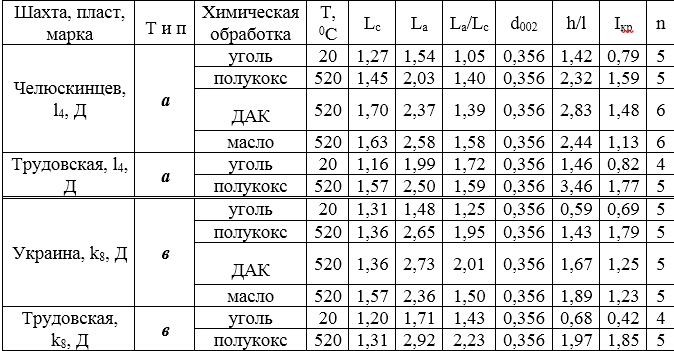
The data presented show that the chemical compounds used in this work affect the size of the carbon mesh package. For coals of weakly reduced type, there is a noticeable increase in the number of layers in the package from 5 to 6, the thickness of the package - (Lc) from 1.45 to 1.70 and the length (La) of the package - from 2.03 to 2.58. Moreover, under the action of DAK, a predominant increase in Lc is observed, and under the action of oil - an increase in La. The maximum degree of ordering (h / l) occurs when processing DAK. Additives on the pyrolysis of reduced coals have a different effect. In this case, the effect of the absorption oil and DAK on different types of coal is opposite. DAK contributes to an increase in the longitudinal, and oil - the transverse dimensions of the package. Analysis of the products of thermal and thermochemical destruction of coal by the EPR method and IR spectroscopy is in progress.
Conclusion
It was shown that the additive DAK and absorption oil change the course of the process of thermal destruction of young coal at different stages, that is, they enter into chemical interaction with coal and the products of their pyrolysis.
Under the action of DAK additives and absorption oil, there is an increase in the yield of semi-coke, i.e. the processes of crosslinking are activated, which is confirmed by the increase in the size of the X-ray package and the degree of order of the carbon networks of the semi-cokes.
High concentration of hydrogen sulfide in semi-coke gas of type в (up to 33%) will allow using this gas for its extraction and further use in the chemical industry.
The high content of hydrogen in type semi-coke gas (up to 47%) will also allow its use in blast furnace production.
References
- Применение нефтяных спекающих добавок в шихтах для коксования // УглеХимический журнал. – 2006. – № 5–6. – С.22–30
- Д.И. Дедовец, В.Н. Шевкопляс, Л.Ф. Бутузова. Обоснование методики оценки надмолекулярной организации углей с использованием рентгеноструктурного анализа, 2008 г.
- Браун, Николай Васильевич, Глущенко, Иван Маркович. Перспективные направления развития коксохимического производства. – М.: Металлургия, 1989. – 271 с.
- Кукаев Е.Н. Спектроскопия электронного парамагнитного резонанса. Методические указания к лабораторной работе/Е.Н. Кукаев, А.Ю. Куксин, А.О. Тишкина. – 2005 г. – 160 с.
- Вяземский А./ Инфракрасная спектроскопия / Журнал «Химия» №21.2002
- Аналитическая химия и технический анализ угля: Учебник для техникумов. Авгушевич Н.В., Броновец Т.М., Еремин И.В. и др. – М.: Недра, 1987. – 336 с.