Summary of the final work
Ñontent
- Introduction
- 1. Relevance of the topic
- 2. Goals, objectives of the research and planned novelty
- 3. The main characteristics of the original man-made materials
- 4. Description of the practical part
- 4.1 Mix preparation
- 4.2 Mixing
- 4.3 Sample Molding
- 4.4 Drying of finished samples
- 4.5 Firing finished samples
- Findings
- List of sources
Introduction
Currently, the industrial enterprises th set of important tasks are resource conservation and ecology production. In turn, the availability of large resources of technological raw materials creates prerequisites for the wide development of the production of building ceramics.
Huge amounts of accumulated waste pose serious economic and environmental problems. According to statistics , at the beginning of 2016 , about 31.5 billion tons of production and consumption was recorded in Russia . Of these , no more than 10% of all types of waste are used and recycled , most of them are stored indoors or dumped in landfills. The secondary use of technogenic waste in the production cycle of ceramic products is a promising and one of the best ways to dispose of them. T Which approach allows not only widen races the mineral resource base with the construction industry, but also to ensure theenvironmental safety of the environment and to preserve natural resources.
surface of the earth or in mine workings, which are waste from mining, processing, metallurgical and other industries and are suitable in quantity and quality for industrial use, which becomes possible as technology of its processing and economic conditions change [ 2 ].
Chemical and mineralogical composition of a variety of large-tonnage industrial waste is not inferior to natural raw materials, and in many cases even surpasses it in technological conditions, which makes it very promising to use them as raw materials .
Dumps, heaps, and sludge collectors placed on an area of 160 -180 thousand hectares, which increases with a speed of 3-6 thousand hectares / year. Low volume of waste processing (no more than 10 %) causes the growth of technogenic contamination of all components of fire and dust protection . The waste problem has a number of serious environmental and economic aspects and requires the adoption of urgent measures to address it. One of the promising and effective ways to solve it is the use of industrial waste to create new technical materials. Of the total amount of annually generated industrial waste, about 120-150 million tons are suitable for reuse. Currently, only about 30% of this amount is used [ 3 ].
1. Relevance of the topic
One of the promising directions for the use of waste is to obtain ceramic building materials: wall, wall and paving products. Disposal of waste into building materials is aimed at solving social and environmental problems, improving the living conditions of the population, creating additional jobs. On the production of 5 million pcs. Ceramic bricks require about 20 thousand tons of clay raw materials. The use of secondary raw materials in the building materials industry will reduce the need for primary mineral and raw material resources, which solves not only environmental but also economic tasks, because raw materials from waste are 2-3 times cheaper than natural ones, and often they are already partially subjected to grinding, thermal processing and other technological impacts that facilitate their use .
One of the most popular building ceramic materials is ceramic brick. The main raw materials for the production of ceramic bricks are clay materials: loams, loess, mudstones and others. Consequently, the above-mentioned technogenic products are in most cases similar in their chemical composition to the main raw materials, which allows them to be used for the production of ceramics and, in particular, for the production of ceramic bricks.
2.Goals, objectives of the research and planned novelty
The purpose of this work is the use of technogenic by-products of the industry as a raw material for the production of ceramic bricks .
To achieve the goal, the following tasks are solved :
- Analysis of the possibility of using PGU dust , terragone rock and other industrial wastes as an additive for the production of ceramic bricks.
- Development of production technology from industrial waste.
- Manufacturing samples studied materials.
- The study of strength and other properties.
Planned scientific novelty : the developed technology of using industrial waste as a raw material for the production of ceramic brick , as well as the methodology for conducting research on the properties of the samples obtained.
The use of technogenic raw materials will provide a practical effect :
- To produce cheap building materials.
- To increase labor productivity, due to the profitable processing of early extracted raw materials, which is a ready-made semi-product and located next to the operating enterprises.
- Release occupied land, rehabilitate them and eliminate sources of environmental pollution, thereby improving the environmental situation around existing enterprises.
Research methods : the manufacture of samples and the study of their properties on the real equipment of the department.
The results of individual stages of the work were reported at a scientific conference and published in a collection.
3. Main characteristics of man-made starting material in
Ceramic brick remains one of the most demanded masonry materials for a long time. The main raw material for its manufacture is clay, and all sorts of additives give this building material various properties. Thanks to good indicators of strength, water resistance, frost resistance and thermal conductivity, it successfully holds a leading position among a large number of modern masonry materials.
The main additives in the research work were used such man-made materials as: debris , CCU dust and metallurgical scale.
The clays used for the production of ceramic bricks by chemical composition vary widely over the content of the main components and are listed in Table3.1.
Table 3.1 - Sample content of the chemical to the Components in Chapter nah
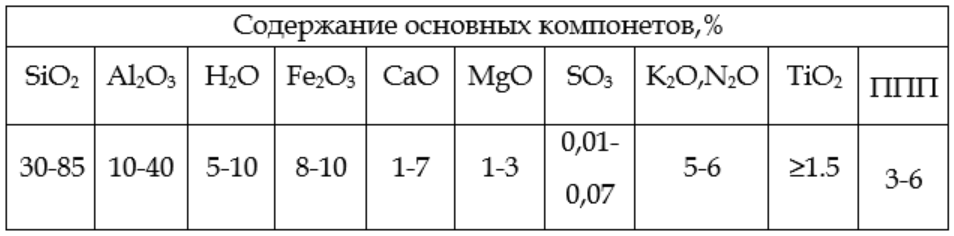
Heated rock - overburden, obtained by the extraction or enrichment of coal, such rock can contain up to 46% of coal, up to 15% of alumina and up to 20% of oxides of silicon and iron. In table 3.2 . The approximate chemical composition of the clay used in the research work is given.
Table 3.2 - The approximate content of chemical components in terrakonnoy rock mine them. named after academician A. A. Skochinsky .

Metallurgical scale is a mixture of oxides formed by the direct action of oxygen when metals are heated in air. Scale is a mixture of oxides of Fe 3 O 4 , FeOand Fe 2 O 3 , and consists of two layers that are easily separated from each other. The inner layer is porous, black-gray in color, the outer is dense and with a reddish tinge, both layers are fragile and have ferromagnetic properties. The composition of the iron scale is not constant and depends on the conditions of production: during prolonged glowing in air, it gradually turns into Fe 2 O 3 , and the latter, in the white heat, loses some of the oxygen, turning into FeO . Iron scale usually consists of 64–73% FeO and 36–27% Fe 2 O 3 , the outer layer contains more Fe 2 O 3 - from 32 to 37%, and the outermost layer even up to 53%.
PGU dust - is formed in the combined-cycle gas turbine unit with intra -cycle gasification during the conversion of coal into other types of fuel, with the subsequent purification of this gas from impurities before burning and with the subsequent transformation of pollutants such as sulfur into useful products. As a result, emissions of sulfur dioxide, soot, etc. are reduced.
4. Description of the practical part
4.1. Mix preparation
The technology for producing pressed brick on the basis of technogenic products in the laboratory begins with the selection of the charge composition and the preparation of raw materials for further use . This is followed by weighing and mixing the components. For high-quality and reliable verification of the properties, we used 3 samples, different in the percentage of the feedstock. To obtain a plastic mass, all components must be strictly metered according to the recipe. To do this, use scales with a permissible measurement error of 0.5%. Table 4 presents the recipe.
Table 4 - Formulation of test samples
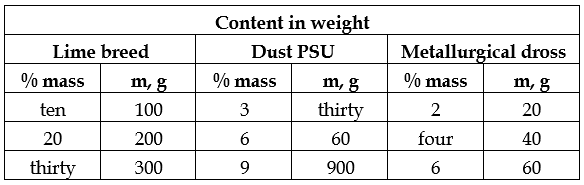
4.2. Preparation of the mixture
The dosed mixture was subjected to grinding, with the help of a mill with grinding bodies, where thorough mixing of all components also took place for their activation. Add the required amount of water to obtain a plastic working mass .
Figure 1 - Mill ( 1 - electric motor, 2 - coupling, 3 - shaft, 4 - drum, 5 - spring)
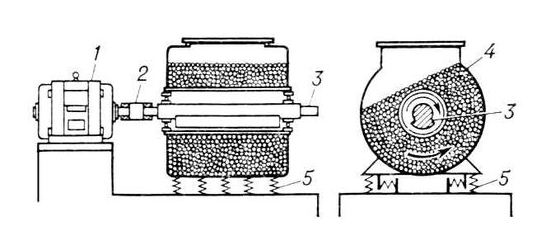
4.3 Sample molding
Under laboratory conditions, the samples were molded by hand using special molds that were lubricated with machine oil to facilitate the molding of samples and not allowing the prepared mass to adhere to the walls of the mold and the substrate, which made it possible to preserve the shape of the product while removing the sample from the mold.
4.4 Drying samples
After molding, the samples are placed on glass substrates, covered with a damp cloth and left for 2-3 days after which the fabric is removed and the samples are left for another day - this operation is called air drying. Then the samples are placed in the drying cabinet and slowly, within 2-3 hours, thetemperature in the area of drying is raised to 110 ± 15 ?Ñ. After that, the temperature in the dryer is raised to 200 ?Ñ and dry the samples for 12 hours or more to remove chemically bound water.
Figure 2 - Laboratory Drying Oven

4.5 Firing samples
After drying, the samples are sent to the furnace, where the test samples will be burned at three different temperatures: 1000, 1050 and 1100 ?Ñ.
Figure 3 - Firing samples in a muffle furnace
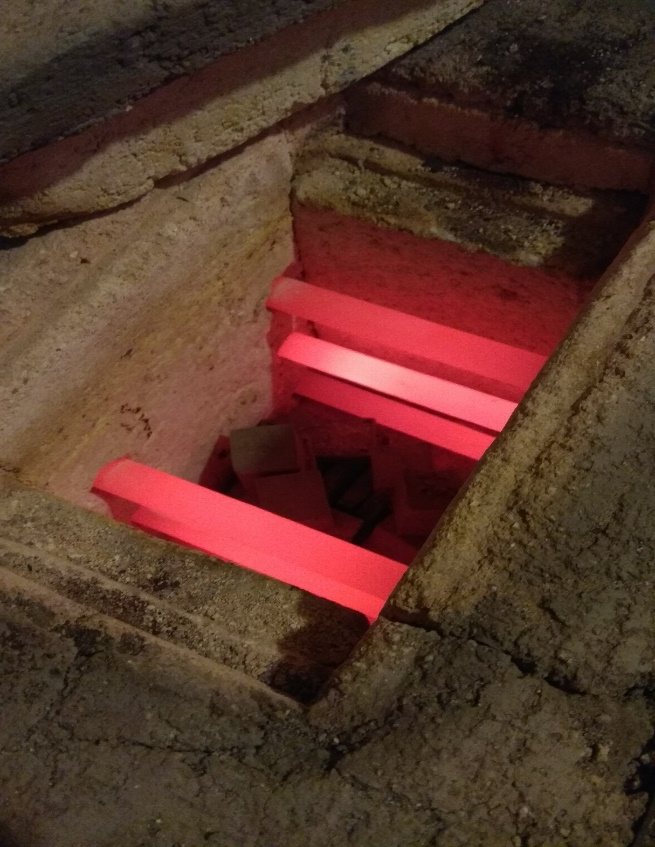
5. Examination of samples for properties
The practical part is not finished yet, a sufficient number of samples were made for conducting experiments. At this stage of master's work, the strength properties of the samples are investigated. The samples are tested for compression channel podvegratsya atie, mo rozostoykost and water absorption.
Âèñíîâêè
Findings
- 1. Man-made waste in the production of building materials [ Electronny resource ] .
- 2. Trubetskoy K.N., Umanets V.N., Nikitin N.B. // Complex use of mineral raw materials. - Yekaterinburg. 1987. Number 12. 18-23 s.
- 3. Kasimov A.M. Industrial waste. Problems and solutions. Technologies and equipment: study guide / A.M. Kasimov , V.T. Semenov, A.A.Romanovsky; by ed. A.M. Kasimov . - Kharkov: KNAMG, 2007. - 411 p.
- 4. Chanturia V.A., Chaplygin N.N., Vigdergauz V.Ye. Resource-saving technologies for the processing of mineral raw materials and environmental protection // Mining Journal. - 2007. - ¹ 2. - p. 91-96.
- 5. Stolboushkin A.Yu. Wall ceramic materials of matrix structure based on non - caking, non - plastic man - made and natural raw materials. Diss . Doctor. tech . sciences. Novosibirsk - 2014. - 365 s.
- 6. Pavlov V. F. The method of involvement in the production of building materials industrial waste // Construction materials. -2003. - ¹ 8. - p. 28-30.
- 7. Fomenko A.I., Kaptyushina A.G., Gryzlov V.S. Expansion of the raw material base for building ceramics. Stroitel'nye materialy , 2013 , no . - 2015. - ¹ 12. - P. 25-27.
- 8. Stolboushkin A. Yu. Improving the decorative properties of wall ceramic materials based on technogenic and natural raw materials. Stroitel'nye materialy, 2013 , no. - 2013. - ¹ 8. - p. 24-29.
- 9. Raut SP, Ralegaonkar RV, Mandavgane Development of sustainable construction materials using industrial and agricultural land use. - 2011. - V. 25. - p. 4037–4042.
- 10. Fomenko A.I., Kaptyushina A.G., Gryzlov Vs Expansion of the source of raw materials for building ceramics. Construction materials. - 2015. - ¹ 12. - P. 25–27.