Abstract – The choice of CAD for the design of technological processes in mechanical engineering
Content
- Introduction
- 1. CAPP-Most Important PLM Systems Module
- 2. CRITERIA FOR THE SELECTION OF CAD PROCESS PRODUCTION PREPARATIONS
- FINDINGS
- List of sources
Introduction
The idea of creating a CAD system that facilitates the work of a process engineer for automating the calculations of processing, welding, surfacing, cutting, labor and material standards, planning, filling in technological documentation, appeared during the operation of the first computers in production. Currently, CAD, CAM, CAE, PLM systems, represent the foundation of CALS technologies .
Computer-aided design systems for technological preparation of production are represented by two types of systems: CAM and CAPP. Consider a variety of CAPP systems whose purpose is to automate the design and planning of technological processes.
Currently, there are many modern CAPP of well-known manufacturers, but the task of choosing and implementing such systems is still relevant for most engineering enterprises of the CIS. Most of the CAD for the design of technological processes in mechanical engineering has an architecture consisting of an information central module and additional modules in the form of a database (production equipment, processing modes, reference data, etc.), modules implementing technology design, production planning (routing and packing), rationing materials and labor, the formation of technological documentation, integration with CAD/PDM/PLM systems.
1. CAPP-Most Important PLM Systems Module
A feature of the engineering production is a long cycle of technical (engineering and technological) preparation of production, comprising 60-90% of the total cycle.
The first ASTPP began to be created as early as the 60s of the twentieth century. However, the computing base on which ASTPP was built up to the beginning of the 90s did not allow for the necessary efficiency and real complexity of the automation processes. Nevertheless, in these conditions a number of basic principles were developed, on the basis of which ASTPP was built. They remain fair and at the present time, however, do not give an answer to the question: how to build ASTPP in modern conditions, taking into account the globalization of industrial production, using such forms of cooperation as the creation of expanded and virtual enterprises.
“To just stay in place, you need to run, but to get somewhere, you need to run twice as fast” (C). This Carroll rule is quite applicable to modern production. More recently, companies that used information technology were “on horseback” – the automation of individual processes gave them significant advantages. But today, IT has ceased to be a winning factor, becoming a vital necessity. The introduction of modern IT systems at certain stages of design or production allows “just to stay in place.” “And in order to get somewhere,” that is, to compete successfully in the global economy, there are no longer enough single software products – end-to-end enterprise automation systems and product life cycles are necessary. Information, once entering the IT space of an enterprise, passes through a single stream through all production preparation cycles and directly the production itself. This allows not to enter the same data over and over again at different stages (which leads to a loss of quality and time), but to build a highly efficient control system.
The essence of the PLM concept is to provide information and organizational support for all phases of the product life cycle. The loss of even one stage prevents the end-to-end flow of information and does not allow the digital model to fully exist. In the engineering industry, such a gap most often occurs between the stages of product design and production. For the most part, problems arise in the field of technological preparation of production due to the traditional division of responsibilities between design offices and production plants, limited ability to implement technical processes in PLM-systems, or simply due to lack of attention to this area.
The experience of engineering projects shows that, relying only on the capabilities of PLM platforms (even such complex ones as the Teamcenter from Siemens Software, Windchill from PTC and Enovia from Dassault Systemes), as a rule, it is not possible to fully implement the support of technological preparation of production, correctly and accurately describe the technological processes and manage them. In practice, this means that the formation of documentation on the technological preparation of production, its transfer in electronic form between the design and production units, as well as maintaining the documentation up to date are at least difficult or not at all possible. Because of this, there are a number of restrictions – for example, when at the design stage it is not possible to take into account the specifics of manufacturing technology or the limitations of the production base of an enterprise. The most important information about the composition of the product, technological processes, necessary resources such as equipment, materials, equipment and personnel support can fall out of the automation circuit. Of course, many of these indicators can be entered manually based on existing experience and assessments of technologists and production workers, but whether they will be accurate is a big question, especially for new products. Consequently, the management of an enterprise is unlikely to get realistic estimates of the cost of a product, the timing of its entry into the market, the necessary resources, and therefore, it cannot make the right decisions.
Computer-aided design of technological processes is designed to eliminate this problem, on the one hand, by providing the necessary tools for creating technological processes to technologists, and on the other – by becoming a source of necessary information on technological preparation of production for other information systems. In the ideal architecture, solutions for enterprise automation CAD systems are part of (an independent module) PLM-systems, providing two-way transmission of information. Today, there are many local CAD systems that successfully solve problems in their field. The most famous: “VERTICAL” of the Russian company ASCON, Timeline from SDI Solutions, TECHCARD of the Belarusian company Intermech. The integration of CAD systems with PDM in many cases can be carried out by regular means, especially if both systems are from the same manufacturer. However, from the point of view of integration and collaboration with top-level PLM systems, the situation is not so simple.
Choosing CAD for the design of technological processes, you must be guided by two equivalent criteria. First, you need to focus on the needs of the enterprise services involved in production planning. Development of technical processes should be convenient and understandable, otherwise there is a high risk that processes will be designed traditionally, that is, on paper, and the system will be reflected only “for a tick”, with a low degree of confidence.
The second criterion is the possibility of issuing technological documentation in accordance with the standards of the enterprise and the flexibility to customize the formats of outgoing documents. All the above systems are initially focused on compliance with the standards for the design and technological documentation as a basic requirement. However, many enterprises in addition to them use their own forms of documents, therefore, special requirements can be implemented in these systems in different ways. In addition, even within the same enterprise, different formats can be used for different customer groups – for “ordinary” external customers and, for example, for military acceptance. Then the system must be configured to implement different types of technical process support.
The integration of CAD in the overall architecture is a prerequisite for adhering to the PLM concept. However, largely due to the complexities of combining these solutions in Russian practice, projects to ensure full-fledged interaction and their joint work are rare. And each of them is unique.
From an architectural point of view, trilateral integration can be used to unite them: CAPP – PLM, PLM – ERP, ERP – CAPP.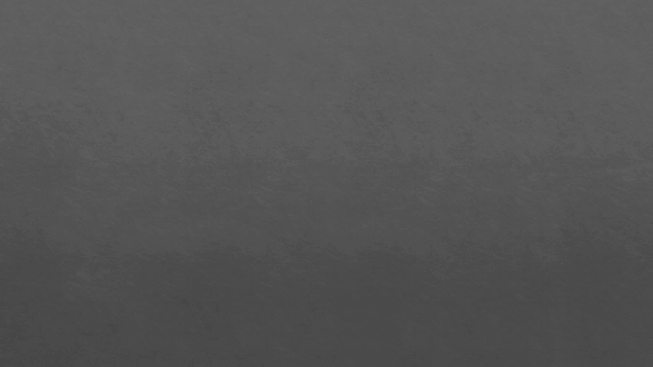
However, the simpler the architecture and the smaller the integration links, the more stable and viable the system is. Therefore, the best option for the architecture is the integration of CAD systems only with PLM as the central link between all engineering applications and the source of necessary information for ERP.
The general approach in such projects assumes that major changes (program improvements) are not made in either PLM or CAD software. The role of the processor and the data interpreter for the two systems must lie with the integration solution. Depending on the complexity of the tasks technologically, this tool can be different – as a simple software add-in that converts data, and, for example, a whole software package that provides data upload, processing, transport and loading into the target system.
Intermediate solution performs data conversion so that they are clear to both PLM and CAD software. One of the most convenient formats for this purpose is the structured list (XML) format. It is in these two issues that the experience and professionalism of the project team can play a decisive role, and it is here that the involvement of consultants familiar with both systems is most often required.
As soon as the question arises of working in two or more systems, the problem of the quality of regulatory reference information RRI and its management issues come to the fore. Implementation options are many: here and CAD with a built-in master data, and a PLM-system with its classifier, and ERP with its. A variant with a separate system for MDM.
The choice of system for storing and managing the RRI is determined by the level of tasks. If it is required to manage technological data in PLM without transferring them to ERP, then the implementation of the RRIs is more logical to implement in the CAD system, since most of the developers of these systems have already provided tools adapted to the requirements of machine builders. Naturally, in this variant the general approach will also change, when simpler logic and means can be used to integrate CAPP and PLM. If an enterprise creates an integrated PLM system for designing technical processes, providing end-to-end design and production support, besides it wants to use ERP capabilities for production planning and management, then it is obvious that it is more convenient to store RRIs in PLM.
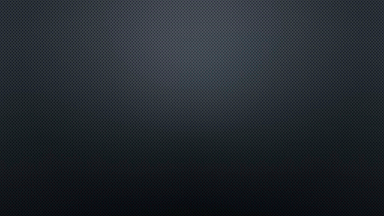
2. CRITERIA FOR THE SELECTION OF CAD PROCESS PRODUCTION PREPARATIONS
To accomplish the task of choosing one of the many existing CAD systems, it is necessary to set some criteria [1,2,3]. These selection criteria include the following:
- Functional system.
- Compliance with current standards and regulations.
- System requirements.
- СCost (license ownership).
- Technical support.
Let us consider in more detail the criteria for the selection of CAD software.
- Functional system. Depending on the nature of the tasks, the type of production and the type of enterprise, a number of requirements can be attributed to the functionality of the system:
- the convenience of the software interface (the criterion, though related to the subjective and individual, but is important when choosing a system);
- Filling in the base delivery (including for various types of processing and execution of calculations for processing options);
- Availability, capabilities and content of the normative reference information modules;
- Opportunities for collective work on the process being developed, in order to reduce the design time;
- Ability to work with control programs;
- The capabilities of the system to control the correctness and completeness of the information in the generated document for the implementation of self-control and norm control;
- Availability and capabilities of automation tools for the development of the technological process;
- System administration capabilities;
- The ability to manage system changes;
- The possibility of expanding the functionality of the system;
- The ability to maintain the current status of technological documentation;
- Protection of information;
- Ability to integrate with CAD / CAM / CAE / PDM systems.
- Compliance with current standards and regulations. The possibility of issuing documentation in accordance with the requirements of USTD, as well as ISO, ANSI, DIN, standards, in the case of enterprises with foreign partners. The presence of Russian, Ukrainian, English, German interface and documentation.
- System requirements. Includes hardware and software requirements and DMS. Here and the ability to work in the dominant operating system (Microsoft - Windows) latest versions, in some cases – the ability to work in the environment of Android, IOS, as well as requirements for the choice of DMS ((for example, Oracle Database, MS SQL Server, PostgreSQL, Firebird, etc.);
- The cost of the system (possession of a CAD software license, leasing opportunities, annual subscriptions, etc.);
- Technical support. Availability and completeness of technical support and supplier services, availability and capabilities of the implementation team at the supplier or in the region, cost of services and technical support.
FINDINGS
CAPP systems are an important component of modern IT technical production preparation platforms, which significantly reduce the duration and increase the productivity of technological preparation of production related to the design of the technology of the product, carrying out the necessary calculations of processing, welding, coating, rationing of labor and materials, the release of the necessary technological documentation . Thus, the choice of CAPP is a complex and important task for the management and users of engineering enterprises. To solve the problem of choosing a CAPP should be guided by the criteria developed (pic.1).
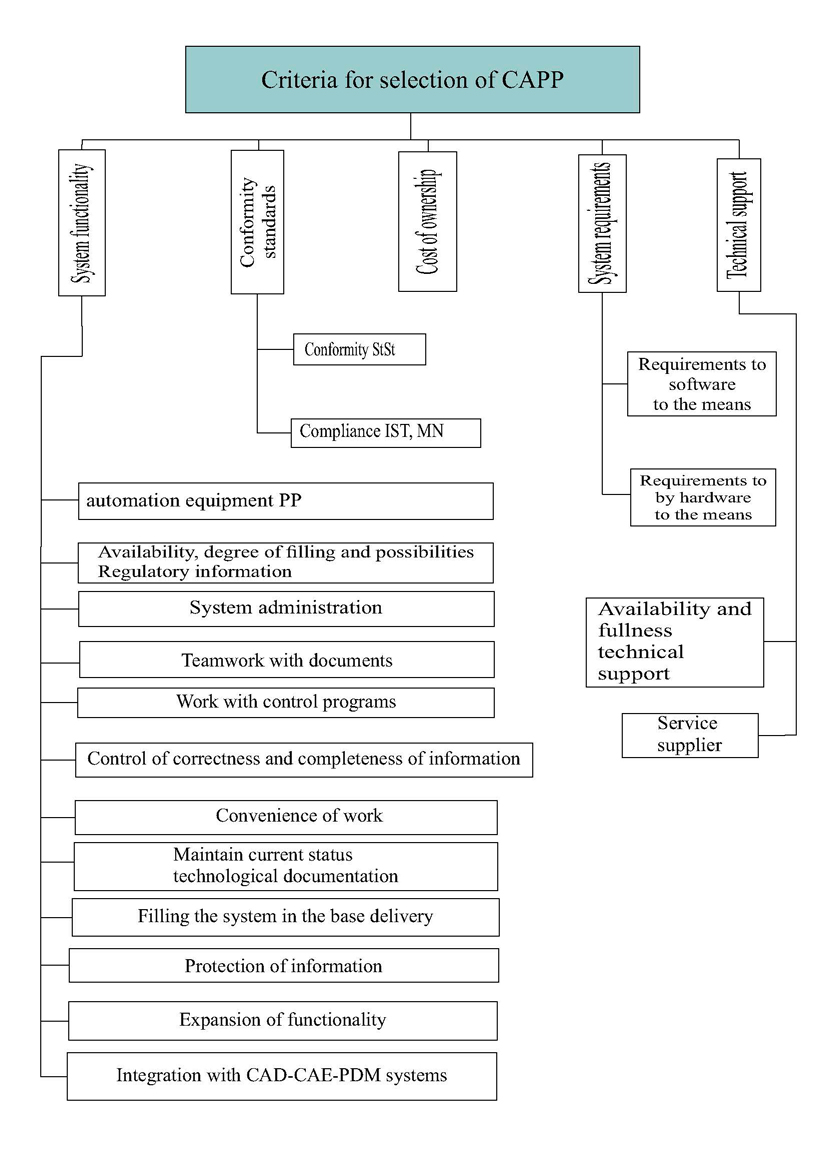
Criteria for selection of CAPP
List of sources
- Горобец И.А., Мишенин А.И., Голубов Н.В. ВЫБОРР САРР СИСТЕМ ДЛЯ ТЕХНОЛОГИЧЕСКОЙ ПОДГОТОВКИ ПРОИЗВОДСТВА – Инженер. Студенческий научно-технический журнал – Донецк: ДонНТУ, 2017. № 1(23)-2(24). С.07-10.
- И.А. Горобец, Н.В. Голубов, А.И. Мишенин Критерии выбора средств САПР технологической подготовки производства – Машиностроение и техносфера ХХ1 века. Сб. трудов ХХV межд. конференции в г. Севастополе 10-16 сентября 2018г. – Донецк: ДонНТУ, 2018. Том 1.– С.247-250
- Горобец И.А., Сидоренко И.В. ЭТАПЫ ВНЕДРЕНИЯ СИСТЕМ АВТОМАТИЗАЦИИ ТЕХНОЛОГИЧЕСКОЙ ПОДГОТОВКИ ПРОИЗВОДСТВА – Инженер. Студенческий научно-технический журнал – Донецк: ДонНТУ, 2016.-№2(20). С.96-99.
- Горобец И.А., Грищенко И.Н. МЕТОДИКА ВНЕДРЕНИЯ СИСТЕМ АВТОМАТИЗАЦИИ ТЕХНИЧЕСКОЙ ПОДГОТОВКИ ПРОИЗВОДСТВА – Сборник трудов XXII международной научно-технической конференции в г. Севастополе 14-21 сентября 2015 г. В 2-х томах. – Донецк: МСМ, 2015. Т. 1.C. 68-72.
- Горобец И.А., Грищенко И.Н., Голубов Н.В. ИССЛЕДОВАНИЯ ПОТРЕБНОСТЕЙ ПРЕДПРИЯТИЙ ОБРАБАТЫВАЮЩЕЙ ПРОМЫШЛЕННОСТИ В САПР И PLM СИСТЕМАХ – Сборник трудов XXII международной научно-технической конференции в г. Севастополе 14-21 сентября 2015 г. В 2-х томах. – Донецк: МСМ, 2015. Т. 1. C. 66-67.
- Горобец И.А., Голенков Е.А., Голубов Н.В. ИСПОЛЬЗОВАНИЕ CALS-ТЕХНОЛОГИЙ В ЖИЗНЕННОМ ЦИКЛЕ МЕХАТРОННОГО ОБОРУДОВАНИЯ - Инженер. Студенческий научно-технический журнал – Донецк: ДонНТУ, 2015.-№1(19). С.179-184
- Горобец И.А., Грищенко И.Н., Голубов Н.В. Выбор автоматизированных систем технической подготовки производства. Машиностроение и техносфера ХХI века.// Сборник трудов ХХI международной научно-технической конференции в г. Севастополь 15-20 сентября 2014г. В 3-х томах. – Донецк: МСМ, 2014. Т.1. 51-53.
- Горобец И.А., Грищенко И.Н. Классификация и критерии выбора автоматизированных систем технической подготовки производства – Материалы пятнадцатой научно-практической конференции
Практика и перспективы развития партнерства в сфере высшей школы
. В 3-х кн. – Таганрог. Изд-во ЮФУ. Кн.3 2014 №14–с.47-53. - Горобец И.А., Грищенко И.Н., Голубов Н.В. Задачи выбора автоматизированных систем технической подготовки производства – Інженер. Студентський науково-технічний журнал – Донецьк: ДонНТУ, 2014. №1(17). С.17-19.
- Горобец И.А., Грищенко И.Н., Голубов Н.В. Классификация автоматизированных систем технической – Інженер. Студентський науково-технічний журнал – Донецьк: ДонНТУ, 2014.-№1(17). С.19-21.