Реферат за темою випускної роботи
Зміст
- Вступ
- 1. Актуальність теми
- 2. Мета і задачі дослідження та заплановані результати
- 3. Основний зміст роботи
- 3.1 Вплив на сили схем шліфування
- 3.2 Параметри круга
- 3.3 Фізичні основи процесу шліфування
- 3.4 Параметри режимів різання
- 4. Рекомендації
- Висновки
- Перелік посилань
Вступ
До нежорстких валів відносяться вали, у яких відношення довжини до діаметру більше 10. Нежорсткі вали широко використовуються в гідроциліндрах приводу подач верстатів, в гідропідйомниках авіаційних, будівельних, дорожніх та інших машин. Точність обробки таких валів відповідає 6...8 квалітетам, шорсткість поверхні Ra=0,63 ... 1,6 мкм. Такі показники точності і якості поверхні зазвичай досягаються шліфуванням.
Внаслідок низької жорсткості даних деталей при їх обробці під дією радіальної складової сили різання відбувається скривлення осі заготовки, внаслідок чого замість циліндричного формується бочкоподібний профіль – діаметри збільшуються від країв до середини перерізу. Для отримання заданої геометричної точності при обробці подібних деталей необхідно проводити кілька проходів, що веде до зниження продуктивності обробки. Тому розробка технологічних способів забезпечення геометричної точності нежорстких валів при круглому шліфуванні є актуальною науковою задачею, що має велике практичне значення.
1. Актуальність теми
Відомий ряд методів забезпечення геометричної точності при шліфуванні нежорстких валів в машинобудуванні. Як і інші види точності при шліфуванні геометрична точність є запорукою не тільки усунення похибки геометричних форм поверхонь (бочкообразности, хвилястості, викривлення осі, овальності і т. д.) , але є запорукою підвищення продуктивності в машинобудуванні.
Магістерська робота присвячена актуальної наукової задачі розробки на забезпечення геометричної точності при шліфуванні не жорстких валів , спрямованого на збільшення продуктивності на виробництві. В якості досвіду використовуються деталь тива вал
,а інструментальними засобами дослідження виступають Solid Works, верстати шліфувальної групи, універсальне складальне пристосування ( УСП ) .
2. Мета і задачі дослідження та заплановані результати
Мета дослідження полягає у визначенні оптимальних сил різання і жорсткості технологічної системи, що забезпечує меншу деформацію заготовки шляхом аналізу теоретичного і практичного матеріалу.
Основні задачі дослідження:
- озглянути поняття і сутність в процесі шліфування необхідної точності обробки.
- Вивчити способи і схеми круглого зовнішнього шліфування.
- Провести аналіз способів забезпечення геометричної точності при шліфуванні нежорстких валів.
- Виявити причини виникнення геометричної не точності при шліфуванні нежорстких валів.
- Вибрати оптимальний шлях вирішення даної задачі.
Об'єкт дослідження: забезпечення точності шліфування валів.
Предмет дослідження: об'єднання методів зменшення апаратурних витрат при реалізації шліфування валів у виробництві.
В рамках магістерської роботи планується отримання актуальних наукових результатів по наступним напрямкам:
- Рішення задачі забезпечення геометричної точності (циліндричності) деталі має два напрямки:
- 1) зниження сил різання
- 2) підвищення жорсткості технологічної системи, що забезпечує меншу деформацію заготовки.
Для експериментальної оцінки отриманих теоретичних результатів і формування фундаменту наступних досліджень, у якості практичних результатівпланується розробка оптимального методу досягнення точності при шліфуванні вала з наступними властивостями:
- Наявність необхідної літератури.
- Наявність необхідного інструменту,обладнання.
3. Основний зміст роботи
Причиною появи бочкообразности при обробці нежорстких валів є прогин заготовки під дією переважно радіальної становить сили різання. Рішення задачі забезпечення геометричної точності (циліндричності) деталі має два напрями: 1) зниження сил різання; 2) підвищення жорсткості технологічної системи, що забезпечує меншу деформацію заготовки.
Другий напрямок вирішується в основному застосуванням рухомих або нерухомих люнетів, які, створюючи додаткову опору, зменшують прогин заготовки.
3.1 Вплив на сили схем шліфування
Зниження сил різання вирішується наступними способами: При шліфуванні діють такі ж сили, як і при інших видах обробки різанням, але їх величина значно менше, так як розміри зрізу невеликі, а різання відбувається при високих швидкостях З схеми сил (рис.1) видно, що рівнодійна R розкладається на три складові: Рz, Ру, Рх і кожна з них є сумою елементарних сил, що виникають в результаті різання окремих абразивних зерен. Найбільшою є радіальна сила Ру, вона в 1,5...3 рази більше сили Рz [1].
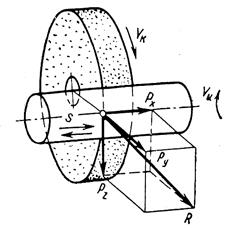
Малюнок 1 – Режими різання при шліфуванні
Пояснюється це тим, що зерна мають негативний кут, а в таких випадках Ру сильно зростає. Сила Ру повинна бути можливо меншою, так як вона викликає прогин деталі, деформує її, припікає. Зменшення Ру досягається зниженням швидкості Vu і подачі Sn (t), своєчасної правкою кола. Величина сили Рх мала і в розрахунках її не враховують. Експериментально встановлено, що сила Рz зростає зі збільшенням Vu, s, Sn і зменшується зі збільшенням Vk.
Шліфування проводиться абразивними колами при рясній подачі в зону різання МОР і є основним методом чистової обробки зовнішніх поверхонь. Розрізняють попереднє, чистове і тонке шліфування. Попереднім шліфуванням забезпечують точність по 8-9 квалітету. Шорсткість поверхні становить 0,4 – 6,3 мкм. Чистове шліфування здійснюють після термічної обробки. Їм забезпечують точність по 6 – 7 квалітету з шорсткістю поверхні 0,2 – 3,2 мкм. Більш висока точність досягається тонким шліфуванням з шорсткістю поверхні 0,025 – 0,1 мкм. Шліфування ділиться на види: кругле і безцентрове [2].
Кругле шліфування зовнішніх циліндричних і конічних поверхонь виконують, на кругло – шліфувальних верстатах причому деталь встановлюється в центрах, патроні або цанге. Існує два основних методи круглого шліфування: з поздовжньою подачею і методом врізання.
Малюнок 1 – кругле шліфування: шліфування з поздовжньою подачею (рис.2а), шліфування методом врізання (рис.2б), глибинне шліфування (рис.2в).
Шліфування з поздовжньою подачею здійснюється зворотно-поступальним переміщенням деталі відносно шліфувального круга. На кожен подвійний хід столу з деталлю коло переміщається до центру заготовки на 0,005 – 0,02 мм. Схема шліфування з поздовжньою подачею представлена на рис 2,а.
Шліфування методом врізання проводиться кругом, ширина якого більше довжини оброблюваної ділянки (рис. 2,б).В даному випадку коло має тільки поперечну подачу. Одночасне шліфування декількох поверхонь методом врізання може бути здійснено фасонним колом (рис. 2,в;). Даний метод більш продуктивний ніж шліфування з поздовжньою подачею, тому його застосовують в масовому і крупносерійному виробництві.
Глибинним шліфуванням (рис. 2,в) за один прохід знімають шар матеріалу на всю необхідну глибину. На шліфувальному крузі формують конічний ділянку довжиною 8 – 12 мм. В ході шліфування конічний ділянку видаляє основну частину шару, що зрізається, а циліндричний ділянку зачищає оброблену поверхню. Поперечна подача відсутня. Шліфувальні круги характеризуються маркою абразивного матеріалу, зернистістю, матеріалом зв'язки, твердістю, структурою, формою, розміром, класом інструменту і класом дисбалансу [2].
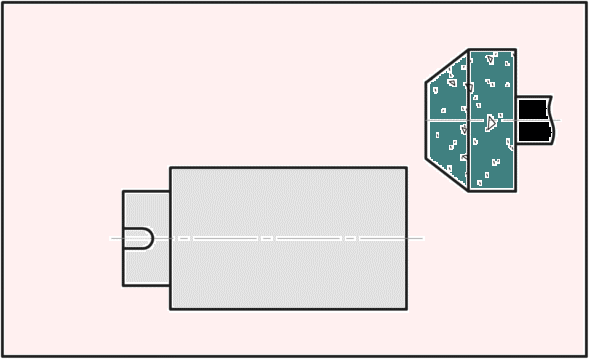
Малюнок 3 – Схема глибинного шліфування(анімація: 8 кадрів, 10 циклів повторення, розмір анімації – 48 кілобайт)
3.2 Параметри круга
Зв'язка
Для виготовлення шліфувальних кругів, брусків і т. д. із зерен абразивного матеріалу, використовується спеціальний матеріал, званий зв'язкою. Зв'язки поділяються на неорганічні (мінеральні) і органічні. З найбільш поширених неорганічних зв'язок є керамічна к, силікатна С і магнезильна М, а з органічних-вулканітова В і бакелітова Б.
Керамічна зв'язка. на якій виготовляють близько 90% шліфувальних кругів та інших інструментів, що складається з вогнетривкої глини, польового шпату, тальку, крейди, кварцу і рідкого скла. Інструменти, виготовлені на цій зв'язці, міцні, мають гарну термохімічну стійкість і добре зберігають профіль. Недолік – висока крихкість.
Вулканітова зв'язка складається з 70% каучуку і 30% сірки. Інструмент, виготовлений на ній, володіє високою еластичністю і найбільшою міцністю, але низьку теплостійкість, тому працювати треба з охолодженням.
Бакелітова зв'язка складається зі штучної смоли, що становить суміш карболової кислоти і формаліну.
Шліфувальні круги на цій зв'язці міцні, еластини, допускають великі окружні швидкості різання. Недолік – підвищена здатність руйнуватися під дією лужних розчинів. Абразиви на цій зв'язці застосовують при тонкому і чистового шліфування, що зменшує небезпеку прижега, крім цього, шліфувальні круги на вулканітовій і бакелітовій зв'язках витримують більш високі окружні швидкості (приблизно в 1,5 більше), ніж на керамічній зв'язці.
Алмазні шліфувальні круги, доводочні бруски роблять на металевій (марок MI, МК, М5, та ін.) і органічної (порошковий бакеліт з наповнювачами марок БІ, Б2, Б3 та ін.) зв'язках. Шліфування виробляють кругами на металевій зв'язці, а доведення – колами неорганічної зв'язці.
Зв'язка служить для отримання абразивного інструменту потрібної форми і визначає міцність кола. Застосовують зв'язки неорганічні і органічні. Неорганічна – керамічна зв'язка (К), складається з вогнетривкої глини, кварцу, рідкого скла та інших Вона володіє високою хімічною, тепло – і вологостійкістю, недорога, має переважне застосування. Недостатня її міцність обмежує швидкість обертання кола до 35 м/сек.
Органічні зв'язки-бакелітові і вулканітові складаються з органічних речовин. Бакелітова в (б) складається з бакеліту-штучної смоли, одержуваної з карболової кислоти і формаліну. Зв'язка міцна, пружна, допускає швидкість кола до 45 ... 50 м / сек, Хімічна і теплова стійкість невисокі. Вона розчиняється в лужному охолоджуючої рідини ( розчин соди у воді) при вмісті соди > 1,5% і втрачає міцність при нагріванні вище 200 С.
Для запобігання від дії лугу кола просочуються парафіном і силікатом. Шліфування ведеться з рясним охолодженням (20...30л/хв). Круги на керамічній зв'язці в 2...3 рази продуктивніше бакелітових, але останні забезпечують кращу якість обробки, без пріжогов. Для попереднього шліфування, як правило, застосовують керамічні кола, а на чистових і доводочних операціях – бакелітові.
Вулканітова зв'язка R (В) виготовляється з вулканізованого каучуку, володіє високою пружністю і міцністю, допускає швидкість кола до 50...60м/с. З неї виготовляють круги відрізні (тонкі) та для безцентрового шліфування. При нагріванні > 150 ?З зв'язка втрачає твердість, тому шліфування ведеться з ЗОР.
Відрізні кола з абразиву ЕБ або КЗ діаметром 100 ... 120мм і товщиною 0,2...0,4 мм виготовляють також на зв'язці ГБ (різновид бакелітової). Їх застосовують для розрізання кремнію, кварцу, кераміки, платини, золота, срібла та ін. [3].
Зернистість
Зернистістю називають номер зерен, що характеризує їх крупність. Абразивні зерна розбиті на 26 номерів зернистості (ГОСТ 3647-59), з них 19 позначені номерами: 200, 160, 125, 100, 80, 63, 50, 40, 32, 25, 20, 16, 12, 10, 8, 6, 5, 4, 3 і сім позначені номерами: М40, М28, М20, М14, М10, М7, М5. Розміри зерна зменшуються від номеру 200 до номеру М5.
Залежно від зернистості Абразивні матеріали поділяються на три групи: шліф-зерна – номери від 200 до 16, шліф-порошки – номери від 12 до 3 і мікропорошки – номери від М40 до М5.
Величина зерна на продуктивність і якість шліфування: чим крупніше зерно, тим продуктивність вище, а чистота і точність обробки нижче. Застосовують зазвичай такі номери зернистості: F10...F12 (200–...100) – грубих робіт; F24...F46 (80...40) – для попереднього, F54...F120 (32...10) – для чистового; F150...F220 (8...5) – для тонкого шліфування і доведення [3].
Твердість круга.
Твердість. Твердістю називають опірність зв'язки виривання абразивних зерен зовнішньою силою. Є суміш ступенів твердості, що складаються кожна з декількох підрозділів.
Характеризується міцністю зв'язки, здатністю її утримувати зерна на поверхні круга. У м'яких кіл зерна утримуються слабо і вони порівняно легко фарбуються, у твердих кіл зерна утримується міцно. Існує наступна шкала твердості: м'які–F, G, H, I, J (М1, М2, МЗ);середньо-м'які K, L (ЗМ1, СМ2); середні M,N (С1, С2); середньо-тверді O,P,Q(СТ1, СТ2, СТЗ); тверді R, S (Т1, Т2); дуже тверді T, V (ВТ1, ВТ2) надзвичайно тверді V, W, X, Y, Z (ЧТ1, ЧТ2). Цифри 1, 2, 3 характеризують зростання ступеня твердості. В процесі шліфування відбувається самозаточування кола. Воно полягає в самовідновленні " ріжучих властивостей кола в процесі експлуатації. Тупі зерна під впливом діючих на них сил вириваються з поверхні круга (зв'язки) або руйнуються і в роботу вступають поруч розташовані гострі зерна або оголені гострі ріжучі грані. Чим швидше і повніше самозатачивается коло, тим інтенсивніше він працює [2].
Ступінь твердості абразивного інструменту
Чим міцніше тримаються зерна, тим твердіше вважається абразивний інструмент. Слід відзначити наступне: чим твердіше шліфований матеріал, тим швидше притупляються зерна кола, а отже, тим м'якше повинен бути обраний коло (слабше зв'язка).
При виборі твердості кола керуються таким правилом: тверді матеріали шліфуються м'якими колами, так як вони інтенсивніше самозаточуються і відновлюють ріжучі здібності; м'які матеріали шліфують більш твердими колами, так як вони повільніше зношуються.
Наприклад, для шліфування деталей із загартованих сталей застосовують кола МОЗ ... СМ1, а для незакалених-СМ2 ... G1. Фасонне шліфування проводиться більш твердими колами для збереження профілю круга.
Круги твердістю ВТ і ЧТ застосовуються для безалмазной правки. Для видалення затупившихся зерен періодично виробляють правку (заточку) кола, інакше він засолюється, тобто на його робочій поверхні налипає метал і шліфування утруднюється [3].
Структура круга
Характеризує внутрішню його будову (мал. 4.) і визначається співвідношенням кількості зерен, зв'язки і пір в одиниці об'єму кола.
Малюнок 4-структури шліфувального кола: а-щільна; б-Середня; в-відкрита; Г–високопориста.
Зерна займають 40...60% обсягу кола. Застосовують 12 структур: від № 1 до № 12 включно. Чим менше номер структури, тим вона щільніше, тим більше зерен в одиниці об'єму, тим менше розмір пір. Структури поділяються на три групи: щільні–№ 1,2,3,4; Середня № 5,6,7; відкриті–№ 8,9,10. Випускаються також високопористі кола зі структурою № 11,12, у яких обсяг пір становить 50...70% від обсягу кола. Вибір структури залежить від в'язкості оброблюваного матеріалу: чим вище в'язкість, тим щільність кола повинна бути менше. В цьому випадку коло засалиться тільки після того, як всі пори будуть заповнені стружкою. Для в'язких матеріалів – міді, алюмінію, пластмас і ін – застосовують кола з відкритою або высокопористой структурою; для твердих і крихких матеріалів – більш щільні, так як вони міцніше і краще зберігають форму; наприклад, для загартованої сталі, чавуну застосовують структуру № 5...6 [3].
Структурою абразивного інструменту називають співвідношення (у відсотках) в одиниці обсягу зерен, зв'язки і пір. Структури позначаються номерами від 0 до 12 і поділяються на 3 групи: щільні структури (№ 0-3), середньої щільності (№4-6) і відкриті (№ 7 – 12).
Чим менше номер структури, тим щільніше розташовані зерна, тим менше пір.
Круги зі структурою 0-3 застосовують при круглому шліфуванні твердих і крихких матеріалів, коли потрібна висока чистота одержуваної поверхні. Структури 4-6 застосовують для зовнішнього круглого шліфування і плоского шліфування м'яких матеріалів, а структури 7-12 для швидкісного шліфування.
Останнім часом застосовують високопористі шліфувальні круги зі структурою № 13 – 18, При швидкісному шліфуванні кола з такою структурою захоплюють повітря, який, створюючи внутрішні повітряні потоки, поглинає тепло, покращуючи тим самим ріжучу здатність абразивних зерен і зменшуючи нагрівання оброблюваної деталі
Клас дисбалансу. Для шліфування кіл він визначає допустимі відхилення від статистичного балансу. Встановлено чотири класи дисбалансу 1, 2, 3 і 4 (ГОСТ 3060-55). Дисбаланс кола збільшується від I-го до 4-го класу.
Клас інструменту. Клас інструменту дає граничні відхилення розмірів. Абразивний інструмент виготовляють двох класів А і Б (ГОСТ 4785-64). Точність інструменту класу А вище, ніж класу Б [4].
3.3 Фізичні основи процесу шліфування
Процес шліфування полягає в нанесенні на поверхню великого числа слідів впливу окремих абразивних зерен. Число і глибина окремих лунок залежать від швидкості, зернистості і структури кола, радіальної сили, що підтискає коло до оброблюваної поверхні. Співвідношення між об'ємом знімається r одиницю часу металу і нормальною силою піджиму є об'єктивною характеристикою ріжучої здатності кола. Так як точність обробки, шорсткість поверхні і знос кола пов'язані з величиною радіальної сили Ру, то ріжучу здатність До кола можна характеризувати об'ємом знімання металу в одиницю часу, що припадають на 10 Н радіальної сили, що виникає при шліфуванні [4].
Різальна здатність круга залежить від умов обробки (режиму різання і правки, характеристики кола, властивостей оброблюваного металу та ін). Ріжуча здатність кола зростає зі збільшенням питомої радіальної сили, швидкості кола, обсягу металу, що знімається в 1 хв, поздовжньої подачі при правці, розмірів зерен і зі зниженням твердості кола. Середні значення ріжучої здатності кола з 1А і 5С при обробці конструкційної сталі 180 – 250 (при ук – 35 м/с) і 250-350 (при г/к – 60 м/с), чавуну – 350 – 500. Експерименти показали, що при обробці загартованої сталі ріжуча здатність зерен 4А вище зерен 1А і 2А. Ріжуча здатність змінюється за період стійкості кола. З затупленням зерен їх здатність до впровадження в оброблювану поверхню знижується. Зниження ріжучої здатності сповільнюється з підвищенням режиму, зі збільшенням діаметра кола і деталі, зі збільшенням абразивних зерен і ударної в'язкості абразиву, зі зменшенням поздовжньої подачі при правці. Для стабілізації ріжучої здатності круга доцільно проводити його правку через малі проміжки часу, не доводячи його до повного притуплення [5].
3.4 Параметри режимів різання
Швидкість шліфування
Швидкість обертання оброблюваної деталі в порівнянні зі швидкістю шліфувального кола дуже мала, то нею нехтують і швидкістю шліфування називають швидкість шліфувального кола.
Швидкість обертання кола має велике значення для процесу шліфування. Продуктивність процесу шліфування зростає зі збільшенням швидкості кола.
Вибирати швидкості потрібно по найбільшим допустимим значенням, зазначеним в ГОСТ 4785 – 64 (в залежності від форми кола, зв'язки, оброблюваного матеріалу, виду шліфування, конструкції верстата) [6].
Тому намагаються користуватися колом найбільшого діаметру, який може бути встановлений на верстаті, і вибирають можливо більше число обертів шпинделя. Обмеженням швидкості кола є, як вже говорили, міцність його і жорсткість верстата, пристосування, деталі. При малій жорсткості системи високі швидкості призводять до вібрацій, що зменшує точність, клас шорсткості оброблюваної поверхні, що збільшує знос кола.[6]
Глибина шліфування (поперечна подача)
При чорновому шліфуванні вигідно працювати з найбільшою глибиною різання (шліфування), що допускається зерном кола, деталлю і верстатом. При цьому глибина різання не повинна перевищувати п'яти сотих поперечного розміру зерна. Так, для кола зернистістю 50 вона повинна бути менше 0,025 мм При збільшенні глибини різання більше допустимої пори кола швидко заповнюються металевою стружкою і коло засолюється.
Глибину шліфування слід зменшувати при обробці нежорсткою деталі, слабо закріпленої на верстаті, і при появі притисків. При опоряджувальному шліфуванні глибина шліфування повинна бути невеликою, що підвищує точність і клас шорсткості обробки.
Тверді і міцні матеріали шліфують на меншу глибину. Із збільшенням глибини шліфування зростає потужність, що витрачається на тертя і дроблення стружки [7].
Поздовжня подача
Поздовжня подача вимірюється в частках ширини кола. Для чорнового шліфування вона становить 0,4 – 0,85 ширини кола за один оборот деталі. Більшу величину подачі, ніж 0,9 приймати не можна, бо при більшій подачі на поверхні шліфованої деталі залишиться гвинтова непрошліфована смуга.
При чистових роботах Поздовжня подача коливається від 0,2 до 0,4 ширини кола за один оборот деталі. Чим більше подача, тим вище продуктивність, але більше шорсткість поверхні. Найбільш раціональні режими різання (vк, vд, ѕпр) вибираються за нормативами, наведеними в довідниках.
При визначенні режимів різання за нормативами спочатку визначають швидкість деталі vд (при прийнятій швидкості кола, розмірах деталі), потім поздовжню подачу ѕпр і поперечну st [7].
Рекомендація:
1. Параметри режиму шліфування слід помножити на коефіцієнт 0,5 – 0,8 при обробці жароміцної сталі і на 1,3 – 1,8 при обробці чавуну.
2. Для чистового шліфування значення поперечної подачі на хід столу не повинні перевищувати значення поперечної подачі попереднього шліфування.
3. При шліфуванні деталей, закріплених в патроні, треба вибирати мінімальні значення поперечної подачі.
4. Для досягнення необхідної шорсткості поверхні в кінці шліфування рекомендується провести один – два проходи без поперечної подачі [8].
Висновки:
Глибину шліфування слід зменшувати при обробці нежорсткою деталі, слабо закріпленої на верстаті, і при появі притисків. При опоряджувальному шліфуванні глибина шліфування повинна бути невеликою, що підвищує точність і клас шорсткості обробки.
Тверді і міцні матеріали шліфують на меншу глибину. Із збільшенням глибини шліфування зростає потужність, що витрачається на тертя і дроблення стружки.
Перелік посилань
- Маталин А.А. Технология машиностроения / А.А. Маталин. – Л.:
Машиностроение
, Ленинград.отд–ние, 1985. – 496 с., ил. - ГМаслов Е.Н. Теория шлифования материалов / Е.Н. Маслов. – М.:
Машиностроение
, 1974. – 320 с. - Лурье Г.Б. Шлифование металлов / Г.Б. Лурье. – М.:
Машиностроение
, 1969. – 172с. - Анурьев В.И. Справочник конструктора – машиностроителя: В 3 т. Т. 3. – 8 – е изд., перераб. и доп. Под ред. И.Н. Жестковой. – М.:
Машиностроение
, 2001. – 864 с. : ил. - Справочник технолога – машиностроителя. В 2 – х т. С74 Т. 1/Под ред. А.Г. Косиловой и Р.К. Мещерякова. – 4 – е изд., перераб. и доп. – М.:
Машиностроение
, 1986. 656 с., ил. - Космачёв И.Г. , Дугин В.Н., Немцев Б. А. Отделочные операции в машиностроении. – Л.: Лениздат, 1985. – 248 с. ил.
- Обработка металлов резанием: Справочник технолога А.А. Панов, В.В. Аникин, Н.Г. Бойм и др.; Под общ. ред. А.А. Панова. – М.:
Машиностроение
, 1988. – 736 с.: ил. - Справочник инструментальщика/ И.А. Ординарцев, Г.В. Филиппов, А.Н. Шевченко и др.; Под общ. ред. И.А. Ординарцева. Л.;
Машиностроение
. Ленинград отделение, 1987, – 846 с.: ил...