Реферат по теме выпускной работы
Содержание
- Введение
- 1. Актуальность темы
- 2. Цель и задачи исследования, планируемые результаты
- 3. Основное содержание работы
- 3.1 Влияние на силы схем шлифования
- 3.2 Параметры круга
- 3.3 Физические основы процесса шлифования
- 3.4 Параметры режимов резания
- 4. Рекомендации
- Выводы
- Список источников
Введение
К нежестким валам относятся валы, у которых отношение длины к диаметру более 10. Нежесткие валы широко используются в гидроцилиндрах привода подач станков, в гидроподъемниках авиационных, строительных, дорожных и других машин. Точность обработки таких валов соответствует 6...8 квалитетам, шероховатость поверхности Ra=0,63…1,6 мкм. Такие показатели точности и качества поверхности обычно достигаются шлифованием.
Вследствие низкой жесткости данных деталей при их обработке под действием радиальной составляющей силы резания происходит искривление оси заготовки, вследствие чего вместо цилиндрического формируется бочкообразный профиль – диаметры увеличиваются от краев к середине сечения. Для получения заданной геометрической точности при обработке подобных деталей необходимо проводить несколько проходов, что ведет к снижению производительности обработки. Поэтому разработка технологических способов обеспечения геометрической точности нежестких валов при круглом шлифовании является актуальной научной задачей, имеющей большое практическое значение.
1. Актуальность темы
Обеспечение геометрической точности при шлифовании нежестких валов в машиностроении. Как и другие виды точности при шлифовании геометрическая точность является залогом не только устранения погрешности геометрических форм поверхностей (бочкообразности, волнистости, искривление оси, овальности и т.д.) , но является залогом повышения производительности в машиностроении.
Магистерская работа посвящена актуальной научной задаче разработки на обеспечение геометрической точности при шлифовании не жестких валов , направленного на увеличение производительности на производстве. В качестве опыта используются деталь тива вал
,а инструментальными средствами исследования выступают Solid Works, станки шлифовальной группы, универсальное сборочное приспособление ( УСП ) .
2. Цель и задачи исследования, планируемые результаты
Цель исследования состоит в определении оптимальных сил резания и жесткости технологической системы, обеспечивающей меньшую деформацию заготовки путём анализа теоретического и практического материала
Основные задачи исследования:
- Рассмотреть понятие и сущность в процессе шлифования требуемой точности обработки.
- Изучить способы и схемы круглого наружного шлифования.
- Провести анализ способов обеспечения геометрической точности при шлифовании нежестких валов.
- Выявить причины возникновения геометрической не точности при шлифовании нежестких валов.
- Выбрать оптимальный путь решения данной задачи.
Объект исследования: обеспечение точности шлифования валов
Предмет исследования: объединение методов уменьшения аппаратурных затрат при реализации шлифования валов в производстве.
В рамках магистерской работы планируется получение актуальных научных результатов по следующим направлениям:
- Решение задачи обеспечения геометрической точности (цилиндричности) детали имеет два направления:
- 1) снижение сил резания
- 2) повышение жесткости технологической системы, обеспечивающей меньшую деформацию заготовки.
Для экспериментальной оценки полученных теоретических результатов и формирования фундамента последующих исследований, в качестве практических результатов планируется разработка оптимального метода достижения точности при шлифовании вала со следующими свойствами:
- Наличие необходимой литературы.
- Наличие необходимого инструмента,оборудования.
3. Основное содержание работы
Причиной появления бочкообразности при обработке нежестких валов является прогиб заготовки под действием преимущественно радиальной составляющий силы резания. Решение задачи обеспечения геометрической точности (цилиндричности) детали имеет два направления: 1) снижение сил резания; 2) повышение жесткости технологической системы, обеспечивающей меньшую деформацию заготовки.
Второе направление решается в основном применением подвижных или неподвижных люнетов, которые создавая дополнительную опору, уменьшают прогиб заготовки.
3.1 Влияние на силы схем шлифования
Снижение сил резания решается следующими способами: При шлифовании действуют такие же силы, как и при других видах обработки резанием, но их величина значительно меньше, так как размеры среза небольшие, а резание происходит при высоких скоростях Из схемы сил (рис.1) видно, что равнодействующая R разлагается на три составляющие: Рz, Ру, Рх и каждая из них является суммой элементарных сил, возникающих в результате резания отдельных абразивных зерен. Наибольшей является радиальная сила Ру, она в 1,5…3 раза больше силы Рz [1].
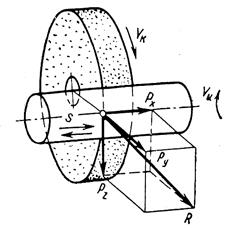
Рисунок 1 – Режимы резания при шлифовании
Объясняется это тем, что зерна имеют отрицательный угол, а в таких случаях Ру сильно возрастает. Сила Ру должна быть возможно меньшей, так как она вызывает прогиб детали, деформирует ее, прижигает. Уменьшение Ру достигается снижением скорости Vu и подачи Sn (t), своевременной правкой круга. Величина силы Рх мала и в расчетах ее не учитывают. Экспериментально установлено, что сила Рz возрастает с увеличением Vu, s, Sn и уменьшается с увеличением Vk [4].
Шлифование производится абразивными кругами при обильной подаче в зону резания СОЖ и является основным методом чистовой обработки наружных поверхностей. Различают предварительное, чистовое и тонкое шлифование. Предварительным шлифованием обеспечивают точность по 8 – 9 квалитету. Шероховатость поверхности составляет 0,4 – 6,3 мкм. Чистовое шлифование осуществляют после термической обработки. Им обеспечивают точность по 6–7 квалитету с шероховатостью поверхности 0,2 – 3,2 мкм. Более высокая точность достигается тонким шлифованием с шероховатостью поверхности 0,025 – 0,1 мкм. Шлифование делится на вида: круглое и бесцентровое [2].
Круглое шлифование наружных цилиндрических и конических поверхностей выполняют, на кругло – шлифовальных станках причем деталь устанавливается в центрах, патроне или цанге. Существует два основных метода круглого шлифования: с продольной подачей и методом врезания [1].
Рисунок 1 – круглое шлифование: шлифование с продольной подачей (рис.2а), шлифование методом врезания (рис.2б), глубинное шлифование (рис.2в).
Шлифование с продольной подачей осуществляется возвратно-поступательным перемещением детали относительно шлифовального круга. На каждый двойной ход стола с деталью круг перемещается к центру заготовки на 0,005 – 0,02 мм. Схема шлифования с продольной подачей представлена на рис 2,а.
Шлифование методом врезания производится кругом, ширина которого больше длины обрабатываемого участка (рис. 2,б).В данном случае круг имеет только поперечную подачу. Одновременное шлифование нескольких поверхностей методом врезания может быть осуществлено фасонным кругом (рис. 2,в;). Данный метод более производителен чем шлифование с продольной подачей, поэтому его применяют в массовом и крупносерийном производстве.
Глубинным шлифованием (рис. 2,в) за один проход снимают слой материала на всю необходимую глубину. На шлифовальном круге формируют конический участок длиной 8 – 12 мм. В ходе шлифования конический участок удаляет основную часть срезаемого слоя, а цилиндрический участок зачищает обработанную поверхность. Поперечная подача отсутствует. Шлифовальные круги характеризуются маркой абразивного материала, зернистостью, материалом связки, твердостью, структурой, формой, размером, классом инструмента и классом дисбаланса [2].
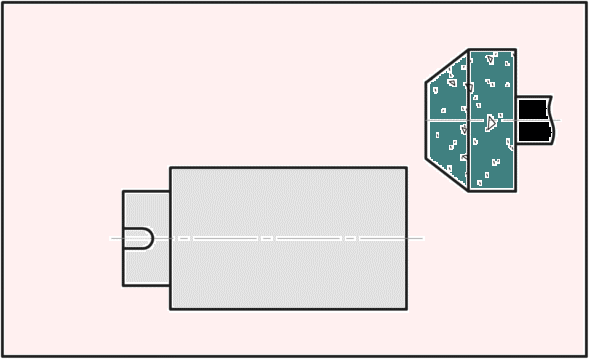
Рисунок 3 – Схема глубинного шлифования(анимация: 8 кадров, 10 циклов повторения, размер анимации –48 килобайт)
3.2 Параметры круга
Связка
Для изготовления шлифовальных кругов, брусков и т.д. из зерен абразивного материала, используется специальный материал, называемый связкой. Связки разделяются на неорганические (минеральные) и органические. Из наиболее распространенных неорганических связок является керамическая К, силикатная С и магнезильная М, а из органических – вулканитовая В и бакелитовая Б.
Керамическая связка. на которой изготовляют около 90% шлифовальных кругов и других инструментов, состоит из огнеупорной глины, полевого шпата, талька, мела, кварца и жидкого стекла. Инструменты, изготовленные на этой связке, прочны, обладают хорошей термохимической стойкостью и хорошо сохраняют профиль. Недостаток – высокая хрупкость.
Вулканитовая связка состоит из 70% каучука и 30% серы. Инструмент, изготовленный на ней, обладает высокой эластичностью и наибольшей прочностью, но низкой теплостойкостью, поэтому работать надо с охлаждением.
Бакелитовая связка состоит из искусственной смолы, составляющей смесь карболовой кислоты и формалина.
Шлифовальные круги на этой связке прочны, эластины, допускают большие окружные скорости резания. Недостаток – повышенная способность разрушаться под действием щелочных растворов. Абразивы на этой связке применяют при тонком и чистовом шлифовании, что уменьшает опасность прижега, кроме этого, шлифовальные круги на вулканитовой и бакелитовой связках выдерживают более высокие окружные скорости (примерно в 1,5 больше), чем на керамической связке.
Алмазные шлифовальные круги, доводочные бруски делают на металлической (марок MI, МК, М5, и др.) и органической (порошковый бакелит с наполнителями марок БI, Б2, Б3 и др.) связках. Шлифование производят кругами на металлической связке, а доводку – кругами неорганической связке.
Связка служит для получения абразивного инструмента нужной формы и определяет прочность круга. Применяют связки неорганические и органические. Неорганическая – керамическая связка (К), состоит из огнеупорной глины, кварца, жидкого стекла и др. Она обладает высокой химической, тепло- и влагостойкостью, недорогая, имеет преимущественное применение. Недостаточная ее прочность ограничивает скорость вращения круга до 35 м/сек.
Органические связки – бакелитовые и вулканитовые состоят из органических веществ. Бакелитовая В (Б) состоит из бакелита – искусственной смолы, получаемой из карболовой кислоты и формалина. Связка прочная, упругая, допускает скорость круга до 45…50 м/сек, химическая и тепловая стойкость невысокие. Она растворяется в щелочной охлаждающей жидкости ( раствор соды в воде) при содержании соды > 1,5% и теряет прочность при нагреве выше 200 С.
Для предохранения от действия щелочи круги пропитываются парафином и силикатом. Шлифование ведется с обильным охлаждением (20…30л/мин). Круги на керамической связке в 2…3 раза производительнее бакелитовых, но последние обеспечивают лучшее качество обработки, без прижогов. Для предварительного шлифования, как правило, применяют керамические круги, а на чистовых и доводочных операциях – бакелитовые.
Вулканитовая связка R (В) изготовляется из вулканизированного каучука, обладает высокой упругостью и прочностью, допускает скорость круга до 50…60м/с. Из нее изготовляют круги отрезные (тонкие) и для бесцентрового шлифования. При нагреве > 150 ?С связка теряет твердость, поэтому шлифование ведется с СОЖ.
Отрезные круги из абразива ЭБ или КЗ диаметром 100…120мм и толщиной 0,2…0,4мм изготовляют также на связке ГБ (разновидность бакелитовой). Их применяют для разрезки кремния, кварца, керамики, платины, золота, серебра и др [3].
Зернистость.
Зернистостью называют номер зерен, характеризующий их крупность. Абразивные зерна разбиты на 26 номеров зернистости (ГОСТ 3647-59), из них 19 обозначены номерами: 200, 160, 125, 100, 80, 63, 50, 40, 32, 25, 20, 16, 12, 10, 8, 6, 5, 4, 3 и семь обозначены номерами: М40, М28, М20, М14, М10, М7, М5. Размеры зерна уменьшаются от номера 200 к номеру М5.
В зависимости от зернистости абразивные материалы подразделяются на три группы: шлиф-зерна – номера от 200 до 16, шлиф-порошки – номера от 12 до 3 и микропорошки – номера от М40 до М5.
Величина зерна на производительность и качество шлифования: чем крупнее зерно, тем производительность выше, а чистота и точность обработки ниже. Применяют обычно следующие номера зернистости: F10…F12 (200 –…100) – грубых работ; F24…F46 (80…40) – для предварительного, F54…F120 (32…10) – для чистового; F150…F220 (8…5) – для тонкого шлифования и доводки [3].
Твердость круга.
Твердость. Твердостью называют сопротивляемость связки вырыванию абразивных зерен внешней силой. Имеется смесь степеней твердости, состоящих каждая из нескольких подразделений.
Характеризуется прочностью связки, способностью ее удерживать зерна на поверхности круга. У мягких кругов зерна удерживаются слабо и они сравнительно легко выкрашиваются, у твердых кругов зерна удерживается прочно. Существует следующая шкала твердости: мягкие- F, G, H, I, J (М1, М2, МЗ);средне-мягкие K, L (СМ1, СМ2); средние M,N (С1, С2); средне-твердые O,P,Q(СТ1, СТ2, СТЗ); твердые R, S (Т1, Т2); весьма твердые T, V (ВТ1, ВТ2) чрезвычайно твердые V, W, X, Y, Z (ЧТ1, ЧТ2). Цифры 1, 2, 3 характеризуют возрастание степени твердости. В процессе шлифования происходит самозатачивание круга. Оно заключается в самовосстановлении режущих свойств круга в процессе эксплуатации. Затупившиеся зерна под влиянием действующих на них сил вырываются из поверхности круга (связки) или разрушаются и в работу вступают рядом расположенные острые зерна или обнаженные острые режущие грани. Чем быстрее и полнее самозатачивается круг, тем интенсивнее он работает [3].
Степень твердости абразивного инструмента
Чем прочнее держатся зерна, тем тверже считается абразивный инструмент. Следует отметить следующее: чем тверже шлифуемый материал, тем быстрее притупляются зерна круга, а следовательно, тем мягче должен быть выбран круг (слабее связка).
При выборе твердости круга руководствуются следующим правилом: твердые материалы шлифуются мягкими кругами, так как они интенсивнее самозатачиваются и восстанавливают режущие способности; мягкие материалы шлифуют более твердыми кругами, так как они медленнее изнашиваются.
Например, для шлифования деталей из закаленных сталей применяют круги МЗ…СМ1, а для незакаленных – СМ2…G1. Фасонное шлифование производится более твердыми кругами для сохранения профиля круга.
Круги твердостью ВТ и ЧТ применяются для без алмазной правки. Для удаления затупившихся зерен периодически производят правку (заточку) круга, иначе он засаливается, т. е. на его рабочей поверхности налипает металл и шлифование затрудняется [3].
Структура круга
Характеризует внутреннее его строение (рис. 4.) и определяется соотношением количества зерен, связки и пор в единице объема круга.
Рисунок 4 – Структуры шлифовального круга:а – плотная; б – средняя; в – открытая; г – высокопористая.
Зерна занимают 40…60% объема круга. Применяют 12 структур: от № 1 до № 12 включительно. Чем меньше номер структуры, тем она плотнее, тем больше зерен в единице объема, тем меньше размер пор. Структуры делятся на три группы: плотные – № 1,2,3,4; средняя №5,6,7 ; открытые – № 8,9,10. Выпускаются также высокопористые круги со структурой № 11,12, у которых объем пор составляет 50…70% от объема круга. Выбор структуры зависит от вязкости обрабатываемого материала: чем выше вязкость, тем плотность круга должна быть меньше. В этом случае круг засалится только после того, как все поры будут заполнены стружкой. Для вязких материалов – меди, алюминия, пластмасс и др. – применяют круги с открытой или высокопористой структурой; для твердых и хрупких материалов – более плотные, так как они прочнее и лучше сохраняют форму; например, для закаленной стали, чугуна применяют структуру № 5…6 [2].
Структурой абразивного инструмента называют соотношение (в процентах) в единице объема зерен, связки и пор. Структуры обозначаются номерами от 0 до 12 и разделяются на 3 группы: плотные структуры (№ 0 – 3), среднеплотные (№4 – 6) и открытые (№ 7 – 12).
Чем меньше номер структуры, тем плотнее расположены зерна, тем меньше пор.
Круги со структурой 0 – 3 применяют при круглом шлифовании твердых и хрупких материалов, когда требуется высокая чистота получаемой поверхности. Структуры 4 – 6 применяют для наружного круглого шлифования и плоского шлифования мягких материалов, а структуры 7 – 12 для скоростного шлифования.
В последнее время применяют высокопористые шлифовальные круги со структурой № 13 – 18, При скоростном шлифовании круги с такой структурой захватывают воздух, который, создавая внутренние воздушные потоки, поглощает тепло, улучшая тем самым режущую способность абразивных зерен и уменьшая нагрев обрабатываемой детали.
Класс дисбаланса. Для шлифования кругов он определяет допустимые отклонения от статистического баланса. Установлены четыре класса дисбаланса 1, 2, 3 и 4 (ГОСТ 3060 – 55). Дисбаланс круга увеличивается от I – го к 4 – му классу.
Класс инструмента. Класс инструмента дает предельные отклонения размеров. Абразивный инструмент изготовляют двух классов А и Б (ГОСТ 4785 – 64). Точность инструмента класса А выше, чем класса Б [3].
3.3 Физические основы процесса шлифования
Процесс шлифования состоит в нанесении на поверхность большого числа следов воздействия отдельных абразивных зерен. Число и глубина отдельных лунок зависят от скорости, зернистости и структуры круга, радиальной силы, поджимающей круг к обрабатываемой поверхности. Соотношение между объемом снимаемого r единицу времени металла и нормальной силой поджима является объективной характеристикой режущей способности круга. Так как точность обработки, шероховатость поверхности и износ круга связаны с величиной радиальной силы Ру, то режущую способность круга К можно характеризовать объемом снимаемого металла в единицу времени, приходящимся на 10 Н радиальной силы, возникающей при шлифовании [4].
Режущая способность круга зависит от условий обработки (режима резания и правки, характеристики круга, свойств обрабатываемого металла и др.). Режущая способность круга возрастает с увеличением удельной радиальной силы, скорости круга, объема снимаемого металла в 1 мин, продольной подачи при правке, размеров зерен и с понижением твердости круга. Средние значения режущей способности круга из 1А и 5С при обработке конструкционной стали 180 – 250 (при ук – 35 м/с) и 250 – 350 (при г/к – 60 м/с), чугуна – 350 – 500. Эксперименты показали, что при обработке закаленной стали режущая способность зерен 4А выше зерен 1А и 2А. Режущая способность изменяется за период стойкости круга. С затуплением зерен их способность к внедрению в обрабатываемую поверхность снижается. Снижение режущей способности замедляется с повышением режима, с увеличением диаметра круга и детали, с увеличением абразивных зерен и ударной вязкости абразива, с уменьшением продольной подачи при правке. Для стабилизации режущей способности круга целесообразно производить его правку через малые промежутки времени, не доводя его до полного притупления [5].
3.4 Параметры режимов резания
Скорость шлифования
Скорость вращения обрабатываемой детали по сравнению со скоростью шлифовального круга очень мала, то ею пренебрегают и скоростью шлифования называют скорость шлифовального круга.
Скорость вращения круга имеет большое значение для процесса шлифования. Производительность процесса шлифования возрастает с увеличением скорости круга.
Выбирать скорости нужно по наибольшим допустимым значениям, указанным в ГОСТ 4785 – 64 (в зависимости от формы круга, связки, обрабатываемого материала, вида шлифования, конструкции станка) [6].
Поэтому стараются пользоваться кругом наибольшего диаметра, который может быть установлен на станке, и выбирают возможно большее число оборотов шпинделя. Ограничением скорости круга является, как уже говорили, прочность его и жесткость станка, приспособления, детали. При малой жесткости системы высокие скорости приводят к вибрациям, уменьшающим точность, класс шероховатости обрабатываемой поверхности, увеличивающим износ круга [6].
Глубина шлифования (поперечная подача)
При черновом шлифовании выгодно работать с наибольшей глубиной резания (шлифования), допускаемой зерном круга, деталью и станком. При этом глубина резания не должна превышать пяти сотых поперечного размера зерна. Так, для круга зернистостью 50 она должна быть менее 0,025 мм. При увеличении глубины резания более допустимой поры круга быстро заполняются металлической стружкой и круг засаливается.
Глубину шлифования следует уменьшать при обработке нежесткой детали, слабо закрепленной на станке, и при появлении прижогов. При отделочном шлифовании глубина шлифования должна быть небольшой, что повышает точность и класс шероховатости обработки.
Твердые и прочные материалы шлифуют на меньшую глубину. С увеличением глубины шлифования возрастает мощность, затрачиваемая на трение и дробление стружки [7].
Продольная подача
Продольная подача измеряется в долях ширины круга. Для чернового шлифования она составляет 0,4 – 0,85 ширины круга за один оборот детали. Большую величину подачи, чем 0,9 принимать нельзя, ибо при большей подаче на поверхности шлифуемой детали останется винтовая непрошлифованная полоса.
При чистовых работах продольная подача колеблется от 0,2 до 0,4 ширины круга за один оборот детали. Чем больше подача, тем выше производительность, но больше шероховатость поверхности. Наиболее рациональные режимы резания (vк, vд, sпр) выбираются по нормативам, приведенным в справочниках.
При определении режимов резания по нормативам вначале определяют скорость детали vд (при принятой скорости круга, размерах детали), затем продольную подачу sпр и поперечную st [7].
Рекомендации:
1. Параметры режима шлифования следует умножить на коэффициент 0,5 – 0,8 при обработке жаропрочной стали и на 1,3 – 1,8 при обработке чугуна.
2. Для чистового шлифования значения поперечной подачи на ход стола не должны превышать значения поперечной подачи предварительного шлифования.
3. При шлифовании деталей, закрепленных в патроне, надо выбирать минимальные значения поперечной подачи.
4. Для достижения необходимой шероховатости поверхности в конце шлифования рекомендуется провести один – два прохода без поперечной подачи [8].
Вывод:
Глубину шлифования следует уменьшать при обработке нежесткой детали, слабо закрепленной на станке, и при появлении прижогов. При отделочном шлифовании глубина шлифования должна быть небольшой, что повышает точность и класс шероховатости обработки.
Твердые и прочные материалы шлифуют на меньшую глубину. С увеличением глубины шлифования возрастает мощность, затрачиваемая на трение и дробление стружки.
Список источников
- Маталин А.А. Технология машиностроения / А.А. Маталин. – Л.:
Машиностроение
, Ленинград.отд – ние, 1985. – 496 с., ил. - ГМаслов Е.Н. Теория шлифования материалов / Е.Н. Маслов. – М.:
Машиностроение
, 1974. – 320 с. - Лурье Г.Б. Шлифование металлов / Г.Б. Лурье. – М.:
Машиностроение
, 1969. – 172с. - Анурьев В.И. Справочник конструктора – машиностроителя: В 3 т. Т. 3. – 8-е изд., перераб. и доп. Под ред. И.Н. Жестковой. – М.:
Машиностроение
, 2001. – 864 с. : ил. - Справочник технолога – машиностроителя. В 2-х т. С74 Т. 1/Под ред. А.Г. Косиловой и Р.К. Мещерякова. – 4-е изд., перераб. и доп. – М.:
Машиностроение
, 1986. 656 с., ил. - Космачёв И.Г. , Дугин В.Н., Немцев Б. А. Отделочные операции в машиностроении. – Л.: Лениздат, 1985. – 248 с. ил.
- Обработка металлов резанием: Справочник технолога А.А. Панов, В.В. Аникин, Н.Г. Бойм и др.; Под общ. ред. А.А. Панова. – М.:
Машиностроение
, 1988. – 736 с.: ил. - Справочник инструментальщика/ И.А. Ординарцев, Г.В. Филиппов, А.Н. Шевченко и др.; Под общ. ред. И.А. Ординарцева. Л.;
Машиностроение
. Ленинград отделение, 1987, – 846 с.: ил..