Внимание! На момент написания данного реферата магистерская работа еще не завершена. Предполагаемая дата завершения: июль 2019 г. Полный текст работы, а также материалы по теме могут быть получены у автора после указанной даты. По всем вопросам обращаться по адресу stepa.sergey.nov@mail.com
Содержание
- Введение
- 1. Актуальность темы
- 2. Цель и задачи исследования
- 3. Исследование условий работы линий расфасовки сыпучих материалов
- 3.1 Виды дозаторов
- 3.2 Виды упаковочных машин
- 3.3 Дозирование сыпучих материалов в производственных условиях
- Список источников
Введение
Объем операций с сыпучими материалами на предприятиях химической, пищевой промышленностях, в сельском хозяйстве и строительстве на территории всего постсоветского пространства исчисляется миллиардами тонн. Значительная часть этих материалов подвергается процессам дозирования, с последующей упаковкой и транспортировкой. Интенсификация технологических процессов с внедрением непрерывных технологических операций определяет повышенные требования к бункерным установкам, устройствам для автоматизированной подачи сыпучего материала в дозатор, а также к дозирующим устройствам.
Автоматизация это одно из направлений научно-технического прогресса, использующее саморегулирующие технические средства и математические методы с целью освобождения человека от участия в процессах получения, преобразования, передачи и использования энергии, материалов, изделий или информации, либо существенного уменьшения степени этого участия или трудоёмкости выполняемых операций. Автоматизация позволяет повысить производительность труда, улучшить качество продукции, оптимизировать процессы управления, отстранить человека от производств, опасных для здоровья; требует комплексного, системного подхода к решению задачи. В состав систем автоматизации входят датчики (сенсоры), устройства ввода, управляющие устройства (контроллеры), исполнительные устройства, устройства вывода, компьютеры [7].
Основная тенденция развития систем автоматизации идет в направлении создания автоматических систем, которые способны выполнять заданные функции или процедуры без участия человека. Роль человека заключается в подготовке исходных данных, выборе алгоритма (метода решения) и анализе полученных результатов. Также в подобных системах предусматривается постепенно наращиваемая защита от нестандартных событий (аварий) или способы их обхода [7].
1. Актуальность темы
Современный рынок основан на конкуренции производителей, успех которых оценивается не по объемам производимой продукции, а по уровню эффективности производства. Этот уровень определяется степенью удовлетворения потребителя с наименьшими затратами. В настоящее время процессы автоматизации по дозированию, упаковке и транспортирове сыпучих материалов занимают одно из ведущих мест в отраслях пищевой, химической, металлургической промышленностях, в строительстве и сельском хозяйстве.
Важным этапом в транспортно-технологических схемах доставки сыпучих материалов от производителя к потребителю является процесс их расфасовки в различные виды тары. Так как дозирование материалов на производстве неотъемлемо связано с их расфасовкой и транспортировкой, во многих случаях за счет физической силы человека, что в свою очередь сопровождается сильным пылевыделением и несет определенную опасность для здоровья человека, возникает необходимость применения автоматических дозирующих и упаковочных линий. Ввиду отсутствия единой модели сыпучей среды возникает необходимость в проведении более тщательного изучения свойств сыпучих материалов при их расфасовке и упаковке [12].
2. Цель и задачи исследования
Целью работы является повышение эффективности полуавтоматических расфасовочных линий сыпучих материалов
Для достижения поставленной цели необходимо решить следующие задачи:
- Исследовать условия работы линий расфасовки сыпучих материалов;
- Определить реологические характеристики характерных сыпучих материалов;
- Классифицировать грузы по текучести и объемному весу;
- Выбрать соответствующие захватные устройства для подачи тары к загрузочному устройству и выдачи загрeженной тары на транспортирующее устройство;
- Разработать алгоритм и провести анализ пневмогидравлической системы для работы манипулятора, в том числе с управлением от программируемого контроллера;
- Проанализировать динамические свойства исполнительных механизмов;
- Выполнить физическое моделирование и уточнить параметры системы расфасовки сыпучих материалов.
3. Исследование условий работы линий расфасовки сыпучих материалов
3.1 Виды дозаторов
На сегодняшний день различают три основных способа дозирования сыпучих веществ: массовый, весовой и объемный.
Весовой способ дозирования основан на измерении веса продукта и отмеривания его по данному критерию с использованием стандартных мер веса – килограмм и грамм. Весовой способ применим практически к любым видам продукта (веществ) и является наиболее распространенным. Единственным исключением являются жидкости и пасты, которые более привычно измерять в литрах или см3 и дозировать объемным или массовым способом [8].
Массовый способ дозирования использует принцип измерения количества продукта, прошедшего (подаваемого) через определенное пространство и применяется, преимущественно, для дозирования жидкостей, паст и газов. Измерение доз в массовом способе происходит с помощью см3 или литров. Наиболее классическим применением массового способа дозирования являются терминалы слива/налива нефтепродуктов [8].
Объемный способ дозирования основан на принципе заполнения продуктом определенного свободного пространства и использует для измерения стандартные меры объема – см3 или литры. В основном, применяется для дозирования жидкостей, паст и газов, но может также использоваться для дозирования различных сыпучих материалов. При этом, объемное дозирование сыпучих продуктов предполагает дальнейший пересчет объемных мер в более привычные весовые [8].
Наиболее применимыми и распространенными дозаторами для сыпучих веществ являются: шнековые, объемные и весовые дозаторы.
Шнековый дозатор – применяется для дозирования сыпучих продуктов, порошков, зернистых материалов (не подвергающихся измельчению), гранул, паст, а также при дозировании суспензий, радиоактивных и других сред, в которых недопустимо сдавливание среды, для обеспечения постоянного расхода. Обычно обладают сравнительно невысокой точностью, просты и надежны, но не способны создать значительный напор жидкости, а также не соответствуют требованиям к компактности и герметичности. Представляет собой, в основном, шнек, заключённый в кожух; рабочий инструмент данного типа может располагаться вертикально, горизонтально или под наклоном, встречаются дозаторы с несколькими шнеками [8].
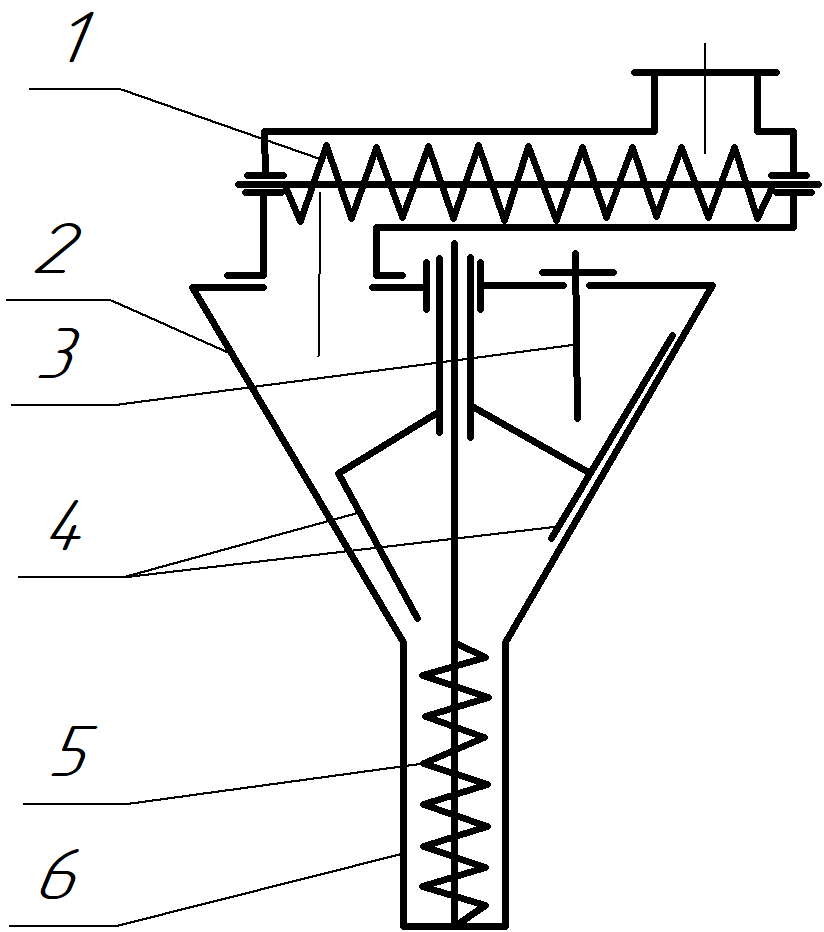
Принципиальная схема шнекового дозатора с двумя шнеками
- Питающий шнек;
- Конический бункер;
- Датчик уровня продукта;
- Лопасти мешалки;
- Дозирующий шнек;
- Корпус дозирующего шнека (кожух).
Объемный дозатор – при помощи данного вида дозаторов дозируют газы, жидкости, пасты, а также твёрдые сыпучие материалы; такие дозаторы просты по конструкции и вполне надёжны, широко применяются в пищевой и иных отраслях промышленности при подаче жидких и сухих дисперсных материалов. Отличаются долговечностью и удобством в эксплуатации. Их производительность регулируют с помощью изменения скорости наполнения, времени цикла или объёма; имеют невысокую погрешность.
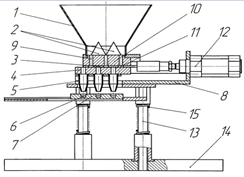
Устройство для объемного дозирования сыпучих материалов
- Загрузочный бункер;
- Ворошитель;
- Шиберная заслонка;
- Питатель;
- Течки;
- Соосная матрица;
- Съемная паллета;
- Подпружиненный инструментальный стол;
- Отводящие каналы;
- Распределительная решетка;
- Мерные емкости;
- Пневмоцилиндр;
- Вертикальные колонки;
- Станина;
- Пружины.
Использование объемного дозатора накладывает определенные ограничения на процесс дозирования:
- Для сыпучих продуктов объемные меры приходится пересчитывать в более привычные весовые. При этом такой пересчет требуется для
каждого вида дозируемого продукта, поскольку продукты с разной плотностью, при одном и том же объеме
стакана
, будут иметь разные весовые показатели. - Пределы дозирования ограничены размерами
стакана
. И хоть производители дозаторов и пытаются делатьстаканы
с регулируемым внутренним объемом, все равно существуют некие пределы, в привязке к изначальному размерустакана
, выйти за которые дозатор не в силах. - Не каждый сыпучий продукт способен быстро просыпаться и качественно заполнять объем
стакана
, особенно в высоком темпе автоматического режима. Липкие, маслянистые или легкие продукты, такие как изюм, инжир, курага, кукурузные палочки, практически невозможно дозировать данным дозатором, поскольку ихтрудносыпучесть
приводит к существенным отклонениям в размерах и весе доз.
Весовой дозатор предназначен для дозирования весовым способом любых сыпучих продуктов за исключением порошкообразных пылящих.
Проблема пылящих продуктов та же, что и у объемного дозатора – возникновение пыли мешает нормальной работе оборудования и загрязняет
упаковочный материал. В остальном весовой дозатор способен дозировать даже трудносыпучие
продукты. Современные весовые дозаторы для
сыпучих продуктов обладают уникальной способностью – они адаптируются под определенные продукты. Также среди достоинств отмечается компактность
датчиков давления, универсальность (процессы взвешивания и дозирования полностью автоматизированы, управление весами сводится к управлению
прибором загрузки), оптимальная точность и большая производительность. Весовые дозаторы конструируются таким образом, чтобы высота падения
сыпучих веществ была минимальной. Кроме того, комбинационные дозаторы оснащаются специальными трассами, по которым и движутся продукты.
Благодаря этому практически полностью исключается возможность повреждения даже самых хрупких продуктов при их фасовке. К недостаткам можно
отнести необходимость предварительного определения гидростатического давления от веса продукта в ёмкости, низкая скорость работы. В сравнении с
объёмными сложны, поэтому имеют малую эксплуатационную надежность и высокую стоимость.
Данный тип дозатора состоит из вибролотка, взвешивающего ковша, подвешенного на тензодатчике и блока управления. Дозирование происходит путем засыпания продукта вибролотком во взвешивающий ковш до достижения весового показателя, выставленного оператором на блоке управления. Когда требуемый вес достигнут, вибролоток останавливается, а ковш высывает свое содержимое в тубус или лейку.
3.2 Виды упаковочных машин
Использование механических устройств для упаковки сыпучих продуктов в несколько раз повышает скорость и эффективность процесса по сравнению с ручной фасовкой. Ориентируясь на бюджет, можно выбрать агрегат следующих видов:
- Полуавтоматический или автоматический станок. Обеспечивает полный технологический цикл от развешивания (дозирования) до запечатывания пачек. Автоматические самостоятельно склеивают упаковки. Необходимо только заправить аппарат пленкой;
- Станки с объемным или весовым дозатором. Первые отмеряют продукт по объему, вторые – по массе. Весовые дозаторы пользуются большим спросом на рынке, дополнительно они комплектуются мультиголовками, позволяющими очень точно развесить даже малые количества сыпучих продуктов, например, специй;
- Горизонтальные или вертикальные механизмы для упаковки сыпучих товаров. Вертикальные станки более компактны и продуктивны. Продукт в них поступает в дозатор самотеком, тогда как в горизонтальном его подвозят транспортером.
Полуавтоматы для расфасовки сыпучей продукции – работают с сахаром, крупами, макаронами. Продукция фасуется в мягкие пакеты, швы завариваются. Полуавтоматические станки работают с погрешностью до 3%. Автоматы для расфасовки обеспечивают точность взвешивания до 2%. Автоматические линии используются для фасовки любых сыпучих товаров, в том числе гранулятов и непищевых (стирального порошка, цемента, песка). Производительность 15-100 пакетов в минуту. Оборудование для кусковых товаров – принципиальное отличие их в большом объеме ковша. Стандартный – восьмилитровый, специального исполнения – до 15 литров. Программа управления предусматривает работу с кусками различных размеров и свойств. Погрешность дозирования составляет два куска.
Оборудование со шнековым дозатором – группа оборудования, оснащенная объемным дозатором шнекового типа. Используется для аккуратной фасовки порошков – муки, стиральных, пудры. Точность расфасовки зависит от механических свойств товара и дозировки и составляет от 4 до 10%.
Станки с мультиголовочным дозатором по весу – оборудование для упаковки замороженных ягод и овощей, пельменей и других
нестандартных
продуктов. Погрешность весовой дозировки составляет до 4%.
3.3 Дозирование сыпучих материалов в производственных условиях
Рассмотрим процесс фасовки сыпучих материалов в производственных условиях на примере муки.
Сегодня машиностроительные заводы производят для муки упаковочное оборудование, автоматизированное и легко обслуживаемое. Такое оборудование требует минимальных затрат: как трудовых, так и временных, а соответственно и энергетических затрат. Обычно оно представлено в виде упаковочной линии вертикальной конструкции, предназначенной для формирования бумажного пакета или пакета из иного материала. Упаковочная линия укомплектована дозаторами, предусмотренными для автоматической процедуры дозирования муки. Дозатор муки конструктивно выполняется:
- или с вертикальным шнеком, работая на основе шнекового дозирования,
- либо с телескопическими чашками, работая как объемный дозатор.
Если линия снабжена дозатором со шнеком, то после дозирования, на одном из этапов, устанавливается система контрольного определения массы муки. Это взвешивающее устройство, если есть отклонение массы продукта с превышением заданного предела, должно вытолкнуть забракованный пакет. Если же имеет место одностороннее отклонение массы муки у трех или четырех пакетов подряд, то по обратной связи на дозатор подается сигнал с целью изменения числа оборотов шнека, и величина дозы корректируется. Современные дозаторы для муки изготавливают из сортов нержавеющей стали, дозаторы комплектуются системой контроля оборотов с помощью энкодера, его скорость регулируется при помощи инвертера (преобразователя). Дозаторы оснащаются задвижками с пневмоприводом, перекрывающими подачу муки. На разгрузочной горловине размещается аспирационный патрубок. Дозирующий шнек может быстро заменяться (имеется патрон для быстрой замены).
Дозаторы могут также устанавливаться автономно. Автоматическая линия для фасования и упаковки муки обычно состоит из системы подачи пустых пакетов, которую называют иначе магазином пустых пакетов, бункера для загрузки муки, оснащённого системой дозирования посредством шнекового дозатора, станции наполнения (карусельного типа или другого исполнения) и устройства утряски пакета, наполненного мукой (для уменьшения его объема). Далее следует линия закрытия пакета. Пакет с мукой из бумаги (1-2 кг) обычно проклеивают горячим клеем, делая предварительно двойной подворот. Для упаковки муки весом по 5-25 кг в пакеты, имеющие ручку, используют зашивку нитками, а внутренний полиэтиленовый слой мешка предварительно запаивается. При больших упаковочных форматах предусматривают возможность использования большого плетеного мешка, имеющего полиэтиленовую вставку и вшивную ручку (как при фасовке больших объёмов сахара). В комплект линии упаковки может входить устройство наполнения и система утряски пакетов (карусельного исполнения, например), рассчитанное на 4-14 позиций с дозированием и наполнением одновременно до 3 пакетов. Магазин пустых пакетов вмещает 300-1200 штук. Магазин может пополняться во время режима эксплуатации линии. Устройство утряски может выглядеть на некоторых линиях в виде вибротранспортера. Для успешной работы упаковочного оборудования муки м ного значит наличие системы аспирации, так как мука относится все же к пылящим продуктам. Некоторое оборудование уже оснащено такой системой. При её отсутствии об этом следует позаботиться предприятию-потребителю. Система управления и регулирования процессами линии расфасовки и упаковки муки реализуется на современных моделях через контроллер PLC и удаленный доступ, имея возможность дистанционного контроля, осуществляемого по локальной сети. Некоторое оборудование выполняется на базе кулачкового механизма, система не имеет вакуумных насосов, это значительно увеличивает эксплуатационную надежность оборудования. Установленная электрическая мощность современной линии упаковки муки составляет в среднем 35 кВт.
Пакеты, выходящие из фасовочной машины, поступают на конвейер, где осуществляется групповая упаковка. Операция группового упаковывания
это обертывание брикета из пакетов с мукой термоусадочной пленкой или растягивающейся пленкой. При использовании полимерной пленки брикет
лучше по всему периметру не оборачивать, так как муке будет трудно дышать
. Чаще всего оборудование группового упаковывания уже входит в
состав упаковочной машины, образуя тем самым линию упаковки или просто линию муки. Поэтому фасовочная машина и автомат группового упаковывания
муки закупаются одновременно и стыкуются в единую технологическую схему. Блок из отдельных упаковок обычно состоит из 6-8 пакетов. Групповая упаковка,
сменив деревянные и пластиковые ящики (многооборотную тару), в которую раньше укладывались пакеты, являясь одноразовой, на самом деле
очень удобна, экономична, компактна, не нуждается в ремонте, предотвращает от попытки подмены продукции или несанкционированного вскрытия.
На упаковочных линиях муки применяются групповые упаковки из пакетов по 1 кг или 2 кг, формирующие по 5-6 пакетов с мукой в несколько рядов.
Для упаковки брикетов в пленку их подают в термоусадочный туннель, где по контуру брикетов отрезается пленка и производится автоматическая
усадка, заключающаяся в сжатии пленки под действием высокой температуры и плотном охватывании ею брикета со всех сторон.
Принцип работы всей линии упаковки для муки можно описать следующим образом: на линии упаковки роботом (манипулятором) происходит автоматический забор из магазина пустых пакетов для наполнения мукой, пакет раскрывается и отправляется в секцию заполнения мукой. Оборудование упаковочных линий муки, предусматривающее использование готовых пакетов для наполнения, занимает меньшую площадь. У линии отсутствует в этом случае целый операционный участок, изготавливающий пакет, и поэтому такое оборудование стоит дешевле. Дешевизна эта, правда, со временем нивелируется, так как бумага в рулоне обходится дешевле, чем готовые пакеты. Все операции на упаковочном конвейере остаются теми же. Однако, чем больше мест дозирования в линии, тем точнее будет доза наполнения и, соответственно, выше производительность машины и всей линии в целом. Чем сильнее операция утряски, тем лучше сформируется пакет. Габариты автомата это также увеличивает.
После фасовки муки в бумажные пакеты до их закрытия не лишней оказывается процедура утряски муки в пакете. Суть этой утряски в том, что наполненный мукой пакет подвергается со стороны донышка внешнему воздействию, ударному или колебательному. В результате процесса утряски происходит деаэрация и уплотнение муки, верхний уровень муки в пакете уменьшается, и верхний край пакета легче заворачивается. Достичь хорошего наполнения пакета и получить красиво сформированный пакет без процесса утряски довольно трудно. При утряске мука и мучная пыль, которые оседают на стенках пакета во время засыпки туда муки, ссыпаются в пакет. В зависимости от выбора конструкции оборудования, утряска может осуществляться при помощи частых ударов или при помощи колебаний. Пакет в процессе дальнейшего движения закрывается автоматически, гребешок на верхнем шве складывается, а затем приклеивается к верхней части пакета. После этого упакованные пакеты направляются на конвейер групповой упаковки, где формируются брикеты из нескольких пакетов в несколько рядов. Сформированный брикет накрывается термоусадочной пленкой и направляется в термоусадочный тоннель. В термотоннеле, где установлена необходимая температура и нужное время выдержки, брикеты движутся по конвейеру. За счет температурного воздействия происходит обтягивание брикетов термоусадочной пленкой, и тепловой температурный удар при этом приходится только на полотно упаковочного материала, а не передаётся продукту.
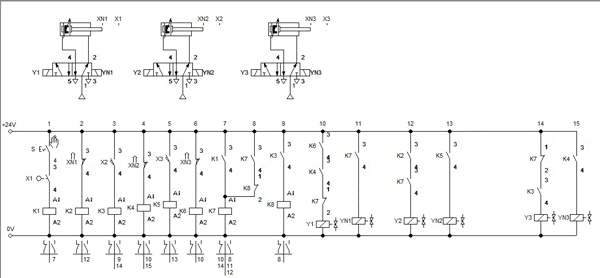
Демострация работы пневмоэлектричесой схемы для дозирования сыпучих материалов массой в 1 кг
(анимация: 5 повторов, 19 кадров, 199 килобайт)
Список источников
- Донской А. С. Математическое моделирование процессов в пневматических приводах: учебное пособие / А.С. Донской. – СПб.: Изд-во Политехн. ун-та, 2009. – 122с.
- Пневмопривод: метод. указ. к выполнению курсового проектирования для студентов спец. 151001
Технология машиностроения
всех форм обучения / Л. В. Ручкин, А. В. Скрипка, В. А. Будьков ; Сиб. гос. аэрокосмич. ун-т. – Красноярск, 2010. – 96 с. - Промышленные мехатронные системы на основе пневмопривода: Учеб. пособие /Е.В. Пашков, Ю.А. Осинский. – Севастополь: Изд-во СевНТУ 2007. – 401 с, ил
- Электропневмоавтоматика 1998 by Festo Didactic GmbH & Co., RechbergstraBe 3, D-73770 Denkendorf. Авторы: Г. Преде, Д. Шольц; Перевод: С.В. Сулига.
Свободно программируемые контроллеры
Festo Didactic GmbH & Co., D-73770 Denkendorf 2004. Авторы: Р. Близинер,Ф. Эбель, К. Лёфтер, Б. Плагеманн, Х. Регбер, Э. Фон Терци, А. Винтер.- Электропневмоавтоматика в производственных процессах: Учебное пособие / Е.В. Пашков, Ю.А. Осинский, А.А. Червякин; Под ред. Е.В. Пашкова. – 2-е изд., перераб. и доп. – Севастополь: Изд-во СевНТУ, 2003 – 496 с., ил.
- Автоматизация [Электронный ресурс]. Режим доступа: https://ru.wikipedia.org/wiki/Автоматизация
- Дозатор [Электронный ресурс]. Режим доступа: https://ru.wikipedia.org/wiki/Дозатор
- Каталог продукции FESTO [Электронный ресурс]. – Режим доступа: https://www.festo.com/cms/ru-uk_ua/index.htm
- Юшин Е.С. Гидро- и пневмопривод машин в нефтегазовой отрасли [Текст] : метод. указания / Е. С. Юшин. – Ухта : УГТУ, 2016. – 27 с.
- Герц Е.В., Крейнин Г.В. Расчет пневмоприводов. Справочное пособие. М.,
Машиностроение
, 1975. – 272 с. с ил. - Рогинский Г.А. Дозирование сыпучих материалов. М.,
Химия
, 1978. – 176 с.