Реферат по теме выпускной работы
Содержание
- Введение
- 1. Актуальность темы
- 2. Цель и задачи исследования, планируемые результаты
- 3. Обзор исследований и разработок
- 3.1 Классификация тормозных устройств
- 3.2 Существующие системы торможения
- 3.3 Фрикционные пары тормозных устройств
- 4. Выбор и анализ геометрической формы фрикционной колодки
- Выводы
- Список источников
Введение
В основных направлениях экономического и социального развития ДНР, указывается на необходимость в угольной промышленности. В сложной цепи операций, связанных с добычей угля, важное число занимают подъемные установки. Общая тенденция к повышению концентрации производства, необходимость перехода к разработке более глубоких горизонтов накладывают свои отпечаток на характер развития и совершенствования оборудования шахтного подъема.
Значительные резервы повышения производительности шахтного подъема современных шахт имеются в увеличении емкости и скорости движения подъемных сосудов сокращении времени переходных процессов (замедление, ускорение) в результате совершенствования конструкции подъемных машин и систем управления электроприводом подъема.
За последние тридцать лет в нашей стране максимальная скорость движения сосудов шахтных подъемных установок увеличился в 1,4 раза и достигла 14 м / с, глубина подъема – в 1,8 раза и составляла на ряде шахт 1500–2000 м, грузоподъемность сосудов – в 3 раза и достигла для угольных шахт 30 т, для железорудных – 50 т. Предполагается, что в ближайшие годы глубины подъема, скорость движения и полезная емкость сосудов будут расти более интенсивно. Проектируются шахтные подъемные машины емкостью вскипел 50 т для угольных и 100 т для железорудных шахт при максимальной скорости движения подъемных сосудов 20 м / с. При создании таких сверхмощных комплексов на первый план выступают вопросы их безопасной эксплуатации. Известно, что основным средством защиты подъемной установки от аварии является ее тормозная система.
1. Актуальность темы
Увеличение объемов добычи полезных ископаемых требует разработки более глубоких горизонтов а значит, и повышение эффективности и надежности работы шахтных подъемных установок, что, будучи созданы и освоены промышленностью, по техническим характеристикам не уступают лучшим зарубежным образцам.
За последние тридцать лет в нашей стране максимальная скорость движения сосудов шахтных подъемных установок увеличилась в 1,4 раза и достигла 14 м / с, высота подъема – в 1,8 раза и составляла на ряде шахт 1500–2000 м, грузоподъемность сосудов – в 3 раза и достигла для угольных шахт 30 т, для железорудных – 50 т. Предполагается, что в ближайшие годы глубины подъема, скорость движения и полезная емкость сосудов будут расти более интенсивно. Проектируются шахтные подъемные машины емкостью вскипел 50 т для угольных и 100 т для железорудных шахт при максимальной скорости движения подъемных сосудов 20 м / с.
При создании таких сверхмощных комплексов на первый план выступают вопросы их безопасной эксплуатации. Известно, что основным средством защиты подъемной установки от аварии является ее тормозная система. Не случайно в последние годы многие исследователи уделяют особое внимание изучению динамических процессов, протекающих в элементах тормозной системы и подъемной установки в режимах торможения, вопросам эффективности применения и надежности тормозных систем, созданию новых технических средств, обеспечивающих программное предохранительное торможение. Большой вклад в решение проблемы обеспечения безаварийной эксплуатации шахтных подъемных установок внесли Э. С. Трауб, А. Г. Степанов, Н. Г. Гаркуша, А. Н. Шатило, Л. В. Колосов, А. А. Белоцерьковский, А . П. Нестеров и другие советские ученые. На основе результатов исследований динамики подъемной установки как многомассовой системы с упругими связями ими разработаны нормативные требования и средства, обеспечивающие безопасность эксплуатации шахтных подъемных установок в режимах торможения. Вместе с тем существующие методы расчета и теоретического исследования динамики тормозных систем, необходимые для определения их рациональных параметров, существенно отстают от требований практики. До последнего времени недостаточно полно разработаны вопросы динамики подъемной установки при рабочем и предохранительном торможении механическими тормозами как с пневматическими, так и с гидравлическими тормозными приводами, а также методы расчетов нагрева и износа колодочных и дисковых тормозов. Таким образом, на основании выше изложенного, вопрос – разработка дискового тормоза для шахтной подъемной машины – является актуальным.
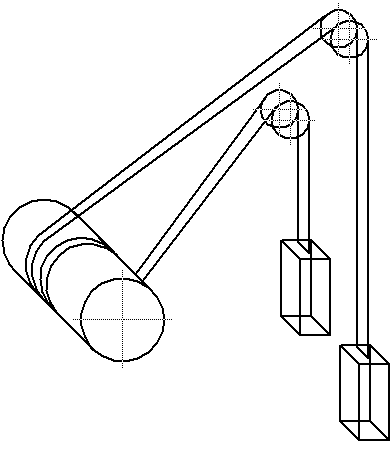
Рисунок 1 – Принцип работы подъемной машины
2. Цель и задачи исследования, планируемые результаты
Цель – разработка рациональной схемы тормозного устройства шахтной подъемной машины Ц 3,5х2А и определения его основных параметров.
Указанная цель может быть реализована решением следующих частных задач:
- Анализ существующих систем тормозов.
- Анализ применяемых фрикционных материалов.
- Разработка эффективной схемы тормоза шахтной подъемной машины.
- Выбор фрикционных материалов тормозной накладки.
- Расчет тормозного устройства.
- Определение удельного давления на колодку трения.
- Определение температуры в момент торможения на поверхности накладки и диска.
- Расчет максимального усилия прижимания тормозной накладки к диску.
- Определение экономического эффекта от применения дискового тормозного устройства.
3. Обзор исследований и разработок
Для обеспечения нормальной эксплуатации подъемно–транспортные машины обеспечиваются надежно действующими тормозными устройствами. Тормоза должны останавливать машину и груз на определенном пути торможения и удерживать груз в подвешенном состоянии при заданном запасе торможения при заданном значении замедления. Тормоза любого исполнительного механизма не только обеспечивают безопасность работы этого механизма и всей машины в целом, но и влияют па производительность. Значение тормозных устройств возрастает в связи с интенсификацией производства, увеличением движущихся масс, скоростей движения и частоты торможения. В современных подъемно–транспортных машинах тормоза в течение короткого периода времени должны превращать в тепловую энергию значительное количество механической энергии и передавать ее в окружающую среду без снижения работоспособности тормоза и машины в целом. [1]
3.1 Классификация тормозных устройств
По конструктивному исполнению рабочих элементов – на тормоза:
- колодочные – с рабочим элементом в виде колодки, что трется по внешней или внутренней поверхности тормозного барабана;
- ленточные – с рабочим элементом в виде ленты трущейся по тормозному барабану;
- дисковые – с рабочим элементом в виде целых дисков или отдельных сегментных колодок,
- конические – с рабочим элементом в виде конуса.
Последние два конструктивные разновидности тормозов обычно объединяют в одну группу тормозов с запирающим усилием, действует вдоль оси – в группу тормозов с осевым нажатием.
По характеру действия приводного усилия – на тормоза:
- нормально замкнутого типа, замыкание которых создается постоянно действующей внешней силой (весом замыкающего груза усилием пружины и т.п.), а размыкание – только при воздействии на него привода стояночного;
- нормально–разомкнутого типа, размыкаются с помощью постоянно действующего внешнего усилия, а замыкаются только при воздействии на него привода стояночного;
- комбинированные, работающие в нормальных условиях как тормоза нормально разомкнуты, а в аварийных условиях – как тормоза нормально замкнутые действием запирающего усилия.
По принципу действия – на тормоза:
- автоматические – нормально замкнутого типа, замыкаются независимо от воли обслуживающего персонала при отключении двигателя механизма, на котором установлено тормоз;
- управляемые – замыкание или размыкание которых производится обслуживающим персоналом при воздействии на орган управления тормозом, независимо от привода механизма.
По назначению:
- на стопорные тормоза, останавливают механизм, вступая в действие в конце движения,
- на тормоза, ограничивающие скорость движения в определенных пределах в течение всего периода работы. Соответствующего исполнительного механизма (спускные тормоза и регуляторы скорости).
Ко всем тормозам, независимо от их конструкции, предъявляются следующие основные требования: высокая надежность конструкции, достаточный тормозной момент для заданных условий работы, плавность торможения, быстрое замыкания и размыкания, конструктивная прочность элементов тормоза, простота конструкции, определяет низкую цену изготовления, удобство осмотра, регулирования и замены износившихся деталей, устойчивость регулирования, обеспечивает надежность работы тормозного устройства, минимальный износ терочным элементов, температура поверхности трения, в процессе работы не превышающая предельную, установленную для данного типа тормоза при данном фрикционном материале, минимальные габариты и масса. При работе во взрывоопасной среде должны применяться подъемно–транспортные машины специального взрывобезопасного или взрыво–защищенного исполнения. [2]
3.2 Существующие системы торможения
Дисковые тормоза
На многоканатной подъемной машине используются приводные элементы дисковых тормозных устройств с выпуском рабочей жидкости при рабочем и предохранительном торможении
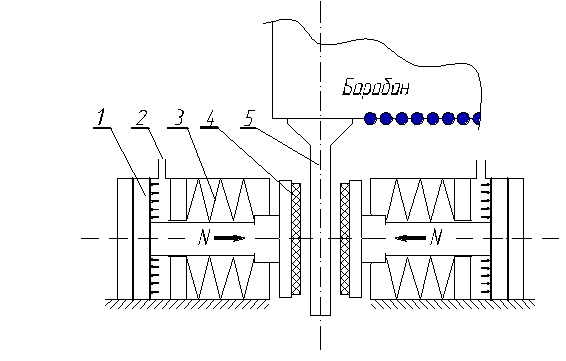
Рисунок 2 – Дисковый тормоз
Колодкочные тормозa
Различают колодочные тормоза с внешним и внутренним расположением тормозных колодок относительно металлического элемента фрикционной пары. В первых сила трения при торможении возникает в результате контакта фрикционной накладки с внешней образующей поверхностью тормозного шкива (бандажом ходового колеса), а в других – с внутренней образующей поверхностью тормозного барабана. Одноколодочные тормоза не находят широкого применения (за исключением тормозов железно дорожного подвижного состава), так как создают значительные усилия, сгибают тормозной вал. Крепления тормозных колодок к рычагам – шарнирное или жесткое. При жестком креплении износ фрикционных накладок по лугу охвата колодок менее равномерный.
Исполнительным органом в тормозных устройствах шахтных подъемных машин обычно применяется тормоз двухколодочный. Ленточные тормоза в шахтных подъемных машинах не допускаются ПБ через возможности разрыва ленты. Кроме того, эти тормоза придают сгибая воздействие на вал тормозного шкива.
Исполнительный орган бывает одинарным, действующим па один тормозной обод, и спаренным, действующим на два тормозных обода. В последнем случае каждый обод имеет свою пару тормозных стоек или балок с колодками, связанными общей передачей рычага с приводом.
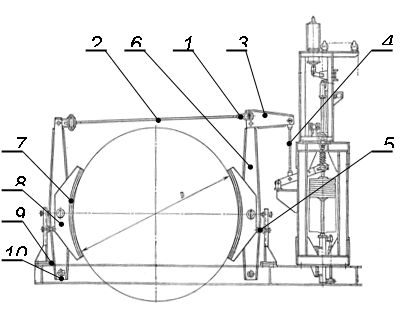
Рисунок 3 – Колодочный тормоз
Тормозные устройства с пружинно–гидравлическим приводом тормоза имеют два исполнительные органы, два пружинно–гидравлические приводы, станцию управления и блокировки. Исполнительные органы работают синхронно и используются как при рабочем, так и при предохранительном торможении. Каждый исполнительный орган тормоза типа колодки влияет на тормозной обод барабана, создавая половину величины необходимого тормозного момента.
Ленточные тормоза
В ленточных тормозах (рис. 4) торможение осуществляется за счет трения гибкой стальной ленты об внешнюю поверхность цилиндрического тормозного шкива или внутреннюю поверхность цилиндрического барабана. Повышение коэффициента трения достигается путем закрепления на рабочей стороне ленты накладки из фрикционного материала. При одинаковых замыкающих усилиях, коэффициенте трения и диаметрах шкивов (барабанов) тормозной момент ленточного тормоза значительно больше, чем колодочного. Ленточные тормоза применяют в экскаваторах, дорожных машинах, кузнечно–прессовом оборудовании, в грузоподъемных машинах и механизмах. К ленточным относятся также тормоза ленточно–колодочные и шарнирно–колодочные.
Угол охвата лентой тормозного шкива обычно составляет около 270 °, однако отдельные конструкции достигают 590 °.
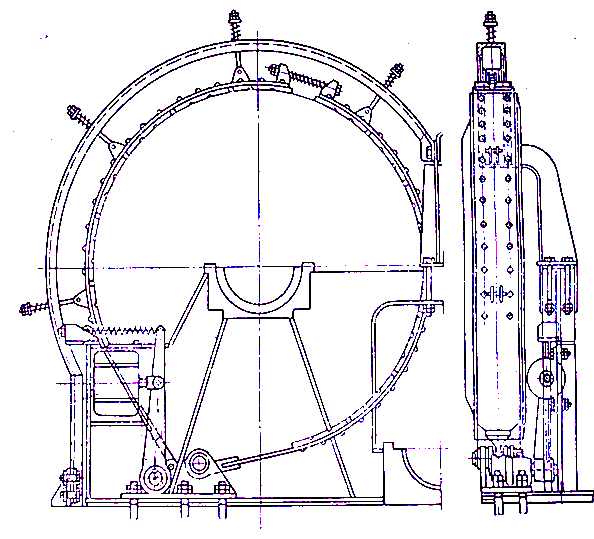
Рисунок 4 – Ленточный тормоз
Тормоза с внешней лентой, в зависимости от схемы ее присоединения к рычагу разделяют на простые, дифференциальные, суммирующие, двухстороннего действия. В простом тормозе наиболее нагруженный набегающий (который натягивается силой трения при вращение шкива) конец лент прикреплен к неподвижной части рабочего механизма, а совпадающей – до рычага. В дифференциальном тормозе концы ленты присоединены к рычагу по обе стороны от оси его колебания, а в подытоживающем – в одну сторону. В тормозе двустороннего действием набегающего (неподвижно закрепленным) становится в зависимости от направления вращения шкива тот или иной конец ленты. Простые и дифференциальные тормоза применяют в механизмах, для которых не требуется обеспечение одинакового тормозного момента. [3]
3.3 Фрикционные пары тормозных устройств
Показатели качества тормозных устройств определяются в основном конструктивным исполнением узла трения и оптимальным сочетанием материалов фрикционной пэры. Для обеспечения стабильности тормозного момента, повышение надежности и износостойкости элементов тормоза применяют специальные материалы с повышенными фрикционными свойствами (фрикционные накладки) в контакте с металлическим контртелом. Фрикционные накладки изготавливают из кожи, пробки, модифицированной древесины, металлов, асбополимерных композиций, порошковых материалов. Они быстро изнашиваются элементы по сравнению с металлическими контртелами и поэтому должны быть достаточно дешевыми, а фрикционный узел должен иметь такую конструкцию, при которой обеспечивается быстрая смена изношенных накладок.
Материалы для фрикционных накладок
При выборе материалов пары трения рекомендуется учитывать вид контакта ее элементов, значение коэффициента взаимного перекрытия, требования к контактной жесткости узла трения, вид охлаждения, наличие или отсутствие смазочного материала.
Фрикционные материалы должны иметь стабильный коэффициент трения, заданные механические и теплофизические свойства, хорошо приробатываться к контртелу (при первом торможении Мф> 0,8Мрасч), должны быть технологичными, коррозионно–стойкими, обладать достаточной механической прочностью, масло, влаго– и огнестойкостью, высокой износостойкостью низкой склонностью к схватыванию в горячем и холодном состоянии.
Верхняя и нижняя границы коэффициента трения залают зависимости от конструкции, назначения и условий эксплуатации тормозного устройства. Нижняя граница коэффициента трения определяет условие обеспечения заданного тормозного момента, а верхний сохранения устойчивости движении транспортного средства при максимально допустимых замедлениях. Значение коэффициента трения для тормозных устройств подъемно–транспортных машин, рекомендуемых составляют 0,35–0,45.
Износостойкость определяет срок службы фрикционных накладок, межремонтные пробеги машин и время ремонтных простоев. Оценивают ее исходя из типа тормоза, условий эксплуатации и качества фрикционного материала. Теплофизические свойства пары трения тормоза определяются в основном теплоемкостью и теплопроводностью материалов. Теплоемкость способствует снижению температуры пара трения за счет поглощения теплоты, а теплопроводность – за счет переноса теплоты от поверхности трения в глубь материала и дальше к поверхности охлаждения.
Механические свойства являются важным показателем материалов. Фрикционная пара тормоза работает в условиях сложного напряженного состояния. Напряжения сжатия фрикционной накладки примерно равны нормальному давлению. Сила трения при торможении вызывает в накладке растягивающие напряжения и напряжения среза. Напряжения среза ориентировочно равны произведению коэффициента трения на нормальное давление. При трении фрикционных материалов в области повышенных температур их твердость пропорциональна площади фактического контакта поверхностей, что трут, и определяется давлением на пятне фактического касания.
Модуль упругости фрикционного материала при упругом контакте влияет на характер фрикционной взаимосвязи и определяет фактическую площадь контакта и давление на пятнах контакта. Фрикционный материал должен иметь минимальные тепловое расширение, усадку и высокий модуль упругости, так как при жестком креплении накладки к металлическому каркасу вследствие теплового расширения и усадки фрикционного материала могут возникать значительные температурные и усадочные напряжения в накладке.
Процесс наложения фрикционной накладки на контртело характеризуется ударным приложением нагрузки, поэтому фрикционный материал должен обладать высокой ударной вязкостью.
При повторно–кратковременном режиме торможения фрикционная накладка испытывает многократные циклические нагрузки и должна иметь достаточное сопротивление усталости при циклических действиях.
Фрикционные и другие характеристики пары трения определяются условиями ее работы. По температурным показателям различают весьма легкий режим работы (до 100 ° С), легкий (до 250 ° С), средний (до 600 ° С), тяжелый (до 1000 ° С) и сверхтяжелый (свыше 1000 ° С). Области применения пар трения тормозных устройств.[4]
4. Выбор и анализ геометрической формы фрикционной колодки
В процессе расчета нагрева диска и фрикционных накладок дискового тормоза приняты следующие допущения:
- Тепловой поток, подводится к тормозному диску, распределяется равномерно по кольцевой площадью трения, а поток подводится к фрикционных накладок, равномерный по их площади трения;
- Тепловой поток, развивается на поверхности трения, линейный и направлен по нормали к поверхности трения.
Аварийность на шахтном подъеме составляет около 4%, а смертельный травматизм более 3% от общего числа аварий и случаев смертельного травматизма на шахтах. Основные опасности на канатном подъеме и спуске людей и грузов по вертикальным и наклонным выработкам следующие: падение в вертикальных или свободное скатывание в наклонных выработках грузовых и людских подъемных сосудов; удары и резкие остановки человеческих подъемных сосудов; падение в выработки перевозимых в сосудах грузов или других предметов; падение людей.
Падение (свободные скатывания) подъемных сосудов, приводит к травмированию людей, находящихся в подъемном сосуде или ниже сосуда, происходит при обрыве подъемных канатов или сцепок. Удары человеческих подъемных сосудов в крепление или армировки при несоблюдении установленных зазоров, а также удары и резкие остановки при переподъйеме сосуда или напуска каната могут привести к серьезному травмированию людей, находящихся в подъемном сосуде. Падающие на выработку грузы и предметы опасные для работающих в ней и перевозимых людей. Очевидна также опасность падения людей в выработке при посадке в подъемный сосуд, высадке из него или при его движении.
Число людей, которых можно одновременно перевозить в каждом этаже клети, определяется из условия свободного их размещения и не должно превышать пяти на 1 м2 полезной площади пола.
Для обеспечения строго направленного движения и исключения колебаний или кручения подъемные сосуды снабжены направляющими башмаками, скользящих по проводникам. Последние являются элементами армировки стволов и могут быть твердыми или эластичными. Как твердые проводники применяют рельсы, металлический коробчатый профиль или деревянные брусья, в качестве эластичных – канат .
Направляющие башмаки на подъемных сосудах могут быть скользящим твердым или упругими – в виде подпружиненных роликовых опор. Достоинство последних заключается в том, что они находятся в постоянном контакте с проводниками, тогда как по мере износа контактных поверхностей твердых направляющих башмаков скольжения и проводников зазор между ними увеличивается.
Однако упругие направляющие менее надежно удерживают подъемные сосуды от боковых смещений. Поэтому Правила безопасности позволяют применять их только в сочетании с твердыми башмаками, служащие в качестве меры предосторожности. Их устанавливают непосредственно на несущие конструкции подъемном сосуде.
Зазоры между контактными поверхностями направляющих башмаков и проводников строго регламентируются Правилами безопасности в зависимости от типа и материала проводников и направляющих. Так, минимальный зазор между направляющими башмаками скольжения и контактных поверхностей металлических проводников составляет 5 мм с каждой стороны, а максимальный – 10 мм. Для деревянных проводников он равен соответственно 10 и 15 мм.
Стальные канаты, применяемые на шахтных подъемных установках, должны соответствовать требованиям действующих ГОСТ или технических условий. В устройствах, служащих для транспортировки людей, должны применяться только канаты марки В, то есть канаты высокого качества. Качество каната определяется механическими свойствами проводов и указывается в заводском акте–сертификате.
Главные канаты людских и грузолюдских подъемных установок должны быть марки В, другие канаты – не ниже марки И. Использование канатов марки ИИ на шахтах не допускается.
Все подъемные канаты перед навеской должны быть испытаны по единой методике на канатно–испытательных станциях, зарегистрированных в МАКНИЫ. Испытанию подлежат отрезки каната длиной не менее 1,5 м.
Пригодность канатов для использования в подъемных установках определяется величиной запаса их прочности. Запас прочности это отношение суммарного разрывного усилия проволок каната, выдержавшие экзамен, к расчету статической нагрузки на него. Расчетная статическая нагрузка складывается из веса подъемного сосуда с прицепным устройством, веса максимального; груза и главного каната длиной от точки востока его со шкива до точки прикрепления к сосуду при нахождении последнего в приемной площадке нижнего горизонта. Если канат уравновешивающий труднее главного, то к весу сосуда и груза добавляют вес не главного, а каната, уравновешивающего.
При навешивание канаты должны иметь запас прочности не ниже 9–кратного для людских подъемных установок, 7,5 кратного – для грузолюдських и 6,5–кратного – для грузовых. [5]
Выводы
В шахтной подъемной машине тормозное устройство является одним из важнейших и ответственных узлов.В данной дипломной работе выполнен анализ существующих тормозных систем с колодочными, ленточными и конусными тормозами, разработана схема дискового тормозного устройства и рассмотрены основные элементы его исполнительного органа (привод).
Недостатками радиальных тормозов являются:
- Низкая быстродействие;
- Низкий к.п.д. за счет многошарнирной системы;
- Нестабильная характеристика;
- Большой угол охвата, большая поверхность охлаждения и возможность перегрева и аварии;
- Низкая ремонтопригодность;
- Сложность конструкции (радиальный зазор регулируется пружинными тягами)
- Низкая надежность по сравнению с дисковыми тормозами.
Преимущества дисковых тормозов:
- Взаимное уравновешивание сил прижатия тормозных колодок к диску, в результате чего барабан и лобовины не нагружаются радиальными усилиями;
- Большая компактность и меньший вес при равных тормозных моментах;
- Меньше инерционность и значительно большее быстродействие подвижных деталей;
- Большая точность управления машиной;
- Меньше тепловая деформация плоской поверхности тормозной колодки и более благоприятные условия охлаждения тормозного поля (путем конвекции и излучения) Отсутствие влияния теплового расширения диска на эффект торможения;
- Простота изготовления плоского диска и ремонта рабочей поверхности с целью восстановления необходимой ее чистоты; Небольшая инерция тормоза, вследствие чего снижаются динамические нагрузки на основные узлы подъемной установки и увеличивается точность управления подъемной машиной.
- На многоэлементном дисковом тормозном устройстве исполнительный орган непосредственно связан с приводом, исключая при этом промежуточные устройства (рычаги, тяги и др.).
В результате проделанной работы предложена схема и рассчитаны основные параметры дискового тормозного устройства к шахтной подъемной машины Ц–3,5х2А
Для созидания необходимого тормозного момента 1050 кНм, определенное количество тормозных элементов – 16 штук.
Рассчитанный диаметр цилиндра 129 мм и штока – 40 мм, для обеспечения усилия прижатия тормозной колодки 100 кН.
Определено максимальное давление на тормозную колодку, при большом прижимании ее к диску 1,55 МПа, который находится в допустимой границе для выбранного фрикционного материала.
Выбранный и обоснованный фрикционный материал тормозного диска – металлокерамика на железнографитовой основе. Этот материал по сравнению с асбокаучуковыми и асбобакелитовыми покрытиями имеет ряд преимуществ:
- допускает значительно больше удельное давление (2,0 против 0,8 – 1,0 МПа);
- имеет более высокий и стабильный коэффициент трения (0,6 против 0,42)
- допускает большую температуру нагрева (400 ° С против 250 ° С);
- имеет значительно большую теплопроводимость.
Рассчитана температура торможения на поверхности трения, при пяти секундном торможении, которая составляет для колодки 134,5° С, для диска – 109,7° С, не превышает максимально допустимой для выбранного фрикционного материала – при этом срок службы тормозного устройства увеличивается с 18 мес. для колодочного тормозного устройства до 23,4 мес. при дисковом тормозном устройства, то есть почти на 30%.
Значительные достоинства дисковых тормозных устройств в отношении тормозных устройств радиального типа, а также широкое применение на зарубежных подъемных машинах различных фирм позволяют предполагать что дисковые тормозные устройства получат широкое применение и на отечественных, особенно на крупных шахтных подъемных машинах.
Список источников
- Песвианидзе А. В. Расчет шахтных подъемных установок: Учеб. Пособие для вузов. – М.: Недра,2005. – 250 с: ил. ISBN 5–247–01840–0.
- Конспект Лекций по дисциплине «Горная механика» Шахтные подъемные установки, механическая часть подъемных установок 2008г.
- С. С. Сиротин. Шахтные подъемные установки. Учебное пособие для студентов горных специальностей. Алчевск: ДГМИ,2007 – 174 с.
- Юдис, Борис Яковлевич. Совершенствование системы предохранительного торможения подъемной установки Алчевск: ДГМИ,2009. – 140 с.
- А.Д. Мехтиев, Проблемы эксплуатации и анализ состояния подъемных установок. Карагандинского государственного технического университета(КарГТУ).
- ГОСТ 2.104–2006. ЕСКД. Основные надписи. – М.: Стандартинформ, 2006. – 18 с.
- ГОСТ 2.105–95*. ЕСКД. Общие требования к текстовым документам. – М.: Стандартинформ, 2006. – 30 с.
- УГОСТ 2.301–68*. ЕСКД. Форматы. [Электронный ресурс] / Электронная библиотека CD «Строительство» v 2.01. (221 файл, 112 Mb) – Пермь: Служба НТИ, 2003.
- ГОСТ 2.321–84. ЕСКД. Обозначения буквенные. – М.: ИПК Изд–во стандартов. 2001. – 4 с.
- . ГОСТ 7.1–2003. Библиографическое описание. Общие требования и правила составления. – М.: Изд–во стандартов. 2004. – 170 с.
- ГОСТ 7.82–2001. Библиографическая запись. Библиографическое описание электронных ресурсов. – М.: Изд–во стандартов. 2002. – 54 с.
- Единая система конструкторской документации. Основные положения. – М.: Изд–во стандартов, 1983. – 351 с.