Abstract
Table of contents
- Introduction
- 1. Theme urgency
- 2. Goal and tasks of the research
- 3. Selection and analysis of the geometric shape of the friction pads
- Conclusion
- References
Introduction
In the main directions of economic and social development of the DPR, the need for the coal industry is pointed out. In a complex chain of operations associated with the extraction of coal, an important number is occupied by lifting installations. The general tendency to increase the concentration of production, the need to move to the development of deeper horizons leave their mark on the nature of the development and improvement of the equipment for mine recovery. The increase in mining operations requires the development of deeper horizons and, therefore, an increase in the efficiency and reliability of the mine hoisting facilities, which, being created and mastered by industry, are not inferior in their performance to the best foreign models.
Significant reserves to improve the performance of the mine lifting modern mines are available in increasing the capacity and speed of movement of the lifting vessels and reducing the time of transient processes (deceleration, acceleration) as a result of improving the design of lifting machines and lift control systems. Over the past thirty years, in our country, the maximum speed of movement of vessels of mine hoisting installations increased 1.4 times and reached 14 m / s, the depth of ascent increased 1.8 times and was 1,500–2,000 m in a number of mines, the carrying capacity of vessels 3 times and reached 30 tons for coal mines, 50 tons for iron ore. It is assumed that in the coming years the depth of ascent, the speed of movement and the effective capacity of the vessels will grow more intensively. Designed mine hoisting machines with a capacity of boiled 50 tons for coal and 100 tons for iron ore mines with a maximum speed of movement of lifting vessels of 20 m / s. When creating such super–power complexes, the issues of their safe operation come to the fore. It is known that its brake system is the main means of protecting a lifting unit from an accident.
1. Theme urgency
The increase in mining operations requires the development of deeper horizons and, therefore, an increase in the efficiency and reliability of the mine hoisting facilities, which, being created and mastered by industry, are not inferior in their performance to the best foreign models. Over the past thirty years in our country, the maximum speed of movement of vessels of mine hoisting installations increased 1.4 times and reached 14 m / s, the height of the rise – 1.8 times and was 1500–2000 m in a number of mines, the carrying capacity of vessels times and reached 30 tons for coal mines, 50 tons for iron ore. It is assumed that in the coming years the depth of ascent, the speed of movement and the effective capacity of the vessels will grow more intensively. Designed mine hoisting machines with a capacity of boiled 50 tons for coal and 100 tons for iron ore mines with a maximum speed of movement of lifting vessels of 20 m / s.
When creating such super–power complexes, the issues of their safe operation come to the fore. It is known that its brake system is the main means of protecting a lifting unit from an accident. Not accidentally, in recent years, many researchers have paid special attention to the study of dynamic processes occurring in the elements of the braking system and lift installation in the braking modes, the effectiveness of the use and reliability of the braking systems, the creation of new technical means that provide software safety braking. A great contribution to solving the problem of ensuring trouble–free operation of mine hoisting installations was made by E. S. Traub, A. G. Stepanov, N. G. Garkusha, A. N. Shatilo, L. V. Kolosov, A. A. Belotserkovsky, A. P. Nesterov and other Soviet scientists. Based on the results of studies of the dynamics of a lifting installation as a multi–mass system with elastic connections, they developed regulatory requirements and means to ensure the safety of operation of mine lifting installations in braking modes. At the same time, the existing methods of calculation and theoretical study of the dynamics of brake systems, which are necessary for determining their rational parameters, lag significantly behind the requirements of practice. Until recently, the issues of the dynamics of a lifting installation with working and safety braking with mechanical brakes with both pneumatic and hydraulic brake drives, as well as methods for calculating the heating and wear of shoe and disc brakes, have not been fully developed. Thus, based on the above, the question – the development of a disc brake for a mine hoist – is relevant.
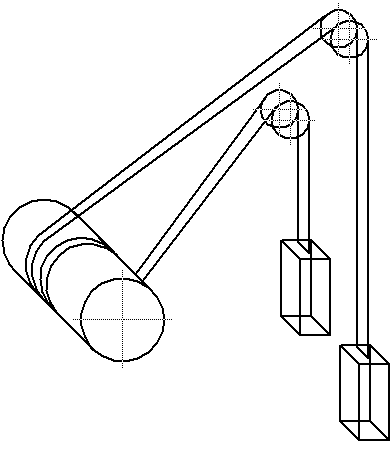
Figure 1 – Principle of operation of the lifting machine
2. Goal and tasks of the research
The goal is to develop a rational scheme of the brake device of the mine hoist C 3,5x2A and determine its main parameters.
This goal can be achieved by solving the following particular tasks:
- Analysis of existing brake systems.
- Analysis of the applied friction materials.
- Development of an effective scheme for a mine lifting machine brake.
- Selection of friction brake lining materials.
- Calculation of the braking device.
- Determination of the specific pressure on the friction block.
- Determination of temperature at the time of braking on the surface of the lining and the disk.
- The calculation of the maximum effort pressing the brake pads to the disc.
- Determination of the economic effect of the use of disc brakes.
Research object: Shape of the friction pads.
Research subject:Selection and analysis of the geometric shape of the friction pads
3. Selection and analysis of the geometric shape of the friction pads
In the process of calculating disk heating and disc brake friction linings, the following assumptions are made: Heat flow is supplied to the brake disc, distributed evenly over the annular friction area, and the flow is supplied to the friction linings uniform over their friction area; Heat flow, develops on the friction surface, is linear and is directed along the normal to the friction surface.
The accident rate at the mine rise is about 4%, and the fatal injuries are more than 3% of the total number of accidents and fatal injuries in the mines. The main hazards on the cable ascent and descent of people and cargo in the vertical and inclined workings are the following: a fall in vertical or free rolling in the inclined workings of cargo and human lifting vessels; shocks and abrupt stops of human lifting vessels; drop in the production of cargoes or other items transported in vessels; the fall of people. Falling (free–flowing) lifting vessels, causing injury to people in the lifting vessel or below the vessel, occurs when the lifting ropes or couplings break. Impacts of human lifting vessels in fastening or reinforcement if the clearances are not observed, as well as strikes and abrupt stops when the vessel is lifted or rope laden, can cause serious injury to people in the lifting vessel. Falling on the production of goods and objects dangerous to working in it and transported people. Obviously, there is also the danger of people falling in making when boarding, lifting, or moving from a lifting vessel.[1]
The number of people who can be simultaneously transported in each floor of a cage is determined from the condition of their free placement and should not exceed five per 1 m2 of usable floor space. To ensure a strictly directional movement and exclude oscillations or torsion, the lifting vessels are provided with guide shoes sliding along the conductors. The latter are elements of the reinforcement of the trunks and can be solid or elastic. How solid conductors are used rails, metal box–shaped profile or wooden bars, as elastic – rope. The guide shoes on the lifting vessels can be sliding hard or elastic – in the form of spring–loaded roller bearings. The advantage of the latter is that they are in constant contact with the conductors, whereas as the contact surfaces of the solid sliding sliding shoes and conductors wear out, the gap between them increases. However, the elastic guides less reliably hold the lifting vessels from lateral displacements. Therefore, the Safety Rules allow you to apply them only in combination with solid shoes, which serve as a precautionary measure. They are installed directly on the supporting structures of the lifting vessel. The gaps between the contact surfaces of the guide shoes and conductors are strictly regulated by the Safety Rules, depending on the type and material of the conductors and guides. Thus, the minimum gap between the sliding sliding shoes and the contact surfaces of the metallic conductors is 5 mm on each side, and the maximum – 10 mm. For wooden conductors, it is 10 and 15 mm, respectively.
Steel ropes used in mine hoisting installations must comply with the requirements of current GOST or technical conditions. In devices that serve to transport people, only B grade ropes must be used, that is, high–quality ropes. The quality of the rope is determined by the mechanical properties of the wires and is indicated in the factory certificate certificate. The main ropes of human and gruzolyudskih hoisting installations must be brand B, other ropes must not be lower than I. All hoisting ropes before installation should be tested using the same methodology at cable test stations registered in MACNIA. Rope lengths of at least 1.5 m are subject to testing. The suitability of ropes for use in lifting installations is determined by the size of their safety margin. Safety factor is the ratio of the total breaking strength of the wire wires that pass the exam to the calculation of the static load on it. The calculated static load is the sum of the weight of the lifting vessel with the hitch, the weight of the maximum; cargo and the main rope length from the point of its east from the pulley to the point of attachment to the vessel when the latter is in the receiving area of ??the lower horizon. If the balancing rope is more difficult than the main one, then the weight of the vessel and the load adds the weight not of the main, but of the balancing rope. When hanging, the ropes should have a safety margin not lower than 9 times for human lifts, 7.5 times for cargo people and 6.5 times for cargo ones.[2–4]
Conclusion
In the mine hoist machine, the brake device is one of the most important and important nodes. In this thesis, an analysis of existing brake systems with shoe, tape and conical brakes is carried out, a diagram of a disk braking device is developed and the main elements of its executive body (drive) are considered.
The disadvantages of radial brakes are:
- Low speed;
- Low efficiency due to the multi–hinge system; Unstable characteristic;
- Large coverage angle, large cooling surface and the possibility of overheating and accident;
- Low maintainability; The complexity of the design (the radial clearance is regulated by spring rods)
- Low reliability compared with disc brakes.
Advantages of disc brakes:
On a multi–element disc brake device, the actuator is directly connected to the drive, excluding intermediate devices (levers, thrust, etc.). As a result of the work done, a scheme has been proposed and the main parameters of the disk brake device for the mine hoist C–3,5x2A have been calculated.
References
- Песвианидзе А. В. Расчет шахтных подъемных установок: Учеб. Пособие для вузов. –М.: Недра,2005. –250 с: ил. ISBN 5–247–01840–0.
- Конспект Лекций по дисциплине «Горная механика» Шахтные подъемные установки, механическая часть подъемных установок 2008г.
- С. С. Сиротин. Шахтные подъемные установки. Учебное пособие для студентов горных специальностей. Алчевск: ДГМИ,2007 – 174 с.
- Юдис, Борис Яковлевич. Совершенствование системы предохранительного торможения подъемной установки Алчевск: ДГМИ,2009. – 140 с.
- А.Д. Мехтиев, Проблемы эксплуатации и анализ состояния подъемных установок. Карагандинского государственного технического университета(КарГТУ).
- ГОСТ 2.104–2006. ЕСКД. Основные надписи. – М.: Стандартинформ, 2006. – 18 с.
- ГОСТ 2.105–95*. ЕСКД. Общие требования к текстовым документам. – М.: Стандартинформ, 2006. – 30 с.
- УГОСТ 2.301–68*. ЕСКД. Форматы. [Электронный ресурс] / Электронная библиотека CD «Строительство» v 2.01. (221 файл, 112 Mb) – Пермь: Служба НТИ, 2003.
- ГОСТ 2.321–84. ЕСКД. Обозначения буквенные. – М.: ИПК Изд–во стандартов. 2001. – 4 с.
- . ГОСТ 7.1–2003. Библиографическое описание. Общие требования и правила составления. – М.: Изд–во стандартов. 2004. – 170 с.
- ГОСТ 7.82–2001. Библиографическая запись. Библиографическое описание электронных ресурсов. – М.: Изд–во стандартов. 2002. – 54 с.
- Единая система конструкторской документации. Основные положения. – М.: Изд–во стандартов, 1983. – 351 с.