Реферат по теме выпускной работы
Содержание
- Введение
- 1. Актуальность темы
- 2. Цель и задачи исследования
- 3. Конвейерная установка как объект автоматизации
- 4. Анализ исследований и разработок по данной теме
- 5. Схемные решения устройства автоматизации промежуточного бункера
- 6. Эксплуатационные требования к устройству автоматизации
- Выводы
- Список источников
Введение
Ленточные конвейеры способны осуществлять непрерывное транспортирование грузов на большие расстояния, что по технологическим причинам обуславливает их незаменимость на шахтах и рудниках. Именно поэтому, особое значение приобретает вопросы надежной и безопасной эксплуатации конвейерных линий.
Контролировать технологические параметры ленточных конвейеров необходимо как для обеспечения непрерывной и безаварийной работы конвейера, так и требуемой производительности конвейера, а также стабилизации погонной нагрузки на ленту. Для решения данных задач необходимо осуществлять оперативное управление конвейерными установками, а также промежуточными бункерами магистральных конвейерных линий.
1. Актуальность темы
Развитие автоматизации шахтных конвейерных линий на протяжении длительного периода определялось необходимостью снижения трудоемкости управления и повышения безопасности эксплуатации конвейерного транспорта. В связи с этим широкое распространение получило автоматизированное управление конвейерной линией, техническая сущность которого заключается в централизации управления процессами пуска-останова конвейеров, а также в обеспечении автоматической защиты от развития аварии при возникновении аварийных ситуаций.[1]
Однако, вопросы автоматизации промежуточных бункеров до сих пор не нашли своего разрешения. Аппаратура контроля работы промежуточных бункеров имеет ограниченные функциональные возможности и устаревшую элементную базу. Таким образом, проблема разработки устройства автоматического управления промежуточными бункерами конвейерных линий актуальна.
2. Цель и задачи исследования
Целью магистерской диссертации является повышение эффективности и безопасности работы конвейерного транспорта путем комплексной автоматизации его работы, а также разработки блока автоматизации работы промежуточных бункеров.
Основные задачи исследования:
3. Конвейерная установка как объект автоматизации
Конвейерные установки благодаря своим качествам (значительная производительность, большая длина транспортировки, способность непрерывно передвигать грузы, пригодность автоматизации и дистанционному управлению, высокая безопасность работ и др.), являются наиболее эффективным средством перемещения насыпных материалов на шахтах (рудниках). Они используются не только для транспортиров¬ки насыпных грузов, но и для перевозки людей.[2]
Использование конвейерных установок на горизонтальных и наклонных выработках позволяет в условиях многих шахт Донбасса иметь конвейеризацию от забоя до околоствольного двора, что в свою очередь обеспечивает перевод транспортирования угля на поток, сокращает количество обслуживающего персонала и создает условия для работы в режиме ресурсосбережения. Поточная технология транспортирования основного груза довольно легко обеспечивается при применении современных средств конвейерного транспорта.
Принцип действия ленточного конвейера заключается в перемещении груза на гибкой бесконечно замкнутой ленте, перемещаемой по неподвижным опорам. Гибкая бесконечная лента огибает приводной барабан и натяжной барабан, а в пролете между ними опирается на ряд роликовых опор, установленных с определенным интервалом на раме. Материал поступает на ленту через загрузочную воронку и разгружается через приводной барабан.
Современные подземные конвейерные линии характеризуются значительной протяженностью и разветвленностью транспортных магистралей, изменяющих со временем свои параметры.[3] Характерной особенностью шахтных конвейерных линий является высокая неравномерность грузопотока, вызванная фактом обслуживания очистного и подготовительного забоев. Именно технологические паузы в работе механизмов являются причиной переменного грузопотока. Неравномерность поступления груза ведет к нерациональному использованию мощности привода (при недогрузке), а также чрезмерному износу тягового органа и снижению надежности АД (при перегрузе).[4] Для стабилизации грузопотока, как правило, используются промежуточные бункера. Схема механизации промежуточного бункера представлена на рисунке 1.
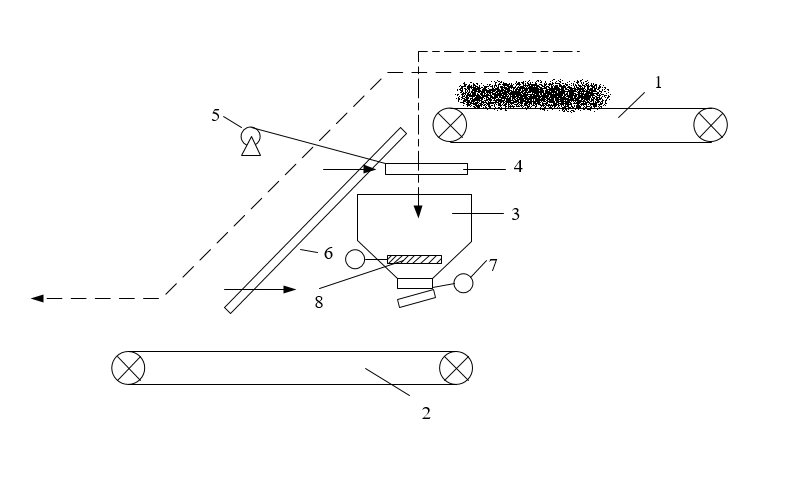
Рисунок 1 – Схема механизации промежуточного бункера: 1– подающий конвейер; 2– принимающий конвейер; 3–бункер; 4–заслонка для перевода в режим загрузки бункера; 5–маневровая лебедка заслонки загрузки бункера; 6– желоб; 7–привод шибера; 8– шибер
(анимация: 7 кадров, задержка 1000 мс, 72 килобайт)
Механизированный бункер работает следующим образом. При нормальной работе транспортной системы грузопоток с подающего конвейера перегружается на принимающий транзитом. При этом заслонка 4 устанавливается в крайнее правое положение и уголь по желобу 6 попадает на принимающий конвейер 2. При остановке конвейера 2 заслонка переводится в крайне левое положение и уголь попадает в бункер 3. Датчиком уровня контролируется верхний уровень угля в бункере. Если срабатывает датчик контроля верхнего уровня загрузки бункера и принимающий конвейер 2 не работает, то подающий конвейер 1 отключается с работы.
Общие требования к системе автоматизации ленточного конвейера:
Выполнение всех требований, предъявляемых к автоматизированным конвейерным линиям, обеспечивает надежное транспортирование полезных ископаемых и безопасную перевозку шахтеров.
4. Анализ исследований и разработок по данной теме
Аппаратура автоматизации конвейерного транспорта шахты
В настоящее время известны следующие аппаратуры автоматизации конвейерных линий:
Комплекс АУК.1М предназначен для управления и контроля работы стационарных и полустационарных неразветвленных конвейерных линий, состоящих из ленточных и скребковых конвейеров с числом конвейеров до 10.[5] Комплекс АУК.1М может применяться также для управления разветвленными конвейерными линиями (до трех ответвлений, каждое из которых управляется как неразветвленная конвейерная линия). Количество конвейеров в линии одного направления не более 10.
Система автоматизированного управления разветвленными конвейерными линиями САУКЛ предназначена для:
шибер,
перегружатель,
питатель);
Комплекс автоматизированного управления конвейерами АУК.3 предназначен для автоматизированного управления неразветвленными конвейерными линиями, состоящими из ленточных и скребковых конвейеров с общим числом конвейеров в линии до 10 включительно, исполнительными органами накопительных бункеров, монорельсовыми канатными дорогами (грузовыми), рельсовыми канатными напочвенными дорогами (грузовыми) и многоканатными дорогами кресельного типа. Комплекс является комплектующим изделием ленточного конвейера (линии конвейеров). Комплекс АУК.3 совместим с комплексом АУК.1М в части линии управления и связи.
Также рассмотрим существующее ныне техническое решение по автоматизации накопительных емкостей и контроля уровня сыпучих материалов. В данный момент на шахтах применяется реле контроля уровня РКУ-1М.
Устройство реле РКУ.1М предназначено для искробезопасного контроля уровня заполнения накопительных емкостей токопроводящими сыпучими материалами и жидкостями с переходным сопротивлением не более 3 МОм, а также для сигнализации по голым проводам с самоконтролем целости линии.[6]
Реле РКУ. 1М выполнено во взрывонепроницаемой оболочке, разделенной перегородкой на отделение вводов и отделение выемной части. На перегородке расположены шесть проходных зажимов для искроопасных цепей и 11 для искробезопасных цепей сигнализации и управления. Оболочка имеет шесть кабельных вводов, предназначенных для гибких кабелей диаметром до 25 мм.Выемная часть представляет собой панель, на которой смонтированы следующие функциональные узлы реле: трансформатор; блок конденсаторов; выключатель; электронный блок; выходные реле; панель управления и сигнализации. В качестве датчика используется датчик уровня ДУ. Он имеет пластмассовый корпус, в нижней части которого установлено охранное кольцо. Кабельный ввод датчика рассчитан на гибкий кабель с наружным диаметром 16-22 мм. Сопротивление изоляции этого кабеля должно быть не менее 10 МОм. Длина линии между реле и датчиком не должна превышать 500 м. Искробезопасность схемы обеспечивается параметрами трансформатора и применяемых элементов, а также выбором режимов их работы в соответствии с техническими характеристиками и применением защитных средств - искрогасящих шунтов и ограничителей.
В качестве датчиков уровня материала в промежуточных бункерах целесообразно использовать электродные датчики, применяемые в РКУ.
В качестве датчика положения регулируемой заслонки примем датчик приближения KLASCHKA типа, Allmetall.[7]
Принцип его работы следующий. Считывание положения осуществляется в данном случаи при помощи индуктивного датчика приближения. Диск выполнен таким образом, чтобы при максимальной частоте оборотов и импульсов установилось соотношение длительности импульса и паузы 1: (0,7…1,3). Коэффициент заполнения импульсов определяется статически:
В качестве датчиков крайних положений шибера и заслонки используются концевые выключатели. Концевые выключатели используются для автоматического выключения исполнительного механизма при достижении подвижной части определенного места. Для шахт опасных по газу и пыли целесообразно выбрать выключатель концевой взрывозащищенный ВКВ, имеющий уровень взрывозащиты повышенная надежность против взрыва
.[8]
5. Схемные решения устройства автоматизации промежуточного бункера
Структурная схема устройства автоматизации работы промежуточного бункера приведена на рисунке 2.
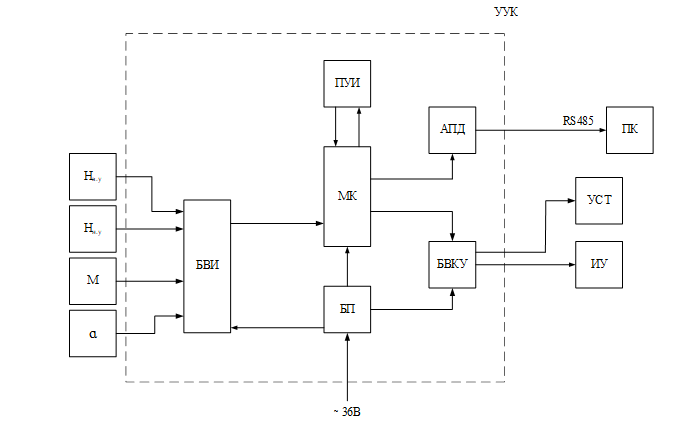
Рисунок 2 – Структурная схема устройства автоматизации работы промежуточного бункера.
Схема работает следующим образом. Сигналы о значениях технологических параметров с аналоговых и дискретных датчиков поступают в блок ввода информации БВИ. Там они приводятся к стандартному виду и далее сигнал поступает на вход микроконтроллера МК. В микроконтроллере происходит обработка полученных данных с датчиков в соответствии с записанной программой. Микроконтроллер МК подает сформированные сигналы управления через блок ввода команд управления БВКУ на исполнительные устройства ИУ и устройства сигнализации УСТ. На пульте управления и индикации расположены светодиоды и информационное табло, которые информируют о том, находятся ли в норме следующие технологические параметры: скорость движения ленты, ее натяжение, отсутствует ли сход ленты. Также на внешнюю панель вынесены кнопки управления оператора. Питание устройства осуществляется при помощи блока питания, предназначенного для формирования напряжения по уровню качеству требуемого системой.
Адаптер передачи данных (АПД) предназначен преобразования уровня и вида сигнала с МК для передачи технологической информации о работе конвейера на ПК горного диспетчера.
В соответствии со структурной схемой разработана функциональная схема устройства, она приведена на рисунке 3.
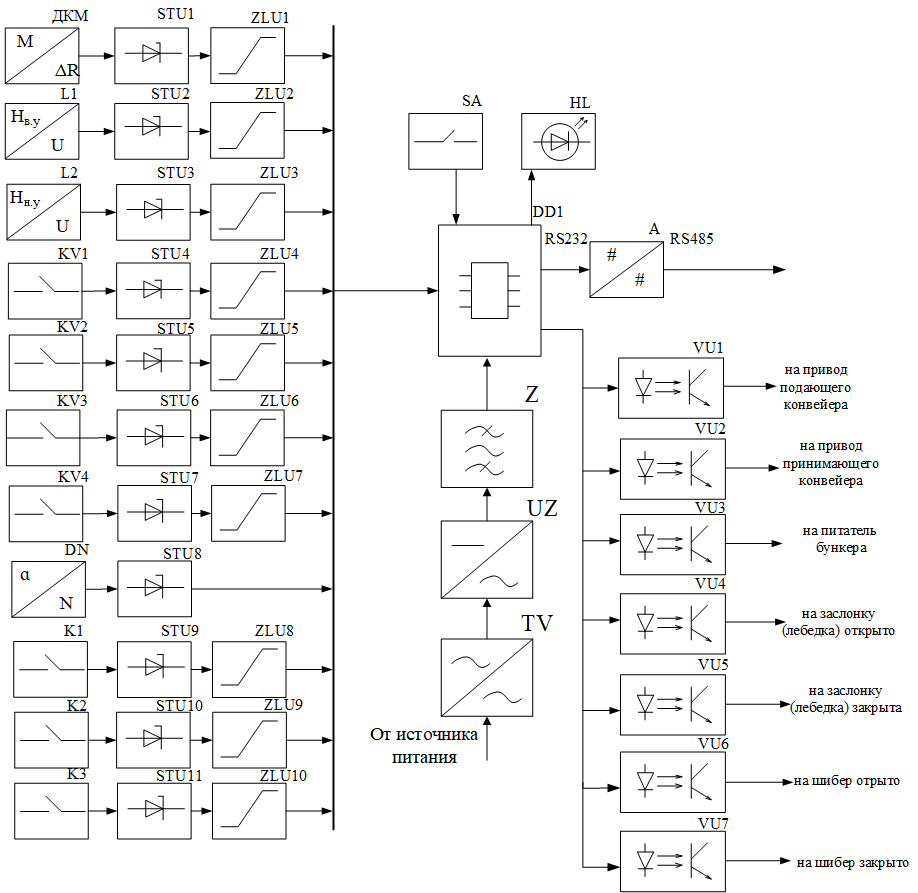
Рисунок 3 – Функциональная схема устройства автоматизации работы промежуточного бункера.
Рассмотрим работу функциональной схемы. Разрабатываемое устройство работает с информационными сигналами со следующих технологических датчиков:
В качестве источников информационных сигналов используются датчик крутящего момента, датчики верхнего и нижнего уровней, датчики крайних положений шибера бункера, датчик положений заслонки, датчик угла открытия шибера и блок-контакты приводов конвейеров и питателя. Датчики нижнего и верхнего уровней производят преобразования сигнала в сигнал напряжения, датчик крутящего момента преобразовывает сигнал в сигнал сопротивления, датчик угла открытия преобразовывает угол открытия заслонки в количество импульсов.
Сигнал от внешнего источника питания (встроенный трансформатор в ПВИ) поступает на силовой трансформатор TV, далее на UZ2, где преобразовывается из переменного напряжения в постоянное и на фильтр Z.
Через интерфейс RS-485 осуществляется обратная связь с диспетчером шахты.
Блок VU представляет собой семисторную оптопару и обеспечивает гальваническую развязку внутренних цепей устройства с линиями связи исполнительного устройства. Через реле сигнал поступает на реверсивный контакт пускателя подающего конвейера, принимающего конвейера, на питатель бункера, на открытие и закрытие заслонки, на открытие и закрытие шибера.
Поскольку устройство применятся в шахтных условиях необходимо обеспечить искробезопасность входных цепей. Для этого применяются блоки искрозащиты (VD1-VD9). Для исключения возможности скачков напряжения от датчиков и повреждения блока микропроцессора включаем токоограничивающие блоки (ZLU1-ZLU10).
6. Эксплуатационные требования к устройству автоматизации
Для обеспечения безопасной эксплуатации ленточных конвейеров обязательным условием является прямолинейность выработки по всей длине става конвейера и отсутствие участков с резким изменением угла ее наклона в вертикальной плоскости.[9]
В соответствии с требованиями Правил безопасности ленточные конвейера должны оборудоваться: датчиками контроля бокового схода ленты типа КСЛ, отключающими привод конвейера при сходе ленты в сторону более 10% ее ширины; устройствами по очистке лент и барабанов; тормозными устройствами; устройствами, улавливающими грузовую ветвь ленты при ее разрыве, или устройствами, контролирующими целостность тросов и стыковых соединений резинотросовых лент в выработках с углом наклона более 10 градусов; средствами защиты, обеспечивающими отключение привода конвейера при превышении допустимого уровня транспортируемого материала в местах перегрузки, снижении скорости ленты до 75% номинальной (пробуксовка), превышении номинальной скорости ленты бремсберговых конвейеров на 8%; устройством для отключения привода конвейера из любой точки по его длине; средствами пылеподавления в местах перегрузок; средствами автоматического и ручного пожаротушения.
Монтаж системы автоматизации:
Мероприятия по предотвращению пожаров
Предусмотрен следующий комплекс противопожарных мероприятий:
В случае возникновения пожара разрабатываются специальные организационно-технические меры по спасению людей:
План ликвидации аварии существующий на шахте должен быть разработан в строгом соответствии с Инструкцией по составлению планов ликвидации аварий
, Правил безопасности в угольных шахтах
.
Выводы
В магистерской диссертации были разработаны критерии управления работой конвейерного транспорта с применением промежуточного бункера по которым достигается его оптимальная работа.
Приняв за основу критерии управления было разработано устройство автоматизации промежуточных бункеров магистральной конвейерной линии, которое удовлетворяет заявленным к ней требованиям. То есть, устройство автоматизации позволяет регулировать работу магистральной конвейерной линии в соответствии с поставленной задачей оптимального функционирования конвейерным транспортом.
Разработана структурная и функциональные схемы устройства, которые отображают структуру построения устройства.
И, как результат проведенной работы было разработано устройство автоматизации промежуточных бункеров магистральной конвейерной линии, которое применяется в составе системы автоматизированного управления разветвленными конвейерными линиями САУКЛ.
При написании данного реферата магистерская работа еще не завершена. Окончательное завершение: июнь 2019 года. Полный текст работы и материалы по теме могут быть получены у автора или его руководителя после указанной даты.
Список источников
- Стадник, Н.И. Справочник по автоматизации шахтного конвейерного транспорта / Н.И. Стадник, В.Г. Ильюшенко, С.И. Егоров и др. – Киев: Техника, 1992. – 436 с.
- Батицкий, И. А. Автоматизация производственных процессов и АСУ ТП в горной промышленности/ И. А. Батицкий, В. И. Куроедов, А. А. Рыжков. – Москва: Недра, 1991. – 303 с.
- Мелькумов, Л.Г. Автоматизация технологических процессов угольных шахт /Л.Г.Мелькумов, Н.Я. Лазукин, Б.Х. Богопольский, Р.Л. Розенберг. – Москва: Недра,1973. -352 с.
- Малиновский, А.К. Автоматизированный электропривод машин и установок шахт и рудников/ А.К. Малиновский – Москва, Недра, 1987.-280 с.
- Бедняк, Г.И. Автоматизация производства на угольных шахтах / Г.И. Бедняк, В.А., Ульшин, В.П. Довженко и др. - Киев: Техника, 1989. – 272 с.
- Толпежников, Л.И. Автоматическое управление процессами шахт и рудников/ Л.И. Толпежников– Москва: Недра, 1985. –352 с.
- Датчики компании KLASCHKA
- Овсянников, Ю. А. Автоматизация подземного оборудования: справ. рабочего / Ю. А. Овсянников, А. А. Кораблев, А. А. Топорков. - Москва: Недра, 1990. - 287с.
- НПАОП 10.0-1.01-10. Правила безпеки у вугільних шахтах. Наказ Державного комітету України з промислової безпеки, охорони праці та гірничого нагляду №62 від 23.03.2010. – 150с.
- Каминский, М. Л. Монтаж приборов и систем автоматизации / М. Л. Каминский, В. М. Каминский .– Москва : Высшая школа, 1997 . – 304 с.
- НПАОП 10.0-5.18-04. Инструкция по противопожарной защите угольных шахт