Реферат за темою випускної роботи
Зміст
- Вступ
- 1. Актуальність теми
- 2. Мета і задачі дослідження
- 3. Конвеєрна установка як об'єкт автоматизації
- 4. Аналіз досліджень і розробок по даній темі
- 5. Схемні рішення пристрою автоматизації проміжного бункера
- 6. Експлуатаційні вимоги до пристрою автоматизації
- Висновки
- Перелік посилань
Вступ
Стрічкові конвеєри здатні здійснювати безперервне транспортування вантажів на великі відстані, що з технологічних причин обумовлює їх незамінність на шахтах і рудниках. Саме тому, особливого значення набуває питання надійної і безпечної експлуатації конвеєрних ліній.
Контролювати технологічні параметри стрічкових конвеєрів необхідно як для забезпечення безперервної та безаварійної роботи конвеєра, так і для необхідної продуктивності конвеєра, а також стабілізації погонного навантаження на стрічку. Для вирішення цих задач необхідно здійснювати оперативне управління конвеєрними установками, а також проміжними бункерами магістральних конвеєрних ліній.
1. Актуальність теми
Розвиток автоматизації шахтних конвеєрних ліній протягом тривалого періоду визначалося необхідністю зниження трудомісткості управління і підвищення безпеки експлуатації конвеєрного транспорту. У зв'язку з цим широке поширення набуло автоматизоване управління конвеєрною лінією, технічна сутність якого полягає в централізації управління процесами пуску-зупинки конвеєрів, а також в забезпеченні автоматичного захисту від розвитку аварії при виникненні аварійних ситуацій.[1]
Однак, питання автоматизації проміжних бункерів досі не знайшли свого вирішення. Апаратура контролю роботи проміжних бункерів має обмежені функціональні можливості і застарілу елементну базу. Таким чином, проблема розробки пристрою автоматичного управління проміжними бункерами конвеєрних ліній актуальна.
2. Мета і задачі дослідження
Метою магістерської дисертації є підвищення ефективності та безпеки роботи конвеєрного транспорту шляхом комплексної автоматизації його роботи, а також розробки блоку автоматизації роботи проміжних бункерів.
Основні задачі дослідження:
3. Конвеєрна установка як об'єкт автоматизації
Конвеєрні установки завдяки своїм якостям (значна продуктивність, велика довжина транспортування, здатність безперервно пересувати вантажі, придатність до автоматизації та дистанційного управління, висока безпека робіт і ін.), є найбільш ефективним засобом переміщення насипних матеріалів на шахтах (рудниках). Вони використовуються не тільки для транспортування насипних вантажів, а й для перевезення людей.[2]
Використання конвеєрних установок на горизонтальних і похилих виробках дозволяє в умовах багатьох шахт Донбасу розміщувати конвеєри від забою до околоствольного двору, що в свою чергу забезпечує переклад транспортування вугілля на потік, скорочує кількість обслуговуючого персоналу і створює умови для роботи в режимі ресурсозбереження. Потокова технологія транспортування основного вантажу досить легко забезпечується при застосуванні сучасних засобів конвеєрного транспорту.
Принцип дії стрічкового конвеєра полягає в переміщенні вантажу на гнучкій нескінченно замкнутой стрічці, яка переміщується по нерухомих опор. Гнучка нескінченна стрічка огинає приводний барабан і натяжний барабан, а в прольоті між ними спирається на ряд роликових опор, встановлених з певним інтервалом на рамі. Матеріал надходить на стрічку через завантажувальну воронку і розвантажується через приводний барабан.
Сучасні підземні конвеєрні лінії характеризуються значною протяжністю і розгалуженістю транспортних магістралей, що змінюють з часом свої параметри.[3] Характерною особливістю шахтних конвеєрних ліній є висока нерівномірність вантажопотоку, викликана фактом обслуговування очисного і підготовчого вибоїв. Саме технологічні паузи в роботі механізмів є причиною змінного вантажопотоку. Нерівномірність надходження вантажу веде до нераціонального використання потужності приводу (при недовантаженні), а також надмірного зносу тягового органу і зниження надійності АД (при перевантаженні).[4] Для стабілізації вантажопотоку, як правило, використовуються проміжні бункера. Схема механізації проміжного бункера представлена на рисунку 1.
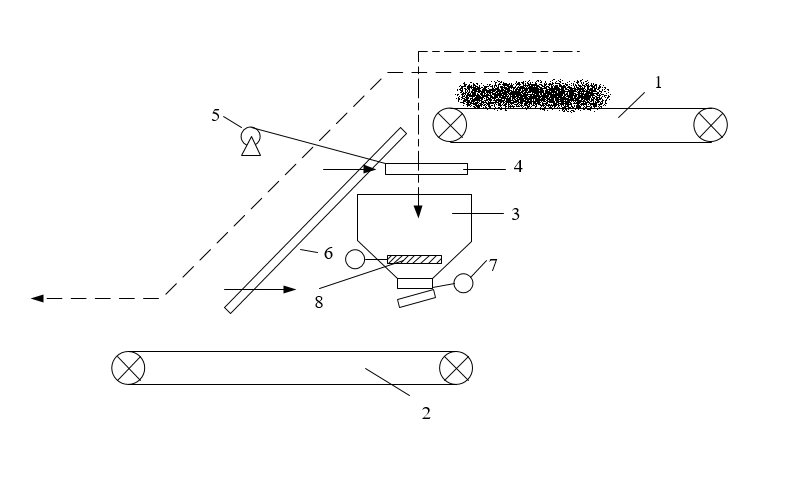
Рисунок 1 - Схема механізації проміжного бункера: 1– подаючий конвеєр; 2– приймаючий конвеєр; 3–бункер; 4–заслонка для переведення в режим завантаження бункера; 5–маневрова лебідка заслонки завантаження бункера; 6– жолоб; 7–привід шибера; 8– шибер
(анімація: 7 кадрів, затримка 1000 мс, 72 кілобайт)
Механізований бункер працює наступним чином. При нормальній роботі транспортної системи вантажопотік з конвеєра, що подає перевантажується на приймаючий транзитом. При цьому заслонка 4 встановлюється в крайнє праве положення і вугілля по жолобу 6 потрапляє на приймаючий конвеєр 2. При зупинці конвеєра 2 заслонка перекладається в вкрайнє ліве положення і вугілля потрапляє в бункер 3. Датчиком рівня контролюється верхній рівень вугілля в бункері. Якщо спрацьовує датчик контролю верхнього рівня завантаження бункера і приймаючий конвеєр 2 не працює, то подаючий конвеєр 1 відключається з роботи.
Загальні вимоги до системи автоматизації стрічкового конвеєра:
Виконання всіх вимог, що пред'являються до автоматизованих конвеєрних ліній, забезпечує надійне транспортування корисних копалин і безпечне перевезення шахтарів.
4.Аналіз досліджень і розробок по даній темі
Апаратура автоматизації конвеєрного транспорту шахти
В даний час відомі наступні апаратури автоматизації конвеєрних ліній:
Комплекс АУК.1М призначений для управління і контролю роботи стаціонарних і напівстаціонарних нерозгалужених конвеєрних ліній, що складаються з стрічкових і скребкових конвеєрів з числом конвеєрів до 10.[5] Комплекс АУК.1М може застосовуватися також для управління розгалуженими конвеєрними лініями (до трьох відгалужень, кожне з яких управляється як нерозгалужена конвеєрна лінія). Кількість конвеєрів в лінії одного напрямку не більше 10.
Система автоматизованого управління розгалуженими конвеєрними лініями САУКЛ призначена для:
шибер,
перевантажувач,
живильник);
Комплекс автоматизованого управління конвеєрами АУК.3 призначений для автоматизованого управління нерозгалуженими конвеєрними лініями, що складаються з стрічкових і скребкових конвеєрів із загальним числом конвеєрів в лінії до 10 включно, виконавчими органами накопичувальних бункерів, монорейковими канатними дорогами (вантажними), рейковими канатними напочвенними дорогами (вантажними) і багатоканатними дорогами крісельного типу. Комплекс є комплектуючим виробом стрічкового конвеєра (лінії конвеєрів). Комплекс АУК.3 сумісний з комплексом АУК.1М в частині лінії управління та зв'язку.
Також розглянемо існуюче нині технічне рішення по автоматизації накопичувальних ємностей та контролю рівня сипучих матеріалів. В даний момент на шахтах застосовується реле контролю рівня РКУ-1М.
Пристрій реле РКУ.1М призначене для іскробезпечного контролю рівня заповнення накопичувальних ємностей струмопровідними сипучими матеріалами і рідинами з перехідним опором не більше 3 МОм, а також для сигналізації по голим проводам з самоконтролем цілості лінії.[6]
Реле РКУ. 1М виконано у вибухозахищеної оболонці, розділеної перегородкою на відділення вводів і відділення виймальної частини. На перегородці розташовані шість прохідних затискачів для іскронебезпечних кіл і 11 для іскробезпечних кіл сигналізації і управління. Оболонка має шість кабельних вводів, призначених для гнучких кабелів діаметром до 25 мм. Виемна частина являє собою панель, на якій змонтовані наступні функціональні вузли реле: трансформатор; блок конденсаторів; вимикач; електронний блок; вихідні реле; панель управління і сигналізації. Як датчик використовується датчик рівня ДУ. Він має пластмасовий корпус, в нижній частині якого встановлено охоронне кільце. Кабельний ввід датчика розрахований на гнучкий кабель з зовнішнім діаметром 16-22 мм. Опір ізоляції цього кабелю має бути не менше 10 МОм. Довжина лінії між реле і датчиком не повинна перевищувати 500 м. Іскробезпека схеми забезпечується параметрами трансформатора і застосовуваних елементів, а також вибором режимів їх роботи відповідно до технічних характеристик і застосуванням захисних засобів - іскрогасящіх шунтів і обмежувачів.
Як датчики рівня матеріалу в проміжних бункерах доцільно використовувати електродні датчики, що застосовуються в РКУ.
Як датчик положення регульованої заслонки приймемо датчик наближення KLASCHKA типу, Allmetall.[7]
Принцип його роботи наступний. Зчитування положення здійснюється в даному випадку за допомогою індуктивного датчика наближення. Диск виконаний таким чином, щоб при максимальній частоті обертів і імпульсів встановилося співвідношення тривалості імпульсу і паузи 1: (0,7 ... 1,3). Коефіцієнт заповнення імпульсів визначається статично:
В якості датчиків крайніх положень шибера і заслонки використовуються кінцеві вимикачі. Кінцеві вимикачі використовуються для автоматичного вимкнення виконавчого механізму при досягненні рухомої частини певного місця. Для шахт небезпечних за газом та пилом доцільно вибрати вимикач кінцевий вибухозахищений ВКВ, що має рівень вибухозахисту підвищена надійність проти вибуху
.[8]
5. Схемні рішення пристрою автоматизації проміжного бункера
Структурна схема пристрою автоматизації роботи проміжного бункера наведена на рисунку 2.
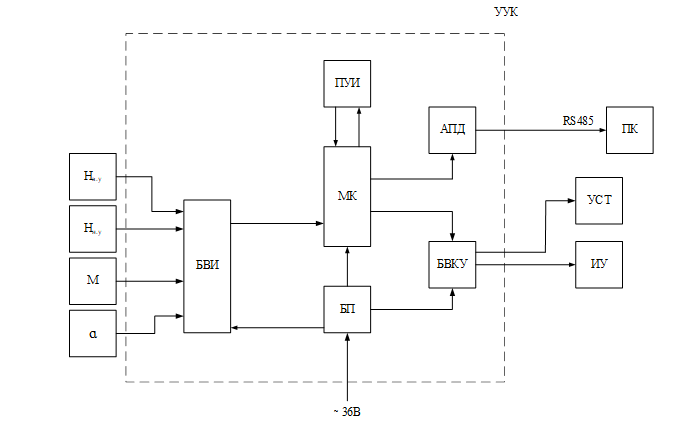
Рисунок 2 - Структурна схема пристрою автоматизації роботи проміжного бункера.
Схема працює наступним чином. Сигнали про значення технологічних параметрів з аналогових і дискретних датчиків надходять в блок введення інформації БВИ. Там вони приводяться до стандартного вигляду та далі сигнал надходить на вхід мікроконтролера МК. У мікроконтролері відбувається обробка отриманих даних з датчиків відповідно до записів програми. Мікроконтролер МК подає сформовані сигнали управління через блок введення команд управління БВКУ на виконавчі пристрої ІУ і пристрої сигналізації УСТ. На пульті управління і індикації розташовані світлодіоди і інформаційне табло, які інформують про те, чи знаходяться в нормі такі технологічні параметри: швидкість руху стрічки, її натяг, відсутність сходу стрічки. Також на зовнішню панель винесені кнопки управління оператора. Пристрій працює за допомогою блоку живлення, призначеного для формування напруги за рівнем якості необхідного системою.
Адаптер передачі даних (АПД) призначений для перетворення рівня і виду сигналу з МК для передачі технологічної інформації про роботу конвеєра на ПК гірського диспетчера.
Відповідно до структурної схемою розроблена функціональна схема пристрою, що наведена на рисунку 3.
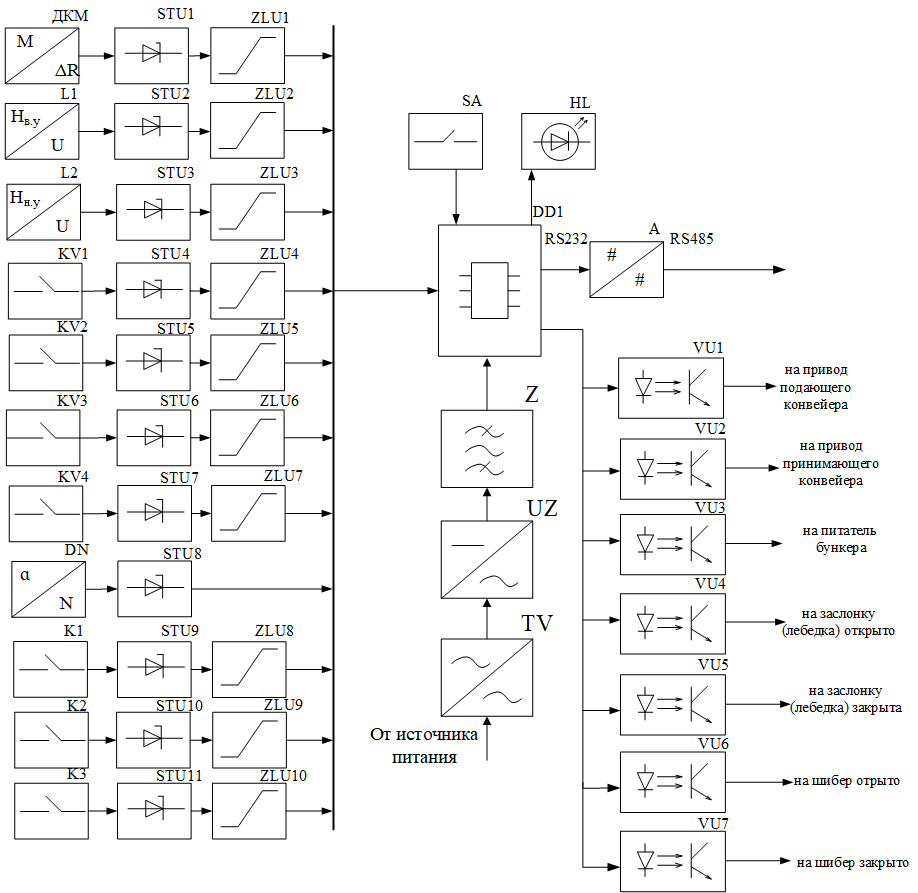
Рисунок 3 – Функціональна схема пристрою автоматизації роботи проміжного бункера.
Розглянемо роботу функціональної схеми. Розроблювальний пристрій працює з інформаційними сигналами з наступних технологічних датчиків:
Як джерела інформаційних сигналів використовуються датчик крутного моменту, датчики верхнього і нижнього рівнів, датчики крайніх положень шибера бункера, датчик положень заслінки, датчик кута відкриття шибера і блок-контакти приводів конвеєрів і живильника. Датчики нижнього і верхнього рівнів виробляють перетворення сигналу в сигнал напруги, датчик крутного моменту перетворює сигнал в сигнал опору, датчик кута відкриття перетворює кут відкриття заслінки в кількість імпульсів.
Сигнал від зовнішнього джерела живлення (вбудований трансформатор в ПВІ) надходить на силовий трансформатор TV, далі на UZ2, де перетворюється з змінної напруги в постійне і на фільтр Z.
Через інтерфейс RS-485 здійснюється зворотний зв'язок з диспетчером шахти.
Блок VU є семісторною оптопарою і забезпечує гальванічну розв'язку внутрішніх ланцюгів пристрою з лініями зв'язку виконавчого пристрою. Через реле сигнал надходить на реверсивний контакт пускача подаючого конвеєра, приймаючого конвеєра, на живильник бункера, на відкриття та закриття заслонки, на відкриття та закриття шибера.
Оскільки пристрій застосуються в шахтних умовах необхідно забезпечити іскробезпеку вхідних ланцюгів. Для цього застосовуються блоки іскрозахисту (VD1-VD9). Для виключення можливості стрибків напруги від датчиків і пошкодження блоку мікропроцесора включаємо струмообмежувальні блоки (ZLU1-ZLU10).
6. Експлуатаційні вимоги до пристрою автоматизації
Для забезпечення безпечної експлуатації стрічкових конвеєрів обов'язковою умовою є прямолінійність вироблення по всій довжині става конвеєра і відсутність ділянок з різкою зміною кута її нахилу у вертикальній площині.[9]
Відповідно до вимог Правил безпеки стрічкові конвеєра повинні бути обладнані: датчиками контролю бічного сходу стрічки типу КСЛ, що вимикають привод конвеєра під час сходження стрічки в бік більш ніж на 10% від її ширини; пристроями для очищення стрічок і барабанів; гальмівними пристроями; пристроями, що вловлюють вантажну вітку стрічки при її розриві, або пристроями, контролюючими цілісність тросів і стикових з'єднань гумотросових стрічок у виробках з кутом нахилу більше 10 градусів; засобами захисту, що забезпечують вимикання приводу конвеєра при перевищенні допустимого рівня матеріалу, що транспортується в місцях перевантаження, зниженні швидкості стрічки до 75% номінальної (пробуксовка), перевищенні номінальної швидкості стрічки бремсбергових конвеєрів на 8%; пристроєм для відключення приводу конвеєра з будь-якої точки по його довжині; засобами пилоподавлення в місцях перевантажень; засобами автоматичного і ручного пожежогасіння.
Монтаж системи автоматизації:
Заходи щодо запобігання пожежам
Передбачений наступний комплекс протипожежних заходів:
У разі виникнення пожежі розробляються спеціальні організаційно-технічні заходи з порятунку людей:
План ліквідації аварії існуючий на шахті повинен бути розроблений в суворій відповідності з Інструкцією по складанню планів ліквідації аварій
, Правил безпеки у вугільних шахтах
.
Висновки
У магістерській дисертації були розроблені критерії управління роботою конвеєрного транспорту із застосуванням проміжного бункера за якими досягається його оптимальна робота.
Прийнявши за основу критерії управління було розроблено пристрій автоматизації проміжних бункерів магістральної конвеєрної лінії, яке задовольняє заявленим до неї вимогам. Тобто, пристрій автоматизації дозволяє регулювати роботу магістральної конвеєрної лінії відповідно до поставленим завданням оптимального функціонування конвеєрним транспортом.
Розроблено структурну та функціональні схеми пристрою, які відображають структуру побудови пристрою.
І, як результат проведеної роботи було розроблено пристрій автоматизації проміжних бункерів магістральної конвеєрної лінії, яке застосовується в складі системи автоматизованого управління розгалуженими конвеєрними лініями САУКЛ.
На момент написання даного реферату магістерська робота ще не завершена. Остаточне завершення: червень 2019 року. Повний текст роботи і матеріали по темі можуть бути отримані у автора або його керівника після зазначеної дати.
Список джерел
- Стадник, Н.И. Справочник по автоматизации шахтного конвейерного транспорта / Н.И. Стадник, В.Г. Ильюшенко, С.И. Егоров и др. – Киев: Техника, 1992. – 436 с.
- Батицкий, И. А. Автоматизация производственных процессов и АСУ ТП в горной промышленности/ И. А. Батицкий, В. И. Куроедов, А. А. Рыжков. – Москва: Недра, 1991. – 303 с.
- Мелькумов, Л.Г. Автоматизация технологических процессов угольных шахт /Л.Г.Мелькумов, Н.Я. Лазукин, Б.Х. Богопольский, Р.Л. Розенберг. – Москва: Недра,1973. -352 с.
- Малиновский, А.К. Автоматизированный электропривод машин и установок шахт и рудников/ А.К. Малиновский – Москва, Недра, 1987.-280 с.
- Бедняк, Г.И. Автоматизация производства на угольных шахтах / Г.И. Бедняк, В.А., Ульшин, В.П. Довженко и др. - Киев: Техника, 1989. – 272 с.
- Толпежников, Л.И. Автоматическое управление процессами шахт и рудников/ Л.И. Толпежников– Москва: Недра, 1985. –352 с.
- Датчики компании KLASCHKA
- Овсянников, Ю. А. Автоматизация подземного оборудования: справ. рабочего / Ю. А. Овсянников, А. А. Кораблев, А. А. Топорков. - Москва: Недра, 1990. - 287с.
- НПАОП 10.0-1.01-10. Правила безпеки у вугільних шахтах. Наказ Державного комітету України з промислової безпеки, охорони праці та гірничого нагляду №62 від 23.03.2010. – 150с.
- Каминский, М. Л. Монтаж приборов и систем автоматизации / М. Л. Каминский, В. М. Каминский .– Москва : Высшая школа, 1997 . – 304 с.
- НПАОП 10.0-5.18-04. Инструкция по противопожарной защите угольных шахт