Abstract
Contents
![]() Animation: 14 frames, ∞ cycles |
---|
Introduction
One of the promising areas of development and improvement of industries is introduction and use of industrial robots in large and medium-sized industries. Industrial robots have great functional flexibility due to progressive actuators, efficient drives, microprocessor systems with advanced software, technical vision and other means of sensation, as well as adaptive capabilities and elements of artificial intelligence. Such robots make it possible to replace humans in production jobs related to heavy, monotonous, dangerous and harmful working conditions. An important feature of industrial robots is the ability to use them to perform work that cannot be mechanized and automated by traditional means [1].
1. Relevance of the topic
A modern industrial robot manipulator is applicable to replace human labor. So, the robot can use a tool grip to hold the tool and implement processing the workpiece, or keep the workpiece itself to feed it into the work area for further processing.
When using a robot, performance is usually improved, as the robot can perform the movement and the positioning of the working tool is much faster than man, and also thanks to the continuous the work of the robot 24 hours a day, without interruptions and stops, in contrast to humans. With the right choice robotic system performance increases by several times or even an order of magnitude, compared with manual production.
2. The purpose and objectives of the study, the planned results
The aim of the work is to develop an automated control system the movement of the links of the industrial two-handed robot designed for loading and unloading of heavy, brittle and sheet materials of glass, steel, plywood and other designs.
The purpose of the development is the improvement of working conditions for working personnel, increasing the efficiency and the exclusion of errors in the handling of goods of varying severity in production.
The tasks of the automatic control system of the two-armed robot are:
- Achievement of specified quality indicators when implementing an automatic system control two-armed robot.
- The implementation of the continuous cycle of the two-handed robot.
- Providing high precision positioning of the robot's tongs by controlling the executive mechanisms.
- Articulated Drive Control for speed and accuracy management of working bodies.
3. Formulation of the problem
The object of control in this work is a two-armed industrial robot (IR). is he is a universal electromechanical device consisting of two manipulators - actuators. The basic elements of the robot are manipulators - mechanisms with several degrees of mobility and are designed to move and orientation of objects in the workspace. Multiple link design ends with a gripper or interchangeable tool that are designed to capture objects a certain form and execution of technological operations, respectively. PR Manipulators designed to perform motor functions when moving objects in space. The movement of the robot is carried out on rails. Structurally, this PR represents open loop consisting of 10 solid bodies (units) connected in series joints that drive the links into rotational motion with the help of power actuators, installed at each joint (Fig. 1) [3].
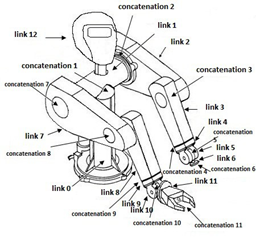
Figure 1 – The design of the two-handed robot
Link 0 is the base of the manipulator, and link 1 is the shoulder joint, which is perpendicularly attached to the base. On it are attached the "hands" of the robot - manipulators. The end of each “arm” is equipped with a working tool - a gripper that is designed to grip and hold objects of manipulation. The relative movement of the joints goes over the links in As a result, the manipulator grips occupy the necessary position in space to capture objects.
The gripping devices of the manipulators are designed for gripping flat sheet materials and have a type of two-point centering grip. This type of gripper provides high precision position in space. The design of grips involves turning grips on 90 ° due to the rotary pneumatic motors built into the tongs. This allows you to capture both horizontally and vertically arranged materials.
4. The composition and principle of operation of the system
Two-handed multi-purpose robots are universal mechanisms with a large spectrum. technological capabilities because Designed for the transport of highly destructive materials complex configuration. Therefore, this control object must provide high accuracy positioning to ensure the integrity of the goods [4].
In general, the process of controlling the movement of links of two-handed PR manipulators can be represented in this way:
Step 1. Set the coordinates of the positioning points, the source and destination points.
Step 2. Move the gripping device to the coordinates of the part captured from the surface.
Step 3. Go to the position to capture the part.
Step 4. Turn on the pneumatic gripper and capture the part.
Step 5. Move the gripper with the part to the desired location.
Step 6. Turn off the gripper.
Step 7. Repeat from Step 2.
Based on the above algorithm, which is the basis of the program of actions of the robot, We define the structure of the object with all the auxiliary devices required for its operation.
The IR consists of the following main parts (Fig. 2):
– manipulator, or otherwise mechanical system of the robot;
– Information system;
– software control system, or otherwise control device.
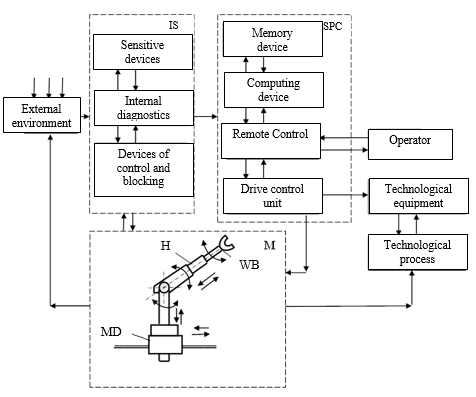
Figure 2 – Scheme of the control system of the robot arm
In the aggregate, the information system and the software control system form the device automatic control.
IR manipulators contain a working body in the form of a gripping device and mechanisms, necessary to perform all of its motor functions:
– gears;
– actuators;
– drives;
– bearing elements.
An actuator IR with a drive and a gripper is called a manipulator arm. To move the manipulator relative to the process equipment are used. movement devices.
Conclusions
The paper presents the development of an automatic motion control system for links. Manipulators of a two-handed robot designed to perform loading and unloading operations of brittle, heavy and sheet materials of plywood, glass, steel and other performances. Bringing the links in motion is carried out on a rigidly defined cyclic the program. At the first stage of the work, the automation object was analyzed, its characteristics and requirements for which it is necessary to carry out the synthesis of tracking ACS.
References
- Козырев Ю.Г. Современные промышленные роботы: Каталог / Под ред. Ю.Г. Козырева, Я.А.Шифрина. – М.: Машиностроение, 1984. – 152 с.
- Фу К. Робототехника / Фу К., Гонсалес Р., Ли К. – М.: Мир, 1989. – 624 с.
- Шахинпур М. Курс робототехники / Шахинпур М. – М.: Мир, 1990. – 527 с.
- Зайцев Г.Ф. Теория автоматического управления и регулирования / Зайцев Г.Ф. – К.: Вища школа, 1989. – 431 с.
- Дорф Р. Современные системы управления / Дорф Р., Бишоп Р; Пер. с англ. Копылова Б.И. – М.: Лаборатория Базовых Знаний, 2004. – 832 с.
- Козырев Ю.Г. Промышленные роботы: Справочник / Козырев Ю.Г. – М.: Машиностроение, 1983. – 376 с.
- Голдсуорт Б. Проектирование цифровых логических устройств / Б. Голдсуорт. – М.: Машиностроение, 1985. – 288 с.
- Уилкинсон Б. Основы проектирования цифровых схем / Б. Уилкинсон. – М.: Издательский дом «Вильямс», 2004. – 320 с.
- Бурдаков С.Ф. Проектирование манипуляторов промышленных роботов и роботизированных комплексов / Бурдаков С.Ф., Дьяченко В.А., Тимофеев А.Н. – М.: Высш. шк., 1986. – 264 с.
- Зенкевич С.Л. Основы управления манипуляционными роботами / С.Л. Зенкевич, А.С. Ющенко. – МГТУ им. Н. Э. Баумана, 2005. - 400 с.
- Филлипс Ч. Системы управления с обратной связью / Филлипс Ч., Харбор Р. – М.: Лаборатория Базовых Знаний, 2001. – 616 с: ил.
- Канунник И.А. Механика роботов и манипуляторов: Учеб. пособие / Канунник И.А., Фалалеева Р.В. - Красноярск: Изд-во Краснояр. аграрного ун-та, 1996. – 376 c.
- Попов Е.П. Основы робототехники: Введение в специальность: Учеб. для вузов по спец. «Роботехнические системы и комплексы» / Попов Е.П., Письменный Г.В. – М.: Высш. шк., 1990. – 224 с., ил.
- Нестеров А.Л. Проектирование АСУТП. Методические указания. Книга 1 / Нестеров А.Л. – СПб Издательство ДЕАН, 2006. – 552 с.
- Олссон Г. Цифровые системы автоматизации и управления / Г. Олссон, Д.Пиани – СПб.: Невский Диаллект, 2001. – 557 с.: ил.