Реферат по теме выпускной работы
Содержание
- Введение
- 1. АКТУАЛЬНОСТЬ РАБОТЫ
- 2. ЦЕЛЬ И ЗАДАЧИ ИССЛЕДОВАНИЯ.
- 3. ТЕХНОЛОГИЧЕСКАЯ СХЕМА ПРОИЗВОДСТВА БАНДАЖЕЙ
- 4. РАЗРАБОТКА МЕРОПРИЯТИЙ ПО СОВЕРШЕНСТВОВАНИЮ ТЕХНОЛОГИИ
- 5.ОПРЕДЕЛЕНИЕ СУММАРНЫХ ОБЖАТИЙ С УЧЕТОМ УШИРЕНИЯ
- Выводы
Введение
В настоящее время прокатка является основным способов изготовления кольцевых изделий в технически высокоразвитых странах. Такое положение связано прежде всего с комплексом достоинств такого способа. В первую очередь к таким достоинствам следует отнести низкую себестоимость получаемых изделий, высокую технологичность и гибкость процесса, универсальность применяемого технологического оборудования. Изделия, получаемые таким способом, имеют более однородную в сечении и ориентированную по окружности структуру металла. Отмеченная универсальность и гибкость процесса позволяет получать изделия диаметром от 100 до 8000 мм и высотой от 10 до 1500 мм. Используемые в качестве исходной заготовки слитки и штанги одного диаметра пригодны для прокатки кольцевых изделий широкого диапазона. При прокатке фасонных в сечении кольцевых изделий используется минимальный парк рабочих валков. Имеет место сравнительно низкая потребляемая мощность деформации.
1. АКТУАЛЬНОСТЬ РАБОТЫ
Производство бандажей для подвижного состава железных дорог, бандажей для трамваев и метрополитена осуществляется на прессопрокатной линии кольцебандажного цеха (КБЦ).
Магистерская работа направлена на создание новых и совершенствование существующих технологий с целью энерго- и ресурсосбережения, а также снижения брака, имеющего прокатное происхождение, при производстве бандажей. Настоящее определяет актуальность данных исследований..
2.ЦЕЛЬ И ЗАДАЧИ ИССЛЕДОВАНИЯ
Усовершенствовать метод расчета калибровок и технологию штамповки и прокатки локомотивных бандажей с учетом распределения суммарных радиального и осевого обжатий в процессе прокатки с учетом уширения.Для достижения поставленной цели необходимо решить следующие задачи: * разработать новый способ производства локомотивных бандажей на одном стане, нормирующий течение металла в гребневую и кольцевую части бандажа в процессе его прокатки с целью повышения качества.
3. ТЕХНОЛОГИЧЕСКАЯ СХЕМА ПРОИЗВОДСТВА БАНДАЖЕЙ
Технологическая схема производства кольцевых изделий принята по утвержденному технологическому заданию ВНИТИ 1) № ТЛЗ -61 -22-19-79 [2]. Технологический процесс производства бандажей на прессопрокатной линии происходит по следующей схеме (рисунок 1):
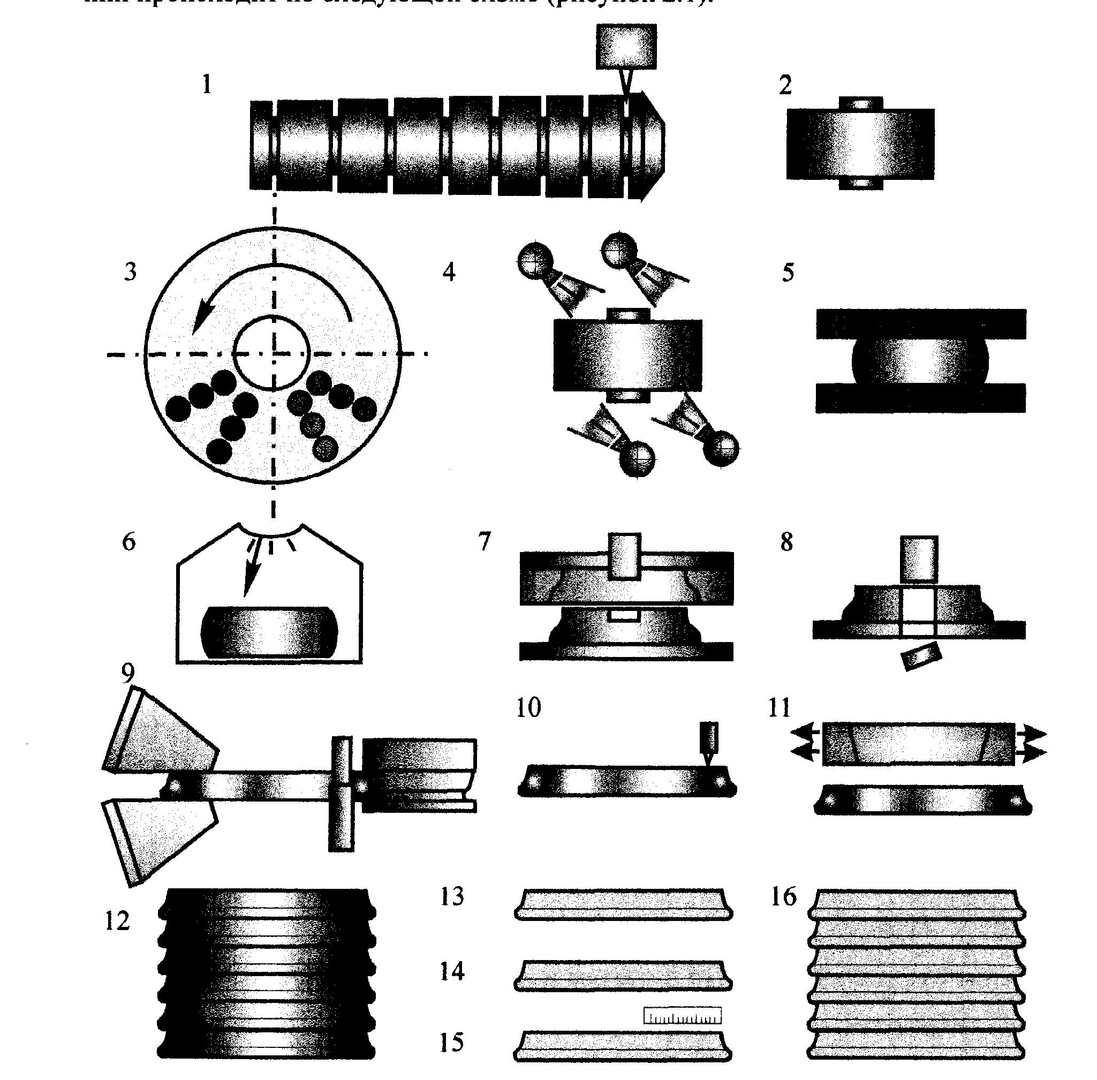
Рисунок 1 — Схема производства бандажей
1. Надрез слитков на слиткоразрезных станах, ломка надрезанных слитков на заготовки и распределение заготовок по весовым категориям на агрегате ломки и сортировке.
2. Осмотр и ремонт заготовок.
3. Нагрев заготовок до 1250-1260°С в кольцевой нагревательной печи.
4. Сбив окалины в камере гидросбива.
5. Осадку заготовки на осадочном прессе усилием 20МН.
6. Взвешивание на весах с целью определения массы выдавливаемого при прошивке металла.
7. Деформация заготовок на заготовочном прессе усилием 40/20МН и выполнение центрального углубления.
8. Прошивка центрального отверстия на прессе усилием 8МН.
9. Прокатка на одном или двух кольцепрокатных станах.
10. Клеймение.
11. Пресс горячей правки.
12. Термообработка.
13. Неразрушающий контроль.
14. Отбор проб для испытаний.
15. Осмотр и замеры.
16. Складирование.
4. РАЗРАБОТКА МЕРОПРИЯТИЙ ПО СОВЕРШЕНСТВОВАНИЮ ТЕХНОЛОГИИ
Технологическая схема производства бандажей имеет существенный недостаток – около 3-4 % брака бандажей по дефектам профиля на прокате. Использованная методика калибровки инструмента деформации (прокатных валков и штампов) допускает появление таких дефектов, как невыполнение гребня, утяжка, неплоскосность и др., что существенно увеличивает себестоимость продукции, что выпускается.
Очевидно, что решения технологических задач проекту должны быть на снижение брака.
Для решения задачи повышения качества бандажей предложено следующее. Во-первых – использование закрытых калибров на кольцепрокатном стане (рис.1). Применение закрытых калибров создает более благоприятную схему деформации в радиальном очаге деформации, и способствует прокатке бандажа с расчетными вытяжками, т.к. высота бандажа=высоте калибра, что, улучшает качество бандажей.
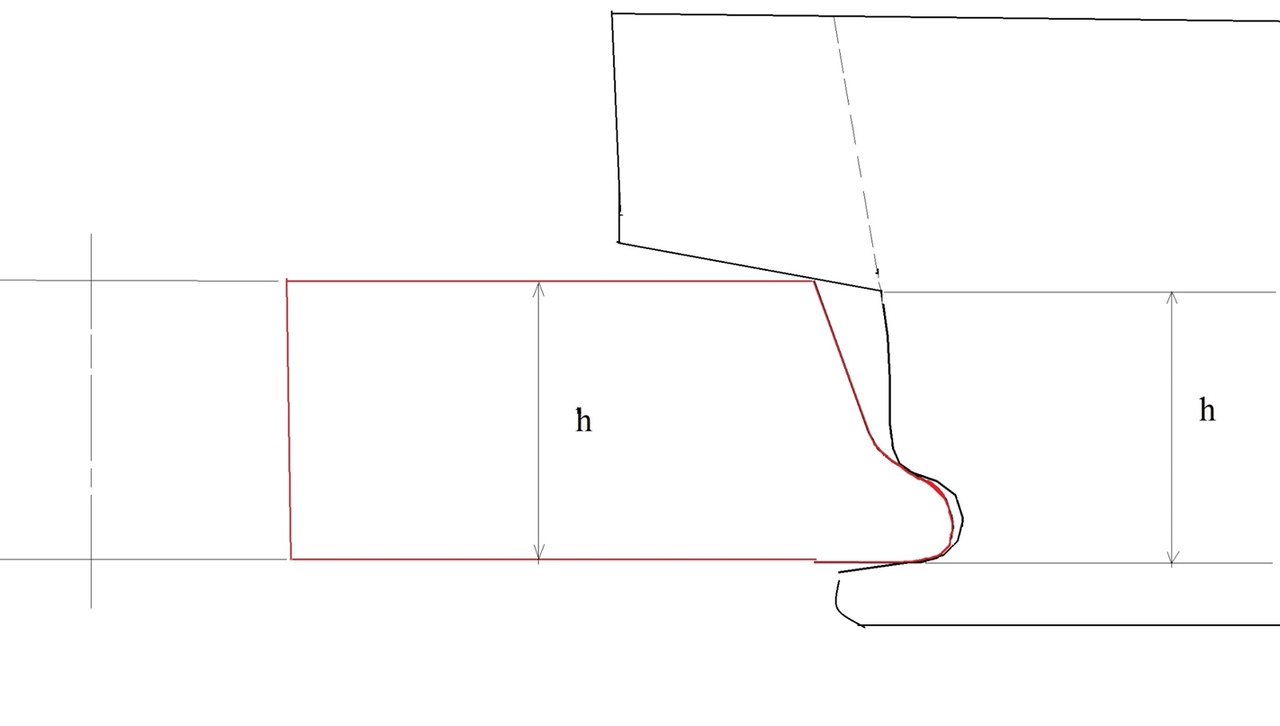
Рисунок 2 – Схема закрытого калибра
Другое – это использование современных методик расчета калибровки, которые исключают при прокатке перетекание металла из гребневой части в кольцевую часть и тем самым позволяют избежать такие дефекты, как утяжка и невыполнение гребня.
На первом этапе определяется величина суммарного осевого обжатия, которое складывается из обжатия как верхним, так и нижним наклонными валками. На практике оно назначается в пределах =(10?30) мм для бандажей, имеющих массу 100?400 кг, соответственно. Тогда высота заготовки L будет равна L= (здесь s– высота бандажа).
Затем необходимо найти размеры гребня заготовки. Они определяются из условия его захода в гребневую часть калибра (рис.3). Заход гребня не должен приводить к такому дефекту как закат. При этом размеры гребня должны быть (с учетом этого условия) максимально возможными. Величины a, b и h определяются из построения (рис.3). При этом необходимо выполнить следующие условия. Во-первых, для исключения образования заката в зоне перехода гребневой части бандажа в кольцевую необходимо, чтобы гребень заготовки в первый момент касания калибра не доходил до дна его гребневой части на величину , равную 5?10 мм (для бандажей, имеющих массу 100?400 кг, соответственно). Во-вторых, дуга у основания гребня бандажа, образованная радиусом r (рис.3) должна плавно переходить в дугу у основания гребня заготовки, образованную радиусом R. Точка контакта указанных выше контуров на рис.3 обозначена буквой А.
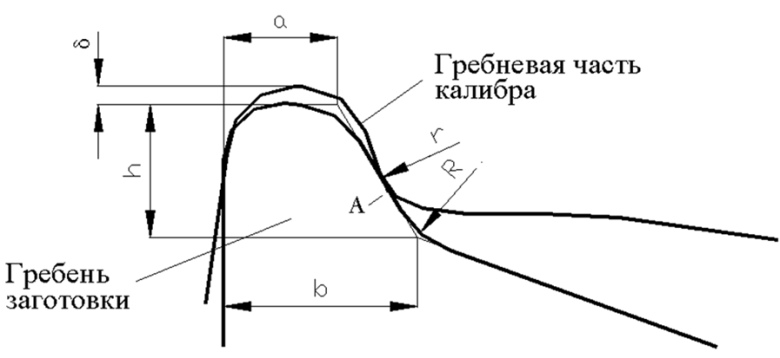
Рисунок 3 – Определение размера гребня заготовки
После этого контур заготовки необходимо расположить относительно контура бандажа так, как это показано на рис.4. Точки скелетов заготовки и бандажа в зоне перехода гребней в кольцевые части должны находиться на одной вертикальной прямой, разделяющей гребневые и кольцевые части бандажа и заготовки.
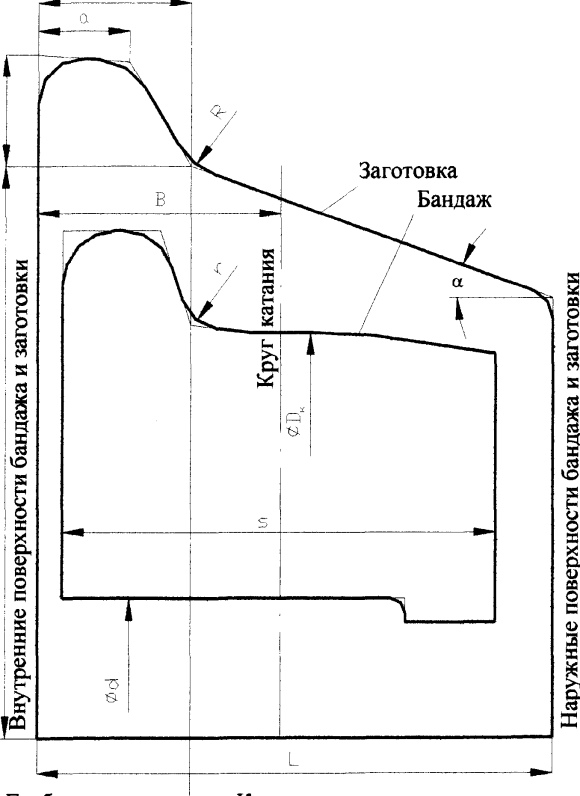
Рисунок 4 – Размещение контуров заготовки и бандажа
Максимальная толщина кольцевой части заготовки H (см. рис.3) находится из условия равенства масс гребневых частей заготовки и бандажа.

где - масса гребневой части заготовки; m- масса бандажа; - масса кольцевой части бандажа; коэффициент в скобках обозначим . Технологические параметры процесса, которые нормируются по данному способу, в частности радиальное осевое обжатие , находим из условия раздельной прокатки гребневой части бандажа из гребневой части заготовки и, соответственно, кольцевой части бандажа из кольцевой части заготовки. Физическая сущность коэффициента k=(1,0?1,03) в выражении (1.1), как раз и заключается в том, что масса гребневой части заготовки , из которой катается гребневая часть бандажа не должна быть меньше последней.
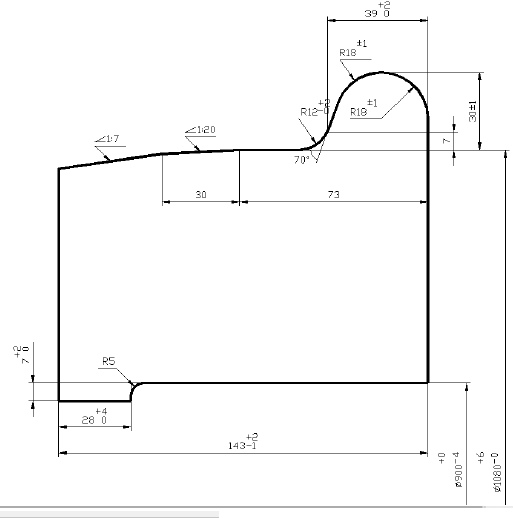
Рисунок 4(а) – Чертеж чистового механически обработанного локомотивного бандажа.
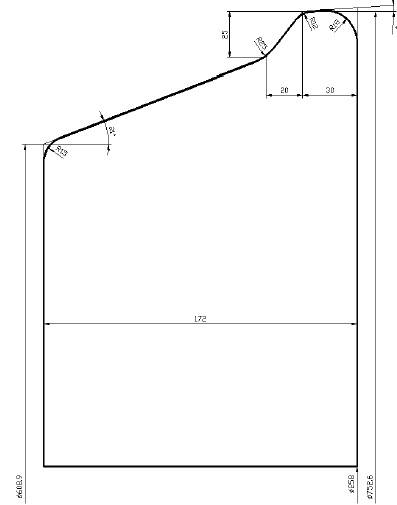
Рисунок 4(б) – Чертеж заготовки полученной на прессе силой.
ОПРЕДЕЛЕНИЕ СУММАРНЫХ ОБЖАТИЙ С УЧЕТОМ УШИРЕНИЯ
Неправильное определение высоты и толщины заготовки и, соответственно, суммарных осевого и радиального обжатий при прокатке кольцевых изделий является причиной получения дефектов готового изделия и, прежде всего, утяжек по боковым и торцевым поверхностям кольцевого изделия. Поэтому важно определить требуемое соотношение как между суммарными радиальным и осевым обжатиями, так и данное соотношение на каждом обороте кольцевого изделия в процессе его прокатки..
Важным условием бездефектной прокатки является отсутствие утяжек. Утяжка на поверхностях кольцевого изделия образуется в том случае, если течение металла в вытяжку (а, соответственно, и в рост диаметра) по различным частям профиля происходит с неодинаковой интенсивностью. Следовательно, условие бездефектной прокатки колец можно записать в виде
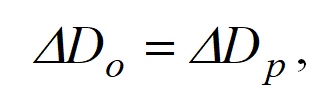
На рис. 3 представлено промежуточное поперечное сечение кольцевого изделия. Предположим, что оно получено в результате обжатия заготовки только в осевом направлении. При этом её диаметр увеличился на величину , а толщина также увеличилась на величину уширения . Определим массу готового кольцевого изделия и массу кольцевой заготовки, полученной после реализации данного осевого обжатия
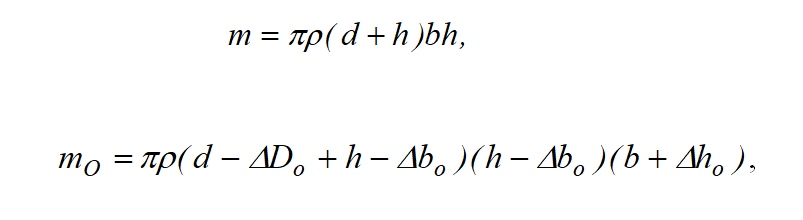
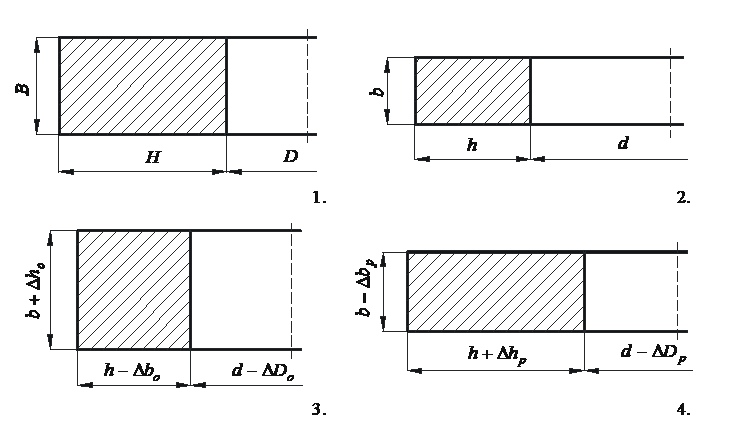
Рис. 5- Схема простановки размеров
1, 2 - сечения исходной кольцевой заготовки и готового кольцевого изделия;
3, 4 - сечения промежуточных раскатов.
Приравнивая массы готового кольцевого изделия и указанного промежуточного раската, получаем

Увеличение диаметра заготовки за счёт реализации осевого обжатия равно

Также представлено и второе промежуточное поперечное сечение кольцевого изделия. Предположим, что оно получено в результате обжатия заготовки только в радиальном направлении. При этом её диаметр увеличился на величину , а высота также увеличилась на величину уширения . Приравнивая массы готового кольцевого изделия и указанного промежуточного раската, получаем

Увеличение диаметра заготовки за счет радиального обжатия равно

Приравнивая и в соответствии с условием (1), получаем первое соотношение для определения размеров исходной заготовки

Уширение заготовки в радиальном направлении вследствие обжатия металла в осевом очаге деформации и уширение заготовки в осевом направлении вследствие обжатия металла в радиальном очаге деформации определим через коэффициенты и осевого и радиального уширения, соответственно

Здесь коэффициенты и определены как функции фактора формы сечения кольцевого изделия других параметров радиального и осевого очагов деформации. Величины осевого и радиального обжатий (см. рис. 5) определены следующим образом

С учётом соотношений данные величины равны

Подставляя функции в условие , в окончательном виде получаем первую зависимость для определения параметров и исходной кольцевой заготовки
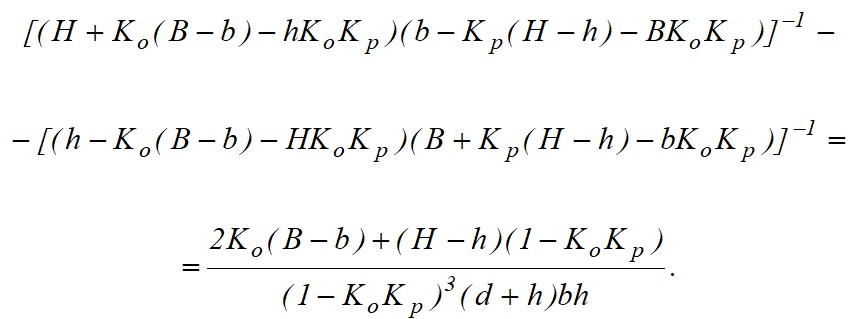
Вторую зависимость найдём, приравнивая массы исходной кольцевой заготовки и готового кольцевого изделия (2). Масса исходной кольцевой заготовки равна
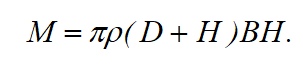
Решая полученное уравнение относительно высоты , окончательно получаем

Система уравнений (12) и (14) определяет параметры заготовки и . Внутренний диаметр исходной кольцевой заготовки , как правило, определяется существующей технологией на прессопрокатной линии и равен диаметру пуансона пресса по прошивке заготовок. Система уравнений (11) определяет соотношения между осевым и радиальным обжатиями, обеспечивающими течение металла в вытяжку и соответственно в рост диаметра с одинаковой интенсивностью в осевом и радиальном направлениях, что является определяющим условием прокатки колец без образования утяжек на его боковых и торцевых поверхностях. Очевидно, что система (11) определяет наиболее рациональные суммарные радиальные и осевые обжатия. Задача определения соотношения между ними на каждом обороте кольцевого изделия в процессе его раскатки должна рассматриваться отдельно.
ВЫВОДЫ:
1. На основе найденных недостатков разработаны мероприятия по совершенствованию технологии: переход к прокатке бандажей малого диаметра на одном кольцепрокатном стане; разработка новой калибровки для производства бандажей малого и среднего диаметра 2. Разработана калибровка для прокатки бандажей на одном стане, что исключает перетекание металла из гребневой части в кольцевую и предотвращает такие дефекты как утяжка и невыполнение гребня.