Abstract
Содержание
- Introduction
- 1.Actuality of theme
- 2.Aim and research tasks
- 3.Methods of receipt of adsorbents
- 4.Beer pellet
- 4.1.Chemical composition and properties of beer pellet
- 4.2.Possibility of the use of beer pellet
- Conclusion
- References
Introduction
The problem of environmental pollution is the most relevant at the present stage of industrial development, including food. Wastes of industrial enterprises affect the processes occurring in ecosystems, and can lead to impaired development of certain types of biocenoses and even to their death.
Model of Moore finite state machine (FSM, offered by E. Moore in 1956 and named in his honor), as synchronous sequential circuit, is the part of numerous digital systems and is used in construction of control devices. High complexity of integrated circuits (which is increasing, according to the G. Moore's law) and theoretical basis of automatic calculations make possible the implementation of comprehensive algorithms of processing information. However direct realization of algorithms can lead to inefficient using of crystal's resources and extension of project's cost.
Among the enterprises of food industry it is separately needed to distinguish brewing industry that is the source of plenty of wastes, to 80% that is made by a beer pellet.
Disposal of beer grains is a big environmental problem for brewing companies. Currently, hundreds of thousands of tons of this waste have accumulated. Beer pellet is a mixture of plant and microbial proteins, complex carbohydrates, organic acids and other substances. Storage of this waste at landfills leads to the release of toxic substances (products of hydrolysis and decay, indole, skitol and ammonia). Today, beer pellets are used for livestock feed production, but the entire volume of this waste is not used.
Beer grains can be used as adsorbents. Adsorbents are highly dispersed natural or artificial materials with a large specific surface on which the adsorption of substances from gases or liquids in contact with it occurs. Adsorbents are used to purify water from metals and impurities, in gas masks, as catalyst carriers, and in medicine for the absorption of gases and poisons.
The most common adsorbents are active (activated) carbons, which are obtained by thermal destruction of substances containing carbon. Most often, birch is used as raw material. Birch activated carbons (BAU) can be used for sorption processes in the food industry and medicine – this indicates the high quality of these adsorbents. But it should be remembered that birch is a long-restored source of raw materials, not to mention the deterioration of the ecological condition of the regions where these trees are massively cut.
1. Theme urgency
A variety of materials with a high specific surface can act as adsorbents: porous carbon (the most common form is activated carbon), silica gels, zeolites, as well as some other groups of natural minerals and synthetic substances. High-quality adsorbents are obtained by pyrolysis of low-resinous tree species, such as birch, which, of course, is not acceptable both from a social and environmental point of view. Therefore, currently actively developing methods for producing active carbons from alternative raw materials.
The main objective of this work is to develop a method for producing new adsorbents from waste products from the food industry. As such raw materials, beer production waste (beer pellet) can be used.
2. Goal and tasks of the research
Development of an approach to the unification of synthesis Moore FSM, directing on hardware amount reduction in FPGA is the goal of research.
Main tasks of the research:
- To consider the possibility of obtaining adsorbents from an unconventional type of raw material.
- Get samples of adsorbents from plant materials.
- To study the effect of alkaline environment on the process of obtaining activated carbon
- To conclude that it is possible to use the obtained samples instead of traditional activated carbons.
3. Methods for producing adsorbents
The most important raw material for the production of activated carbons is wood (in the form of sawdust), charcoal, peat, peat coke, some bituminous and brown coals, and also semi-coke of brown coals.
Finely chopped wood waste, carbonized in rotary kilns or apparatuses with moving layers. Lump and granular coals, as well as pressed articles of charcoal dust and binder, are activated in shaft and rotary kilns with water vapor or carbon dioxide at 800 °C. During activation, the pore volume, specific surface area of the sorbent increase, the ratio between the volumes of micro-, meso- and macropores changes. The rate of gasification of surface carbon during activation depends on the degree of structural ordering of the carbon material. Carbon is most easily and quickly gasified in disordered areas of the carbon surface. The formed coals prepared with a binder must be thermally treated before activation at a temperature of about 5000° C; in these cases, the binder is partially carbonized. The quality of activated carbon depends on the properties of the starting carbon-containing material and on the mode of activation. A characteristic of the degree of activation of coal is a burn, that is, the percentage of burnt coal in relation to its initial amount. Active charcoals are characterized by a high degree of purity and fine porosity [1].
The number and size of the resulting pores are determined by the nature of the raw materials and the operating parameters of the heat treatment process. The speed of heating the raw materials is important. The total pore volume, as well as the number of large pores (macropores), increase significantly with an increase in the heating rate of raw materials. Slow heating rates are realized in pyrolysis technologies in fixed bed reactors. More productive pyrolysis technologies are based on the use of crushed raw materials and reactors with the so-called fluidized or fluidized bed: small particles of the raw material carried away by the gas stream are as if in a boiling state. The advantage of fluidized bed reactors is a high mass and heat transfer rate, which provides an increased intensity of the pyrolysis process compared to pyrolysis technologies in a fixed bed of raw materials. Pore volume and pore radius distribution can also be controlled by changing the duration of the pyrolysis process. In fluidized bed reactors, the residence time of the particles of ground material in the pyrolysis zone is from tenths of a second to several minutes [2].
Silica gel is also an important adsorbent today. This is one of the very first mineral synthetic sorbents that found wide application in industry. Silica gel has not lost its industrial significance, despite the fact that in recent years adsorption processes have been rapidly developing using unique crystalline sorbents – zeolites.
Technical silica gel is prepared as follows: by reacting a solution of sodium silicate or potassium (water glass) with hydrochloric or sulfuric acid, a gel is obtained which is dried, then broken into pieces, washed with water, dried again, ground, fractionated and calcined until the moisture is completely removed. Commercial silica gel is produced in the form of grains or spherical granules [1].
It should be noted that modern approaches to the study of structural and sorption properties make it possible to predict the correspondence of the structure of porous materials to the problems of their application and theoretically substantiate the patterns of adsorption of various substances.
4. Beer grains
One of the main brewing waste is beer grains. A medium-sized enterprise produces about 35,000 tons of this waste annually. In this case, most of the grains are exported to landfills [1].
The technological process of beer production: after boiling the mash (a mixture of malt and water) in the filter tank, the solid phase is separated from the liquid phase (beer wort). The solid phase is beer grains. Beer pellet from the filter tank is discharged into the buffer tank of the brewhouse. Partial squeezing takes place in it and with the help of a screw it is discharged into storage tanks of 80 m3 and 120 m3. Beer grains are also loaded from the drives by a screw device into trucks and transported from the enterprise [4]
Beer pellet is a brewery waste — thick remaining after cooking and suctioning barley wort. Contains particles of nuclei and shell of grain [4]. There remains beer grains in the process of producing barley wort. The main feature of this secondary brewing product is that it simply contains a huge amount of nutrients and minerals. Therefore, in agriculture, it is used primarily as a source of protein when feeding animals.
In its normal state, beer grains contain about 80% water. It is impossible to store it in this form for more than three days. After a certain time (depending on air temperature), the pellet acidifies and loses its useful properties. Moreover, various kinds of toxins begin to accumulate in it. Therefore, transporting this product over long distances is impractical. In order to avoid acidification and reduce the weight of the pellet intended for transportation, it is pre-dried. In this case, from 3-4 tons of wet mass, 1 ton of dry product is usually obtained. There is also equipment designed for the production of granulated beer pellets [5].
4.1 Chemical composition and properties of beer grains.
There are a lot of useful substances in beer grains. Information on what exactly is part of the dried product and in what quantities can be obtained from the table below (table 1).
Table 1 – Comp osition of beer grains
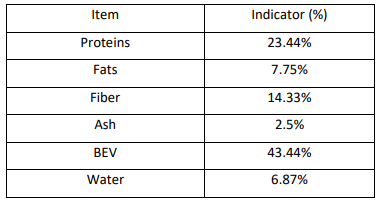
In addition, the composition of beer grains includes such trace elements as:
– zinc – 105 mg/kg;
– iron – 205 mg/kg;
– copper – 15 mg/kg;
– phosphorus – 0.5 mg/kg;
– calcium – 0.37 mg/kg.
grains also contain a very large number of amino acids (glycine, alanine, threonine, etc.) [6].
4.2 Possibility of using beer grains
In agriculture, beer pellets are most often used for fattening pigs, cattle and cattle. Thus, one of the main areas of its use is the production of animal feed. Also, grains are often used as fertilizers in the cultivation of cultivated plants. Another area of the economy in which grains are used is the food industry. Most often it is used for baking flour products for dietary purposes. In this case, it serves as a valuable source of dietary fiber. Sometimes grains are also used as biofuels. Most often in this way it is used by the breweries themselves [6,7].
This study examined the use of beer grains as an adsorbent. A variety of materials with a high specific surface can act as an adsorbent: porous carbon (the most common form is activated carbon), silica gels, zeolites, as well as some other groups of natural minerals and synthetic substances. Highquality adsorbents are obtained by pyrolysis of lowresinous tree species, such as birch, which, of course, is not acceptable both from a social and environmental point of view. Therefore, currently actively developing methods for producing active carbons from alternative raw materials.
The object of the study was dry beer grains. Beer pellet is a dried brewing waste. As a processing method, pyrolysis with an alkali solution was chosen [8,9].
The assessment of the effectiveness of processing beer grains was carried out by histological studies, which make it possible to visually determine the effectiveness of the action of hydrolyzing agents on the components of beer grains at the microstructural level. The preparations were fixed, stained with methylene blue and microscopic at a magnification of x 400.
The results are presented in figure 1
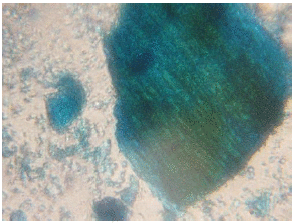
Figure 1 – The microstructure of beer pellets and the microstructure of beer pellets subjected to alkaline hydrolysis (x400)
Table 2 presents data on the adsorption of phenol from an aqueous solution by the beer pellet additive system.
Table 2 – Phenol adsorption pyrolysis products of beer grains with various additives. The initial concentration of phenol in a solution of 1 mg/l.
Efficiency of active coals спектрометрически was studied on the stripe of absorption of phenol in an ultraviolet area.
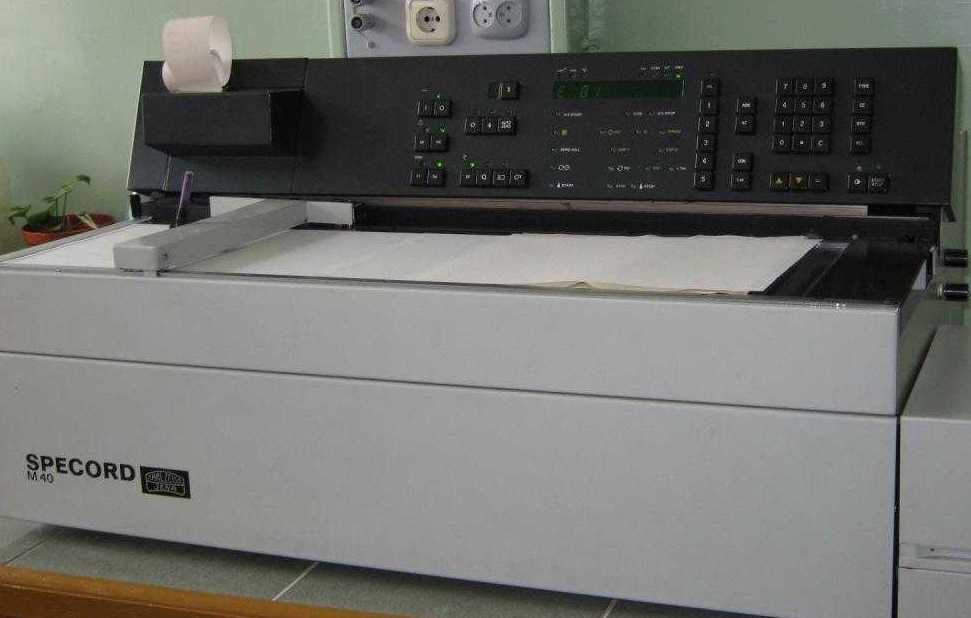
Picture 3 – By the infra-red spectrophotometer of SPECORD 75 IR SPECORD 75 IR
Table 1 – Phenol adsorption pyrolysis products of beer grains with various additives. The initial concentration of phenol in a solution of 1 mg/l.
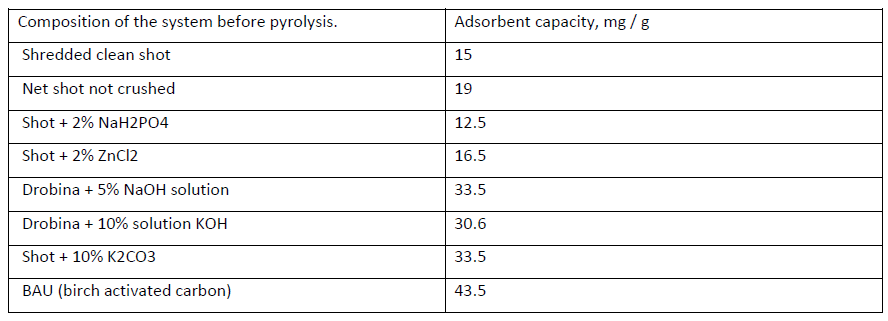
As can be seen, a significant increase in the adsorption capacity of the grains is achieved by processing it before pyrolysis with an alkali solution.
Conclusion
The work is devoted to the urgent task of searching for new adsorbents based on rapidly renewable plant materials.
The work considered:
- Methods of producing an adsorbent.
- studied the chemical composition and property of beer grains.
- Studied beer grains during processing before pyrolysis with an alkali solution. It can be concluded that a significant increase in the adsorption capacity of the grains is achieved.
The production and use of carbon-containing adsorbents based on natural mineral and organic components is advisable, because they can replace existing wood-based adsorbents, which will significantly improve the environment of the region.
This master's work is not completed yet. Final completion: May 2020 The full text of the work and materials on the topic can be obtained from the author or his head after this date.
References
- Гориславец С. П. Пиролиз углеводородного сырья / С. П. Гориславец, Д. Н. Тменов, – Киев: Наукова думка, 1977. – 309 с.
- Мухин В. М. Новые технологии получения активных углей из реактопластов / В. М. Мухин, И. Д. Зубова, В.В. Гурьянов А. А. Курилкин, В. С. Гостев – 2009 – 195с.
- Еремина А. О. Углеродные адсорбенты из гидролизного лигнина для очистки сточных вод от органических примесей / А. О. Еремина, В.В. Головина, Н.В. Чесноков, Б.Н. Кузнецов Journal of Siberian Federal University. Chemistry 1 (2011 4) с.100 – 107
- Прохоров А. М. Пивная дробина // Отоми Пластырь М. : Советская энциклопедия, 1975. (Большая советская энциклопедия : [в 30 т.] / Прохоров А. М. 1969 – 1978, т. 19).
- Главачек Ф. Пивоварение = Pivovarstvi / Ф. Главачек, А. Лхотский; Пер. с чешск. И. В. Холодовой; Под ред. А. П. Колпакчи. М.: Пищевая промышленность, 1977. – 624 с. – 10 500 экз. (в пер.)
- Алексанян И. Ю. Исследование процесса сушки при утилизации отходов спиртового и пивного производств / И. Ю. Алексанян, Ю.А. Максименко // Известия ВУЗов. Пищевая технология. 2004. – №4. – С.59 – 62.
- ТУ 20.15.80-004-00351432-2017 «Солодовая (пивная) дробина «Р». Технические условия»
- Колпакчи А. П. Вторичные материальные ресурсы пивоварения / А. П. Колпакчи., Н. В. Голикова, О. В. Андреева. М.: Агропромиздат, 1986 – 159 с.
- Васильев А. В. Кислотный и ферментативный гидролиз отходов пивоваренной промышленности / А. В. Васильев, В. И. Панфилов, И.В. Шакир, А.В. Афанасьев, М.А. Цыганков // Химическая технология – 2007. – Т. 8 – №1 –17 – 21с.