Abstract
Contents
- Introduction
- 1. Analysis of the state of the automation issue
- 2. Analysis of the drying process as a control object
- 3. Analysis of existing self-propelled guns
- Conclusion
- References
Introduction
Beer pellet is a waste of beer production, which remains after processing barley wort. The largest amount of beer pellets is produced in spring and summer, in the months when there is already a lot of green barley and the sale of pellets is delayed. When sales are delayed, the pellet must be preserved by drying so that this product does not deteriorate. Removing moisture from solid and pasty materials allows you to reduce the cost of transportation, give them the necessary properties, as well as reduce corrosion of equipment and pipelines during storage or subsequent processing of these materials.
Moisture can be removed from materials by mechanical means (wringing, settling, filtering, centrifuging). However, a more complete dehydration is achieved by evaporation of moisture and removal of the generated vapors, i.e., by heat drying.
Drying beer grains, as a rule, does not represent any technical or technological problem. The material has known and stable properties and is perfectly dried in various types of drying plants. Separately, there is the question of adding residual brewer's yeast to the dried grains. Such an additive allows you to increase the level of protein in the finished product, which means the quality and cost of the final product – dry beer grains.
1. MANAGEMENT OBJECT ANALYSIS
Drying is often the final stage of production and is characterized by significant energy intensity. In modern conditions of increasing energy consumption, on the one hand, and a shortage of energy resources, on the other, energy conservation issues are being raised more and more sharply. Despite the established principles of energy saving in technology, there is no unambiguous solution to their implementation, therefore, the problem of energy saving is relevant.
Drying is a thermal process of dehydration of solid materials by evaporation of moisture and removal of the formed vapors. With this substance, heat transfer and diffusion movement of moisture occurs. The productivity of the drying process is determined by the time interval necessary to reduce the moisture content of the material from the initial to the final value.
Drying beer grains, as a rule, does not represent any technical or technological problem. The material has known and stable properties and is perfectly dried in various types of drying plants. Separately, there is the question of adding residual brewer's yeast to the dried grains. Such an additive allows you to increase the level of protein in the finished product, which means the quality and cost of the final product - dry beer grains. At the same time, residual brewer's yeast has a relatively high relative humidity, and also contains a large number of living yeast cells.
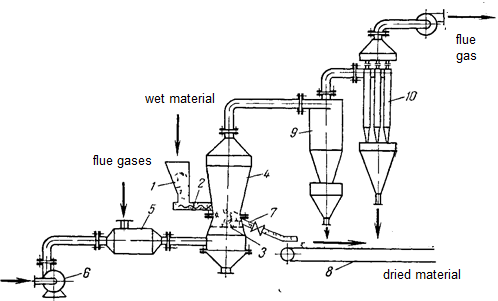
Figure 1 – One-dimensional fluidized bed dryer
2. Formalization of the control object
When developing an automated control system for drying a fluidized bed furnace, the most important stage in the synthesis of the system is the analysis of the process as a control object, that is, the determination of input and output variables, finding mathematical dependencies between input and output variables describing the behavior of the control object.
At low speeds, the bulk layer, the filter layer itself and its volume does not change, it remains stationary. With an increase in the flow rate of oxygen-enriched air, the layer resistance increases due to the friction of the gas mixture on the surface of the feed and when gas jets pass through channels of various cross sections formed between the particles of the concentrate. Upon reaching a certain gas flow rate, called minimally critical, the bulk layer of the concentrate changes qualitatively and volumetricly and goes into a fluidized state, acquires the properties of the liquid listed above. [ 4 ]
Thus, for the drying process in the KS furnace, we can distinguish input material variables whose properties change in this process.
For this process, these features are:
- Fbv, Mbv - wet bard;
- Fpv – primary air consumption;
- Fвв – secondary air consumption;
- Fpg – natural gas consumption;
- MBS – dry bard;
- Fog – off-gas.
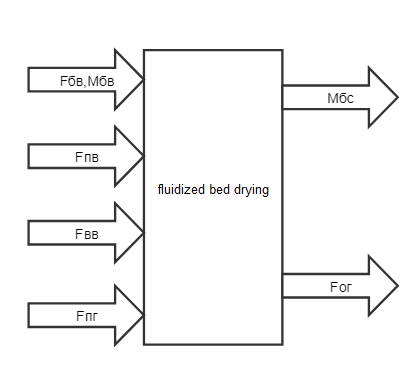
Figure 2 – Scheme of material flows and information variables
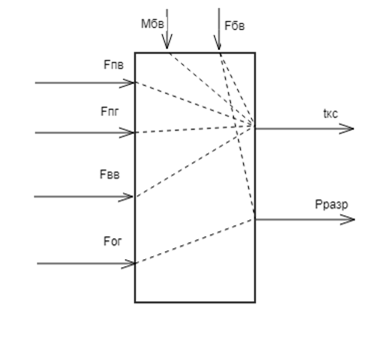
Figure 3 – Block diagram of the control object
Of the many factors affecting the temperature of the fluidized bed, we can distinguish the gas supply to the furnace. Gas flow rate is the control action. The main perturbations of the process are changes in the bard flow rate, its initial humidity and initial temperature.
2. Analysis of existing self-propelled guns
Currently, two methods are used to control the temperature of the layer: by changing the supply of wet material and by changing the flow rate of the drying agent.
When using the first method, the productivity of the dryer will automatically increase (in the case of a decrease in the initial moisture content of the material). However, in this case, an intermediate hopper should be placed between the dryer and the previous technological apparatus, which is undesirable, and often simply unacceptable. The automatic control circuit of the operation of such a dryer includes units for regulating the ratio of fuel to primary air consumption, temperature of the drying agent at the inlet of the dryer, drying agent consumption, fluidized bed temperature, fluidized bed level and vacuum in the dryer.
When using the second method of regulating the temperature of the layer, the regulating effect is introduced by changing the fuel consumption, the temperature of the drying agent at the inlet to the dryer is controlled by changing the flow of secondary air.
Thus, the existing system has several disadvantages, namely:
- not high enough quality of the finished product;
- slightly higher specific heat consumption;
- large inertia of the system, i.e. low accuracy.
Conclusion
In this section, the synthesis of self-propelled guns with a fluidized bed dryer type SKS-B is performed. It is shown that the implementation of the required control and data management functions allows you to get the necessary quality indicators, it is possible only when using the dual-circuit structure of the developed self-propelled guns. Mathematical models of fluidized bed temperature control elements are obtained. Based on the models of ACS elements, PI controllers of the internal and external ACS circuits were selected and configured.
The obtained parameters of the regulators and the double-circuit structure of self-propelled guns provide the necessary quality indicators for controlling the temperature of the fluidized bed, which is confirmed by the obtained simulation results.
References
- Bespalov A. V., Kharitonov N. And. Chemical process control systems. Textbook for universities. – M.: Academic book, 2007 – C. 690.
- Bespalov A. V., Kharitonov N. And. Task book on chemical process control systems. Textbook for universities. – M.: Academic book, 2007 – C. 690.
- Dorf R., Bishop R. Modern management systems. – M .: Laboratory of Basic Knowledge. – 2002 – C. 832.
- Lucas B. A. Theory of control of technical systems. Training course for universities. Yekaterinburg: Publishing House of the UGGGA, 2002. – C. 675.
- Phillips Ch., Harbor & nbsp; R. Feedback management systems. – M .: Laboratory of Basic Knowledge, 2001 – C. 616.
- Denisenko V. PID – regulators: principles of construction and modification. Article, C. 8