Зміст
- Вступ
- 1. Мета і завдання дослідження
- 2. Огляд досліджень і розробок
- 2.1 Огляд міжнародних джерел
- 2.2 Огляд національних джерел
- 3. Синтез системи автоматичного регулювання натягу сталевої штаби
- 3.1 Розробка математичної моделі об'єкта управління
- 3.2 Розробка структурної схеми електропривода моталки
- 3.3 Аналіз динаміки САР натягу сталевої штаби
- Висновок
- Перелік джерел
Вступ
Реверсивний стан холодної прокатки – це прокатна кліть, обжимаються смугу в валках тиском на неї, створюваним нажімнимі пристроями, і її натягом, створюваним розмотувати моталкой (до кліті) і намотують моталкой (після кліті) при заданій швидкості обертання валків. Реверс валків кліті і моталок дозволяє повторювати обтиснення чергуванням напрямку прокатки. Регулювання товщини можливо, як впливом на тиск, так і впливом на натяг смуги. Виходячи з жорстких вимог до забезпечення режимів роботи в реверсивних станах, що мають високі швидкості прокатки, жорсткі технічні вимоги, а також вимоги до якості підсумкового матеріалу, потрібно вести безперервний контроль за протіканням процесів прокату металу і розробку більш сучасних рішень для задоволення умов режиму роботи. Застосування класичних схем управління не завжди задовольняє вимоги до прокату, це повʼязано з не завжди точним настроюванням регуляторів, високою складністю обʼєкта регулювання, збільшенням контурів регулювання, які ведуть до погіршення показників завадостійкості і швидкодії, неможливістю автоматичної перенастроювання регуляторів при зміні режимів роботи. Виникнення пружних деформацій в кліті тягне за собою зміну тиску металу на валки, а, отже, і впливає на величину зазору між ними, що і призводить до появи поздовжньої різнотовщинності листа. В даний час вимоги до точності прокатки складають не більше ± (0,025–0,05) мм від необхідної товщини смуги. Таким чином, проблема забезпечення заданої товщини смуги є досить актуальною.
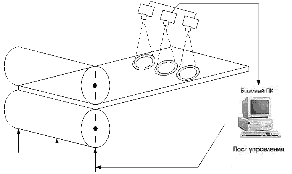
Зображення процесу прокатки робочого тіла
(Анімована картинка, кількість циклів – 6, кількість кадрів – 5, розмір – 9.2 КБ)
1. Мета і обʼєкт дослідження розробки
Мета розробки – стабілізація реверсивної прокатки за рахунок САУ компенсує флуктуацій натягу робочого тіла на вході і виході з кліті.
Обʼєкт розробки – система автоматичного регулювання натягу сталевої штаби в умовах одноклетьевим реверсивного стану холодної прокатки.
2. Огляд міжнародних джерел
Виникнення пружних деформацій в кліті тягне за собою зміну тиску металу на валки, а, отже, і впливає на величину зазору між ними, що і призводить до появи поздовжньої різнотовщинності листа. В даний час вимоги до точності прокатки складають не більше ± (0,025–0,05) мм від необхідної товщини смуги. Таким чином, проблема забезпечення заданої товщини смуги є досить актуальною.
2.1 Огляд досліджень і розробок
Розглянемо існуючий спосіб регулювання натягу смуги (рис.2.1).
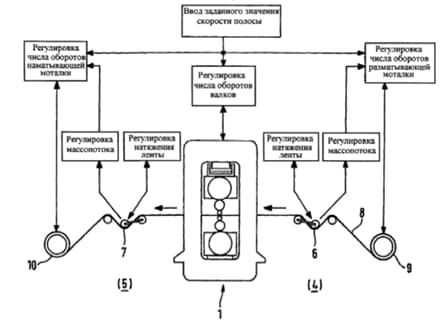
Рисунок 2.1 – Схема регулювання натягу смуги і масспотоков за допомогою рухливих роликів
В даному способі запропонований прокатний стан для холодної прокатки металевої смуги, зокрема зі сталі, з прокатної кліттю і засобами для установки зазору між валками. Також представлені моталки для розмотування і змотування смуги розташовані до і після прокатної кліті відповідно, відрізняються тим, що між моталкой для розмотування смуги і прокатної кліттю розташований накопичувач смуги для регулювання натягу смуги в процесі прокатки з постійно змінюється по заздалегідь заданим профілем товщини смуги, при цьому накопичувач виконаний у вигляді рухомого ролика, встановленого з можливістю регулювання його положення регулятором зусилля його приводного пристрою з урахуванням заданого значення зусилля отримується виходячи з вимірюваного на рухомому ролику дійсного значення його кутового зміщення і заздалегідь заданого значення натяжна смуги, а також додатково з урахуванням заданого профілю зміни товщини смуги.
Виходячи з вище перерахованого можна запропонувати, щоб між моталкой розташованої перед окремою прокатної кліттю для холодної прокатки і самої окремої прокатної кліттю знаходився накопичувач смуги, призначений для регулювання массопотоков і регулювання натягу в процесі прокатки.
За рахунок накопичувача смуги, розташованого по напрямку руху смуги перед окремою прокатної кліттю, компенсується зміни массопотоков або зміни швидкості руху смуги, викликані змінами товщини смуги або профілю товщини тобто форми кривої зміни товщини смуги.
Таким чином, існуюча система має ряд недоліків, а саме:
- недостатньо висока якість продукту;
- невідповідність швидкостей моталок на вході і виході з кліті;
- велика інерційність системи, тобто низька точність і надійність управління процесом прокатки;
- тривале проведення процесу прокатки смуги.
2.2 Огляд національних джерел
Коли положення Sʼ поршня 6 змінюється як показано на рис.2.2, для регулювання товщини прокату в прокатному стані, натяг, прикладена на робоче тіло, на вхідний і вихідний сторонах починають флуктуировать.
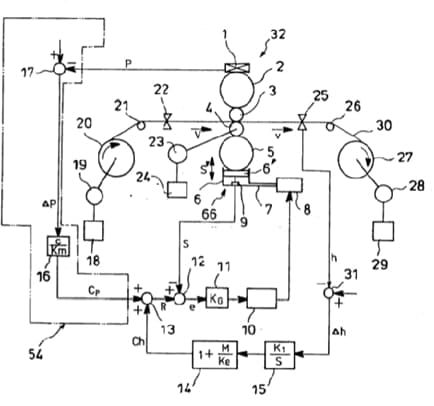
Рисунок 2.2 – Загальний пристрій класичної САРТ реверсивного прокатного стану
Якщо зазор між робочими валками зменшується, що призводить до зменшення товщини прокату, робоче тіло почне збільшуватися й натяг на вхідний і вихідний сторонах буде зменшуватися. Такі флуктуації натяжений може бути поглинена за рахунок зміни швидкостей моталок, але вони мають велику інерцію і таке поглинання дещо повільніше ніж використання регулювання зазору між робочими валками за допомогою гідронажімной системи. Результатом зниження натяжений на вхідний і вихідний частинах є збільшення деформаційного опору робочого тіла, що зводить нанівець зменшення зазору між робочими валками, тобто, товщина прокату не зменшується. Іншими словами, зменшуючи товщину робочого тіла за допомогою високошвидкісної гідронажімной системи, вона не може зменшуватися швидше, ніж зміна швидкості моталок.
3. Синтез системи автоматичного регулювання натягу сталевої штаби
У розділі синтезу в якості обʼєкта управління необхідно розглянути регулятор натягу робочого тіла в проміжках між моталкой і реверсивної кліттю. Так як саме він повинен компенсувати флуктуації натягу сталевої штаби, що виникають із-за варіацій товщини робочого тіла, які викликають дисбаланс швидкості прокатки ΔV на вхідний і вихідний сторонах стану.
3.1 Розробка математичної моделі обʼєкта управління
При розробці концепції побудови системи (рис.2.1) було виявлено, що регулятор натягу, служить для того, щоб змінити модуль Юнга робочого тіла, тому він відхиляє резонансну частоту wn, що викликається інерційністю моталки і коефіцієнтом пружності (модулем Юнга) робочого тіла в область, де вони не впливають на систему регулювання. Ще раз повторимо структурну схему регулятора натягу (рис.3.1).
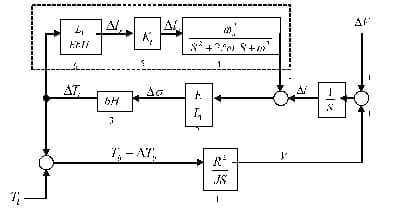
Рисунок 3.1 – Структурна модель робочого тіла в МК-проміжку
Отримаємо аналітичну модель обʼєкта управління по структурній схемі регулятора натягу (рис.3.1). Дана модель відображає залежність зміни натягу робочого тіла в поздовжньому напрямку від можливої зміни швидкості прокатки. За структурою рис.3.1, не враховуючи поки динаміку регулятора натягу, запишемо вираз в термінах перетворення Лапласа для зміни натягу:
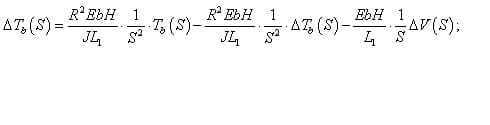
де E – модуль Юнга робочого тіла; b – ширина робочого тіла; H – товщина робочого тіла; L 1 – відстань між робочою кліттю і моталкой; J – момент інерції моталки разом з котушкою; R – радіус котушки; S – оператор Лапласа; ΔV – зміна швидкості прокатки; ΔT b – зворотне зміна натягу.


Висловлюючи ΔT b (S) отримаємо рішення в операторної формі для зміни натягу між моталкой і кліттю щодо необхідного завдання ΔT b(S) і обурює впливу від швидкості прокатки ΔV(S):

Таким чином, передавальна функція обʼєкта по каналу обурення зміна натягу робочого тіла – зміна швидкості робочого тіла має вигляд:
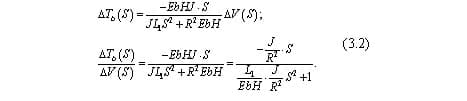
З виразу (3.2) випливає, що динаміка по обуренню носить коливальний характер. З метою отримання виразу для власної частоти коливань обʼєкта, перепишемо (3.2) наступним чином, з огляду на, що частота є зворотна величина постійної часу, тоді:
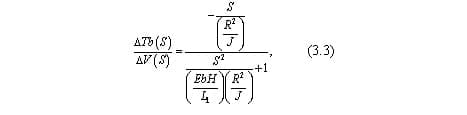
Звідси отримаємо власну частоту коливань, пам'ятаючи про те, що при квадраті оператора Лапласа варто значення постійної часу також в квадраті:
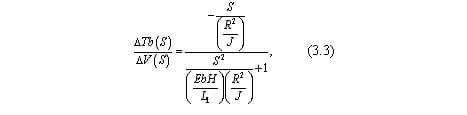
З (3.4) випливає, що власна частота коливань визначається конструкційними параметрами і може бути обчислена. Міркуючи аналогічним чином, отримаємо передавальну функцію системи з блоками всередині області, зазначеної пунктирною лінією (тобто з урахуванням системи регулювання):
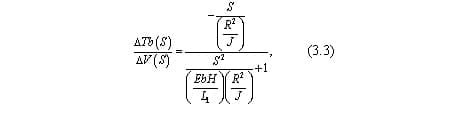
Тоді аналогічно, з виразу (3.4) отримаємо вираз для резонансної частоти:

де
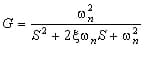
динамічна характеристика регулятора натягу. З (3.5) випливає, що правильно підібране значення коефіцієнта посилення регулятора натягу Kt (S) може усунути явище залежності натягу від резонансу моталки. Тоді товщина прокату не буде змінюватися, навіть якщо зазор між робочими валками змінюється з великою частотою, як це виходить у традиційних відомих системах регулювання.
Доведемо спроможність моделі методами математичного моделювання. При моделюванні об'єкта значення конструктивно-технологічних параметрів наступні:
- b – ширина робочого тіла 1800 мм;
- H – товщина робочого тіла на вході 0,52 мм, на виході 0,3 мм;
- L1 – відстань між робочою кліттю і моталкой 0,5 мм;
- J – момент інерції моталки разом з котушкою, 500 кг м2;
- R – радіус котушки, 0,25;
- V – швидкість прокатки, 20 ... 30 м / с;
- Tb – натяг робочого тіла, 1020 Кгс = 10000 Н.
Чисельне значення власної частоти коливань визначимо за формулою
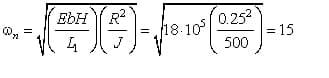
Аналіз динаміки обʼєкта, а відповідно і спроможності моделі будемо проводити в результаті моделювання схеми наведеної на рис.3.2. На схемі швидкість прокатки, тобто швидкість робочого тіла задається ступінчастим набросом з можливим її зміною в момент часу 5 с.
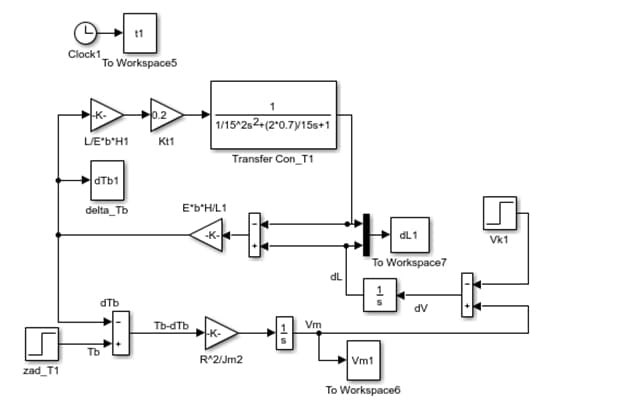
Рисунок 3.2 – Схема моделювання регулятора натягу
Швидкість моталки V m обурюється зміною швидкості ΔV робочого тіла через можливої зміни натягу на вхідний і вихідний сторонах стану і / або через варіацій товщини робочого тіла, які викликають дисбаланс швидкості через суматор . Перехідні процеси швидкості моталки при різних значеннях коефіцієнта посилення регулятора натягу Kt наведені на рис.3.3. З графіків видно, що коефіцієнт Kt варіюється в межах від 0,2 до 1, змінюючи перехідні процеси швидкості моталки від коливального до апериодического.
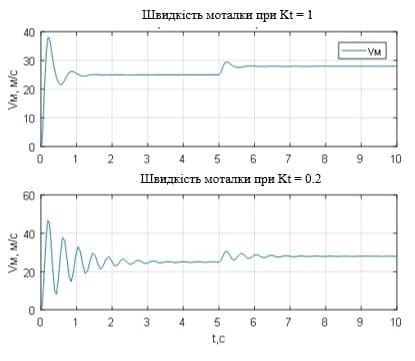
Рисунок 3.3 – Перехідні характеристики швидкості моталки при різних значеннях коефіцієнта регулятора натягу
Значення ΔV інтегрується в різницю подовжень Δl в поздовжньому напрямку робочого тіла, перехідні характеристики яких наведені на рис.3.4. З метою докази працездатності концепції управління, на рис.3.4. спеціально наведені перехідні процеси подовжень робочого тіла без регулятора натягу і з регулятором при різних значеннях його коефіцієнта посилення. Без регулятора натягу перехідний процес подовжень, а відповідно і зміни натягу робочого тіла (рис.3.5) носить коливальний характер, що свідчить про великий інерційності моталки, яка управляється відхиленням натягу від необхідного значення ΔTb так, щоб компенсувати вплив ΔV. І відбувається ця компенсація дуже повільно (рис.3.4 і 3.5 червоним кольором ).
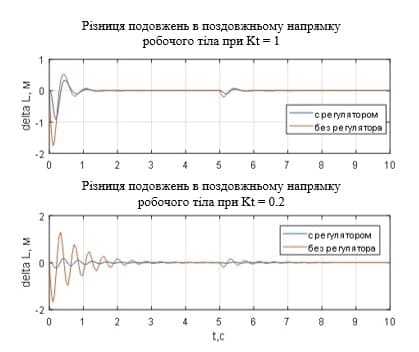
Рисунок 3.4 – Перехідні характеристики різниці подовжень робочого тіла при різних значеннях коефіцієнта регулятора натягу
Зміна натягу ΔT b конвертується в зміна подовження Δlr (рис.3.2). Отримане значення посилюється в Kt раз для отримання величини Δlc, за допомогою якої і відбувається регулювання натягу. Таким чином, перехідний процес відбувається набагато швидше, так як на нього не впливає інерційність моталки (рис.3.4 і 3.5 синім кольором).
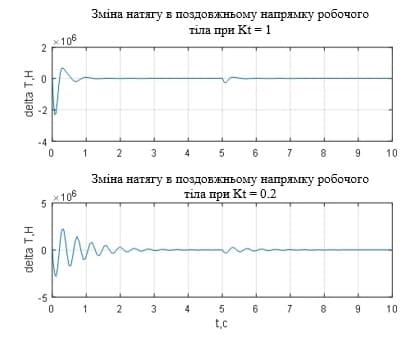
Рисунок 3.5 – Перехідні процеси зміни натягу робочого тіла при різних значеннях коефіцієнта регулятора натягу
Таким чином, перехідні характеристики, наведені на рис. 3.3 – рис.3.5 адекватно доводять працездатність методу регулювання натягу робочого тіла між моталкой і кліттю реверсивної прокатки. Підбір коефіцієнта посилення Kt дозволяє компенсувати флуктуації натягу робочого тіла, що виникають з обʼєктивних причин. Фактично регулятор натягу, служить для того, щоб змінити модуль пружності Юнга робочого тіла, відхиляючи резонансну частоту wn, що викликається інерційністю моталки в область, де вона не впливають на систему регулювання.
Отже в даному підрозділі докладно був описаний об'єкт управління, яким є контур регулювання натягу. Для повної структури системи регулювання натягу необхідно додати модель електроприводу моталки, що забезпечує заданий натяг робочого тіла в проміжку між моталкой і кліттю. Дана модель буде розглянута в наступному підрозділі.
3.2 Розробка структурної схеми електропривода моталки
Для вирішення завдання розглянемо загальний принцип регулювання натягу [2-4]. Момент двигуна r необхідний для створення натягу T на котушці моталки з радіусом R, дорівнює:

З іншого боку, вихідний момент двигуна моталок дорівнює:

З (3.6) та (3.7), отримаємо:
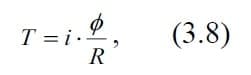
де i – струм двигуна, Φ – поле магнітної індукції двигуна. Якщо регулювання влаштовано так, що радіус котушки R стає пропорційний полю магнітної індукції Φ, то Φ/R приймає постійне значення і натяг T стає пропорційно току двигуна i.
При розробці математичної моделі уніфікованого електроприводу (ЕПП) постійного струму, необхідно врахувати, що структура його управління триконтурна з принципом підлеглого регулювання [5-10]. Це означає, що зовнішнім контуром є контур регулювання натягу, який встановлює завдання на внутрішній контур – регулятор швидкості обертання двигуна моталки, який, в свою чергу коригує і обмежує завдання на контур регулятора струму якоря двигуна моталки. Такі структури підлеглого регулювання реалізовані в стандартних уніфікованих ЕПУ.
Математичну модель трехконтурной САУ електроприводом моталки можна представити у вигляді системи інтегро-диференціальних рівнянь (3.9):
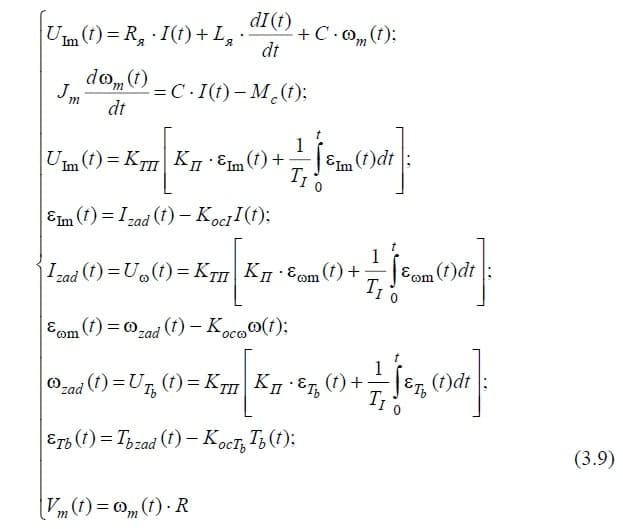
Тут відомими функціями часу є: UIm(t) – керуючий вплив (ЕРС джерела живлення електродвигуна) (B), регульоване по ПІ – закону управління [5– 10]; Uw(t), U T b (t) – керуючі впливу для контурів керування швидкості обертання моталки і натягу робочого тіла, відповідно, регульовані по ПІ – закону управління [5-10].
M c(t) – рівноваги вплив (момент власної навантаження електроприводу, тобто опір деформації робочого тіла у вогнищі деформації, наведене до ротора двигуна) (H * m).
Відомими також є параметри системи:
- C – постійна машини (B * c); C e=Cn=C – (Двигун з постійним магнітним потоком і компенсацією магнітного потоку якоря);
- Rя – активний опір силових ланцюгів ТП – Д (Ом);
- Lя – індуктивність силових ланцюгів ТП – Д (Гн);
- Jm – момент інерції моталки, наведений до ротора електродвигуна (кг * м2);
- R – радіус моталки;
Невідомими в цій системі є: w – швидкість обертання двигуна (рад/с); I – ток якоря (A), відповідний електромагнітного моменту MЕМ=C * I, (H * m); T b – натяг моталки (H).
На рис. 3.6 приведена схема моделювання САУ ЕПУ моталки, заснована на системі інтегродиференціальних рівнянь (3.9).
Параметри уніфікованого ЕПУ, які необхідні для розрахунку коефіцієнтів передачі та сталих часу двигуна наступні:
- номінальна потужність 67 КВт;
- номинальная частота вращения 1500 об/мин;
- номинальное напряжение 600 В;
- номинальный вращающий момент 426,5 Нм;
- номинальный ток якоря 117,5 А;
- индуктивность силовых цепей ТП–Д 0,001 Гн;
- активное сопротивление силовых цепей ТП–Д 0,01 Ом.
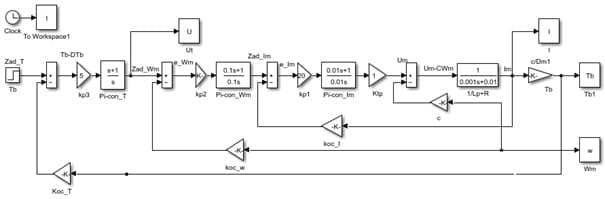
Рисунок 3.6 – Схема моделювання ЕПУ моталки
3.3 Аналіз динаміки САР натягу сталевої штаби
Аналіз динамічних процесів в системі автоматичного регулювання натягу робочого тіла між моталкой і реверсивної кліттю будемо проводити в результаті моделірівованія повної схеми, що включає модель ЕПП моталки і регулятора натягу. Дана схема моделювання наведена на рис. 3.7.
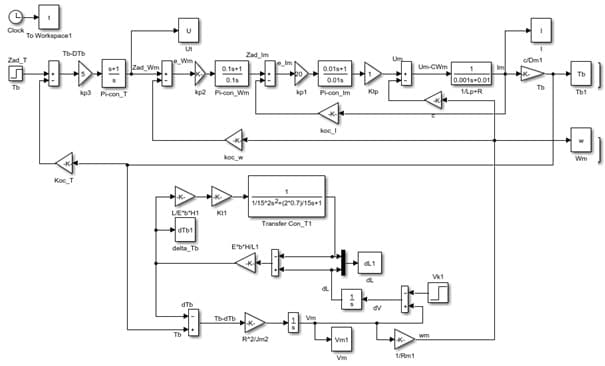
Рисунок 3.7 – Схема моделювання САР натягу сталевої штаби
Проаналізуємо перехідні процеси в САР. На рис.3.8 наведені перехідні процеси ЕПУ моталки при коефіцієнті посилення регулятора натягу, рівного 0,1.
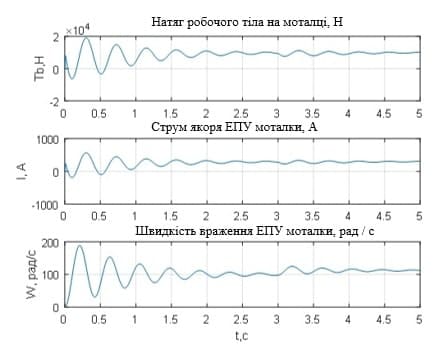
Рисунок 3.8 – Перехідні процеси в системі ЕПП моталки при коефіцієнті регулятора натягу Kt=0.1
З графіків видно, що процеси по основним регульованим змінним носять коливальний характер і до моменту зміни швидкості прокатки в 3 з не встановлюються. Швидкість моталки також має динаміку коливань (рис.3.9). Зміни натягу, викликані обуренням швидкості прокатки, свідчать про те, що моталка не справляється з компенсацією зміни швидкості прокатки навіть з 25 м/с до 28 м/с (рис.3.10) в силу своєї великої інерційності.
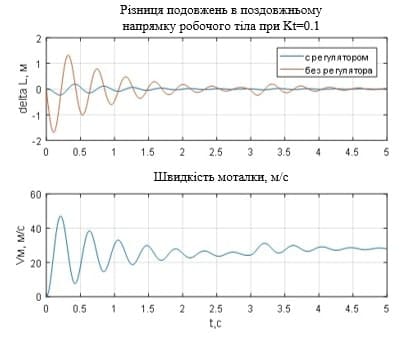
Рисунок 3.9 – Перехідні процеси зміни натягу робочого тіла при Kt=0.1
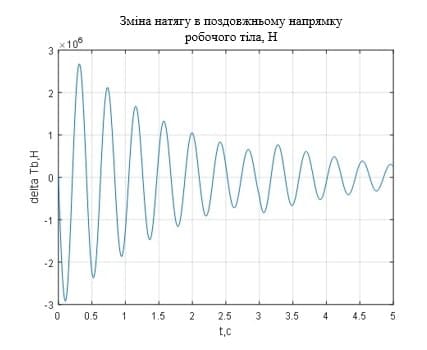
Рисунок 3.10 – Перехідні процеси зміни натягу робочого тіла при Kt=1
З метою можливості швидкої компенсації виникаючих флуктуацій натяжений сталевої штаби, скорегуємо коефіцієнт регулятора моталки Kt, який навіть при наявності інерції моталки забезпечить хороший результат, за рахунок відхилення резонансної частоти wn, що викликається інерційністю моталки в область, де вона не впливають на систему регулювання.
Перехідні процеси за основними регульованим змінним ЕПУ мають апериодический характер (рис.3.11), час регулювання 0,8 с, що є хорошим показником для об'єктів даного класу [10]. Відпрацювання зміни швидкості прокатки відбувається за 0,25 с.
Перехідні процеси подовження і зміни натягу робочого тіла уздовж осі прокатки свідчать про те, що флуктуації натягу смуги при зміні швидкості прокатки компенсуються протягом 0,5 с (рис.3.12, рис.3.13).
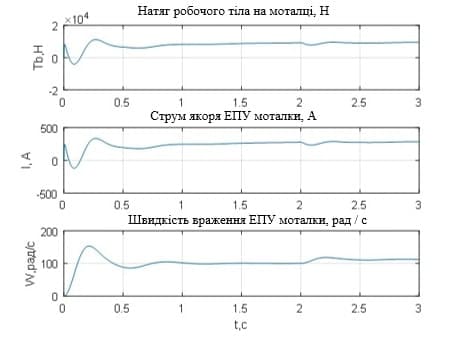
Рисунок 3.11 – Перехідні процеси в системі ЕПУ моталки при коефіцієнті регулятора натягу при Kt=1
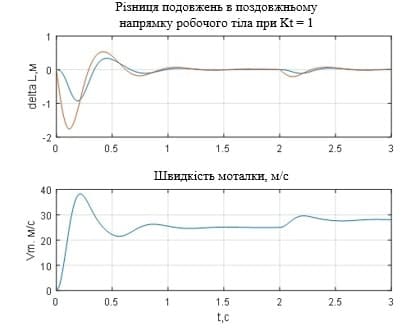
Рисунок 3.12 – Перехідні процеси в системі ЕПУ моталки при коефіцієнті регулятора натягу при Kt=1
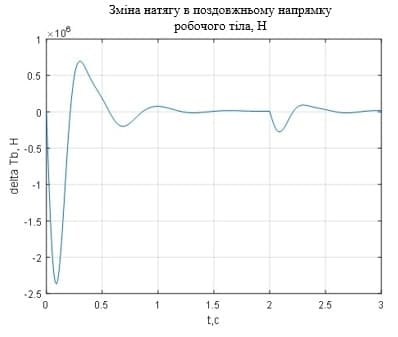
Рисунок 3.13 – Перехідні процеси зміни натягу робочого тіла при Kt=1
Таким чином, аналіз динамічних процесів в САР натягу сталевої штаби довів працездатність запропонованої концепції управління. Практика дослідження і моделювання схеми рис. 3.7 показала, що чисельне значення коефіцієнта посилення регулятора натягу в даних технологічних умовах реверсивної прокатки, що дає задовільні результати за швидкодією САР лежить в межах від 0,5 до 1 од.
Перелік джерел
- Дружинин Н.Н. Непрерывные станы, как объект автоматизации. — М.: Металлургия, 1975. — 336 с.
- Выдрин В.Н., Федосиенко А.С. Автоматизация прокатного производства. — М.: Металлургия, 1984 — 472 с.
- Кузнецов Б.И., И.О. Опришко, И.М. Богаенко и др. Автоматизация управления листовыми прокатными станами. — К.: Техника, 1992. — 231 с.
- Гудвин Г.К., Гребе С.Ф., Сальгадо М.Э., Проектирование систем управления, 2004г — 962 с.
- Афанасьев В.С. Автоматизированный электропривод в прокатном производстве: Уч. для вузов. — М.: Металлургия, 1977. — 280 с.
- Комплектные тиристорные электроприводы: Справочник /Под. ред. В.М. Перельмутера. — М.: Энергоатомиздат, 1988. — 319 с.
- Перельмутер В.М., Сидоренко В.А. Системы управления тиристорным электроприводом постоянного тока. М.: Энергоатомиздат, 1988.
- Башарин А.В., Новиков В.А., Соколовский Г.Г. Управление электроприводами: Учебное пособие для вузов. — Л.: Энергоатомиздат. Ленинградское отделение, 1982. — 392 с.
- Ключев В.И. Теория электропривода: Учебное пособие для вузов., 2—е изд. перераб. и доп. — Л.: Энергоатомиздат, 1998. — 704 с.
- Дралюк Б.Н., Конторович Б.И., Маланов А.Л.// Электропривод и автоматизация мощных машин: Сб. науч. тр. — Свердловск: НИИтяжмаш, 1991г. С.81—96.
- Дралюк Б.Н., Конторович Б.И., Маланов А.Л.// Внедрение микропроцессорной САРТ на реверсивном стане холодной прокатки. Изд. "Металлургия", "Сталь" N 5, 1996, с.33—36.
- 7. Тиристорные электропривода прокатных станов /В.М. Перельмутер, Ю.Н. Брауде, Д.Я. Перчик, В.М. Книгин /Под ред. В.М. Перельмутера. – М.: Металлургия, 1978. — 151 с.