Abstract
When writing this essay, the master's work is not completed. Final completion of work – June 2021. The full text of the work and materials on the topic can be obtained from the author or his manager after that date.
Contents
- Introduction
- 1. Relevance of the topic
- 2. The purpose and objectives of the study
- 3. Review of research and development conclusions
- Conclusion
- List of sources
Introduction
Gas turbine engines occupy a monopoly position as engines of modern aircraft and helicopters. The main development trend in aircraft and engine building is an increase in the specific parameters of the working process, loads on parts, and an increase in their operating temperatures. As a result, the design of the engine becomes more complex, making it difficult to maintain a high level of reliability.
Expansion of the range of application of gas turbine engines in terms of operating conditions (temperature, climatic conditions, the presence of dust, etc.) necessitates finishing and hardening works. Although these problems are inherent in all types of aircraft engines to varying degrees, they are most acute for helicopter engines.
A modern aircraft gas turbine engine is a complex engineering design. Teams from various branches of science and technology made a huge contribution to its creation. In the design and manufacture of engines, the latest advances in metallurgy, metal processing technology, electronics and other areas are used. Therefore, the production of gas turbine engines is considered science intensive. It is worth considering the high cost and long production time of a new engine, in connection with which the tasks of increasing the engine resource and increasing its reliability are put to the fore [1].
Since a wide range of irreversible physical and chemical changes (accumulation of fatigue damage, wear, aging, etc.) occurs during engine operation, the state and properties of parts and assemblies are irreversibly changed. As a result, there comes a moment when these changes lead to failures, complete loss of performance, which will violate flight safety [2].
The reliability and durability of gas turbine engines (GTE) is largely determined by the most critical and loaded parts – compressor and turbine blades, the geometric shape of which undergoes significant changes during operation.
1. Relevance of the topic
The service life and reliability of modern aircraft engines directly depends on the operational endurance of the turbocharger blades, which are massive parts. The blades of gas turbine engines are parts with a complex geometric spatial shape. During operation, they are affected by a number of negative factors, which inevitably leads to intensive wear and a short, compared to other engine parts, resource.
The durability of compressor and turbine blades is largely determined by their thermal state and the level of existing loads and stresses. When changing the engine operating modes, speed and altitude of the helicopter flight, the conditions of thermal and mechanical loading of the blades change significantly.
The master's work is devoted to an urgent scientific task – the development of a new approach to the synthesis of the technological process of applying special coatings to the blades of a turbocharger, aimed at increasing their operational resistance.
Measures aimed at increasing the hardness of the surface layer of blades, for example, chrome plating, carburizing, etc., did not lead to a significant level of resistance to erosive wear. The reason was the formation of a brittle solid surface layer and the presence of microcracks in it, followed by spalling of solid dust particles upon impact [3]. Along with this, the creation of special coatings makes it possible to increase the wear resistance by about 2-3 times.
2. The purpose and objectives of the study
The aim of the study is to improve the quality of the turbocharger blades of a gas turbine engine due to finishing and hardening treatment by applying special coatings.
The main objectives of the study:
- Explore the current state of the art.
- To develop general principles of applying special coatings for turbocharger blades of a gas-turbine engine.
- To synthesize the structure of the technological process of applying special coatings.
- Synthesis of technological equipment for the application of special coatings for the blades of a GTE turbocompressor.
- Develop recommendations for improving the quality of GTE turbocharger blades by applying special coatings.
Research object: the structure of the technological process of hardening treatment of blades of a turbocharger of a gas-turbine engine by applying special coatings
Research subject: relationships and patterns between the operations of the technological process of applying special coatings of turbocharger blades of a gas-turbine engine.
3. Review of research and development conclusions
During the operation of gas turbine engines, individual units and parts change their properties and the output parameters of the engine change accordingly. These changes are manifested in natural wear of the blades, loss of their original shape and changes in the physical and mechanical properties of the material, accumulation of damage, etc. [4]. In this regard, the reliability of the engine, incorporated in the design and production, changes during operation. Over time, the damageability of the blades and the reliability determined by them reaches such values that a sharp decrease in flight safety becomes possible.
Under the influence of design, production and operational factors, the state of the turbine and compressor blades changes, as well as the parameters of the engine's working process. All faults are usually divided into two groups: damage – violation of serviceability of the object or its component parts; failures – violation of the object's performance. To understand the physical essence of the occurrence of failures, it is convenient to present the GTE operation in the form of three periods, characterized by a certain type of change in the failure rate (Im. 1).
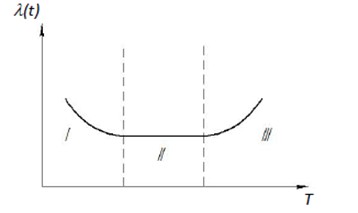
Image 1 – Failure rate function graph
The failure rate can be divided into three groups: failures occurring in the initial period of the arrival of products for operation (break-in failures); sudden or random failures characteristic of the entire period of operation; failures that are caused by a change in the strength and geometric parameters of products due to a long time of operation of products (gradual failures).
The reasons that lead to the decommissioning of the engine[5]:
- Destruction of compressor blades – 35%;
- Destruction of turbine blades – 30%;
- Engine surge – 15%;
- Ingress of foreign objects – 10%;
- Gas temperature overshoot – 10%.
The service life of the blades for civil aviation engines is within 10,000 ... 20,000 hours, and for military aviation – 500 ... 1000 hours. It should be noted that the blades of a turbocharger operate at high gas temperatures reaching 1200 ° C for turbines, for a compressor – 600 ° C[6].
As a result of operation, the turbine and compressor blades are affected by many factors due to the peculiarities of the influence of the environment in which the engine is operated (ingress of foreign objects, corrosion, fretting corrosion, icing, erosion, wear, etc.) [7,8]. In the course of work on the analysis of blade damage and identification of factors that have a negative impact on engine performance, the most common damage to GTE blades was identified, shown in image 2.
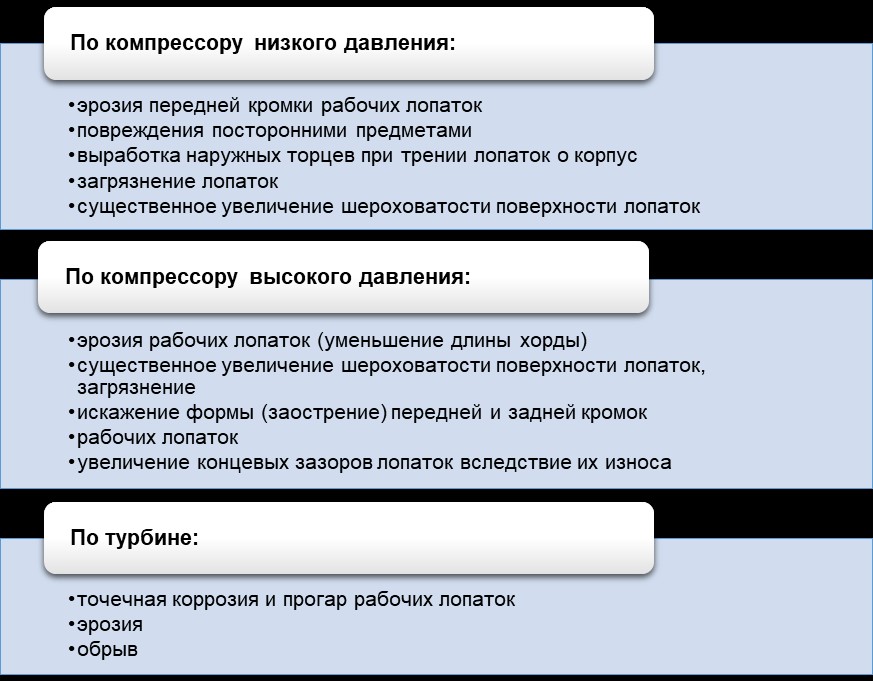
Image 2 – Typical damage to compressor and turbine blades
In the production of blades, high-strength, heat-resistant steels and alloys are widely used, which have large ultimate strength, endurance and corrosion resistance. However, a typical defect for these materials is microstructural irregularity, which results in zones with poor mechanical properties.
Unfortunately, the strength of structures is significantly less than the strength of the materials from which the structures are made. The reasons for this phenomenon are the presence of residual stresses in the blades, anisotropy of properties, changes in material properties as a result of operation.
The loads experienced by individual engine parts can be divided into two groups: deterministic and stochastatic.
The first group includes loads from aerodynamic forces on the blades under steady-state engine operation, from centrifugal forces of rotating parts. The second group of loads is random. These include the loads on the compressor elements (including blades) associated with the dynamic imbalance of the rotor and temperature fluctuations when changing the engine operating mode.
It is this group of loads that introduces uncertainty into the structure of acting loads. Effective effective forces are the result of the addition of deterministic and random (vibration) loads. The most dangerous are the resonant vibrations of the blades [7].
Up to 60% of GTE blades failures are of fatigue nature and are associated with the action of alternating stresses arising from vibrations. Failure of one blade usually leads to an avalanche process of damage or destruction of others, imbalance of the rotor, surging and other serious damage to the engine.
Due to the difficult operating conditions of helicopter engines (takeoffs and landings using unprepared takeoff and landing sites, long-term operation near the earth's surface), the turbocharger blades are subject to erosive wear [8].
The wear of the blades of the first compressor stages occurs along the entire height due to the uniform distribution of the dust flow. The blades of the last stages have a pronounced wear along the periphery, which is explained by the centrifugation of the dust flow in the stages. The action of centrifugal forces on dust particles leads to its concentration at the periphery, and the blades of the last stages, which are thinner, turn out to be the most wearing parts of the gas turbine engine. Wear of parts of the compressor flow path can cause surge.
The turbine blades are also subject to erosive wear, mainly the trailing edges of the nozzle blades are abraded, which leads to an increase in the temperature regime and a decrease in the maximum engine power.
During the operation of helicopter engines, conditions almost always arise under which the turbine and compressor blades undergo various types of corrosion. The main types of corrosion for which GTE blades are rejected are: pitting, fretting corrosion, sulphide-oxide corrosion, high-temperature corrosion, etc.[1, 5,7]
The most important direction of technological support of high durability of compressor and turbine blades of helicopter gas turbine engines is the application of protective coatings.
Image 3 shows compressor blades with a protective coating applied.
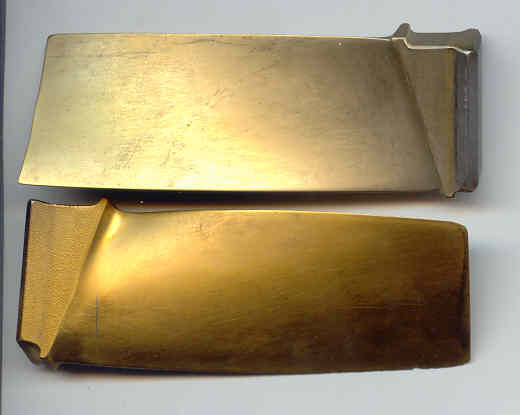
Image 3 – Protective coating on GTE blades
There are many methods of coating the surface of parts, in particular, detonation, chemical-thermal, galvanic, diffusion, plasma, etc., which differ in physicochemical processes of formation.
The most widely used coatings are those based on chemical deposition (CVD) and physical deposition (PVD), as well as various thermal-gas coatings. However, with a significant change in the geometry of the blades, the use of CVD and PVD coating methods is not advisable. The application of the methods of HTN coatings allows obtaining coatings with high characteristics of adhesive and cohesive strength [11,12].
The choice of the most optimal coating method, which will provide the required operational properties of the blades with minimal economic costs, can be conventionally presented in the form of a diagram shown in image 4.
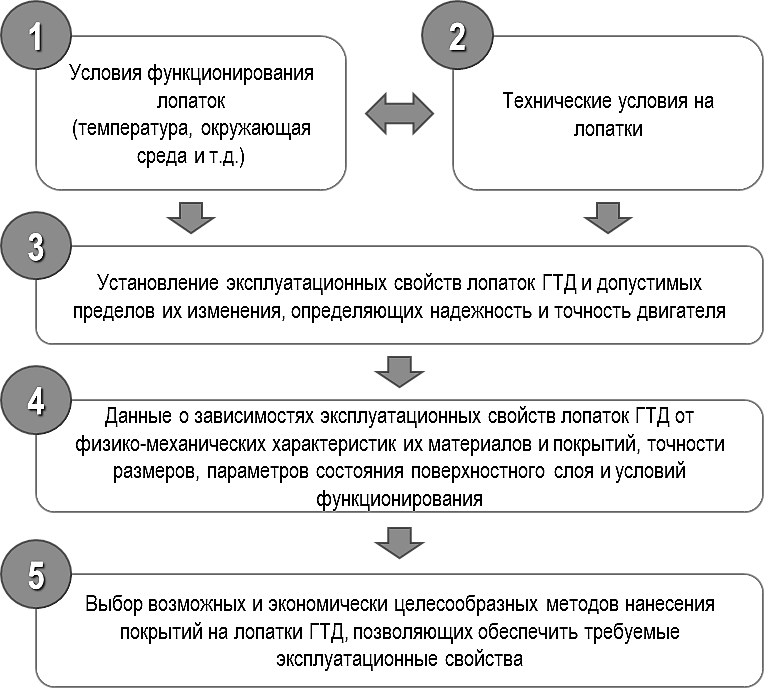
Image 4 – Coating method selection scheme
Conclusion
To obtain a high level of structural strength of the surface layer of compressor blades, various coating methods are used. The applied coatings make it possible to protect the base material from operational influences, and also significantly increase the service life of both the blades and the engine as a whole.
The most promising materials for the formation of hard protective coatings on GTE blades are titanium carbide and nitride. They have high microhardness and crack resistance. Titanium is a high-tech and affordable material, perfectly dispersible by ion-plasma vacuum deposition methods.
The most promising methods for improving the quality and performance of GTE blades are methods of finishing and hardening surface treatment by applying protective coatings.
When writing this essay, the master's work has not yet been completed. Final completion: October 2021. The full text of the work and materials on the topic can be obtained from the author or his manager after that date.
Список источников
- Eliseev Yu.S. Technology of operation, diagnostics and repair of gas turbine engines: Textbook. allowance. / Yu.S. Eliseev, V.V. Krymov, K.A. Malinovsky, V.G. Popov. – M .: Higher school, 2002 . – 355 p.
- Orlov K.Ya., Parkhimovich V.A. Repair of aircraft and helicopters. Moscow: Transport, 1986 . – 295 p.
- Grigoriev V.A. Helicopter gas turbine engines / V.A. Grigoriev, V.A. Zrelov, Yu.M. Ignatkin and others; under total. ed. V.A. Grigoriev and B.A. Ponomarev. - M .: Mashinostroenie, 2007 . – 491 p.
- V. V. Shashkin Aviation GTEs in ground installations / V.V. Shashkin, V.M. Kapralov, M.G. Kalashnikov, O.A. Rudakov, A. Ya. Yaroshenko. – L .: Mechanical engineering, Leningrad. department, 1984 . – 228 p.
- Sirotin N.N. Design and operation, damageability and performance of gas turbine engines. (Basics of designing aircraft engines and power plants). – M .: RIA "IM-Inform", 2002. – 442 p.
- Mashoshin O.F. Aircraft GTE rotor blades: design, strength, operation. Study guide for students. / O.F. Mashoshin, B.A. Chichkov. – M .: MSTU GA, 2017 . – 80 p.
- Keba I.V. Diagnostics of aircraft gas turbine engines - Moscow: Transport, 1980 – 248 p.
- Chichkov B.A. Aircraft GTE rotor blades. Part I. Operational damage of rotor blades. / B.A. Chichkov. / Moscow State Technical University of Civil Aviation, 2000. – 74 p.
- Skubachevsky G.S. Aircraft gas turbine engines: design and calculation of parts. / G.S. Skubachevsky. - M .: Mashinostroenie, 1969 . – 545 p.
- Boguslaev V.A., Muravchenko F.M. etc. Technological support of operational characteristics of GTE parts. Compressor and fan blades. Part 1. Motor Sich OJSC, 2003. – 420 p.
- Zenin B.S. Modern technologies of surface hardening and coating / B.S. Zenin and A.I. Slosman; Tomsk Polytechnic University. – 2nd ed. – Tomsk: Publishing house of Tomsk Polytechnic University, 2012. – 120 p.
- Sinani, I.L. Coating methods / I.L. Sinani, E.M. Fedoseeva, G.A. Beresnev: textbook. allowance. – Perm: Publishing house of Perm. state tech. University, 2008 . – 110 p.