Abstract
Content
- Introduction
- 1. Theme urgency
- 2. Goal and tasks of the research
- 3. Researches and develompents review
- 4. Pneumatic feeder diagram
- Conclusion
- References
Introduction
The technical re–equipment of metallurgy in the coming years will be carried out in conditions of stabilization, and in the future, a decrease in the production of the main types of metal products and will be determined by the main task – to meet the needs of the national economy for ferrous metals of the required quality and range with a significant increase in the efficiency of production and use of metal in consuming industries.
1.Theme urgency
Among the most important strategic tasks facing the iron and steel industry are:
– reducing the metal consumption of production by about 2 times;
– doubling the productivity of the industry;
– radical renewal of fixed assets and increasing the economic efficiency of the industry in a market economy and self–financing;
– complex solution of issues of social development, environmental protection, rational use of natural resources and industrial waste.
These tasks should be solved in the process of technical re–equipment, reconstruction and renovation of each metallurgical enterprise and, in particular, each specific workshop.
At the same time, in the overwhelming majority of cases, there is no need to increase the volume of production at individual enterprises, although the capacity and productivity of reconstructed and new units and even workshops may increase. In each specific case, the main tasks are to improve the quality and expand the range of metal products, improve conditions and increase labor productivity, solve environmental problems and increase production efficiency.
In this regard, the choice and economic justification of options for the reconstruction of metallurgical production facilities, in particular, the converter shop, become especially relevant.
The most important measures to improve the efficiency of the system for feeding and loading bulk materials are:
– increasing the share of finished goods production, obtained in one processing from a continuously cast billet, with a corresponding decrease in the specific consumption of metal and energy;
– the use of automatic non–destructive testing of the original workpiece with subsequent cleaning of the workpieces and automatic control of the finished product surface;
– implementation of automation tools using programmable controllers and industrial computers.
From a conveyor that feeds bulk materials into a converter run, bulk materials are dropped onto a mobile reversible conveyor located above the bins and distributes materials over them. Materials from the bins are dispensed using feeders [1].
2. Goal and tasks of the research
The aim of the work is to increase the efficiency of the system for loading bulk materials into the steelmaking converter
The object of the study are the proceses of feeding and loading of bulk materials
The subject of the research is the parameters of the system for feeding and loading of bulk materials.
3. Researches and develompents review
Feeders with a capacity of 220 m3/h are installed in the bunkers, and feeders with a capacity of 720 m3/h are installed under the ore and fluorspar bins. Feeders supply materials to batcher scales 3–5t. In addition to reloading bins common to all conveyors, two intermediate bins 4 are installed in the area of each conveyor, containing a stock of ferroalloys for one melt. Materials from the hoppers are fed into the bucket using a rotary chute.
A model of the oxygen converter is shown in Fig. 1.
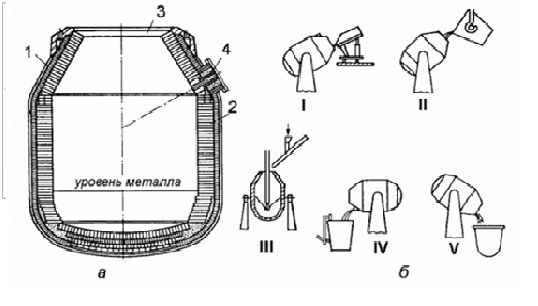
Figure 1 – Converter circuit (a) main periods of melting (b): I – scrap loading; II – pouring cast iron; III – loading of slag–forming additives and blowing with oxygen; IV – drainage of steel; V – slag discharge; 1 – casing; 2 – lining; 3 – neck;
4 – side outlet of steel (tap hole)
4. Pneumatic feeder diagram
The gate is supposed to be controlled according to the following pneumatic drive scheme (Fig. 2) [3]. The automated control system will use electro–pneumatic elements and a controller [4].
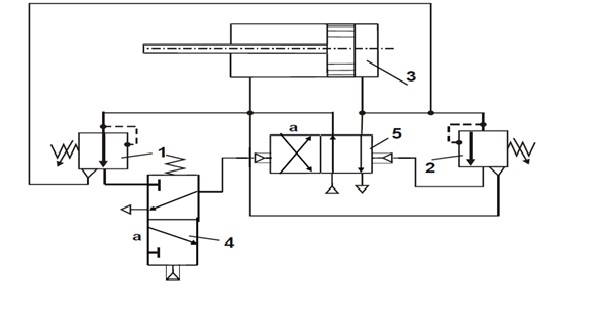
Figure 2 – Control circuit of the pneumatic drive of the gate with pressure control in the working cavity of the pneumatic cylinder: 1,2 – sequence valves; 3 – pneumatic cylinder; 4 – pneumatic switch; 5 – main pneumatic valve.
Conclusion
The task of further work is to substantiate the parameters of the automatic control system for the drives of gates for feeding and loading bulk materials into the converter based on electropneumatic drive elements and a freely programmable controller. When writing this essay, the masterʼs work has not yet been completed. Final completion: June 2021. The full text of the work and materials on the topic can be obtained from the author or his manager after that date.
References
- Целиков А. И. Машины и агрегаты металлургических заводов. В 3–х томах. Т2. Машины и агрегаты сталеплавильных цехов. Учебник для вузов / А.И. Целиков // – М.; Металлургия 1988. – 432с.
- Михайловский В. Н. Основы проектирования металлургических заводов. Определение объёмно–планировочных решений, состава и количества основного технологического и подъёмно–транспортного оборудования сталеплавильных цехов: учеб.пособие./В. Н Михайловский// Спб.: Изд–во Политехн. ун–та, 2013.–215с.
- Лаптева Н. Е. Пневмопривод и средства автоматики 2009.
- Шахматов Е. В. Пнеммопривод и средства автоматики: учеб. пособие – Самара: Издательство СГАУ, 2006 – 112с.
- Пневматические распределители [Электронный ресурс]. Режим доступа:
https://pnevmex.ru/catalog/pnevmaticheskie-raspredeliteli/. - Шиберные задвижки [Электронный ресурс]. Режим доступа:
http://armatek.ru/about/truboprovodnaya_armatura/shibernye_zadvizhki/. - Расчет пневомоцилиндра [Электронный ресурс]. Режим доступа:
https://emc.kiev.ua/%D1%80%D0%B0%D1%81%D1%87%D0%B5%D1%82-%D0%BF%D0%BD%D0%B5%D0%B2%D0%BC%D0%BE%D1%86%D0%B8%D0%BB%D0%B8%D0%BD%D0%B4%D1%80%D0%B0/.