Реферат
Содержание
1. Анализ существующих конструкций сталкивателей заготовок.
По способу передачи толкающего усилия различают следующие конструкции сталкивателей: реечные, винтовые, рычажные, цепные, фрикционные. Для привода сталкивателей преимущественно используют электромеханический привод, но иногда применяются гидравлический или пневматический приводы.
Реечный толкатель (рис. 1) предназначен для перемещения отдельных блюмов и слябов с рольганга в нагревательную печь и продвижения через неё всего ряда заготовок.
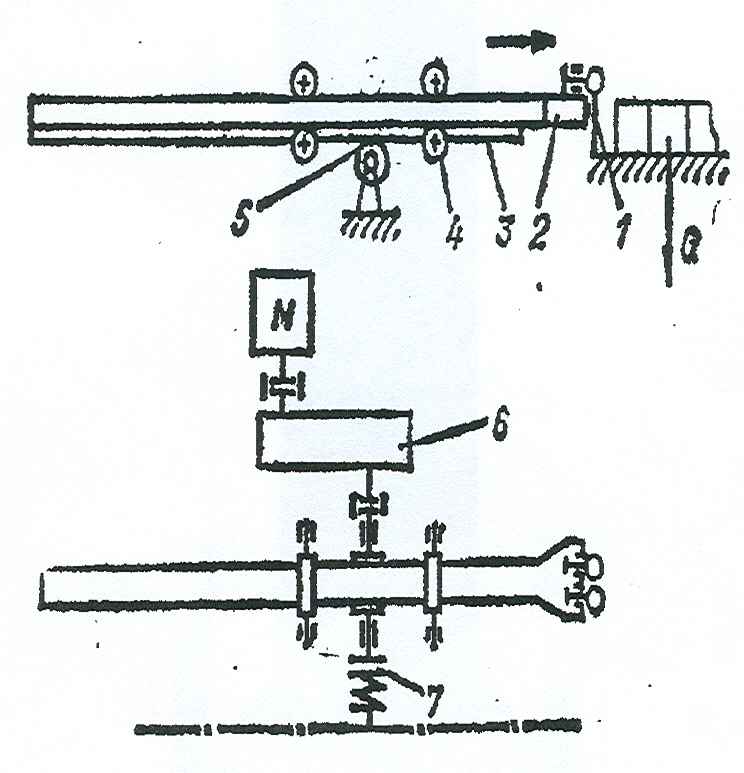
1 – толкающий элемент;
2,3 – зубчатые рейки;
4 – направляющие ролики;
5 – шестерня;
6 – редуктор;
7 – соединительная муфта
Толкающая штага снабжена толкающими пальцами с пружинными амортизаторами. При движении штанги вперёд в опорных катках пальцы упираются в торец штанги и толкают перед собой блюм. При движении штанги назад и наличии на рольганге следующего блюма, пальцы отклоняются вверх, и головка штанги беспрепятственно отклоняется в исходное положение, после чего замыкающая пружина прижимает толкающие пальцы к торцу штанги. С нижней стороны штанги закреплена зубчатая рейка, при помощи которой на штангу передаётся толкающее усилие от привода через приводную шестерню. Скорость движения заготовки, толкаемой реечным толкателем, 0,2 – 0,25 м/с.
Винтовой толкатель (рис.2) подаёт заготовки в печь, продвигает их по ходу печи и выгружает через окно выдачи; применяется для преодоления усилий до 700 кН при ходе линейки до 2,5 м.
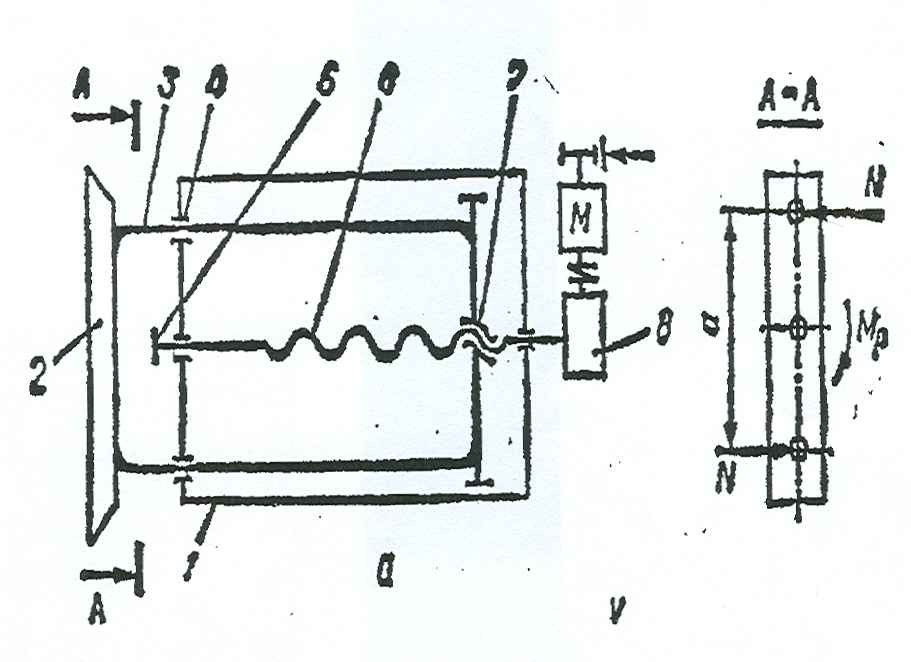
1 – станина;
2 – линейка;
3 – штанга;
4 – направляющая;
5 – подшипник;
6 – винт;
7 – гайка;
8 – редуктор
Винтовой толкатель состоит из неподвижной рамы, на которой установлены передняя и задняя стойки. К передней сойке прикреплены направляющие втулки для штанг, радиальный и упорный подшипники для переднего конца винта. При вращении винта перемещаются гайка и связанная с ней траверса. Траверса в свою очередь жёстко связана с задними концами штанг, которые проходят через направляющие втулки передней стойки, и их передние концы присоединены к общей толкающей головке. Такая конструкция обеспечивает работу винта только на сжатие. Винт вращается от привода, состоящего из электродвигателя, редуктора, соединительной муфты и тормоза.
Недостатками винтовых сталкиваетелей являются: быстрый износ гайки (срок службы не более 2-х лет), низкий коэффициент полезного действия самой пары винт-гайка. Достоинством винтовых сталкивателей по сравнению с реечными являются меньшие габариты и металлоёмкость.
Штанги сталкивателей выполняют кованными, сварными и, для толкателей рассчитанных на малое усилие, из катаных заготовок круглого сечения. Кованные и сварные штанги более сложны в изготовлении, сложнее получается и конструкция направляющих. Однако применение штанг прямоугольного сечения, для реечных сталкивателей, позволяет выполнить зубчатые рейки в виде отдельных деталей, изготовляя их из более прочной и износостойкой стали (40Х, 40ХН), и при износе зубьев заменять, сохраняя тяжёлые и дорогие штанги. Штанги толкателей круглого сечения проще в изготовлении, но в этом случае зубья приходится нарезать на них. В этом случае при износе зубьев штанги должны заменяться целиком.
В отличие от конструкций толкателей, у которых штанга с большим ходом и движется возвратно-поступательно в результате реверсивного движения электродвигателя, у рычажного толкателя (рис.3) возвратно-поступательное движение толкающего устройства происходит при непрерывном вращении электродвигателя в одном направлении. Обычно рычажные толкатели рассчитаны на малые и средние толкающие усилия со скоростями движения 2…3 м/мин и ходом толкателя в пределах 200…600 мм. Преобразование вращательного движения двигателя в возвратно-поступательное движение толкающего устройства в рычажном толкателе происходит следующим образом. Электродвигатель вращает входной вал редуктора, на выходном валу которого расположен кривошип. Кривошип соединён шатуном с рычагом, закреплённым на валу.
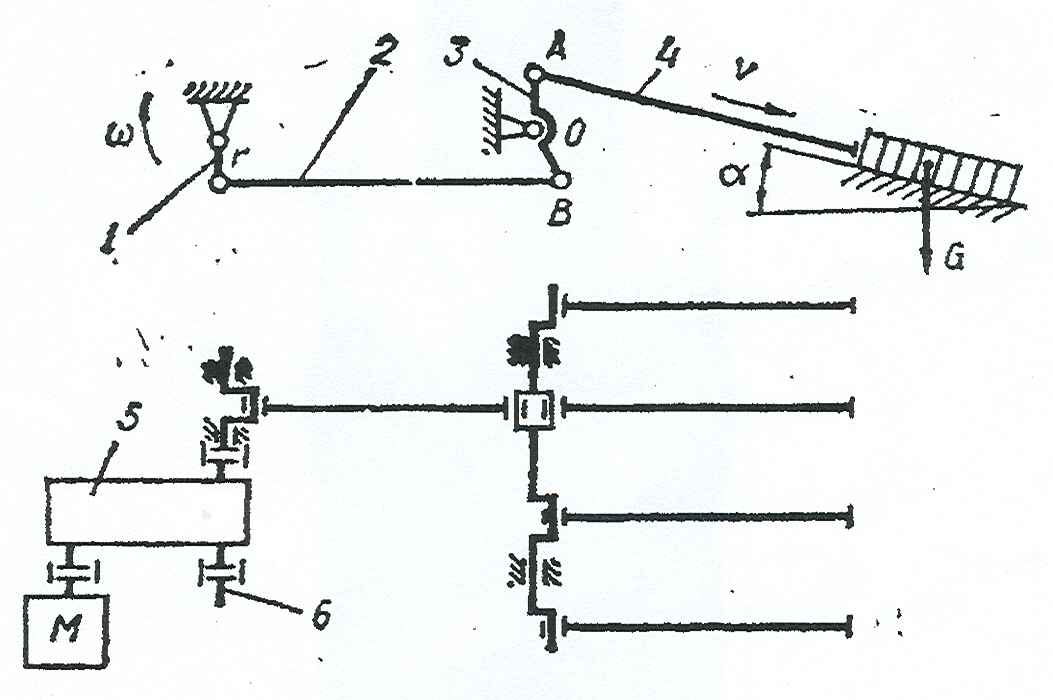
1 – вал;
2 – шатун;
3 – рычаг;
4 – штанга;
5 – редуктор;
6 – выходной вал редуктора
На этот же вал насажены несколько коротких рычагов, к которым одним концом шарнирно присоединены толкающие штанги. Штанги проходят через окна печи и другим концом скользят по направляющей плите внутри печи. При движении вперёд штанги проталкивают через печь весь ряд длинных заготовок на величину хода. При обратном движении штанг между ними и концом ряда заготовок подаётся следующая заготовка, после чего цикл повторяется. Штанга расположена под углом, который приблизительно равен углу наклона печи. Ход штанги составляет 500 – 550 мм. Продолжительность рабочего и холостого хода 10 с.
На данный момент времени на стане 390 Макеевского филиала ПАО ЕМЗ
установлен рычажный
сталкиватель
заготовок, конструкция которого показана на рисунке 4. По конструкции этот сталкиватель аналогичен
конструкции выше описанного рычажного сталкивателя. Различия состоят в том, что сталкиватель стана
390 имеет гидравлический привод вместо электромеханического, и толкающая штанга 1 (рис.5) движется в
направляющих роликах 5, закреплённых на раме 4. Этот сталкиватель проталкивает в печь одну
заготовку, которая поступает на шагающие водоохлаждаемые балки печи.
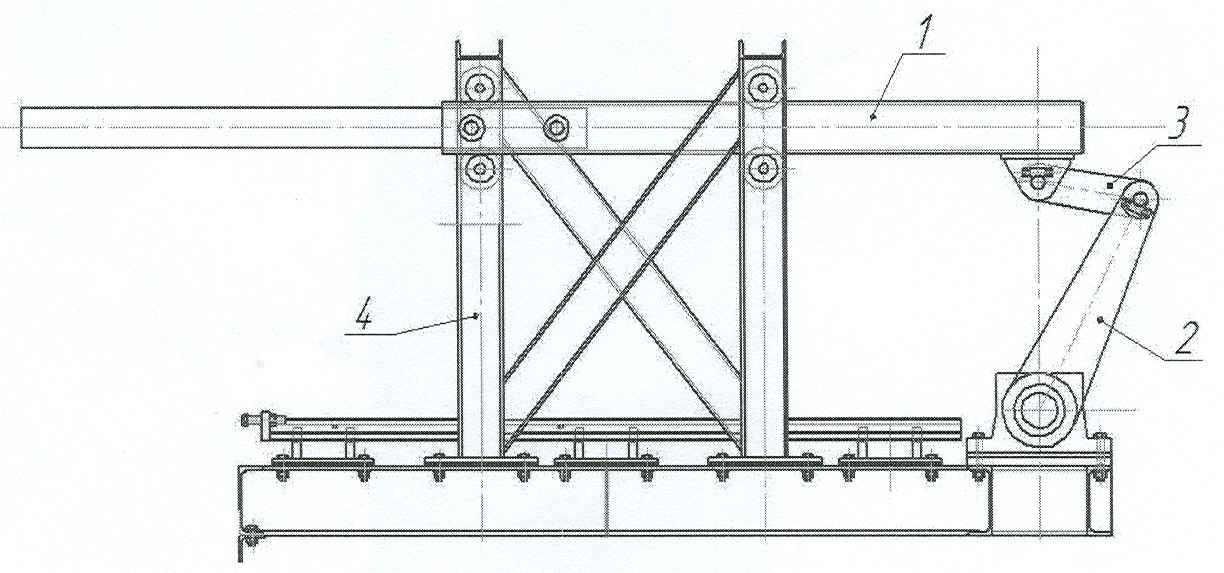
1 – толкающая штанга;
2 – рычаг;
3 – тяга;
4 – рама;
5 – направляющие ролики;
6 – вал
В процессе эксплуатации этого сталкивателя был выявлен следующий недостаток: при проталкивании заготовки в печь толкающие штанги 1 не одновременно вступают в работу. Это вызвано погрешностями при изготовлении элементов сталкивателя. В результате этого, нагрузка от усилия сталкивания заготовки не перераспределяется равномерно между толкающими штангами и, соответственно, валами 6. Это приводит к скручиванию валов и срезу пальцев тяг 6.
Для устранения данного недостатка предлагается жёсткие тяги 3 заменить на регулируемые (рис.5). Это решение позволит путём изменения длины тяг отрегулировать положение толкающих штанг, чтобы последние одновременно вступали в работу.
Регулируемая тяга состоит из двух проушин, соединённых между собой резьбовым стержнем. На одной стороне стержня нарезана правая резьба, на второй – левая. Соответственно, одна проушина имеет правую резьбу, другая левую. При вращении резьбового стержня он будет либо вкручиваться, либо выкручиваться из проушин. Таким образом, будет меняться длина тяги. Для предотвращения самопроизвольного вкручивания или выкручивания резьбового стержня в процессе работы, предусмотрены две контрящие гайки.
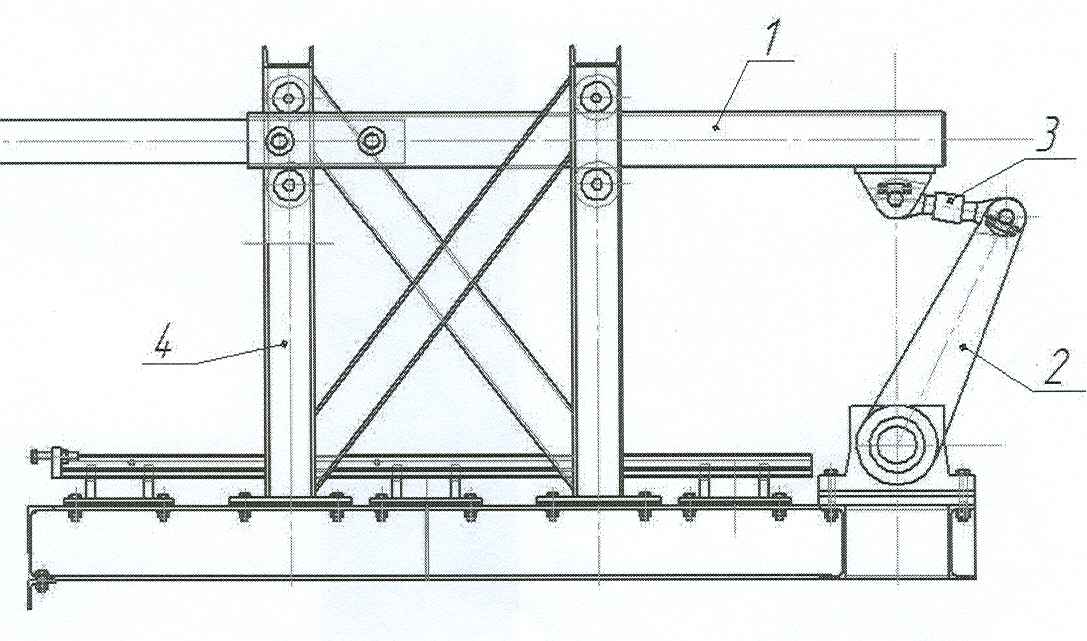
1 – толкающая штанга;
2 – рычаг;
3 – регулируемая тяга;
4 – рама;
5 – направляющие
ролики; 6 – вал
Техническая характеристика сталкивателя стана 390:
– сечение сталкиваемой заготовки, мм 150×150
– длина сталкиваемой заготовки, м 12
– масса сталкиваемой заготовки mз, кг 2120
Привод сталкивателя гидравлический
– ход h, мм 650
Цикл сталкивания tц, с 6
– ход вперёд tв, с 3
– ход назад tн, с 3
2. Виды износа валов
В процессе эксплуатации металлургического оборудования встречаются различные виды физического износа: пластичные деформации и изломы; эрозионно-кавитационные, коррозионные, коррозионно-механические и механические повреждения [2].
Механическим износом называют процесс постепенного разрушения поверхности деталей при их относительном движении. Классификацию механических видов износа разработали М.М. Хрущёв [3], И.В. Каргельский и Е.М. Швецова [4], Б.И. Костецкий [5] и др.
Контактируемые поверхности деталей машин характеризуются микрорельефом и волнистостью, которыми в начальный момент работы узлов трения определяются площадь фактического контакта, давление и время приработки. В процессе эксплуатации под действием рабочих нагрузок и деформаций образуется рабочий рельеф, состоящий из впадин и выступов. Их размеры зависят от внутреннего строения материалов деталей и процессов пластической деформации. В период относительного движения в поверхностных слоях контактируемых деталей возникают упругопластические деформации, которые, в свою очередь, вызывают появление вторичных (физических, химических, механических) процессов.
Профессор Б.И. Костецкий выделяет пять основных видов механического износа: износы схватыванием I и II рода, окислительный, осповидный и абразивный.
Износ схватыванием I рода наблюдается при трении скольжения. Условия его возникновения: малая скорость относительного движения (до 1 м/с для узла трения, состоящего из двух стальных деталей), высокое давление, превышающее предел текучести на площадках фактических контактов, отсутствие смазки или защитной плёнки оксидов и низкая температура нагрева поверхностных слоёв (до 100ºС).
Механизм разрушения поверхностей трения заключается в следующем. Взаимодействие рабочих рельефов при давлениях, превышающих предел текучести, сопровождается интенсивными пластическими деформациями, в результате которых разрушаются плёнки оксидов и вскрываются химически чистые металлические поверхности. Кроме того, пластические деформации способствуют максимальному сближению деталей и образованию в поверхностных слоях текстур из предельно деформированных кристаллов, расположенных по направлению относительной скорости. Если расстояния предельно малы и соизмеримы с размерами атомных решёток, то между ориентированными кристаллами двух деталей появляются металлические связи (схватывание), показанные на рис. 6,а точками и линией 1. Дальнейшее относительное перемещение деталей приводит к наклёпу (упрочнению) металла в местах образования связей.
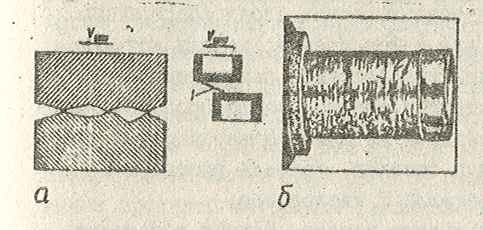
При предельных значениях твёрдости и хрупкости металлические связи разрываются. На контактной поверхности детали из менее прочного металла образуются хаотически расположенные вырывы, а на детали из прочного металла – налипания. Налипшие частицы высокой твёрдости способствуют развитию вторичных процессов местной пластической деформации и микрорезанию поверхностей трения. Внешний вид поверхности детали, работающей в условиях износа схватыванием 1-го рода, показан на рис. 6, б, где отчётливо видны хаотически расположенные вырывы.
Скорость изнашивания деталей составляет 10… 15 мкм/ч. Силы трения определяются геометрическими характеристиками рабочих рельефов, площадью контактных поверхностей и прочностью металлических связей. Коэффициент трения достигает 4…6 ед.
Окислительный износ развивается в условиях трения качения и трения скольжения со скоростями относительного движения деталей 1,5… 7 м/с (без смазки). При граничной смазке интервал относительных скоростей увеличивается до 20 м/с.
Механизм разрушения поверхностей определяется сложными взаимодействиями материалов деталей с кислородом окружающей среды: насыщением металлов кислородом за счёт химических реакций (хемосорбция), проникновением кислорода в поверхностные слои деталей (диффузия) и растворением кислорода в поверхностных слоях (адсорбция). Эти процессы наиболее характерны для узлов трения, детали которых изготовлены из материалов с высокой твёрдостью и повышенным пределом текучести. В зависимости от характера и интенсивности процессов диффузии, адсорбции и хемосорбции основной металл в поверхностных слоях деталей может превращаться в плёнки оксидов, твёрдые растворы и различные химические соединения металла с кислородом.
Различают три формы окислительного износа. Первая характеризуется непрерывным образованием и разрушением ультрамикроскопических плёнок адсорбционных оксидов. Заметных пластических деформаций и диффузионных явлений не отмечается. Вторая форма окислительного износа проявляется при возникновении в поверхностных слоях деталей неупорядоченных твёрдых растворов и эвтектик химических соединений металла с кислородом. Третья форма – сплошные плёнки химических соединений металла с кислородом. Изнашивание поверхностей заключается в периодическом появлении и скалывании твёрдых и хрупких химических соединений. Внешний вид детали, работающей в условиях окислительного износа, показан на рис. 7. В центре видна матовая полоса, состоящая из оксидов, твёрдых растворов и химических соединений металла с кислородом.
Скорость изнашивания минимальная по сравнению с другими видами механического износа и составляет 0,1… 0,5 мкм/ч. Коэффициент трения зависит от формы и колеблется в пределах 0,3… 0,7.
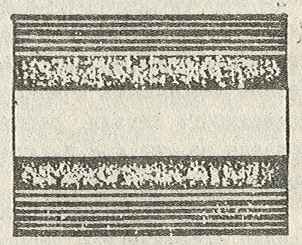
Износ схватыванием 2-го рода. Условия его образования: трение скольжение, высокие давления и скорость относительного перемещения (υотн>4 м/с), сочетание которых обуславливает большие потери энергии на трение, высокий градиент и интенсивное возрастание температуры в поверхностных слоях (до 1600ºС). Механизм разрушения поверхностей зависит от интенсивности внешних механических воздействий и свойств материалов деталей.
Различают три стадии износа схватыванием 2-го рода. Первая стадия соответствует интервалу температур, мало снижающих механические свойства материалов (для сталей до 600ºС). С повышением температуры механические свойства стали понижаются, и может наступить момент, когда давления станут выше фактического предела текучести. В этом случае взаимодействие рабочих рельефов, сопровождающееся интенсивными пластическими деформациями, приводят к разрушению плёнок оксидов и образованию металлических связей. Дальнейший ход механизма разрушения такой же, как и при износе схватыванием 1-го рода, но внешний вид поверхностей имеет существенное отличие: вырывы частиц на детали из менее прочного материала расположены не хаотически, а чередуются примерно через одинаковые промежутки (рис. 8,а).
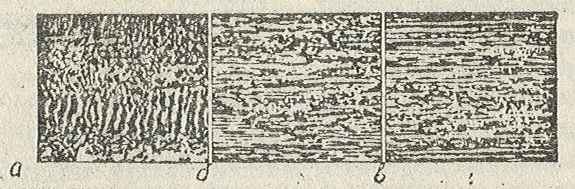
Вторая стадия износа развивается в интервале температур 600…1400ºС. Такая температура заметно снижает механические свойства сталей, и металл размягчается. Разрушение деталей характеризуется контактным схватыванием и пластическим разрывом металлических связей. На контактной поверхности более прочной детали видны налипание и размазывание металла (рис. 8,б), а на поверхности менее прочной детали – вырывы.
Третьей стадии износа соответствует температура плавления. Расплавленные слои металла уносятся со смазкой, и на поверхностях трения появляются оплавленные бороздки (рис. 8,в).
Скорость изнашивания деталей составляет 1… 5 мкм/ч. Коэффициент трения колеблется в пределах 0,1… 0,5.
Осповидный износ возникает при трении качения, переменных или знакопеременных нагрузках и высоких давлениях, достигающих предела выносливости.
Механизм разрушения поверхностей по теории А.К. Динника, Н.М. Беляева и др. заключается в следующем. Взаимодействие двух упругих тел с пространственно-криволинейными поверхностями в объёме металла, расположенного под точкой контакта А (рис. 9), вызывает нормальные σ и касательные τ напряжения. Максимальные нормальные напряжения соответствуют координате х=0, а максимальные касательные – координате у=0,7а, т.е. появляются не на поверхностях трения, а внутри деталей. Площадки суммарных максимальных напряжений расположены под некоторым углом β (β<45º) к плоскости контакта. Многократные нагружения вызывают усталость материала, и, как следствие, на плоскостях максимальных напряжений внутри детали зарождаются трещины. Их развитие приводит к разрыву контактной поверхности, что принципиально изменяет характер взаимодействия деталей. Движение шара через разрыв поверхности сопровождается динамическими явлениями. Если шар движется влево, то ударные нагрузки вызывают наклёп и скалывание I участка по стрелке с. При движении шара вправо наблюдается скалывание II участка. В местах образования сколов на контактных поверхностях появляются осповидные углубления. Интенсивность образования микротрещин зависит от напряжений, возникающих в деталях в период механической обработки, и различных концентраторов.
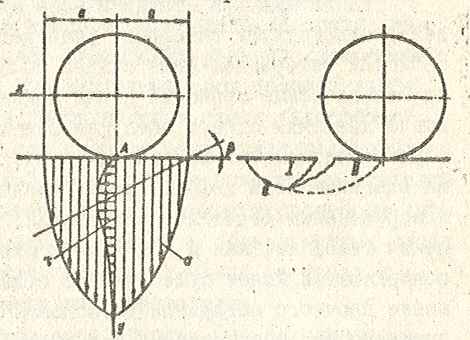
Абразивный износ развивается при трении скольжения. Условия его возникновения: наличие на поверхностях трения абразивных частиц, деформирующих микрообъёмы поверхностных слоёв и вызывающих процессы микрорезания. Интенсивность изнашивания зависит от размеров, формы, свойств абразивов и материалов деталей, от относительных скоростей и давлений. Скорость изнашивания деталей колеблется в пределах 0,5…5 мкм/ч.
Излом – разрушение детали, вызываемое низким качеством материала, дефектами изготовления, нарушениями правил эксплуатации, случайными механическими повреждениями и другими факторами. По характеру нагружения деталей различают статические и усталостные изломы. Статические изломы возникают под действием чрезмерных кратковременных нагрузок. Эти изломы в зависимости от скорости нагружения и исходной структуры материала могут быть вязкими и хрупкими.
Усталостные изломы, возникающие под действием циклических нагрузок, различны по внешнему виду, однако все они возникают с небольших трещин, которые, увеличиваясь, полностью разрушают вал. Классификация усталостных изломов (рис. 10) предложена проф. В.М. Гребенником [3]. Стрелками на рисунке показано направление распространения фронта трещины; умеренные номинальные напряжения соответствуют нижней половине кривой усталости, а высокие – верхней половине. Такая классификация позволяет оценить вид и значение рабочих нагрузок, конструктивные особенности деталей, способствующие развитию усталостных изломов. Она наглядно иллюстрирует условия зарождения и развития трещин и может быть использована для разработки мероприятий, направленных на уменьшение поломок оборудования.
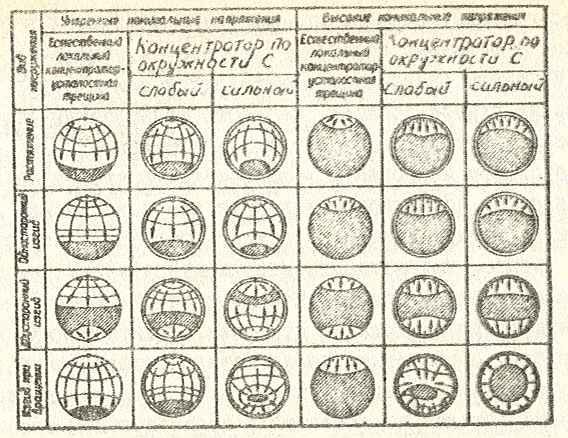
Коррозионные повреждения представляют собой процесс разрушения деталей вследствие химического или электрохимического взаимодействия с окружающей средой.
Химические повреждения возникают в электрически нейтральных средах при реакциях между материалом валов и активными составляющими внешней среды (например, кислородом, сернистым газом). В результате образуются неустойчивые плёнки оксидов, разрушение которых под действием рабочих усилий изменяет геометрические размеры деталей. Коррозионные повреждения , вызванные электрохимическим воздействием, наблюдается в тех случаях, когда на поверхности вала появляются точки или участки с различными электрическими потенциалами. Например, граница и сердцевина зерна, напряжённый и ненапряжённый участки металла, чистый металл и оксиды. Анодные участки имеют более высокий электронный потенциал и поэтому подвергаются разрушению.
В зависимости от свойств внешней среды различают коррозию в электролитах, атмосферную и газовую. Атмосферная коррозия развивается при нормальном давлении и температуре не превышающей 80ºС. В окружающей среде металлургических цехов содержится влага, различные соли, щёлочи и кислоты, водные растворы которых представляют собой электролит. Он осаждается на деталях и способствует образованию микрогальванических элементов. Разрушение поверхностей валов в начальный момент имеет точечный характер, а в дальнейшем – сплошной. Внешней средой при газовой коррозии являются газы, горячий воздух и пар. Такому износу подвергаются многие детали металлургических машин из-за взаимодействия контактируемых поверхностей с кислородом воздуха.
Эрозионно-кавитационные повреждения образуются в период контакта деталей с потоками жидкости и газа, движущимися с большой скоростью. Механизм разрушения поверхностей заключается в непрерывном образовании плёнок оксидов. Скорость изнашивания деталей увеличивается, если в потоке имеются твёрдые частицы.
Под действием коррозии и механических факторов на поверхности деталей появляются коррозионно-механические повреждения (коррозионные усталость и растрескивание, фреттинг-коррозия). Коррозионная усталость – процесс интенсивного разрушения деталей при одновременном действии коррозии и циклических напряжений. Коррозионное растрескивание возникает под действием коррозии и статических напряжений. Фреттинг-коррозия образуется, когда детали, соединённые прессовой или горячей посадкой, совершают малые относительные движения. Механизм разрушения деталей заключается в периодическом образовании защитных плёнок окислов на границе контактирующих поверхностей [2].
Выводы. Проанализировав признаки и условия возникновения видов износа валов, а также то, что главный вал работает на кручение и изгиб при переменных нагрузках, то можно сделать вывод об усталостном характере излома главного вала в результате возникновения и развития усталостной трещины. Опорные шейки главного вала подвержены, прежде всего, абразивному износу из-за некачественных уплотнений и неправильного режима смазывания.
Список литературы
-
Радчик И., Рябков В., Сушко А. Комплексный подход к вопросам повышения надёжности работы основного и вспомогательного оборудования современного металлургического производства. Журнал
Национальная металлургия
, №1, 2006, с.24-29. -
Седуш В.Я. Надежность, ремонт и монтаж металлургических машин. – К.: НМК ВО, 1992.– 368 с.
-
Гребенник В.М. Усталостная прочность и долговечность металлургического оборудования. – М.: Машиностроение, 1969. – 256 с.
-
Хрущов М.М. Классификация условий и видов изнашивания деталей машин// Трение и износ в машинах. Сб. VIII. – М.: Изд-во АН СССР, 1953. – С. 5 – 17.
-
Швецова И.Е., Крагельский И.В. Классификация видов разрушения поверхностей деталей машин в условиях сухого и граничного трения // Трение и износ в машинах. Сб. VIII. – М.: Изд-во АН СССР, 1953. – С. 18 – 38.
-
Костецкий Б.И. Сопротивление изнашиванию деталей машин. – К.: Машгиз, 1959. – 478 с.
-
Іванченко Ф.К., Гребеник В.М., Ширяєв В.І. Розрахунок машин і механізмів прокатних цехів. – Київ: Вища школа, 1995. – 455 с.