Реферат по теме выпускной работы
Содержание
- Введение
- 1. Актуальность темы
- 2. Цель и задачи исследования
- 3. Описание способов контроля рабочей поверхности алмазного шлифовального круга
- 4. Описание конструкции устройства для профилографирования рабочей поверхности алмазного шлифовального круга
- Выводы
- Список источников
Введение
Шлифование алмазным кругом является довольно сложным и дорогостоящим процессом, требующим грамотного обращения с алмазным инструментом и понимания природы износа шлифовальных кругов. Для предотвращения преждевременного разрушения режущей поверхности алмазного круга необходимы сведения о геометрических характеристиках рабочей поверхности, интенсивности износа абразива и связки, отклонения геометрии круга и его пористости [1].
Одним из методов определяющим данные параметры является метод профилографирования. Этот метод является разновидностью микрометрического метода измерения износа.
На профилографе измеряется величина, так называемого «первичного износа» – за который принимается разница в высоте микронеровностей от линии впадин до гребешка – замеренную на одном и том же участке в различные моменты испытания. Для измерения износа методом профилографирования используют профилограф-профилометры.
Данный метод заключается в следующем. С одного и того же микроучастка исследуемой поверхности снимаются профилограммы до начала испытания и после.
На профилограммах контуры одних и тех же впадин остаются постоянными, а выступы, вследствие износа, меняют свою высоту. Определяя общее уменьшение выступов от линии впадин, получаем величину первичного износа. В случае, если она превышает высоту неровностей в качестве постоянной базы, от которой производится измерение, выбирается нерабочий участок исследуемой поверхности.
Недостатком метода является невозможность снятия профилограммы до и после испытания с одного и того же сечения, что приводит к появлению погрешности в определении величины линейного износа. Эта погрешность тем больше, чем меньше сама величина износа по сравнению с величиной неровностей поверхности [2].
1. Актуальность темы
Технологический процесс шлифования является одним из широко распространенных в машиностроении. Так, в отечественном машиностроении доля шлифовальных станков составляет 12 %, а в автомобилестроении – до 25 %.. К шлифовальному кругу, как к режущему инструменту, предъявляются большие требования в отношении поддержания остроты режущих кромок и сохранения требуемой формы профиля круга. Алмазное шлифование является сложным дорогостоящим процессом, требующим грамотного применения алмазного инструмента и понимания природы износа шлифовальных кругов.
Шлифовальные алмазные круги состоят из рабочего алмазного слоя и корпуса. Алмазный слой состоит из наполнителя, связки и самого алмазного порошка. Поэтому для предотвращения несвоевременного разрушения режущей поверхности алмазного круга необходимы сведения о состоянии рабочей поверхности круга, а именно: число зерен на единице рабочей поверхности, плотность распределения вершин зерен по высоте рабочей поверхности, высота рабочего слоя, состояние вершин алмазных зерен. Также к шлифовальному кругу, как к режущему инструменту, предъявляются большие требования в отношении поддержания остроты режущих кромок и сохранения требуемой формы профиля круга. Если прочность закрепления абразивных зерен в инструменте ниже прочности самих зерен, то изнашивание происходит за счет выкрашивания зерен, а круг работает в режиме самозатачивания. Самозатачиванием называют свойство круга сохранять работоспособность вследствие образования новых режущих кромок в процессе обработки. Если прочность абразивных зерен окажется ниже прочности их закрепления в шлифовальном круге, то изнашивание происходит частично за счет хрупкого разрушения и скалывания зерен, а частично — в результате их истирания обрабатываемым материалом. Такое изнашивание носит название затупления круга и заключается в образовании площадок износа на поверхности абразивных зерен и уменьшении режущей способности инструмента, что проявляется в увеличении силы резания до двух раз. Кроме того, неравномерный износ круга приводит к изменению его профиля. Нестабильность рабочих характеристик шлифовального круга, изменение их во время обработки заготовок приводит к изменению качества поверхности слоя детали. Поэтому возникает необходимости в правки шлифовального круга.
2. Цель и задачи исследования
Целью работы является проектирование устройства для автоматизированного контроля рабочей поверхности алмзного шлифовального круга и исследование его выходных характеристик
Объектом исследования явлется устройство для автоматизированного контроля рабочей поверхности алмазного шлифовального круга.
Предметом исследования является контроль рабочей поверхногсти методом профилографирования
3. Описание способов контроля рабочей поверхности алмазного шлифовального круга
Для восстановления режущей способности шлифовальных кругов, их геометрической формы и микропрофиля рабочей поверхности периодически производят правку, т. е. приводят круг в работоспособное состояние. Существует большое количество методов измерения степени износа шлифовального круга, которые рассмотрены ниже.
Косвенный способ измерения степени износа алмазных шлифовальных кругов путем измерения силы резания. Силы резания при шлифовании влияют на качество обработанной поверхности, а также по уровню сил можно оценить степень износа алмазного круга и своевременно прибегнуть к восстановлению его режущих свойств. Экспериментальное определение величины и характера изменения сил резания при шлифовании производилось многими исследователями с применением различных измерительных средств. На первых этапах исследовательских работ определяли силу резания через измерения мощности, развиваемую электродвигателем при шлифовании с помощью ваттметра. Величину тангенциальной составляющей силы резания определяют расчетным путем [1]:
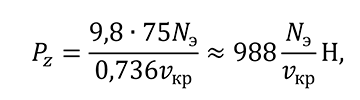
где Nэ-эффективная мощность в кВт, развиваемая на шпинделе; νкр-окружная скорость круга в м/с. Рассматриваемый метод прост, но не позволяет измерить составляющие силы резания и не точен, так как определяет полную мощность, включая и потери на трение в механизмах станка.
Для непосредственного измерения составляющих сил можно использовать динамометрические устройства. Динамометр может быть изготовлен в виде упругой муфты с плоскими радиально-расположенными пружинами [1]. Можно так же использовались проволочные датчики сопротивления, установленные на двух центрах (переднем и заднем) станка. Два динамометрических центра позволяют фиксировать силу резания в процессе шлифования при любом положении шлифовального круга относительно обрабатываемой детали. Однако, данный метод применим только при установке детали в центрах.
Способ бесконтактного измерения степени износа алмазных шлифовальных кругов путем измерения вибрации шлифовального круга [2]. При изменении состояния рабочей поверхности круга возникают вибрации, вызванные как вибрациями непосредственно самого шлифовального круга, так и механизмами станка.
Перемещение в технологической системе при возникновении вибрации основаны на измерении расстояния между шлифовальным кругом и датчиком емкостным методом. Схема измерения показана на рисунке 1. Емкостной датчик образован металлической пластиной 1 с устройством 2 для измерения начального зазора Δ и поверхностью шлифовального круга 3, которую предварительно смачивают электропроводной жидкостью. В качестве электропроводной жидкости используют эмульсию или водопроводную воду. При измерении шлифовальный круг приводят во вращение. В качестве привода используют либо специальный стенд (при установке шлифовального круга на оправку), либо привод станка (при измерении непосредственно на шпинделе станка). При наличии относительных колебаний между поверхностью круга и пластиной 1 изменяется величина зазора Δ, что приводит к изменению емкости зазора между пластиной 1 и влажной поверхность шлифовального круга 3. Изменение емкости с помощью специального усилителя 4 преобразуется в электрический сигнал, который записывается регистрирующим прибором 5 (см. рис. 1).
Это способ является бесконтактным способом измерения степени износа шлифовальных кругов и почти не находит практического применения, так как имеет низкую точность измерения. Данный метод является косвенным принципом измерения степени износа круга, отличающийся сложностью обработки результатов измерения и значительными погрешностями, не позволяет оценить неравномерность износа. Неточность в измерении вызваны зависимостью зазора от состояния жидкости, которая не контролировано меняется.
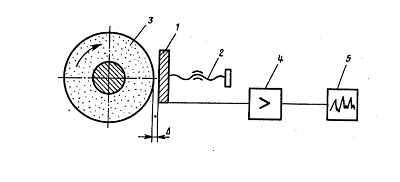
Рисунок 1 – Схема измерений вибраций шлифовального круга.
Фотоэлектрический метод бесконтактного измерения степени износа шлифовального круга [3]. На рис. 2 изображена принципиальная схема измерительного устройства при измерении степени износа алмазно-абразивного круга.
Фотоэлектрическое устройство для бесконтактного измерения степени износа рабочего инструмента содержит оптико-электронный блок, включающий в себя два осветителя 1, объектив 2, полевую диафрагму 3, конденсатор 4, два фотоприемника 5 и блок 6 сравнения; регистратор, выполненный в виде стрелочного индикатора 7; и два светоотражающих элемента 8 и 9, выполненные в виде пластин.
Светоотражающие элементы 8 и 9 закреплены на боковой поверхности круга 10, причем элемент 8 размещен в зоне износа, а элемент 9 - вне ее. Устройство работает следующим образом: перед началом измерений схема настраивается таким образом, чтобы на выходе блока 6 сравнения сигнала не было, то есть показание индикатора 7 было нулевым. По мере износа круга 10 с уменьшением его размеров уменьшается и площадь отражающего элемента 8, поскольку он размещен по краю круга. При этом сигнал, который считывается фотоприемником, регистрирующим величину потока элемента 8, уменьшается, а сигнал, полученный другим фотоприемником от базового отражающего элемента 9, остается неизменным. Баланс схемы нарушается, на выходе блока 6 сравнения появляется выходное напряжение, по величине которого и судят о снижении износа алмазно-абразивного круга 10.
Фотоэлектрический метод является бесконтактным методом, прост в реализации, но главный недостаток - относительно небольшая точность. В качестве излучателя светового потока используется поверхность рабочего инструмента. Для повышения точности измерения степени износа инструментов с низкой отражательной способностью устройство снабжено двумя отражающими световой поток элементами, один из которых размещен в зоне износа, а второй - вне ее и является базовым. Рассматриваемый метод позволяет определить только линейный износ, но не характеризует состояние рабочей поверхности шлифовального круга.
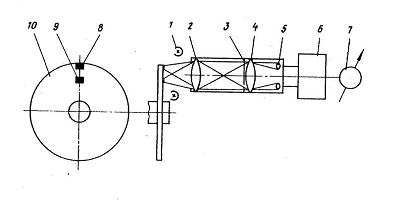
Рисунок 2 – Фотоэлектрическое устройство для бесконтактного измерения степени износа шлифовального круга.
Пневматический метод бесконтактного измерения степени износа шлифовального круга [4]. Известен способ бесконтактного измерения степени износа алмазных шлифовальных кругов с помощью пневматического датчика. Предлагаемый метод заключается в том, что к торцу шлифовального круга подводится сопло, через которое подается воздух под давлением, расход подводимого воздуха определяют за счет разности показаний длинномера пневматического датчика. В качестве измерительной базы принимают рабочую поверхность алмазного шлифовального круга. Это позволяет повысить точность измерения износа шлифовального круга в процессе работы.
Оптический метод измерения степени износа шлифовального круга [5, 6]. Большинство оптических методов основаны на лазерной триангуляции. Основные элементы установки: лазерный диод и позиционно-чувствительный детектор (ПЧД) с усилителем и двумя линзами (рис. 3).
Датчик крепится на двух осях блока шагового привода с возможностью перемещения в направлении, перпендикулярном к поверхности шлифовального круга и в осевом направлении. Данный метод позволяет проводить измерения при скорости круга до 300 м/с. Так же возможно определить радиальное биение.
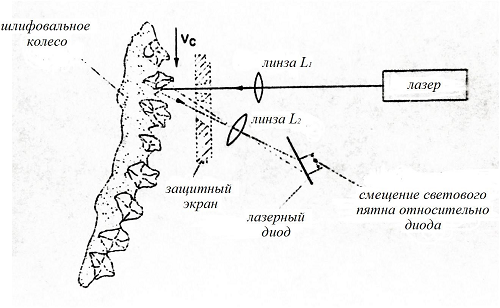
Рисунок 3 – Оптическая установка для измерения степени износа шлифовального круга.
Метод профилографирования. Данный метод относится к экспериментальному определению характеристик рабочей поверхности круга. Линейный износ круга измеряется с помощью специального стационарного приспособления в 6 фиксированных точках по периферии и в трех точках вдоль образующей круга с точностью 0,001мм. Измерение диаметра шлифовальных кругов менее 50 мм в процессе его работы производили микрометрами с погрешностью ±0,004мм. Характер износа алмазных зерен исследуется по фотографиям, полученным на металлографическом микроскопе ММР с увеличением 200х – 500х.
На кафедре ДонНТУ было разработано специальное устройство (рис. 4) для записи режущего профиля алмазного круга на металлической связке с выделением зерен из общего рельефа круга. Оно построено на базе профилограф-профилометра 4, электронного блока 3 и приспособления 2. Информация выводится на ленту самопишущего прибора профилограф-профилометра 5. На приспособлении 2 располагается датчик профилограф-профилометра, который регистрирует колебания коромысла с лопаточкой, которое, перемещающегося в соответствии с изменением профиля круга.
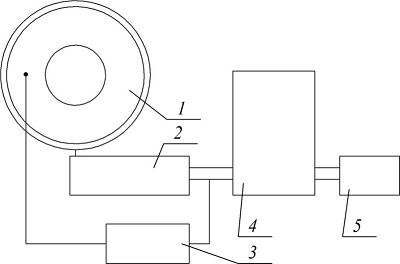
Рисунок 4 – Структурная схема устройства для записи режущего профиля алмазного круга.
Здесь же располагается привод вращения круга, состоящий из малооборотного двигателя, блока редукции и приводного капролонового ролика. При помощи пониженной редукции достигается очень малая частота вращения алмазного круга – 1 оборот за 10 часов для круга диаметром 200 мм, соответствующая линейной скорости перемещения, равной 1 мм/мин. Такая скорость трассировки круга соответствует скоростям протяжки датчика, применяемым при профилографировании поверхности детали. Перед записью профиля рабочей поверхности круга производилась тарировка всего измерительного устройства. Для этого использовалась микрометрическая скоба с ценой деления 2 мкм. Длина профилограммы составляла не менее 15-20 мм рабочей поверхности круга.
Привод вращения круга имеет возможность смещения в вертикальном направлении, что позволяет его использовать для различных размеров алмазных кругов. В качестве контактирующего элемента применяется лопаточка, выполненная из закаленной стали. Толщина ее составляет 0,05 мм, а ширина варьировалась в пределах от 0,1 до 0,7 мм в зависимости от зернистости круга и задач исследований. Запись алмазных зерен воспроизводит изображение набора частиц, находящихся в пересекаемой плоскости щупа, в искаженном виде. Профилограмма поверхности круга является плоскостью ортогональных проекций всех элементов структуры, содержащихся в объеме, отсекаемом краями щупа. Анализ получаемого рельефа круга по профилограмме требует применения методов стереологической реконструкции поверхности, которая аналогична анализу структуры фольги при электронной микроскопии.
Недостатком этого метода является возможность осуществления измерения только при отсутствии процесса резания и скорости круга 0,01 м/с.
4. Описание конструкции устройства для профилографирования рабочей поверхности алмазного шлифовального круга
Исследование положения алмазных зерен РПК проводят на измерительном комплексе, который позволяет регистрировать рельеф рабочей поверхности кругов на металлической связке методом профилографирования с последующей регистрацией данных на ПЭВМ. Измерительный комплекс включает устройство для закрепления шлифовального круга с узлом его вращения, комплект приборов профилометра-профилографа (устройство для профилографирования и блок усиления), компьютер, оборудован преобразователем аналогового сигнала в дискретный, и дисплей и позволяет регистрировать рельеф рабочей поверхности кругов на металлической связке с выделением рельефа зерен и связки. принципиальная схема комплекса представлена на рис. 5 и его принцип действия на рис. 6.
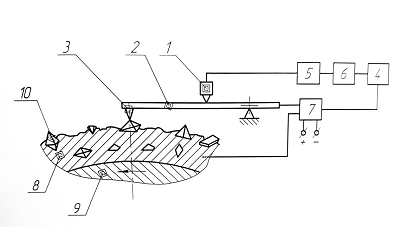
Рисунок 5 – Схема устройства для регистрации рельефа режущей поверхности алмазных кругов на металлической связке.
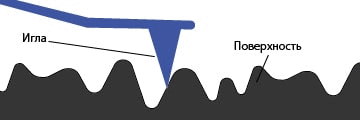
Рисунок 6 – Принцип действия профилографа
(анимация: 5 кадров, 10 повторов, 44.8 килобайт)
Измерительный комплекс работает следующим образом. При вращении круга 9 ощупывающая игла 3 огибает профиль рабочей поверхности круга, осуществляя колебания коромыслом 2 относительно оси качания. Эти колебания воспринимаются датчиком 1, сигнал от которого поступает на входной порт компьютера 4 через блок согласования и преобразователь 6 непрерывного электрического сигнала в дискретный.
Когда ощупывающая игла 3 находится на алмазном зерне 10, сигнал от датчика поступает на блок согласования 5, где он уменьшается до уровня в ... 5 В, затем он попадает в преобразователя 6, в котором непрерывный электрический сигнал от датчика превращается в дискретный, а затем на порт компьютера 4. Одновременно на этот же порт поступает сигнал от ключевого элемента 7, который придает сигнала соответствующий алмазному зерну код «1». На дисплее компьютера отображается рельеф алмазного зерна соответствующим цветом или толстой линией (рис. 7).
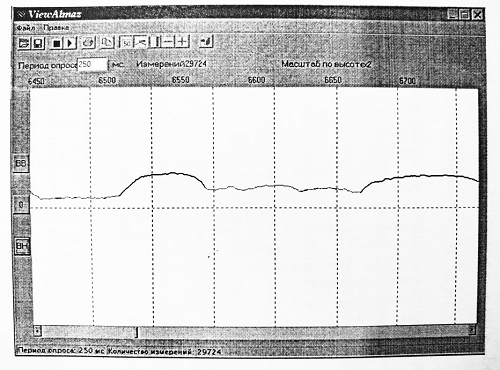
Рисунок 7 – Окно программы для регистрации параметров РПК с фрагментом профилограммы рельефа алмазных зерен (жирная линия) и рельефа связки (тонкая линия)
При сходе ощупывающей иглы 3 из зерна 10 она попадает на токопроводящую связку 8 и сигнал от датчика продолжает поступать на порт компьютеру через блок согласования 5 и преобразователь 6 непрерывного электрического сигнала в дискретный. В это же время на порт компьютера через ключевой элемент 7 поступает сигнал, соответствующий металлической связке с кодом «0».
На дисплее компьютера отображается рельеф металлической связки соответствующим цветом или тонкой линией.
Таким образом, профилограмма содержит информацию о параметрах РПК.
Для преобразования аналоговых сигналов величиной 0 ... + 5 BВ цифровые коды для записи в ПЭВМ используется многофункциональное устройство NVL08. Выходной дифференциальный сигнал электронного блока профилографа величиной несколько вольт имеет уровень относительно земли около 140 ... 170 B. Для согласование его с входом NVL08 был изготовлен устройство, схема которого показана на рис. 8.
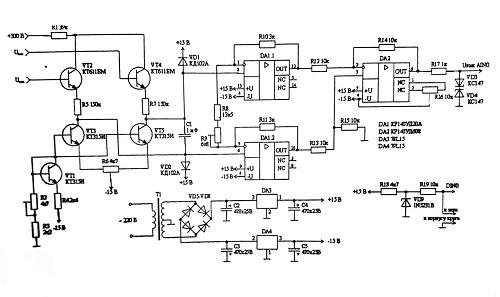
Рисунок 8 – Принципиальная электрическая схема согласующего устройства
На транзисторах VT1 - VT5 собрана схема, снижает входное напряжение. Транзисторы VT3, VT4, базы которых подключаются к выходам электронного блока профилографа, служат повторителями напряжения, не безобразят работу электронного блока (входной ток составляет десятки микроампер). Транзистор VT1 с резисторами R2 i R4 служит для задания токов транзисторов VT3 и VT5. Эти транзисторы работают в режиме источников тока и обеспечивают совместно с резисторами R5 i R7 смещение синфазного сигнала от высокого (140 ... 170 В) до примерно нулевого уровня с небольшим уменьшением полезного (дифференциального) сигнала. Резистор R6 служит Для установки нуля на выходе схемы. На операционных усилителях DA1.1, DA1.2 DA2 реализуется вычитание сигналов преобразования дифференциального сигнала в заземленный сигнал требуемой величины (Регулирование осуществляется резистором R9). Для ограничения сигнала на входах DA1.1 и DA1.2 установлены диоды VD1 и VD2. Резистор R17 и стабилитроны VD3 i VD4 служат для ограничения напряжения на входе NVL08 к пяти вольт. Устройство на элементах R18, R19 и VD9 выдает сигнал, равный единицы, когда игла находится на алмазе, и равен нулю, когда игла касается связки..
Для управления запуском аналого-цифрового преобразователя (АЦП) устройства NVL08 и предварительной обработки результатов измерений разработано программное обеспечение, позволяющее проводить запуск АЦП через заданные промежутки времени и запоминать результаты измерений высоты алмазных зерен и связки вдоль линии исследования.
Изготовленное устройство для автоматизации записи параметров рабочей поверхности алмазного круга к ПЭВМ позволяет кардинально снизить трудоемкость исследований параметров РПК. Рельеф РПК оценивали следующими параметрами: разновысотностью зерен относительно наиболее выступающего зерна, расстоянием между зернами на рабочей поверхности круга и величиной выступания зерен из связки [7].
Выводы
Из всего выше сказанного делаем вывод, что к наиболее перспективным относится оптический метод определения характеристики рабочей поверхности круга. Однако, в связи с отсутствием материальной базы и программного обеспечения, для обработки результата сканирования практическое применение данного метода затруднено. С информативной точки зрения оптическому методу наиболее соответствует метод профилографирования. С помощью данного метода можно оценивать такие изменения на рабочей поверхности как: число зерен на единицу рабочей поверхности, плотность распределения вершин зерен, высоту рабочего слоя, состояние вершин алмазных зерен. Поэтому устройство для автоматизированного контроля рабочей поверхности алмазного шлифовального круга мы будем делать на основе этого метода.
При написании данного реферата магистерская работа еще не завершена. Окончательное завершение: июнь 2021 года. Полный текст работы и материалы по теме могут быть получены у автора или его руководителя после указанной даты.
Список источников
- Маслов Е.Н./Теория шлифования материалов-Москва: Машиностроение, 1974-320 с.
- Авторское свидетельство №444632. СССР. Способ бесконтактного измерения вибраций шлифовального круга/ Болотов Б.Е., Трубников В. В. – №1897640/258; заяв. 28.03.73; опуб. 30.09.75.
- Авторское свидетельство №448366. СССР. Фотоэлектрическое устройство для бесконтактного измерения степени износа рабочего инструмента/ Ронталь Г.Д., Ивашев Ф. Д., Френкель Ш.Т., Вогман Г.А. - №1696795/25-28 ; заяв. 17.09.71; опуб. 30.10.74, Бюль. №40.
- Авторское свидетельство №236026. СССР. Способ бесконтактного измерения степени износа алмазых шлифовальных кругов / Мамедов Д.М., Лятифов Ф. Д., Тренин А.П., Садыхов А.И. - №1053461/25-8 ; заяв. 14.11.66 ; опуб. 24.01.69, Бюль. №6.
- Toenshoff, H. K., Karpuschewski, B., Werner,F., 1993, Fast Sensor System for Diagnosis of Grinding Wheel and Workpiece, 5th Intern. Grinding Conf., Cincinatti, Ohio, USA.
- Toenshoff, H. K., Karpuschewski, B., Hinkenhuis, H.: Regent, C.,1997, Potentiale der Uberwachung und Regelung von Schleifprozessen. VDS-Fachtagung Schleif-technik im Wettbewerb., 09.-10. Oct., Aachen.
- Гусев В.В., Молчанов А.Д. К определению микрогеометрии рабочей поверхности шлифовального круга в статике // Вісник Харківського державного технічного університету сільського господарства. Випуск 10. «ПІДВИЩЕННЯ НАДІЙНОСТІ ВІДНОВЛЮЕМИХ ДЕТАЛЕЙ МАШИН. ФІЗИЧНІ ТА КОМПЬЮТЕРНІ ТЕХНОЛОГІЇ»-Харків:ХДТУСГ.-2002.-С.379-384.