Реферат по теме выпускной работы
Содержание
- Введение
- 1 Технологический процесс как объект автоматизации. Цель проектирования и требования к разрабатываемому устройству автоматизации
- 2 Критический обзор существующих решений и выбор базовой аппаратуры автоматизации
- 3 Обоснование направления автоматизации технологической установки
- 4 Разработка структурной и функциональной схем устройства автоматизации
- Выводы
- Список источников
Введение
Содержание
- Введение
- 1 Технологический процесс как объект автоматизации. Цель проектирования и требования к разрабатываемому устройству автоматизации
- 2 Критический обзор существующих решений и выбор базовой аппаратуры автоматизации
- 3 Обоснование направления автоматизации технологической установки
- 4 Разработка структурной и функциональной схем устройства автоматизации
- Выводы
- Список источников
Введение
Шахта является сложным многофункциональным предприятием, к основным технологическим процессам которого относятся добыча и транспортировка полезного ископаемого. Работа других машин и механизмов, не задействованных непосредственно в этих процессах, относится к вспомогательным и служит для обеспечения надежного, производительного и безаварийного функционирования всего предприятия.
К таким вспомогательным процессам горного предприятия относится и процесс обеспечения шахтных потребителей теплотой на отопление, вентиляцию, горячее водоснабжение и проветривание горных выработок. От его надежной работы зависит безопасность и возможность работы всего предприятия, поскольку воздух подаваемый в шахту не должен иметь температуру ниже +20 С во избежание обмерзания стволов. Также требуется выполнять и санитарно–гигиенические требования. Именно поэтому устойчивая, и экономичная работа котельных установок шахты – чрезвычайно важна.
Повышать надежность и эффективность котельных установок возможно как путем замены устаревшего котельного оборудования на более современное, с большим КПД, с меньшими требованиями к качеству топлива, а также путем внедрения системы автоматического управления их работой и защиты от аварийных состояний и опасностей. В научном проекте предлагается перейти от устаревших слоевых топок на технологию НТКС, которая позволит эксплуатировать низкосортное топливо, внедрить комплексную автоматизацию технологических процессов по всей шахте, в том числе и автоматизацию котельной установки с принимаемыми топками НТКС.
Таким образом, значительно повысится экономичность работы предприятия, появится возможность сжигать некондиционное топливо, и оперативно обеспечивать тепловые нужды шахтных абонентов. Следовательно, тема магистерской диссертации – разработка системы автоматического управления котельной установкой шахты – чрезвычайно актуальна.
1.Технологический процесс как объект автоматизации. Цель проектирования и требования к разрабатываемому устройству автоматизации
Характеристика котельной установки шахты, тепловых сетей и потребителей
В настоящее время для теплоснабжения объектов основной промплощадки шахты установлены три котлоагрегата ДКВР –10–13, один ДКВР – 20–13 и два КЕ –25–14. Котлоагрегаты №1 (ДКВР –10), №4 (КЕ–25) и №6 (КЕ–25 – не рабочий, отсутствует) паровые №2,3 (ДКВР–10) и №5 (ДКВР – 20) водяные.
В котельной котлоагрегат КЕ–25–14 №6 с 2004 года находиться в ремонте, который из–за отсутствия финансирования до настоящего времени не выполнен. Котлоагрегат КЕ–25–14 №4 и остальные также требуют, проведения технического диагностирования и соответствующего ремонта.
Котлоагрегаты укомплектованы механическими топками и забрасывателиями. Для использования тепла выходящих дымовых газовов паровые котлы оборудован экономайзером. Стабилизация процессов горения осуществляется дутьевыми вентиляторами.
Температура питательной воды 80 оC. Обескислораживание питательной воды осуществляется в деаэрационной установке ДСА, емкость 50м3. Каждый котел оборудован дымососом. Дымовые трубы кирпичные.
Кроме того в котельной установлены следующие группы насосов:
–подпиточные К45/55 (3 шт.) и НСВ60/40 (1шт);
–солевой К20 (1шт.) N–11квт, n–1500 об/мин;
–конденсатные К20 (1шт);
–сетевые Д320/50 (2шт.) N–75квт, n–1500 об/мин;
–питательные ЦНСГ60/132 n–3000 об/мин и ЦНСГ38/132 n–1500об/мин.
Техническая характеристика котельного оборудования сведена в таблице 1.
Таблица 1 – Техническая характеристика котельного оборудования шахты Лидиевка
.
№ п/п | Наименование | ДКВР 10/13с паровой | ДКВР 10/13с водогрейный | ДКВР 10/13с водогрейный | КЕ 25/14с паровой | ДКВР 20/13с водогрейный | КЕ 25/14с паровой (не рабочий) |
---|---|---|---|---|---|---|---|
1 | 2 | 3 | 4 | 5 | 6 | ||
1 | Номинальная произодительность, т/ч | 10 | 10 | 10 | 25 | 20 | 25 |
2 | Давление пара, Мпа (кгс/см2) | 1.3(13) | 1.3(13) | 1.3(13) | 1.4(14) | 1.3(13) | 1.4(14) |
3 | Температура пара, оC | Насыщенный 194 | Насыщенный 194 | Насыщенный 194 | |||
4 | Температура питательной воды, оC | 80 | 80 | 80 | 80 | 80 | 80 |
5 | Поверхность нагрева, м3: | ||||||
радиационная | 47.9 | 47.9 | 47.9 | 97 | 51.3 | 97 | |
конвективная | 179 | 179 | 179 | 407 | 357.4 | 407 | |
общая котла | 206,9 | 206,9 | 206,9 | 498 | 408,7 | 498 | |
6 | Объем, м3: | ||||||
паровой | 2.63 | 2.63 | 2.63 | 15.8 | 1.84 | 15.8 | |
водяной | 9.11 | 9.11 | 9.11 | 4.21 | 10.6 | 4.21 | |
7 | КПД, % | 83,5 | 83,5 | 83,5 | 83,5 | 87.9 | 83.6 |
8 | Комплектность поставки: | ||||||
Топка | ТЛЗМ | ТЛЗМ | РПК | ТЧЗМ 2.7/5,6 | ТЧЗМ | ТЧЗМ 2–2,7х5,6 | |
Забрасыватель | ЗП–600 (2шт) | ЗП–600 (2шт) | ЗП–600 (2шт) | ЗП–600 (2шт) | ЗП–600 (2шт) | ЗП–600 (2шт) | |
Экономайзер | ЭБ1–300 | – | – | ЭП–330 | – | ЭП1–646 | |
Дымосос | Дн–12,5 N–75квт n–1500 об/мин | Д–12,5 N–75квт n–1500 об/мин | Д–12,5 N–75квт n–1500 об/мин | ДН–17у N–132квт n–1500 об/мин | Д–17у N–110квт n–1500 об/мин | Дн–15 N–75квт n–980 об/мин | |
Вентилятор дутьевой | ВДн–10 N–11квт n–1500 об/мин | ВДн–10 N–11квт n–1500 об/мин | ВДн–10 N–11квт n–1500 об/мин | ВДн–12,5 N–75квт n–1500 об/мин | ВДн–12,5 N–55квт n–1000 об/мин | ВДн–12,5 N–40квт n–980 об/мин | |
Золоуловитель | БЦ–2–5х(4+2) | БЦ–2–5х(4+2) | БЦ–2–5х(4+2) | БЦ–2х6х7 | БЦ–2–7х(5+3) | БЦ–2–7х(5+3) |
Приготовление регенерационного раствора осуществляется в солерастворителе С–1,0–1,0 диаметром 1000мм. В котельной установлены один солерастворитель и солевой бак емкость 16 т.
Очистка уходящих дымовых газов от каждого котла осуществляется в блоке батарейных циклов тип БЦ.
В котельной используется вода питьевого качества из городского водопровода. Расход воды на подпитку котлов составляет 31394м3/год.
Общая жесткость исходной воды – 7,0 мгэкв/кг
1–я ступень очистки – 0,2–0,5 мгэкв/кг
2–я ступень очистки – 0.01–0.02 мгэкв/кг
Фильтрующий материал – сульфоуголь. Расход соли 4т/месяц.
Топливом для котельной служит уголь шахты им. Челюскинцев
марки Д
и ДГ
с зольностью 48,6%, влагой 10,9%, выходом летучих 44%, с низшей теплотой сгорания 3557 ккал/час отбираемый после сортировки на техкомплексе.
Расход топлива в год по котельной составляет 14380 т/год.
Котельная вырабатывает пар, перегретую воду и горячую воду.
Количество вырабатываемого тепла составляет 27259,4 Гкал/год.
На шахте Лидиевка
пар используется на приготовление горячей воды для бань, отопления зданий и сооружений, и для прачечной. Горячая вода служит теплоносителем для калориферной на клетевом стволе и отоплением здания АБК–2.
Температура теплоносителя воды 60–35 оC. Давление пара 0,8–1 кгс/см2.
Паропровод d=200мм от котельной к тепловому пункту шахты Лидиевка
, расположенному в центральной части подвала здания АБК–1, проложен по воздуху под породными галереями, передающими породу от техкомлексов шахт к погрузочному пункту в автосамосвалы. Трубопровод возврата конденсата d–100мм. был проложен внутри породных галерей.
Теплоносителем системы отопления здания АБК является горячая вода, поступающая от котельной по трубопроводам диаметром 200мм (подающий и обратный) длиной 800м проложенным по воздуху на опорах разной высоты вдоль железнодорожного пути совместно с трубопроводами диаметром 300м питающими калориферную клетьевого ствола. Резервирующий подающий трубопровод к калориферной не предусмотрен.
Тепловой пункт АБК–1 расположен в подвальной части здания в блоке с помещениями насосной хозяйственно–бытового и противопожарного водоснабжения. В тепловом пункте размещены пять пароводяных подогревателей, бак горячей воды для бани емкостью 25м3, два бака для сбора конденсата емкостью по 9м3, три сетевых насоса подачи горячей воды для бани, два циркуляционных насоса марки К 45/55 системы отопления здания, два насоса ЦНСГ 60/90 для возврата конденсата в котельную, паровая гребенка, коммутационные трубопроводы с задвижками. Приборы контроля и учета прокачки отсутствуют. Часть пароводяных подогревателей находится в неработающем состоянии.
По резервному варианту (в зависимости от режима работы котельной) горячая вода для отопления АБК–1 может вырабатываться в пароводяном подогревателе. ПП1–53–7–10 получающим пар от котельной по трубопроводу диаметром 200мм длиной 850м проложенному по воздуху под галереями передающими породу от шахты к погрузочному комплексу. Конденсат после подогревателей собирается в конденсатных баках. По проекту конденсат из баков теплового пункта насосами ЦНС 60/90 должен возвращаться в конденсатных бак котельной по трубопроводу диаметром 100мм, проложенному по вышеуказанным породным галереям. Температура конденсата в баках теплового пункта составляет 70–80 оC.
В связи с эпизодической работой насоса возврата конденсата (откачивает конденсат из баков за 10минут) и наличием на трубопроводе возврата сифонов (ломанный по вертикали профиль), при сильных морозах вода в сифонах успевала замерзнуть, что приводило к порывам трубопровода. В настоящее время трубопровод возврата конденсата находится в полуразобранном состоянии. Возврат конденсата отсутствует. Конденсат из баков используется для пополнения (примешивания) бака приготовления горячей воды для бани.
Отопление и вентиляция
На основной промплощадке расположены следующие отапливаемые здания: здания АБК и АБК–1, мехцех, стройцех, мастерские, столовая и другие объекты поверхностного комплекса.
Теплоносителем для системы отопления и вентиляции служит вода с фактическими параметрами 60–35 оC и пар давлением 0,8–1 кгс/см2. В качестве нагревательных приборов в системе отопления используются радиаторы и регистры из гладких труб.
В бытовом комбинате находятся респираторная, прачечна, сушилка, душевые. Списочный состав трудящихся шахты 217 человек. Шахта работает в 2 смены.
Прачечная оборудована тремя центрифугами, стиральными машинами МСТ 503(1шт), КП–219(1шт),КП–122(1шт), швейной машинкой и сушильным барабаном КП–306 (1шт–не рабочий).
В максимальную смену стирается 180 кг сухого белья, в сутки 500кг.
Количество смен работы прачечной –2 смены.
Респираторная оборудована сушильной камерой, пылесосом, бытовой стиральной машиной. Обработка респираторов происходит вручную после каждой смены раствором хлорамина.
Сушилка для спецодежды оборудована регистрами с электротенами.
В душевых установлено 100 душевых сеток.
Системы отопления зданий находится в удовлетворительном состоянии.
В столовой приготовление пищи реализуемой в обеденном зале составляет 100 условных блюд в максимальную смену.
Тепловые сети
Тепловые сети на основной промплощадке шахты в основном проложены на высоких и низких опорах по стенам зданий. Участок от АБК к столовой – подземно. Паропровод проложен по воздуху под галереями передающим породу от шахты к погрузочному пункту.
Трубопроводы изолированы минераловатными изделиями с покровным слоем из рубероида. На многих участках трубопроводов изоляция разрушена.
Компенсации температурных удлинений предусмотрены за счет П–образных компенсаторов и углов поворота трассы.
Как видим на данный момент котлогарегаты шахты оборудованы слоевыми низкопроизводительными топками. В рамках модернизации котельного оборудования предприятия рекомендуется заменить их на более экономичные и удобные в плане комплексной автоматизации топки НТКС, которое позволят не только автоматизировать процесс получения теплоносителя, но и сжигать низкосортное некондиционное топливо, добываемое шахтой.
Технология сжигания твердого топлива в топках НТКС
Прежде всего необходимо определить, почему шахтные котельные рационально оборудовать топками именно такого типа. Последние годы качество добытого угля значительно снизилась, что привело к снижению его рыночная стоимости. Также часто оказывается, что затраты на транспортировку топлива могут превышать его стоимость. В таком случае нерационально использовать низкосортное топливо далеко от шахты или направлять его на углеобогатительный комбинат. Таким образом, самым экономичным вариантом являются расходы низкосортного топлива на внутренние нужды шахты. А максимальную теплоотдачу при сжигании такого топлива можно получить только от топок НТКС, которые позволяют сжигать уголь с содержанием пепла более 70%. Именно поэтому рационально оборудовать топками данного типа именно шахтные котельные.
Топливо в топках НТКС сжигается в псевдоожиженом слое, что способствует существенному улучшению доступа кислорода к топливу в процессе горения, и как следствие интенсификации горения и теплоотдачи к поверхностям нагрева, а также более полному сгоранию топлива. Данные факторы позволяют уменьшить объём топочного пространства, а следовательно и металлоёмкость котлов, способствуют экономии 1–5% топлива.
Псевдоожиженый (кипящий) слой представляет собой совокупность полидисперсных частиц, через которые продувается ожижающий воздух с определённой скоростью, достаточной для ожижения и не превышающей скорость уноса частиц топлива из топки. При этом частицы топлива находятся во взвешенном состоянии и интенсивно перемешиваются по объёму топки, благодаря чему улучшается поступление воздуха ко всем частицам топлива и интенсифицируется процесс горения[1].
Схема, поясняющая работу топки низкотемпературного кипящего слоя, представлена на рисунке 1.
Дутьевой воздух для ожижения слоя подаётся в топку через воздухораспределительную решётку при помощи высоконапорного дутьевого вентилятора ВМЦ–6 со скоростью достаточной для кипения слоя (2,5–4 м/с). Коэффициент избытка воздуха, подаваемого в топку на 1кг угля составляет 1,2–1,6 теоретически необходимого для сгорания топлива.
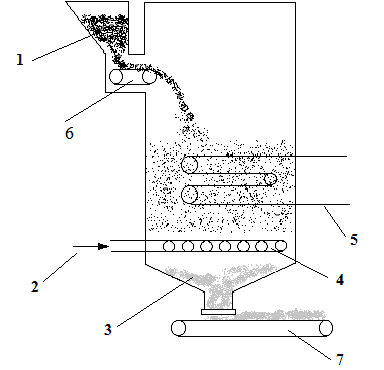
Рисунок 1 – Установка НТКС: 1 – топливо, 2 – ожижающий воздух, 3 – зола, 4 – воздухораспределительная решетка, 5 – погружные поверхности нагрева, 6 – система топливоподачи, 7 – разгрузчик золы
Воздухораспределительная решётка – это основная часть оборудования, обеспечивающего способ сжигания в НТКС. Она обеспечивает равномерное распределение ожижающего агента по всему сечению топки, а также равномерное распределение топлива и удаление золы из слоя.
Воздухораспределительная решётка представляет собой совокупность труб, приваренных к воздухораспределительному коллектору, к которым приварены патрубки с колпачками, имеющими по периметру отверстия, через которые под высоким давлением подаётся воздух в топку.
Топливо в топку подаётся из топливного бункера при помощи забрасывателя барабанного типа ЗП–600. Причём фракционный состав топлива не должен превышать 13 мм, что следует из условий псевдоожижения слоя. Требуемый фракционный состав топлива обеспечивается посредством применения дробилки или узла отсева на стадии топливоподготовки и в угольный бункер поступает топливо с фракцией до 13 мм.
Для бесперебойной и безаварийной работы топок низкотемпературного кипящего слоя (НТКС) большое значение имеет поддержание температуры и высоты слоя, что в процессе сжигания угля обеспечивается своевременностью удаления накапливающейся золы.
Наиболее надёжными и безаварийными в работе оказались разгрузчики качающегося типа, состоящие из стола с отверстием для просыпания золы, кривошипно–шатунного механизма, редуктора и электродвигателя. Практическая реализация низкотемпературного способа сжигания связана с преодолением ряда технических трудностей, наиболее значительными из которых являются необходимость предотвращения шлакования слоя и повышенные требования к топливоподготовке (диаметр частиц топлива должен быть 6 – 13 мм).
Наиболее целесообразно обеспечить температуру слоя, равной 800–850 С. Температуры близкие к 800 С определяются наиболее оптимальными условиями связывания оксидов серы, выделяющимися из топлива в процессе горения, доломитом и известняком, а также щелочноземельными металлами, содержащимися в золе топлива. При этих температурах снижаются и выбросы оксида азота.
Удаление шлака из топок с НТКС не вызывает затруднений, так как кусочки шлака, вследствие их большой плотности, тонут в кипящем слое и собираются в нижней части топки. Шлакоудаляющие устройства должны обеспечить необходимую герметичность.
Основным условием надёжной работы топки с НТКС является равномерное распределение воздуха по всей площади топки. Это достигается установкой воздухоподающих колпачков с 6–8 отверстиями для прохода воздуха, скорость которого при прохождении слоя (зеркала горения) составляет 0,5 – 4 м/с. Конструкция колпачка должна исключать попадания шлака или топлива в воздухоподающие каналы при прекращении подачи воздуха. В топки с НТКС воздух должен в зависимости от высоты слоя поступать под давлением 3–10 кПа.
Для достижения такого давления применяются высоконапорные вентиляторы, например, ВМЦ 6. Коэффициент избытка воздуха, подаваемого в топку на 1 кг угля несколько выше, чем для слоевых топок, и составляет 1,2–1,6 теоретически необходимого.
В связи с тем, что размер кусков топлива, подаваемых в топку не превышает 13мм, а скорости воздуха в слое повышенные, много мелких частиц несгоревшего топлива уносятся с дымовыми газами в газоочистку, где они улавливаются и возвращаются в топку на дожигание [1].
Сжигание топлива в низкотемпературном кипящем слое обладает рядом преимуществ по сравнению с традиционным слоевым сжиганием топлива. Наиболее существенные преимущества:
– в низкотемпературном кипящем слое можно сжигать низкореакционные и высокозольные угли с зольностью до 75–80%, что недостижимо при других способах сжигания. Это обусловлено стабилизацией процесса горения топлива из–за наличия в слое большого количества нагретых до 800–950оC твёрдых частиц с высокой удельной теплоёмкостью;
– упрощается конструкция топочных устройств и возможность их механизации и автоматизации;
– повышается КПД котлов при сжигании низкосортных и высокозольных углей;
– улучшается условия труда обслуживающего персонала за счет возможности автоматизации процесса сжигания, поддержание температуры горения топлива ниже начала размягчения золы, обеспечивающей бесконгроментарное его сжигание;
– достигается высвобождение обслуживающего персонала на жаротрубных котлах устаревшей конструкции.
Рассмотрим цели и задачи магистерской диссертации.
При работе котлоагрегата, оборудованного топкой низко–температурного кипящего слоя (НТКС) возможно спекание твердых частиц в слое вследствие повышения температуры выше критической или погасание слоя из–за снижения температуры ниже допустимой границы [1]..
Эти ситуации являются аварийными и влекут за собой значительные простои оборудования, дополнительные затраты рабочих сил и материалов.
Следовательно, важной функцией, обеспечивающей безаварийность работы, является оперативный контроль и прогнозирование параметров объекта по которым можно судить о возможности наступления аварийной ситуации.
Также для обеспечения экономически эффективной работы котлоагрегта необходимо регулировать его производительность в зависимости от фактического теплового спроса, что приводит к снижению затрат топлива.
Таким образом, целью научной работы является повышение эффективности и безопасности работы котлогрегата путем комплексной автоматизации его работы.
Разрабатываемая система должна удовлетворять следующим требованиям:
–контролировать в оперативном режиме основные технологические параметры котлоагрегата;
–регулировать его производительность согласно полученного задания;
–иметь соответствующую сигнализацию, а также внешние устройства связи с оператором;
–быть конструктивно реализовано на микропроцессорном блоке;
–иметь соответствующую защиту от попадания влаги и пыли, а также климатическое исполнение.
2. Критический обзор существующих решений и выбор базовой аппаратуры автоматизации
В промышленной практике на данный момент при эксплуатации котельных НТКС пользуются приборами системы "Контур" [8]., принцип работы которой подробно рассмотрен ниже.
Система автоматического регулирования процесса горения оборудована приборами системы Контур
, обеспечивающих регулирование подачи твердого топлива в топку в зависимости от нагрузки котла с корректировкой по температуре в кипящем слое, поддержание оптимального соотношение топлива и воздуха, поддержание необходимого устойчивого разрежения в топке. Рассмотрим ниже подробнее его работу.
Контур регулирования Топливо
(См. Рис. 2.2) содержит датчик (манометр 56), регулятор (5в) и пусковую аппаратуры (NS / KM11) для управления однооборотный электродвигателем механизма регулирования топливоподачи (5д – исполнительный механизм).
Автоматическая регулировка подачи топлива в топку производится по сигналам от датчика давления пара (в случае парового котла), представляющая собой электрический манометр РТ / 56 с дистанционной передачей сигнала (показаний) Регулятору РСК / 5в. Манометр преобразует давление пара, подводимого от барабана парового котла, в электрический сигнал переменного тока.
Контур регулирования Воздух
состоит из датчика (манометра 216), регулятора (21в), пусковой аппаратуры (NS / KM12) для управления однооборотный электродвигателем (21д) механизма поворота направляющего аппарата в трубе, подводящей дутьевого вентилятора.
Корректирующий сигнал на регуляторы 5в и двадцать первого поступает от корректирующего устройства 5д (дифзвено), что получает, в свою очередь, сигнал от датчика 5а (термопара). Корректирующее звено выполняет роль обратной связи.
Регулятор Разрежение
176 обеспечивает поддержание постоянного разрежения с высокой точностью. Импульс разрежения берется в верхней части топки датчиком (тягомеры) 17а, преобразующий разрежения в электрический сигнал, поступающий на регулятор 176. С регулятора сигнал поступает на пусковые аппаратуры (NS / KM13) управления однооборотный электродвигателем исполнительного механизма 17д поворота направляющего аппарата, установленного в трубе, подводящей дымососа. При изменении разрежения в топке на величину, превышающую нечувствительность усилителя регулятора, электродвигатель исполнительного механизма 17д перемещает направляющий аппарат дымососа, пока не восстановит заданное разрежение.
Регулировка Уровень воды
осуществляется регулятором 25а, что получает импульс от датчика уровня 256 и воздействует на исполнительный механизм 25д, что сочлененный с управляемой задвижкой .на трубопроводе питательной воды. Датчиком уровня служит манометр 256, подключен к барабану через уравнительную емкость 25а.
Схеме автоматизации осуществляется теплотехнический контроль (См. Рис. 2.2): температуры розжига котла (2а, 26), температуры кипящего слоя (по, 36), температуры уходящих газов (1а, 16), давлением воздуха после дутьевого вентилятора (9), давления пара (11 ), давления жидкого топлива в подводящий и напорном патрубках топливного насоса (12, 13), разрежение в топке котла (18), разрежения перед дымососом (20), уровня воды в барабане котла (246), уровня топлива в бункере (26а) , температуры воды до и по контуру охлаждения (6а, 8а), давления воды по контуру охлаждения (15, 16), расходы воды через контур охлаждения (22а, 226, 22в), сопротивления кипящего слоя (31а). Схема защиты обеспечивает автоматическое прекращение подачи топлива при возникновении аварийных режимов, повышении температуры в кипящем слое, повышении давления дутьевого воздуха, уменьшении разрежения в топке котла, отклонение уровня воды в барабане котла, повышении температуры воды по контуру охлаждения, отклонении давления воды по контуру охлаждения, снижение расходы воды через контур охлаждения.
Схема предусматривает запоминание причины аварии. Аварийный останов котла сопровождается светозвуковой сигнализацией.
Структурная схема регулирования параметров котла оборудованного топкой НТКС с регуляторами Р–25 приведена на рисунке 3.
Каждый контур регулирования содержит регулирующий прибор Р25. Приборы регулирующие Р25 предназначены для применения в схемах автоматического регулирования и управления различными теплотехническими приборами, которые выполняют следующие функции:
–суммирование сигналов от источников информации (датчиков первичных приборов), введение сигнала задания и усиления сигнала отклонения;
–формирование ПИ–закона регулирования совместно с исполнительным механизмом постоянной скорости (совместно с дифференциатором формирование ПИД–закона регулирования);
–формирование сигналов постоянного и переменного тока для управления исполнительным механизмом;
–ручное управление исполнительным механизмом;
–преобразование сигнала от дифференциально–трансформаторного датчика положения исполнительного механизма в сигнал постоянного тока.
Выходные цепи приборов позволяют управлять различной коммутационной аппаратурой сигналами 24 В постоянного тока или 220 В переменного тока, а также управлять исполнительными механизмами, снабжёнными электродвигателями с симметричными обмотками МЭО–73.
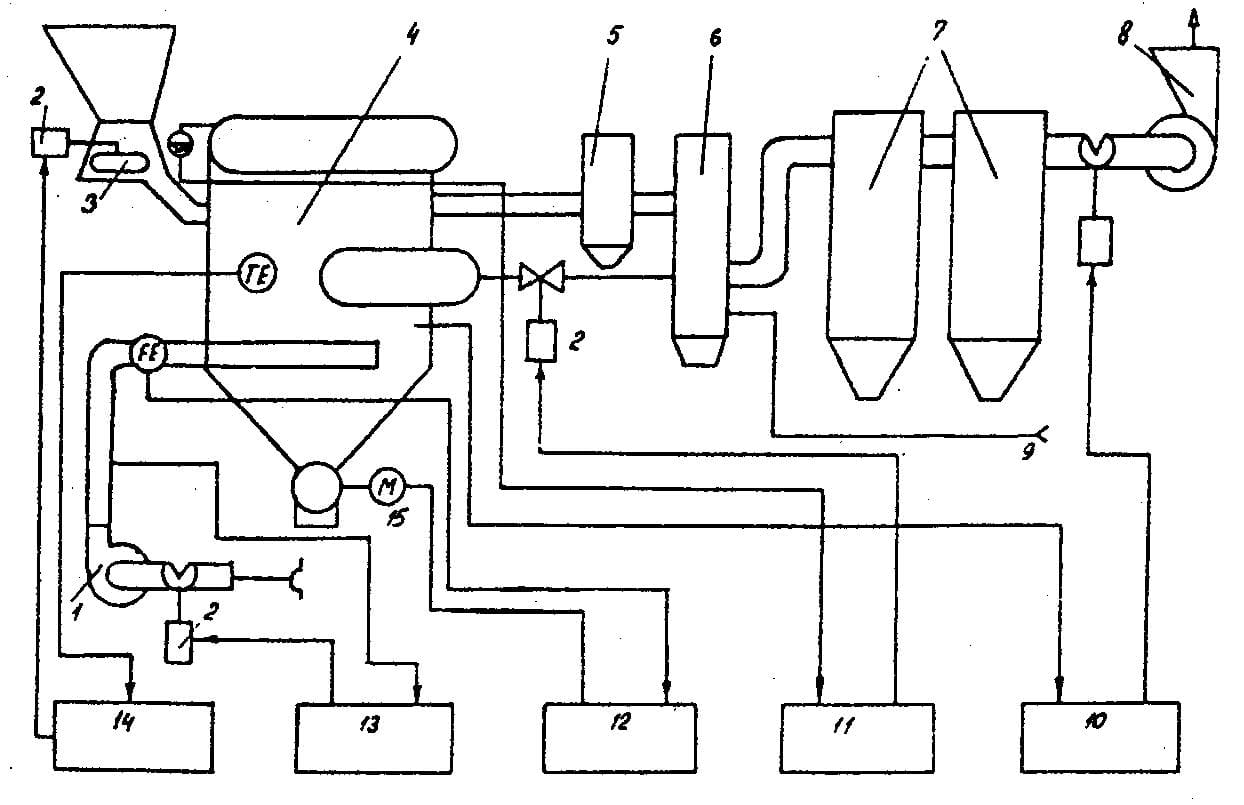
Рисунок 3 – Структурная схема регулирования параметров котла оборудованного топкой НТКС: 1 – дутьевой вентилятор, 2 – исполнительный механизм МЭО; 3 – забрасыватель топлива; 4 – котёл; 5 – прямоточный циклон (циклон возврата уноса); 6 – экономайзер; 7 – циклоны первой и второй ступени очистки дымовых газов; 8 – дымосос; 9 – подпиточный трубопровод; 10,11,12,13,14 – регуляторы соответственно разрежения, уровня, выпуска шлака, расхода воздуха и топлив
Основная проблема существующей системы автоматизации состоит в том, что хоть регуляторы и удерживают параметры в заданных пределах, но они не связаны между собой. Следовательно, можно сделать вывод – регу–лирование параметров может быть не оптимальным (связующее звено между контурами регулирования – человек).
Однако, как следует из описания схемы, регулирования технологических параметров осуществляется по нескольким разомкнутым контурам, без учета состояния других показателей. Так что, невозможно достичь высокого качества регулирования технологического процесса, оперативно и экономично обеспечить требуемую производительность.
На основе опыта работы системы "Контур" при дальнейшем проектировании целесообразно будет заменить регуляторы расхода дутьевого воздуха и температуры слоя на одно микропроцессорное устройство. Контуры стабилизации разрежения над топкой и высоты НТКС целесообразно и экономично оставить на базе системы КОНТУР
, так же как и технологические датчики и исполнительные механизмы технологических устройств.
Для измерения разрежения дымососа используется дифтягомер типа ДТ2–50. Вторичный преобразователь типа КСДЗ работает по дифтрансформаторной схеме с выходным напряжением 0…0,5 В переменного тока.
Расход воздуха в топку измеряется дифманометром типа ДМ3583М. Максимальный уровень сигнала вторичного преобразователя 0,5 В переменного тока. Перепад давления в слое и над слоем, для контроля высоты слоя, измеряется дифманометром типа ДМ3583М с вторичным преобразователем, аналогичным датчику расхода воздуха.
Температура КС измеряется термоэлектрическим преобразователем типа ТХА 706–02 [3] с чувствительностью 30 мkВ/оC и инерционностью установления показаний 60 секунд.
Температура теплоносителя измеряется термоэлектрическим преобразователем типа ТХК–0515 [3] с чувствительностью 24 мkВ/оC и инерционностью установления показателей 60 секунд.
3. Обоснование направления автоматизации технологической установки
Анализ состояния вопроса показал, что на данный момент не существует эффективной системы комплексного автоматического управления производительностью шахтной котельной установки, что позволило бы повысить ее технико–экономические показатели.
Рассмотрим ниже методы управления производительностью котлоагрегата НТКС.
Простейший метод регулирования тепловой нагрузки котла – за счет изменения подачи топлива в слой с последующим изменением температуры слоя НТКС и соответственно измерением теплоотдачи к поверхностям нагрева в котлах. Применение данного метода, однако, ограничено узким диапазоном рабочих температур НТКС. При снижении температуры НТКС ниже 700 оC резко понижается степень выгорания топлива и интенсивность горения, при температуревыше 950 оC возникает угроза шлакования топки. Поэтому степень регулирования по данному методу существенно зависит от температуры тепловоспринимающей поверхности. В водогрейных котлах низкого давления температуры поверхностей нагрева ~950 оC и изменение температуры слоя в области 7000-950 оC ведет к регулированию теплового потока на 20%. Обычно этот способ используется при регулировании тепловой нагрузки котлов малой мощности, используемых в шахтных котельных. Условием применения метода с максимальным КПД является поддержание в топке избытка воздуха, соответствующего минимальному значению тепловых потерь, что не осуществляется при работе существующих в данный момент котлоагрегатов.
Еще один способ — регулирование нагрузки изменением скорости дутьевого воздуха.
Регулирование скорости дутьевого воздуха приводит к соответствующим изменениям порозности и высоты КС, а при частичном погружении трубных пучков в КС – величины погруженной поверхности нагрева. При этом из–за больших значений коэффициентов теплоотдачи слоя существенно изменяется тепловая нагрузка котла. При снижении теплового напряжения и соответствующем уменьшении подачи топлива возможна работа в диапазоне 50–100% номинальной теплопроизводительности. Для надежного регулирования величины теплопроизводительности по данному методу необходимо знание зависимости степени расширения НТКС, расслоения и уноса слоя, а также зависимости теплообменных характеристик и скорости эрозии труб от тепловой нагрузки агрегата.
В ряде малых котлов с топками НТКС реализована система терморегулирования за счет расширения слоя, при которой погруженный трубный пучок отводит около 50% теплоты сгорания топлива. Изменение площади погружных поверхности нагрева при сжигании зольных топлив при вводе в топку серопоглощающих присадок может быть достигнуто за счет изменения массы материала слоя (за счет изменения скорости выгрузки частиц и (или) кратковременного отключения системы ввода присадок). Следует заметить что данный метод применим лишь в котлоагрегатах с погруженными поверхностями нагрева, которые не нашли широкого применения в связи с их повышенным износом из–за абразивных свойств материала слоя.
Учитывая сложность и разносторонность протекающих процессов (необходимость анализа процесса), целесообразно эксплуатацию топок осуществлять в автоматическом режиме. Отсюда приходим к выводу об использовании вместо разрозненных контуров регулирования однокристальной микро–ЭВМ или готовой ЭВМ с устройствами согласования, коммутации, развязки и т. д. К разрабатываемому устройству автоматизации необходимо выдвинуть следующие требования:
–контроль таких технологических параметров: температуры НТКС, расхода твердого топлива, скорости дутьевого воздуха, высоты слоя, разрежения в топке;
– регулирования производительности топки расходу твердого топлива и по скорости дутьевого воздха;
– разработка устройства на базе микропроцессора с обязательным наличием удаленного интерфейса связи;
– визуализация технологического состояния топок КС;
– конструктивное исполнение не ниже IP54, климатическое исполнение УХЛ3.
4. Разработка структурной и функциональной схем устройства автоматизации
На основании разработанного алгоритма работы системы автоматического управления производительностью котла была разработана его структурная схема , представленная на рис. 4..
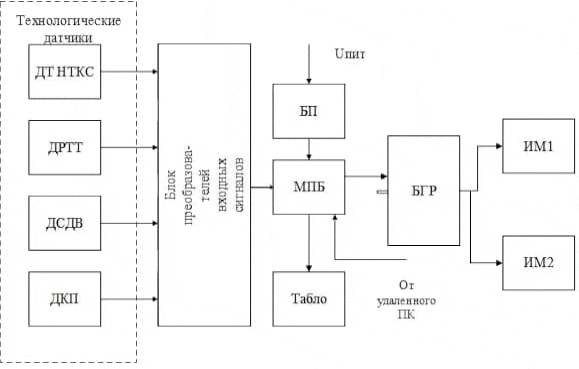
Рисунок 4 – Структурная схема блока автоматизации
(анимация: 9 кадров, задержка 1000 мс, 117 килобайт)
На приведенной схеме приняты следующие обозначения:
– ДТ НТКС – датчик температуры НТКС;
– ДРТТ – датчик расхода твердого топлива;
– ДСДВ – датчик скорости дутьевого воздуха;
– ДКП – датчики концевых положений ИМ для контроля их крайних положений
– МПБ – микропроцессорный блок, который регулирует производительность НТКС согласно полученного задания согласно текущей технологической информации значение температуры НТКС на заданном уровне, регулируя другие технологические параметры. В его состав входят:
– БГР – блок гальванических развязок. преобразует сигналы управления на исполнительные механизмы ИМ дозатора твердого топлива и дутьевого вентилятора согласно командам управления от МК.
– БП – блок питания.
На рисунке 5 приведена функциональная схема устройства автоматизации, работа которой заключается в следующем.
Информационный сигнал от датчика температуры НТКС ВТ (термопару) через усилитель А1 поступает на входной порт микропроцессорного устройства DD1. Аналогично, на другие порты микроконтроллера поступают сигналы от следующих технологических датчиков: BF – датчик расхода твердого топлива (тахогенераторный) через ограничитель ZL, 1ВР – датчика расхода дутьевого воздуха ВР – через выпрямитель UZA1; КА1 и КА2 – датчики крайних положений исполнительных механизмов (концевые выключатели) через ограничитель амплитуды ZL2 и ZL3, соответственно. Также в порт микроконтроллера с головного компьютера (или с клавиатуры оператором) через преобразователь интерфейса DD2 поступает значения уставки.
В соответствии с программным обеспечением микропроцессорное устройство DD1 вырабатывает управляющие сигналы ИМ дозатора твердого топлива и дутьевого вентилятора дутьевого воздуха ИМ1и ИМ2 с помощью семисторных оптронов VU1 и VU2.
Микросхемы DD2 и DD3 предназначены для усиления сигналов интерфейса RS485. Через DD2 происходит дуплексный обмен информацией с внешним компьютером оператора (так называемый высший уровень САУ) сигнал кодовые импульсы поступают к персонального компьютера и от него в режиме дуплексной связи. Через DD2 информация выводится на информационному табло. Местное управление осуществляем с кнопок управления. Дополнительная светодиодная индикация работы схемы управления реализована на свет диодах HL1 ... HL5.
Питается схема от сети напряжением 380 В через источник питания стабилизированного напряжения, который состоит из выпрямителя UZ2, фильтра Z и стабилизатора STU.
Выводы
В результате выполнения исследовательской работы была проанализирована котельная установка шахты как объект автоматизации. Были изложены основные технологические особенности топок фактически применяемых на шахте, и, ввиду их недостатков, в проекте была предложена их замена на более высокопроизводительные и экономичные топками НТКС.
Была сформулирована цель работы, которая заключалась в повышение эффективности функционирования котельной путем ее комплексной автоматизации, а также сформулированы требования к системе автоматического управления.
Приняв за основу эти требования были предложены схемотехнические решения устройства автоматического управления производительностью котла с топкой НТКС по расходу твердого топлива и скорости дутьевого воздуха.
При написании данного реферата магистерская работа еще не завершена. Окончательное завершение: июнь 2021 года. Полный текст работы и материалы по теме могут быть получены у автора или его руководителя после указанной даты
Список источников
- Сжигание угля в кипящем слое и утилизация его отходов/ Ж.В. Вискин и др.–Донецк:Типография "Новый мир", 1997. –284 с.
- Сидельковский Л.Н., Юренев В.Н. Котельные установки промышленных предприятий: Учебник для вузов. – 3–е изд., перераб. – М.:Энергоатомиздат, 1998. – 528 с.: ил.
- Чистяков В.С. Краткий справочник по теплотехническим измерениям. – М.: Энергоатомиздат, 1990. – 320 с
- Гутников В.С. Интегральная электроника в измерительных устройствах.–М.:Энергоатомиздат,1988
- Лавриненко В.Ю. Справочник по полупроводниковым приборам – К.: Техника, 1984
- Голубцов М.С. Микроконтроллера AVR: от простого к сложному. – М.: Cолон–пресс, 2003.
- Интернет–ресурс. http://radio–uchebnik.ru/microbase/
- Батицкий В. А., Куроедов В. И., Рыжков А. А. Автоматизация производственных процессов и АСУ ТП в горной промышленности; Учеб. для техникумов.– М.: Недра, 1991.