Автореферат на тему магистерской работы "Система автоматического регулирования планшетности полосы в процессе проката"
На современном этапе развития прокатного производства основной тенденцией следует считать освоение и внедрение в производство принципиально новой техники и технологии, обеспечивающей наряду с увеличением объема производства- повышения качества листовой стали.
Одним из направлений в области повышения качества листовой стали является улучшение ее планшетности (ровности поверхности).
Наиболее актуальна проблема получения планшетной формы при прокатке полос на широкополостных станах, а также при прокатке тончайших полос, лент, жести, фольги.
Данное исследование носит сугубо учебный характер.
Рис1. Изображение процесса прокатки листа
Этот рисунок анимирован
Весьма важными вопросами при построении таких систем являются получение достоверной информации о планшетности в процессе прокатки, т. е. наличие надежного и простого датчика для контроля планшетности полосы, а также выбор средств (исполнительного органа), с помощью которых возможно наиболее эффективно и однозначно осуществлять корректировку формы полосы.
В связи с этим большое значение приобретают методы и устройства для определения профиля, а также системы регулирования профиля прокатываемых полос на станах горячей и холодной прокатки.
Известны следующие основные методы определения профиля полосы при прокатке:
- посредством измерения толщины полосы по ширине с помощью стационарно установленных либо сканирующих рентгеновских или радиоизотопных толщиномеров (о толщине материала можно судить по интенсивности прошедшего сквозь вещество или обратно рассеянного излучения);
- электромагнитный, основанный на различии величин магнитного потока по ширине непланшетной полосы (основанный на различии величин магнитного потока по ширине пепланшетной полосы, не является наилучшим методом, т.к. как правило, участки полосы, имеющие наибольшее отклонение механических свойств от среднего значения, имели неоднородную микроструктуру);
- механический - путем определения разницы напряжений по ширине, передающихся на измерительный валок;
- пневматический - измерением натяжения в различных точках по ширине полосы с помощью пневмокамер давления;
- оптический - по изменению отражения или фактического изображения профиля и др.
Эти методы реализуются в устройствах для определения профиля полосы (профиледетекторы), а приборы, принцип которых основан на указанных методах, находят применение в системах автоматического регулирования профиля полосы на станах горячей и холодной прокатки.
Основная часть
Причиной отклонения формы листового проката от заданной является различие условий деформации по ширине листов и полос. Различные условия процесса прокатки в поперечном направлении вызывают неравномерность деформаций и скоростей течения металла по ширине полосы
[1].
Согласно данным работы
[2] неплоскостность возникает вследствие неравномерности длин продольных участков полосы, вышедших из очага деформации. Неравномерность длин продольных участков полосы определяется распределением продольных скоростей металла по ширине полосы на входе и выходе из валков, которое зависит в свою очередь от распределения по ширине высотной деформации, натяжения, условий трения, деформации полосы в поперечном направлении. Неравномерность высотной деформации определяется профилем подката и формой межвалковой щели, которая зависит от профилировки, упругого прогиба, неравномерности сплющивания и износа валков.
Неравномерность удельных натяжений по ширине полосы изменяет характер распределения величины критического угла и продольной скорости металла на выходе из валков по ширине. Например, при большем удельном натяжении на середине полосы критический угол и скорость металла на выходе из валков на этом участке увеличиваются, что вызывает смещение центрального участка полосы относительно крайних в направлении прокатки. В связи с этим при равномерном обжатии по ширине полосы происходит образование краевой волнистости перед валками и центральной - за ними.
Прокатка полос с проявлением всех описанных факторов характерна для ШСГП и СХП. При прокатке на (тонко листовых станах)ТЛС влияние натяжения на формирование плоскостности листов отсутствует. В связи с этим преобладающим фактором, определяющим условия получения неплоскостности листов, является неравномерность обжатия по ширине полосы.
На неплоскостность листового проката влияют также размеры листов. С уменьшением толщины и увеличением ширины листа склонность его к потере плоскостности при прочих равных условиях повышается.
Большое число факторов, влияющих на неплоскостность листового проката, и сложность их определения затрудняют расчеты технологических параметров для обеспечения прокатки полос без нарушения плоскостности. Наибольшее распространение для практических расчетов нашло условие плоскостности, которое характеризуется равенством вытяжек по ширине полосы или листа
[3]:
 |
(1) |
где h
0, h
1 - толщина листа у кромки до и после прохода, мм; δ
0, δ
1 - поперечная разнотолщинность листа до и после прохода, мм; μ
0 - средний коэффициент вытяжки по ширине листа, мм.
Исследования показали
[4], что имеется интервал допустимой разности значений коэффициента вытяжки по ширине Δμ
кр, при котором прокатываемые полосы не теряют плоскостности.
Листы и полосы не теряют плоской формы, если
[4]
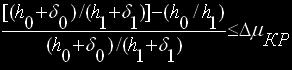 |
(2) |
Условно (2) не зависит от характера потери плоскостности, т. е. оно справедливо при значениях разности коэффициента вытяжки больших нуля (на полосе возникает "короб") и меньших нуля (возникает "волна"). Значение Δμ
кр для тонких листов и полос определяют по формуле
[5]
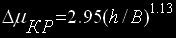 |
(3) |
для толстолистового проката по формуле
[6]
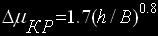 |
(4) |
Следует отметить, что уравнения (1) - (4) не учитывают влияния на плоскостность натяжения и различия в коэффициенте трения по ширине листа при прокатке и пригодны только для приближенных расчетов. Этот недостаток в производственных условиях компенсируют регулированием неплоскостности полос системами регулирования профиля валков и режимов обжатия.
Способы управления поперечным профилем и формой полос в ходе прокатки отличаются по принципу действия, надежности, диапазону и точности регулирования, быстродействию, уровню капитальных затрат на реализацию и эксплуатацию, а также по другим показателям. Наиболее широкое распространение получили: 1) зонное охлаждение бочки рабочих валков; 2) принудительный изгиб рабочих валков в вертикальной плоскости; 3) гидропрофилирование опорных валков; 4) осевая сдвижка рабочих валков; 5) перекрещивание валков; 6) смещение рабочих валков вдоль направления прокатки.
Станочное и тепловое профилирование валков. Изменение поперечного профиля полос путем изменения исходной величины выпуклости (вогнутости) бочки валков на отечественных листопрокатных станах по-прежнему является самым распространенным способом регулирования. Прокатываемые полосы группируют по марочному и размерному признакам и прокатывают с применением различных профилировок рабочих валков. Это, однако, увеличивает необходимый парк рабочих валков, затраты на их подготовку, а также снижает производительность стана из-за дополнительных перевалок.
Корректировку станочного профиля рабочих валков производят либо во время плановых перевалок по мере износа валков, либо при смене типоразмера планируемой партии полос.
Принцип компенсации прогиба валков под действием усилия прокатки лежит также в основе теплового и гидравлического профилирования валков, являющихся, в отличие от станочного, оперативными средствами регулирования. Тепловое профилирование валков, несмотря на инерционность, получило широкое распространение на современных станах холодной прокатки
[1] благодаря возможности регулирования непараболических составляющих поперечного профиля прокатываемых полос и, соответственно, аналогичных составляющих эпюры удельных натяжений. Способ в течение ряда лет достаточно хорошо исследован и используется в системах автоматического регулирования профиля и формы (САРПФ), как правило, в качестве дополнительного канала регулирования.
Регулирование плоскостности полос изменением усилия прокатки. Воздействие на плоскостность полос изменением усилия прокатки основано на изменении упругого прогиба валкового узла. Желаемого эффекта, как правило, достигают изменением либо обжатия, либо натяжения полосы. Данный метод успешно используется при прокатке в непрерывной группе клетей при перераспределении частных обжатий между последней клетью и предыдущими. Применение метода связано с технологическими ограничениями, основным из которых является возможность прокатки нестабильной толщины полосы на выходе из стана. Метод также способствует образованию неплоскостности полос в межклетьевых промежутках, контролировать которую в большинстве случаев невозможно, что увеличивает вероятность порывов полос.
По мере уменьшения толщины прокатываемой продукции возрастает загрузка станов по энергосиловым параметрам, поэтому резервы, а следовательно, и возможности перераспределения обжатий по клетям сужаются.
Принудительный изгиб и гидравлическое профилирование валков. Простота конструктивного исполнения, высокое быстродействие и эффективность систем принудительного изгиба валков определили его широкое применение на отечественных и зарубежных станах совместно со станочным и тепловым профилированием валков. Принцип действия противоизгиба валков также сводится к компенсации прогиба валков под действием усилия прокатки. Этот способ на определенном этапе развития прокатного оборудования помог решить проблему оперативного регулирования плоскостности полос
[7], его применение позволило в 2-3 раза сократить число станочных профилировок при прокатке идентичного сортамента полос. Однако вскоре стало очевидно, что увеличение изгибающего усилия, применявшееся с целью отказа от перевалок валков по ширинным группам прокатываемых полос, приводит к нежелательным последствиям. Системы принудительного изгиба рабочих валков не компенсируют в полной мере изменяющихся условий прокатки полос различных ширин, в результате чего образуется неплоскостность, повышается вероятность обрывов полос. Влияние принудительного изгиба рабочих валков на плоскостность полос, ширина которых составляет 0,65 длины бочки и менее, резко снижается, возникают комбинированные виды неплоскостности, например сочетание центральной и краевой волнистости. Попытки снизить один из видов неплоскостности изгибом валков приводит к усугублению другого. Нежелательные последствия связаны также с повышенным выходом из строя подшипников рабочих валков (в 2-3 раза) , интенсивным износом бочек валков по краям. Увеличение протяженности скосов или врезов на опорных валках позволяет увеличить диапазон регулирования, но обусловливает повышение концентрации межвалковых нагрузок при одновременном увеличении их абсолютной величины, что сокращает продолжительность кампании валков. Несколько улучшить условия контактного взаимодействия валков и одновременно увеличить диапазон регулирования удалось благодаря применению систем изгиба валков парой сил (рис. 2).Это решение, однако, привело к существенному усложнению конструкции валкового узла в целом, снижению допустимого момента, прилагаемого к удлиненным шейкам приводных рабочих валков. Улучшение условий нагружения подшипниковых опор достигается, по-видимому, путем усиления каждой из сдвоенных подушек. Однако для выполнения равного регулирующего воздействия требуются большие усилия, прилагаемые к каждой половине сдвоенной подушки
Рис. 2
Схемы регулирования поперечного профиля и формы полос системами принудительного изгиба валков парой сил:
1-приложение пары сил к сдвоенным подушкам рабочих ваков; 2-автономное приложение пары сил к двум дополнительным подушкам опорных валков
Изгиб рабочих валков в горизонтальной плоскости. Использование данного способа регулирования предполагает установку рабочих валков со смещением по направлению прокатки относительно опорных, а также принудительный изгиб рабочих валков, усилие которого направлено в противоположную сторону. Эффективность способа повышается с уменьшением отношения диаметра валка к длине его бочки. Приращение межвалкового зазора при изгибе рабочих валков в горизонтальной плоскости существенно меньше его прогиба и зависит от диаметра опорного валка, также влияющего на эффективность способа. Отметим, что этот способ не нашел широкого распространения в практике листопрокатного производства.
Известно его применение на 5-валковом стане Тейлора с одним регулируемым рабочим валком малого диаметра и на стане MKW, где рабочие валки изгибаются при помощи роликовых опор.
Гидравлическое профилирование валков. Метод основан на изменении давления рабочей жидкости в полости между осью опорного валка и бандажом, благодаря чему регулируется выпуклость бандажа. Как правило, в клети используют один гидропрофилируемый опорный валок. Возможно применение гидропрофилированных рабочих валков. Метод может быть использован на станах как горячей, так и холодной прокатки. Высокое быстродействие (0,06 мм/с), точность регулирования, а также возможность установки систем на действующих клетях без существенных реконструктивных изменений определяют перспективность гидропрофилирования валков. Известны бандажированные валки, в которых масло закачивается во внутреннюю полость под высоким давлением, и составные валки, которые представляют собой свободно вращающийся вокруг неподвижной оси полый цилиндр, прижимаемый к рабочим валкам гидростатическим давлением жидкости. Разработаны варианты вращающихся и смещаемых в осевом направлении бандажей.
Взаимная ориентация валков. К способам оперативного регулирования относится осевая сдвижка валков, перекрещивание валков, а также смещение рабочих валков относительно опорных вдоль направления прокатки.
Перекрещивание валков. При перекрещивании осей валков в горизонтальной плоскости межвалковый зазор остается неизменным в проекции точки пересечения осей валков и по мере удаления от нее к краям бочек постепенно увеличивается. Поперечный профиль полосы в очаге деформации приобретает "пропеллерообразную" форму. Изменение угла перекрещивания (рис. 2) в процессе прокатки позволяет изменять профиль межвалкового зазора в пределах, ограниченных только величиной возникающих при этом осевых усилий на валках, которые могут достигать 15 % от усилия прокатки и более.
Очевидно, что внедрение этого эффективного способа в широкую практику сдерживает основной его недостаток - большие осевые усилия на перекрещенных валках, для восприятия которых необходимо применение усложненных подшипниковых узлов.
Рис. 3
Принцип действия способа регулирования поперечного профиля полосы перекрещиванием валков:
а-профиль выпуклый, валки соосны; б-профиль прямоугольный, прогиб скомпенсирован; в-профиль вогнутый, угол перекрещивания увеличен
Смещение рабочих валков вдоль плоскости прокатки. Применение смещения рабочих валков относительно опорных вдоль направления прокатки первоначально было вызвано необходимостью снижения их вибраций, устранения перекосов валков путем односторонней выборки зазоров в направлении прокатки между подушками рабочих и направляющими подушек опорных валков или стойками станины. Кроме того, традиционное смещение рабочих валков по ходу прокатки улучшает захват полосы валками. Направление и величина смещения рабочих валков определялись направлением и величиной результирующей горизонтальной составляющей усилия прокатки и разности переднего и заднего натяжения полосы. Поэтому рабочие валки в первой клети непрерывного стана холодной прокатки в последнее время смещают против хода полосы, так как переднее натяжение полосы здесь значительно превосходит заднее. В последующих же клетях рабочие валки смещают по направлению прокатки. В частности в 1-й клети НСХП 2500 Магнитогорского металлургического комбината рабочие валки смещены на 12 мм против хода прокатки, в 1-й клети НСХП 1700 Карагандинского металлургического комбината - на 6 мм. В работе предложено величину смещения a рабочих валков выбирать по зависимости
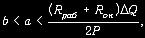 |
(5) |
где b - полуширина площадки сжатия на контакте рабочего валка с опорным; R
раб, R
оп - соответственно радиусы рабочего и опорного валков; ΔQ- разность между передним и задним натяжением полосы при прокатке; Р - усилие прокатки в клети.
При смещении рабочих валков относительно опорных при прокатке возникает горизонтальная составляющая усилия прокатки. Значение этого усилия определяет прогиб рабочих валков в плоскости прокатки. Целенаправленное изменение размера смещения дает возможность регулировать прогиб рабочих валков и соответственно поперечный профиль и форму прокатываемой полосы. Данный принцип регулирования применяется в ряде конструкций 6-валковых клетей типа CVC6-HS, разработанных фирмой "Шлеманн зимаг" и клетей типа ХСС, разработанных в Японии. Значение смещения рабочих валков в клетях типа CVC6-HS составляет 15-20 мм, а интервал регулировки ± 12-15 мм. Усилие, развиваемое исполнительными механизмами, достигает 450-500 кН. Работа системы направлена на создание профиля межвалкового зазора, идентичного поперечному профилю прокатываемой полосы.
Недостатком данного способа регулирования является сравнительно узкий диапазон регулирования, снижение жесткости валкового узла, невозможность уменьшения диаметра рабочего валка без применения дополнительных поддерживающих устройств, повышенные вибрации рабочих валков вследствие изменений переднего и заднего натяжений.
Осевая сдвижка валков. Применительно к клетям кварто существует две основные цели применения способа. Первая заключается в "размытии" износа рабочих валков путем их циклического осевого перемещения и предупреждения образования локальных утолщений профиля прокатываемых полос, что наиболее важно в условиях станов горячей прокатки. Вторая цель состоит в плавном изменении профиля межвалкового зазора при осевом перемещении профилированных рабочих валков (рис. 4). Эта возможность в равной степени представляет интерес для горячей и холодной прокатки. При осевой сдвижке S-образно профилированных валков, имеющих переходящие один в другой выпуклый и вогнутый участки по длине бочки, профиль межвалкового зазора плавно изменяется от выпуклого до вогнутого. Профилировка верхнего валка идентична профилировке нижнего, однако валки развернуты друг относительно друга на 180° так, что между ними образуется симметричный межвалковый зазор. Разница диаметров рабочего валка по длине бочки может составлять 0,3-0,8 мм. Возникающее вследствие этого рассогласование окружных скоростей составляет 0,05-0,2 %. В зависимости от обжатия рассогласование скоростей между валком и прокатываемой полосой составляет 5-40 % для зоны отставания и 0,5-5 % для зоны опережения (такое рассогласование скоростей является незначительным). Сдвижка валков с выпукло-вогнутым профилем может осуществляться как предварительно, так и в процессе прокатки под нагрузкой. Способ является одним из наиболее эффективных по воздействию на поперечный профиль и форму полос в процессе прокатки.
Рис. 4
Схема регулирования поперечного профиля полосы осевой сдвижкой S-образно профилированных валков
а-выпуклый профиль; б-прямоугольный профиль; в-вогнутый профиль
В клетях кварто, в которых длина бочки рабочего валка равна длине бочки опорного, осевая сдвижка цилиндрических рабочих валков изменяет поперечный профиль полосы благодаря изменению схемы нагружения валков - по аналогии с изменением длины краевых скосов на опорных валках. Идентичен механизм воздействия осевой сдвижкой промежуточных валков в многовалковых клетях, например в 6- и 20-валковых. Известны также варианты регулирования утонения кромок прокатываемых полос различных ширин путем позиционирования конусного участка по длине бочки каждого рабочего валка напротив кромок прокатываемой полосы. При этом длина бочки рабочих валков превышает длину бочки опорных валков.
Следует отметить, что при очевидных преимуществах данный способ усложняет профилирование валков, повышает неравномерность нагружения и износ опорных валков, усложняет конструкцию клети, обуславливает увеличение длины бочки валков.
Изменение жесткости валкового узла. Этот способ оперативного регулирования поперечного профиля и формы полос (рис. 5) не имеет единого регулирующего воздействия в отличие от ранее рассмотренных схем. Так, регулирование осевой сдвижкой промежуточных валков в 6-валковых НС-клетях (рис. 5,а) и рабочих валков в 4-валковых K-WRS-клетях можно было бы отнести к осевой сдвижке валков. Однако существенным является то, что регулирование в этих клетях, в отличие от клетей CVC-4 и CVC-6, осуществляется изменением изгибной жесткости валкового узла вдоль длины бочки, а не изменением положения профилированных валков.
Рис. 5
Схемы ризменения жесткости клетей:
а-НС-клеть; б-клеть ВНИИметмаша; в-клеть ИЧМа
Прогиб рабочих валков в многовалковых клетях во многом определяется характером их контакта с опорными (промежуточными) валками на краевых участках длины бочки за пределами ширины полосы (рис. 5,а). Осевая сдвижка промежуточных валков, края которых устанавливают напротив кромок прокатываемых полос, является эффективным способом регулирования поперечного профиля полос. При этом диапазон регулирования плоскостности полос при помощи принудительного изгиба рабочих валков увеличивается в 3-4 раза. Жесткость 6-валкового узла НС-клети снижается прямо пропорционально уменьшению длины межвалкового контакта промежуточных валков при их осевой сдвижке. Однако изгибная жесткость валкового узла повышается благодаря уменьшению длины опорной поверхности промежуточных валков. Таким образом, основными преимуществами НС-клетей по сравнению с клетями кварто являются повышение изгибной жесткости валкового узла, отсутствие необходимости профилирования валков для прокатки полос по ширинным группам. Так, установка в качестве первых двух НС-клетей на 6-клетьевом стане жести позволила увеличить толщину подката на 42,5 % (с 2,3 до 4 мм), а оснащение стана холодной прокатки на заводе фирмы "Син ниппон сейтецу" в г. Хирохата позволило при сохранении сортамента стана снизить число клетей с пяти до четырех. Вместе с тем анализ фактических показателей работы НС-клетей в Японии, ФРГ выявил также ряд их недостатков: сложность конструкции клети, невысокую надежность, низкую стойкость рабочих и опорных валков вследствие повышенных контактных нагрузок, в частности вблизи края бочки промежуточных валков, меньшую жесткость валкового узла вследствие наличия дополнительных межвалковых контактов, а также прогиб рабочих валков меньшего диаметра вдоль направления прокатки.
Клеть ВНИИметмаша (рис. 5,б) содержит рабочие валки, опорные валки с одинаковой длиной бочки и снабжена дополнительными опорными роликами с укороченной (0,3-0,5) длиной бочки. Регулирующее воздействие в клети осуществляется путем вертикальной установки укороченных опорных роликов, обеспечивающих перераспределение усилия прокатки в заданном соотношении между опорами опорных валков и дополнительными опорными роликами, которые позволяют осуществлять регулирование прогиба валков. Разработчики отмечают такие основные преимущества клети ВНИИметмаша по сравнению с клетями кварто: высокая нагрузочная способность благодаря совместному восприятию усилия прокатки опорами опорных валков и опорных роликов, широкие возможности совместного регулирования поперечного профиля и толщины полосы воздействием опорного ролика.
Первоначально клеть была разработана и предназначена для толстолистовых станов с большой длиной бочки (5000 мм), где усилие прокатки велико и его изменение обуславливает высокие требования к жесткости клети. Повышение жесткости клети путем увеличения диаметра и массы опорных валков связано со сложностью в изготовлении, транспортировке и эксплуатации.
В то же время клеть ВНИИметмаша в ее современном конструктивном исполнении имеет ряд недостатков. Так, торцы укороченного опорного ролика, несмотря на достаточно низкое соотношение твердости бочек роликов и валков, оставляют отпечатки на бочках опорных валков, которые, в свою очередь, передаются на рабочие валки. Отсутствие систем компенсации кольцевого износа валков, например, путем их осевой сдвижки, сокращает продолжительность эксплуатации валков. Кроме того, в клетях кварто невозможно использовать дополнительные опорные ролики из-за недостаточного запаса высоты окна станины.
В магистерской работе предполагается проведение исследований использования систем управления профилем проката.
Литература
- Развитие конструкций листовых станов для прокатки полосы точного профиля в СССР и за рубежом. — М., 1976. — 52 с. (Обзорная информ./НИИинформтяжмаш. Сер. Металлургическое оборудование).
- Kabayashi, Yasuda, Makajima//Hitachi Rew. — 1988. — V. 37. — № 4. — P. 213–220.
- Суяров Д.И. Качество тонких стальных листов.-М.:Металлургия, 1964.-171 с.
- Железнов Ю. Д. О неравномерности деформации критической в отношении плосткостности тонкого листа при прокате.-Изв. вузов. Чер. металлургия, 1969. №11, с. 91-96
- Григорян Г. Г. Разработка методик оценки эффективности каналов управления поперечным профилем полос в чистовой группе стана.-Изв. вузов. Чер. металлургия, 1979, №5, с. 138-141
- Соколов В. А. Повышение качества толстых листов на станах штучной прокатки.-Пр-во листа: Темат. отрасль. сб. 1975, №3, с. 72-75
- Герцев А. И., Меерович И. М., Топалер С. М. Машины и агрегаты металлургического производства//Тр. ВНИИметмаш. — 1984. — С. 159–170.