ВСТУП
Актуальність теми
В останні роки
у зв'язку з утворенням і нагромадженням
значної кількості відходів і
необхідністю рішення екологічних проблем
зростає значення їхньої утилізації.
Переважний у сталеплавильному
виробництві киснево-конвертерний процес
розвивається в напрямку матеріало- і
енергозбереження.
До відходів
конвертерного виробництва крім металів
відносяться й неметалічні ресурси:
вторинні вогнетривкі матеріали, шлаки,
шлами й пил. Особливу увагу варто
приділити шламам конвертерного
виробництва, які досліджені менш інших
вторинних ресурсів. Крім цього шлами
конвертерного виробництва відносяться до
таких, що важко утилізуються. Труднощі в
утилізації цих шламів виникають через
підвищений зміст у них кольорових
металів, особливо цинку й свинцю, зміст
яких найчастіше перевищує в дефіцитних
цинковій і свинцевій рудах, яких на
Україні практично немає.
Мета
-
розробити заходи
щодо зниження негативного впливу
відходів конвертерного виробництва
на навколишнє середовище;
-
розробити
ресурсозберігаючу технологію для
конвертерного переділу;
-
удосконалити наявні
схеми підготовки вторинних
матеріальних ресурсів конвертерного
виробництва до утилізації,
забезпечивши тим самим більш повну
утилізацію даних відходів;
-
довести економічну
ефективність від впровадження
ресурсозберігаючих технологій і
використання принципово нових схем
підготовки відходів до утилізації.
Завдання
-
розглянути джерела й
металургійну цінність вторинних
матеріальних відходів конвертерного
виробництва;
-
розглянути процес
утворення відходів виробництва;
-
виявити залежність
кількості відходів, що утворюються,
від виду використовуваних очисних
споруджень і застосовуваної
технології виплавки конвертерної
сталі;
-
сформулювати основні
напрямки підвищення екологічної
безпеки конвертерного
виробництва;
-
оцінити економічний
ефект при переході конвертерного
виробництва на більш досконалу
технологію виробництва сталі й
утилізації відходів;
-
дати комплексну
оцінку розробленої технології
виробництва конвертерної сталі й
утилізації відходів виробництва.
Наукова
новизна роботи полягає в тому, що раніше
розглядались питання, стосовно
утилізації відходів сталеплавильного
виробництва в цілому. Дана робота
розглядає ресурсозберігаючі технології й
способи утилізації відходів
конвертерного виробництва.
Практична
цінність роботи полягає в тому, що
розглянуті технологічні заходи
екологічно й економічно доцільно
впроваджувати на металургійних
підприємствах України, тим самим
підвищуючи екологічну безпеку
конвертерного виробництва.
АНАЛІЗ РЕСУРСОЗБЕРЕЖЕННЯ
Й УДОСКОНАЛЕННЯ ТЕХНОЛОГІЇ УТИЛІЗАЦІЇ
ВТОРИННИХ РЕСУРСІВ КИСНЕВО-КОНВЕРТЕРНОГО
ВИРОБНИЦТВА СТАЛИ НА МЕТАЛУРГІЙНИХ
ПІДПРИЄМСТВАХ УКРАЇНИ
Одним зі
шляхів зниження матеріалоємності
продукції й економії сировинних ресурсів
є підвищення рівня використання відходів
виробництва, які неминуче утворюються як
у сфері матеріального виробництва, так і
в сфері споживання. Виробничий досвід
показує, що використання відходів
конвертерного виробництва технічно
можливе й економічно вигідне.
Незважаючи на
проведену роботу рівень використання
вторинних матеріальних ресурсів ще
недостатньо високий з різних причин, але
в першу чергу через відсутність об'єктів
відповідної підготовки, недостатньо
розроблених технологій, відсутності
систематизованої літератури насамперед
довідкового характеру.
У цей час
основним методом використання шламів
газоочисток конвертерів є добавка їх до
агломераційної шихти.
Для утилізації
на аглофабриці конвертерний шлам повинен
бути попередньо збезводнений. У цей час
найбільш раціональною схемою
зневоднювання є схема, що передбачає
згущення шламової пульпи в радіальних
згущувачах, фільтрування на
вакуум-фільтрах і сушіння в сушильних
барабанах. При наявності на підприємстві
в достатній кількості сухих відходів
(вапно, відсівання агломерату й т.д. )
сушіння можна заміняти змішуванням
шламів із цими відходами.
Схема утилізації
шламів конвертерного виробництва
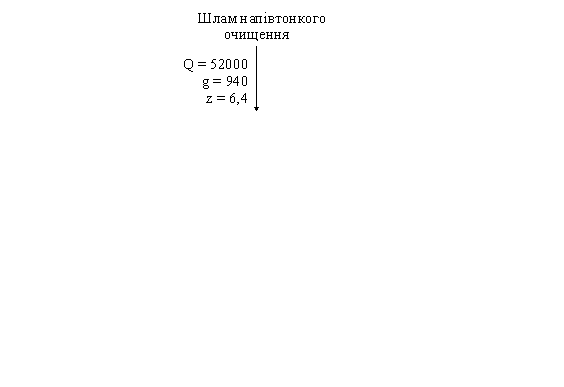
Іноді
конвертерний шлам на аглофабриках
використовується без механічного й
термічного зневоднювання, безпосередньо
у вигляді густої пульпи після згущення
(300-700 г/л) у радіальних згущувачах
або в гідроциклонах і радіальних
згущувачах. Шлам у розпорошеному виді
подається в змішувальний барабан
аглофабрики. Перевага такого способу -
низькі капітальні витрати й
експлуатаційні витрати. Необхідною
умовою успішної експлуатації схем є
надійне автоматичне дозування шламу в
змішувальний барабан залежно від
вологості шихти й щільності згущеного
шламу.
Для повернення
шламу газоочисток у конвертер необхідно
його попереднє ошматовування. Є також
методи ошматовування, розроблені
спеціально для конвертерних шламів.
Ошматовування шламу для конвертерного
виробництва застосовується за наступною
схемою. Стічна вода газоочистки
конвертерного цеху надходить у пастку,
де осаджуються найбільш великі частки.
Перелив пастки попадає через змішувальну
камеру в радіальний згущувач. У
змішувальну камеру також подається
вапняне молоко. Злив радіального
згущувача направляється на повторне
використання в систему газоочистки, а
згущений шлам - на лійку, що харчує
барабанний вакуум-фільтр. Збезводнений
до вологості 28-32 % шлам від
вакуум-фільтра й велика фракція,
уловлена в пастці, стрічковим конвеєром
подаються в живильник обертової
трубчастої печі, де здійснюється сушіння
шламу, його комкування й випал окатишів
при температурі 1150°С.
Обкотиші охолоджуються в
охолоджувальному барабані й
завантажуються в залізничний вагон.
Передбачуваний
обсяг використання шламу конвертерних
газоочисток утилізується як добавка до
агломераційної шихти. Для повернення
шламу в конвертерне виробництво варто
розробити, опираючись на закордонний
досвід, ефективну схему підготовки
шламів, що дозволила б одержати
кондиційний матеріал у вигляді обкотишів
або брикетів. Така схема дозволила б
зняти проблему обезцинкування
конвертерних шламів, для яких дотепер
немає дешевої технології видалення
цинку.
Іншим способом
утилізації залізовмісних пилів і шламів
конвертерного виробництва є включення їх
до складу шихти при виробництві цементу
й інших будівельних матеріалів, а також
ряду фарб, наприклад, охри й барвників.
Пульпу й
збезводнений шлам можуть використовувати
тільки на аглофабриках (або фабриках по
виробництву обкотишів), тому що тільки в
шихту цих виробництв можна подавати
зволожені матеріали. Зокрема, пульпу
можна подавати в змішувальні барабани
цих виробництв. При цьому, оскільки
потреба у волозі на аглофабриці може
перевищувати кількість вологи, що
поступає з пульпою, іноді доводиться
навіть додавати вологу в змішувач. Однак
через збільшення витрат на
транспортування цей метод доцільно
використовувати лише при близькому
розташуванні на території підприємства
сталеплавильного й агломераційного
цехів.
Одним з
перспективних методів підготовки шламів
до утилізації є сушіння розпорошеної
пульпи в потоці (переважно) нагрітих
газів. При випробуванні методу були
отримані гарні результати, однак метод
поки не знайшов впровадження у
виробництво. Цей метод доцільно
сполучити з подачею отриманих при його
використанні густих (пастоподібних)
шламів у змішувачі
(барабани-огрудковувачі) аглофабрик:
шлам з вологовмістом 40 - 50 % (по
масі) розпорошується евольвентними
форсунками, що забезпечує рівномірне
зволоження шихти. Останній шлях
привабливий своєю простотою, однак
виникають утруднення, пов'язані з
дозуванням шламів. З метою підвищення
надійності зазначеного засобу
проводяться ретельне пророблення методу
дозування і обробка вузлів дозувального
апарата.
Останнім
часом у зв'язку з інтенсифікацією
киснево-конвертерного процесу підсилився
винос із агрегату з газами, що
відходять від нього, великих фракцій
пилу. Тому необхідно проводити
класифікацію стічних вод перед їхнім
надходженням на основні спорудження. Для
зневоднювання конвертерних шламів
найбільш широко застосовуються радіальні
відстійники, наприклад, діаметром 30 м,
які при питомому навантаженні 2 м3/(м2·ч)
дозволяють одержати прояснену воду із
залишковим змістом суспензії, що не
перевищує 200 мг/л.
Підготовку
конвертерних шламів до утилізації в
агломераційній шихті доцільно робити
разом з відходами, що містять залізо. У
випадку ж, коли на металургійному
підприємстві є мартенівське й
конвертерне виробництва, найбільш
доцільно робити спільну підготовку їхніх
шламів до утилізації.
Конвертерні
шлаки, з яких навіть порівняно повно
витягнутий метал, містять ряд коштовних
елементів. Їх досить раціонально
використовувати в металургії, наприклад
в аглодоменому і ливарному виробництві,
як флюс замість вапняку.
Зараз у нашій
країні й за кордоном конвертерні шлаки
переробляють переважно у твердому стані.
Їх дроблять, піддають грубому відбору
металу, іноді вдруге дроблять і
сепарують. Широко випробуваного й
впровадженого у виробництво засобу
переробки конвертерних шлаків у рідкому
стані дотепер немає. Тільки на окремих
заводах випробовують напівпромислові або
промислові грануляційні установки.
Залежно від
часу перебування в чашах (з моменту
наповнення до кантування) і обсягу їхні
шлаки можуть надходити на переробку в
рідкому або у твердому стані. Показано,
що навіть через 2 ч після наповнення до
80% розплаву в чаші залишається в
рідкому стані.
Зі
сталеплавильних шлаків для використання
в якості оборотного продукту у
металургійному переділі найбільшу
цікавість представляють шлаки
конвертерного виробництва. Конвертерні
шлаки мають у своєму складі коштовні для
металургійного переділу такі компоненти
як Ca, Mg, Mn, Ca2, Al2O3,
Fe. Крім того, у конвертерному шлаку
поточного виробництва втримується від 3
до 9 % заліза у вигляді "корольків".
Основність
кінцевих конвертерних шлаків перебуває
на рівні 2,8 - 3,5, а вміст СаО у
вапняку і у конвертерному шлаку
перебуває приблизно на одному рівні (46
- 52 %). Це дозволяє використовувати
конвертерні шлаки замість вапняку в
печах і вагранках ливарних цехів.
Як показують
термодинамічні розрахунки, витрати тепла
на дисоціацію вапняку й одержання
шлакового розплаву приблизно в 1,5-1,7
рази більші, ніж при застосуванні
конвертерних шлаків.
Якщо врахувати
ще й те, що вапняк природний матеріал,
запаси якого, в остаточному підсумку,
обмежені, а конвертерні шлаки є відходом
виробництва, перевага його використання
в металургійному переділі замість
вапняку безперечна.
Переробка
конвертерних шлаків поточного
виробництва проводиться на стаціонарній
ділянці шлакопереробки з використанням
засобу термодроблення. Передбачено
окрему переробку рідких шлаків і
ковшових залишків. До технології
первинної переробки конвертерних шлаків
на стаціонарній ділянці відноситься:
-
транспортування шлаків на ділянку;
- злив шлаків
у ями-траншеї;
- пересування
шлаковозів у секцію для вибивки ковшових
залишків і вибивка останніх;
-
термодроблення й охолодження шлаків
водою;
- розробка
остиглих шлаків екскаватором;
- витяг
великогабаритного скрапу;
-
транспортування остиглих шлаків
автотранспортом на дробильно-сортувальну
ділянку.
На стаціонарну
ділянку шлакопереробки направляються
рідкі шлаки тільки з конвертерів. Злив
шлаків з конвертерів відбувається в
чисті, підготовлені чаші без бою цегли,
виробничого сміття, скрапу й інших
відходів. Заповнені шлаками чаші в
максимально короткий термін (щоб
кількість рідких шлаків у чаші до
моменту кантування була не менш 50 %)
надходять на стаціонарну ділянку.
Технологія
термодроблення включає пошарове
заливання рідких шлаків до глибини шару
шлаку 1,5 - 2 м у спеціальні секції,
зрошення водою з витратою 0,1 - 0,15 м3/тч
на 1м2 площі після кантування
кожної порції шлаку. У ямах-секціях
термодроблений шлак розробляється
екскаватором і відвантажується або
безпосередньо в автосамоскиди або
формується в тимчасовий штабель.
Фракційний склад термодробленого шлаку
допускає пряме завантаження шлаків у
доменні печі без додаткового дроблення.
Термодроблений
конвертерний шлак може використовуватися
в шихті доменних печей і вагранок;
грубодроблені ковшові залишки можуть
використовуватися в шихті доменних
печей, а також після дроблення на
ДСУ-200 - в агломераційній шихті
(фракція < 10 мм).
Відвантажується споживачам
термодроблений шлак, по хімічному складі
повинен мати СаО не менш 45 %, SіО2
не більше 20 %, Feзаг не менш
10 %, вологість не більше 7 %. Зміст
сторонніх домішок не повинен
перевищувати 5 %.
Досвід роботи
Єнакіївського металургійного заводу
показує, що в аглошихті можна
використовувати конвертерні шлаки
фракції 0-10 мм із витратою 30-50 кг/т
агломерату без погіршення
техніко-економічних показників роботи
аглофабрики. У доменні печі й вагранки
ливарних цехів відправляються
конвертерні шлаки фракції 10-40 мм. При
використанні конвертерних шлаків у
мартенівських печах замість вапняку за
рахунок більш раннього шлакоутворення
спостерігається більш повне видалення
фосфору в шлаки.
ВИСНОВКИ
Таким чином, з
економічної й екологічної точок зору
використання високоефективних
газоочисних систем з організацією повної
й комплексної утилізації відходів
дозволить збільшити техніко-економічні
показники виробництва сталі й значно
знизити рівень забруднення навколишнього
середовища. Використання конвертерних
шлаків замість вапняку в металургійному
переділі дуже вигідно, тому що дозволить
знизити витрати природних шихтових
матеріалів і коксу, а також скоротити
викиди вуглекислого газу й пилу.
Організація процесів, що контролюють рух
цинку в металургійних процесах,
дозволить істотно знизити негативний
вплив цинку на технологію доменного
виробництва при утилізації пиловиносу
сталеплавильних агрегатів, а також
раціонально вирішити питання одержання
додаткової кількості дефіцитного цинку з
відходів чорної металургії. Комплексний
підхід до вирішення екологічних проблем
конвертерного виробництва дозволить
істотно поліпшити екологічний стан на
металургійних комбінатах країни.
ЛІТЕРАТУРА
1 Бойченко
Б. М. Конверторне виробництво сталі:
теорія, технологія, якість сталі,
Дніпропетровськ.: 2004 – 470 с.
2 Вторичные
материальные ресурсы черной металлургии:
В 2-х т. Т. 2: Шлаки, шламы, отходы
обогащения железных и марганцевых руд,
отходы коксохимической промышленности,
железный купорос: (Образование и
использование): Справочник/ В. Г.
Барышников, А. М. Горелов, Г. И. Папков
и др. – М.: Экономика, 1986. – 344 с.
3 В.А.
Куличенко, М.А. Поживанов, А.Д.
Зражевский – Ресурсосберегающие
технологии кислородно- конвертерных
процессов. Часть 2. г.Днепропетровск:
Днипро, 1995г.,213с.
4 Внутренний
и глобальный рециклинг отходов
производства – путь к малоотходным
технологиям / И. А. Дорошев //
Металлург. – 2001. - №10. С. 35 – 36.
5 Экологические
проблемы черной металлургии Донбасса /
И. М. Мищенко, А. И. Мищенко, С. В.
Кольцов, Г. С. Клягин //
Металлургическая и горнорудная
промышленность. – 2003. - №3. С. 136 –
137.
6 Состояние
и перспективы комплексной переработки
вторичных ресурсов черной металлургии
Донецкой области// доц. Ростовский В. И.
7 Утилизация
пылей и шламов в черной металлургии.
Толочко А. И., Славин В. И., Супрун Ю,
М., Хайрутдинов Р. М. Челябинск:
Металлургия, Челябинское отделение,
1990. – 152 с.
8 Розенгарт
Ю. И. Вторичные энергетические ресурсы
черной металлургии и их использование.
– Киев : Вища школа, 1988. – 328 с.
9 Элементы
безотходной технологии в металлургии :
Учебное пособие для вузов / Шульц Л.А. –
М.: Металлургия,1991.174с.
10 Довгопол
В. И. Использование шлаков черной
металлургии. – Изд. 2-е, перераб. и доп.
М.: Металлургия, 1978. – 168 с.
11 Панфилов
М. И. Металлургический завод без
шлаковых отвалов. – М.: Металлургия,
1978. – 248 с.
12 Экономика
комплексного использования железорудного
сырья / В. И. Довгопол, А. А. Медведев,
А. Н. Потанина, Г. А. Урявин. М.:
Металлургия, 1992. – 176 с. |