Tkachenko Andrey Vladimirovich
Faculty: Mechanical
Speciality: Metallurgical
equipment
Theme of master's work: "Granular fireproof material optimal ingredients for steal sassing start without oxygen "
Leader of work: Yeronko Sergey Petrovich
Significance of work
Development of charging in the sliding shutter channel which provides its practically absolute opening during the casting without burning by oxygen. It significantly reduces the oxide contents in steel during the initial moments of casting and at bucket changing. In cooperation with other actions application special loadings provides essential improvement of blanks quality, especially cast at an initial stage and after replacement of one steel teeming ladle to another.
In this connection development of charging equipment in the sliding shutter channel is now of great value.
The purpose and research problems
Elaboration of optimal loadings in the channel of sliding shutter which would provide its practically absolute opening, during the steel casting.
Practical value of work
Results of theoretical researches will be used at development of charging, by elaboration of the engineering specifications and manufacturing of laboratory installation.
1. Highly technological charging for opening sliding shutter of steel teeming ladle.
Steel casting experience on MNLZ (metal works) shows that as the basic sources of additional pollution of metal by nonmetallic dirt secondary oxidation of steel can serve at its movement from steel teeming ladle to a crystallizer, and also refractory and auxiliary materials to which steel comes into contact while moving.
In the beginning of casting an intermediate ladle filling occurs at an open metal surface up to charging heat-insulating mixture. All this period metal has contacts with the atmosphere. According to the data first 5-6 minutes of casting the contents of oxygen in steel is 3-4 times higher, than at the established casting process.
The degree of steel purity on the back end of blank worsens again, so at full discharging a steel-ladle into teeming ladle a quantity of slag appears and gets into it too. Additional hit of slag dirt in steel are quite possible at last portions casting of every steel teeming ladle because of funnel effect. At the beginning of submission of metal from new teeming ladle probably additional pollution of steel owing to hit in teeming ladle of products from burning the channel sliding shutter by oxygen.(fig.1)
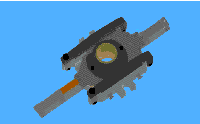
Fig. 1 - the circuit of sliding shutter work with hydrodrive
For the front part of blank it is established, that pollution by nonmetallic dirt considerably decreases when using aò open charging without oxygen burning of the sliding shutter channel, gunned layer on the magnesite basis which is put on walls and the bottom of teeming ladle and heat rice peel ashes insulation coverings which is delivered on metal surface.
Special value for blank quality and rhythmical work at MNLZ (metal works) is given to application of specific chemical and grain-size classification of charging which is filled in the l sliding shutter channel before filling it with metal (fig. 2). With implementation of out-of-furnace metallothermy into technological process metal staying period in a ladle increased and that its turn raised requirements to quality and charging operational properties.
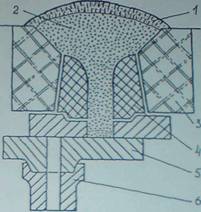
Fig. 2 - a common view of the circuit of filling a sliding shutter nozzle with charging:1 - sintered charging layer being in contact with steel; 2 - charging without thermophysical transformations; 3 - nested block; 4 - top glass; 5 - sliding shutter; 6 - collector.
Burning the sliding shutter channel by oxygen is accompanied by iron oxides formation which gets into the teeming ladle. In practice increase in the oxygen contents (1,5-2,0 times) in a head part of blank is noticeable when burning the sliding shutter channel.
Usually the mixture of quartz sand with amorphous graphite [2] is used for charging. However such charging is characterized by a low level of the sliding shutter channel opening (30-60 %) with a high degree of fluctuations in results from one portion of material to another. When using quartz sand as sliding shutter charging at some Japanese factories special attention is pay to its chemical structure (SiO2> =98 %), that raises a parameter of sliding shutter openability without burning [3].
A lot of metal works use staurolite concentrate (49,6 % Al2O3; 27,5% SiO2; 12,2% Få2Î5.3,5 of % TiO2) of grain-size structure of 0,4-0,7 mm. However this material needs burning at temperature 250-350 C and that, in fact, complicates its use.
Recently many factories have paid attention to creation of specially prepared mixtures that provide required set of operational properties. For example, in the USA charging which structure includes quartz sand with the size of grain 0.5-3,5 mm plated by fine particles of a mineral from group field øïàòîâ with temperature of fusion of 1000-1700 it is patented. Feldspar contents in charging are fluctuating from 5% to30% and size of its particles is less than 0,15 mm. This material, conglomerating at contact with liquid steel, forms a crust which prevents penetration of metal into pores between particles. At sliding shutter opening it collapses under pressure of liquid steel [4].
According to data received at Novolipetsk metal works when using a specific mixture developed at Borovich refractory products factory the results of sliding shutter opening about 80% [5] were achieved. The concept of a mixture for charging in the sliding shutter channel should suggest its opening in all cases except for emergency which as the statistical analysis shows cannot exceed amount of 1,0-1,5%...