Введение.
Актуальность.
Цели и задачи работы.
1.Обзор по теме.
1.1. Spectr-Met.
1.2. Intron-Set.
2.Научная новизна.
2.1.Основные этапы металлографии.
2.2.Методы обработки изображений.
Заключение.
Список литературы.
|
Введение
Черные металлы являются основным материалом, который используют в различных отраслях
промышленности: в машиностроении, авиастроении и судостроении, для изготовления металлоконструкций
для промышленного и жилищного строительства, транспортных коммуникаций и техники. При
выходе на международный рынок задача получения комплекса свойств того или иного металла
становится еще более актуальной, так как позволяет найти равноценный отечественный
заменитель иностранным маркам стали как по составу, так и по свойствам.
на начало
Актуальность
В Донбассе существует три наиболее известных и ведущих металлургических завода г. Донецка:
ДонецкСталь, ДМЗ и ИСТИЛ. Все они – современные металлургические мероприятия, которые в
год выпускают около 1 млн. тонн жидкой стали и предоставляют свою продукцию не только в
страны бывшего СНГ, но и за рубеж. При этом продукция должна быть качественной, чтобы не
потерять клиентов и сохранить свою конкурентоспособность на мировом рынке. А для этого одним
из самых важных аспектов является контроль за качеством выпускаемой продукции. Однако на
все три завода существует только одна центральная лаборатория, которая осуществляет контроль
соответствия выплавленной стали заказу покупателя. К тому же контроль проводится по ограниченному
числу характеристик путем визуального сравнения проверяемого образца с эталоном. Поэтому
проблема металлографического анализа считается весьма актуальной на сегодняшний день.
Необходимость компьютеризации данного процесса считается оправданной, так как это повысит
точность проводимого анализа, сократит время на его выполнение и облегчит труд работников лаборатории.
на начало
Цели и задачи работы
Целью работы является рассмотрение теоретических основы проведения металлографического
анализа, характеризация основных понятий, принципов и методов анализа, необходимых для создания
подсистемы металлографического анализа. Также целью является обоснование необходимости
разработки данной подсистемы, несмотря на существование программных пакетов, которые
решают проблему распознавания металлографических изображений. Для этого необходимо произвести
анализ входной и выходной информации, рассмотреть общесистемное обеспечение для поддержания
работоспособности системы.
Для построения системы металлографического анализа срезов стали необходимо решить
следующие основные задачи:
- выполнить анализ производственного цикла выплавки стали и проанализировать процесс
контроля качества выпускаемой металлургической продукции;
- выделить основные этапы металлографического анализа и проанализировать основной из
них – этап определения размера зерна стали;
- определить наиболее оптимальные методы распознавания текстуры металлографического
изображения среза;
- выбрать наиболее оптимальные методы определения размера зерна стали.
на начало
1.Обзор по теме
На данный момент уже существуют системы для решения проблемы проведения металлографического
анализа и не только. Но проблема в их избыточности: большинство функций просто
не нужно в контексте рассматриваемых предприятий и вида контроля. Приобретение таких
систем просто невыгодно. Рассмотрим некоторые из таких систем.
1.1. Spectr-Met
Программный пакет SPECTR MET 5.6 - универсальный программный инструмент, обеспечивающий
полный цикл работы с металлографическими изображениями: ввод и обработку изображений,
калибровку по размеру, количественные оценки и анализ изображений структур по ГОСТам
с формированием протоколов и отчетов. Легкий ввод новых процедур количественных оценок
и анализа структур по любым требуемым нормам, не требующий изучения никаких внутренних
языков программирования; надежность работы, точность результатов; эффективность и удобство
работы благодаря эргономичному, простому и понятному интерфейсу, автоматизации рутинных
операций обработки и анализа изображений, наглядному количественному анализу, возможности
создания отчетов с оригинальными изображениями и таблицами результатов измерений; удобный
фотоальбом для быстрой работы с большими объемами изображений.
Основные функции пакета SPECTR MET :
- количественые оценки и анализ изображений структур по ГОСТам с формированием протоколов
и отчетов;
- калибровка по изображению тест-объекта;
- измерения - “точка-точка” с построением профиля яркости на измеряемом отрезке; определение
в ручном и автоматическом режимах балла зерна по двум различным алгоритмам, учитывающим
степень однородности структуры; движущаяся шкала и сетка для быстрого измерения линейных
размеров и площадей;
- фазовый анализ - проводится вручную или автоматически (2 алгоритма), позволяет
оценивать процентные соотношения фаз в образце. Результат - мультифазное изображение
и таблица процентного содержания выделенных фаз. Для проверки правильности разделения
введена функция вычитания фаз;
- морфологические операции;
- морфологический анализ - выделение на изображении связных областей (зерен металлов
и т.п.) и контуров объектов;
- распознавание и альбомы эталонных структур - удобное средство при анализе структур
металлов методом сравнения с эталоном;
- обработка изображений - регулировки яркости, контрастности, гамма-коррекция с отображением
изменения гистограммы; шумоподавление (2 алгоритма); поиск и подчеркивание границ (для
задач микродефектоскопии); фильтр резкости с минимальным уровнем вносимых шумов; специальный
фильтр преобразование цветного изображения в серое с максимальным сохранением контраста
и деталей; фильтры коррекции характерных искажений видеоизображения.
1.2. Intron-Set
Этот программный пакет обработки и анализа изображений металлографии также предназначается
для ввода, преобразования и анализа изображений в материаловедении. Результаты анализа
обрабатываются статистически. Пакет позволяет проводить анализ изображений в полуавтоматическом
и автоматическом режимах и решать широкий спектр задач количественной металлографии.
Основные возможности и преимущества пакета:
- количественные оценки и анализ производиться по ГОСТам;
- осуществлен ввод процедур количественных оценок и анализа структур по любым нормам;
- ввод изображений с цифровых фотокамер и сканеров, а также с устройств преобразования
изображений в цифровую форму;
- наличие фотоальбома для работы с большими объектами изображений;
- сохранение библиотек изображений и отчетов на съемных носителях;
- пакетная обработка изображений с помощью макрокоманд.
Недостатки существующих систем. В принципе, обе рассмотренные системы имеют одни и те
же недостатки. Выделим самые главные из них:
- избыточное количество реализованных функций металлографического анализа, в то время как
в контексте рассматриваемой задачи необходима реализация лишь основных из них;
- основная задача выявления и определения размера зерна сталей и сплавов решена лишь
двумя алгоритмами;
- необоснованная необходимость в сложном и дорогостоящем оборудовании (цифровые камеры,
преобразователи, оцифровщики и т.д.), которая излишня в данной задаче;
- достаточно высокая цена систем в свете того, что процентов 60% из реализованных
возможностей просто не нужны для рассматриваемого анализа.
Поэтому считаю применение существующих систем нецелесообразным.
на начало
2.Научная новизна
Научной новизной этой работы можно считать применение нестандартных методов для решения
поставленной задачи. В качестве этого можно рассматривать применение Марковских полей и
скрытых Марковских моделей для распознавания текстуры изображений срезов различных сплавов.
В большинстве своем эти методы применяются для распознавания лиц, речи и факсимильного текста.
Также новизной можно считать реализацию процесса определения размера зерна четырьмя способами
(согласно ГОСТам), а не двумя, как реализовано в существующих системах.
2.1.Основные этапы металлографии
Процесс выплавки стали начинается с заказа сплава и заканчивается проверкой готовой
продукции. Этот процесс включает следующие основные этапы:
1. Оформление предварительного заказа на необходимую марку стали и соответствующих
требований к ней. Передача основных требований к продукции в технический отдел.
2. Отделом договорной документации составляется договор с заказчиком. Параллельно
составляется спецификация на выплавку заказа, где указываются все требования к продукции.
3. Далее спецификация передается в цех на выплавку заказа. После выплавки отбираются
образцы продукции для контроля на соответствие спецификации, которые передаются в
центральную контрольную лабораторию.
4. Результаты проведения анализа формируются в виде протокола испытаний, который
передается в цех производства и отгрузки готовой продукции. Сертификатчики цеха вносят
данные из протокола испытаний в сертификат качества.
5. Далее лаборатория вносит данные анализа в статистическую базу.
Анализ металлографический продукции предусматривает несколько проверок. Типовая схема
организации анализа приведена на рис. 2.1 ниже.
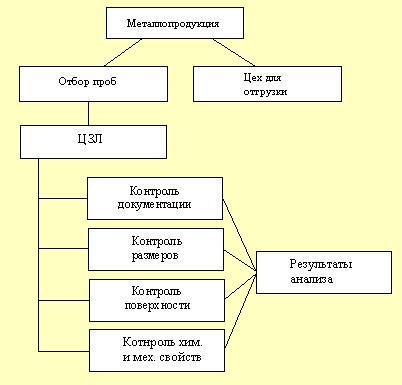 Рисунок 2.1 Типовая схема организации металлографического анализа.
Основным этапом металлографического исследования является металлография – позволяет
получить информацию о морфологии элементов структуры. Этапы металлографии:
1. Электронная микроскопия. Для исследования металлов применяется обычно сканирующий
электронный микроскоп, в котором пучок электронов с помощью системы развертки сканирует
поверхность образца.
2. Микромеханические испытания. Основной характеристикой металлов и сплавов являются их
механические свойства, т. е. способность выдерживать нагрузки и деформироваться.
Разработано большое количество стандартных методов механических испытаний.
3. Выявление и определение величины зерна сплава. На этом этапе определяются:
- величина действительного зерна после горячей деформации или любой термической обработки;
- склонность зерна к росту – определение величины зерна после нагрева при температуре
и времени выдержки, установленных нормативно-технической документацией на стали и сплавы;
- кинетика роста зерна – определение величины зерна после нагрева в интервале температур
и времени выдержки, установленных нормативно-технической документацией на стали и сплавы.
Процесс определения размера зерна. Итак, для проведения металлографического исследования
нужно разрезать образец, отшлифовать и отполировать поверхность разреза (приготовить
металлографический шлиф), обработать специальным реактивом для данного класса материалов
(протравить), сфотографировать разные участки шлифа с различными увеличениями и сравнить
с эталонными фотографиями в металлографическом атласе либо сделать анализ любыми другими
известными методами. На основании этих данных можно сделать заключение о химическом составе
сплава, различных структурных составляющих и режимах предшествующей термической обработки.
С помощью микроанализа можно определить структуру сплава не только в равновесном, но и в
неравновесном состоянии, что в ряде случаев позволяет установить предшествующую обработку
сплава.Изменение структуры от поверхностного слоя к середине изделий указывает на
характер нагрева (наличие окисления или обезуглероживания стали) или на применение
химико-термической обработки (цементации, азотирования и т. д.).
Определение размеров зерен проводится либо методами количественной металлографии, либо
путем сопоставления структуры с заранее составленными шкалами. Это процесс включает
следующие этапы:
1. Приготовление микрошлифов.
В оптическом микроскопе рассматриваются микрошлифы — специальные образцы металла, имеющие
шлифованную и полированную гладкую поверхность, отражающую световые лучи.
2. Изучение микроструктуры.
Изучение микроструктуры начинают с рассмотрения шлифа в нетравленном виде, т. е. после
полирования и промывки. В этом случае в поле зрения микроскопа можно заметить отдельные,
обычно небольшие, темные участки.
3. Травление.
Для определения размера зерна шлиф подвергают травлению. Зерна чистых металлов или твердых
растворов имеют неодинаковую кристаллографическую ориентировку. Поэтому на приготовленную
плоскость микрошлифа приходятся зерна, срезанные по разным кристаллографическим направлениям
и имеющие в этих направлениях неодинаковые свойства.
Методы определения размера зерна.
Зерна металлов – это отдельные кристаллы поликристаллического конгломерата, разделенные
между собой смежными поверхностями, называемыми границами зерен. При наличии двойников
зернами считают кристаллы вместе с двойниками. Величина зерна – это средняя величина случайных
сечений зерен в плоскости металлографического шлифа. Фотография среза сплава представлена ниже на рис. 2.2.
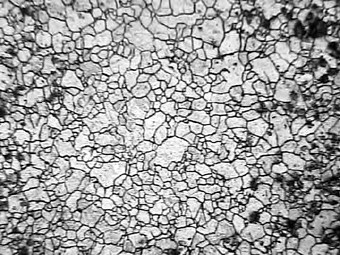 Рисунок 2.2 Срез сплава стали.
Величина зерна определяется с помощью следующих методов, описанных в стандарте (ГОСТ 5639-82):
1. Метод визуального сравнения с эталонами шкал.
Величину зерна определяют при увеличении 100х. После просмотра всей площади шлифа выбирают
несколько типичных мест и сравнивают их с эталонами, которые приведены на рис. 2.3. Сравнение
проводится на фотоснимке. Шкалы представлены десятью эталонами в виде схематизированной
сетки, ограничивающей размеры зерен. Эталоны приведены в виде круга диаметром 79,8 мм, что
соответствует натуральной площади на шлифе 0,5 мм.
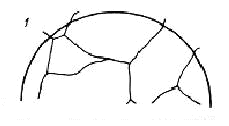 Рисунок 2.3 Этaлонные шкалы.
(Анимация включает в себя 5 циклов и 19 кадров. Для запуска анимации обновите страницу.)
2. Метод подсчета количества зерен, приходящихся на единицу поверхности шлифа, с определением
среднего диаметра и средней площади зерна.
Этот метод заключается в определении количества зерен на единице поверхности шлифа (1 мм кв)
и расчете средней площади и среднего диаметра зерна. Подсчет зерен проводится на
микрофотографии в поле зрения, ограниченном окружностью диаметром 79,8 мм, что соответствует
0,5 мм2 поверхности шлифа при увеличении 100х.
3. Метод подсчета пересечений границ зерен отрезками прямых с определением среднего условного
диаметра в случае равноосных зерен, количества зерен в 1 мм2 в случае неравноосных зерен.
Метод состоит в подсчете зерен, пересеченных отрезком прямой, и определении среднего
условного диаметра (в случае равноосных зерен) или количества зерен в 1 мм2 (в случае
неравноосных зерен). Подсчет пересечений в обоих случаях производится на микрофотографиях,
на которых проводят несколько отрезков произвольной длины. Длину отрезков выбирают с таким
расчетом, чтобы каждый из них пересекал не менее 10 зерен, при этом увеличение подбирают
так, чтобы на исследуемой поверхности было не менее 50 зерен. Подсчитываются точки
пересечений отрезков прямых линий с границами зерен. Зерна на концах прямой, не пересеченные
ею целиком, принимают за одно зерно. При этом методе определяют суммарную длину отрезков L,
выраженную в мм натуральной величины на шлифе, и суммарное число пересеченных зерен N.
Измерения проводятся не менее чем в пяти характерных местах шлифа. Допускаются расхождения
результатов пяти определений при подсчете пересечений не более 50%.
4. Метод измерения длин хорд с использованием микрофотографии с определением относительной
доли зерен определенного размера.
Метод основан на замере линейных размеров отрезков – хорд, отсекаемых в зернах прямыми линиями,
и применяется для определения величины зерна в разнозернистой структуре. Замер длин хорд
проводится на микрофотографии. При этом 100 мм при увеличении 100х соответствует длине 0,8мм
или 1мм на шлифе. Замер проводят не менее чем в пяти наиболее типичных полях зрения, при этом
в каждом поле зрения проводят не менее трех прямых в произвольных направлениях. Значения
длин хорд относят к определенной размерной группе.
2.2.Методы обработки изображений
Текстуры являются важной характеристикой изображений естественных объектов и важным
элементом зрительного восприятия. Машинному анализу текстурных изображений посвящено значительное
количество исследований, существенную часть которых занимает проблема сегментации изображений
по текстурным признакам. В данном случае для распознавание текстур будут использоваться Маркосвкие
случайные поля и скрытые Марковские поля.
Марковские модели являются мощным средством моделирования различных процессов и распознавания образов.
По своей природе Марковские модели позволяют учитывать пространственно-временные характеристики сигналов,
и поэтому получили широкое распространение в распознавании речи, а в последнее время и изображений (в
частности лиц).
Введем основные понятия, необходимые для рассмотрения данного метода:
- Поле зрения – это произвольное конечное множество. Обозначается символом Т. Наиболее
часто встречается поле зрения в виде прямоугольного участка двумерной целочисленной решетки

- Пиксель – элемент поля зрения. Элементами поля зрения являются натуральные числа Т={1,2,…,m}.
- Палитра – произвольное конечное множество как и поле зрения. Обозначается символом Х={1,2,…,n}.
- Цвет – это элементы палитры.
- Изображение на поле зрения Т с палитрой Х – это функция , которая
каждому пикселю поля зрения ставит в соответствие какой-то цвет из палитры. Сужение этой
функции на подмножество поля зрения обозначается ,
а значение функции в пикселе t c T обозначим как .
- Разметка поля зрения Т на l сегментов – это функция . При
этом множество {1,2,…,l} называется множеством меток и обозначается символом К.
- Структура поля зрения Т – это семейство подмножеств этого
поля зрения .
Если на множестве всех изображений задана случайная величина
N, то эту случайную величину называют случайным полем.
Марковскими называются все случайные поля, распредение вероятностей которых имеет следующий вид:

В этом методе структурная сегментация изображений рассматривается как частный случай генерирования
марковских случайных полей. При этом цвет каждого пикселя состоит из двух компонент – цвета и
метки. При этом неявно предполагается, что структура поля зрения для различных текстур совпадает.
Каждая модель представляет собой набор N состояний ,
между которыми возможны переходы. В каждый момент времени система находится в строго определенном состоянии.
В наиболее распространенных Марковских моделях первого порядка полагается, что следующее состояние зависит
только от текущего состояния.
При переходе в каждое состояние генерируется наблюдаемый символ, который соответствует физическому
сигналу с выхода моделируемой системы. Набор символов для каждого состояния ,
количество символов М. Выход, генерируемый моделью, может быть также непрерывным. Существуют также модели,
в которых набор символов для всех состояний одинаков. Символ в состоянии в
момент времени t генерируется с вероятностью . Набор всех таких вероятностей
составляет матрицу . Матрица определяет вероятность
перехода из одного состояния в другое: . Считается, что А не зависит от времени.
Если из каждого состояния можно достичь любого другого за один переход, то и
такая модель называется эргодической. Модель также имеет вероятность начальных состояний
, где .
Обычно в реальных процессах последовательность состояний является скрытой от наблюдателя и остается
неизвестной, а известен только выход системы, последовательность наблюдаемых символов
, где каждое наблюдение – символ из V, и Т – число наблюдений в последовательности.
Поэтому такие модели называют скрытыми Марковскими моделями.
В распознавании образов скрытые Марковские модели применяются следующим образом. Каждому классу i соответствует
своя модель . Распознаваемый образ представляется в виде последовательности наблюдений
О. Затем для каждой модели вычисляется вероятность того, что эта последовательность
могла быть сгенерирована именно этой моделью. Модель , получившая наибольшую вероятность,
считается наиболее подходящей, и образ относят к классу j.
Недостатком скрытых Марковских моделей является то, что модель не обладает различающей способностью,
т. е. алгоритм обучения только максимизирует отклик каждой модели на свои классы, но не минимизирует
отклик модели на другие классы и не выделяются ключевые признаки, отличающие один класс от другого.
Таким образом, похожие классы могут оказаться слабо различимыми и при увеличении объема базы или
использования в более широких условиях скрытые Марковские модели могут оказаться ненадежными.
на начало
Заключение
Наиболее важной проблемой в анализе и классификации изображения на сегодняшний день является
классификация текстур, которые расположены под различными углами и в разном масштабе. Эту проблему
можно решить с помощью разновидностей Марковских моделей. Применение Марковских моделей имеет ряд
преимуществ:
1. Математическая структура скрытых Марковских моделей очень богата и позволяет решать математические
проблемы различных областей науки.
2. Грамотно спроектированная Марковская модель дает на практике хорошие результаты работы.
Основное же преимущество Марковских моделей состоит в том, что разметка и каждая текстура характеризуется своими
Марковскими случайными полями, не зависящими друг от друга. Это позволяет легко модифицировать
распознающую систему. Введение новой текстуры или удаление существующей происходит в рамках
модели очень просто. Кроме того, в данной модели легко учитываются априорные знания о разметке.
на начало
Список литературы
1. Сорокин, В. Г. Стали и сплавы: марочник / В. Г. Сорокин, М. А. Гервасьев – Москва 2001г.;
2. Солнцев, Ю. П. Стали и сплавы: справочник / Ю. П. Солнцев – 2003г.;
3. Ресурсы Internet:
- www.ngmk.info;
- www.yandex.ru;
- www.vikipedia.ru;
4. Цопкало, Н. Н. Математическое программирование и распознавание образов: статья / Н. Н. Цопкало – 2006г.;
5. Яковлев, А. В. Методы анализа и синтеза текстур: статья / А. В. Яковлев – 2006г.;
6. Гончаров, А. В. Разработка и исследование алгоритмов и методов детекции и идентификации образов: статья / А. В. Гончаров – 2006 г.
на начало
|