ВВЕДЕНИЕ
Актуальность темы
Каждое изделие в машиностроении, поставляемое в условиях жесткой конкуренции на внутренний и внешний рынок, должно обладать новым уровнем свойств и отвечать всевозрастающим требованиям, предъявляемым потенциальными потребителями к функциональным, экономическим и эстетическим свойствам. Поэтому основная цель в развитии машиностроения это постоянное улучшение качества изделий, одновременно находя оптимальный вариант сочетания вышеперечисленных свойств изделия, необходимых потребителю. Одним из направлений улучшения изделия является повышение точности обработки его поверхностей, которая непосредственно влияет на функциональные и эстетические качества изделия и это необходимо совершать наиболее экономичными путями и средствами. Вопросы оптимизации обработки деталей в течение длительного периода времени привлекают внимание исследователей и производственников. Но основная масса исследований точности и оптимизации условий обработки проводилась для наружных поверхностей. Вместе с тем, обработка отверстий занимает не менее важное место в машиностроении и по объему не уступает процессам обработки наружных поверхностей. Кроме того, обработка точных отверстий относится к числу наиболее трудоемких процессов, является более сложной, чем обработка наружных поверхностей, что обусловлено более тяжелыми условиями протекания процесса, меньшей жесткостью режущих инструментов. При обработке отверстий необходимо обеспечивать не только точность размера и формы, но также точность положения оси обрабатываемого отверстия относительно наружной поверхности [1, с. 3]. Большое значение для производства имеет выявление возможностей и необходимых условий по уменьшению технологического наследования исходных погрешностей, поскольку они оказывают решающее влияние на точность, производительность труда при чистовой обработке отверстий и на последующую надежность работы деталей в узле машины. Проблемные задачи повышения точности, виброустойчивости и производительности обработки отверстий мерными концевыми инструментами решаются путем управления перемещениями инструмента в плоскости, перпендикулярной его оси за счет оптимизации конструктивных параметров, ориентации колебательной системы и режимов резания. Последние тесно связаны с размерной стойкостью инструмента, точностью, себестоимостью и производительностью обработки отверстий [1, с.4].
Сверление спиральными сверлами - один из основных методов обработки отверстий. Этому процессу посвящено достаточно большое количество публикаций. Однако, большинство из них направлены на исследования стойкости, производительности обработки отверстий, технологии изготовления, конструкции и условиям эксплуатации сверл. Количество работ, посвященных исследованию точности обработки отверстий невелико. Это объясняется сложностью процесса сверления, в частности: отсутствием доступа к режущим кромкам, переменной скоростью резания и, связанной с этим неоднородностью стружкооб-разования вдоль режущих кромок, относительно малой жесткостью сверла, наличием крутильных колебаний. Для более ясного понимания влияния перечисленных факторов на точность обработки, процесс сверления следует исследо¬вать в динамике, и при этом рассматривать станок, инструмент и деталь как единую технологическую систему.
В связи с этим исследование процесса формообразования при сверлении является актуальной задачей.
Цель и задачи исследования
Цель работы – повышение точности обработки отверстий на основе управления траекториями формообразования при сверлении.
Для достижения поставленной цели следует решить следующие задачи:
1. Выявить факторы, влияющие на форму и размеры траекторий формо-образования и определить методы по снижению негативного влияния этих факторов на точность обработки.
2. Разработать методику расчета и построения геометрического образа обрабатываемого отверстия и прогнозирования точности обработки на основе измерения траекторий формообразования.
3. Провести экспериментальные исследования по измерению траекторий оси вращения шпинделя станка и инструмента на реальном станке в ходе про-цесса резания в реальном масштабе времени.
Научная новизна и практическая ценность
Разработка математической модели построения геометрического образа обрабатываемого отверстия при сверлении.Разработка методики прогнозирования точности обработки отверстия на основе измерения траекторий формообразования.
В результате исследований влияния различных факторов,таких как разные схемы закрепления, неуравновешенная радиальная сила резания,режимы резания и другое на увод оси сверла, должна появиться программа на ANSYS 5.6.,при изготовлении которой будет создана модель процесса глубокого сверления, которая позволит проследить деформации инструмента, распределение напряжений, температур, нагрузок, возникающих в процессе глубокого сверления.
С практической точки зрения это даст возможность более правильно спроектировать режущий инструмент, учесть различные нюансы, касающиеся выбора тех или иных исходных данных при проектировании, облегчит работу проектирования и выбора режущего инструмента при обработке отверстий.
1 ОСНОВНЫЕ ПАРАМЕТРЫ ТОНОСТИ ОТВЕРСТИЙ, ОБРАБАТЫВАЕМЫХ ОСЕВЫМИ ИНСТРУМЕНТАМИ
Точность обработки определяется следующими параметрами:
- отклонением размера отверстий,
- отклонением формы отверстий,
- отклонением расположения осей (поверхностей отверстий),
- шероховатостью поверхности отверстий.
Размер удобнее выражать не в абсолютной форме, а с помощью отклонения его от номинального размера. Отклонение размера отверстий – алгебраическая разность между размером действительным и номинальным. Отклонения могут быть положительными (если размер больше номинального) и отрицательными (если размер меньше номинального) [4, с. 10]. Отклонение формы отверстий – отклонение реальной формы от формы номинальной поверхности. Различают следующие виды отклонений формы:
- овальность (отклонение от круглости, при котором отверстие имеет форму овала),
- огранка (отклонение от круглости, при котором реальный профиль представляет собой многогранную фигуру с числом граней, иногда изменяющимся по длине отверстия),
- конусообразность,
- бочкообразность,
- седлообразность,
- волнистость профиля продольного сечения, при котором образующие имеют регулярную волнистость, приводящую к ступенчатости отверстия с незначительными перепадами диаметра. Отклонение расположения осей или поверхностей отверстий – отклонение реального расположения от номинального (заданного). Различают следующие виды отклонений расположения осей (поверхностей) отверстий:
- отклонение от параллельности отверстий,
- отклонение от перпендикулярности оси,
- отклонение от соосности,
- отклонение от симметричности,
- отклонение от пересечения осей. Шероховатость поверхности отверстий – совокупность неровностей поверхности с относительно малыми шагами на базовой длине.
2 ПРИЧИНЫ ВОЗИКНОВЕНИЯ НЕТОЧНОСТЕЙ И ОШИБОК ПРИ ОБРАБОТКЕ ОТВЕРСТИЙ
На точность отверстий при обработке отверстий осевыми инструментами влияют факторы, которые являются причинами возникновения различных дефектов:
- пластическая деформация поверхностного слоя заготовки при образовании стружки, способствующая появлению шероховатости,
- геометрия режущего инструмента, вызывающая такую погрешность как наследственность,
- несовпадение диаметра инструмента, вступающего в работу, с диаметром отверстия, на поверхность которого он опирается своими направляющими элементами, являющееся причиной появления волнистости профиля продольного сечения отверстия,
- погрешность этапа установки и переустановки, вызывающая отклонение оси обработанного отверстия заготовки от заданного положения относительно принятой базы, и которая становится возможной из-за невозможности точного соединения основных и вспомогательных баз осевого режущего инструмента и металлорежущей системы вследствие неопределенности расположения их системы координат; неопределенность базирования при принятых в практике комплектах баз для осевого режущего инструмента и металлорежущей системы [6, с. 41].
- конструкция вспомогательного инструмента,
- точность станка,
- биение отверстия, вызывающее увод и непрямолинейность оси, которое становится возможным вследствие коробления заготовки из-за перераспределения остаточных напряжений в процессе обработки отверстия;
- деформации заготовки при закреплении на станке.
- частота собственных колебаний инструмента способствует появлению огранки,
- попадание стружки в зону резания, вызывающей надира и царапины,
- направление и величина стружечных канавок, от которых зависит величина шероховатости поверхности полученного отверстия.
3 СВЕРЛА
Сверление является основным способом образования глухих и сквозных отверстий в сплошном металле а также используется для расширения предварительно просверленных отверстий.
Oбработанные сверлением отверстия имеют параметр шероховатости Rа=20...5мкм и точность, соответствующая 12 ... 14-му квалитету (реже 10 и 11-го квалитетов). Причиной сравнительно невысокой точности просверленных отверстий является геометрия сверла, отклонение от соосности сверла со шпинделем станка, отклонение от симметричности заточенной режущей части сверла, малая жесткость сверла.
Сверление и рассверливание отверстий может производиться по двум различным схемам:
1) вращается сверло — деталь неподвижна;
2) вращается деталь — сверло неподвижно.
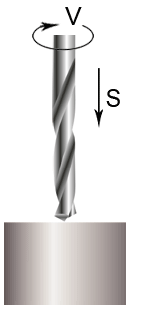
Рис.1 Схема процесса сверления. Анимированный рисунок. Количество кадров - 7, число циклов повторения - 30.
В обоих случаях сверло перемещается вдоль оси отверстия в движении подачи. Иногда применяется такая схема, когда и обрабатываемая деталь и сверло вращаются в противоположных направлениях. При работе по первой схеме отверстие получается цилиндрическим, но возможен увод оси сверла. При работе по второй схеме ось отверстия получается прямолинейной, совпадающей с осью вращения детали, но возможно образование конусности и изменение диаметра отверстия по длине [3, с. 6]. Сверлами изготовляются отверстия диаметром от 0,25 до 80 мм. Сверла с диаметром вне указанных пределов встречаются как исключение. Применение сверл большего диаметра ограничивается жесткостью конструкций сверлильных станков и обрабатываемы деталей, а малого диаметра — жесткостью самого сверла. Для уменьшения усилия подачи отверстия большого диаметра сверлят в два прохода: сначала сверлом меньшего диаметра, а затем другим сверлом рассверливают на требуемый размер. При этом диаметр предварительного сверла принимают равным половине диаметра окончательного сверла. Обработка ступенчатых отверстий производится также последовательным сверлением. С точки зрения производительности, такие отверстия выгоднее сверлить, начиная с большего диаметра. Однако для уменьшения усилия подачи сначала сверлят отверстие сверлом малого диаметра, а затем рассверливают его на необходимую длину сверлом требуемого диаметра.
По форме обрабатываемого отверстия различают сверла: цилиндрические, конические, призматические и комбинированные.
Сверла цилиндрические применяются для обработки гладких цилиндрических отверстий. В зависимости от характера выполняемой работы, на практике встречаются цилиндрические сверла следующих типов:
1) сверла перовые, применяемые для обработки отверстий при отсутствии спиральных сверл, а также для сверления твердых материалов;
2) сверла с прямыми канавками, применяемые для обработки вязких материалов, и с косыми канавками;
3) сверла спиральные стандартные, применяемые для обработки разных материалов;
4) сверла для глубоких отверстий, применяемые тогда, когда специфические трудности обработки отверстий с отношением d>5—6 затрудняют или полностью исключают возможность применения стандартных сверл. Основными разновидностями этого типа сверл являются: сверла спиральные и перовые удлиненные, сверла ружейные, сверла пушечные и кольцевые.
5) сверла конические и призматические. Конические сверла применяются для обработки за один проход конических отверстий небольшой конусности. Призматические сверла находят применение для сверления многогранных отверстий. Сверла комбинированные применяются главным образом для обработки двухступенчатых отверстий и центровых отверстий [4, с. 9].
4 РАЗРАБОТКА ГЕОМЕТРИЧЕСКОЙ МОДЕЛИ СВЕРЛЕНИЯ
При ассиметричной заточке режущих кромок система сил, действующих на сверло, приводится к осевой силе, крутящему моменту и неуравновешенной радиальной силе, при симметричной заточке - к осевой силе и крутящему моменту. Характер изменения сил резания, по мере увеличения скорости резания, определяется сменой видов контактного взаимодействия. Однако, при сверлении, обычно, одновременно существуют несколько видов контактного взаимодействия. Это объясняется тем, что скорость резания на главной режущей кромке у вспомогательных режущих кромок максимальна, а у перемычки -приближается к нулю.
В результате воздействия силовых факторов, происходит возникновение погрешностей обработки. Сверлению присущи два вида погрешностей: разбивка отверстия и увод оси отверстия. Разбивка отверстия происходит в результате контакта вспомогательных режущих кромок с поверхностью обрабатываемого отверстия. Увод сверла происходит вследствие изгибных деформаций инструмента и копирования погрешности обработанной поверхности на вновь образуемую поверхность. Деформация сверла оказывает воздействие на узлы и детали станка, прежде всего на шпиндель.
На рисунке 1 представлена расчетная схема определения геометрического образа обрабатываемого отверстия в поперечном сечении заготовки детали.
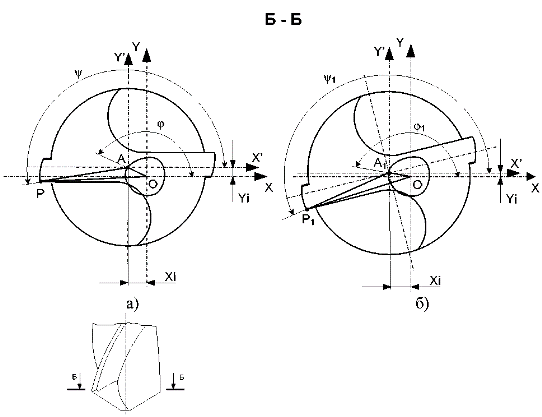
Рис. 2 Математическая модель определения геометрического образа обрабатываемой поверхности при сверлении
Координатными осями технологической системы являются XOY. Система координат инструмента обозначена X’OY’. Ось вращения сверла движется по некоторой траектории и в момент времени t1, соответствующий углу пово-рота шпинделя, равному φ, находится в точке А с координатами Xi, Yi. Вспомогательные режущие кромки в некотором сечении Б - Б находятся в положении, изображенном на рисунке, с периферией в точке Р.
Положение каждой точки вспомогательной режущей кромки определяется только углом поворота сверла ψ и высотой сечения Б-Б. В системе координат сверла X’OY’ их положение (координаты точки P в рассматриваемом сечении) можно выразить следующими выражениями:
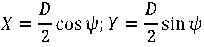
где D – диаметр сверла в рассматриваемом сечении.
На схеме величина D/2 соответствует отрезку АР.
С учетом обратной конусности сверла отрезок АР можно выразить как:
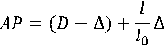
где D – диаметр сверла у главных режущих кромок; Δ – обратная конусность, выражаемая разностью диаметров на расстоянии l0 (l0=100 мм), l=l0-Zi – расстояние, характеризующее расположение рассматриваемого сечения сверла, Zi – расстояние от перемычки до рассматриваемого сечения сверла.
Zi – расстояние от перемычки до рассматриваемого сечения сверла.
Координаты точек главных режущих кромок определяются следующим образом. На торцовой поверхности сверла радиус произвольной точки х режущей кромки образует с плоскостью, проходящей через ось сверла, угол δx, который cвязан со значением радиуса выражением:

где c – ширина перемычки, rx– радиус точки.
Тогда координаты точки режущей кромки в системе координат X’OY’ определяются следующим образом:
X=rxcos(ψ-δR-δx); Y=rxsin(ψ-δR-δx)
где rx – радиус точки х главной режущей кромки, δx – угол определяю-щий, положение точки х главной режущей кромки, δR – угол определяющий, положение точки, находящейся на периферии главной режущей кромки.
При повороте шпинделя на угол φ1, ось сверла переместится в точку A1. Сверло при этом совершает оборот вокруг своей оси и занимает положение соответствующее углу ψ1, периферия сверла в рассматриваемом сечении переместится в точку P1.
В идеальном случае приращение угловых перемещений шпинделя и свер-ла равны: Δψ = Δφ
Это соответствует работе станка на холостом ходу. При резании же воз-никают угловые и продольные деформации, которые изменяют угол спирали сверла. Из экспериментальных данных следует, что при резании фактические приращения угла поворота сверла меньше чем приращения угла поворота шпинделя: Δψ ≤ Δφ [4].
Следует отметить, что сверло, находясь в отверстии, не имеет возможности свободно перемещаться в материале, т.е. положение главных режущих кромок относительно стабильное, режущие кромки при этом опираются на поверхность резания. Положение главных режущих кромок не определяет геометрический образ обрабатываемой поверхности в поперечном сечении. В то же время вспомогательные режущие кромки касаются уже обработанной поверхности.
Из рассматриваемой схемы можно определить положение вспомогательных режущих кромок, которое и будет определять геометрический образ обрабатываемой поверхности в поперечном сечении.
Координаты точки Р в идеальной системе координат XOY определяются из выражений: X= ±AP cosψ ± Xi ; Y= ±AP sinψ ± Yi.
В основу математического определения геометрического образа в поперечном сечении заложена формула определения расстояния между двумя точками, лежащими на плоскости:
d=V(X2-X1)2+(Y2-Y1)2
где X1, X2, Y1, Y2 - координаты точек в декартовой системе координат. Тогда мгновенный радиус Rд обрабатываемой поверхности в идеальной системе координат определяется выражением [5]:
(1)
где AP - отрезок равный радиусу сверла в рассматриваемом сечении, ψ -угол поворота сверла,Xi, Yi - координаты оси сверла в идеальной системе координат.
Это выражение является обобщенной функцией геометрического образа при сверлении. Определив экспериментально траекторию оси вращения сверла, то есть текущие координаты Xi и Yi, по углу поворота шпинделя j и углу поворо¬та сверла ψ подставив их в формулу (1) можно определить форму обрабатываемой поверхности детали в рассматриваемом сечении.
При вращении шпинделя с одновременным движением подачи, все точки режущих кромок сверла переместятся вдоль оси Z на величину равную:
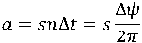
где s - подача м/об, n - частота вращения инструмента, об/мин, Δt -промежуток времени, за который совершено перемещение, Δψ - угловое перемещение инструмента, рад.
Таким образом, точки режущих кромок сверла совершают сложное движение, состоящее из следующих составляющих движений: вращение сверла вокруг своей оси, перемещение оси по некоторой стохастической траектории, пе-ремещение, соответствующее движению подачи.
Т.о. можно определить положение точек режущих кромок сверла в любой момент времени.
ЗАКЛЮЧЕНИЕ
Решение задач увеличения производительности труда, эффективности производства, повышения качества выпускаемой продукции тесно связано с точностью обработки отверстий мерными концевыми инструментами, широко использующимися в машиностроении. Проблема повышения точности обработки деталей решается в трех направлениях: улучшение качества системы СПИД; устранение факторов, порождающих погрешность обработки, управление процессом обработки. При обработке отверстий концевые инструменты являются наименее жестким звеном в системе СПИД. В связи с этим улучшение качества технологической системы достигается, в основном, путем повышения жесткости, виброустойчивости, износостойкости и оптимизации геометрических параметров инструмента. Подавление факторов, вызывающих погрешность обработки отверстий, осуществляется обычно ужесточением требований к качеству изготовления и заточки концевых инструментов. Однако это связано с большими затратами и малоэффективно. Наиболее перспективным является третье направление — управление процессом обработки отверстий. Проблема управления точностью обработки отверстий мерными концевыми инструментами требует решения широкого круга вопросов, начиная с исследования закономерностей образования погрешностей обработки, математического описания процесса образования обработанной поверхности и ее погрешностей в зависимости от условий обработки, разработки способов и средств управления, и кончая широким внедрением в промышленность. Технологическая задача повышения точности и производительности обработки отверстий мерными концевыми инструментами сведена к задаче оптимального управления, решаемой на основе использования принципа максимума путем оптимизации конструктивных параметров, ориентации колебательной системы инструмента и режимов резания.
Разработанная математическая модель построения геометрического образа обрабатываемого отверстия при сверлении и методика построения геометрического образа и прогнозирования точности обработки отверстия на основе измерения траекторий формообразования позволяют производить расчет и построение геометрического образа обрабатываемого отверстия в трехмерном пространстве с высокой точностью и на его основе определять показатели точности отверстия.
Список источников
1. Холмогорцев Ю.П. Оптимизация процессов обработки отверстий. - М.: Машиностроение, 1984. - 184с.
2. Быков С.Ю., Соколов А.В., Юркевич В.В. Исследование траектории вращения шпинделя при сверлении. // Волжский технологический вестник. На-учный технический производственный журнал. Волгоград. №2. 2005. С 38-42.
3. Королева Е.М., Никишина Н.А. Работа осевого режущего инструмента в металлорежущей системе Вестник машиностроения, 2000, № 12 – С. 41 - 45.
4. Быков С.Ю. Факторы, определяющие качество процесса сверления спиральными сверлами // Известия волгоградского государственного техниче-ского университета. Серия «Прогрессивные технологии машиностроения». Вы¬пуск 2. №4. Волгоград. гос. техн. ун-т. – Волгоград, 2006. С. 25-28.
5. Юркевич В.В., Быков С.Ю., Емельянов П.Н. Измерение траекторий формообразования при сверлении // Измерительная техника. – Москва, 2006.
6. Лакирев С.Г. Обработка отверстий. - М.: Машиностроение, 1984. - 208 с.
7.Родин П.Р.Основы проектирования режущих инструментов.-К.:Вища школа,1990-с.258
8. Основы формообразования поверхностей резанием. Родин П.Р. Киев, Издательское объединение «Вища школа», 1977, 192с.
9. Люкшин В.С. Теория винтовых поверхностей в проектировании режущих инструментов. М., «Машиностроение», 1968.
10. Федотенок А.А. Кинематические связи в металлорежущих станках. М., Машгиз, 1960.
11. Автореферат магистерской работы Федосова Н.Н. ДонНТУ, 2006.