Автореферат по теме выпускной работы
Введение
1. Литературный обзор
2. Экспериментальная часть
3. Планированный эксперимент
Выводы
Перечень ссылок
ВВЕДЕНИЕ
Одной из насущных проблем коксохимической промышленности является проблема расширения сырьевой базы коксования путем привлечения в шихту для коксования угля низкой спекаемости (газового и слабоспекающегося), вместо дефицитного хорошо спекающегося. Для решения этой проблемы используют разные методы подготовки угольной шихты для коксования, в частности – уплотнение угольной загрузки путем ее частичного брикетирования. Наиболее эффективным представляется брикетирование шихты со связующим веществом: добавка связующего вещества обеспечивает получение крепких брикетов, снижая тем самым часть шихты, которая поддается брикетированию, и повышает спекаемость частично брикетированной шихты, что должно способствовать увеличению прочности кокса из нее. В качестве связующих веществ применяются каменноугольный пек и битумы. Однако эти продукты используются в других весьма важных отраслях промышленности. В то же время ежегодно на коксохимических заводах образуется значительное количество смолистых отходов, которые не находят, в большей части должного применения. Отсутствие эффективного способа утилизации смолистых отходов является основной причиной того, что на большинстве коксохимические заводов эти отходы вывозят в отвал. Хотя это более простой и относительно дешевый способ уничтожения отходов, однако в связи с изменением требований к охране окружающей среды, он не может применяться в будущем.
Приходится констатировать, что и другие способы уничтожения отходов (захоронение, сжигание биоразложения) в данном случае являются абсолютно неэффективными.
Проводились исследования посвященные возможности использования смолистых отходов коксохимического производства в качестве связующего вещества для частичного брикетирования угольной шихты.
Актуальность темы: Использование отходов производства является достаточно актуальным вопросом, так как одной из насущных проблем коксохимических предприятий является проблема утилизации смолянистых отходов производства, которые не находят применения. Отсутствие эффективного способа утилизации отходов является основной причиной того, что их вывозят в отвал. Однако экологическая ситуация в будущем не позволит утилизировать отходы таким способом.
Научной значимостью является возможность использования отходов коксохимического производства в качестве связующего вещества при частичном брикетировании угольной шихты перед коксованием и получении качественного кокса.
Практическая ценность результатов работы: получение кокса с использованием отходов коксохимического производства необходимого качества.
1 ЛИТЕРАТУРНЫЙ ОБЗОР
Современная угольная сырьевая база очень непостоянная по марочному составу и технологическим свойствам, уголь неравномерно поставляется на заводы, а шихта для коксования является многокомпонентной. На дестабилизацию качественных показателей шихты заметно влияют поставки бинарных смесей состава марок Г + Ж, которые колеблются. Кроме того, на заводы прибывает до 10–15% угля внеплановых поставок, марочная структура которых отличается от плановой пониженным содержанием хорошо спекающегося угля. Колебания качественных показателей шихты не могут быть ликвидированы только путем организационных мероприятий в угольной промышленности. Потому проблема получения доменного кокса из шихты современного марочного состава, который колеблется, с повышенным участием слабоспекающегося угля и угля, который не спекается, при слоевом процессе коксования может быть решена только путем внедрения новых эффективных технологических процессов подготовки этой шихты с повышением плотности загрузки. Одним из таких процессов является процесс частичного брикетирования шихты со связующим [1, c. 179-182].
Технологическая эффективность коксования трамбуемой шихты обусловлена одним основным фактором – сокращением расстояния между отдельными частицами уплотняющегося в 1,4–1,5 раза угольного пирога. В результате облегчается равномерное деление и смачивание поверхности разнохарактерных угольных зерен жидкой фазой пластичной угольной массы, создаются благоприятные условия протекания реакций распада – синтеза, снижается усадка структуры полукокса, кокса, который образуется. То есть во всем массиве коксуемой загрузки улучшаются условия спекания угольных зерен разного размера и степени метаморфизма, что по своему технологическому эффекту равнозначно повышению спекаемости начальной угольной шихты. Эффективность коксования частично брикетированных шихты в значительной степени также определяется увеличением плотности коксуемой угольной загрузки [4, c. 10-18].
Наиболее существенное заключается в том, что частично брикетированная угольная шихта очень неоднородная по плотности, повышение которой в целом обусловлено введением в шихту брикетов с высокой плотностью. Потому эффект улучшения спекаемости, характерный для шихты, уплотненной трамбованием, оказывается прежде всего для брикетированной части шихты. Другое отличие технологии частичного брикетирования шихты – дополнительный эффект связующего как спекающей добавки для брикетированной части шихты. Но этим роль связующего не ограничивается. Связующее также инициирует вспучивание брикетов, первичный объем которых растет при коксовании у 1,2–1,6 раза в зависимости от вида связующего. В результате дополнительно уплотняется не брикетированная шихта в промежутках между брикетами (при 30% брикетов в шихте и увеличении их объема у 1,3 раза на ~ 0,6 г/см3), то есть улучшается ее спекаемость [5, c. 143-149].
Исследования в этом направлении велись во многих странах (КНР, Венгрии, Индии, США, Австралии, ЮАР). В промышленных условиях метод брикетирования шихты применяется в ФРГ (без связующего) и особенно широко в Японии (со связующим) [3, c. 12-13].
Наиболее важные вопросы, которые возникают при разработке этого метода и требуют изучения и решения:
– эффективный марочный состав шихты;
– повышение насыпной плотности шихты и производительности коксовых печей;
– часть брикетирования;
– эффективность брикетирования части шихты или угольных смесей;
– выбор связующих веществ и их части в брикетах;
– эффективность брикетирования без связующего и со связующим [6, c. 24-27].
Эффективность всех новых методов подготовки угольной шихты перед коксованием, в том числе и брикетирование, в значительной мере обусловлена повышением плотности угольной загрузки в печных камерах. При этом повышение плотности не только служит средством увеличения производительности печей, но и улучшает условия спекания продуктов деструкции угольных зерен разной крупности и степени метаморфизма, а следовательно, механической прочности кокса.
Частичное брикетирование является способом уплотнения угольной шихты и добавки связующих веществ. Увеличение плотности шихты при этом составляет 800–870 кг/м3, приводит к повышению прочности кокса [2, c. 31].
2 ЭКСПЕРИМЕНТАЛЬНАЯ ЧАСТЬ
2.1 Коксование
Проведение испытания заключается в: приготовлении сырья для брикетирования, брикетировании и потом коксовании.
Приготовление начального сырья для производства брикетов. Суть приготовления заключается в следующем: берется навеска угольной шихты (или отдельных марок угля). В емкость помещается соответствующее количество связующего (10, 15, 20%), которое нагревается на паровой бане до температуры плавления, которая составляет ~ 90 °С (в качестве связующих веществ использовали кислую смолку, полимеры, фусы, отходы нафталина). Когда связующее вещество переходит в жидкое (расплавленное) состояние, его начинают смешивать с угольной шихтой или с отдельными марками угля. Перемешивание ведут определенное время, до полного смешивания и образования однородной массы (без комков) шихты со связующим. Далее, смеси дают остыть и приступают к брикетированию. Брикетирования проводят на ручном прессе при давлении 500 и 1000 атм. На прессе получают брикеты массой ~ 6-7 г и плотностью ~ 1,2 кг/см3.
Полученные брикеты испытывались на прочность при раздавливании. Для этого использовали тот же ручной пресс и образцовый динамометр, типа ДОСМ-0,5-3.
После приготовления брикетов приступают к коксованию, для чего брикеты смешивают с шихтой в определенной пропорции (30 % брикетов и 70% шихты). Для коксования образцов в лабораторных условиях применялся аппарат Сапожникова (пластометричний аппарат), представленный на рис. 2.1. Аппарат состоит из следующих деталей:
1 - плита, 2 - стойка, 3 - муфта для крепления рычага, 4,6 - шарнирные валики, 5 – рычаг, 7 – штемпель, 8 – стакан, 9 – трубка для термопары, 10 – пленка прижимная, 11 – дно стакана, 13 – кирпич верхний, 14 – кирпич нижний, 15 – электрод, 16 – скоба направляющая, 17 – стойка направляющая, 18 – груз, 19 – подвеска груза, 20 – стойка барабана, 21 – барабан с часовым механизмом, 22 – перо, 23 – винт установочный. Груз 18, обеспечивающий во время пластометричного испытания давление на угольную загрузку в I кг на см2.
Рисунок 2.1- Пластометрический аппарат
Электрообогрев аппарата проводится способами, обеспечивающими заданный температурный режим. Термопара для измерения температур до 750°C с соответствующим гальванометром.
Перед испытанием дно стакана, трубка для термопары и головка штемпеля должны быть тщательным образом очищены от прикоксовавшихся во время предыдущего испытания частиц.
Из асбеста толщиной 0,5–1 мм вырезают два кружка диаметром 59 мм. В них прорезают отверстия для трубки термопары.
Из миллиметровки вырезаем полоску, по ширине соответствующую высоте барабана, а по длине немного более длины его круга. На длинной стороне полосы (по кругу барабана) сверху отмечаем через каждые 10 минут деление соответствующие 0, 10, 20, 30, и т.д. до 160 минут.
В стакан вставляем дно так, чтобы оно вошло в пазы стакана полностью и центр углубления для термопары совпал с центром отверстия для термопары в прижимной планке.
Перед загрузкой угля в стакан, нижнюю часть стакана изнутри устилаем полосой фильтровальной бумаги размером 60х200 мм, на дно стакана кладем нижний асбестовый кружок (с одним отверстием). Отверстие кружка должно совпадать с углублением в днище стакана. Трубку для термопары устанавливают в углубление дна и закрепляют в вертикальном положении прижимной планкой.
Навеску шихты и брикеты загружают в стакан. После загрузки угля, из трубки для термопары снимают прижимную планку, на уголь налагают верхний асбестовый кружок, а выступающие края фильтровальной бумаги загибают поверх него. Потом в стакан ставят штемпель и опять закрепляют прижимной планкой трубку для термопары. Стакан помещают в верхний кирпич, штемпель сочленяют с рычагом и к рычагу подвешивают груз.
На барабане, соединенном с вращающим его механизмом, закрепляют изготовленную, как указанная выше, полосу миллиметровки, горизонтальные линии концов какой должны совпадать. Барабан устанавливают на штативе с таким расчетом, чтобы на миллиметровке мог расположиться график пластометричной кривой.
После того, как уголь загружен и аппарат собран, включают ток при введенном реостате. Скорость нагревания угля регулируют с помощью реостата по показаниям амперметра и гальванометра. Время отмечаем по барабану, скорость вращения которого отвечает 1 мм в минуту.
Нагрев ведем так, чтобы через 30 минут после включения тока температура достигла 250°С.
От 250°С до конца опыта (700 °С) нагрев ведем со скоростью 3 °С в минуту или 30 °С в 10 минут.
Во время проведения опыта необходимо периодически проводить продувки нагревателей воздухом, во избежание скопления газов в нагревательном пространстве и оседание на стержнях графита. При достижении 700 °С нагрев прекращаем. После того, как установка остынет, разгружаем стакан и оцениваем полученный кокс.
Характеристику твердого нелетучего остатка устанавливаем по следующим показателям:
– трещиноватость (слабо трещиноватый, трещиноватый, сильно трещиноватый);
– пористость (мало пористый или пористый, с мелкими или крупными порами);
– бахрома (низкая, средняя, высокая);
– губка (маленькая, средняя, большая, с мелкими или крупными пузырьками, полая);
– блеск (матовый, полуматовый, полублестящий, блестящий);
– цвет (светло-серый, серый, темно-серый, черный);
– сплавленность (рыхлый, спеченный, сплавленный, проплавленный).
Бахромой называют то, что образуется по краям твердого нелетучего остатка слой, который отделяется от основной массы. Губка – это сильно пористый верхний слой нелетучего остатка, который на вид напоминает застывшую пену. Наличие бахромы и губки – признак хорошей спекаемости угля [7, c. 17-25].
2.1 Определение прочности кокса
Для исследования кокса в мировой практике используют разные конструкции барабанов. Отличие их заключается в преобладании усилий, дробящих или истирающих, к глубине разрушения на конечной стадии испытания.
В Украине определения прочности кокса в производственных условиях ведут в малом и большом барабанах, а в лабораторных – копровым методом или по методу ВУХИНа.
2.2.1 Определение механической прочности тела кокса копровым методом
Суть метода определения прочности заключается в определении работы разрушения кокса, которая приходится на единицу площади, снова образуемой поверхности.
От пробы кокса, осторожно измельченного до 9–13 мм, отбирают навеску 20 г, взвешивают с точностью до 0,01 г и насыпают ровным слоем на дно стального стакана I (рис. 2.2). Стакан устанавливают на специальную подставку 2, а в стакан вставляют металлическую трубку 3, вертикальное положение которой проверяют по склону 4. После этого на исследуемую пробу сбрасывают груз 5 массой 1 кг 15 раз, так что при расстоянии от основания груза к дну стакана в 1 м осуществляется работа в 147 Дж.
Рисунок 2.2- Лабораторная установка для определения механической прочности кокса копровым методом.
1–стакан; 2–подставка; 3–трубка; 4–склон; 5–груз.
После обработки кокса описанным способом его рассеивают на ситах с отверстиями 9; 5; 2,5; 1; 0,5 мм и каждую фракция взвешивают. Полученные данные служат для подсчета индекса прочности П, который определяется работой разрушения А, которая тратится на образование единицы новой поверхности, то есть
П=dA/dS
Если рассматривать частицу кокса как шар диаметром d дм, а кажущуюся плотность принять равной 1, число частиц в каждой фракции массой а (в кг), а их поверхность в (дм2) S=6a/d
Вычитая начальную поверхность Н зерна кокса до разрушения из суммарной поверхности кокса после разрушения К получаем прирост поверхности
S1=6(∑ai/bi-∑a/b)
Индекс прочности равен
П=А/6(∑ai/bi-∑a/b), Дж/дм2
где аi – масса каждого класса рассева, г;
di – диаметр каждого класса, мм;
a – вес начальной пробы, г;
d – средний диаметр частиц начальной пробы, мм;
А=147 Дж.
За диаметр зерен каждого класса принимают среднеарифметическое значение диаметров сит, который ограничивают данный класс.
Класс –0,5 мм не учитывают, поскольку поверхность его частиц очень большая по сравнению с суммарной поверхностью других классов. Потому за начальную массу кокса принимают не 20 г, а уменьшенную на значение массы под решетного продукта после рассеивания на сите с отверстиями диаметром 0,5 мм.
Испытания образцов кокса по указанному методу показали, что индекс прочности колеблется от 35 до 100 Дж/дм2. С повышением температуры образований кокса индекс прочности увеличивается.
В случае малопрочного кокса индекс П может оказаться обезображенным (преувеличенным), поскольку в разрушаемой пробе будет особенно большое содержание класса –0,5 мм, который при расчете не учитывается.
В связи с этим прочность тела кокса целесообразно также характеризовать следующими двумя показателями, полученными при испытании кокса копровым методом: показателем сопротивления дроблению Р, который выражается выходом класса +2,5 мм (в %) и показателем истираемости И, равным выходу класса –0,5 мм (в %).
Обычно кокс нормальной прочности характеризуется следующими величинами: Р = 79-82 % ; И = 10–12 % [10, c. 19-21].
Рисунок 2.3 – Последовательность выполнения эксперимента (8 кадров, 7 повторений, размер 130 KB, сделано в MP Gif Animator)
3 ПЛАНИРОВАННЫЙ ЭКСПЕРИМЕНТ
Факторный эксперимент, осуществляют с помощью матрицы планирования, в которой используют кодируемые значения факторов [9, c. 103].
Таким образом, основной задачей исследования является определение функции отклика объекта по ортогональным планам второго порядка, а затем и оптимальных условий управления исследуемым процессом [8, c. 95].
В качествах технологических параметров процесса производства кокса с использованием брикетов и отходов производства (фусов 67%, кислой смолки 30%, полимеров 3%), которые являются наиболее важным в обеспеченные его качества, были выбраны:
– Процентное содержание связующего вещества, которое добавляется к брикетам, SV.
– Давление прессования брикетов, Р.
Ниже приведенные интервалы варьирования двух основных влияющих факторов:
Содержание связующего вещества (SV): 14-18%;
Давление (Р): 300-700 Па.
Были разработаны четыре композиционных плана для эксперимента. При которых в одном случае брикетируется шихта, во втором – уголь марки СС, в третьем – уголь марки Г, в четвертом – смесь угля марки СС и Г в равном соотношении (1:1). Один из планов представлен в таблице 1.
Таблица 1 – Ортогональный УКП для двух факторов
Факторы |
Отклики |
Кодированная форма |
Натуральная форма |
Прочность, % |
Истираемость, % |
Связующее SV, % |
Давление, атм |
Связующее SV, % |
Давление, атм |
-1 |
-1 |
10 |
300 |
35.15 |
32,29 |
0 |
-1 |
14 |
300 |
37,55 |
29,94 |
1 |
-1 |
18 |
300 |
34.17 |
33,18 |
-1 |
0 |
10 |
500 |
34.8 |
32,63 |
0 |
0 |
14 |
500 |
35.27 |
32,4 |
1 |
0 |
18 |
500 |
28.78 |
36,61 |
-1 |
1 |
10 |
700 |
34.54 |
32,95 |
0 |
1 |
14 |
700 |
35.94 |
31,31 |
1 |
1 |
18 |
700 |
31.16 |
34,19 |
После проведения факторного эксперимента были получены данные, которые обработаны в специальном программном пакете. А также получены пластометрические кривые, приведенные в рис.3.1
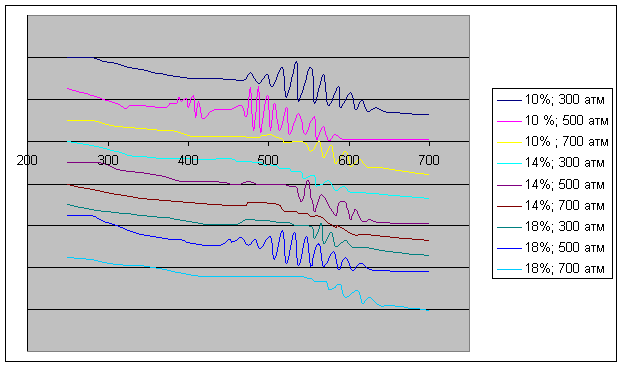 Рисунок 3.1 – Пластометрические кривые факторного эксперимента
Выполненные расчеты дали возможность получить уравнения регрессии, которые показывают связь между факторами и их комбинацией, которые характеризуют качество кокса.
Значения коэффициентов регрессии в уравнениях показывают силу влияния каждого фактора, или их комбинации на значение выходного параметра.
Проведенный статистический анализ показал, что приведенные в табл. 2 уравнения адекватны экспериментальным данным при уровне значимости 0,05. Таким образом, полученная система уравнений является достаточно точной математической моделью процесса получения кокса заданного качества.
Таблица 2 – Основные регрессионные уравнения показателей качества кокса в кодированном виде
Параметр |
Уравнение регрессии в кодированном виде |
Прочность |
Pr=35,052-1,73X1-0,872X2-3,154X1²-0,6X1X2+1,802X2² |
Истираемость |
Is=33,164+1,442X1+1,065X2+1,88X1²+0,402X1X2-0,652X2² |
Также в результате расчета были получены поверхности отклика для этих двух показателей (прочности и истираемости), которые представлены на рис. 3.2.
Рисунок 3.2 – Поверхность отклика для показателей прочности (1) и истираемости (2)
Из полученных данных видно, что наибольшая прочность (Pr) кокса составляет 37,83%, достигается при минимальном давлении (Р) (рис. 3.2) и при небольшом содержании связующего вещества (S), а наименьшая истираемость (Is) (рис. 3.2) составляет 31,30% – при минимальном давлении (P) и минимальном содержании связующего вещества (S).
ВЫВОДЫ
Способ использования отходов коксохимического производства в качествах связующего вещества при частичном брикетировании угольной шихты перед коксованием является реализованным для промышленного использования, что дает возможность использовать отходы коксохимического производства, тем самым снижая влияние отходов на окружающую среду.
По полученным коксам можно сделать вывод, что использование полимеров в качестве связующих веществ приводит к получению не достаточно крепких брикетов и мелкого кокса, а также при коксовании было сильное газовыделение, и резко изменялось давление, что видно с пластометричних кривых.
Использование фусов приводит к получению мелкого кокса, однако имеем хорошую усадку, то есть коксовый пирог хорошо будет выходить из камеры коксования, и не будет происходить забуревания печей.
Все полученные коксы являются равномерными по своей структуре, в ни одном не было заметно наличия брикетов, это говорит о том, что все брикеты хорошо спеклись.
Из полученных данных видим, что при увеличении количества связующего вещества увеличивается плотность брикетов, а с ней увеличивается насыпная плотность загрузки.
Наибольший выход кокса получили при использовании в качествах связующего вещества полимеров и кислой смолки (1:1), но при этом усадка коксового пирога не большая, а самый низкий при использовании полимеров.
ПЕРЕЧЕНЬ ССЫЛОК
- Браун Н.В., Глущенко И.М. Перспективные направления развития коксохимического производства. – М.: Металлургия, 1989. – 271с.
- Ухмылов Г.С. Освоение прогрессивных процессов расширения сырьевой базы коксования за рубежом. – М., 1987(обзорная информация ин-т «Черметинформация», серия коксохимическое производство, вып. 1, 45с.)
- Дюканов А.Г., Васильев Ю.С., Гречко Ю.И., Никитина Т.Е. Брикетирование угольных шихт перед коксованием и перспективы его совершенствования // Кокс и химия. 1990. №6. С 12-13.
- А.Г. Дюканов, Ю.И. Юрченко, Т.Е. Никитина, Ю.В. Бессчастный. Частичное брикетирование шихты и перспективы его внедрения на южных коксохимических заводах // Новые технологии в углекоксовом производстве. тематический сборник научных трудов. 1988. С 10-18.
- Повышение эффективности процесса слоевого коксования / Б.И.Мениович, С.И.Пинчук, А.Г.Дюканов. – К.: Техника, 1985. 230с.
- Глущенко И.М., Браун Н.В., Цвениашвили В.Ж., Долгих О.Ф. Исследование частичного брикетирования угольной шихты и связующих материалов для заводов Приднестровья // Кокс и химия.1988. №6. C. 24-27.
- Методические указания к лабораторному практикуму «Исследование технологических показаний твердых горючих ископаемых»./ сост.: Акимова Л.М., Новицкий П.Л. – Донецк; ДПИ, 1986. – 36с.
- Ю.П. Адлер, Е.В. Маркова, Ю.В. Грановский. Планирование эксперимента при поиске оптимальных условий. – М.: «Наука», 1976. – 280с
- Спиридонов А.А. Планирование эксперимента при планировании технологических процессов. М.: Машиностроение, 1981. – 184с.
- Н.С.Грязнов, Ю.А.Нечаев, Л.В. Копелиович, В.Г.Мищихин. К теории коксования угольных шихт при их частичном брикетировании со связующим //Кокс и химия. 1989. №6. с. 19-21.
- Патент РФ 2186823
Способ подготовки угольной шихты к коксованию.
© ДонНТУ Кныш Ю.А. 2009
|