Автореферат з теми випускної роботи
Вступ
1. Літературний огляд
2. Експериментальна частина
3. Планований експеримент
Висновки
Перелік посилань
ВСТУП
Однією з насущних проблем коксохімічної промисловості є проблема розширення сировинної бази коксування шляхом залучення в шихти вугілля низької спікливості (газового і слабоспікливого), натомість дефіцитного добре спікливого. Для вирішення цієї проблеми використовують різні методи підготовки і коксування вугільних шихт, зокрема – ущільнення вугільного завантаження шляхом її часткового брикетування. Найбільш ефективним представляється брикетування шихти з сполучною речовиною: добавка зв'язуючої речовини забезпечує отримання міцних брикетів, знижуючи тим самим частку шихти, що піддається брикетуванню, і підвищує спікливість частково брикетованої шихти, що повинно сприяти збільшенню міцності коксу з неї. У якотсті сполучної речовини застосовується кам'яновугільний пек і бітуми. Проте ці продукти використовуються і в інших важливих галузях промисловості. У той же час щорічно на коксохімічних заводах утворюється значна кількість смолянистих відходів, що не знаходять, в більшій частині цілеспрямованого застосування. Відсутність ефективного способу утилізації смолянистих відходів є основною причиною того, що на більшості коксохімічні заводів ці відходи вивозять у відвал. Хоча це і більш простій і відносно дешевий спосіб знищення відходів, проте у зв'язку із зміною вимог до охорони навколишнього середовища, він не може застосовуватися в майбутньому.
Доводиться констатувати, що і інші способи знищення відходів (захоронення, спалювання, біорозкладання) в даному випадку є абсолютно неефективними.
Проводилися дослідження присвячені можливості використання смолянистих відходів коксохімічного виробництва як добавка для часткового брикетування вугільних шихт.
Актуальність теми: використання відходів коксохімічного виробництва є актуальним вопросом, тому що однією з насущних проблем коксохімічних підприємств є проблема використання смолянистих відходів виробництва, які не використовуються. Відсутність ефективного способу утилізації даних відходів є основною причиною того, що їх вивозять в отвал. Однак екологічна ситуація у майбутньому не дозволить утилізовувати відходи таким чином.
Науковою значимістю є можливість використання відходів коксохімічного виробництва у якості зв'язуючої речовини при частковому брикетуванні вугільної шихти перед коксуванням та отримання якісного коксу.
Практична цінність результатів роботи: отримання коксу (з використанням відходів коксохімічного виробництва) необхідної якості.
1 ЛІТЕРАТУРНИЙ ОГЛЯД
Сучасна вугільна сировинна база украй непостійна по марочному складу і технологічним властивостям; вугілля нерівномірно поставляється на заводи, а шихти для коксування є багатокомпонентними. На дестабілізацію якісних показників шихти помітно впливають постачання бінарних сумішей марок Г + Ж, складу, що коливається. Крім того, на заводи прибуває до 10–15% вугілля позапланових постачань, марочна структура яких відрізняється від планової пониженим вмістом добре спікливого вугілля. Коливання якісних показників шихти не можуть бути ліквідовані тільки шляхом організаційних заходів у вугільній промисловості і вони збережуться в найближчій перспективі. Тому проблема отримання кондиційного доменного коксу з сучасних шихт марочного складу, що коливається, з підвищеною участю слабоспікливого вугілля та вугілля, що не спікається, при шаровому процесі коксування може бути вирішена тільки шляхом впровадження нових ефективних технологічних процесів підготовки цих шихт з підвищенням щільності завантаження. Одним з таких процесів є спосіб часткового брикетування шихт з тим, що пов'язує [1, c. 179-182].
Технологічна ефективність коксування трамбованих шихт обумовлена одним основним чинником – скороченням відстані між окремими частинками ущільненого в 1,4–1,5 разу вугільного пирога. В результаті полегшується рівномірний розподіл і змочування поверхні різнохарактерних вугільних зерен рідкою фазою пластичної вугільної маси, створюються сприятливі умови протікання реакцій розпаду – синтезу, знижується усадка структури напівкоксу, що утворюється, – коксу. Тобто у всьому масиві коксованого завантаження поліпшуються умови спікання вугільних зерен різної крупнини і ступеня метаморфізму, що по своєму технологічному ефекту рівнозначно підвищенню спікливості початкових вугільних шихт.
Ефективність коксування частково брикетованих шихт в значній мірі також визначається збільшенням щільності коксованого вугільного завантаження [4, c. 10-18].
Найбільш істотне полягає в тому, що коксована частково брикетована шихта украй неоднорідна по щільності, підвищення якої в цілому обумовлене введенням в шихту високощільних брикетів. Тому ефект поліпшення спікливості, характерний для шихт, ущільнених трамбуванням, виявляється перш за все для брикетованої частини шихти.
Інша відмінність технології часткового брикетування шихти – додатковий ефект того, що пов'язує як спікливої добавки для брикетованої частини шихти. Але цим роль того, що пов'язує не обмежується.
Зв'язуючє також ініціює спучення брикетів, первинний об'єм яких зростає при коксуванні в 1,2-1,6 разу залежно від виду того, що пов'язує. В результаті додатково ущільнюється не брикетована шихта в проміжках між брикетами (при 30% брикетів в шихті і збільшенні їх об'єму в 1,3 разу на ~ 0,6 г/см3), тобто поліпшується її спікливість [5, c. 143-149].
Дослідження в цьому напрямі велися в багатьох країнах (ПНР, Угорщини, Індії, США, Австралії, ЮАР). У промислових умовах метод брикетування шихт застосовується у ФРН (без того, що пов'язує) і особливо широко в Японії (з тим, що пов'язує) [3, c. 12-13].
Найбільш важливі питання, що виникають при розробці цього методу і вимагають вивчення і рішення:
- Ефективний марочний склад шихти;
- Підвищення насипної щільності шихти і продуктивності коксових печей;
- Частка брикетування;
- Ефективність брикетування частини шихти або вугільних сумішей;
- Вибір зв'язуючих речовин і їх частка в брикетах;
- Ефективність брикетування без того, що пов'язує і з тим, що пов'язує [6, c. 24-27].
Ефективність всіх нових методів підготовки вугільних шихт перед коксуванням, у тому числі і брикетування, значною мірою обумовлена підвищенням щільності вугільного завантаження в пічних камерах. При цьому підвищення щільності не тільки служить засобом збільшення продуктивності печей, але і покращує умови спікання продуктів деструкції вугільних зерен різної велечини і ступеня метаморфізму, а отже, механічну міцність коксу.
Часткове брикетування є способом ущільнення вугільної шихти і добавки зв'язуючих речовин. Збільшення щільності шихти при цьому становить 800-870 кг/м3, приводить до підвищення міцності коксу [2, c. 31].
2 ЕКСПЕРИМЕНТАЛЬНА ЧАСТИНА
2.1 Коксування
Проведення випробування полягає в: приготуванні сировини для брикетування, потім саме брикетування і потім коксування.
Приготування початкової сировини для виробництва брикетів.
Суть приготування полягає в наступному:
Береться навішування вугільної шихти (або окремих марок вугілля).
У ємність поміщається відповідна кількість того, що пов'язує (10, 15, 20%), яка нагрівається на паровій бані до температури розплавлення, яка складає ~ 90 °С (у якості речовини що пов’язує використовували кислу смолку, полімери, фуси, відходи нафталіну). Коли зв'язуюча речовина переходить в рідкий (розплавлений) стан, її починають змішувати з вугільною шихтою або з окремими марками вугілля. Перемішування ведуть певний час, до повного змішування і утворення однорідної маси (без грудок) шихти з тим, що пов'язує. Далі суміші дають остигнути і приступають до брикетування. Брикетування проводять на ручному пресі при тиску 500 і 1000 атм. На пресі одержують брикети масою ~ 6-7 г і щільністю ~ 1,2 кг/см3.
Одержані брикети випробовувалися на міцність при роздавлюванні. Для цього використовували той же ручний прес і динамометр зразковий, типу ДОСМ-0,5-3.
Після приготування брикетів приступають до коксування, для чого брикети змішують з шихтою в певній пропорції (30 % брикетів і 70% шихти).
Для коксування зразків в лабораторних умовах застосовувався апарат Сапожникова (пластометричний апарат), представлений на рис. 2.1, що складається з наступних деталей:
1 - плита, 2 - стійка, 3 - муфта для кріплення важеля, 4,6 - шарнірні валики, 5 - важіль, 7 – штемпель, 8 – стакан, 9 – трубка для термопари, 10 – плівка притискна, 11 – дно стакана, 13 – цеглина верхня, 14 – цеглина нижня, 15 – електрод, 16 – скоба, що направляє, 17 – стійка, що направляє, 16 – вантаж, 19 – підвіска вантажу, 20 – стійка барабана, 21 – барабан з годинниковим механізмом, 22 – перо, 23 – гвинт настановний.
Вантаж 18, що забезпечує під час пластометричного випробування тиск на вугільне завантаження в I кг на см2 .
Рисунок 2.1 – Пластометрічний апарат.
Електрообігрів апарату проводиться способами, що забезпечують заданий температурний режим. Термопара для виміру температур до 750°C з відповідним гальванометром.
Перед випробуванням, дно стакана, трубка для термопари і головка штемпеля повинні бути ретельно очищені від прикоксовавшихся під час попереднього випробування частинок.
З азбесту завтовшки 0,5-1 мм вирізують два кружки діаметром 59 мм. У них прорізають отвори для трубки термопари.
З міліметрівки вирізуємо смужку, по ширині відповідну висоті барабана, а по довжині трохи більш довжини його кола. На довгій стороні смуги (по колу барабана) зверху відзначаємо через кожні 10 хв. ділення відповідні 0, 10, 20, 30, і т.д. до 160 хв.
У стакан вставляємо дно так, щоб воно увійшло до пазів стакана повністю і центр поглиблення для термопари співпав з центром отвору для термопари в притискній планці.
Перед завантаженням вугілля в стакан, нижню частину стакана зсередини вистилаємо смугою фільтрувального паперу розміром 60х200 мм, на дно стакана кладемо нижній азбестовий кружок (з одним отвором). Отвір кружка повинен співпадати з поглибленням в дні стакана. Трубку для термопари встановлюють в поглиблення дна і закріплюють у вертикальному положенні притискною планкою.
Навішування шихти і брикетів завантажують в стакан. Після завантаження вугілля, з трубки для термопари знімають притискну планку, на вугілля накладають верхній азбестовий кружок, а виступаючі краї фільтрувального паперу загинають поверх, його. Потім в стакан ставлять штемпель і знову закріплюють притискною планкою трубку для термопари. Стакан поміщають у верхню цеглину, штемпель зчленовують з важелем і до важеля підвішують вантаж.
На барабані, сполученому з обертаючим його механізмом, закріплюють виготовлену, як вказано вищє, смугу міліметрівки, горизонтальні лінії кінців якої повинні співпадати. Барабан встановлюють на штативі з таким розрахунком, щоб на міліметрівці міг розташуватися графік пластометричної кривої.
Після того, як вугілля завантажене і апарат зібраний, включають струм при введеному реостаті. Швидкість нагрівання вугілля регулюють за допомогою реостата за свідченнями амперметра і гальванометра. Час відмічаємо по барабану, швидкість обертання якого відповідає 1 мм в хвилину.
Нагрів ведемо так, щоб через 30 хв після включення струму температура досягла 250°С.
Від 250°С до кінця досвіду (700 °С) нагрів ведемо із швидкістю 3°С в хвилину або 30°С в 10 хвилин.
Під час проведення досвіду необхідно періодично проводити продування нагрівачів повітрям, щоб уникнути скупчення газів в нагрівальному просторі і осідання на стрижнях графіту. Досягши 700°С нагрів припиняємо. Після того, як установка остигне, розвантажуємо стакан і оцінюємо отриманий кокс.
Характеристику твердого нелеткого залишку встановлюємо за наступними показниками:
тріщинуватість (слабо тріщинуватий, тріщинуватий, сильно тріщинуватий);
пористість (мало пористий або пористий, з дрібними або крупними порами);
бахрома (низька, середня, висока);
губка (маленька, середня, велика, з дрібними або крупними бульбашками, порожниста);
блиск (матовий, напівматовий, напівблискучий, блискучий);
колір (світло-сірий, сірий, темно-сірий, чорний);
сплавленість (рихлий, спечений, сплавлений, проплавлений).
Бахромою називають те, що утворюється по краях твердого нелеткого залишку, шар, який відділяється від основної маси. Губка – це сильно пористий верхній шар нелеткого залишку, який на вигляд нагадує застиглу піну. Наявність бахроми і губки – ознака хорошої спікливості вугілля [7, c. 17-25].
2.1 Визначення міцності коксу
Для дослідження коксу у світовій практиці використовують різні конструкції барабанів. Відмінність їх полягає в переважанні зусиль, що дроблять або стираючих, до глибини руйнування на кінцевій стадії випробування.
В Україні визначення міцності коксу у виробничих умовах ведуть в малому і великому барабанах, а в лабораторних – копровим методом або по методу ВУХІНа.
2.2.1 Визначення механічної міцності тіла коксу копровим методом
Суть методу визначення міцності полягає у визначенні роботи руйнування коксу, що доводиться на одиницю площі, знов утворюваної поверхні.
Від проби коксу, обережно подрібненого до 9-13 мм, відбирають навішування 20 г, зважують з точністю до 0,01 г і насипають рівним шаром, на дно сталевого стакана I (рис. 2.2). Стакан встановлюють на спеціальну підставку 2, а в стакан вставляють металеву трубку 3, вертикальне положення якої перевіряють по схилу 4. Після цього на досліджувану пробу скидають вантаж 5 масою I кг 15 разів, так що при відстані від підстави вантажу до дна стакана в 1 м здійснюється робота в 147 Дж.
Рисунок 2.2- Лабораторна установка для визначення механічної міцності коксу копровим методом.
1 – стакан; 2 – підставка; 3 – трубка; 4 – схил; 5 – вантаж.
Після обробки коксу описаним способом його розсіюють на ситах з отворами 9; 5; 2,5; I; 0,5 мм і кожну фракцію зважують. Одержані дані служать для підрахунку індексу міцності П, який визначається роботою руйнування А, одиниці нової поверхні, що витрачається на утворення, тобто
П=dA/dS
Якщо розглядати частинку коксу як кулю діаметром d дм, а щільність, що здається, прийняти рівною 1, число частинок в кожній фракції масою а (у кг), то їх поверхня в (дм2) S=6a/d
Віднімаючи початкову поверхню Н зерна коксу до руйнування з сумарної поверхні коксу після руйнування К одержуємо приріст поверхні
S1=6(∑ai/bi-∑a/b)
Індекс міцності рівний
П=А/6(∑ai/bi-∑a/b), Дж/дм2
де аi–маса кожного класу розсівання, г;
di–діаметр кодного класу, мм;
a–вага початкової проби, г;
d–середній діаметр частинок початкової проби, мм;
А=147 Дж.
За діаметр зерен кожного класу приймають середньоарифметичне значення діаметрів сит, що обмежують даний клас.
Клас – 0,5 мм не враховують, оскільки поверхня його частинок дуже велика в порівнянні з сумарною поверхнею інших класів. Тому за початкову масу коксу приймають не 20 г, а зменшену на значення маси під решітного продукту після розсівання на ситі з отворами діаметром 0,5 мм.
Випробування зразків коксу по вказаному методу показали, що індекс міцності коливається від 35 до 100 Дж/дм2. З підвищенням температури утворень коксу індекс міцності збільшується.
У разі маломіцного коксу індекс П може виявитися спотвореним (перебільшеним), оскільки в руйнованій пробі буде особливо великий зміст класу -0,5 мм, який при розрахунку не враховується.
У зв'язку з цим міцність тіла коксу доцільно також характеризувати наступними двома показниками, отриманими при випробуванні коксу копровий методом: показником опору дробленню Р, який виражається виходом класу +2,5 мм (в %) і показником стиранності И, рівним виходу класу – 0,5 мм (у %).
Звичайно кокс нормальної міцності характеризується наступними величинами: Р = 79-82 % ; И = 10-12 % [10, c. 19-21].
Рисунок 2.3 - Послідовність експерименту (8 кадрів, кількість повторень 7, розмір 130 КВ, зроблено в MP Gif Animator)
3 ПЛАНОВАНИЙ ЕКСПЕРИМЕНТ
Факторний експеримент, здійснюють за допомогою матриці планування, в якій використовують кодовані значення факторів [9, c. 103].
Таким чином, основною задачею дослідження є визначення функції відгуку об’єкта по ортогональним планам другого порядку, а потім оптимальних умов управління досліджуваним процесом [8, c. 95].
У якості технологічних параметрів процесу виробництва коксу з використанням брикетів та відходів виробництва (фусів 67%, кислої смолки 30%, полімерів 3%), що є найбільш важливими у забезпечені його якості, були обрані:
- Відсотковий вміст пов’язуючої речовини, що додається до брикетів, SV.
- Тиск пресування брикетів, Р.
Нижче приведені інтервали варіювання двох основних впливових факторів:
- Вміст пов’язуючої речовини (SV): 14–18%;
- Тиск (Р): 300–700 атм;
Було розроблено чотири композиційні плани для експерименту. При яких в одному випадку брикетується шихта, у другому – вугілля марки СС, у третьому – вугілля марки Г, у четвертому – суміш вугілля марки СС та Г у рівному співвідношенні (1:1). Ці плани представлені у таблиці 1.
Таблиця 1 – Ортогональний УКП для двох факторів
Фактори |
Відгуки |
Кодована форма |
Натуральна форма |
Міцність, % |
Стиранність, % |
Зв’язуюче SV, % |
Тиск, атм |
Зв’язуючє SV, % |
Тиск, атм |
-1 |
-1 |
10 |
300 |
35.15 |
32,29 |
0 |
-1 |
14 |
300 |
37,55 |
29,94 |
1 |
-1 |
18 |
300 |
34.17 |
33,18 |
-1 |
0 |
10 |
500 |
34.8 |
32,63 |
0 |
0 |
14 |
500 |
35.27 |
32,4 |
1 |
0 |
18 |
500 |
28.78 |
36,61 |
-1 |
1 |
10 |
700 |
34.54 |
32,95 |
0 |
1 |
14 |
700 |
35.94 |
31,31 |
1 |
1 |
18 |
700 |
31.16 |
34,19 |
Після проведення факторного експерименту були отримані дані, які були оброблені в спеціальному програмному пакеті. А також отримані пластометричні криві, приведені на рис. 3.1
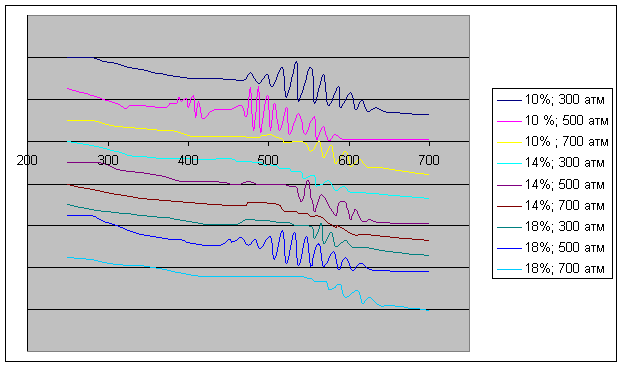 Рисунок 3.1 – Пластометричні криві факторного експерименту
Виконані розрахунки дали можливість отримати рівняння регресії, які показують зв'язок між факторами та їх комбінацією, що характеризують якість коксу.
Значення коефіцієнтів регресії у рівняннях показують силу впливу кожного фактора, або їх комбінації на значення вихідного параметру.
Проведений статистичний аналіз показав, що приведені в табл. 2 рівняння адекватні експериментальним даним при рівні значимості 0,05. Таким чином, отримана система рівнянь є достатньо точною математичною моделлю процесу отримання коксу задоної якості.
Таблиця 2 – Основні регресійні рівняння показників якості коксу в кодованому виді
Параметр |
Рівняння регресії в кодованому виді |
Міцність |
Pr=35,052-1,73X1-0,872X2-3,154X1²-0,6X1X2+1,802X2² |
Стиранність |
Is=33,164+1,442X1+1,065X2+1,88X1²+0,402X1X2-0,652X2² |
Також в ррезультаті розрахунку були отримані поверхні відгуку для цих двох показників (міцності та стиранності), які представлені на рис. 3.2.
Рисунок 3.2 – Поверхня відгуку для показників міцності (1) та стиранності (2)
З отриманих даних видно, що найбільша міцність (Pr) коксу складає 37,83%, що досягається при мінімальному тиску (Р) (рис. 3.2) та при невиликому вмісті пов'язуючої речовини (S), а найменша стиранність (Is) (рис. 3.2) складає 31,30% – при мінимальному тиску (P) и мінімальному вмісті пов'язуючої речовини (S).
ВИСНОВКИ
Спосіб використання відходів коксохімічного виробництва у якості пов'язуючої речовини при частковому брикетуванні вугільної шихти перед коксуванням є реалізованим для промислового використання, що дає можливість використовувати відходи коксохімічного виробництва, тим самим знижуючи вплив відходів на навколишнє середовищє. По отриманих коксах можна зробити висновок, що використання полімерів як зв’язуючих речовини приводить к отриманню не досить міцних брикетів та дрібного коксу, а також при коксуванні було сильне газовиділення, та різко змінювався тиск, що видно з пластометричних кривих.
Використання фусів приводить до отримання дрібного коксу, однак маемо хорошу усадку, тобто коксовий пиріг добре буде виходить з камери коксування, та не буде відбуватися збурювання печей.
Усі отримані кокси є рівномірними по своїй структурі, в жодному не було помітно наявності брикетів, це говорить про те, що всі брикети добре спеклися.
З отриманих даних бачимо, що при збільшенні кількості зв’язуючої речовини збільшується щільність брикетів, а з нею збільшується насипна щільність завантаження.
Найбільший вихід коксу отримали при використанні у якості зв’язуючої речовини полімерів та кислої смолки (1:1), але при цьому усадка коксового пірога не велика, а найнижчий при використанні полімерів, як зв’язуючої речовини.
ПЕРЕЛІК ПОСИЛАНЬ
- Браун Н.В., Глущенко И.М. Перспективные направления развития коксохимического производства. – М.: Металлургия, 1989. – 271с.
- Ухмылов Г.С. Освоение прогрессивных процессов расширения сырьевой базы коксования за рубежом. – М., 1987(обзорная информация ин-т «Черметинформация», серия коксохимическое производство, вып. 1, 45с.)
- Дюканов А.Г., Васильев Ю.С., Гречко Ю.И., Никитина Т.Е. Брикетирование угольных шихт перед коксованием и перспективы егосовершенствования // Кокс и химия. 1990. №6. С 12-13.
- А.Г. Дюканов, Ю.И. Юрченко, Т.Е. Никитина, Ю.В. Бессчастный Частичное брикетирование шихты и перспективы его внедрения на южных коксохимических заводах // Новые технологии в углекоксовом производстве. тематический сборник научных трудов. 1988. С 10-18.
- Повышение эффективности процесса слоевого коксования / Б.И.Мениович, С.И.Пинчук, А.Г.Дюканов. – К.: Техника, 1985. 230с.
- Глущенко И.М., Браун Н.В., Цвениашвили В.Ж., Долгих О.Ф. Исследование частичного брикетирования угольной шихты и связующих материалов для заводов Приднестровья // Кокс и химия.1988. №6. C. 24-27.
- Методические указания к лабораторному практикуму «Исследование технологических показаний твердых горючих ископаемых»./ сост.: Акимова Л.М., Новицкий П.Л. – Донецк; ДПИ, 1986. – 36с.
- Ю.П. Адлер, Е.В. Маркова, Ю.В. Грановский. Планирование эксперимента при поиске оптимальных условий. – М.: «Наука», 1976. – 280с
- Спиридонов А.А. Планирование эксперимента при планировании технологических процессов. М.: Машиностроение, 1981. – 184с.
- Н.С.Грязнов, Ю.А.Нечаев, Л.В. Копелиович, В.Г.Мищихин. К теории коксования угольных шихт при их частичном брикетировании со связующим //Кокс и химия. 1989. №6. с. 19-21.
- Патент РФ 2186823
Способ подготовки угольной шихты к коксованию.
© ДонНТУ Книш Ю.О. 2009
|