Реферат по теме выпускной работы
Актуальность темы
Нарастающий дефицит и постоянное удорожание коксующихся углей может стать сегодня мощным стимулом к развитию бескоксовой металлургии – направления, связанного с разработкой новых способов получения железа из руд, исключающих использование кокса, что позволит снизить затраты топливных ресурсов, улучшить и ускорить процесс плавления, сократить выбросы пыли и токсичных соединений. Это приведет к снижению себестоимости продукции и снижению вредного воздействия на окружающую природную среду.
Цель и задачи дипломной работы:
Отразить актуальность сравнения эколого-экономических показателей альтернативных процессов коксовой и безкоксовой металлургии, необходимость разработки рекомендаций по развитию элементов бескоксовой металлургии в Украине.
Новизна работы
Новизна работы заключается в том, что предлагаются для внедрения в доменное производство современные технологии, которые позволяют достичь планируемых целей и задач этой работы.
Практическая значимость результатов
Результат данной работы — разработка технологических методов для внедрения в условиях доменного производства. Использование этих методов позволит предприятию организовать более эффективное производство чугуна, обеспечив минимальное негативное воздействие производства на окружающую среду, позволит снизить возможные экологические платежи за выбросы, снизит себестоимость продукции за счет снижения энергозатрат и уменьшения экологических выплат.
Введение
Черная металлургия, бесспорно, относится к отраслям повышенной экологической опасности, поэтому в предлагаемой узкому кругу читателей- специалистов металлургического профиля – магистерской дипломной работе сделана одна из первых попыток сравнительного анализа ресурсо – экологических и иных характеристик производства первичного металла в менее экологичных доменных печах и более логичных экономичных агрегатах прямого восстановления железа из руд.
Этим обусловлена высокая природоохранная актуальность дипломной работы. В экологических оценках принимают участие производства, сопряженные с конкурирующими агрегатами (доменная печь – агрегат прямого восстановления железа) и обеспечивающие не только поставки сырья, топлива, других ресурсов, но и выпуск готовой металлопродукции.
В ХХI веке и, по – видимому, в более отдаленной перспективе основное количество черных металлов будут производить по традиционной высокопроизводительной схеме двойного передела «доменная печь – конвертер или иной сталеплавильный агрегат». В течение более двух веков производство по схеме «чугун – сталь» настолько радикально модернизировано и достигло больших высот в основном по линиям роста производительности и экономической эффективности процессов, что доля основной – конверторной стали многие десятилетия будущего вряд ли составит менее 70% от общей ее выплавки. Однако для этой схемы производства характерны колоссальные вредные выбросы (например в условиях изношенных и морально устаревших предприятий Украины) которые обусловлены не только состоянием агрегатов но и самой сутью производства кокса и агломерата, пока почти фатально необходимых для выплавки первичного металла – передельного чугуна. Металлургический кокс является энергетической базой всей мировой, так называемой коксовой черной металлургии, а его производство характеризуется большим набором ядовитых и зловонных выбросов. Вредные выбросы агломерации почти не пахнут, но абсолютное их количество очень велико. На долю триады «коксовое – агломерационное доменное производство» приходится более 70 – 80% выбросов пыли, оксидов углерода, серы, сероводорода, аммиака, фенолов, бензолов, диоксинов, фуранов и прочих супертоксичных веществ. Этим трем, принадлежащим металлургическому комбинату производствам, предопределена длительная перспектива развития, поэтому так остро необходимы кардинальные меры их экологической модернизации.
Альтернативный способ прямого получения металла из руд («руда» - обобщенное понятие, включающее концентрат, мелкую руду, агломерат, окатыши, железосодержащие отходы) очень привлекает своей повышенной экологичностью: ему не нужны кокс и агломерат.
В связи с изложенными мобилизующими соображениями задачами исследований в дипломной работе являются:
- общая характеристика процессов, сравнение экологических показателей вредных выбросов, ресурсопотребления при производстве первичного металла по двум упомянутым схемам, в том числе сравнение основных показателей экологических балансов по схемам производства металлопродукции (проката) «кокс – агломерат – чугун – конвертертерная сталь», «метализованные окатыши – конвертер» и «метализованные окатыши – электросталь».
- разработка комплексных мероприятий по экологизации процессов схемы «кокс – агломерат – чугун – конвертертерная сталь».
Основной целью работы является повышение экологической безопасности производства первичного металла, как по традиционной схеме, так и по варианту прямого извлечения железа из руд. Ориентировочное снижение газопылевых выбросов при комплексной схеме модернизированного производства первичного металла (доля метализованных окатышей вероятно достигнет 10 – 15% от выплавки чугуна на предприятиях Украины) может превысить 30 – 50% ныне существующих выбросов отрасли.
Обзор исследований по теме в ДонНТУ
Перспективы развития технологий прямого восстановления.
Более трех тысяч лет назад возник самый древний способ получения железа — сыродутный процесс. Позднее появились более экономичные, более производительные способы, но они оказались связаны с необходимостью промежуточного этапа получения чугуна. Однако идея создания рентабельного про¬цесса получения железа непосредственно из руд другими, более совер¬шенными по сравнению с сыродутным способами не умерла. Всплеск интереса к реализации этой идеи относится к 1931 —1934 гг., когда на крупповских заводах в Германии был осуществлен в промышленных масштабах крупповский сыродутный процесс (Krupp-Renn-verfahren).
Процесс осуществлялся во вращающихся наклонных футерованных трубчатых печах, в которые с одной стороны загружали угольную или коксовую мелочь, железную руду, колошниковую пыль и т. д., а с другой стороны (там, где выдавалась готовая крица) были установлены горелки для сжигания топливоугольной пыли.
Температура в зоне образования крицы достигала 1250-1350С. Таких установок в мире в предвоенные годы и годы второй мировой войны работало несколько десятков.
Практика показала нерентабельность этих установок из-за низкой производительности, их неэкономичности и производственных трудностей (нередки случаи размягчения кусков крицы, слипания и налипания на стенки агрегата). Кроме установок такого типа определенное распространение получили установки по методу Виберга и завода «Хаганес» (Швеция) и некоторые другие.
Все эти способы получили ограниченное распространение. Однако теперь многие фирмы и институты ряда стран ведут интенсивные изыскания в этом направлении, что вызвано рядом причин.
1. Возможность получения железа непосредственно из руд меняет в корне всю технологическую цепочку современной металлургии. На рис.1 схематично показано сравнение обычной технологии получения чугуна и технологии по методу COREX. При работе агрегата COREX (или ROMELT, или другого подобного) нет необходимости сооружать коксовые батареии агломерационные фабрики, отсутствуют затраты на поиски коксующихся углей и получение кокса.
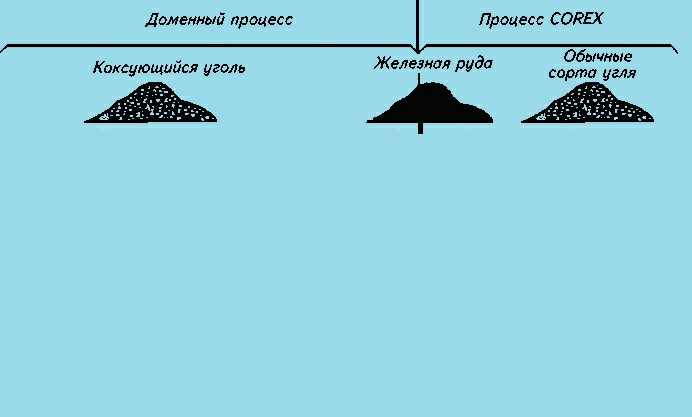
2. Коксохимические предприятия и агломерационные фабрики дают наибольшее количество выбросов газов и пыли в атмосферу, потребляют значительные массы воды и занимают большие площади земельных угодий; это наиболее экологически неблагополучные отрасли металлургического производства. Условия труда работающих на коксохимическом и агломерационном производствах наиболее тяжелые и вредные в черной металлургии.
3. Рациональная технология прямого получения железа позволит эффективно использовать полезные компоненты в природнолегирован-ных рудах
.4. Рациональная технология получения железа непосредственно из руд позволяет решать очень серьезную проблему организации производства чистых от примесей цветных металлов марок стали. Кроме того, при наличии чистых шихтовых материалов можно по мере необходимости «разбавлять» состоящую из металлолома «грязную» (по примесям цветных металлов) шихту.
5. Агрегаты жидкофазного восстановления (в частности, типа ROMELT) обеспечивают эффективную переработку шлаков, шламов и других отходов, содержащих ценные компоненты.
Пока еще затруднительно окончательно оценить результаты ведущихся во многих странах исследований в этом направлении. Технологии
К настоящему времени имеется значительное число технологий бескоксового производства металла, получивших промышленное распространение. Все их можно классифицировать следующим образом:
• процессы жидкофазного восстановления,
• процессы твердофазного восстановления,
• комбинированные процессы.Процессы жидкофазного восстановления пока не получили значительного распространения, однако имеют неплохие перспективы.
Среди процессов жидкофазного восстановления выделяется процесс `Ромелт`, разработанный в Московском институте стали и сплавов (МИСиС) под руководством профессора В. А. Роменца и реализованный в 1985 году на полупромышленной установке в Липецке. Одностадийный процесс жидкофазного восстановления `Ромелт` обеспечивает переработку железосодержащих материалов (в виде пыли железной руды, шлаков, шламов) с применением некоксующихся углей.
Разработанная технология позволяет получить чугун, отличающийся от доменного пониженным содержанием кремния и марганца (0,05-0,15%). Она не требует применения кокса и позволяет использовать в качестве основного топлива неподготовленные энергетические угли с различным содержанием летучих веществ (до 35-40%), дает возможность перерабатывать любые виды мелкого (не более 20 мм) железосодержащего сырья (руду, концентрат, пыль, шлам, окалину, стружку) без предварительного окускования и при относительно низком содержании железа.
Производительность процесса достигает 300-400 тыс. т в год, что позволяет использовать его в условиях малого производства. Агрегат жидкофазного восстановления более компактен, чем агрегат твердофазного восстановления. К недостаткам данного процесса следует отнести пониженный по сравнению с доменным процессом тепловой КПД и низкую скорость восстановления.Среди процессов твердофазного восстановления следует особо отметить процесс Midrex, разработанный в 1965 - 1967 годах американской компанией Midland Ross. Первые две шахтные печи производительностью по 200 тыс. т в год были запущены в 1969 году в Портланде (США). В 80-е годы на ОЭМК (Россия) был построен крупнейший в Европе цех с 4 печами Midrex с проектной производительностью 1,7 млн. т в год. В качестве железорудного материала здесь используется кусковая руда, окатыши или агломерат, а в качестве восстановителя – природный газ.
Преимуществом данного процесса является повышенная чистота окатышей по сере, фосфору и пониженное содержание углерода в окатышах. Производительность достигает 4 млн. т в год. Весь цикл восстановления занимает 8-12 часов.
Среди комбинированных процессов следует выделить процесс Соrех, разработанный германской фирмой Korf Stahl в 1976 году. Он сочетает в себе твердофазное и жидкофазное восстановление. В нем используются отдельные реакторы для восстановительной и плавильной стадий. Полупромышленное опробование на разных видах сырья и топлива было проведено с 1981 по 1987 годы на установке производительностью 60 тыс. т чугуна в год в Кельне (Германия). В дальнейшем технологию приобрела австрийская фирма Voest Alpine.
В основе процессов Соrех лежит концепция доменной печи, модифицированная для обеспечения возможности прямого применения некоксующихся углей для восстановления железа из кусковой руды, окатышей и агломерата.
Производительность установок достигает 700 тыс. т в год. Из-за наличия первой стадии предварительного высокого восстановления этот процесс имеет более высокий расход топлива, чем доменный. Преимущества этого и других комбинированных процессов заключаются в более рациональном использовании тепла отходящего газа и более высокой степени использования восстановителя.Наибольшее развитие бескоксовое производство стали получило в странах Латинской Америки, и Ближнего Востока. Это объясняется, в первую очередь, наличием природных ресурсов (богатых железных руд, природного газа, источников электроэнергии), а, во-вторых, дефицитом металлолома и высокими ценами на него.На сегодня в мире наиболее широко распространены технологии Midrex. Лидирующие позиции в данном сегменте рынка эта компания удерживает последние 30 лет. По технологиям Midrex в прошлом году было получено около 40 млн. т металлизированных окатышей или 60% от общемирового производства.
Крупнейшим `парком` установок Midrex владеет корпорация Arcelor Mittal, имеющая предприятия по выпуску восстановленного железа в Германии, Канаде, Мексике, Тринидаде и Тобаго и ЮАР, общие мощности которых (созданные в 1971-1999 годах) составляют около 6 млн. т в год, или 13% мирового производства губчатого железа по данной технологии.
Чугун
Напомним, что чугун получают в доменных печах восстановлением железа из железорудных материалов (агломерата, окатышей и др.). При горении кокса идут реакции
С + О2 + 3,762N2 = С02 + 3,762N2,
С + СО2 + 3,762N2 = 2CO + 3,762N2.
При частичном обогащении возду¬ха кислородом коэффициент 3,762 соответственно уменьшается (это соотношение долей азота и кислорода в воздухе:
79/21 = 3,762).
В области высоких температур при наличии углерода идет реакция:
С02 + С = 2СО.
Образующийся оксид СО — восстановитель, и атмосфера в доменной печи восстановительная. В зоне высоких температур идет прямая реакция восстановления железа углеродом кокса:
FeO + С = Fe + СО - Q.
Степень восстановления железа в доменной печи 99—99,9 %, поэтому доменный шлак содержит < 1 % FeO. В восстановительных условиях печи восстанавливаются и другие оксиды, поступающие в доменную печь с шихтой (оксиды кремния, марганца, фосфора и др.):
SiO2 + 2С = [Si] + 2CO - Q,
МпО + С = [Мп] + СО - Q,
ЗСаО • Р2О5 + 5С = 2[Р] + ЗСаО + SCO - Q.
Используемый в доменной печи кокс содержит некоторое количество серы. Сера содержится и в железоруд¬ных материалах (в виде FeS, CaS, CaSO3). Около 10 % содержащейся в шихте серы удаляется из печи вместе с газами.
Оставшаяся сера распределя¬ется между металлом (чугуном) и шлаком в соответствии с коэффициентом распределения LS = (S)/[S], величина которого в значительной мере зависит от основности шлака:
[S] + Реш+ (СаО) = (CaS) + (FeO).
При наличии в доменной шихте оксидов марганца возможна реакция:
(МпО) + [S] + С = (MnS) + CO.
Из предыдущей формулы видно, что в доменной печи благоприятные условия для удаления серы в шлак, так как благодаря восстановительной атмосфере содержание FeO в шлаке ми¬нимально. При этом важно по возможности повысить а(СаО) т.е. работать со шлаками высокой основности. В то же время при повышении основности растет вязкость шлака, т. е. соответственно требуется увеличить расход кокса для поддержания более высокой температуры и расход известняка. При этом снижается производительность печи, так как часть объема печи занята дополнительными количествами кокса, известняка и шлака. Практически величина LS колеблется в пределах 30 — 70, а содержание серы в чугуне составляет 0,015 — 0,050%. При работе на сернистом коксе (например, из углей Донбасса) содержание серы выше.
Таким образом, выплавляемый в доменных печах чугун содержит некоторое количество серы, фосфора (практически весь фосфор, содержащийся в доменной шихте, восстанавливается и переходит в чугун), кремния, марганца. Кроме того, в процессе контакта капель жидкого чугуна, стекающих в горн печи через слой раскаленного кокса, происходит науглероживание металла. Содержание углерода в чугуне во многом определяется наличием в чугуне тех или иных при¬месей. Мп, Сг, V образуют карбиды, способствуя увеличению содержания углерода в чугуне. Si, P, Си способствуют снижению содержания углерода. Поэтому в ферромарганце и в высокомарганцовистом чугуне содержание углерода выше, чем в обычном передельном (до 7%), а в литейных чугунах с повышенными концентра¬циями кремния содержание углерода ниже (3,5 - 4,5%).
Одна из эмпирических формул для расчета содержания углерода в чугуне:
%С = 4,8 + 0,03 %Мп - 0,27 %Si -- 0,32 %Р-0,03 %S.
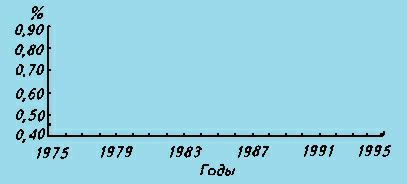
Обычно передельный (используемый для передела чугуна в сталь) чугун имеет состав, мас.%: С 4,4—4,6; Si 0,2-0,8; Мп 0,2-0,6; Р < 0,3; S < 0,05.
Таким образом, в чугуне ~94% Fe и 6% различных примесей. В процессе передела чугуна в сталь в окислительных условиях основная масса примесей окисляется. Кроме того, при использовании кислорода для продувки сталеплавильной ванны часть железа (1—2%) испаряется, окисляется и в виде пылегазовых выбросов покидает агрегат. Масса шлака в момент окончания плавки стали составляет 10 — 20% от массы металла. Шлак содержит 20—25% оксидов железа, или 1,5 — 2,5% Fe от массы металла. Этот расчет показывает, что при плавке стали из шихты, состоящей на 100 % из жидкого чугуна, около 10% ее массы переходит в шлак и в газовую фазу и расход металлошихты на 1 т жидкой стали превышает 1100 кг.
Мировая цена 1т жидкого чугуна 140 — 160 долл. США, цена металлолома ниже, она меняется в зависимости от конъюнктуры рынка. Этим объясняется стремление металлургов гибко реагировать на колебание цен и максимально использовать в шихте металлолом.
Обзор исследований по теме в Украине
В нашей стране проекты перехода на бескоксовые технологии находятся пока еще только на этапе исследований. В качестве примера хочется привести последние разработки Института черной металлургии им. Некрасова для аглодоменного передела. Они предполагают замену кокса и природного газа низкосортным углем в металлургическом производстве с усовершенствованием цикла переработки первичного металла в конечный продукт и, как следствие, улучшением экологических условий в районах металлургического производства.Сущность разработок заключается в создании газификаторов угля, генерирующих горячий восстановительный газ для вдувания в доменные печи и агрегаты бескоксового получения металла. На первом этапе предполагается замена в доменной плавке 40 - 50% кокса низкосортным углем при полном исключении природного газа, а на втором – создание новой технологии бескоксового получения первичного металла. Был разработан и частично испытан прифурменный газификатор измельченного угля, габариты которого вписываются в существующий фурменный прибор доменной печи. Реализация первого этапа разработки позволит заменить до половины кокса низкосортным углем с увеличением производительности единичных агрегатов в 1,5 раза при снижении энергозатрат и эксплуатационных расходов на 10%. Срок окупаемости затрат не превысит 1 года. Вторым этапом разработки предполагается перестройка доменной плавки на бескоксовую технологию путем реконструкции традиционной доменной печи с подачей горячих восстановительных газов через установленные по окружности горна реакторы-газификаторы измельченного угля и разделения печного пространства на зону твердофазного восстановления (шахту) и плавильно-восстановительный горн со сводом, который для шахты является днищем. Перегруз материалов из шахты в горн будет осуществляться шнеками через течки, а газ из горна в шахту будет поступать через газоотводы после охлаждения до 9000С.Данная технология уже осваивается на комбинате `Арселор Миттал Кривой Рог` (АМКР) и ферросплавных заводах Украины. Предполагается, что ее внедрение позволит уменьшить себестоимость металла на 20%, что при величине капитальных затрат, соизмеримой с затратами на капитальный ремонт печи, даст срок окупаемости менее 1 года. Выбросы в окружающую среду уменьшаются в соответствии с сокращением коксохимического производства.
Литература
- Кудрин В.А. Теория и технология производства стали: Учебник для вузов. - М.: "Мир", ООО "Издательство ACT".- 2003 - С.30 - 31
- Фомина О. Дефицит и дороговизна коксующегося угля подталкивают металлургов к более широкому применению альтернативных технологий выплавки стали [Электронный ресурс] / http://www.bau.ua/news_firm/ru_7152/
- Платонов О.И. В мировой химической промышленности // Кокс и химия. - 2007. - № 7. - С. 45-46. Юдашкин М.Я. Пылеулавливание и очистка газов в металлургии.- М: Металлургия, 1984.- 320с.
- Андоньев С.М., Зайцев Ю.С., Филипьев О.В. Пылегазовые выбросы предприятий черной металлургии.- Харьков, 1998. - 246 с.
- Старк С.Б. Пылеулавливание и очистка газов в металлургии.- М.: Металлургия, 1977.- 328 с.
- Юсфин Ю.С., Пашков Н.Ф. Металлургия железа.- М.: Акаддемкнига, 2007
- Развитие бескоксовой металлургии [Электронный ресурс] / http://azwin.ru/razvitie_beskoksovoi_metallurgii-2.html
- КОРЕКС-ПРОЦЕСС [Электронный ресурс] / http://www.metallobaza.com/abc/k/koreks_pro.htm
- В. Ф. Пашинский, И. Г.Товаровский, П. Е. Коваленко, Н. Г. Бойков. Доменная плавка с вдуванием коксового газа.- К.: Техника, 1991. - 104с.
- Николаева А.К. Анализ ресурсосбережения и разработка мероприятий для организации малоотходного доменного производства [Электронный ресурс] / http://masters.donntu.ru/2007/fizmet/nikolayeva/diss/index.htm