“Research and Development of the Device for Automatic Ignition of the Boiler Installation with Low-temperature Fluidized Bed”
Content
Introduction
1. A theme urgency
2. The purpose and problems of research
2.1 The work purpose
2.2 The main problems of the research
2.3 The subject of the research
2.4 The object of the research
3. Prospective scientific novelty of the received results
4. The review of developments and researches on a theme
5. The results of the work
5.1 Analysis process
5.2 The algorithm of ignition BFB
5.5 Modeling of automatic process control ignition
5.6 Technical implementation of the automatic control ignition
6. Practical significance of the results
7. Approbation of the work results
Conclusions
Bibliography
Introduction
Higher energy prices, the deficit of own fuel resources, reduction of coal quality, the growth requirements for reducing pollution of the environment requires the introduction of the improved method of burning coal.
It is the availability of energy resources determines the pace and scale of development of individual areas of industrial and agricultural production. The main objectives are to provide a more comprehensive processing of raw materials, creation of resource-saving techniques and technologies, drastic reduction of losses and waste. Many countries, the restructuring of the fuel balance to reduce dependence on oil and gas has revived interest in coal mining topics in recent years.
Today, these requirements meet boilers with low-temperature fluidized bed (bubbling fluidized bed — BFB). Fuel is burned in the furnaces fluidized bed, which contributes significantly to improve the access of oxygen to the fuel in the combustion process, high heat transfer to the surfaces of heating, as well as more complete combustion [1].
It is possible to use waste coal and coal-mining, non-conventional and low-grade fuels (wood chips and other wood waste, peat, sludge, etc.) with this technology, while allowing the burning of different fuels in a furnace device. Application the technology of fuel combustion in a fluidized bed ensures stringent environmental regulations on emissions SO2 and NO2 without building additional facilities for sulfur- and nitrogen removal. However, the practical realization of this method in industrial installations associated with overcoming a number of difficulties inherent in the specifics of this process.
Today ignition of the low-temperature fluidized bed has been performing manually by the operator. This poses a risk to staff and significantly reduces the quality of process control. Therefore, to achieve optimal control of ignition, it should be implemented in an automatic mode.
A theme urgency
At present, ignition of the boiler with low-temperature fluidized bed has been performing manually by the operator and not always successful and, consequently, is accompanied by forced unproductive downtime of equipment. There is a danger of staff, due to fire or explosion of fuel, failure of mechanical equipment. Therefore, in order to exclude the presence of personnel near the danger zones ignition of the boiler must be carried out in automatic mode. Existing the automation system are made on the basis of outdated regulators P25, which are not allow to realize an algorithm of software process control.
Violation of ignition process of the algorithm often leads to loss of liquid fuels because of the unstable flame at the burner. Implementation of automatic ignition in accordance with a certain algorithm will improve rational use of fuel, to ensure compliance with environmental standards and reduce the wear of mechanical equipment, and material costs for its repair.
The purpose and problems of research
The work purpose — To improve the efficiency and reliability of the ignition of low-temperature fluidized bed through the development of the device for automatic ignition.
The main problems of the research:
- Research the state of the problem of automatic ignition.
- Justification of the mathematical model of fluidized bed.
- Research of the mathematical model of fluidized bed.
- Development and Justification the algorithm of automatic ignition low-temperature fluidized bed using a plasma-fuel systems.
- Modelling of automatic process control ignition fluidized bed.
- Development the technical solutions of the device for automatic ignition
The subject of the research: Process of automatic ignition low-temperature fluidized bed.
The object of the research: Boiler installation with low-temperature fluidized bed.
Prospective scientific novelty of the received results
Prospective scientific novelty consists in the following:
Development of a mathematical model of fluidized bed;
Development of algorithm for automatic ignition low-temperature fluidized bed using a plasma-fuel systems;
Implementation of the correction in the circuit temperature;
Rationale for the structure of the automatic control ignition;
Моделирование процесса розжига низкотемпературного кипящего слоя;
Development of the device for automatic ignition of the fluidized bed.
The review of developments and researches on a theme
To derive the low-temperature fluidized bed boiler for stationary mode, you have to heat the bed to the ignition temperature of fuel particles. Currently, there are three ways to run the boiler with fluidized bed [2]: hot air from the ignition burner on the highway blast; by burning gas or fuel oil in burners, installed over a layer or incineration in a layer of gas-air mixture, fuel oil, other fuels with a high content of volatiles.
There ara several methods of reducing the consumption of fuel oil by burning low-rank coals: the reconstruction of burners, the separate and blended coal combustion and preheat fuels — oil, high heating of air and dusty mixture, thinning of grinding, etc. — does not solve the problem of reducing the consumption of liquid fuels, especially at the stage of kindling Boilers.
For the ignition, except fuel oil and gas, can be used pulverized coal burners, equipped with plasma generators. Research of ИТФ СО АН, СибНИИЭ and КазНИИЭ showed that the plasma combustion technology for coal dust fuel with plasmatrons appears promising way to solve the problem of highly efficient use of low-grade fuels [3].
Analysis of patent documentation registered in Ukraine has been established that the closest technical solution to the developed device is the patent for the invention “Devices for automatic ignition of the boiler” (УКРПАТЕНТ: published 30.09.1996) [4]. This device is built on the basis of relay switching circuits and as a result has low reliability, difficulty in implementing the algorithm of optimal control and ignores the characteristics of low-temperature fluidized bed and a plasma-fuel systems.
The research and control of fluidized bed devoted a lot of development on a global level. An interesting technical solution is a patent for control system of fluidized bed: “Fluidized Bed Combustion Optimization Tool And Method Thereof”, registered in the U.S. (published 25.02.2010) [5]. Basis of the Control System is a neural network model of the object and the controller. The object into account technological, ecological and economic parameters of the process control. The disadvantage of this invention is the lack of a control contour plasma-fuel system.
The description of the received results of the work
Analysis Process
For heating the fluidized bed and the ignition of coal used oil. Co-firing coal and having a higher reactivity of oil worsens the environmental performance of an Economic boilers: 10–15% increases mechanical unburning fuel and reduces efficiency of 2–5%, it increases the speed of high-temperature corrosion-screen surfaces, decreasing the reliability of boiler equipment An increase of 30–40% yield of nitrogen oxides and sulfur.
Violation of ignition process of the algorithm often leads to loss of liquid fuels because of the unstable flame at the burner. Therefore, for energy and cogeneration plants require systems that provide reliable without oily ignition and improve environmental performance. To achieve these objectives can be used in pulverized coal burners, equipped with plasma generators. This technology consists in heating fuel mixture (coal dust + air) arc plasma. Plasma gas (air) is blown through the electrodes, forming a plasma torch, the mean temperature of which varies in the range of 5000 – 6000 K [6].
Installation diagram of plasma-fuel system (PFS) on boiler BFB shown at Fig. 1 [7]. Coal dust, forming part of the mixture, contained in the pulverized-coal bunker (Fig. 2)
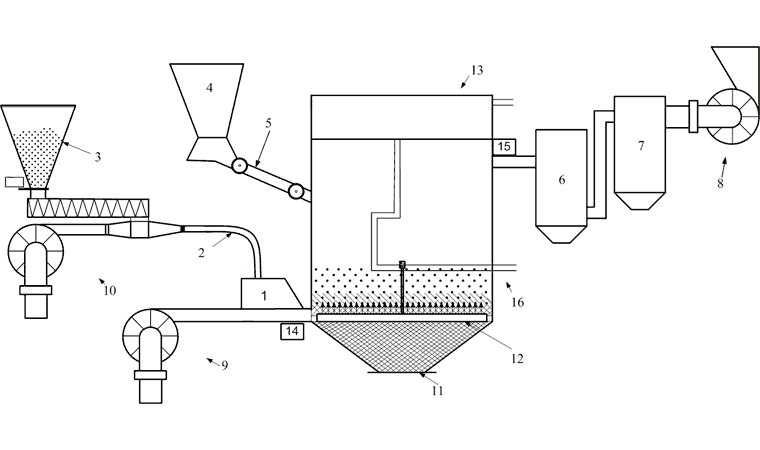
Figure 1 — Scheme of boiler BFB using PFS
(animation: volume — 134 KB; size — 760x450; number of shots — 20; delay between
shots — 1500 ms; delay between last and first shorts — 2000 ms, number of
repetition cycles — infinity)
Description:
1 — PFS;
2 — Dust lead;
3 — Hopper for coal dust;
4 — Bunker for solid fuel;
5 — Apron Feeder;
6 — Economizer;
7 — Cyclone;
8 — Smoke exhauster;
9 — Blow fan;
10 — Blow fan of PFS;
11 — Device Ash;
12 — Distribution plate;
13 — Boiler;
14 — Pressure transmitter;
15 — Converter dilution;
16 — Coolant loop.
Pulverized coal bunker for the explosion is made in private. With the help of a screw feeder, which is rotated by drive motors, coal dust gets into the mixing chamber with the primary air and then through pyleprovod circular cross section with a flow rate of more than 25 m / s (to avoid dust deposits) is sent to the burner.
When turned off by locking screw feeder chute, feed coal mixture. At times, certain algorithm of PFS, control slide gate is realized by one-turn electric machinery.
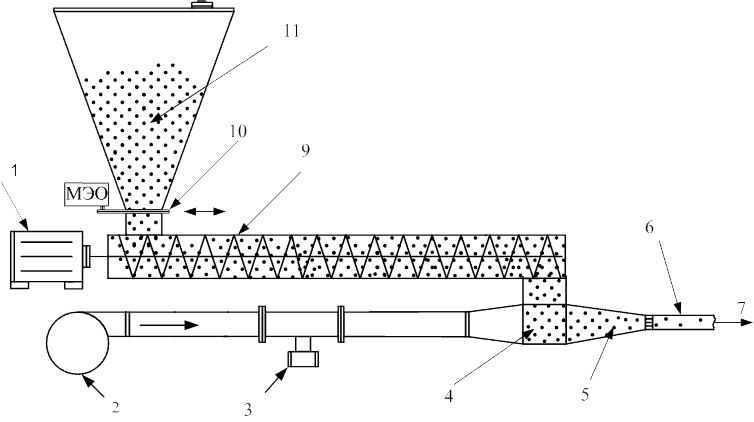
Figure 2 — The design of injection systems fuel mixture
Description:
1 — Drive motor;
2 — Blower fans PFS;
3 — Flow;
4 — Mixing chamber;
5 — Air-coal misture;
6 — Pulverized-coal conduit;
7 — Burner;
8 — Screw Feeder;
9 — Sliding;
10 — Coal dust.
In the PFS used coal-fired burner (Fig. 3) [9], in which muffle of oil burners replaced with a special muffle of heat-resistant steel or cast iron with insulating coating.
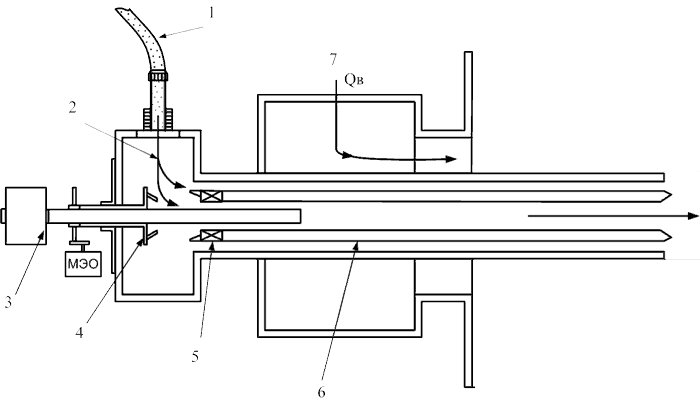
Figure 3 — The design of the burner for PFS
Description:
1 — Pulverized-coal conduit;;
2 — Aerosmith;
3 — Plasmatron;
4 — Movable adjusting cap;
5 — The twisting mechanism;
6 — Muffle;
7 — Air.
The algorithm of ignition BFB
To implement the technology PFS in the automation process control ignition boiler BFB development the algorithm, which differs from the traditional method of ignition with the use of fuel oil [10] and it is characterized by a sequence of the following operations:
- Preparing the system to run (to check if a sufficient amount of coal dust and solid fuel in the bunkers for ignition, the closure guiding devices and smoke exhauster blower fans, closing the cover of the adjusting in the plasma torch, opening gate bunker coal dust).
- Turn on circulation pump, and checked the flowmeter for water flow through the surface of the cooling layer at the entrance and exit from the boiler.
- Overlapping bypass duct, the inclusion of the blower fan plasma-fuel system in the amount of 44% of the theoretically necessary quantity of air for combustion of coal dust.
- The inclusion of the plasma torch and the heating muffle to a temperature of 8000C, which is necessary for stable combustion fuel mixture.
- The inclusion and installation of smoke sucker dilution is 6 Pa.
- Turning the fan blowing of air fluidize and installation of pressure in the grille to 4 kPa.
- Aafter reaching the temperature of the muffle 8000C included worm feeder supply of coal dust and changing the position of the adjusting cap ensured its sustained inflammation using the device for flame.
- When thetemperature of bed is 4500C feeder will supply of solid fuel in the combustion chamber and the proportional-integral control law ensures a smooth increase in temperature.
- When the temperature of the bed is 7000C PFS must be disable .
- Open the bypass duct.
Further process of BFB is carried out automatically.
It should provide for emergency shutdown of the boiler automatically in case of an emergency or when you click on “accident”.
Emergency stop should be made in the following situations:
- Violation of the circulation of water through the boiler;
- Turn off blower fans or smoke sucker.
It should:
- Disable fuel feeder;
- Turn off the circulation pump;
- Close the gate bunker coal dust;
- Disable the worm feeder (if enabled);
- Turn off the plasmatron (if enabled);
- Close the lid of the adjustment of the burner;
- Turn off blower fans TCP (if enabled);
- Disable the smoke exhauster;
- Turn off blower fans fluidize the air.
Modeling of automatic process control ignition
The dynamic characteristics of the combustion chamber is a very important element for the development of automated monitoring and regulation.
Speed of system response to dynamic perturbation can be estimated using the equation of thermal balance layer [12]:
 |
(1) |
where: Sсл, Sw — surface bed and the external heat exchanger; Сs, Сg — heat of the material bed and gas; ρр, ρg — density of particles and gas; Нсл, Тсл — height and temperature of the bed; jт — fuel consumption at 1m2 fluidized bed; QT — lower heat combustion of fuel; q4, q3 — heat loss due to chemical and mechanical incompleteness of combustion; U0 — upward velocity of gas in the total cross section; Т0, Тf — temperature blast air and coolant; hw — heat transfer coefficient of the heating surface; Iз and Iл — loss of heat from the diverted ash and radiation through the surface of the fluidized bed.
Consumption of solid fuels for heating is determined from the expression:
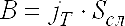 |
(2) |
After appropriate transformations we obtain the transfer function of the fluidized bed along the contour of the solid fuel:
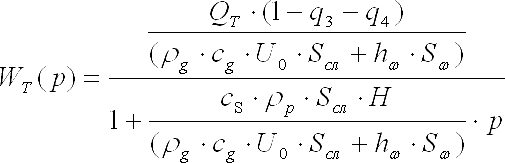 |
(3) |
Ignition and heated fluidized bed by a plasma-fuel system (PFS). Applying the same steps for this circuit we obtain the transfer function:
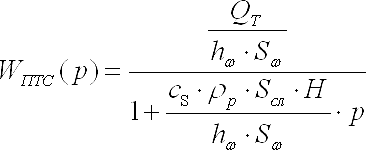 |
(4) |
Simulation parameters was adopted to boiler DKVR-10-13.
Research of characteristics of the BFB using (18) made in the Matlab package Simulink. Real and measured the temperature of fluidized bed in the ignition process of the boiler is shown at figure 4.
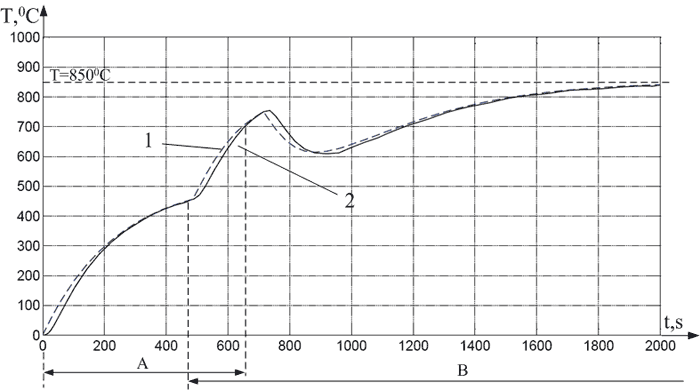
Figure 4 — The real and measured temperature of the boiler
Description:
1 — Real temperature of the boiler;
2 — Measured temperature of the boiler;
A — Working of PFS;
B — Supply of solid fuel.
A negative temperature gradient (Fig. 4) caused an instantaneous disconnection title in reaching 7000 C due to reduced amount of heat introduced into fluidized bed.
Smooth off PFS implemented to reduce the consumption of coal dust linearly. Fig .5.
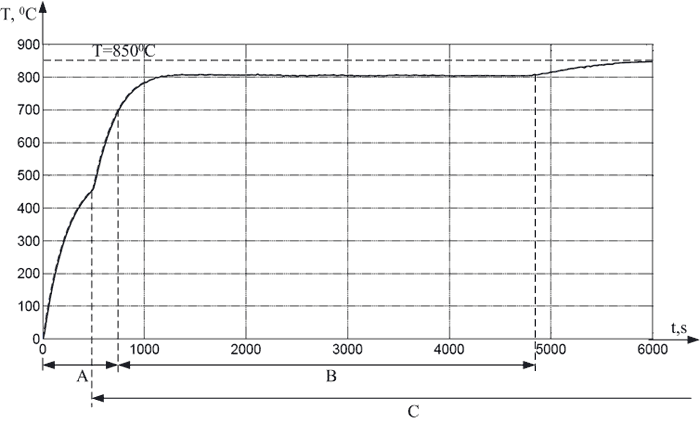
Figure 5 — temperature of the fluidized bed for a smooth trip PFS
Description:
A — Working of PFS;
B — Smooth off PFS;
B — Supply of solid fuel.
Technical implementation of the automatic control ignition
Block diagram of the developed device is shown at Figure 6. The device performs the automatic ignition of BFB in accordance with a specified algorithm.
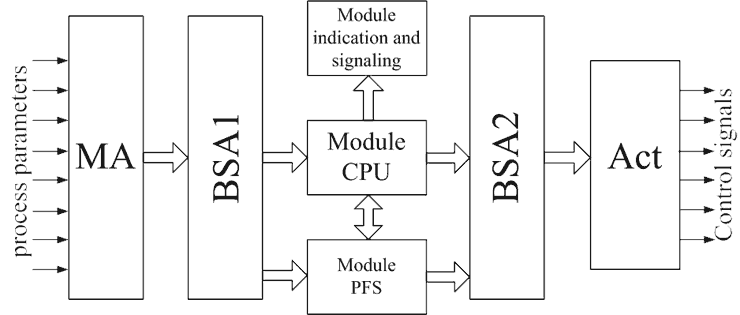
Figure 6 — Block diagram of the automatic ignition
Automatic ignition device consists of three modules, each of which is based on mikrprotsessornoy technology:
1) Central processing unit (CPU) implements the function of control of the unit. In accordance with the algorithm of ignition, on the basis for received information from the measuring aid Microcontroller extradite control actions on actuators (Act), also generates signals permission (prohibition) on the job title and passes relevant information in the module display and alarm. CPU module organizes the transfer of information on the state parameters for the boiler on a computer through the RS-485.
2) Module PFS in accordance with design algorithms and information which received from the transducers performs the control of the plasma-fuel system.
3) Module indication and signaling serves light and sound the alarm about the current technological process and the emergency operation.
To ensure the protection of control circuits blocks the signal alignment (BSA1 and BSA2) provide galvanic isolation control modules with chains transducers and actuators.
Practical significance of the results
Automating the process for ignition of BFB using plasma-fuel systems will generate a stationary boiler operation, subject to specified requirements and restrictions will create a secure environment for staff and improve the quality of process control.
Approbation of the work results
The results of my research work were approved at the following conferences and competitions:
- V Scientific Conference “Donbass–2020: PROSPECTS SEEN FOR YOUNG SCIENTISTS”, which was held in the Donetsk National Technical University (DonNTU) 25–27 May 2010. Report: “Automating the process ignition of low-temperature fluidized bed”.
- X Scientific Conference and graduate students in the city of Donetsk, May 18-19, 2010. “Automation of technological objects and processes. Search for the young.” Report: “Development of algorithm ignition low-temperature fluidized bed and its implementation”.
- Ukrainian contest for the best scientific work of students in the direction of “Mining”. Theme research: “Research the process ignition of the boiler with low-temperature fluidized bed and justification of the structure for control system”. As a result of the contest winner was awarded a diploma of III degree.
- XI international youth conference “Severgeoekoteh-2010”, March 17–19, 2010 in Ukhta, Komi Republic. Section 1: Automation and Electrical Engineering (with Donetsk National Technical University, Donetsk, Ukraine). Report: “The rationale for the structure of control system and research ignition of low-temperature fluidized bed ”.
- Univercity contest of student research papers 2009–2010 academic year in “Mining”. Theme research: “Research the process ignition of the boiler with low-temperature fluidized bed and justification of the structure for control system”. As a result of the contest was awarded a diploma of the winner.
- VIII International Scientific and Technical Student Conference “Fluid”, Report: “Modelling of ignition low-temperature fluidized bed.”
- Competition scholarship program of the Victor Pinchuk Foundation “Zavtra.UA” 2009-2010 academic year. Theme research: “Development of automated process control ignition low-temperature fluidized bed boiler.” As a result of the contest received 65.13 of the ball.
- IX Scientific Conference and graduate students in the city of Donetsk, May 20–22, 2009. “Automation of technological objects and processes. Search for the young.” Report: “The device for automatic ignition of low-temperature fluidized bed boiler using plasma-fuel systems.”
Conclusions
Application of plasma-fuel system provides a reliable without oily ignition and improve the environmental performance of the boiler as a whole. This excludes the accident and loss for ignition of fuel arising from the use fuel oil for ignition fluidized bed. Developed a functional diagram for the ignition of low-temperature fluidized bed using PFS.
Based on the heat balance equation fluidized bed transfer functions along the contours of BFB title and feeding of solid fuel. According to the results of calculations carried out modeling of ignition fluidized bed using a proportional-integral controller in the circuit feeding the solid fuel. A negative temperature gradient is caused by momentary disable PFS in reaching 700 0C due to decreasing the amount of heat introduced into fluidized bed. As a result, modeling the ignition with a continuous outages of coal dust in the PFS of the nominal value to zero, with the appropriate configuration control of fuel supply, obtained a smooth increase in temperature, which excludes the appearance of a negative gradient.
Thus, to ensure automatic ignition BFB should produce disabling of PFS by a smooth variation flow of coal dust. If this condition is ignition of the boiler is carried out in safe mode, deleted zashlakovka layer and excessive wear of equipment.
Application of the developed device automatic ignition of the boiler to create a safe environment for the operator, reduce downtime and improve the technical, economic and environmental performance of the ignition of the BFB.
Bibliography
- Вискин Ж. В., Шелудченко В. И.и др. Сжигание угля в кипящем слое и утилизация его отходов — Донецк: Типография “Новый мир”, 1997. — 284 с.
- Махорин К. Е., Хинкис П.А. Сжигание топлива в псевдоожиженном слое. Киев:Наук. Думка, 1989 – 204с.
- Бурдуков А. П., Чернова Г. В., Коновалов В. В., Чурашев В.Н. Разработка технологии безмазутной плазменной растопки и подсветки на основе пылеугольного топлива ультратонокого помола.
- Чушенко А. В., Маранценбаум А. И., Лебедев В. Ф. Описание патента на изобретение устройства автоматического розжига котла. УКРПАТЕНТ [electronic resource] / Чушенко А. В., Маранценбаум А. И., Лебедев В. Ф./ —Mode of access: http://base.ukrpatent.org/searchINV/..
- Xinsheng Lou, Carl H. Neuschaefer, Paul J. Panos, Josrph W. Quinn. Патент США: «Fluidized Bed Combustion Optimization Tool And Method Thereof» [electronic resource] / Xinsheng Lou, Carl H. Neuschaefer, Paul J. Panos, Josrph W. Quinn. / — Mode of access: http://www.freepatentsonline.com/20100049561.pdf
- Аскарова А. C., Карпенко Е. И., Мессерле В. Е., Устименко А. . Плазмохимическая активация горения и газификация угля. [electronic resource] / Аскарова А. C., Карпенко Е. И., Мессерле В. Е., Устименко А. Б./ — Mode of access to the articl: http://www.isuct.ru/istapc2008/PROC/P-8.PDF
- Гавриленко Д. А., Гавриленко Б. В. Автоматизация процесса розжига низкотемпературного кипящего слоя.Электронный сборник научных трудов V научно-практической конференции "ДОНБАСС-2020: ПЕРСПЕКТИВЫ РАЗВИТИЯ ГЛАЗАМИ МОЛОДЫХ УЧЕНЫХ", секция 6.33 ДонНТУ, 25–27 мая 2010 года.
- Гавриленко Д. А., Гавриленко Б. В. Устройство автоматического розжига котлоагрегата низкотемпературного кипящего слоя с использованием плазменно-топливных систем. Автоматизация технологических объектов и процессов. Поиск молодых. Сборник научных трудов IX научно-технической конференции аспирантов и студентов в г. Донецке 20 – 22 мая 2009 г. — Донецк, ДонНТУ — 2009, с. 14 – 19.
- Тимошевский А. Н., Засыпкин И. М., Ващенко С. П., Векессер Ю. Г., Комарицын В. К. Применение систем плазменного воспламенения угольной пыли в котлах Таштагольской производственно-отопительной котельной.
- Гавриленко Д. А., Гавриленко Б. В. Разработка и реализация алгоритма розжига низкотемпературного кипящего слоя. Автоматизация технологических объектов и процессов. Поиск молодых. Сборник научных работ X научно-технической конференции аспирантов и студентов в г. Донецке 18–20 мая 2010 г. — Донецк, ДонНТУ — 2010.
- Махорин К. Е., Хинкис П. А. Сжигание топлива в псевдоожиженном слое. Киев: Наук. Думка, 1989 — 204с.
- Гавриленко Д. А., Гавриленко Б. В. Обоснование структуры системы управления и исследование процесса розжига низкотемпературного кипящего слоя. СЕВЕРГЕОЭКОТЕХ-2010. Сборник научных работ XI Международной молодежной научной конференциии — Ухта, УГТУ, 2010. — 440 с.
Note
When writing this abstract the master’s qualification work is not completed. Date of final completion of work: December, 1, 2010. Full text of the work and materials on a work theme can be received from the autor or his scientific supervisor after that date.
|