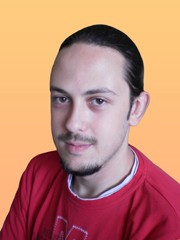
Д.т.н. Зори А.А., к.т.н. Украинский Ю.Д., асс. Кузнецов Д.Н.
Источник: Зб.наук.пр. ДонДТУ. Серiя: Обчислювальна технiка та автоматизацiя, випуск 12: – Донецьк: ДонДТУ, ТОВ «Лебiдь». – 1999.– С. 320-327
Abstract
In the given work the task of development of a subsystem of measurement and account of the charge of natural gas for pipelines of the large diameters is put. In a basis the method of definition of the charge of gas on average speed in measuring section is fixed. For measurement of speed is used termoanemometr of constant temperature.
На современном этапе развития производства большое внимание уделяется проблемам повышения эффективности использования технологического оборудования, улучшения качества технологических процессов и достоверности учета материальных ценностей и энергетических ресурсов. Многие технологические процессы связаны с транспортированием вещества по трубопроводам. Непременным условием эффективного ведения таких процессов является наличие достоверной информации об их параметрах и в первую очередь о массовом или объемном расходе вещества.. Без этих измерений очень трудно контролировать утечки и исключать потери ценных продуктов. Снижение погрешности измерений хотя бы на 1% может обеспечить многомиллионный экономический эффект. Роль и значение расходомеров еще более возрастает в связи с удорожанием энергоносителей и необходимостью максимальной экономии энергетических и водных ресурсов страны.
Самое большое распространение на трубах большого диаметра получили расходомеры переменного перепада давления. В основе их работы лежит зависимость от расхода перепада давления, создаваемого устройством (диафрагмой, соплом), которое устанавливается в трубопроводе [1]. Существенными недостатками данного типа расходомеров являются:
Возросшие требования к точности измерений расхода в широком диапазоне скоростей предопределили необходимость разработки подсистемы, основанной на ином принципе измерений. ГОСТ 8.361-79 устанавливает правила измерения расхода для труб диаметром от 300 мм путем определения скорости потока в характерных точках. При этом наиболее целесообразно местную скорость потока измерять в точках, где она равна средней скорости в данном сечении (в точках средней скорости). При развитом турбулентном течении измеряемой среды точки средней скорости расположены на расстоянии (0,242±0,013)r от внутренней поверхности стенки трубы, где r – внутренний радиус трубы в измерительном сечении.
В качестве измерителя скорости предполагается использование термоанемометра (ТА), удовлетворяющего требованиям малости чувствительного элемента (независимости измеряемой скорости от градиента скорости в данной точке). До настоящего времени ТА не нашел широкого применения по следующим причинам:
В настоящее время все эти недостатки технологически устранимы. Загрязнение чувствительного элемента, как показали опыты, происходит на передней критической образующей чувствительного элемента. Поэтому необходимо использовать в качестве чувствительного элемента тело обтекания, с малой зависимостью теплоотдачи от загрязнения критической образующей. Дополнительная стабильность характеристик первичного преобразователя достигается путем искусственного старения при его эксплуатации с повышенной температурой перегрева.
Появившиеся в последнее время многоразрядные АЦП позволяют успешно преодолевать недостаток ТА, связанный с малой разрешающей способностью при больших измерительных скоростях, а успехи радиоэлектроники в производстве прецизионных операционных усилителей (ОУ), делают возможным построить аппаратуру с достаточной временной и температурной стабильностью.
В СКТБ «Турбулентность» коллективом авторов был разработан ТА удовлетворяющий требованиям ГОСТа 8.361-79. В основу измерения массовой скорости газа положен термоанемометрический принцип, основанный на зависимости тепловой мощности, рассеиваемой нагретым до постоянной температуры телом (первичным преобразователем), от разности температур тела и газа и массовой скорости газа относительно тела. Упрощенная функциональная схема ТА постоянной температуры представлена на рис. 1.
Рисунок 1 – Функциональная схема простейшего ТА
Для однозначности определения значения скорости необходимо иметь значения температур газа и первичного преобразователя (ПП), мощности, теплофизических свойств газа при данной температуре и индивидуальных характеристик ПП. В данном приборе температура нагретого тела задается и поддерживается термоанемометром постоянной температуры, выходной сигнал которого определяет мощность, рассеиваемую на ПП. Температура газа определяется термометром сопротивления. Индивидуальные характеристики чувствительных элементов температуры и скорости определяются при градуировках. Теплофизические свойства газа определяются по составу газа из сертификата газоснабжающей организации.
В качестве чувствительных элементов ТА и термометра используются промышленные полупроводниковые терморезисторы СТ3-19 [5], располагаемые на державке диаметром 10 мм. Температура чувствительного элемента ТА поддерживается постоянной на уровне 120 °С.
При использовании термистора в качестве ПП термоанемометра появились сложности с расшифровкой сигнала, вызванные тем, что теория ТА разработана для нагретой проволочки или пленочки, имеющих непосредственный контакт с газом и в предположении, что по ПП нет градиента температуры [2, 3]. В нашем случае из-за наличия стеклянной оболочки термистора температура его поверхности не равна температуре полупроводника, поэтому уравнение теплового баланса будет иметь следующий вид:
, (1)
где Nu – число Нуссельта, L – безразмерный коэффициент теплопроводности в стеклянной оболочке термистора, A – безразмерный коэффициент потерь тепла на естественную конвекцию, В – безразмерный коэффициент потерь тепла на вынужденную конвекцию, является функцией температуры потока, Re – число Рейнольдса, n – показатель степени.
Задача определения постоянных коэффициентов L, A, n и функции B решается путем индивидуальной градуировки ПП. Градуировочные характеристики были определены путем обработки экспериментальных данных, полученных для воздуха на аэродинамической трубе АДС-25/20 производства НИИ им. Д.И. Менделеева г. Санкт-Петербург. В результате были получены следующие характерные значения: L=0,002; А=0,0008; В=5Е-6; n=0,5. С помощью теории подобия результаты обработки были успешно перенесены для случая использования в качестве измерительной среды природного газа [4].
При построении ТА и термометра были использованы классические схемы [2, 3]. В термометре чувствительный элемент введен в цепь отрицательной обратной связи. В качестве активных элементов применяются прецизионные операционные усилители серии OP177.
В целом структурная схема подсистемы измерения и учета расхода природного газа для трубопроводов больших диаметров представлена на рис.2.
Рисунок 2 – Структурная схема подсистемы.
Здесь: 1,2 – ПП термоанемометра и термометра; 3 – термоанемометр; 4 – термометр; 5,6 – преобразователи ток-напряжение ТА и термометра; 7 – двухканальный АЦП; 8 – микропроцессор; 9 – индикация; 10 – архив; 11 – часы реального времени; 12 – интерфейс; 13 – блок питания; 14 – блок искробезопасности.
Пробный запуск описанной подсистемы производится на газораспределительных станциях Ростовгоргаз в составе автоматической системы сбора и обработки информации. При эксплуатации более 6 месяцев получены удовлетворительные результаты. Основная приведенная погрешность измерения расхода в диапазоне скоростей от 1 до 100 м/с не превышает 2,5%.
Выводы
Литература