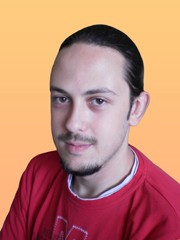
Кузнецов Д.Н. ассистент
Источник: Зб.наук.пр. ДонНТУ. Серія: Обчислювальна техніка та автомати-зація. Випуск 58: – Донецьк: Вид-во ДонНТУ. – 2003. – С.75-80
Аннотация
Выполнено исследование погрешностей определения скорости газа по методу измерения динамического давления. Выявлен критический режим градуировки, при котором суммарная погрешность максимальна. Установлена зависимость, между допустимой погрешностью измерения температуры газа и погрешностью измерения динамического давления, при которых суммарная погрешность измерения скорости газа не превышает установленного предела.
Постановка задачи исследований.
Для увеличения точности и эффективности градуировок термоанемометров в СКТБ “Турбулентность ” при Донецком нацианальном университете была разработана ИИС автоматизации и контроля градуировок ТА [1, 2]. В состав ИИС входят следующие основные измерительные каналы:
Градуировка осуществляется на аэродинамической установке АДС-200/250 путем сопоставления данных измерений ТА с данными, полученными от образцового средства измерения скорости газа. В качестве образцового средства измерения (ОСИ) скорости газа используется трубка Пито. При этом скорость газа определяется, согласно ГОСТ 17.2.4.06–90, по методу измерения динамического давления газа (Рд)
Рд=Рп – Рст, (1)
где Рп – полное давление газа, Па, Рст – статическое давление газа, Па;
и последующего расчета скорости газа по формуле
, (2)
где – плотность газа при рабочих условиях, кг/м3, Ратм – атмосферное давление, Па, Т – температура газа, °С.
При расчете градуировочных зависимостей целесообразно оперировать критериальными соотношениями, что в дальнейшем даст возможность проводить измерения в газах иного состава, используя результаты градуировки на воздухе. Число Рейнольдса для трубки Пито
, (3)
где d – диамитр измерительного отверстия трубки, – динамическая вязкость газа.
При проектировании измерительных каналов ИИС градуировки ТА возникла необходимость в оценке погрешностей образцового средства измерения скорости газа при различных скоростях и температурах газового потока, с целью выявления критической области измерений, в которой погрешность максимальна.
Оценка погрешностей определения скорости газа.
Из (3) следует, что число Рейнольдса определяется косвенным путем и для его расчета необходимо выполнить прямые измерения динамического давления и температуры газа. Доверительная граница неисключенной систематической погрешности измерения числа Рейнольдса трубкой Пито [3]:
, (4)
где W1, W2 – частные относительные погрешности измерения числа Re, обусловленные погрешностями прямых измерений динамического давления и температуры газа соответственно; DРд, DТ – абсолютные погрешности измерений разности давлений и температуры газа; K – коэффициент, обусловленный принятой доверительной вероятностью Р и числом m составляющих dосн (при Р=0,95 К=1,1 и мало зависит от m).
Найдем частные производные (весовые функции), входящие в (4):
; (5)
. (6)
Исследуем частные погрешности W1 и W2, определим характер их изменения во всем диапазоне скоростей и температур градуировки и выделим критические области, в которых погрешности максимальны. Вычисления осуществим в пакете MathCad. На рис.1 представлены графики зависимости частной погрешности W1 от числа Re (от скорости) при граничных температурах градуировки и DPд=1 Па. Из результатов приведенных на рисунке следует, что погрешность W1 возрастает с уменьшением скорости потока и его температуры. Таким образом, критическим режимом для W1 является режим с минимальными скоростью и температурой потока. На рис.2 представлены результаты исследования частной погрешности W2 при DТ=1°С, которые показывают, что W2 не зависит от скорости газа и возрастает с уменьшением его температуры. Критический режим для W2 – минимальная температура градуировки.
На основании результатов исследований частных погрешностей W1, W2 делаем вывод, что ОСИ дает максимальную погрешность измерений при минимальной скорости и температуре воздушного потока.
Рисунок 1 – Зависимость W1 от Re при граничных значениях температуры газа.
Рисунок 2 – Зависимость W2 от Re при граничных значениях температуры газа.
Выполним исследование суммарной погрешности ОСИ скорости газа для выявленного критического режима с минимальной скоростью и температурой потока (Re=500 и Т=0 °C). Погрешность ОСИ по техническому заданию (ТЗ) не должна превышать 0,5%. Проанализируем полученные результаты. На рис.3 представлены графики зависимости суммарной относительной погрешности ОСИ dОСИ от абсолютной погрешности измерения динамического давления DРд при различных значениях абсолютной погрешности измерения температуры газа DТ.
Рисунок 3 – Зависимость суммарной погрешности ОСИ от погрешности измерения температуры газа при различных значениях DРд.
Рисунок 4 – Зависимость суммарной погрешности ОСИ от погрешности измерения динамического давления при различных значениях DТ.
Рисунок 4 содержит аналогичные результаты, но полученные для случая, когда DТ является непрерывным аргументом, а DР – дискретным.
Из результатов исследований следует, что с уменьшением погрешности измерения давления, растет предел допустимой погрешности по температуре и наоборот, чем выше класс точности термометра, тем менее точный нужен дифманометр.
Установим связь между допустимой погрешностью термометра и погрешностью дифманометра, обеспечивающие заданное значение суммарной погрешности ОСИ. Для этого перепишем выражение (4) относительно DТ:
. (7)
Графическая интерпретация зависимости (7) представлена на рис.5.
Рисунок 5 – Зависимость погрешности измерения температуры газа от погрешности измерения динамического давления, обеспечивающие заданное значение суммарной погрешности ОСИ (dОСИ=0,5 %).
Анализ результатов показывает, что при DРд<1,5Па допустимый уровень DТ слабо зависит от DРд и находится в пределах от 0,8 до 1 °С. Однако с увеличением DРд от 2 Па и выше требования к точности измерения температуры газа резко возрастают и при DРд=2,5 Па предел допустимой погрешности по температуре составляет всего 0,35 °С. Полученная зависимость позволяет по заданной суммарной погрешности ОСИ скорости газа поставить требования к точности измерительных каналов температуры газа и динамического давления.
Выводы
Литература