Abstract
on master's work
"Expert System of Faults Diagnostics in Internal Combustion Engine Work"
Introduction
Electric cars now is a very complex system consisting of more than one hundred articles and is about 30% of the value of the car. In modern cars a lot of "smart" bloat. Parking sensors and rain, autodarkening mirrors, passenger recognition of obstacles and similar functions can often be found in the lists of complete sets in Auto Dealers. The use of but HIGH achieving electronics and microprocessor technology facilitated the development of computer diagnostic systems for finding defects in the car, including the engine. But since computer systems diagnosis, do not always loyal to the analysis of diagnosis and response to resolve a problem. Therefore, the analysis of problems in the car and finding solutions, is engaged in the mechanic, who should have no small amount of knowledge to understand the data and find the right solution to correct the problem, which consumed much time and effort.
To create a better computer system for vehicle diagnostics and updating of computer systems involved in a lot of scientists, thereby trying to improve the rating of the concept car brand in the world market and making a step in the future of the auto-computerization.
The proposed computer diagnostic system, conducting the processing and analysis of data obtained from the vehicle's sensors for identifying problems in the engine ZMZ - 406, as well as determining further damage due to no decision proposed system.
1 Relevance of the topic
By the technical perfection of internal combustion engines (ICE), first car, in recent times are making increasing demands, including the reliability in operation. Effective way of ensuring reliability is the systematic monitoring of technical state of engine.
Diagnosis of the technical state of engines in service provides, on the one hand, safety and reliability of the expense of timely maintenance and repair and, on the other hand, provides a complete implementation of the resource nodes engine that helps reduce costs, improve economic and environmental performance of internal combustion engines.
Diagnosis allows for timely implement the necessary control systems and engine components for which performance indicators are consistent with the required level, but also lets you control the quality of assembly and repair of power units.
2 REVIEW OF RESEARCH AND DEVELOPMENT RELATED
1) Error Detection in engines using fuzzy logic
The study was based extra fuzzy logic, fault detection system was developed to diagnose errors internal combustion engine and the system included with the engine test stand. Input variables of fuzzy logic classifier were purchased through the map data acquisition and RTS 232 port. The basis of the rules of this system was developed, considering the theoretical knowledge, experiential knowledge, and the results of the experiment. The accuracy of the fuzzy logic classifier was tested by experimental studies that were performed under different conditions of error. Using advanced error detection system, and ten common mistakes that were observed in an internal combustion engine were successfully diagnosed in real time. With these features the system could easily be used to detect errors in the testing laboratories and workshops of service.
2) Use of neural-network models with vibroacoustic diagnostics engine (for example, diagnosis of cam timing). [10]
The aim is to create a method of diagnosis, for example, assessment of the thermal clearance in the gas distribution mechanism (GDM), based on the application of neural-network models for analyzing the spectrum of vibration body parts of the engine
To achieve this goal it was necessary to solve the following tasks:
- To conduct theoretical studies of excitation and propagation characteristics of vibration on the hull to determine the engine capacity of diagnosing the state of timing on the basis of analysis of the spectrum of vibration cylinder engine.
- To investigate the possibility of using neural-network models to obtain diagnostic information about the thermal gap in timing by analyzing the spectrum of vibration of the cylinder block.
- The required structure of the neural-network model for analyzing the spectrum of vibration, providing after training to obtain reliable diagnostic information.
- An experimental setup, develop methodologies and conduct a pilot study of the spectra of vibration of the cylinder block engines to identify the effect of these changes on the technical state of engine components (for example, RM). Collect data bank on the spectra of vibration engine at normal and increased thermal gaps in the timing.
- Implement the software implementation of neural-network model, its training and on this basis show the effectiveness of neural networks for vibroacoustic diagnostics engine on the example of diagnosing thermal gap in timing.
- Assess the prospects of the developed methods in systems onboard diagnostics.
The efficiency of neural-network models for diagnosing the state of units and parts engine based on analysis of data on the vibrations of the cylinder block.
The structure of neural-network models, ensuring the reliable diagnostic information about the thermal gap in timing. Substantiated and confirmed the possibility of obtaining diagnostic information by analyzing the spectrum of vibration of the cylinder block without the angle of rotation of the engine crankshaft.
3 Characteristics of the object
Description
To control the engine ZMZ - 406, built next electrical system Figure 1. All elements of the electric motor control play many important roles, as, for example an incorrect indication transmitted from the sensor mass air flow control unit, can lead to engine shutdown. In the state of the engine is not working most of the elements to check meaningless because in the complex work they give some technical testimony, typical for each engine. It is therefore very important issue of diagnosis during engine operation.
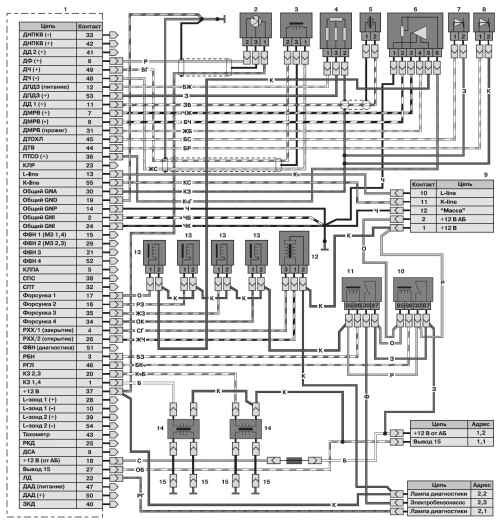
Figure 1. Electrical design of complex microprocessor engine control system
1 - control block M 1.5.4 engine, 2 - sensor phase 3 - sensor speed and synchronization, 4 - sensor throttle position, 5 - knock sensor, 6 - air mass flow sensor, 7 - coolant temperature sensor, 8 - air temperature sensor in the intake pipe 9 - diagnostic connector, and 10 - switch the engine management system, and 11 - the fuel pump relay, 12 - lights idling, 13 - nozzle, and 14 - ignition coil: 15 - Spark Plug
Influencing factors at work ICE
Upon receipt of evidence from the sensors electrical motor control, can determine the current or to predict possible future problems in the DIC (Table 1) [8].
Table 1. Factors influencing the work of ICE and sensors by identifying the problem.
Many factors affect |
The names of sensors, according to indications, which determine the problem. |
After starting, the engine is deaf. |
Sensor mass air flow |
Overheating |
Coolant temperature sensor |
Strike or failure of one of the cylinders |
For the sequential shutdown of cylinders, the output of the sensor phase will vary greatly. |
Contact with water in the fuel tank |
Sensor phase |
The engine will not start |
Defective crankshaft position sensor, a violation of its installation or break in the wires connecting the sensor to the controller. |
The engine does not develop full power and acceleration |
Defective gauge or absolute pressure. |
and many similar problems, so introducing sensors to more quickly trace the existing problems, obstacle to the normal operation of the engine. In this regard, have conducted a number of tests in time of internal combustion engines, for the establishment of normal sensor readings in different test conditions (Table 2).
Table 2: Permissible sensor readings during idle operation engine
|
sensor phase |
sensor speed and synchronization (norms) |
throttle position sensor (norms) |
knock sensor |
sensor mass air flow (norms) |
coolant temperature sensor (norms) |
air temperature sensor in the exhaust pipe (rules) |
1 |
1 |
0 |
0 |
1 |
0 |
25 |
24 |
2 |
2 |
740 |
0 |
1 |
2 |
30 |
50 |
3 |
3 |
800 |
0 |
0 |
3 |
40 |
70 |
4 |
4 |
800 |
0 |
0 |
5 |
50 |
75 |
5 |
2 |
840 |
10 |
0 |
7 |
60 |
75 |
6 |
4 |
880 |
15 |
0 |
10 |
60 |
75 |
7 |
3 |
920 |
20 |
0 |
14 |
65 |
80 |
8 |
2 |
960 |
22 |
0 |
18 |
65 |
80 |
9 |
1 |
1000 |
24 |
0 |
23 |
65 |
80 |
10 |
4 |
1200 |
28 |
0 |
28 |
65 |
85 |
11 |
3 |
1400 |
50 |
0 |
30 |
70 |
85 |
12 |
2 |
1600 |
70 |
0 |
35 |
70 |
85 |
13 |
1 |
1800 |
75 |
0 |
40 |
70 |
90 |
14 |
1 |
2000 |
100 |
0 |
50 |
75 |
90 |
15 |
2 |
2200 |
90 |
0 |
45 |
75 |
90 |
16 |
4 |
2000 |
70 |
0 |
40 |
75 |
90 |
17 |
3 |
1600 |
50 |
0 |
35 |
80 |
90 |
18 |
1 |
1200 |
30 |
0 |
20 |
80 |
80 |
19 |
3 |
900 |
10 |
0 |
10 |
80 |
80 |
20 |
4 |
840 |
0 |
0 |
10 |
75 |
80 |
Using computer diagnostics, we can determine fuel consumption, volume of air to enrich the fuel and fuel mixture, engine power when disconnecting one of the cylinders, throttle opening, etc.
4 Elements and methods of
Using an array of data transmitted from the sensors for each unit of time, you can analyze the operation of the engine, finding the problem and continuing problem with no resemblance to the data base of rules.
This creates a neural network, in which the number of input neurons corresponds to the number of input data sets of sensors which are connected with the engine and affect its performance. For our task we use a multilayer neural network (Figure 2). On the input layer receives data from sensors in the hidden layer are processed in conjunction with the base rules, and the output layer is formed by a decision - an error or a problem uptime engine.
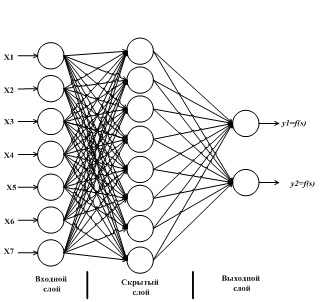
Figure 2. Scheme of multilayer neural network
Where X1 - X7 array of data from sensors phase, speed and synchronization, throttle position, detonation, mass air flow, coolant temperature, air temperature in the exhaust pipe, respectively, and y1 = f (s) and y2 = f (s) the results of the neural network of the state of DIC after diagnosis.
Also expected visual view of the real and admissible evidence in real time (Figure 3, 4).

Figure 3. Normal and defect of index sensor crankshaft rotation.
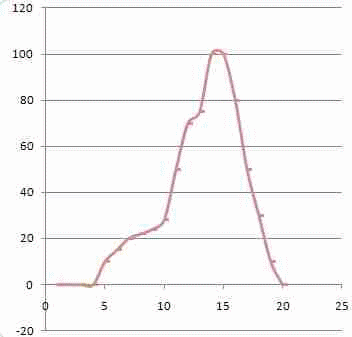 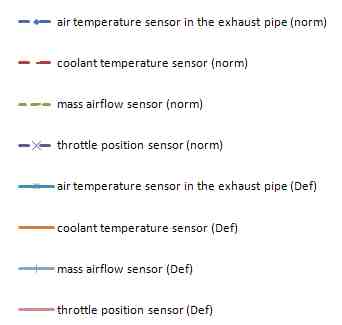
Figure 4 Normalized faulty readings of the sensors and control systems ICE
(Animated picture contains 8 frames, the delay between shots 1.5 seconds and delay in the final frame for 5 seconds,
amount of animation 152 KB)
The knowledge base plays an important role in the system, because it will be stored normal values of sensors in certain working conditions, as well as the margin of error. The knowledge base will store the list of failures and malfunctions, which will be used to identify the problems of the engine to be used by neural network.
Conclusion
The proposed predictive method will be used in designing expert systems for diagnosis and analysis of current and future problems in the engine GAZ 3110 with customized complete set of electrical control motor.
This Master's website has been development during the writing of master's work, that's why finish results will be absent in the abstract.
LIST OF SOURCES USED
- http://ru.wikipedia.org/ - а free, multi-lingual, multi-purpose Internet Encyclopedia.
- http://arteg.ru/catalog/index.php?Lev2=24 - auto service diagnostic equipment.
- Giryavets AK The theory of controlling motor gasoline AM Stroiizdat., 1997. 173 p.
- Pinsky FI, Davtyan RI Microprocessor control system motor engine. Textbook. - M.: Legion - Avtodata, 2004. -136s.
- Sosnin DA, Yakovlev, VF The latest automotive electronic systems. - Moscow: Solon-Press, 2005.
- Akimov SV, Chizhkov JP Electric cars. A textbook for high schools. - M.: ZAO KZHI "Driving" 2004.
- Diagnosis of automobile electronic systems devices SPE NTS. - Samara.: 2007.
- http://www.pawlin.com/content/view/43/16/
- AA Stotsky "Instruments and systems, management, monitoring, diagnostics." 2008 № 12 p. 47
- K.Il. Luthin Using neural-network models with vibroacoustic diagnostics engine (for example, diagnosis of cam timing). Abstract. Volgograd - 2009
top
|