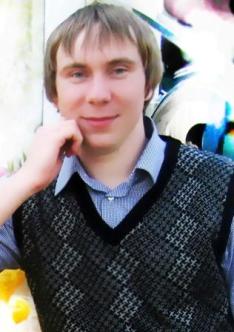
Ievgenii Poltavskyi
Faculty: | Physical-and-metallurgical |
Chair: | Indastrial thermal power |
Speciality: | Thermal power stations |
Theme of Master's thesis: | Analysis and improvement of methods and processes of gasification of solid fuels for use in thermal power |
Scientific adviser: |
Professor Dmitry Parkhomenko |
e-mail: |
loste@mail.ru |
MASTERS'S THESIS ABSTRACT
The limited world reserves of oil and natural gas, raising their prices and growing such environmental
problems cause transition of the world economy to the new energy sources.Clearly,that the mega coal mining regions as the Donbass,
will build its strategy on gradual transition to cleaner energy sources, namely coal-based.At the same time coal as energy source has very
significant negative characteristics.All this problems can find a positive solution due to coal gasification.
This direction of coal utilization is associated with its so-called "non-energy" use.
This is processing of coal on to other kindes of fuels (eg, combustible gas, coke, etc.) preceding or concomitant to receipt of a thermal energy.
For example, in Germany during World War II technology of coal gasification was actively used for production of motor fuels. In South Africa
the SASOL plant is using this technology, the first design of which was also performed in Germany in the 30's and 40's of the XX century,
Currently plant produces more than 100 kinds of products from brown coal. (This process of gasification is also known as "method of Lurgi».)
The most important characteristic of a coal gasification process is the possibility of its widespread use.
Uniqueness of the technology is connected the fact that the raw syngas we can receive more than one hundred products for various
industries: steel, power, chemicals, petrochemicals, etc.. The syngas is the raw material for alternative fuels, such as synthetic
natural gas (SNG), ethanol, diesel, jet fuel, as well as many others, thet the same time are environmentally friendly. In addition, the cost of
syngas is lower than natural.In favor of coal gasification, as well as the use of syngas as a whole, says the follow
ing:
– coal gasification provides an opportunity to produce energy and products at low cost, which provides competitive
advantage in the market of expensive energy;
– Although a major power plant using gas from coal, require large investments(like any other large-scale production),
operation costs by installing the gasification of coal will be potentially lower than for conventional coal plants, because the first are more
effective and do not require expensive equipment for environmental protection;
– gas from coal could replace increasingly expensive natural gas used as fuel or raw.
I believe that in a world that need to reduce greenhouse gases, coal gasification will benefit from
the economic as well as with environmental point of view.
Rapid development of coal gasification is projected in the world. Expected to increasing of coal gasification capacity by 70% by 2015,
with 80% of this growth occurring in Asia. The reason for this is not only an increase of population, but high prices of oil and natural
gas. It leds increased interest to alternative energy sources.
In my master work, I plan to undertake an analysis of existing brands of the Donbass coal; as the main
(basic); and new, dynamically developing, installations for the gasification, thereby identifying the most suitable ratio of coal and brand.
During the analysis will cover the following basic schemes gasification:
Scheme of "Lurgi" gasification technology.
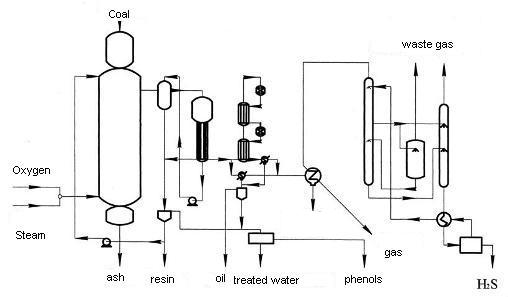
GasificationAutothermal Gasification under pressure in the sheet reactor with countercurrent movement
of coal and steam mixture.This gas generator is used successfully by many enterprises in a wide range of large-scale industrial assemblies.
Process established long time ago remains the only large-scale and quite perfect process of gasification under pressure.Despite the fact that many
technological stages of the process will still be refined, in technical terms this method is the most deeply developed currently.Productivity of a gasifier contemplates 75000 м3/h.
Scheme of "Vinkler" gasification technology.
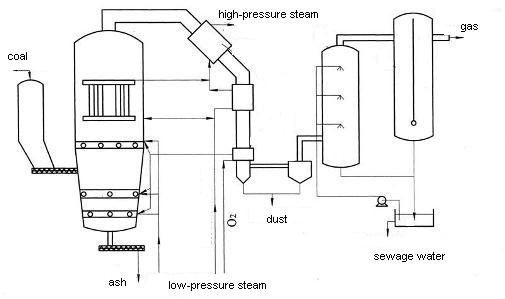
Autothermal water vapor - gasification with air or oxygen in a fluidized bed under normal pressure.
It is known 16 industrial units with 36 gas generators, nominal capacity of which synthesis gas is from 5000 to
60000 м3/h,which corresponds the consumption of coal approximately from 3 to 35 t/h.Nowadays some of these plants still being exploited.
A new version of the process involves gasification of dry brown coal with oxygen or direct hot air under pressure (fever heat - Winkler process)
Scheme of "Kopers-Tottsek" gasification technology.
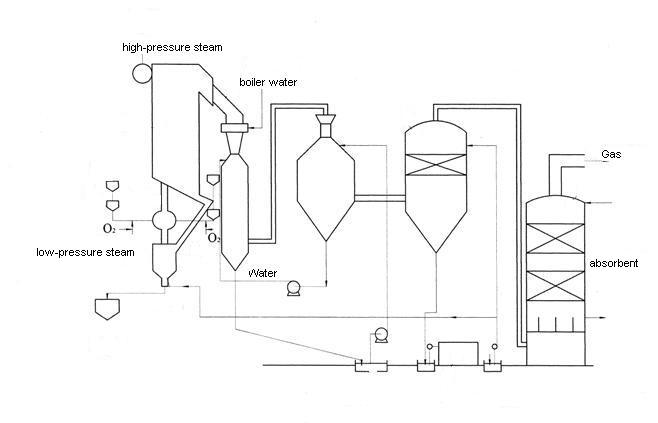
Autothermal steam – oxygen Gasification of balanced mixture under normal pressure in a parallel flow mode.
Gasifiers with two burners heads have been manufactured predominantly till now.The length of such gas generator is 7,5 м.
The inner diameter is up to 3,5 м ,internal volume is approximately 28 м3. The volume of a gas generator with four burners heads is twice more.
Consumption of coal contemplates 13,5 t/h for a gas generator with two burners heads, with four - 20,8 t/h.Production of unstripped gas contemplates
21000 м3/h, for a gas generator with two burners heads, with four - 32300 м3/h.
Scheme of "Teksako" gasification technology.
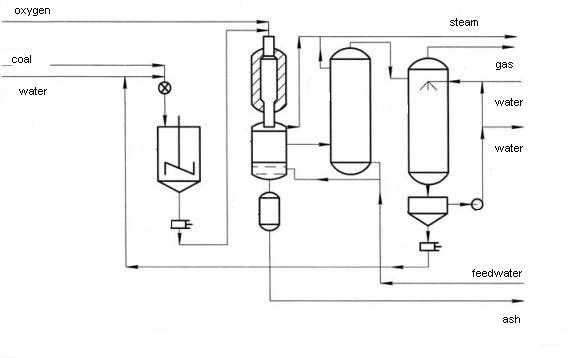
Autothermal Gasification of coal under pressure in forward flow of steam and oxygen.
In 1978 in the plant Morgantauie (West Virginia) firm Olney Mathieson Chemical Corporation commissioned the industrial installation with gas
productivity at the level of 6500 м3/h to obtain synthesis-gas by Texaco technology.This technology does not depend on the type of coal.
Scheme of "Lurgi-Rur-100" gasification technology.
Autothermal Gasification in a backflow with a steam – oxygen mixture in layered reactor under pressure of 10 MPa.
The gas generator is designed for pressures up to 10 MPa and flow rate of 7.1 t / h clean coal.There are two gazootbornyh channel for pure gas and
semi-coking gas, as well as a built-cold water jacket to produce high pressure steam.The generator has two alternately operating coal Gateway, a
shaft, which rotates with the distributor of coal and a few agitators, provided due to a tendency of coal to sintering under high pressure.
One of the possible targets of gas generator improvement is a change in particle size distribution of coal in the direction of small fractions.
In addition, zabalastovany coal should be used. The ultimate goal is to use a wet raw coal.In studies being conducted up to now stone coal was
used firstly, then hard-coal enrichment waste with high maintenance of ash and finally gas coal enrichment waste.
The gas generator for this process looks the following way:
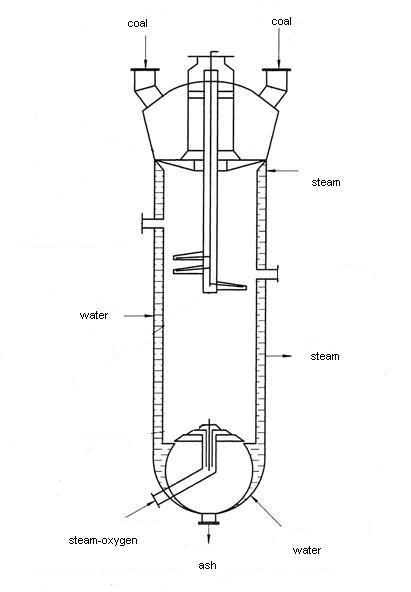
The analysis will receive the following data: enthalpy of formation of various grades of coal; assessing the impact of heat of combustion of fuel on
the enthalpy of its formation; influence of the enthalpy of formation on the basic parameters of the process of gasification;
influence of moisture and ash content of coal on its enthalpy of formation;the influence of enthalpy of formation of coal on the adiabatic
temperature and composition of gasification products; the influence of enthalpy of formation of coal on the heat of combustion and output of
the generator gas.Next will be a mathematical model of the process of gasification for the selected method and brand of coal. To construct the
mathematical models and engineering calculations suffice to consider the total kinetic parameters of reactions of carbon with О2,
СО2 and Н2О. The result of calculation should be the most steam / oxygen effective ratio of the mixture and its influence o
n the composition of synthesis gas at various temperatures and pressures and possible suggestions for improvement of either the gas generator,
or an existing process.
References:
1. Шпильрайн Э.Э., Малышенко СП., Кулешов Г.Г. Введение в водородную энергетику. Глава 2,1 Под ред. В.А. Легасова.-М.: Энергоатомиздат, 1984.-264 с.-С. 50—70..
2. Физика и научно-технический прогресс (ФиНаТ-2005)/Донец. нац. техн. ун-т, Физ.-металлург. фак
3. Мамась М.П. Теоретические аспекты применения водородного топлива и его продуктов/ Охрана навколишнього середовища/ ДонНТУ; Редкол.: Є.О. Башков.-2006.
4. Гольцов В.А., Везироглу Т.Н., Гольцова Л.Ф. Водородная цивилизация будущего – новая концепция Международной ассоциации водородной энергетики // Вестник водородной экономики и экологии. – Донецк: ДонНТУ, 2004.