CIRCULATING FLUIDIZED-BED TECHNOLOGY TOWARD ZERO CO2 EMISSIONS
ABSTRACT
Based on VGB, IEA statistics, demand for new power plant capacity in EU15 countries in 2030 will be 500 to 600 GW, due to the increase in energy demand and also the decommissioning of aging power plants. With many of the EU15 countries having large coal reserves, coal is still considered a viable candidate to account for a proportion of that new capacity. CO2 emissions will be one of the key issues to consider when planning the new capacity.
The proven high efficiency circulating fluidized-bed (CFB) technology offers a good solution for CO2 reduction both in repowering of coal fired power plants and in greenfield power plants. CFB technology has excellent fuel flexibility, offers the opportunity to further reduce CO2 emissions by co-combusting coal with biofuels. Foster Wheeler (FW) is working towards a near 100% reduction in CO2 with its Oxy-CFB technology, which is under development.
This paper presents the existing status of CFB technology in respect of boiler efficiency and fuel flexibility. Examples of the high-efficiency repowering CFB projects both with sub-and supercritical steam parameters from Estonia (Narva) and Poland (Turow and Lagisza) will be presented. The paper also describes experiences from one utility CFB project in Thailand (NPS) with high biofuel and coal co-combustion capability. The main advantages of the CFB technology for oxycombustion and a development plan for the Oxy-CFB will be presented.
INTRODUCTION
About 30% of European power generating capacity is coal fired and this percentage is much higher in some EU countries: over 90% in Poland and over 50% in the Czech Republic, Greece and Germany. These countries are using mainly fairly low-quality indigenous coal resources. Coal is expected to remain the leading fuel source of power generation for a long time. The EU is facing the challenge to reduce its greenhouse gas emissions by 8% by 2012 compared to 1990 levels, whilst also dealing with secure of energy supply, competitiveness and sustainable development in energy policy.
When considering either new plants or repowering of old plants, efficiency and environmental performance are key issues. High efficiency means lower fuel requirements, and lower levels of ash and emissions, including CO2. In the near future the main market for CFB in Europe will be the replacement of existing old coal-fired units. Utilization of proven high efficiency CFB technology is an ideal solution both for repowering and for new plants. CFB technology has proven excellent fuel flexibility and also offer the option to co-combust of biofuels with different grades of coals, which can further reduce CO2 emission.
CFB technology is now proven at utility-scale. Plant sizes up to 300 MWe are in operation today. The net efficiency of those conventional subcritical designs is approximately 3840%, depending on fuel and condenser conditions. During recent years, once-through supercritical (OTSC) CFB technology has been developed, enabling the next stage in CFB development to proceed medium-scale (<500 MWe) commercial projects such as Lagisza, with net efficiencies near 45%. However, scaling up the technology further to ‘real’ utility scale (600800MWe) with net efficiency of 4550% is needed to fulfill the future requirements of utility operators.
FW is continuously working on improving the efficiency and co-combustion capability of its CFB boilers. Efficiency increases and co-firing of coal with CO2neutral fuels provide a technically and economically feasible solution to the CO2 issue in the short and medium term, while major emission cuts possibly required in the future call for more powerful solutions. Post-combustion capture of CO2 from power station flue gases is considered technically feasible, but in combustion with air, the flue gas volumes are large and CO2 very much diluted with N2. Separation of CO2 from such a stream is costly, and other options are being explored.
In oxyfuel combustion systems, the fuel is burned in a mixture of pure O2 and recirculated flue gas, instead of air. The absence of air nitrogen produces a flue gas stream with a high concentration of CO2, making it much easier to separate the CO2. CFB technology appears to be ideally-suited for oxyfuel combustion, and as a longer term activity, FW is developing its CFB for oxycombustion to provide the potential for nearly 100% reduction of CO2.
REPOWERING WITH HIGH EFFICIENCY CFB
Many existing power plants in Europe are old and inefficient, and a large percentage need to be repowered. As shown in Figure 1, over 60% of capacity is more than 20 years old. In addition, the efficiency of these older power plants is modest.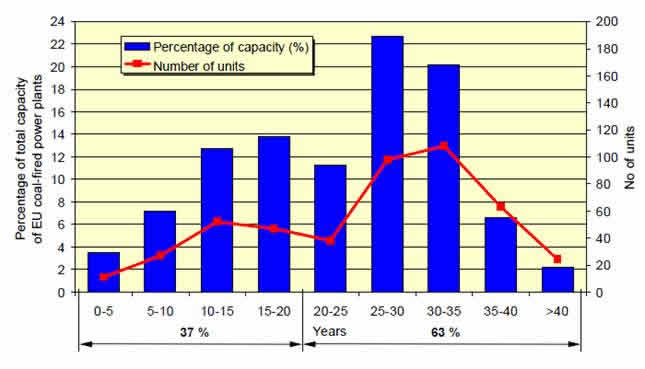
Elektrownia TURÓW S. A. Repowering Project
One of the most high-profile repowering projects using fluidized bed technology is the Turów power station in the Silesia region of southern Poland. This station, originally comprising 10 units each of 200 MWe in capacity, has undergone comprehensive repowering. Three of the old units have been modernized with backend emission equipment, and six units have been repowered with CFB boilers. One unit has been decommissioned. The Turów power station with six CFB units is currently the largest in the world based on fluidized-bed technology. Figure 2 shows the power plant with the first two units under construction. The space available for the new units was very limited, and the boilers had to fit into the old boiler house sections.
Figure 2. The Turów power station in Poland.
The repowering was carried out in three phases, all using Foster Wheeler CFB boilers and Alstom turbines. The first phase contracted at $375 million in June 1995 involved repowering of Units 1 and 2 (2 x 235 MWe). In November 1996, an agreement was reached on a $198 million second phase, to replace the third unit (235 MWe). A $660 million contract extension for Phase III covering Units 4, 5 and 6 was signed in December 1999. The first three units were of conventional CFB design, while FW's secondgeneration design was selected for the last three units. Implementing the second-generation design increased the capacity to 261.6MWe instead of 235 MWe, within the footprint of the old, pulverized coal 200 MWe units /1/.
The increase in capacity was achieved not only thanks to the inherent characteristics of the new technology, but the steam conditions of the boilers were also increased compared to the old pulverized coal (PC) boilers. The third phase units are designed to produce 195.5 kg/s of superheated steam at 16.65 MPa pressure and 565 °C temperature, and 180.7 kg/s of reheat steam at 3.85 MPa pressure and 565 °C temperature. Better steam values and better overall performance also mean better overall efficiency /1/. Design details can be found in /2/. The technology was considered very well-suited to burning low-heating-value Polish brown coal. Design ranges for the brown coal LHV, moisture content, ash content and sulfur content were 7.1-10.2MJ/kg., 40-48 %-w,6.5-31.5 %w and 0.4-0.8%w, respectively. Phase III boilers offered a substantial increase in efficiency, from 31.2% to 40.4% compared to the original boilers. Units 1 to 6 are now in successful operation, meeting all guarantees. It is noteworthy that there has been a considerable emissions reduction compared to the original situation. NOx has been cut by 19 %, SO2 by 92%, dust by 91% and CO2 by 24%.
MULTIFUEL COMBUSTION IN CFB
Improving the conditions for the effective use of renewable energy sources is a priority focus
area when developing power generation technologies. The following Figure 5 presents the
effect of plant net efficiency and the portion of biomass on CO2 emissions. When increasing
the net efficiency from the level of average European efficiency level (~35%) to the
efficiency levels of today’s CFBs (45%), CO2 emissions will be decreased by more than 20%.
When substituting also 15% coal with biomass, the CO2 emissions will be decreased by
approximately 35% with CFB technology.
Figure 5. Effect of plant net efficiency and portion of biomass on CO2 emissions.
Benefits and Costs
Oxycombustion in a CFB boiler seems to provide typical benefits of CFB boilers, in particular the fuel flexibility. Low combustion temperature contributes to low NOx levels and cost-effective SO2 capture with limestone. In addition, higher O2/CO2 ratios are expected to lead into higher combustion efficiency and will reduce the flue gas flow rates and thus increase the boiler efficiency. Smaller furnace volumes may lead into several percent cost reductions at the boiler island.
In greenfield and also retrofit applications it is possible to incorporate dual-firing capability in the CFB boiler design, that is, the same boiler can be operated in air-blown mode or in oxycombustion mode. Such a provision can be included to account for future requirements in new projects, or the operating mode can even be selected on the basis of overall cost optimization including varying price of CO2 emission credits.
PC vs. CFB in Oxycombustion
Competition between PC and CFB is somewhat similar to the air blown case, with differences in fuel flexibility, emissions with or without flue gas cleanup equipment, ash streams etc. However, the flexibility of the fluid-bed process may offer additional potential for CFB, e.g. in making temperatures more uniform with high O2 feed and local heat production rates, under varying load conditions. The smaller furnace volume and flue gas flow could reduce costs of the boiler island up to 8%. The inherent sulfur capture characteristics of CFB may provide an additional cost benefit, depending on the limits set by the plant and sequestration. The cost structure is similar to oxy-PC, as for both technologies the major cost increases, both the investment and operational costs, are due to the ASU and CO2 treatment. The numbers vary for various studies, and especially the transport and storage cost may deviate greatly due to location-specific factors and uncertainties in the storage options. In various studies [9, 10,11] including both PF and CFB hard-coal-firing cases, the specific investment cost has been slightly below 2,000 €/kWe (assuming 1 € = 1.20 $) for oxycombustion power plants, and about 1,100 – 1,300 €/kWe for air-blown units. The cost of electricity (COE) increases not only due to the higher investment but also because of the reduced efficiency (due to increased parasitic power consumption). For instance in a U.S. PF boiler study undertaken by FW [10], the COE increased from 46.1 to 64.1 $/MWh in air firing vs. oxycombustion.
REFERENCES
1. Lundqvist R. et. al. “Repowering and retrofitting of old power plants with circulating
fluidized bed technology in Central and Eastern Europe”, PowerGen Europe, 1998
2. Roman Walkowiak, Elektrownia Turów S.A., Andrzej Wójcik, Foster Wheeler Energy
International, Inc., Foster Wheeler Energia Polska Sp. z o.o. “Third Phase of Turów
Rehabilitation Project”, PowerGen Europe, 2001
3. Hotta A. et. al. ”Enhanced performance using CFB boilers to fire oil shale compared to
PC technology”, PowerGen Europe, 2005
4. Venäläinen I., Psik R. ”460 MWe Supercritical CFB Boiler Design for Łagisza Power
Plant”, PowerGen Europe, 2004
5. Venäläinen I et. al. “Scaling up OnceThrough
Supercritical CFB Boilers to 800 MWe ”,
PowerGen Europe, 2005
6. Pyykkönen A., Hotta A. ”Foster Wheeler 2 x150 MWe CFB boilers started up
successfully in NPS power plant in Thailand”, PowerGen Asia, 2000.