Реферат за темою випускної роботи
Зміст
1. Вступ
2. Предмет та об'єкт досліджень
3. Новизна роботи
4. Актуальність теми
5. Практична значимість результатів
6. Огляд розробок і досліджень по темі
6.1 Огляд розробок і досліджень на локальном уровне
6.2 Огляд розробок і досліджень на національному рівні
6.3 Огляд розробок і досліджень на світовому рівні
7. Огляд основних питань
8. Имеющиеся результаты
9. Висновки
Література
Вапно споживається різними галузями
промисловості, і тому до його якості
пред'являються різноманітні вимоги.
У сталеплавильному виробництві
застосовується вапно з дуже низькою
реакційною активністю, яке не взаємодіє
з вологою повітря й не містить гідрату окису
кальцію, у результаті розкладання якого
в сталеплавильних печах виділяється водень.
У мартенівському виробництві використовується
й слабообоженне вапно через те, що двоокис,
що виділяється у ванні, вуглецю сприяє кращому
перемішуванню розплаву. Для електрометалургійних
процесів потрібне вапно з дуже низьким змістом
залишкової СО2, що сприяє зниженню витрати
електроенергії в електродугових печах.
Одержання продукту із заданими властивостями,
що відповідає вимогам різних галузей народного
господарства, вимагає розробки відповідних
технологічних режимів і конструкцій печей.
Перелічені вище типи агрегатів мають суттєві
недоліки, пов'язані з підвищеною витратою палива
й непостійною якістю продукції, що випускається.
Показати актуальність
порівняння ресурсо-енергозберігаючих
показників альтернативних варіантів виробництва вапна, необхідність розробки рекомендацій з розвитку технологій виробництва вапна в Україні.
Новизна роботи полягає в тому, що пропонуються для впровадження
у виробництво вапна сучасні энерго-ресурсозберігаючі технології,
які дозволяють досягтися планованих цілей і задач цієї роботи.
Виробництво флюсів є однієї з найбільш масштабних і гострих проблем
чорної металургії особливо при виробництві особливо чистих сталеи. Одночасно
існує проблема раціонального використання мінералів, найважливішими з яких є
металургійні або флюсові вапняки. Незважаючи на поширеність вапняків у природі,
запаси флюсових вапняків обмежені.
У процесі виробництва вапна неминуче
утворюються побічні продукти й відходи, які, з одного боку,
складають великі втрати мінеральної сировини й, з іншої, завдають
величезної шкоди навколишньому середовищу. При видобутку й переробці
вапняної сировини утворюється значна кількість дрібних фракцій. Крупність
вапняку в процесі виробництва вапна залежить від типу застосовуваного
випалювального агрегату. У цей час використовують печі для виробництва кускового вапна.
Дрібну фракцію відправляють у відвали, що впливає на стан навколишнього середовища й знижує вихід вапняку.
У дипломній роботі планується провести аналіз ресурсозбереження й енергозбереження виробництва вапна,
представити можливі варіанти й технологічні схеми підготовки й утилізації вторинних матеріальних
і енергетичних ресурсів вапняного виробництва.
Результат даної роботи — розробка технологічних методів для впровадження
в умовах виробництва вапна. Використання цих методів дозволить підприємству організувати
більш ефективне виробництво вапна, забезпечивши мінімальний негативний вплив виробництва
на навколишнє середовище, дозволить знизити можливі екологічні платежі за викиди, знизить
собівартість продукції за рахунок зниження енерговитрат і зменшення екологічних виплат.
У Донецькому національному технічному університеті фізико-металургійного
факультету на кафедрі Рудно-термічні процеси й маловідходні технології велися розробки по
видобутку, використанню й застосуванню флюсів.
Одна з таких розробок представлена нижче.
Організація ресурсозбереження при видобутку й використанні флюсів у чорній металургії
До складу шихти металургійних меж входять основні флюси: вапняк і продукт його випалу — вапно.
Усі стадії підготовки й виробництва флюсів негативно впливають на стан навколишнього природного
середовища. Видобуток вапняків супроводжується зміною природніх гідрогеологічних умов. Це веде
до порушення режиму водойм і деформації земної поверхні. Знизити вплив відкритих розробок на гідросферу
можливо за рахунок створення надійного водозахисту кар'єру від поверхневих і підземних вод.
Основними забруднюючими речовинами при відкритому способі видобутку вапняків є пил і шкідливі гази.
Наймогутнішим джерелом викиду їх в атмосферу є вибух гірської маси. За один масовий вибух в атмосферу
викидається 100—125 т пилу й 6000—10000 м3 газів. Основні заходи щодо зниження пилегазовикидів при цьому
наступні: зрошення підготовлених до вибуху ділянок і прилягаючої до них зони й застосування вибухових
речовин з позитивним кисневим балансом (аміачна селітра), при вибуху яких виділяються не пил і отрутні
гази, а кисень. Для зниження пилу при роботах, гірську масу необхідно воложити водою методом зрошення.
Відкритий спосіб розробки родовищ вапняків супроводжується утвором значної кількості розкривних порід,
що йдуть у відвали. Так площа, займана відвалами ВАТ "Новотроїцьке рудоуправління" становить 6 млн.т,
у яких заскладовано більш 250 млн.т таких відходів. Ці матеріали є коштовною сировиною для будівельної
промисловості й можуть використовуватися в якості бутового каменю, щебенів, матеріалу для готування бетонів,
обладнання баластового шару залізничних колій, будівництва автомобільних доріг і інших цілей.
Основним напрямком по охороні земель при відкритій розробці родовищ вапняків є зменшення об'єму виробленого
простору й скорочення площ, що приділяються під відвали, за рахунок збільшення частки внутрішніх відвалів і
оптимізації параметрів зовнішніх. Для зниження пилу поверхні відпрацьованих відвалів необхідно робити біологічну
рекультивацію їх поверхні.
Збагачення вапняків здійснюється на дробильно-збагачувальних фабриках (ДЗФ) флюсо-добувних підприємств.
Основними стадіями збагачення є дроблення, класифікація й на деяких підприємствах промивання.
Ресурсозберігаюча технологія збагачення вапняків передбачає комплексне використання некондиційного
вапняку й хвостів збагачення в стройіндустрії й у сільськім господарстві, а також переведення
збагачувальних фабрик на безстічну технологію. Для поліпшення умов праці приміщення ДЗФ обладнуються
аспіраційними системами, після яких утворюється значна кількість пилу. Для усунення вторинного пилу
при розвантаженні пиловловлювачів пропонується застосовувати технологічну схему зі зволоженням пилу
в спеціальних вібраційних змішувачах, які пройшли промислове випробування при зволоженні металургійних
гідрофобних пилів на вітчизняних і закордонних підприємствах. Уловлений і зволожений пил можливо
використовувати в технологічному потоці ДЗФ для подальшої утилізації в суміжних галузях промисловості.
Рисунок 1 — Печі для випалу — вертикальні
Виробництво вапна здійснюється
на вапняно-випалювальних ділянках
металургійних підприємств, із
застосуванням різних агрегатів,
що працюють із використанням твердого
палива, що супроводжується викидами в
атмосферу токсичних газів. По екологічних
і технологічних міркуваннях такі печі,
повинні бути виведені з експлуатації,
а замість необхідно ввести печі, що
працюють на природному газі, що дозволить
знизити викиди шкідливих газів в атмосферу.
Основними сучасними агрегатами, що відповідають
цим цілям є обертові печі й печі киплячого шару.
Після очищення технологічних газів, що відходять
від цих агрегатів утворюється пил. Утвір пилу
залежить від типу випалювальної печі. У газі
після обертових печей утримується до 100 г/м3
пили, а після печей киплячого шару ще більше.
Крім відсівань вапна (0—8 мм) на вапняно-
випалювальних ділянках утворюється аспіраційно
вапняно-вапняковий пил (0—3 мм).
Зазначені відходи після відповідної підготовки
доцільно використовувати в агловиробництві для
інтенсифікації процесу спікання аглошихт і
для підготовки вологих шламів до утилізації.
Основним інтенсифікатором аглопроцесу є
відсівання вапна. При використанні вапна
доцільно здійснювати її здрібнювання.
Здрібнювання до 3—0 мм при подачі її в
аглошихту або до 12 мм при подачі в концентрати
й шлами на складах дозволить різко підвищити
ефективність її використання, знизити її
витрата на 10—20 %, зменшити потреба у
твердім паливі шляхом спікання, а також
інтенсифікувати процес агломерації й
підвищити міцність спека. Таким чином,
при видобутку, підготовці й раціональному
використанні флюсів у виробництві чорних
металів і в інших суміжних галузях промисловості
можна досягтися оптимального ступеня
ресурсозбереження [1,1—2].
В Україні є величезна кількість розробок по одержанню комплексних флюсів для киснево-конвертерної плавки. Усі розробки містять коштовний науково-технічний потенціал.
ЕМЗ
На Єнакіївському металургійному заводі в обертовій вапняно-випалювальній печі досліджувався процес одержання комплексного флюсу на основі вапна при випалі вапняку з окалиною. Розмір фракції вапняку й окалини становив 25-60 і 0-5 мм відповідно. Обертові печі опалюються природним газом із застосуванням пальника типу «труба в трубі». Спільний випал вапняку з окалиною при тій же продуктивності печі по вапну вимагає додаткової витрати тепла, яка повинен є компенсований збільшенням росходу природного газу. Однак, за рахунок високої температури газів, що відходять, витрата газу не змінювалася. Продукт випалу представляє шматки вапна, покриті міцної залізистою оболонкою. Ступінь чорності матеріалу при випалі чистого вапняку становить 0,27, а при випалі вапняку, покритого окалиною, 0,80. Невелике ядро «недоупала», спостережуване у звичайнім вапні, відсутнє у вапні, покритою оболонкою феритів [4, 597].
ДонНДІчермет і ЄМЗ
Донецький науково-дослідний інститут чорної металургії і Єнакіївський металургійний завод для прискорення шлакоутворення запропонували різні способи: поліпшення якості вапна (збільшення її реакційної здатності, попереднє здрібнювання, застосування доломітизированого вапна), заливання в конвертер готових рідких шлаків, використання кінцевих шлаків попередньої плавки, застосування спеціальних плавнів і флюсів, виготовлення й застосування штучних флюсів (агломерату, окатишів, брикетів, спеціальних сортів вапна), вдмухування пилоподібної перевести. Різноманітність пропонованих розв'язків пояснюється труднощами додання основному шлакоутворювальному матеріалу (флюсу) властивостей, які диктуються особливостями сучасного киснево-конвертерного виробництва. Розроблена технологія одержання флюсу являє собою доповнення до процесу випалу вапна в обертовій вапняно-випалювальній печі. Головною її особливістю є нанесення на поверхню вапна пилоподібних добавок, що флюсують (залізорудного концентрату, колошниковому пилу). На Єнакіївському металургійному заводі була споруджена досвідчена установка для одержання конвертерного флюсу. Покриття, що утворюється на вапні, поліпшує умови транспортування й зберігання флюсу. Стиранність флюсу вийшла приблизно вдвічі меншої, чому чистої вапна. Кількість вологи, поглиненої флюсом за першу добу, не перевищує 2 %. Присутність феритів «розпушує» структуру вапна й перешкоджає утвору суцільної плівки двухкальцієвого силікату [6, 410-412].
ДонНДІчермет
Донецьким науково-дослідним інститутом чорної металургії (ДонНДІчермет) розроблена технологія виробництва конвертерного залізофлюса із замасленої окалини методом гарячого окомковання. Вихід окалини з розвитком прокатного виробництва постійно збільшується. Окалина дрібних фракцій накопичується у відстійниках у вигляді нетранспортабельної маси й містить звичайно до 15 % мастил і 20 % вологи. Зміст заліза в окалині звичайно становить 70 %. Технологія забезпечує ефективну переробку окалини різних фракцій з високим змістом вологи й масел. технологія виробництва полягає в окомкованні, що пересипаються шихтових матеріалів розплавами, що утворюються на їхній поверхні при обробці шихти високотемпературним факелом. Перед оплавленням поверхні шихтові матеріали послідовно проходять усі стадії сушіння до декарбонізації, при цьому масло спочатку випаровується, а потім згоряє у високотемпературній окисній зоні над шаром шихти. Тому що використання замасленої окалини у вихідному стані в процесі гарячого окомковання важко, її попередньо змішують із 20 % ( по масі) вапна. Завдяки гідратації вапна вологою окалини остання здобуває сипкість і задовільну транспортабельність. Технологія поряд з утилізацією окалини забезпечує істотне зниження матеріалоємності киснево-конвертерного й прокатного виробництв [5, 32-33].
США
В США запропоновані
способи одержання феровапна
в обертовій печі. По одному способу в обертову
піч завантажують вапняк і окатиші діаметром 9,5—15,9 мм,
виготовлені з окалини й вапняку фракції 6,3—12,7 мм.
Обертова піч має довжину 44 м і діаметр 2,75 м. Витрата
матеріалів у зоні завантаження становить: окатишів 500
кг/година, вапняку 18200 кг/час. температуру випалу
підтримують у межах 1300—1375оC. Феровапно містить
близько 2 % оксидів заліза. Відмінною рисою іншого
способу є введення в обертову піч доломіту (13 т/ч) і
прокатної окалини (2—3,5 т/ч). При температурі випалу
близько 1100оC одержують флюс, що містить 1,07 Sio2;
22,29 % Fe2 про3; 42,26 % Cao; 33,13 % Mgo; 0,014 % S.
Отриманий флюс у кількості 68 кг/т шихти, що
завантажується, може бути використаний для
рафінування металу в конвертері [4, 49].
Росія
На ВАТ «Сєвєрсталь» успішно використовується
технологія застосування вапняно-магнезіального флюсу
в конвертерній плавці. Цей матеріал підвищує стійкість
футеровки конвертера в 1,5—1,7 рази при підтримці по
закінченню продувки металу змісту магнію в шлаках
більш 8 %. Використання в конвертерній плавці вапна
(60 % СаО; 30 % Mgo) у кількості до 30 кг/т сталі
призвело до росту стійкості футеровки до 3000 плавок.
В умовах ВАТ «Сєвєрсталь» уведення обоженного доломіту
з одночасним торкретуванням гарнісажу на футеровку
конвертера її стійкість досяглася 4500 плавок.
Швидкість зношування футеровки, особливо
виготовленої з периклазоуглеродістих вогнетривів,
залежить від змісту оксидів заліза й магнію в шлаках.
Чим більше насичений шлаки оксидами магнію, тем менше
активність оксидів заліза. При концентрації оксидів
магнію в шлаку вище межі насичення оксид магнію починає
виділятися зі шлаків. У цьому випадку на футеровці
можуть виникати нарости. Тому зменшення активності
заліза шлаку тільки добавками матеріалів приводить
до зміни процесів, що відбуваються при продувці,
погіршуючи технологічні показники плавки. Одним з
ефективних способів підвищення шлакоутворення й
підвищення реакційної здатності шлаків з одночасним
збільшенням у ньому кількості оксидів магнію -
використання в конвертерній плавці
вапняно-магнезіального флюсу, оксиди заліза якого
перешкоджають утвору силікатів кальцію й магнію. Флюс
виготовляють з доломіту й залізистого конвертерного
шламу. Доломит легко руйнується, а флюс має високу
міцність і стійкість до стирання. [3, 46—48].
Японія
Фірма «Син ниппон сэйтэцу», Японія,
розробила установку для обробки твердих відходів
прокатного виробництва, у якій у якості теплоносія
використовують гаряче доменне дуття. З дуттям несуться
органічні речовини в газоподібній формі, при цьому
неорганічні відходи перетворюються в залізовмісний
шлаки [4, 47]. У Японії запатентований спосіб
знежирення замасленої окалини шляхом подачі
останньої в розвантажувальний кінець обертової печі
при агломерації рудних матеріалів. пари, що виділяються,
масел в окисній зоні служать додатковим паливом, а
нагріту окалину разом з поверненням уводять в аглошихту
[4, 47].
СХЕМА ВИРОБНИЦТВА ВАПНА
Природна крейда із природною вологістю 25%
і сумарним змістом карбонатів кальцію й магнію
92—97% добувається відкритим способом
і автотранспортом доставляється на основне
виробництво. Основне виробництво складається зі стадій:
1. Ділянка приймання природної крейди
й готування крейдового шламу;
2. Ділянка зберігання запасу готового шламу;
3. Грубне відділення;
4. Підйомно-транспортна система готової продукції;
5. Силосний склад готової продукції;
6. Відділення газів, що відходять;
7. Допоміжні виробництва.
Рисунок 2 — Схема виробництва вапна
Природна крейда з автотранспорту розвантажується в прийомну кишеню глиноболтушки, туди ж подається вода в необхідних кількостях. При роботі глиноболтушки шматки мела за допомогою обладнання, що перемішує, подрібнюються, переходять у зважений стан, у глиноболтушці виходить крейдовий шлам., що має сметанообразную консистенцію. Для додання шламу необхідної рухливості в нього додається пластифікатор. Готовий шлам самопливом надходить у проміжний збірник шламу, що представляє собою залізобетонну ємність. У міру нагромадження, шлам із проміжного збірника откачується одним з насосів у вертикальний шламбасейн.
Готовий шлам під час знаходження в проміжному збірнику
шламу й горизонтальному шламбасейні перемішується за
допомогою подачі стисненого повітря через барботери.
Ділянка зберігання запасу готового шламу складається
із двох залізобетонних шламбасейнов і насосного шламу.
Грубне відділення містить у собі: Піч випалу,
Барабанний холодильник.
Піч працює за принципом протитечії.
З «холодного» кінця печі подається
сировина у вигляді шламу, на «гарячому» кінці
печі проводиться спалювання природного газу.
У міру просування матеріалу по печі з «холодного»
кінця до «гарячого», він проходить чотири зони:
• Зона сушіння — тут відбувається випар вологи зі шламу, надходить у зону шлам з вологістю—40—42%, наприкінці зони крейда з вологістю 5-12%;
• Зона нагрівання — тут відбувається нагрівання матеріалу до температури реакції термічної дисоціації;
• Зона дисоціації — тут відбувається перетворення крейди у вапно при температурах 1150—1350°С;
• Зона охолодження — тут вапно прохолоджується потоком холодного повітря. Далі вапно з температурою 600—800 °С надходить у холодильник барабанного типу, де прохолоджується до 100°С.
З холодильника вапно системою конвеєрів направляється
на склад готової продукції.
На всіх вузлах пересилань вапна передбачений
відсос повітря для зниження пилу в повітрі робочої
зони, з наступним його очищенням у системах аспірації.
Кінцевий реверсивний стрічковий конвеєр дозволяє
розподіляти вапно по силосам залежно від якості вапна.
гази, що відходять, віддаляються з «холодного» кінця
печі проходять двоступінчасте очищення. Спочатку димові
гази проходять попереднє, грубе очищення в пилових
камерах, потім остаточну в електрофільтрах.
Ступінь очищення 99,9%. Очищені гази,
що відходять, димососом викидаються в димар.
Уловлена в процесі очищення димових газів пил,
що містить 30—40% вапна й 60—70% мела,
збирається системою конвеєрів у бункер.
Використання відходів виробництва
вапна в аглодоменому виробництві
Розроблені різні варіанти й технологічні
схеми підготовки й утилізації вторинних
матеріальних і енергетичних ресурсів при
виробництві вапна. Використання відходів
виробництва вапна в аглодоменому виробництві.
Для зниження вологості аглошихти використовують
основну кількість сухих залізовмісних відходів
комбінату й вапняний пил газоочищення печей киплячого
шару. Істотний недолік печі киплячого шару -
значний (40—45 %) пилевинос дрібних фракцій
матеріалу з печі.Що вловлюється системою
газоочищення вапняний пил (крупністю 0—1 мм)
вивантажують із бункера в цементовоз
і доставляють на агловиробництва.
Частину її використовують при підготовці
замасленої окалини, а основну масу накачують
у бункери вапна шихтового відділення аглофабрики
й дозують у шихту (рис).
1 — автотранспорт для вапна;<
2 — магістраль стисненого повітря;
3 — відводи стисненого повітря;
4 — пневмотранспорт вапна;
5 — бункери вапна шихтового відділення;
6 — пиловловлювачі;
7 — конвеєр шихти;
8 — прийомний бункер;
9 — стрічковий конвеєр;
10 — склад, підготовки замасленої окалини;
11— штабель суміші окалини з вапном;
12 — залізничний вагон;
13 — вагоноперекидач;
14 — штабель рудної суміші;
15 — бункери рудної суміші шихтового відділення.
Рисунок 3 — Схема використання вапна на агловиробництві:
а — вапняного пилу на аглофабриці;
б — відсівань вапна на аглофабриці;
в — вапняного пилу при підготовці замасленої окалини.
Аналіз можливих схем перекладу виробництва вапна на
нові енергозберігаючі технології дозволяє
рекомендувати використання як сировину природної
крейди вологістю 23—28% без додавання вологи при г
отуванні шламу, переклад обертових печей на суху
технологію, що дозволяє зменшити питому витрату пали
ва з 270—310 до 210—220 кілограмів на одну тонну
вапна, або в середньому на 25% .
Енергозберігаюча
технологія виробництва вапна з
тонкомолотого вапняку
При видобутку й переробці вапняної
сировини утворюється значна кількість
дрібних фракцій. Крупність вапняку в
процесі виробництва вапна залежить від
типу застосовуваного випалювального
агрегату. У цей час використовують печі
для виробництва кускового вапна.
Дрібну фракцію відправляють у відва
ли. У той же час при виробництві заліз
орудних окатишів у технології внєпечної
обробки чавуну й стали застосовують мелко
дісперсне вапно з розміром часток менш 10
0 мкм, яку одержують шляхом млива кусково
го вапна в мірошницьких агрегатах. При ць
ому необхідно використовувати добавки, щ
о знижує якість вапна й підвищує її собів
артість. Крім того, процес млива сполуче
ний із проблемами екологічного характе
ру. Таким чином, виробництво вапна із др
ібних фракцій вапняку доцільно як з екол
огічної, так і з економічної точки зору.
Технологія одержання вапна
із брикетованої крейдової крихти
Мети технології:
— Одержання якісного вапна із крейдової крихти,
що утворюється при видобутку кускової крейди.
— Утилізація відходів добувної промисловості.
— Економія первинної сировини.
Найбільш ефективним напрямком використання
крейдової крихти, що утворюється при видобутку
мела, що і йде у відвал, є виробництво вапна.
Воно може бути налагоджене практично на тому ж
устаткуванні, що й виробництво звичайного вапна.
Основним методом окусковання крейдової крихти
перед випалом є брикетування. У якості сполучног
о кращі характеристики виявляє рідке скло. Можл
иво також використання деяких солей. Органічні
сполучні менш кращі, тому що містять сірку або
пиролізуються при випалі, у результаті чого брик
ети можуть передчасно руйнуватися. Використа
ння як сполучне відсівання вапна й вапняно
му пилу крейдових брикетів, що утворюють
ся при випалі, пояснюється необхідністю
їх утилізації у власнім виробництві,
а також їх більш низькою вартістю в порі
внянні з рідким склом. Схема технологі
ї представелена на малюнку.
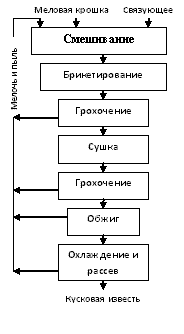
Рисунок 4 — Технологія виробництва вапна із крейдової крихти
Ця технологія забезпечує максимальний ступінь утилізації вторинних ресурсів у виробництві
флюсів у порівнянні з відомими аналогами. Забезпечує стабільно високу якість і низьку вартість продукту.
За результатами аналізу роботи, були виділені основні існуючі альтернативні
варіанти виробництва вапна з перероблених відходів:
— Енергозберігаюча швидкісна технологія виробництва високоякісного порошкового вапна;
— Енергозберігаюча технологія виробництва вапна з тонкомолотого вапняку;
— Технологія одержання вапна із брикетованої крейдової крихти.
Запропоновані технології дозволяють:
— втягнути в оборот значну кількість відходів;
— визволити величезні площі, зайняті під складування цих відходів;
— поліпшити екологічний стан прилягаючих територій;
— підвищити ефективність металургійного виробництва;
— одержати значний економічний ефект.
8. Висновок
У роботі розглянутий процес виробництва вапна, проведений аналіз ресурсозбереження, енергозбереження при виробництві, зазначена цінність вторинних ресурсів, запропоновані технологічні схеми підготовки й утилізації ВМР і ВЕР, дана техніко-економічна оцінка й екологічна оцінка ефективності організації ресурсозбереження й енергозбереження виробництва вапна.
1. Металлург, 8 (2004).
2. Табунщиков Н.П., Исследование шахтных известково-обжигательных печей. — М.—Л., 1977г. — 362 с.
3. Смирнов Л.А. Использование ожелезненного известково-магнезиального флюса
в конвертерной плавке // Сталь. — 2000, № 11. — С. 46—48.
4. Борисов В.М., Жук А.Д., Матюк И.Я. Перспективы использования
дисперсных отходов прокатного производства в черной металлургии (Обзор) //
Черная металлургия.- 2001, № 21 (905).— С. 45—60.
5. Гаврин Э.Г., Абросимов А.С. Производство конвертерного железофлюса
из промасленной окалины // Бюллетень.— 2005, № 2. —С. 32—33.
6. Дидковский В.К., Роговцев Н.И. Технология производства и
применения конвертерного флюса // Сталь. — 2003, № 5. — С. 410—412.
7. Металл и литьё Украины, 2—11’2002год.
8. Брусиловский Г.Н., Производство извести — М., 1954г. — 256 с.
9. Монастырев М.И., Производство извести — М., 1986г. — 208 с.
10. Табунщиков Н.П., Производство извести — М., 1974г. — 238 с.
11. Металл и литьё Украины, 3—4 ’2004год.
12. Технология производства железофлюса на
Докучаевском флюсо-доломитном комбинате [Электронный ресурс].-Режим доступа: URL:
http://www.dfdk.com.ua
13. Организация ресурсосбережения при добыче и использовании
флюсов в черной металлургии [Электронный ресурс]. — Режим доступа: URL: http://donntu.ru
14. Портал магистров Доннту, Пономарева Н.[Электронный ресурс]. — Режим доступа: URL:
http://masters.donntu
15. Производство извести [Электронный ресурс]. — Режим доступа: URL:
http://www.izvesta.com/
16. Технология производства извести [Электронный ресурс]. — Режим доступа: URL:
http://www.ptechnology.ru
17. Бойко, Федоров. Производство извести [Электронный ресурс]. — Режим доступа: URL:
http://waste.ua
|