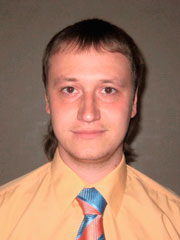
Тема випускної роботи | Підсистема оптимізаціі роботи автоматизованих технологічних комплексів із використанням багатокритеріальних генетичних алгоритмів |
Науковий керівник | к.т.н. доцент Секірін Александр Іванович |
Факультет | Комп'ютерних наук та технологій |
Кафедра | Автоматизованих систем керування |
Спеціальність | Інформаційні керуючі системи |
Зміст
1. Мета й завдання роботи
2. Вступ. Обгрунтування актуальності теми роботи.
3. Запланована наукова новизна
4. Запланована практична цінність
5. Огляд досліджень і розробок з теми
6. Постановка завдання дослідження
7. Опис об'єктно-оринтованого модулювання
8. Багатокритеріальні генетичні алгоритми
9. Заключення
10.Список літератури
Забезпечення високої ефективності роботи автоматизованих технологічних комплексів механообробки і максимального використання можливостей обладнання за рахунок використання розробленої комп'ютерної підсистеми багатокритеріальної оптимізації.
• Провести аналіз методів, моделей, алгоритмів та інструментальних засобів для оптимізації роботи АТК
• Провести вибір і обгрунтування методу для оптимізації роботи виробничої дільниці, вибрати основні критерії для оцінки ефективності роботи АТК
• Розробити узагальнену модель АТК
• Використовуючи модель АТК розробити і програмно реалізувати алгоритм для складання субоптимальних розкладів роботи устаткування враховуючи одночасно кілька критеріїв
На практиці людської діяльності, будь то професійна сфера чи повсякденне життя, постійно виникають завдання вибору, що передбачають в результаті прийняття рішення. Тільки в ряді випадків, особа, яка приймає рішення здійснює вибір (приймає рішення) інтуїтивно, спираючись на власний досвід і здоровий глузд, а вирішення більш складних завдань потребує особливого підходу, так як в даному випадку завдання прийняття рішення являє собою, по суті, вже оптимізаційну задачу .
У процесі управління складними технологічними комплексами та організаційно-технічними системами необхідно постійно приймати непрості рішення, пов'язані з урахуванням багатьох критеріїв протікання виробничих процесів і обмежень на ресурси. Без використання можливостей сучасної обчислювальної техніки досить складно зробити оптимальний вибір. У зв'язку з цим необхідно розробляти і впроваджувати системи підтримки прийняття рішень.[1]
Необхідність впровадження інформаційних систем управління більш гостро стоїть перед підприємствами машинобудівної галузі. Машинобудування є однією з найбільш наукомістких, складних, що вимагають висококваліфікованих кадрів галузей матеріального виробництва. Рівень розвитку машинобудування визначає рівень розвитку держави в цілому.[2]
Основою для створення комп'ютеризованих виробничих систем є автоматизовані технологічні комплекси (АТК). Це технологічні структури з закінченим виробничим циклом (ділянка, цех) та різним ступенем автоматизації. АТК включає в себе автоматизоване технологічне обладнання для механічної обробки деталей, а також допоміжне обладнання: автоматизований транспорт і автоматизовану складську систему.
АТК являє собою складний динамічний об'єкт. Для ефективного використання такого об'єкту необхідно формувати і динамічно коректувати з урахуванням зміни ситуації на виробництві оптимальний розклад роботи устаткування. На реальний виробничий процес впливає ряд зовнішніх факторів:
- збої в транспортно-складської системи;
- введення у виробництво нової деталі;
- вихід з ладу технологічного обладнання.
Для розробки методу оптимізації необхідна модель АТК, яка забезпечить близьке до реальності відображення процесу роботи устаткування і руху матеріальних і інформаційних потоків.
Оптимізації роботи АТК дуже трудомістка задача, вирішення якої має величезне значення для роботи всього підприємства. У традиційному підході присутні істотні недоліки, тому в результаті роботи планується отримати нові методи, які дозволяють створювати більш гнучкі моделі, ніж методи статистичної обробки інформації.
Для забезпечення високої ефективності роботи виробничих ділянок і максимального використання можливості обладнання, необхідно створювати близькі до оптимального розкладу роботи верстатів (ГВМ). Основним інструментом для цього є моделювання і оптимальне керування.
Невивченим залишається рух партій деталей безпосередньо у виробничому середовищі, на виробничій ділянці згідно з технологічним маршрутом. Створення програмних комплексів для моделювання та управління роботою виробничих ділянок, складання близьких до оптимальних розкладів роботи устаткування, є актуальною науково-технічною задачею [3].
На основі аналізу існуючих розробок в області еволюційних методів перспективним вирішенням складних комбінаторних задач багатокритеріальної оптимізації є використання генетичних алгоритмів. Це дозволить скоротити час отримання оптимальних або прийнятних розкладів роботи, і швидко реагувати на зміну виробничої ситуації.
Дане завдання вже вирішувалася за допомогою генетичних алгоритмів, де хромосоми ділилися на 2 рівні. Перший рівень відповідав за черговість запуску партій деталей в обробку, а другий за розмір цих партій.[3] Наукова новизна моєї роботи полягає в обліку одночасно декількох критеріїв завдяки використанню багатокритеріального підходу до оптимізації.
Моделювання роботи автоматизованих технологічних комплексів механообробки дозволить отримувати оцінки завантаження всіх видів обладнання та виявляти «вузькі місця», що знижують ефективність роботи АТК. Проведення на моделі аналізу різних варіантів їх усунення дозволить розробляти практичні рекомендації, що забезпечують підвищення завантаження технологічного обладнання. Застосування модифікованого дворівневого генетичного алгоритму спільно з об'єктною моделлю дозволить отримувати субоптимальних розкладу роботи обладнання за кількома критеріями, що забезпечує високу ефективність функціонування АТК механообробки.
• глобальний
Створений ряд програмних продуктів, які можна віднести до ERP систем, наприклад, LEKIN та TACTIC. Із закордонних авторів можна зазначити: Rong Zhou, Jun Zhang, Alan S. Manne та ін.
• національний
У цілому по Україні було знайдено безліч робіт із суміжних областей з розроблювальною підсистемою. Можна зазначити такі існуючі розробки по даній темі як: система технологічної підготовки, оперативного планування й диспетчерського контролю «ФОБОС», (MRP-II) ERP-система «Компас», СПРУТ-ОКП, Zenith SPPS та ін.
• локальний
За результатами пошуку серед матеріалів порталу магістрів ДонНТУ були знайдені роботи Андрєєнковой О.О. та Башєва В.Г. в которых рассматривались проблемы оптимальной загрузки оборудования и управления производственным участком в различных отраслях. у яких розглядалися проблеми оперативно-календарного планування в різних галузях. З наукових праць викладачів нашого університету по даній темі були знайдені роботи Секіріна О.І.
Фактично завдання оптимізації роботи складається з двох етапів:
- розробка моделі АТК
- розробка алгоритму оптимізації
Укрупнено робота підсистеми показана малюнку 1
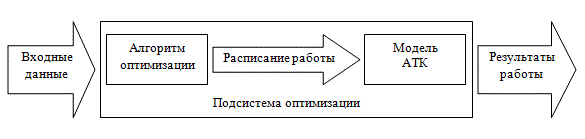
Малюнок 1 – схема роботи підсистеми оптимізації
У загальному вигляді завдання оптимізації можна описати таким чином: є n деталей, які необхідно обробити на L верстатах. При цьому необхідно скласти розклад роботи устаткування, черговість запуску деталей у виробництво і розміри партій запуску, які будуть задовольняти одночасно декільком критеріям оцінки якості розкладу.
Запишемо основні критерії, за якими може бути проведена оцінка ефективності отриманого розкладу:
1. Мінімізація тривалості циклу виготовлення деталей
Tопт = Т > min, (1.1)
где Т - загальний час виробничого циклу
где Тij - тривалість циклу технологічної операції i-ой партії деталей;
αij - тривалість простою перед початком виконання j-ої технологічній операції над i-ої партією деталей; p>
2. Максимізація середнього коефіцієнта завантаження технологічного обладнання (максимізація завантаження обладнання) p>
Копт з = 1/m∑Kз -> max, або Копт з = -1/m∑-Kз -> min (1.3)
где m - кількість обладнання
Kз – коефіцієнт завантаження i-го устаткування.
Коефіцієнт завантаження i-гo обладнання визначається відношенням часу продуктивної роботи до загального часу за формулою:
3. Мінімізація часових витрат на переналагодження обладнання
где tн – загальний час, витрачений на переналагодження обладнання
Τij – час, витрачений на переналагодження i-го верстата j-ий раз
n – кількість переналагоджень
Тобто фактично необхідно мінімізувати кількість перенастроювань:
n -> min (1.6)
При цьому необхідно враховувати наступні обмеження: p>
1. Обмеження за обсягами виготовлення: p>
Nпл=Nф, (1.7)
где Nф - фактичне виготовлене кількість деталей i-го типу (i=l,...,K);
Nпл - заданий у виробничій програмі кількість деталей i-го типу.
К - номенклатура деталей, що виготовляються.
2. Обмеження по термінах виготовлення:
Tпл ≥Tф , (1.8)
где Tф - фактичний термін виготовлення i-ої деталі (i=l,...,K);
Tпл - директивний термін виготовлення i-ої деталі.
3. Обмеження по фонду часу роботи технологічного обладнання:
где Тij - тривалість виконання технологічної операції;
Ri - ресурс i-ой групи обладнання.
У реальних умовах виробництва на функціонування цеху механообробки впливають різні впливи {V k }, які призводять до відхилень випуску деталей від виробничої програми.
Завданням управління є забезпечення випуску продукції згідно виробничій програмі (N пл ) по кількості і у встановлені терміни при ефективному використанні ресурсів (R l ) в умовах дії збурень (V k ). Забезпечення високої ефективності використання ресурсів (R l ) та функціонування цеху в цілому досягається за рахунок оптимізації розкладів роботи устаткування.
Процес виготовлення деталей D i (i = l, ..., п) розбивають на технологічні операції Про ij sub> (i = 1,..., п; j = l,..., m). Деталі одного типу поєднуються в транспортні партії і в розрізі розкладів розглядаються як технологічна одиниця. Кожна операція може бути виражена:
Оij = <Нij ,Тij>, (1.10)
где Нij - номер групи технологічного обладнання;
Тij - тривалість виконання операції.
Технологічний маршрут являє собою послідовність виконуваних операцій, які проходить i-я деталь у процесі обробки:
Мi = < Оi1, Оi2,..., Оim > (1.11)
Операция Оij повинна виконуватися без перерви з самого початку. Якщо позначити через tij - час початку виконання операції Оij, а через tij' -момент закінчення обробки, то має виконуватися рівність:
tij' = tij + Tij (1.12)
Очевидно, що час початку обробки залежить від часу виконання попередніх операцій і завжди виконується нерівність: tij ≤ tij+1. Тоді сукупність {tij} (i=1,..., n; j=l,..., m), що задовольняють всім технологічним і тимчасовим обмеженням, є розкладом роботи.
Опис об'єктно-оринтованого модулювання
Об'єктне моделювання - моделювання, при якому всі модельований компоненти системи представляються у вигляді об'єктів з особливою структурою, набором параметрів і методів, описаних за допомогою комп'ютерних мов моделювання. Такий підхід дозволяє легко створювати моделі об'єктів з уже створених прототипів, що робить процес моделювання та організації процесу взаємодії більш простим [7].
У сучасному об'єктно-орієнтованому моделюванні часто велике значення має поняття події. Об'єкти являють собою спрощений опис реальної суті наочної області, яка ідеалізується. Якщо відповідні моделі адекватні розв'язуваної задачі, то працювати з ними виявляється набагато зручніше, ніж з низькорівневим описом всіх можливих властивостей і реакцій об'єкта.
Об'єктно-орієнтоване моделювання грунтується на описі структури та поведінки проектованої системи, тобто, фактично, відповідає на два основних питання:
1) з яких частин складається система;
2) у чому полягає відповідальність кожної з частин.
Враховуючи модульний принцип побудови АТК, даний підхід є найбільш прийнятним. При побудові моделі виділено такі класи:
- гнучкий виробничий модуль (ГВМ);
- автоматизований транспортний модуль (АТМ);
- автоматизований склад (АС);
- система управління (СУ).
Для управління комплексом і створення подій введено додатковий керуючий клас «диспетчер подій».
Багатокритеріальні генетичні алгоритми
Генетичний алгоритм - це алгоритм, який дозволяє знайти задовільне рішення до аналітично нерозв'язним або важко вирішуваним проблем через послідовний підбір та комбінування шуканих параметрів з використанням механізмів, що нагадують біологічну еволюцію.[8]
При використанні ГА завдання оптимізації переформуліруется в задачу знаходження максимуму деякої функції f(x1, x2, …, xn), що називається функцією пристосованості (fitness function). Вона повинна невід'ємним значення на обмеженій області визначення (для того, щоб ми могли для кожної особини вважати її пристосованість, яка не може бути негативною), при цьому не потрібні безперервність і диференційовність.
Робота класичного ГА складається з трьох операцій: селекція, кроссінговер та мутація. На малюнку вони відображени під номерами 1, 2 та 3.
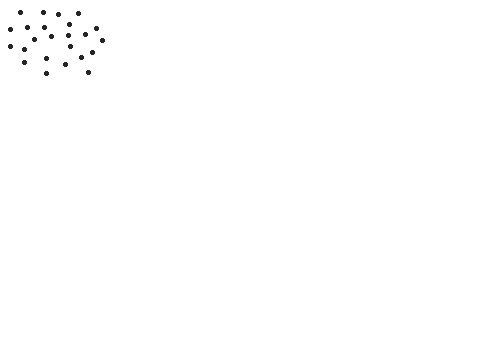
Притаманні генетичним алгоритмам властивості сприяють їх ефективному застосуванню при вирішенні задач багатокритеріальної оптимізації, оскільки ГА засновані на використанні безлічі потенційних рішень - популяції та глобальному пошуку в декількох напрямках. Також ГА не пред'являють ніяких вимог до виду цільових функцій і обмежень.
При застосуванні генетичних алгоритмів для вирішення конкретної задачі необхідно вибрати або розробити основні компоненти, такі як метод кодування потенційного рішення, генетичні оператори кросинговеру і мутації, метод відбору батьків, побудувати функцію пристосованості (фітнес-функцію), що дозволяє оцінювати потенційні рішення.
Оскільки багатокритеріальна оптимізація є природним розвитком звичайної чисельної або комбінаторної оптимізації, то багато розроблені методи були поширені на цей більш загальний випадок. При використанні ГА для багатокритеріальної оптимізації центральним питанням є побудова функції пристосованості. За останні десятиліття розроблено декілька підходів.
Для оптимізації роботи АТК пропонується використовувати метод зваженої функції. Він є природним розвитком класичних методів оптимізації, де нова «спільна » цільова функція будується із заданих у вигляді зваженої суми:
Тут кожної цільової функції fi(x) присвоюється своя вага wi і завдання зводиться до скалярного випадку. При цьому різні ваги wi дають різні рішення в сенсі Парето.
Враховуючи специфіку області застосування, метод є оптимальним, тому що критерії оцінки мають різну значущість. Наприклад, при упорі на скороченні часу тривалості циклу обробки деталі, тим самим зменшуючи час «пролежування» деталі на складі, може збільшитися час простою робочих місць, що є економічно недоцільним [2].
Заключення
Автоматизація обробного і допоміжного обладнання з використанням сучасних комп'ютерних технологій, в умовах розвитку машинобудування, є одним з основних напрямів технічного прогресу в машинобудуванні. Обладнання повинно забезпечувати виконання заданої номенклатури технологічних операцій на ділянці в установлений термін і мати здатність оперативно реагувати на зміну виробничої ситуації.
Для забезпечення високої ефективності роботи автоматизованих виробничих комплексів необхідно створювати близькі до оптимального розкладу роботи обладнання.
У роботі був проведений аналіз методів, моделей та алгоритмів для оптимізації роботи АТК, розглянуті інструментальні засоби, які використовуються для оперативного управління виробництвом в машинобудуванні. У результаті роботи було досліджено питання розробки методів багатокритеріальної оптимізації, виявлені переваги і недоліки існуючих комп'ютерних систем, методів та алгоритмів.
Для подолання недоліків запропоновано багатокритеріальний генетичний алгоритм для оптимізації роботи АТК на машинобудівному підприємстві.
Список літератури
1. Шеховцов А.В., Крючковский В.В., Мельник А.Н. «Решение многокритериальной оптимизации с использованием адаптивных алгоритмов» [электроний ресурс] — Режим доступу: http://aaecs.org/shehovcov
2. Сачко Н.С. Организация и оперативное управление машиностроительным производством // Н.С. Сачко – Новое знание, 2006. – 520 с.
3. Секирин А.И. Использование генетических алгоритмов для оптимизации работы автоматизированных технологических комплексов механообработки [электроний ресурс] — Режим доступу: http://masters.donntu.ru/2009/kita/aleksandrova
4. В.И. Ковальский Организация и планирование производства на машиностроительном предприятии. // М.: Машиностроение, 1986. – 288с.
5. Туровец О.Г. Организация производства и управления предприятием. // О.Г. Туровец, В.Б. Родионов, М.И. Бухалков. – М: Издательский дом «Инфа-М», 2005. – 346с.
6. М. Скворцова Математическое моделирование [электроний ресурс] — Режим доступу: http://mat.1september.ru
7. Николаенко В.Л., Паршук А.П. Статья: Методика объектного моделирования системы оптимизации производственных затрат [электроний ресурс] — Режим доступу: http://www.pdaa.edu.ua/np/pdf2/36.pdf
8. Исаев С. Популярно о генетических алгоритмах [электроний ресурс] — Режим доступу: http://algolist.manual.ru
9. Дилигенский Н.В., Дымова Л.Г., Севастьянинов П.В. «Нечеткое моделирование и многокритериальная оптимизация производственных систем» // М.: «Издательство Машиностроение - 1», 2004
10. В.М. Курейчик "Генетические алгоритмы и их применение" // Издательство ТРТУ, издание второе, 2002. - 242 с.